玩具模具设计.docx
《玩具模具设计.docx》由会员分享,可在线阅读,更多相关《玩具模具设计.docx(15页珍藏版)》请在冰豆网上搜索。
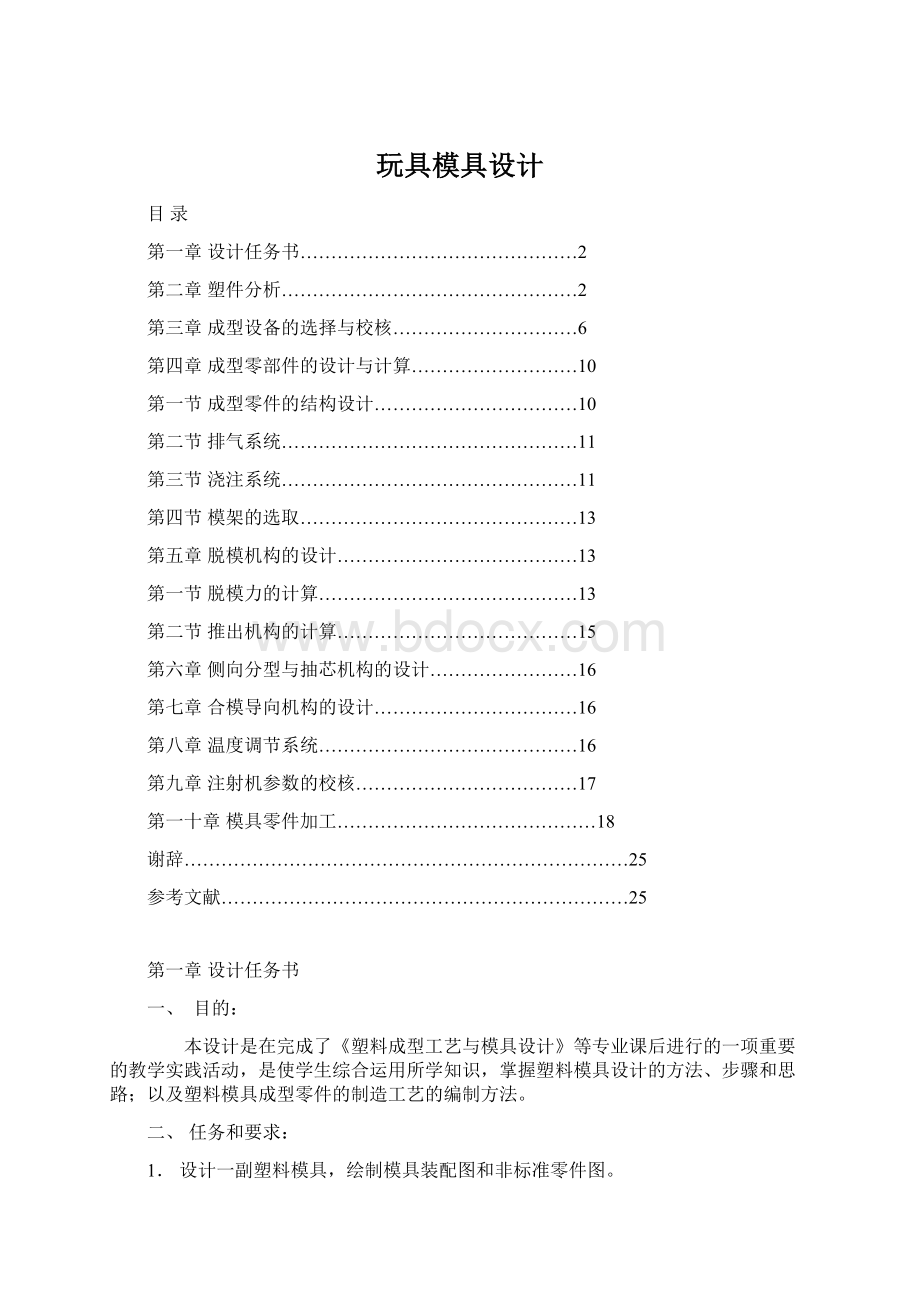
玩具模具设计
目录
第一章设计任务书………………………………………2
第二章塑件分析…………………………………………2
第三章成型设备的选择与校核…………………………6
第四章成型零部件的设计与计算………………………10
第一节成型零件的结构设计……………………………10
第二节排气系统…………………………………………11
第三节浇注系统…………………………………………11
第四节模架的选取………………………………………13
第五章脱模机构的设计…………………………………13
第一节脱模力的计算……………………………………13
第二节推出机构的计算…………………………………15
第六章侧向分型与抽芯机构的设计……………………16
第七章合模导向机构的设计……………………………16
第八章温度调节系统……………………………………16
第九章注射机参数的校核………………………………17
第一十章模具零件加工……………………………………18
谢辞………………………………………………………………25
参考文献…………………………………………………………25
第一章设计任务书
一、目的:
本设计是在完成了《塑料成型工艺与模具设计》等专业课后进行的一项重要的教学实践活动,是使学生综合运用所学知识,掌握塑料模具设计的方法、步骤和思路;以及塑料模具成型零件的制造工艺的编制方法。
二、任务和要求:
1.设计一副塑料模具,绘制模具装配图和非标准零件图。
2.说明书。
内容包括:
1)产品零件的成型工艺分析和结构分析。
2)必要的计算过程。
3)模具结构的选择分析。
4)模具工作原理(动作)分析;零件制造工艺选择分析(内容包括:
成本经济性、加工精度、加工质量、加工效率等)。
第二章塑件分析
一:
材料的选择
该塑件为玩具。
根据参考资料2《塑料成型工艺与模具设计》,选择其材料为丙烯腈——丁二烯——苯乙共聚物(ABS)工程材料,ABS的介绍如下:
⒈基本特性:
ABS是由丙烯腈、丁二烯、苯乙烯共聚而成的。
这三种组分的各自特性,使ABS具有良好的综合力学性能。
丙烯腈使ABS有良好的耐化学腐蚀性及表面硬度,丁二烯使ABS坚韧,苯乙烯使它有良好的加工性和染色性能。
ABS无毒、无味,呈微黄色,成形的塑料件有较好的光泽。
密度为1.02~1.05g/cm³。
ABS有极好的抗冲压强度,且在低温下也不迅速下降。
有良好的机械强度和一定的耐磨性、耐油性、耐水性、化学稳定性和电气性能。
ABS有一定的硬度和尺寸稳定性,易于成型加工。
经过调色可配成任何颜色。
其缺点是耐热性不高,连续工作温度为70°C左右,热变形温度为93°C左右。
耐气候性差,在紫外线作用下变硬变脆。
2.主要用途:
ABS广泛用于水表壳、纺织器材、电器零件、文教体育用品、玩具等。
3.成型特点:
ABS在升温时粘度增高,所以成型压力比较高,塑料上的脱模斜度宜稍大,ABS易吸水,成型加工前应进行干燥处理;易产生熔接痕,模具设计时应注意尽量减少浇口对流道的阻力;在正常的成型条件下,壁厚、熔料温度及收缩率影响极小。
要求塑件精度高时,模具温度可控制在50~60°C,要求塑件光泽和耐用时,应控制在60~80°C
ABS的注射工艺参数
注射类型
螺杆式
螺杆转速(r/min)
30~60
喷嘴形式
直通式
温度(℃)
190~200
料筒温度
前段(℃)
200~210
中段 (℃)
210~230
后段 (℃)
180~200
模具温度(℃)
50~80
注射压力(MPa)
70~120
保压力(MPa)
50~70
注射时间(S)
3~5
保压时间(S)
15~30
冷却时间(S)
15~30
成型周期(S)
40~70
二:
塑件结构分析
结构特点:
该塑件最大壁厚大概是3mm厚的壳体,壳体外部没有很高的要求,,所以可以采用点浇口的形式。
由于该塑件较小,采用一模多腔比较合适。
壳体内部结构较复杂,所以采用镶嵌式凸凹模结构。
改塑件分为上下两壳,如图1、图2和图3所示:
图1塑件后盖图
图2塑件前盖图
图3塑件前盖图
第三章设备的选择与校核
为了保证注射质量和充分发挥设备的能力,应根据注射模一次成型的塑料体积和质量来初步确定注射机的类型。
根据理论和在实际生产中的经验得出塑件和浇注道之间材料的总和应该在注射机理论注射量的50%~80%之间。
(一)、型腔数量的确定
要点:
既要保证最佳的生产经济性,技术上又要充分保证产品的质量,也就是应保证塑料件最佳的技术经济性。
⑴塑料制作的批量和交货周期方面:
该塑件是大批量生产的产品,交货周期要短,使用多型腔模具可提供独特的优越条件。
⑵质量控制要求方面:
该塑件不属于高精度生产要求的产品,精度要求不高采用多型腔有较高的生产效率。
⑶塑料品种和其他方面:
该塑件所用塑料为ABS工程塑料,流动性能好;浇口位置在靠近塑件边缘上,另外塑料尺寸小,形状简单。
经过以上分析和本人经验所得,总结出:
采用一模四腔是最佳形式,具有最佳的经济性。
(二)型腔的布局
要点:
型腔的排布与浇注系统布置密切相关,型腔排布应使每个型腔都通过浇注系统从总压力中均等地分得所需的足够压力,以保证塑料熔体同时均匀地充满每个型腔,使各型腔的塑件内在质量均一稳定。
这就要求型腔与主流道之间的距离尽可能最短,尽可能地采用平衡的流道和合理的浇口尺寸以及均匀的冷却等。
经分析本人确定的型腔布局为平衡式型腔布局如图4所示:
图4型腔布局图
(三)选用注塑机
1.锁模力 注射成型时,塑件在模具分型面上的投影面积是影响锁模力的主要因素,其数值越大,需要的锁模力与塑件在水平分型面上的投影面积有关,为了可靠地锁模,不使成型过程中出现溢料现象,应使塑料熔体对形腔的成型压力与塑件和浇注系统在分型面上的投影面积之和的乘积小于注射机额定锁模力,即:
F>(nA1+A2)P=1014.4×90×80%=7.30kN
式中:
F-注射机的额定锁模力(N)
P-塑件熔体对形腔的成型压力(MPa)其大小一般是注射压力的80%。
ABS的注射压力取90MPa。
2.注射量 模具型腔能否充满与注射机允许的最大注射量密切相关,设计模具时,应保证注射模内所需熔体总量在注射机实际的最大注射量的范围内,根据生产经验,注射机最大注射量是其允许最大注射量(额定注射量)的80%,由此有:
m≥(nm1+m2)/80%=75/80%=93.75g
式中:
m-注射机允许的最大注射量(g)
3.开模行程 S(合模行程)指模具开合过程中动模固定板的移动距离,它的大小直接影响模具所能成型的塑件高度,注射机最大开模行程Smax应大于开模行程S:
Smax≥S=H1+H2+5~10=12+23+10=45mm
式中:
H1-推出距离(脱模距离)(mm)
H2-包浇注系统凝料在内的塑件高度(mm)
根据以上计算和所用塑料的有关数据,选用注射机为:
注射机的参数
合模力(KN)
500
注射压力(MPa)
122
额定注射量(cm³)
60
最大开(合)模行程(mm)
180
拉杆空间(mm)
190*300
注射行程(mm)
170
模具厚度(mm)
最大
200
最小
70
喷嘴球面半径(mm)
12
喷嘴直径(mm)
2
(四)分型面
要点:
1、分型面选在塑件最大轮廓处;2、要便于塑件顺利脱模;3、满足塑件外观质量要求;4、便于模具加工制造。
分析:
塑料件表面有外观质量要求,不允许留下痕迹,而且有较大的拔模角,分型面设在塑件中部不能顺利脱模。
塑件开模后要留在动模上侧,以便于顶出脱模如果设计在塑件边缘上,则采用平直分型面,分型面设计如图5所示:
图(5)分型面形式
这种设计虽然不够曲面分型面的排气效果好,但模具加工制造要简易得多,加式费用也可节省很多,总之是利大于弊了。
第四章成型零部件的设计与计算
模具中决定塑件几何形状和尺寸的零件即成型零件设计,包括凹模、型芯、镶块、凸模和成型杆等。
第一节成型零件的结构设计
一、凹模的设计:
凹模是成型塑件外表面的主要零件,按其结构不同,可分为
整体式和组合式两类。
该塑件底面较复杂,但是为了使产品的美观,决定采用整体式凹模。
即塑件中所有凹入的地方都做成一个整体。
二、凸模和型芯的设计:
凸模和型芯是成型塑件内表面的零件。
⒈凸模的结构
分析该塑件,结构比较复杂,且位置关系有一定的要求,为了保证位置关系以及尺寸,将凸模设计为整体式。
第二节排气系统
利用型芯与模板的配合间隙排气,间隙控制在0.03~0.05mm之间。
第三节浇注系统
1、主流道和浇口套的设计
为了便于凝料从主流道中拔出,主流道设计成圆锥形,内壁必须光滑,表面粗糙度应为Ra0.4。
由于主流道要与高温塑料及喷嘴接触和碰撞,所有模具的主流道部分通常设计成可拆卸更换的主流道衬套,简称浇口套,以便选用优质钢材(如T8A等)单独加工和热处理(硬度为HRC53~57)。
由于在浇口套的小端设计有分流道,必须要止转,所有浇口套设计成整体嵌入式,大端用螺丝坚固在定模固定板上。
如图6所示:
图6主流道形式
d=注射机喷嘴直径+1=3mm
SR=喷嘴球面半径+2=14mm
h球面配合高度=5mm
D取6mm
2、分流道的设计
选用圆形截面的流道,虽工艺性不佳,但流动性,传热性等方面都好,流道也尽量做到最短,以减少热量和压力的损失。
所以设计如图7所示:
图7分流道形式图
3、浇口的设计:
产品表面不允许有浇口痕迹,所以浇口位置设在塑件里面,就必须采用潜伏式浇口,另外考虑到流动性和脱模等方面,所以设计成如图8所示:
图8浇口设计图
4、冷料穴的设计
冷料穴设计在流道较角处,为了方便把流道取出,使其保留在动模一侧,便于脱模,冷料穴也可作为拉料的作用。
第四节模架的选取
模架的选取应综合考虑型腔的大小与布置、凸凹模结构形式、推出机构、合模导向机构等方面。
根据成型零件的计算和,还有注射机的参数,尽量选取标准模架.
第五章脱模机构的设计
第一节脱模力的计算
注射成型后,塑件在模具内冷却定型,由于体积的收缩,对型芯产生包紧力,塑件要从模腔中脱出,就必须克服因包紧力而产生的摩擦阻力。
一般而论,塑料制件刚开始脱模时,所需克服的阻力最大,所以选择此时作为临界条件。
塑件脱模时的型芯的受力分析如图9所示:
图9型芯受力分析图
根据力平衡原理,列出平衡式:
则:
式中
——塑件对型芯的包紧力;
——脱模时型芯所受的摩擦阻力;
——脱模力;
——型芯的脱模斜度。
又
于是
而包紧力为包容型芯的面积于单位上包紧力之积,即:
由此可得:
式中
——塑料对钢的摩擦系数,约为0.1~0.3;
——塑件包容型芯的面积;
——塑件对型芯的单位面积上的包紧力,一般情况下模外冷却的塑件
约取2.4~3.9×107Pa;模内冷却的塑件约取0.8~1.2×107Pa。
第二节推出机构的设计
一、推出机构的选择:
选择推杆推出机构
推杆推出是一种最简单常用的推出形式。
推出元件制造简便,更换容易,滑动阻力小,推出效果好。
根据塑件的分析和推杆的设计要点,选择圆形推杆推出机构,其尺寸为Φ4mm
技术要求:
1、材料T10碳素工具钢
2、热处理要求HRC≧50
3、工作配合部分表面粗糙度Ra≤0.8µm
二、推出机构的导向与复位
为了保证推出机构在工作过程中灵活、平稳,每次合模后推出
机构能回到原来的位置,需要设计推出机构的导向与复位装置。
一)、导向零件
推出机构的导向零件,通常由推出导柱与推板导套
所组成,其导向装置见装配图。
二)、复位零件
用复位杆复位,采用圆形截面,设置四根复位杆,位置设在
推杆固定板的四周,以便推出机构合模时复位平稳,复位杆端面
与所在的动模平齐。
第六章侧向分型与抽芯机构的设计
该塑件由于挂钩的地方跟分型面是平行的,所以要设计出抽芯机构,具体结构见非标准零件图。
第七章合模导向机构设计
本设计采用导柱导向定位。
导柱导向机构的主要零件是导柱和导套。
一、导柱
导柱的结构形式可采用带头导柱和有肩导柱,导柱导面部分长度比凸模端面高出8~12㎜,以避免出现导柱未导正方向而型芯先进入型腔。
导柱材料采用T10,HRC50~55,导柱固定部分表面粗糙度Ra为0.8μm,导向部分Ra为0.8~0.4μm,本设计采用四根导柱,固定端与模板间采用H7/m6过渡配合,导向部分采用H7/f7间隙配合。
二、导套
导套常采用带头导套的形式,采用H7/m6配合镶入模板。
具体结构尺寸见装配图。
第八章温度调节系统
为了使模温控制在一理想的范围内,现设计一模具温度调节系统。
由于本次设计的塑料ABS黏度和流动性一般,模温为50~80℃,故无须设计加热系统,只需设计冷却系统以确保合理的模温。
常用的冷却方法有水冷却、空气冷却和油冷却,本设计设计采用的是水冷却,经济实惠。
冷却系统机构的确定:
对于不同的塑件,冷却水道的位置形状也不一样。
具体结构见装配图。
第九章注射机参数的校核
一、模具与注射机安装模具部分相关尺寸的校核
1、喷嘴尺寸
XS-Z-60型注射机的喷嘴球面半径为12mm,而本次设计的模具主流道始端凹下的球面半径为13mm,与之相适应,故满足要求。
2、模具厚度
模具厚度H必须满足:
Hmin﹤H﹤Hmax
式中:
Hmin-注射机允许的最小模具厚度;即动、定模板之间的最小开距;模具外形尺寸。
本设计的模具外形尺寸为300mm*300mm,XS-Z-60型注射机模板尺寸为330mm*440mm,在其范围内,故满足要求。
二、行程的校核
开模行程S(合模行程)指模具开合过程中动模固定板的移动距离。
它的大小直接影响模具所成型的塑件高度。
注射机XS-Z-60的最大开模行程Smax与模具无关,它的开模距离由连杆机构的冲程或其它机构的冲程所决定的,不受模具厚度的影响,由于此模具是双分型面注射模。
由〈参1〉公式(4-9)得
Smax≥S=H1+H2+a+5~10
S—开模行程
H1—推出距离(mm)
H2—包括浇注系统凝料在内的塑件高度(mm)
a—取出浇注系统凝料必须的长度(mm)
Hmax—注射机允许的最大模具厚度;
XS-Z-60型注射机模具最小厚度为70mm,最大模具厚度为200mm,本次设计的模具厚度为﹤200mm,故模具厚度满足要求。
初步估算Smax≥S满足要求。
三、顶出装置的校核
XS-Z-60型号的注射机的顶出装置为两中心顶杆机械顶出,此模具的顶出机构也采用中心顶杆机械顶出,故相适应。
第十章模具零件加工
(一)塑料模具制造技术要求
模具精度是影响塑料成型件精度的重要因素之一,为了保证模具精度,制造时应达到以下技术要求:
a、组成塑料模具的所有零件,在材料加工精度和热处理质量等方面均应符合相应图样的要求。
b、组成模架的零件应达到规定的加工要求,装配成套的模架应活动自如,并达到规定的平行度和垂直度要求
c、模具的功能必须达到设计要求
d、为了鉴别塑料成型件的质量,装配好的模具必须在生产条件下试模,并根据试模存在问题进行修整,直至试出合格的成型件为止。
一、加工要求:
1)模具分型面及组合件的结合面应很好贴合,局部间隙不大于0.02mm
2)模具成型表面的内外锐角、尖边、图样上未注明圆角时允许不大于0.3mm圆角(分型面及结合面除外)。
当不允许有圆角时。
应在图样上注明。
3)图样中未注明公差的一般尺寸其极限偏差按GB1804,其孔按H13,轴按h13,长度按J14。
4)模具中各承压板(模板)的两承压面的平行度公差按GB1184附录一的5级。
5)导柱、导套孔对模板平面的垂直度公差按GB1184附录一的4级。
导柱、导套之间的配合按H8/f8。
6)模具中安装镙钉(镙栓)之螺纹孔及其通孔的位置公差不大于2mm,或相应各孔配作。
7)导柱(直导柱、台肩导柱)其配合部位的大径与小径的同轴度公差t按GB1184附录一的5级。
8)导套(直导套、带头导套)外圆与内孔的同轴度公差t按GB1184附录一的5级。
9)主流道衬套的中心锥孔应研磨抛光,不得有影响脱浇口的各种缺陷。
二、装配要求:
1)顶出制品的推杆的端面与所在的相应型面保持齐平,允许推杆端面高出型面不大于0.1mm。
2)注射模的复位杆,其端面应与模具分型面齐平,允许低于分型面不大于0.03mm。
3)型芯、凸模、镶件等,其尾部高度尺寸未注明公差时,其端面应在装配后与其配合的零件齐平。
4)制品同一表面的成型腔分布在上、下模或两模时,装配后沿分型面的错边不大于0.05mm,并其组合尺寸不超过型腔允许的极限尺寸。
5)凸模与凹模装配后的配合间隙,应保持周围均匀。
6)需保持同轴的两个以上零件,其同轴度必须保证装配要求,使各配合零件能顺利装卸,活动自如。
7)模具导向件的导向部分,装配后保证滑动灵活,无卡滞现象。
8)模具中供两次分型用的拉杆、拉板装配后,各工作面应在同一平面内,允许其极限偏差为±0.1mm。
9)模具装配后,两安装平面应保持平,其平行度公差按按GB1184附录一的6级。
三、综合要求:
1)模具、模架及其零件的工件表面,不应有碰伤、凹痕、裂纹、毛刺、锈蚀等缺陷。
2)经热处理后的零件,硬度应均匀,不允许有脱碳、软点、氧化斑点及裂纹等缺陷。
热处理后应清除氧化皮,脏物油污。
3)配通用模架模具,装配后两侧面应进行同时磨削加工,以保证模具能顺利装入模架。
4)模具的冷却水道应保证畅通。
(二)零件加工
成型零部件:
为了保证导向作用,动、定模的导柱,导套孔的孔距精度应控制在0.01mm以内。
因此,必须用坐标镗床对动、定模镗孔。
在缺少坐标镗床的情况下,较普遍采用的方法是将动、定模合在一起,在车床、铣床或镗床上进行镗孔。
成型零部件采用优质碳素工具T8A钢,强度高,耐磨性好,热处理变形小,有时还要求耐腐蚀,调质淬火低温回火≥55HRC
型芯的加工:
把成型面的曲面图通过计算机产生刀具加工路径进行数控铣外形加工,再铣型芯,钻推杆孔,加工浇口。
型腔的加工:
把成型面的曲面图通过计算机产生刀具加工路径,留余量在数控铣上加工成型,再用电火花加工成型。
导柱导套加工:
孔径与导柱相配,一般采用H7/m6,为了保证导向作用,要求导柱、导套的配合间隙小于凸、凹模之间的间隙。
外径与上模座相配,采用H/r过盈配合,另一端则与导套滑动配合。
为了保证导向精度、加工时除了使导柱、导套的配合符合尺寸精度要求外,还应满足配合表面间的同轴度,即导柱两个外圆表面间的同轴度以及导套外圆与内孔表面的同轴度要求。
为了使导柱、导套的配合表面硬而耐磨而中心部分具有良好韧性,用T8A,表面耐磨、有韧性、抗弯曲。
不易折断,热处理:
表面淬火,低温回火≥55HRC。
导柱在热处理后修复中心孔,最后进行磨削时,可利用两端中心孔进行装夹,并应在一次装夹中将导柱的两个外圆磨出,以保证两表面间的同轴度。
导套磨削加工时,可夹持非配合部分,在万能磨床上将内外圆配合面一次装夹磨出,以达到同轴度要求。
用这方法加工时,夹持力不宜过大,以免内孔变形。
或者是先磨内圆,再以内圆定位,用顶尖顶顶住芯轴磨外圆。
这种加工方法不仅可以保证同轴度,且能防止内孔的微量变形。
导柱、导套端部转弯处必须圆滑,以防止在运动中将配合面划伤。
因此,全部精磨后,必须用油石将圆弧处磨圆滑,消除磨削后在圆弧处出现的棱带。
(三)零件工艺路线:
此处省略 NNNNNNNNNNNN字。
如需要完整说明书和设计图纸等.请联系 扣扣:
九七一九二零八零零另提供全套机械毕业设计下载!
该论文已经通过答辩
谢 辞
在此次的毕业设计中,叶东老师在设计过程中给予了我正确的指导,在众多方面提供了方便和便利,为论文的合理性、可行性和完善性提供了有利的帮助。
在此表示衷心的感谢。
同时,系领导和老师也在设计过程中时常关心我、督促我,在查阅文件资料方面提供了很大的便利,在此也表示衷心的感谢。
希望以后还有机会能听到老师们的谆谆教悔。
参考文献
《塑料成型工艺与模具设计》屈华昌主编机械工业出版社
《机械设计手册》徐灏主编机械工业出版社
《模具设计与制造简明手册》冯炳尧、韩泰荣、蒋文森编辑上海科学技术出版社
《模具制造》黄健求主编机械工业出版社