精馏塔精馏段温度串级系统.docx
《精馏塔精馏段温度串级系统.docx》由会员分享,可在线阅读,更多相关《精馏塔精馏段温度串级系统.docx(18页珍藏版)》请在冰豆网上搜索。
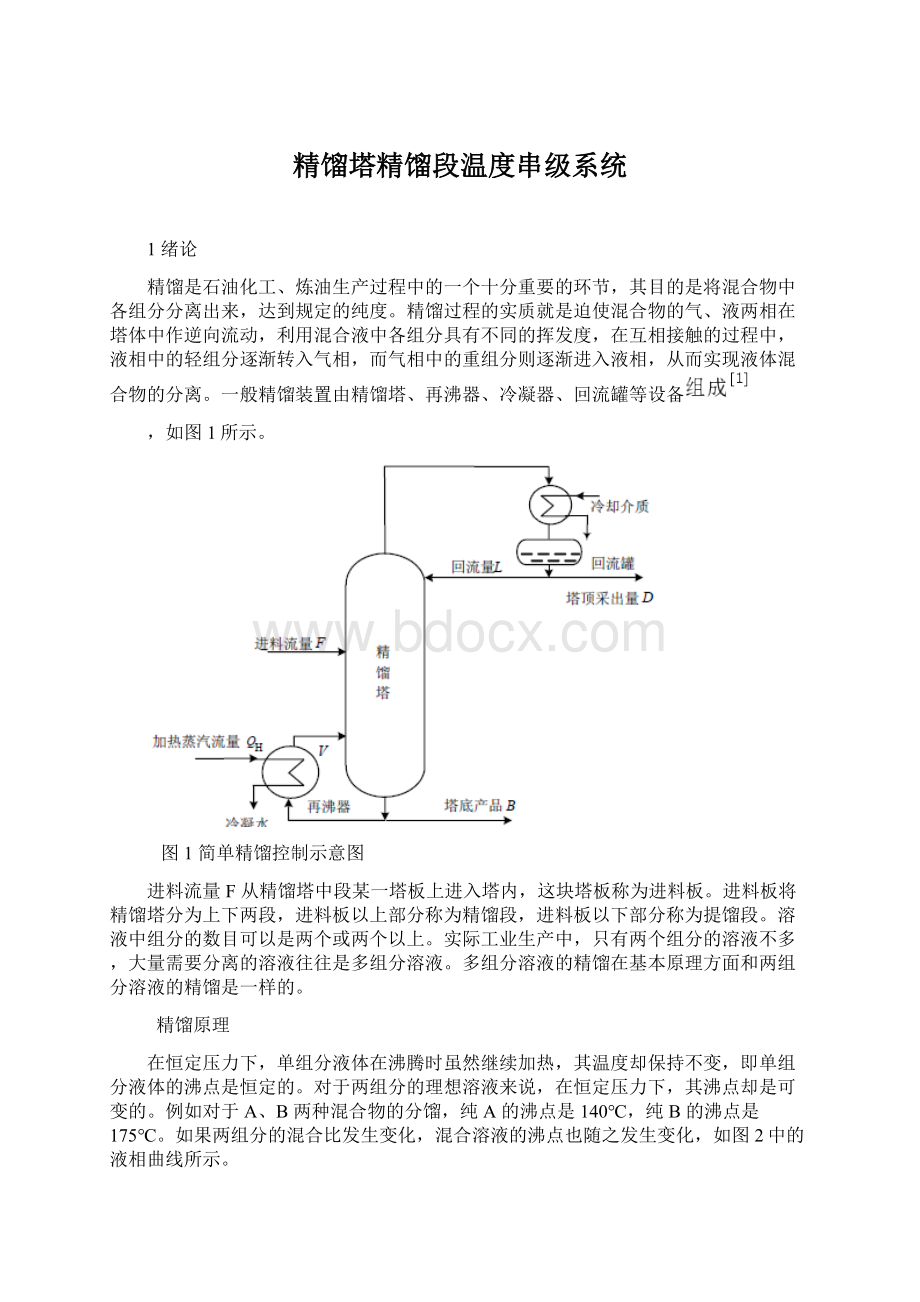
精馏塔精馏段温度串级系统
1绪论
精馏是石油化工、炼油生产过程中的一个十分重要的环节,其目的是将混合物中各组分分离出来,达到规定的纯度。
精馏过程的实质就是迫使混合物的气、液两相在塔体中作逆向流动,利用混合液中各组分具有不同的挥发度,在互相接触的过程中,液相中的轻组分逐渐转入气相,而气相中的重组分则逐渐进入液相,从而实现液体混合物的分离。
一般精馏装置由精馏塔、再沸器、冷凝器、回流罐等设备
,如图1所示。
图1简单精馏控制示意图
进料流量F从精馏塔中段某一塔板上进入塔内,这块塔板称为进料板。
进料板将精馏塔分为上下两段,进料板以上部分称为精馏段,进料板以下部分称为提馏段。
溶液中组分的数目可以是两个或两个以上。
实际工业生产中,只有两个组分的溶液不多,大量需要分离的溶液往往是多组分溶液。
多组分溶液的精馏在基本原理方面和两组分溶液的精馏是一样的。
精馏原理
在恒定压力下,单组分液体在沸腾时虽然继续加热,其温度却保持不变,即单组分液体的沸点是恒定的。
对于两组分的理想溶液来说,在恒定压力下,其沸点却是可变的。
例如对于A、B两种混合物的分馏,纯A的沸点是140℃,纯B的沸点是175℃。
如果两组分的混合比发生变化,混合溶液的沸点也随之发生变化,如图2中的液相曲线所示。
图2
设原溶液中A占20%,B占80%,此混合液的沸点是164.5℃,加热使混合液体沸腾。
这时,与液相共存的气相组分比是A占%,B占%。
这些气体单独冷凝后所形成的混合液体中,A占%,B占%;如果使此冷凝后的混合液体沸腾,其沸点是154.5℃。
这时气相组分比又变成A占%,B占%,这样反复进行上述操作,不断蒸发和冷凝,最终就可将A分离
。
串级控制
串级控制是改善调节质量极为有效的方法,在过程控制中得到了广泛的应用。
对精馏塔精馏段温度串级控制系统引起出口温度的因素很多:
被加热流量的和温度的扰动,压力的波动、热质的变化,回流量的扰动等,而对这些扰动单回路控制系统并不能把所有的干扰都包含进去,不能是出口温度稳定在要求的值上,为解决上述滞后时间和控制要求之间的矛盾,保持出口流量温度的恒定,可以通过温度串级控制系统来实现。
2精馏塔精馏段温度串级系统的原理与结构
单回路控制系统能解决工业过程自动化过程的大量参数定值控制问题。
对于多数复杂控制系统,如多输入多输出系统、大滞后系统和扰动较大的系统等简单控制系统就很难控制,无法满足控制系统的
。
串级控制系统在改善复杂控制系统的控制指标方面具有较大的优势。
变量的选择
被控变量的选择
对于二元精馏塔,当塔压恒定时,温度与成分之间有一一对应的关系,因此,常用温度作为被控量。
对于多元精馏塔.由于石油化工过程中精馏产品大多数是碳氢化合物的同系物。
在一定塔压下,温度与成分之间仍有较好的对应关系。
误差较小。
因此。
绝大多数精馏塔当塔压恒定时采用温度作为间接质量指标。
操纵变量的选择
精馏段的温度控制精馏段温度控制以精馏段产品的质量为控制目标.在恒压下根据温度检测点的位置不同。
有塔顶温度控制、灵敏板温度控制和中温控制等类型。
操纵变量可选择回流量或塔顶采出量。
而回流量L的动态响应快,温度稍有变化,即可通过调节回流量L加以控制,能够很好的克服扰动对选择如图1所示在
。
工艺描述
影响精馏塔提馏段过程的因素是多方面的,而精镏段是在一定物料平衡和能量平衡的基础上进行操作的,分析精馏塔的无聊和能量平衡对制定精馏塔精馏段的控制至关重要。
精馏塔的基本
。
以二元简单精馏为例,介绍物料平衡和能量平衡的基本关系。
物料平衡:
(2-1)
增大,
,
减小。
式中F,D,B——进料、顶馏出液和底馏出液量;
——进料、顶馏出液和底馏出液中轻组分含量。
能量平衡:
(2-2)
式中分离度
s增大,
增大,
减小。
说明塔系统分离效果增大
为塔特性因子,V为上升蒸汽量,是有再沸器施加热量来提高的。
增大,分离效果增大,能耗增大。
对于一个既定的塔,进料组分一定,
和
一定,
完全确定。
分析精馏塔提馏段过程,本文对主回路采用串级控制系统,其主、副诃节器所起作用各有侧重。
主调节器起定值控制作用,且主控参数(提馏段温度)允许波动范围很小,一般要求无余差,因此采用需要高精度的免疫PID控制器;由于再沸器加热量的变化能够较快地反映在提馏段温度变化上,且能够通过阀门进行控制,因此选择回流罐的液位量控制作为串级控制的副控参数。
在串级控制中,副调节器起随动控制作用,且副控参数的调节也是为了保证主控参数的控制质量,可以有一定的余差,因此副调节器采用P调节器。
由于进料量和进料温度对进料馏段温度影响较大。
精馏塔精馏段控制的原理
我们的控制目的是使塔温保持恒定,现选用精馏段的温度,与回流量来构成串级随动控制.如图3所示图中TC表示温度调节器,LC表示量调节器液位调节器,TC通常按PID调节规律,流量调节器按P调节规律。
当温度发生变化时,由主调节器(温度调节器TC)进行控制,其输出作为副调节器(液位调节器LC)的给定值,最终控制阀门的开度,主控回路的输出作为副控回路设定值修正的依据,副控回路的输出作为真正的控制量作用于被控对象,液位一旦发生变化,副控回路及时地控制阀门的开度位置,较快地克服了液位的变化对出料温度的影响如果液位是恒定的,只需测量实际温度,并使其与温度设定值相比较,利用二者的偏差控制管道上的阀门就能保持温度的恒定。
路中,以补偿过程的动态特性,使被控对象的滞后时间
超前反映到控制器,有效地解决了大惯性环节的时间滞后问题,减少了系统的超调量,加速了系统的调节过程,另外,通过增大液位调节器的比例增益,系统的等效时间常数可以获得较小的数值,从而增加了副控回路的响应速度,提高了系统的工作
。
在这个计算机串级随动控制系统中,串级控制起到了及时检测系统中可能引起被控量发生变化的一些因素并加控制,阀位与流量得到了及时的调节,使塔温的控制达到了良好的控制效果,并且使系统具有一定的自适应能力,有效地解决了对象的等效纯滞后时间
很长的问题。
二次干扰为该系统的主要扰动,副控回路有效而快速地克服二次扰动的影响。
当扰动发生在副回路内,例如液位发生波动引起精馏段的温度变化时,由于有副控回路的存在,液位调节器能及时地动作,快速消除了扰动的影响;当扰动发生在副控回路以外时,如物料、能量的转输变化引起提馏段的温度变化,温度调节器及时改变其输出信号,由副控回路去改
变流量,克服了扰动
图3精馏塔精馏段温度串级控制系统
3仪表的选型
过程控制系统一般都是负反馈控制系统,主要由被控对象、传感器和变送器、控制器
和执行机构等四部分组成。
其中,传感器与变送器属于检测仪表,控制器和执行机构则属
于控制仪表。
检测与控制仪表是过程控制系统的基本组成部分,是实现生产过程自动化必
不可少的工具。
检测仪表将生产工艺参数变为电流信号或气压信号后,不仅要求由显示仪表显示或记
录,让人们了解生产过程的情况,还需要将信号传送给控制仪表,对生产过程进行自动控
制,使工艺参数符合预期要求。
检测仪表将生产过程中有关的工艺参数准确及时地测量出
来,并转换为标准信号如0~10mADC电流信号,4~20mADC电流信号或20~100kPa
的气压信号,送往控制仪表或显
温度控制(调节器)SR3-8I选型
SR1/SR3/SR4级PID调节器选
温度变送器
变送器如果由两个用来测量温差的传感器组成,输出信号与温差之间有一给定的连续函数关系。
故称为温度变送器。
变送器输出信号与温度变量之间有一给定的连续函数关系(通常为线性函数),早期生产的变送器其输出信号与温度传感器的电阻值(或电压值)之间呈线性函数关系。
标准化输出信号主要为0mA~10mA和4mA~20mA(或1V~5V)的直流电信号。
不排除具有特殊规定的其他标准化输出信号。
变送器有电动单元组合仪表系列的(DDZ-Ⅱ型、DDZ-Ⅲ型和DDZ-S型)和小型化模块式的,多功能智能型的。
前者均不带传感器,后两类变送器可以方便的与热电偶或热电阻组成带传感器的变送器。
所以在次选用DDZ-III型变送器。
热电偶温度变送器技术指标[9]
冷端温度补偿:
-15~+75℃
输出电流:
4~20mA
输出回路供电:
12~30VDC
最小工作电压:
12VDC
负载电阻与供电电源的关系:
负载电阻(包括引线电阻)=供电电源(V)-12(V)/0.02A
※综合参数
标准精度:
±%
温度漂移:
基本误差/10℃
热电阻引线补偿:
±%(0~10Ω)
负载变化影响:
±%(允许负载范围内)
电源变化影响:
±%(12~30V)
开机响应时间:
<1S(0~90%)
工作环境温度:
-20~+70℃
防护等级:
IP00/IP54(传感器防护等级决定)
电磁兼容:
符合IEC61000,EN61000
液位调节器选型
液位调节器主要
1、测量范围:
0—6000mm
2、测量精度:
±10mm
3、介质密度:
≥0.5g/cm
4、工作压力:
5、工作温度:
80℃120℃200℃
6、介质粘度:
≤
(对粘度大或低温易结晶介质要选用夹套型)
7、测量界位比重差:
0.15g/cm
液位变
液位变送器是对压力变送器技术的延伸和发展,根据不同比重的液体在不同高度所产生压力成线性关系的原理,实现对水、油及糊状物的体积、液高、重量的准确测量和传送
主要技术指标
测量范围:
~100m(由用户自选)
精度:
、、级
工作温度:
-20~200℃
输出信号:
二线制4~20mADC
电源电压:
标准24VDC(12~36VDC)
不灵敏区:
≤±%FS
负载能力:
0-600Ω
相对温度:
≤85%
防护等级:
IP68
防爆标志:
ExiaⅡCT4-6
调节阀选型
1)阀型的选择
调节阀阀型最好选择功能齐全、重量轻的全功能超轻型调节阀去代替其他调节阀产品,可简化选用期货产品因功能不齐全而担心选型不当(如直行程类阀的防堵问题;切断与压差的关系等)的麻烦。
2)执行机构的选择
执行机构的选择:
①选用进口电子式执行机构,克服一系列不可靠问题;②薄膜式执行机构选用精小型系列;③活塞式执行机构应考虑齿轮条式;④告诉阀关闭的压差,由生产厂选定执行机构大小。
3)材料的选择
这一问题较复杂。
因许多腐蚀介质对聚四氟乙烯不存在腐蚀,故宜选用全四氟耐腐蚀阀,使耐腐蚀场合的选型得到大大简化,只是当温度>180℃、<-40℃、PN≥时,再支考虑耐蚀合金。
4)弹簧范围的选择
对配薄膜执行机构的阀,现绝大部分场合均配定位器,可以充分利用250KPa的气源,选用一种中等刚度,又可兼顾较大输出力的弹簧60~180KPa;同理,对活塞执行机构选用150~300KPa.
5)流量特性的选择
①当参数弄不准时,选对数特性:
②当被调系统的响应速度较快时,如流量调节、液体压力调节,选对数特性;当系统的响应速度较慢时,液位系统、温度调节系统、选直线特性;③S值较小时,选对数特性;④阀可能小开度工作时,选对数特性。
• 流向的选择
对单密封类的直行程调节阀,通常选流开型;当要求切断和防冲蚀时,选流闭型(流闭型稳定性差,应考虑相应的稳定性措施)。
• 填料的选择
当带定位器时,尽量选用耐磨、耐温、寿命长、密封可靠的石墨填料。
• 定位器与转换器的选择
转换器没有定位的提高输出力、提高动作速度、提高位置精度的三大作用,故通常应选用定位器(定位器与转换器价格
。
4精馏塔精馏段温度串级控制的研究
精馏过程由于内在机理复杂,对控制作用的响应缓慢,参数间关联密切,因此控制要求高,难度大。
又由于其非线性、强耦合、质量参数在线检测困难等特点,使得精馏塔的自动控制问题成为过程控制界研究
精馏塔借助于冷凝器的冷却来保持其精馏段的温度恒定,由于冷凝器的传热和精馏塔的传质过程,使对象的等效纯滞后时间
很长。
实验和经验表明,塔温控制对象可近似为一个纯滞后环节和一个一阶环节组
。
在精馏塔精馏段温度控制系统中,保持回流量的恒定与塔温发生变化能及时地调节回流阀门的开度使塔温保持恒定是我们的最终控制目的。
如果采用传统的控制算法,回流量得不到及时地调节,温度变化以后才调节回流阀门的开度来改变蒸气的供给量,产生了过程上的时间滞后问题,使被控对象的等效时间很长不能及时地反应系统所承受的扰动,从而达不到预期的控制效果。
本文针对这个问题,提出采用主控回路和副控回路相配合的温度串级控制系统,主回路控制器采用PID控制算法,副回路采用P控制算法,最大可能的满足控制系统的要求。
图4精馏塔精馏段温度串级控制系统结构图
精馏塔温度串级过程中的主要假设
(1)塔段(房室,Compartment)和塔板
严格机理动态模型由于模型结构复杂,计算时间长,难以用于实际应用,
因此模型简化是重要的一环。
1986年Benallow提出的房室(Compartment)简
化方法是最有效的模型简化方法之一。
它根据邻近塔板的内回流量、温度等变量
相差较小的特点,将几块塔板合为一个塔段并作为一个控制体来分析和建模。
在进行精馏塔的塔段划分时,依据两个原则。
一是根据生产装置的特点,比如循环取热涉及的塔板划为一个段,有侧线输出的塔板一般作为塔段的分割点。
另一个原则是塔段含塔板数不宜过大,在本文模型中一个塔段最多含三块塔板。
(2)用虚拟组份划分石油馏份
复杂的石油馏份是无法用纯组成来描述的,目前比较成熟也得到认可的方法
是用虚拟组份代表石油馏份,有其相应的一整套计算公式和经验关联式用于计算
虚拟组份的物性。
由于所建立的精馏塔模型为通用模型,对虚拟组份的划分不十
分严格,可用于二元或多元轻重组份的模型建立。
(3)塔板汽液混合情况
每层塔板中的汽液两相充分混合,或说处于径向全返混状态,可以用集中
参数模型处理,Murphree板效率可应用于每个塔板。
(4)塔板汽液平衡情况
汽液两相物流在离开塔板时达到汽液相平衡,在此基础上可以得到基于平
衡级的MESH方程,大大简化了模型的计算。
(5)塔内气体
气体在塔内气速很高,在塔板上停留时间很短,因此,同液体蓄存量相比,
气体蓄存量可以忽略不计,只考虑气体在塔板空间的动态过程。
(6)塔板内温度分布均匀,压力恒定。
(7)忽略塔器设备的热容及热量损失。
(8)塔板间汽液相传递滞后忽略不计。
在以上主要假设条件下,可建立基于平衡级的精馏塔MESH方程的数学表
。
模型的建立
图5精馏塔精馏段温度控制系统方框图
式
中
为等效被控过程的放大系数,
等效被控过程的时间常数。
可见等效被控过程的时间常数小于被控过程的时间常数,随着
的增大,时间常数减小的效果更明显,副回路的动态响应快的多。
(4-1)
一次扰动作用下,扰动回路传递函数为
(4-2)
系统输出对输入的传递函数为
(4-3)
主回路系统采用PID控制,副回路采用P控制能最大限度的满足被控对象的控制通道的放大系数较大,时间常数较小,滞后时间较
。
以二元精馏塔为例,其模
为:
(4-4)
其中:
为塔顶馏出物浓度(mol%);
为塔底馏出物浓度(mol%);
为回流量(lb/min);
为蒸汽输入量(lb/min);d(t)为进料速率(lb/min)。
而对于精馏段不存在
,
,则二元精馏塔的模型:
(4-5)
上式
为出口流量,而本课题研究的是对出口温度T的控制,所以上式需转变为温度的函数,由于存在
,则精馏塔主对象传递函数可简化为:
(4-6)
副对象是采用典型的惯性环节,传递函数是
调节阀
,取
=1
副调节器采用比例调节(P)规律,传递函数为
,调节阀和副测量变送器分别为
,
。
.
主调节器采用PID控制规律。
液位计选用单溶液位计传递函数是一阶惯性环节,干扰在此可忽略。
以某石油加工企业精馏塔精馏段温度控制系统为
,通过数据采集进行建模,得到主控广义对象传递函数为
,广义副对象传递函数为:
。
5仿真
建立了精馏塔的动态仿真数学模型;然后,将该模型应用于实际连续多相精馏塔,并编程进行了仿真,通过改变精馏塔迸料流量、进料组成、加热蒸汽量和回流比等操作变量对该塔进行扰动实验,得到一系列精馏塔组分浓度变化的过渡过程曲线,从而了解该塔的动态特性。
实验结果表明,该模型能够比较准确地预测精馏塔在各种干扰和操作条件下的动态行为,其稳态结果与实际情况基本一致。
因此,本模型对于精馏过程的控制系统分析和设计具有较高的实际应用价值和理论指导意义[22]。
根据经验试凑法初步假设副回路PID控制器的参数K=3,TI=0,TD=0,仿真得到曲线如图所示:
经反复试验,当取K=15,TI=0,TD=0,仿真得到曲线如图所示,曲线衰减效果良好,符合设计要求。
经反复主回路PID控制器K=10,TI=4,TD=1,仿真得到曲线如图所示:
6结束语
设计思想
研究精馏塔的精馏塔精馏原理,分析精馏段流程,选取出口流量作为被控对象选出被控对象,这些都是很容易从书本中找到根据,本课题研究的是精馏塔精馏段温度控制,所以把出口温度T作为被控变量;在选取温度作为被控变量后到操纵变量的选取,这一过程从分析被控对象的特性和结合精馏塔的流程图,塔出口流量和回流量都对被控对象影响很大,接着根据课题选取间接控制方案,排除塔出口流量作为操纵变量,最后选取回流量作为操纵变量,得出系统控制方框图;根据精馏塔物料平衡和能量平衡,求解被控对象模型;根据控制系统的实际情况结合仪表的参数选取仪表;分析被控对象的特性,查阅控制系统可能出现的问题选取控制算法,调节控制参数进行系统仿真,继而控制系统性能,此过程中也将工程参数进行了最优整定。
系统分析
该系统有效地解决了对象等效纯滞后时间很长的问题,能及时检测到系统中可能引起被控制量发生变化的许多因素并加以控制实践表明,串级控制技术是改善自动控制系统调节品质的有效方法之一,精馏塔精馏段温度控制问题是一个典型的时间大滞后问题,温度串级控制技术应用,有效地抑制惯性、迟延性的影响,并且鲁棒性强的特点,改善了控制系统的调节品质,该系统把主要的扰动包含在副控回路中,通过副控回路的调节作用,在扰动影响到主控回路被调参数之前,大大地削弱了扰动作用的影响,该系统还采用了一个测量中间变量,作为副控回路的被调参数,这种控制方法在热处理,化工,机械加工,金属冶炼等行业中也具有广泛的用途和推广价值。
在此次的课程设计中,通过对系统完整设计,使自己对以前所学习的理论知识有了更远的延伸,懂得一般控制系统的建立过程,在心中形成了完整的思路;通过查阅大量文献资料,在短时间内从中涉猎自己所想要的,提高自己的主动分析和自学能力,最后感谢刘广璞老师和王泽兵老师对我们的细心指导,正是有了他们的指导和教诲,使本次试验可以顺利的完成,为自己以后精彩的人生奠基了很好的基石。
7参考文献
[1]俞金寿等.北过程自动化及仪表[M].北京:
化学工业出版社,2006.
[2]谭天恩等.化工原理[M].北京:
化学工业出版社,2008,45~63.
[3]袁荣华.王毅.陈春刚神经网络技术在试验精馏塔控制中的应用[J],西安交通大学学报2002(9).
[4]王毅等.过程装备控制技术及应用[M].北京:
化学工业出版社,2010,13~16.
[5]孔祥波.精馏塔自动控制及应用[J].吉林广播电视大学学报,2010(8),87~88.
[6]吴兴纯.李江涛.微分先行计算机串级控制在精馏塔提馏段温控中的应用[J].昆明理大学学报(理工版),2005(4)
[7]张井岗等.过程控制与自动化仪表[M].北京:
北京大学出版社,2008,68~84。
[8]&mnid=87&classname=LJ
[11][12]刘兴高等.内部热耦合精馏塔数学模型及数值解法[J].浙江大学学报2001.
[13]KIMDH.Tuning“aPIDcontroueruBingimmunenet—workmodelandfuzzyset[Cl.IEEEIntemationalsymposiumonlndustrialElectIoni-cs.2001.12—16:
1656~1661.
[14]彭道刚等.基于灰色预测的汽温模糊免疫PID控制[J].动力工程,2007,27
(1):
72~75.
[15]周国雄,蒋辉平.基于分层结构模糊免疫PID的孵化过程控制[J].农业工程学报,2007。
23(12):
167~170.
[16]刘久斌,李德桃.电厂锅炉燃烧系统的模糊免疫PID控制[J].动力工程,2005,25(5):
673~675.
[17]王起林.化工精制工序中精馏塔建模与仿真的研究[D].浙江大学博士论文2003,36~42.
[18]范文雪.精馏塔动态数学模型的建立、仿真及控制的研究[D].北京化工大学硕士论文,2005,67~74.
[19]WoodRW,BerryMCompositionControlofaBinary
DistillationColumn[P].ChemicalEngineeringScience(S0009-2509),
1973,(28)1707~1717.
[20]周国雄等.精馏过程提馏段温度的前馈和免疫PID—P串级控制研究[J].电子技术应用,2010,36
(1).
[21]黄克谨等,精馏塔通用动态仿真软件及其在控制系统设计中的应用[J],系统仿真学报,1994,6(4):
49~56.