45#钢管断裂原因分析要点.docx
《45#钢管断裂原因分析要点.docx》由会员分享,可在线阅读,更多相关《45#钢管断裂原因分析要点.docx(13页珍藏版)》请在冰豆网上搜索。
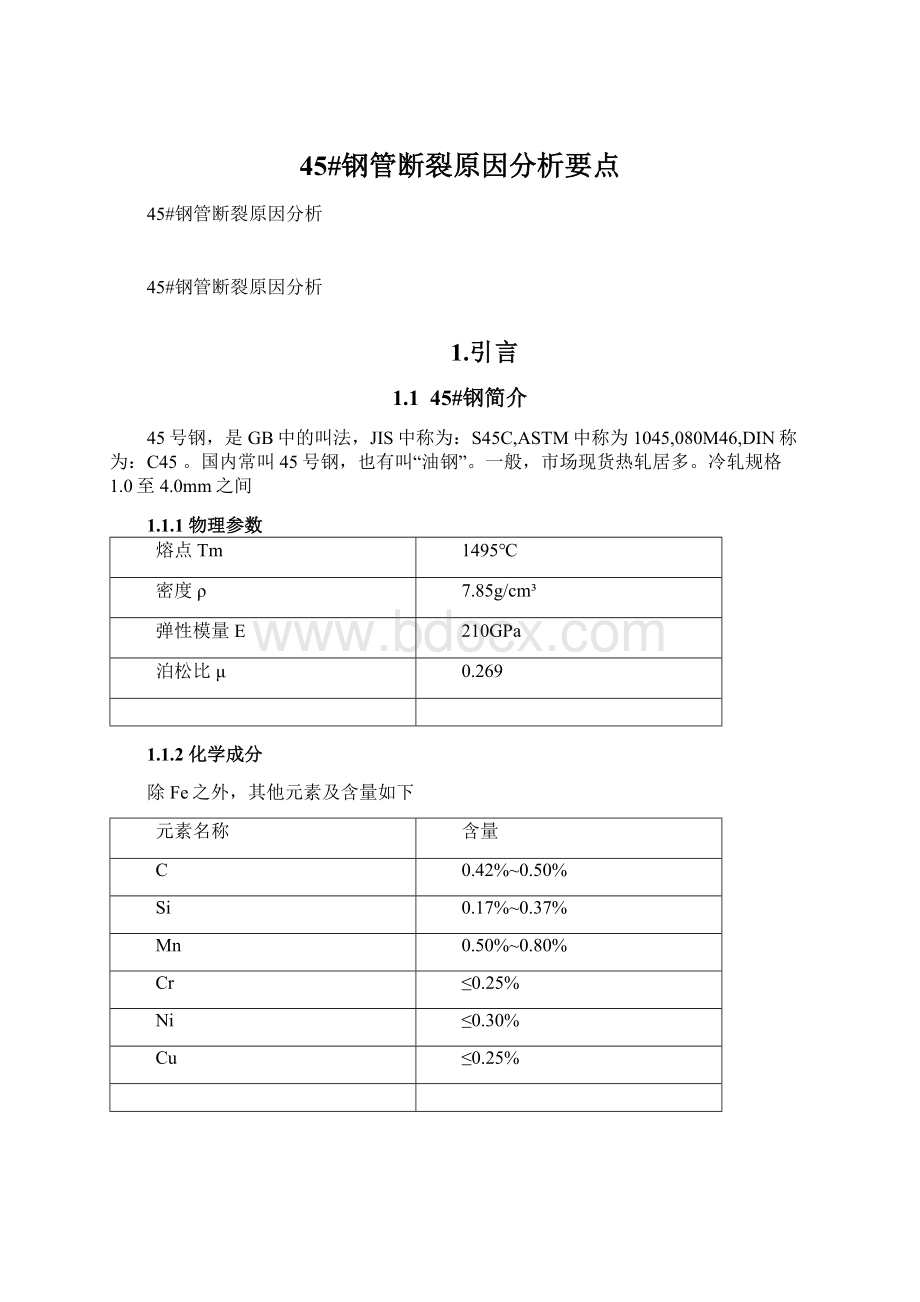
45#钢管断裂原因分析要点
45#钢管断裂原因分析
45#钢管断裂原因分析
1.引言
1.145#钢简介
45号钢,是GB中的叫法,JIS中称为:
S45C,ASTM中称为1045,080M46,DIN称为:
C45 。
国内常叫45号钢,也有叫“油钢”。
一般,市场现货热轧居多。
冷轧规格1.0至4.0mm之间
1.1.1物理参数
熔点Tm
1495℃
密度ρ
7.85g/cm³
弹性模量E
210GPa
泊松比μ
0.269
1.1.2化学成分
除Fe之外,其他元素及含量如下
元素名称
含量
C
0.42%~0.50%
Si
0.17%~0.37%
Mn
0.50%~0.80%
Cr
≤0.25%
Ni
≤0.30%
Cu
≤0.25%
1.1.4钢的热处理简介
45#钢为优质碳素结构钢,含C量为0.45%,属中碳钢,其优点是硬度不高但易于切削加工,缺点是淬火性能不好,所以如果需要表面硬度较高,又希望发挥45#刚优越的机械性能,常将45#钢作调质(先850℃正火,再840℃淬火加600℃回火处理)加表面淬火(加热温度视情况而定,约860℃左右进行淬火)处理,而不是渗碳加淬火,这样虽然前者获得的表面耐磨性比后者稍低,但保证了其芯部耐冲击的性能。
正火,又称常化,是将工件加热至Ac3(Ac3是指加热时自由铁素体全部转变为奥氏体的终了温度,一般是从727℃到912℃之间)或Acme(Acme是实际加热中过共析钢完全奥氏体化的临界温度线)以上30~50℃,保温一段时间后,从炉中取出在空气中或喷水、喷雾或吹风冷却的金属热处理工艺。
其目的是在于使晶粒细化和碳化物分布均匀化。
正火与退火的不同点是正火冷却速度比退火冷却速度稍快,因而正火组织要比退火组织更细一些,其机械性能也有所提高。
另外,正火炉外冷却不占用设备,生产率较高,因此生产中尽可能采用正火来代替退火。
对于形状复杂的重要锻件,在正火后还需进行高温回火(550-650℃)高温回火的目的在于消除正火冷却时产生的应力,提高韧性和塑性。
钢的热处理种类分为整体热处理和表面热处理两大类。
常用的整体热处理有退火,正火、淬火和回火;表面热处理可分为表面淬火与化学热处理两类。
正火是将钢件加热到临界温度以上30-50℃,保温适当时间后,在静止的空气中冷却的热处理工艺称为正火。
正火的主要目的是细化组织,改善钢的性能,获得接近平衡状态的组织。
正火与退火工艺相比,其主要区别是正火的冷却速度稍快,所以正火热处理的生产周期短。
故退火与正火同样能达到零件性能要求时,尽可能选用正火。
大部分中、低碳钢的坯料一般都采用正火热处理。
一般合金钢坯料常采用退火,若用正火,由于冷却速度较快,使其正火后硬度较高,不利于切削加工。
45#钢为优质碳素结构钢,含C量为0.45%,属中碳钢,其优点是硬度不高但易于切削加工,缺点是淬火性能不好,所以如果需要表面硬度较高,又希望发挥45#刚优越的机械性能,常将45#钢作调质(先850℃正火,再840℃淬火加600℃回火处理)加表面淬火(加热温度视情况而定,约860℃左右进行淬火)处理,而不是渗碳加淬火,这样虽然前者获得的表面耐磨性比后者稍低,但保证了其芯部耐冲击的性能
1.1.5热处理后力学性能标准
抗拉强度σb
600MPa
屈服强度σs
355WPa
伸长率δ
16%
断面收缩率ψ
40%
冲击功Ak
39J
1.2钢管主要生产工艺
无缝钢管的生产方法,大致分为斜轧法(孟内斯曼法)和挤压法。
斜轧法(孟内斯曼法)是先用斜轧辊将管坏穿孔,然后用轧机将其延伸。
这种方法生产速度快,但对管坯的可加工性要求较高,主要适用于生产碳素钢和低合金钢管。
挤压法则是用穿孔机将管坯或钢锭穿孔,再用挤压机挤压成钢管,这种方法比斜轧法效率低,适用于生产高强度合金钢管。
斜轧法和挤压法都必须先将管坯或钢锭加热,生产的钢管称为热轧管。
用热加工法生产的钢管有时候可根据需要再进行冷加工。
冷加工有两种方法:
一种是冷拔法,就是将钢管通过拔管模拉拔,使钢管逐渐变细、伸长;另一种方法是冷轧法,它是将孟内斯曼兄弟发明的热轧机应用于冷加工中的方法。
无缝钢管的冷加工,可以进步钢管的尺寸精度和加工光洁度,改善材质的机械性能等。
无缝化钢管(热轧钢管)的生产工艺
钢管的无缝化主要是通过张力减径来完成的,张力减径过程是空心母材不带芯棒的连续轧制过程。
在保证母管焊接质量的条件下,焊管张力减径工艺是将焊管整体加热到950摄氏度以上,再经张力减径机(张力减径机共有24道次)轧制成各种外径与壁厚的成品管,采用此工艺所生产的热轧钢管与普通的高频焊管有本质的区别通过加热炉加热后其焊缝与母体的金相组织和机械性能可以达到完全一致此外,通过多道次的张力减径机轧制和自动控制使得钢管的尺寸精度(尤其是管体圆度和壁厚精度)优于同类无缝管。
世界发达国家生产的流体管,锅炉管中已大量采用焊管无缝化工艺,随着社会的发展,国内热轧焊管逐步代替无缝管的局面已经形成
1.3材料的断裂失效
1.3.1断裂简介
固体材料在力的作用下分成若干部分的现象称为断裂。
材料的断裂是力对材料作用的最终结果,它意味着材料的彻底失效。
研究材料断裂的宏观与微观特征、断裂机理、断裂的力学条件,以及影响材料断裂的各种因素不仅具有重要的科学意义,而且也有很大的使用价值。
1.3.2断裂的类型及断口特征
材料的断裂过程大都包括裂纹的形成与拓展两个阶段。
由于材料品类的不同,及引起断裂的条件各异,材料断裂的机理与特征也并不相同,若按照断裂前与断裂过程中材料的宏观塑性变形的程度,可以把断裂分为脆性断裂与韧性断裂;按照晶体材料断裂和裂纹拓展的途径,分为穿晶断裂和沿晶断裂;按照微观断裂机理,分为解理断裂和剪切断裂;按照作用力的性质还可分为正断和切断等。
材料的断裂表面成为断口,用肉眼、放大镜或电子显微镜等手段对材料断口进行宏观及微观的观察分析,以了解材料发生断裂的原因、条件、断裂机理以及与断裂有关的各种信息的方法,称为断口分析法。
1.3.3韧性断裂与脆性断裂
韧性断裂是材料断裂前及断裂过程中产生明显宏观塑性变形的断裂过程。
韧性断裂时一般裂纹拓展过程较慢,而且要消耗大量塑性变形能。
断口用肉眼或放大镜观察时,往往呈暗灰色,纤维状。
纤维状是塑性变形过程中,众多微细裂纹的不断拓展和相互连接造成的,而暗灰色则是纤维断口表面对光的反射能力很弱所致。
其形貌如图1。
脆性断裂是材料断裂前基本上不产生明显的宏观塑性变形,表现为快速断裂过程。
其断口一般与正应力垂直,宏观上比较齐平光亮,常呈放射状或结晶状。
其形貌如图2。
图1图2
图3图4
1.3.4穿晶(晶界)断裂与沿晶断裂
对于晶体材料,发生断裂时裂纹拓展的路径分为穿晶和沿晶多数为脆性断裂。
1.3.5剪切断裂和解理断裂
剪切断裂与解理断裂是两种不同的微观断裂方式,是材料断裂的两种重要微观机理。
剪切断裂。
剪切断裂是材料在切应力作用下沿滑移面滑移分离而造成的断裂。
某些纯金属尤其是单晶体金属可产生纯剪切断裂,其断口呈锋利的楔形;大单晶体的纯剪切断口上,用肉眼就可观察到很多直线状的滑移痕迹。
对于多晶体,由于晶粒间的相互约束,位错沿着相互交叉的滑移面移动,从而在微观断口上呈现出“蛇形滑动”花样。
随变形度的加剧,蛇形滑动花样平滑化,形成“涟波”花样,变形再继续增加,涟波花样进一步平滑化,而在断口上留下无特征的平坦面,称为“延伸区”。
剪切断裂的另一种形式为微孔聚集型断裂。
其断口在宏观上常呈现暗灰色、纤维状,微观断口特征花样则是端口分布大量“韧窝”。
微孔聚集断裂过程包括微孔形核、长大、聚合直至断裂。
一般来说,其实微孔的尺寸主要取决于杂质物或第二项质点的大小和他们间的距离,以及金属材料本身塑性的好坏。
若塑形相同,质点间距减小,则韧窝尺寸和深度都减小。
在相同质点间距下,塑性好的材料韧窝深。
在三向应力作用下,韧窝呈等轴状,而在切应力作用下,常呈椭圆形或抛物线形。
韧窝形貌见图3。
解理断裂。
在正应力作用下,由于原子间结合力破坏引起的沿特定晶面发生的脆性穿晶断裂称为解理断裂。
实际解理断口是由许多大致相当于晶粒大小的解理面集合而成的。
这种大致以晶粒大小为单位的解理面称为解理刻面。
解理裂纹的拓展往往是沿着晶面指数相同的一族相互平行,但位于“不同高度”的晶面进行的。
不同高度的解理面之间存在台阶,众多台阶的汇合便形成河流花样。
解理台阶、河流花样和舌状花样是解理断口的基本微观特征。
如图4.
2.实验内容
分析钢管断裂的原因,首先要通过观察断裂面的微观形貌特征来判定断裂的种类,再从钢管组织入手,观察组织形貌,即45#钢中铁素体及渗碳体组织多少及分布,找到断裂原因。
再辅以硬度检测,以证明断裂分析结论的准确性。
2.1试验样品及仪器
2.1.1试验样品
45#钢管断裂试样
2.1.2试剂及药品
实验所用的试剂原料如下表所示。
表2.1实验中使用的试剂
Table2.1Thereagentusedinexperiment
试剂名称
厂家
金属切削液
天津籣娅懿科技发展有限公司
无水乙醇
莱阳经济技术开发区精细化工
硝酸
莱阳经济技术开发区精细化工
三氧化二铬
天津市大茂化学试剂厂
线切割专用钼丝
自贡硬质合金有限责任公司成都分公司
金相砂纸
上海砂轮厂
2.1.3实验仪器
表2.2实验中使用的仪器设备
仪器名称
厂家
DK7725电火花线切割机
苏州普光机电有限公司
电火花线切割机控制机
苏州普光机电有限公司
JSM-6380LV扫描电子显微镜
日本电子
PG-1金相试样抛光机
上海金相机械设备有限公司
MDJ系列金相显微镜
重庆奥特光学仪器有限责任公司
AxioScopeA1pol偏光显微镜
北京普瑞塞斯仪器有限公司
MHV2000型数显显微硬度计
上海材料试验机厂
KQ2200B型超声波清洗器
昆山市超声仪器有限公司
2.2实验过程
2.2.1金相及硬度检测
2.2.1.1金相试样的线切割制备
先将断裂钢管加持在DK7725电火花线切割机上,再输入操作程序,紧丝,对边并定中心,然后运行线切割机,得到粗加工的待测试样。
如图
图5
2.2.1.2金相试样的粗磨及抛光
将切割好的试样,选取垂直于钢管断裂面的一侧表面依次用800目、1200目、2000目的砂纸打磨,至表面光滑,再在PG-1金相试样抛光机上抛光,至表面光亮若镜面,在偏光显微镜下观察,没有划痕。
图7为所制样品。
图7图8
2.2.1.3腐蚀
取无水乙醇5ml,浓硝酸95毫升,混合,至均匀,配制体积分数为5%硝酸酒精溶液。
取0.5ml滴在金相试样表面,置通风处,至表面干燥。
2.2.1.4金相检测
将腐蚀后的样品置于MDJ系列金相显微镜上,从边缘向内部观察组织形貌,先使用×50镜头整体观察,再使用×100及×200镜头细微观察,并拍摄金相组织照片以供分析。
2.2.1.5硬度检测
将试样加载在MHV2000型数显显微硬度计载物台上,设置加载力为4.9N,加载时间10秒,从裂纹边缘向试样内部依次测试硬度。
约每0.1mm间距取一测试点,共10取样点。
2.2.2断裂试样的扫描检测
2.2.2.1断面预处理
将试样在超声仪中超声处理30分钟,以清洗断裂截面,为做显微扫描做准备。
清洗后断裂面如图8
2.2.2.2试样断口扫描
将超声清洗后的样品,使用JSM-6380LV扫描电子显微镜,扫描观察表面形貌。
扫描时,一次使用×23,×100,×500的扫描镜头,并拍摄扫描照片以供分析。
3实验结果分析与讨论
3.1断口形貌分析
肉眼观察断口形貌,可发现图8中左下角处的裂纹源。
样品的断口裂纹源处存在明显的纤维区和放射区,而由于钢管试样较大,剪切唇并不明显,所以钢管的断裂属于微孔聚集型剪切断裂
图9
(1)图9
(2)
图9(3)
微孔聚集型断裂是材料韧性断裂的普通方式。
钢管端口在宏观上常呈现暗灰色,纤维状,微观断口特征则是端口上分布的大量“韧窝”如图9
(1),图9
(2)所示。
微孔聚集型断裂包括微孔形核,长大,聚合至断裂。
微孔的形核是通过第二相碎裂或与基体界面脱离,如图9(3)所示,并在材料塑性变形到一定程度时产生的。
随塑性变形的的进一步发展,大量位错进入微孔,使微孔逐渐长大。
微孔长大的同时,与相邻微孔的基体横截面不断减小,最终微孔连接聚合形成微裂纹。
随后在裂纹尖端附近存在三向压应力区和集中塑性变形区,在该区形成新的微孔。
新的微孔借助內缩颈与裂纹连通,是裂纹向前推进一步,如此不断进行下去,直至最终断裂,便形成通常见到的宏观上呈纤维状,微观上为韧窝的纤维区。
纤维区中裂纹拓展速度较慢,并伴随有更大的塑性变形。
当裂纹达到某一临界尺寸后,产生更大的应力集中,裂纹以低能量撕裂的方式快速拓展,并形成放射区。
放射区有放射线花样特征。
放射线平行于裂纹拓展方向而垂直于裂纹前端轮廓线,并逆指裂纹源。
放射区的断裂过程虽然与纤维区不同,但仍属于韧性撕裂过程。
3.2金相组织分析
该钢管的金相组织如图
图10
(1)图10
(2)
图10(3)图10(4)
在金相图片中可明显观察到白色羽毛状的铁素体魏氏组织和灰色块状珠光体组织。
该钢管的生产原料为45#钢锭,生产工艺为将钢锭加热到1000℃左右,保温奥氏体化,在冲击成形,然后正火轧制而成。
45#钢属亚共析钢,奥氏体化后正火处理,得到铁素体和珠光体组织,而正火工艺的冷却速度较快,奥氏体发生亚共析转变,使得先析出相铁素体不仅含量降低,而且形态也会发生变化。
通常在正火处理时,加热温度过高,保温时间过长及炉内温度不均匀等都可以造成局部过热,即生成粗大的奥氏体晶粒,若冷却速度快,铁素体析出时便呈片状或针状的魏氏组织,如图10
(1),图10
(2)。
魏氏组织会造成局部应力集中,使钢的塑性降低,性能恶化。
在该批钢管的生产中,奥氏体化温度高于1000℃,而45#钢的正火温度一般设定在840到870℃,谷此批钢管的正火温度是稍高的。
正火温度高,造成了两个效应,即奥氏体晶粒粗大和冷却速度快,这两个因素均对魏氏组织的形成起到促进作用。
由于先共析铁素体沿奥氏体晶界析出,所以在金相组织照片中可依旧可以看到原奥氏体晶粒轮廓,其晶粒大小在200μm左右,图10(3),图10(4)。
考虑到钢管的生产时间在冬季,较高的正火温度和较低的环境温度,使得正火过程中温度降低速度较快。
结合对断口形貌的分析,可知正火过程产生的魏氏体便是引起应力集中的第二相,轧制时引发了钢管的断裂。
3.3硬度分析
硬度是表征材料软硬程度的力学性能指标,一般认为是指材料表面上不大体积内抵抗变形或开裂的能力。
显微硬度属于压入法硬度测试,压入法的硬度值是材料表面抵抗另一物质局部压入时所引起的塑性变形能力。
压入法硬度试验的应力状态最“软”,最大切应力远大于最大正应力,所以在此应力下几乎所有材料都会产生塑性变形。
压入法所测数值与材料静强度和疲劳强度都有比较好的对应关系,由于硬度与强度之间存在非常好的对应关系,在实践中,硬度几乎成了强度的代名词。
硬度试验数据如下表所示
表2.3断裂面附近显微硬度硬度值
d/mm
0.1
0.2
0.3
0.4
0.5
0.6
0.7
0.8
0.9
1.0
HV
127
144
134
161
146
157
145
155
152
163
断裂面附近硬度变化曲线图
由硬度实验数据可知,测试点硬度值随与断裂面之间的距离增大而增大。
对于亚共析钢,其软相组织为铁素体,故硬度试验表明靠近断裂面处析出铁素体的量比其他区域要高。
如前所分析,钢管在正火过程中生成魏氏组织是造成断裂的原因,这与硬度试验结果是一致的。
结论
试验通过对45#钢管断裂面的扫描分析及断裂面附近的金相分析和硬度分析,得到如下结论;
45#钢锭在进行奥氏体化预处理时,加热温度较高,导致奥氏体晶粒粗大。
后续正火工艺,由于初始温度(即奥氏体化温度)较高,冷却速度稍快,致使先析出相铁素体形成魏氏组织。
魏氏组织严重恶化钢的性能,使钢的强度、塑性和冲击韧性显著降低,容易发生断裂,。
魏氏组织在钢管中造成应力集中,在轧制时先是产生显微裂纹,随后裂纹不断扩大,并发生剪切断裂。
钢中的魏氏组织一般可通过细化晶粒的正火、退火以及锻造等方法加以消除,程度严重的可采用二次正火加以消除。