快速处理综采工作面大型断层超深孔扩裂爆破技术方案.docx
《快速处理综采工作面大型断层超深孔扩裂爆破技术方案.docx》由会员分享,可在线阅读,更多相关《快速处理综采工作面大型断层超深孔扩裂爆破技术方案.docx(16页珍藏版)》请在冰豆网上搜索。
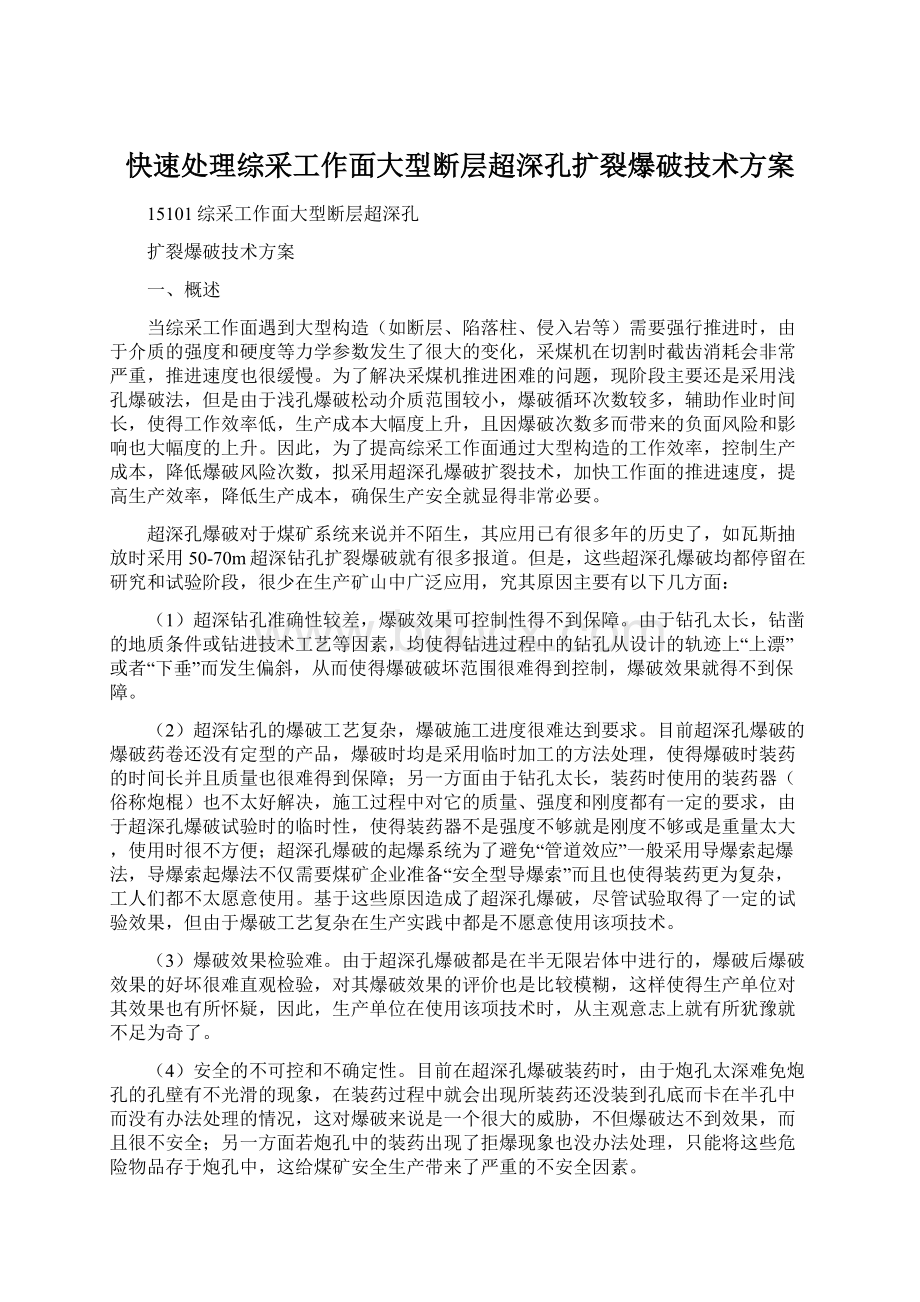
快速处理综采工作面大型断层超深孔扩裂爆破技术方案
15101综采工作面大型断层超深孔
扩裂爆破技术方案
一、概述
当综采工作面遇到大型构造(如断层、陷落柱、侵入岩等)需要强行推进时,由于介质的强度和硬度等力学参数发生了很大的变化,采煤机在切割时截齿消耗会非常严重,推进速度也很缓慢。
为了解决采煤机推进困难的问题,现阶段主要还是采用浅孔爆破法,但是由于浅孔爆破松动介质范围较小,爆破循环次数较多,辅助作业时间长,使得工作效率低,生产成本大幅度上升,且因爆破次数多而带来的负面风险和影响也大幅度的上升。
因此,为了提高综采工作面通过大型构造的工作效率,控制生产成本,降低爆破风险次数,拟采用超深孔爆破扩裂技术,加快工作面的推进速度,提高生产效率,降低生产成本,确保生产安全就显得非常必要。
超深孔爆破对于煤矿系统来说并不陌生,其应用已有很多年的历史了,如瓦斯抽放时采用50-70m超深钻孔扩裂爆破就有很多报道。
但是,这些超深孔爆破均都停留在研究和试验阶段,很少在生产矿山中广泛应用,究其原因主要有以下几方面:
(1)超深钻孔准确性较差,爆破效果可控制性得不到保障。
由于钻孔太长,钻凿的地质条件或钻进技术工艺等因素,均使得钻进过程中的钻孔从设计的轨迹上“上漂”或者“下垂”而发生偏斜,从而使得爆破破坏范围很难得到控制,爆破效果就得不到保障。
(2)超深钻孔的爆破工艺复杂,爆破施工进度很难达到要求。
目前超深孔爆破的爆破药卷还没有定型的产品,爆破时均是采用临时加工的方法处理,使得爆破时装药的时间长并且质量也很难得到保障;另一方面由于钻孔太长,装药时使用的装药器(俗称炮棍)也不太好解决,施工过程中对它的质量、强度和刚度都有一定的要求,由于超深孔爆破试验时的临时性,使得装药器不是强度不够就是刚度不够或是重量太大,使用时很不方便;超深孔爆破的起爆系统为了避免“管道效应”一般采用导爆索起爆法,导爆索起爆法不仅需要煤矿企业准备“安全型导爆索”而且也使得装药更为复杂,工人们都不太愿意使用。
基于这些原因造成了超深孔爆破,尽管试验取得了一定的试验效果,但由于爆破工艺复杂在生产实践中都是不愿意使用该项技术。
(3)爆破效果检验难。
由于超深孔爆破都是在半无限岩体中进行的,爆破后爆破效果的好坏很难直观检验,对其爆破效果的评价也是比较模糊,这样使得生产单位对其效果也有所怀疑,因此,生产单位在使用该项技术时,从主观意志上就有所犹豫就不足为奇了。
(4)安全的不可控和不确定性。
目前在超深孔爆破装药时,由于炮孔太深难免炮孔的孔壁有不光滑的现象,在装药过程中就会出现所装药还没装到孔底而卡在半孔中而没有办法处理的情况,这对爆破来说是一个很大的威胁,不但爆破达不到效果,而且很不安全;另一方面若炮孔中的装药出现了拒爆现象也没办法处理,只能将这些危险物品存于炮孔中,这给煤矿安全生产带来了严重的不安全因素。
多年来,针对上述问题进行了研究和实践,已形成了多项专利和施工的配套工具,能够较好的解决上述问题。
采用超深孔扩裂爆破处理高瓦斯矿井综采工作面大型构造的研究,首先需要解决工作面在大药量爆破前提下的瓦斯涌出问题,其次是需要解决超深孔爆破技术的实用性和可操作性问题,也就是说要在确保安全的前提下高效、快速的通过大型构造的问题。
根据超深孔爆破已有的研究成果和《煤矿安全规程》的要求,设计本技术方案。
由于超深孔爆破药量较大,影响范围大。
为了控制爆破对瓦斯所带来的压力,摸清大爆破对瓦斯的影响,岩石介质与爆破参数之间的关系,钻孔设备所能达到的定位精度,以及结合采煤工艺参数,确实保证试验的安全、可控,并达到预期的爆破效果,确定如下爆破试验的设计原则:
(1)根据采煤高度,将爆破破碎范围控制在采高范围内,尽最大努力不伤及到顶、底板;
(2)对爆破区域必须一次性破碎到位,避免重复爆破处理时的钻孔困难和效率低下的问题;
(3)控制一次起爆药量,弄清爆区瓦斯和煤尘(煤尘具有爆炸性)情况,若不清或有疑问时,必须查清或采取措施后再施工,以确保生产安全。
根据上述原则和15101工作面的采高(3m)参数,以及以前研究的药卷直径与爆破破坏范围的经验,暂时确定药卷直径Φ63mm、炮孔深度15-20m、一次爆破药量控制在200kg以内。
二、15101工作面概述
(一)工作面概况
15101工作面走向长150m,倾斜长平均458m,煤层厚度为6.0m,煤层倾角平均为8°。
15101工作面采用倾斜长壁后退式综合机械化低位放顶煤全部垮落采煤法。
工作面采用MG300/730-WD采煤机,工作面切眼长150m,采高3.0±0.1m,循环进度0.8m,放煤高度3.0±0.1m,放顶煤区段平均为135m,“一采一放”为一循环。
工作面共布置102组支架,其中端头支架(型号ZTA6500/19.5/34)6组,中间支架(型号ZF4800/17/32)96组。
目前工作面胶带顺槽推进127.9米,轨道顺槽推进120.6米,平均回采长度124.25米。
截止目前工作面剩余可采长度290米,剩余可采储量34万吨。
(二)工作面煤层及顶底板情况
工作面地面标高+1250—+1340m;工作面标高+923—+967m。
井下位置及四邻采掘情况:
15101首采工作面南部为专用回风下山、东部为出煤巷、西部为15102工作面回风顺槽。
煤层情况:
工作面开采煤层属下太原组下端下部的15#煤层,该煤层赋存稳定,煤厚变异较小,煤层结构较复杂。
煤体以黑色、块状为主,粒状次之,内夹黄铁矿,呈团块状,煤质为贫煤。
煤层直接顶板为泥岩、砂质泥岩,厚度10m左右,硬度系数3.0;老顶为K2灰岩,硬度较大,含水性微弱,厚度7m左右,硬度系数6.0;直接底为铝质泥岩,厚度1.8m左右,硬度系数3.0;老底为砂质泥岩,厚度3.5m左右,硬度系数3.5—4.0。
(三)工作面地质构造
本工作面总体地势东北高西南低,总体呈一单斜构造。
工作面东部坡度较缓,西部较大,局部地方底板出现起伏变化,形成小型褶曲,在褶曲转折端会造成煤层及顶板裂隙发育,煤层破碎。
在15101工作面轨道顺槽,分别距离内切眼58m处和出煤巷100m处发育有X11和X12两个陷落柱,两陷落柱特征分别为X11:
长轴方向N30ºE,直径42×26m;X12:
长轴方向N60ºE,直径54×32m,且均位于回采范围内,对回采工作有一定的影响。
15101工作面高抽巷在里程269m处揭露一落差1.5m,倾角41°,倾向为323°的正断层。
15101工作面胶带顺槽距出煤巷129m处有一小型向斜,在距出煤巷157m处有一小型背斜。
根据首采工作面坑透资料显示,在X11陷落柱距离内切眼10m范围内可能会衍生出一个落差1.5m左右的正断层。
目前工作面在10#支架破煤层底板,割采岩石。
由47#支架位置开始采面进入全岩,全岩至79#结束,其中岩石最厚位于70#支架左右煤层位于回采顶1m,后在90#支架处进入全煤,回采至机尾留有底板三角煤2m左右。
工作面在81#支架处存在一条倾角为50°,断距为0.5m的Fj1正断层。
预计延伸长度不超过20m,未在轨道顺槽有出露。
(四)工作面水文地质
工作面煤层直接充水含水层为太原组K2灰岩含水层,该含水层赋水性一般较弱。
15101工作面回采范围内地质条件较为简单,局部地方底板出现起伏变化,形成小型向斜及背斜构造,在向斜及背斜转折端会造成煤层及顶板列隙发育,回采至该处时可能会出现涌水增大现象,向斜轴部在回采过程中还会形成积水区。
矿井奥灰水位为:
+823-+825m,本工作面开采最低标高为+923m,故目前不涉及承压开采。
X11和X12陷落柱经钻探验证不导水,高抽巷在掘进至F3断层时,水量无变化。
在回采过程中,由于顶板自然脱落,造成裂隙发育,预计会破坏顶板K2、K3、K4三层含水层,但这三层含水层赋水性都较弱,且已经打设顶板疏放水孔,在回采过程中预计水量约为15m³/h,施工队组及时完善排水设施保证正常回采。
根据电法勘探显示,15101工作面内无富水区域,
工作面最大涌水量10m3/h;正常涌水量5m3/h。
(五)煤层自燃性及爆炸倾向性
2015年山西省煤炭工业局综合测试中心对佳瑞煤业14#、15#煤层进行了煤层自燃倾向性鉴定,鉴定结论为:
14#煤层为(Ⅱ)类自燃, 最短发火期为75天;15#煤层为(Ⅲ)类不易自燃,最短发火期为97天。
2015年山西省煤炭工业局综合测试中心对14#、15#煤层进行了煤尘爆炸性鉴定,鉴定结论为:
14#煤层煤尘具有爆炸性,火焰长度30mm,14号煤煤尘云最大爆炸压力0.56MPa,最大压力上升速率34.71MPa/s,煤尘云爆炸下限浓度20g/m3,煤尘最低着火温度640℃,煤尘层最低着火温度290℃,岩粉用量55%;15#煤层煤尘具有爆炸性,火焰长度20mm,15号煤煤尘云最大爆炸压力0.55MPa,最大压力上升速率30.09MPa/s,煤尘云爆炸下限浓度20g/m3,煤尘最低着火温度640℃,煤尘层最低着火温度290℃,岩粉用量50%。
(六)瓦斯含量
根据2012年瓦斯等级鉴定报告的批复,佳瑞煤业公司属高瓦斯矿井。
15101工作面15#煤层预抽前瓦斯含量9.8m3/t,预抽后瓦斯含量5.59m3/t,预抽后无明显瓦斯动力现象。
瓦斯压力0.3MPa以下。
三、3207工作面陷落柱超深孔爆破设计
(一)超深钻孔的钻凿与定位
超深钻孔高质量的钻凿和准确定位是实现超深孔爆破关键和基础,因此,正确认识超深钻孔的偏斜机理和影响偏斜的因素,然后针对性这些因素进行改进才是解决问题的正确方法。
1、超深钻孔产生偏斜原因分析
钻进过程中钻孔偏斜是主、客观因素共同作用的结果。
地质因素是钻进时的客观因素,技术和钻进工艺因素是钻进时的主观因素。
在不同的条件下,两类因素对钻孔偏斜的影响程度是不同的,有时地质因素是主导因素,有时技术和工艺因素是主导因素。
(1)地质因素
影响钻孔偏斜的地质因素主要是钻进岩体的产状、硬度、研磨性、密度、矿物成分、变质程度及结构构造等。
地质因素影响的基础是岩体的非均质性,它对钻孔方向及钻孔特征有着多种作用。
岩石的层理、裂隙、断层、软硬互层、溶洞、卵砾石等结构构造使岩层具有非均质性,造成钻头在孔底受力不均衡,形成倾倒力矩,引起钻孔偏斜,其中层理和软硬互层对钻孔的偏斜最具影响。
地质因素是客观因素,一旦选定地层和钻孔的开孔参数,专业技术人员一般不会去改变地质情况,而主要利用钻孔在地层中的偏斜规律合理地设计钻孔轨迹。
(2)技术因素
技术因素影响具体表现在以下几点:
1)在开孔钻进中,因钻孔方位、倾角校放的不是很准确。
造成钻机立轴与钻孔不在同一条中心线上造成钻孔的偏斜。
2)开孔时立轴内的钻杆过长,立轴筒磨损间隙较大,容易使立轴产生较大的摆动,直接影响钻头在孔底钻进时的稳定性。
3)使用了弯曲的接首、钻杆等,都会使钻具连接后不正,导致钻孔歪斜。
4)在扩孔钻进中,因孔内各处的硬度、孔径大小不一致,钻头可在钻孔内左右移动,靠向孔内一侧,使受压弯曲的钻杆挠度加大,钻头轴线与钻孔的轴线不重合,不能和钻进方向保持一致。
(3)钻进工艺参数
钻进工艺参数是指钻压、转速和钻井液等,钻进工艺参数的选取与所用钻进方法、地层情况、组合钻具所要达到的目的以及钻头的技术参数都有关系。
适当的调整钻进工艺参数决定着组合钻具能否很好地发挥作用。
例如钻压的大小直接决定钻具挠曲变形的大小,转速的大小决定回转产生离心力的大小,而离心力的大小决定挠曲变形和钻具自重对钻孔轨迹作用的程度。
所以为使组合钻具充分发挥调整钻孔轨迹的作用,应根据实际钻进情况,合理选用钻进工艺参数。
工艺因素影响具体表现在以下几点:
1)钻机、钻具的组合使用不当。
不能根据钻孔岩性和使用钻机的特点合理配置钻机和组合钻具。
2)钻进施工时,误操作或钻机加压过大,导致钻杆产生严重的弯曲。
3)在松散或较破碎的煤层或岩层中钻进,使用的冲洗液量过大,会较严重地破坏孔壁,造成孔内局部的塌孔,至使孔径无故扩大。
加压钻进时,钻杆有弯曲空间,钻孔易产生偏斜。
2、预防钻孔偏斜措施
从上述对钻孔偏斜的原因分析可知,为了保证钻孔质量,在钻孔施工过程中,贯彻“防斜为主,纠斜为辅;一旦偏斜坚决纠”的原则,因此加强对钻孔弯曲的预防工作是十分必要的。
预防钻孔偏斜,要看准主要问题,根据实际经验,应从引起钻孔偏斜的三个基本因素的分析,及时抓好以下几条原则:
(1)正确开孔,保证开孔角度(方位角与倾角)符合设计要求;
(2)在保证顺利钻进的前提下,采取一切措施,尽量缩小孔壁间隙;
(3)粗径钻具长度适当,接起来不弯曲;
(4)根据岩层的具体情况和施工的特殊需要,适当减小钻进压力;
具体的实施方法,应当从以下几点出发:
(1)保征安装质量。
地基要修平、要坚固,支架要安平、安正,机器要装平、装正和装稳。
(2)开孔前准确的找好主轴。
可靠地把钻机基脚和主轴变角装置固定牢固。
(3)钻机的有关部件,磨损过大的要换新的。
(4)适当地加粗径钻具。
(5)根据岩层情况,适当地减轻钻进压力。
遇到开孔、换径、换层、扩孔、溶洞、裂隙等情况,更应当把压力控制在最低限度。
3、钻孔方案
(1)钻机型号
根据工作面情况和搬移方便,易于操作的要求,拟采用石家庄万达生产的ZYJ-270/170单腿液压回转钻机,该钻机配备的钻杆直径为42mm,钻头直径为75mm。
(2)钻孔深度
根据勘测资料在工作面处的揭露情况数据可知,断层岩层在当工作面眼12°向前推进时,前方的岩石分布情况,如图1所示。
根据设计原则重点处理全岩区域以及岩多煤少区,因此确定爆破范围,长度上以支架42#到79#为界,宽度30米。
根据现有钻孔情况,确定最大孔深15米,分两阶段爆破。
因此其炮眼深度为9-15m即可,如图2所示。
(3)钻孔位置及孔间距
根据现场工作面地质勘探情况,结合采煤高度3.0m和以往模拟实验与现场爆破的经验,Φ63mm的药卷的爆破作用半径等因素,现场确定钻孔布置位置。
暂时拟取采高一半为布置钻孔的中位置,波动200mm处布孔,孔间距暂时取2.0m左右。
水平方向打眼拟采用的炮孔布置方案如图2所示。
图1工作面沿12°推进时可能遭遇的岩石范围
标注单位m
图2超深孔爆破设计方案俯视及正视图
(二)装药量确定与装药工艺
1、装药壳体的设计
为了使超深孔爆破的装药更为顺利、更为方便,根据爆破模拟实验和柱状药包爆破破裂区范围,特设计了适用于煤矿的扩裂爆破壳体结构。
该壳体结构为PVC材质,其外径为63mm、内径60mm;有效装药长度为1000mm,并且各壳体之间可以通过螺纹连接,有一定的连接力,其示意图如图3所示。
因此,采用这种壳体的装药结构,可以为装药和爆破带来如下好处:
(1)具有抵抗爆炸冲击波或爆炸应力波的压缩作用,减小炸药动压减敏作用;
(2)药包具有一定的刚度,使药包与炮孔之间更具有适应性,装药更为顺利和通畅;
(3)各药包之间可以紧密连接起来形成药柱,并且它们的连接均具有一定的强度,在装药时可以使整个药柱自由进出,可以避免装药还没有装到位而卡在孔中而没有办法处理的情况,有利于爆破安全。
图3装药壳体及其连接
2、装药量的确定
根据扩裂爆破的装药特点,即炮孔内采用连续装药结构,因此,装药量可以根据炮孔长度,计算出装药的药包个数,再乘以每个药包的药量即可。
根据上述装药壳体的设计,每个壳体大概能装药2.85-2.95kg左右。
因此,根据试验确定的炮孔长度计算试验爆破的总药量,但是,为了保证安全一次爆破总药量不大于200kg为好,爆破作业后观察爆破效果,评估现场作业安全情况。
拟用爆破参数如表1。
共50个炮孔,每孔需两发雷管,共消耗雷管100。
分9次起爆,最小单次准备药量80kg,最大单次准备药量160kg。
表1爆破参数表
炮眼编号
炮眼孔深(m)
装药长度(m)
填塞长度(m)
药量(kg)
爆破编号
雷管段位
准备药量(kg)
装药方式
联线方式
2
12.5
7
5.5
20.7
Ⅰ
1
156
(39包)
正向起爆
串联
3
15
9
6
26.6
Ⅰ
4
15
9
6
26.6
Ⅰ
3
5
15
9
6
26.6
Ⅰ
6
15
9
6
26.6
Ⅰ
5
7
15
9
6
26.6
Ⅰ
8
15
9
6
26.6
Ⅱ
1
160
(40包)
正向起爆
串联
9
15
9
6
26.6
Ⅱ
10
15
9
6
26.6
Ⅱ
3
11
15
9
6
26.6
Ⅱ
12
15
9
6
26.6
Ⅱ
5
13
15
9
6
26.6
Ⅱ
14
15
9
6
26.6
Ⅲ
1
160
(40包)
正向起爆
串联
15
15
9
6
26.6
Ⅲ
16
15
9
6
26.6
Ⅲ
3
17
15
9
6
26.6
Ⅲ
18
15
9
6
26.6
Ⅲ
5
19
15
9
6
26.6
Ⅲ
20
15
9
6
26.6
Ⅳ
1
160
(40包)
正向起爆
串联
21
15
9
6
26.6
Ⅳ
22
15
9
6
26.6
Ⅳ
3
23
15
9
6
26.6
Ⅳ
24
15
9
6
26.6
Ⅳ
5
25
15
9
6
26.6
Ⅳ
26
15
9
6
26.6
Ⅴ
1
80
(20包)
正向起爆
串联
27
15
9
6
26.6
Ⅴ
28
15
9
6
26.6
Ⅴ
3
续表1
炮眼编号
炮眼孔深(m)
装药
长度(m)
填塞长度(m)
药量(kg)
爆破编号
雷管段位
准备药量(kg)
装药方式
联线方式
30
9
5
4
14.8
Ⅵ
1
124
(31包)
正向起爆
串联
31
10.5
6
4.5
17.7
Ⅵ
32
11.5
7
4.5
20.7
Ⅵ
3
33
12
7
5
20.7
Ⅵ
34
13
8
5
23.6
Ⅵ
5
35
13
8
5
23.6
Ⅵ
36
13.5
8
5.5
23.6
Ⅶ
1
144
(36包)
正向起爆
串联
37
13.5
8
5.5
23.6
Ⅶ
38
13.5
8
5.5
23.6
Ⅶ
3
39
13.5
8
5.5
23.6
Ⅶ
40
14
8
6
23.6
Ⅶ
5
41
14.5
8
6
23.6
Ⅷ
42
15
9
6
26.6
Ⅷ
1
160
(40包)
正向起爆
串联
43
15
9
6
26.6
Ⅷ
44
15
9
6
26.6
Ⅷ
3
45
15
9
6
26.6
Ⅷ
46
15
9
6
26.6
Ⅷ
5
47
15
9
6
26.6
Ⅷ
48
15
9
6
26.6
Ⅸ
1
136
(34包)
正向起爆
串联
49
15
9
6
26.6
Ⅸ
50
15
9
6
26.6
Ⅸ
3
51
15
9
6
26.6
Ⅸ
52
15
9
6
26.6
Ⅸ
5
合计
743.5
443
300
1267.6
1280
(320包)
3、装药工艺
超深孔扩裂爆破的装药是一个关键技术之一,装药好坏或顺利与否,关系到爆破效果的好坏和爆破的安全,因此,在进行装药时要按如下步骤进行。
(1)药包准备与加工
本次试验由于没有现成的药包,试验时必须现场进行加工,加工时先将药包壳体清理干净,再将直径35mm的水胶炸药药卷装入已准备好的壳体内,装入时还应边装边震动壳体,使炸药密实的装入壳体中,炸药装入高度达到最下刻线为止。
(2)探孔
在装药前,为避免炮孔的孔壁有不光滑的现象,先要进行探孔作业,即在装药器上装上与药卷直径稍大的导向头(本次试验时采用70mm)对全长炮孔进行探孔,探孔时如炮孔遇有不光滑的点需要反复推察,使探孔探头能顺利通过为准。
如果遇孔壁完整度差、装药安全存在风险的炮孔,应做好标记,报废该孔,不得继续装药作业,需重新施工。
(3)装药
装药时应有四人配合作业,孔口两人,一人抓住已装入的药包,另一个连接新药包,开始时可以两人用手直接将药包送入。
当药包加长到一定长度后,由于药包重量的增加,孔口的两人不能将药包送入孔中时,另外一人则用装药器辅助他们将药柱送入炮孔中,还有一人记录装入的药包个数。
当接入的药包全部连接好后,一次将所有药柱送入孔中。
(三)起爆系统设计
本次超深孔爆破所使用的炸药为水胶炸药,而水胶炸药在超深孔爆破时,由于先爆的炸药所产生的冲击波或爆炸应力波,对后起爆的炸药产生了动压作用,使后起爆的炸药出现减敏作用,直至爆轰熄灭。
因此,为了解决这个问题,在以往的超深孔爆破中,基本上都采用了导爆索起爆法,以增强超深孔炸药的起爆效果。
但是导爆索起爆法由于装药的不便利,使得装药时间很长,工作效率低,因此,使得超深孔爆破在生产单位很难形成实际的生产率,为了改变这种现状,本次在药卷壳体设计时就已经考虑了这种动压减敏的副作用,因此试验时就采用正向起爆即可。
起爆药包并联接入两个同段煤矿许用毫秒电雷管。
药包外的起爆线用1mm2爆破钢丝线接出,连接时要接紧、接牢,并用防水胶布密封接头,且要使起爆线进行短路连接。
当炮孔填塞好后,再将各起爆线串联接入起爆母线网路,起爆母线要达到300m长(达到远距离起爆的要求),并且中间无接头。
(四)填塞工艺
炮孔的填塞材料俗称炮泥,它的作用是保证炸药反应完全、充分,使其放出最大热量和减少有毒气体生成量,提高炸药的热效率,使炸药的化学能尽量多的转变成机械功。
同时在有瓦斯和煤尘爆炸危险的工作面,除了降低爆炸气体逸出自由面的温度和压力外,还起到阻止灼热固体颗粒从炮孔飞出,减少引燃瓦斯的机会。
在炮孔中不同位置的炮泥,爆破后的运动规律是不同的。
爆炸时炮眼内产生的压力不仅作用在孔壁上,也同时作用在炮泥上,但炮泥不是刚体,而是可压缩的材料,在爆轰压力作用下,靠近装药部分的炮泥开始时运动速度增加很快,基本上按线性增长,这时炮泥产生很大的塑性变形,使其密度不断增大,当密度增大到一定程度后,炮泥和孔壁之间的摩擦力和横向推力也增大,如果此时的摩擦力和抗剪强度大于爆生气体的推力,炮泥的运动速度相对要减小,甚至停止运动。
随着爆轰压力的继续升高,对炮泥的推力不断增大,炮泥中的剪应力也不断增大,直至克服炮泥与孔壁之间的摩擦力和炮泥的剪应力,使炮泥迅速向孔外滑动而抛出炮孔。
靠近孔口的炮泥刚开始时,由于惯性作用向外运动的速度很小,但当爆炸应力波传播到孔口后,从自由面产生反射拉伸作用,使孔口炮泥向外抛出;同时炮孔内爆生气体对内层炮泥的作用不断增强,其运动速度也会越来越大,推动孔口炮泥产生向外运动的速度也增大,最终两者速度相等一起抛出炮孔。
超深孔爆破的填塞也是非常重要的,它不但关系到爆破效果的好坏也关系到爆破的安全。
因此,需要根据超深孔爆破的不同目的,对炮孔进行针对性的填塞。
为了达到本次试验的目的,填塞时需要注意如下几点:
1、填塞长度的确定
根据相关文献,避免冲孔的安全封孔长度计算公式为L≥nR/(2fλ),其中现场试验爆破孔半径R为37.5mm,侧压系数f为0.3,摩擦