年产300万吨合格铸坯转炉车间设计.docx
《年产300万吨合格铸坯转炉车间设计.docx》由会员分享,可在线阅读,更多相关《年产300万吨合格铸坯转炉车间设计.docx(13页珍藏版)》请在冰豆网上搜索。
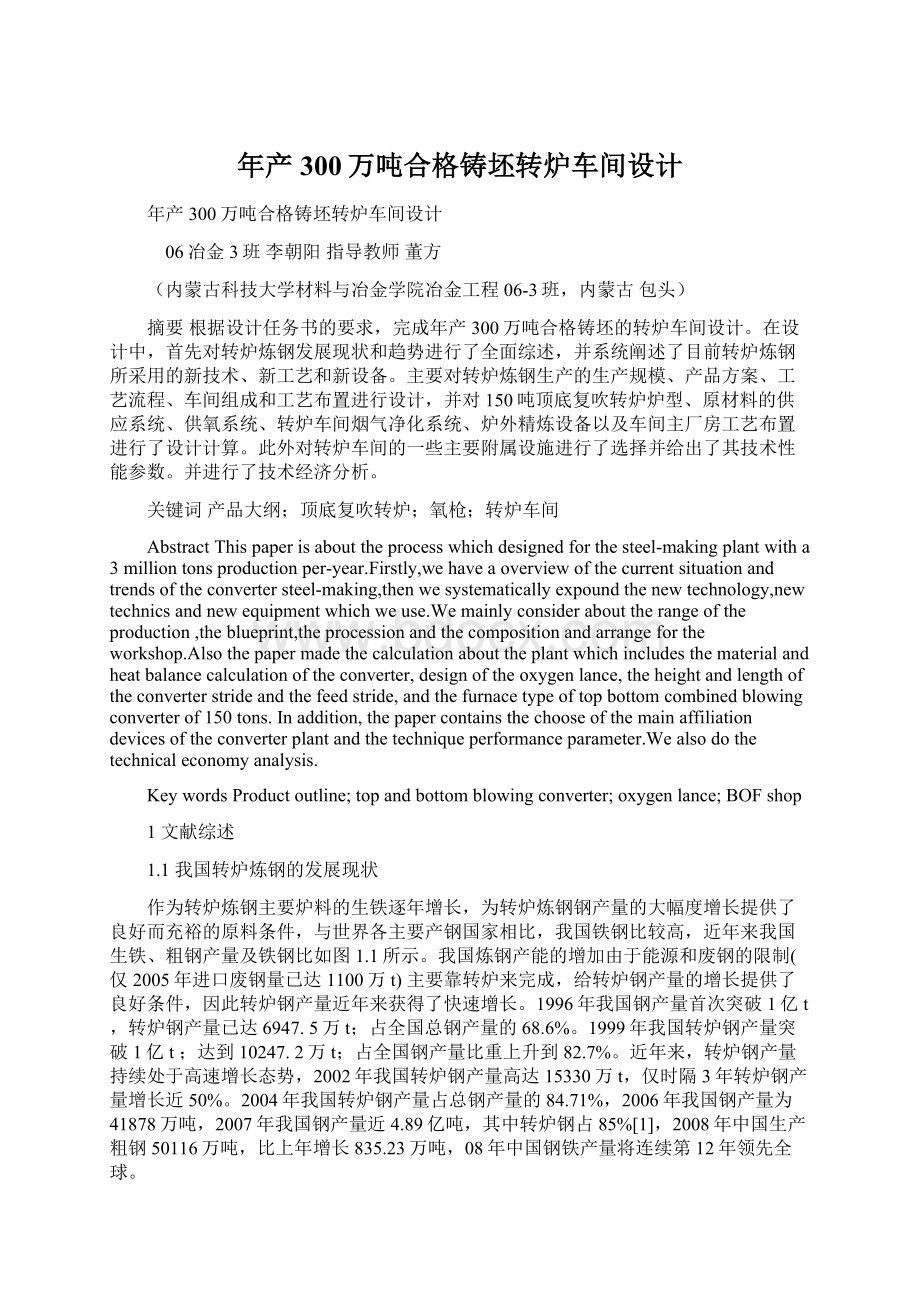
年产300万吨合格铸坯转炉车间设计
年产300万吨合格铸坯转炉车间设计
06冶金3班李朝阳指导教师董方
(内蒙古科技大学材料与冶金学院冶金工程06-3班,内蒙古包头)
摘要根据设计任务书的要求,完成年产300万吨合格铸坯的转炉车间设计。
在设计中,首先对转炉炼钢发展现状和趋势进行了全面综述,并系统阐述了目前转炉炼钢所采用的新技术、新工艺和新设备。
主要对转炉炼钢生产的生产规模、产品方案、工艺流程、车间组成和工艺布置进行设计,并对150吨顶底复吹转炉炉型、原材料的供应系统、供氧系统、转炉车间烟气净化系统、炉外精炼设备以及车间主厂房工艺布置进行了设计计算。
此外对转炉车间的一些主要附属设施进行了选择并给出了其技术性能参数。
并进行了技术经济分析。
关键词产品大纲;顶底复吹转炉;氧枪;转炉车间
AbstractThispaperisabouttheprocesswhichdesignedforthesteel-makingplantwitha3milliontonsproductionper-year.Firstly,wehaveaoverviewofthecurrentsituationandtrendsoftheconvertersteel-making,thenwesystematicallyexpoundthenewtechnology,newtechnicsandnewequipmentwhichweuse.Wemainlyconsiderabouttherangeoftheproduction,theblueprint,theprocessionandthecompositionandarrangefortheworkshop.Alsothepapermadethecalculationabouttheplantwhichincludesthematerialandheatbalancecalculationoftheconverter,designoftheoxygenlance,theheightandlengthoftheconverterstrideandthefeedstride,andthefurnacetypeoftopbottomcombinedblowingconverterof150tons.Inaddition,thepapercontainsthechooseofthemainaffiliationdevicesoftheconverterplantandthetechniqueperformanceparameter.Wealsodothetechnicaleconomyanalysis.
KeywordsProductoutline;topandbottomblowingconverter;oxygenlance;BOFshop
1文献综述
1.1我国转炉炼钢的发展现状
作为转炉炼钢主要炉料的生铁逐年增长,为转炉炼钢钢产量的大幅度增长提供了良好而充裕的原料条件,与世界各主要产钢国家相比,我国铁钢比较高,近年来我国生铁、粗钢产量及铁钢比如图1.1所示。
我国炼钢产能的增加由于能源和废钢的限制(仅2005年进口废钢量已达1100万t)主要靠转炉来完成,给转炉钢产量的增长提供了良好条件,因此转炉钢产量近年来获得了快速增长。
1996年我国钢产量首次突破1亿t,转炉钢产量已达6947.5万t;占全国总钢产量的68.6%。
1999年我国转炉钢产量突破1亿t;达到10247.2万t;占全国钢产量比重上升到82.7%。
近年来,转炉钢产量持续处于高速增长态势,2002年我国转炉钢产量高达15330万t,仅时隔3年转炉钢产量增长近50%。
2004年我国转炉钢产量占总钢产量的84.71%,2006年我国钢产量为41878万吨,2007年我国钢产量近4.89亿吨,其中转炉钢占85%[1],2008年中国生产粗钢50116万吨,比上年增长835.23万吨,08年中国钢铁产量将连续第12年领先全球。
1.2我国转炉炼钢发展趋势
一些高附加值钢种多为低合金高强度或微合金高强度钢种,特别是V、Nb、Ti微合金化钢种将受到关注。
由于我国的炼钢技术相对有一些落后,一些高附加值的特殊钢的缺口仍旧是靠进口来填补,这给我们钢铁企业很大的压力,同时也给了我们很好的市场来发展我国的钢铁业。
今后我国汽车、造船、集装箱、机械制造、油、气输送管线、电工等用钢仍将大幅度增长,大型转炉炼钢厂将依靠自身的装备优势(配置热连轧或宽厚板轧机),结合日新月异的冶炼工艺技术进步,努力增产这类高附加值钢种,提高我国钢铁企业在世界钢铁市场中的竞争力和占有率,满足市场需求[2]。
1.3转炉炼钢存在的问题
我国中、小型转炉炼钢厂(车间)生产量达到6000万t以上,与前后工序配套的有小高炉、小连铸、小轧机已形成一定的综合生产能力。
中、小型转炉钢厂是在我国钢铁发展的历史中形成的,今后在一段较长的时间应配合我国钢铁行业的产业结构调整政策和优化工艺及调整产品结构的发展战略。
搞好扩容改造挖潜,相应提高技术和装备水平,比如适当增设铁水脱硫设施和根据钢种要求增设炉外精炼装置,以求在增产的同时进一步提高钢的质量,扩大冶炼钢种范围,降低消耗,改善环保条件,在市场竞争中继续求得生存发展。
今后应抑制低水平中小型转炉重复建设。
2.生产规模及产品方案
2.1生产规模
新建转炉用于向新建的板坯连铸机供应钢水,根据连铸机工序要求,年产合格铸坯为300万吨。
2.2产品方案
生产钢种有碳结钢、优质碳结钢、超低碳钢、低合金高强度钢及耐热钢、管线钢、压力容器用钢等专用钢种,见下表。
表2.1生产钢种及所占比例
钢种
牌号
执行标准
比例%
数量(万吨)
碳素结构钢
Q195~275
GB/T7912.1-1989
40
76
优碳钢
SPCCSPHD
GB/T710-1991
25
47.5
SPCC~SPCE10~20号
低合金钢
16MnQ345A(B)510L
管线钢
GB/T1591-1994
GB/T3273-1989
20
38
无取向硅钢
50W470~50W1300
15
28.5
合计
100
190
3.设备选型及技术性能
3.1转炉[3]
A.转炉公称容量
年产300万吨合格铸坯需要合格刚睡的质量为
Q=3000000/0.98×0.98
式中:
Q—车间生产能力,吨钢/年
第一个0.98—炉外精炼钢水的收得率
第二个0.98—连铸后金属的收得率
Q=3123698t
据年产300万吨合格铸坯可大致估算出炉子的公称容量
Q=365×1440×n×T×η/τ
式中:
Q—车间生产能力,3123698吨钢/年
n—车间经常吹炼转炉座数,取1.75
T—每座转炉平均产钢量,t
τ—每一炉钢的冶炼周期,取33min
η—车间年有效作业率,81%
从而可以算出T=138.4t取公称容量为150t
B.转炉炉型设计
(1)原始条件:
①炉子平均出钢量为150吨钢水
②原料为生铁、废钢、铁合金,并用矿石法操作;
(2)熔池尺寸计算:
①熔池直径计算:
根据前述生产实践情况,选取供氧时间为14.5min
根据经验公式:
D=K(G/t)1/2
式中:
G—新炉金属装入量,t,可近似的取其公称容量150t;
t—平均每炉钢纯吹氧时间,14.5min
K—比例系数,取1.55
所以D=1.55×(150/14.5)1/2=4.985m=4985mm
②熔池深度计算:
由于选用转炉类型为顶底复吹型转炉,故本设计使用截锥型炉底。
根据公式
Vc=G/Ύ
式中:
Vc—熔池体积,m3
G—新炉金属装入量,t,可近似的取其公称容量150t;
Ύ—钢水密度,Ύ=6.8t/m3
则Vc=G/Ύ=150/6.8=22.06m3
又有通常倒截锥体顶面直径b=0.7D
故催在如下关系式:
Vc=0.574hD2
式中:
h—熔池深度,m
则可以求出h=Vc/0.574D2
h=1.547m=1547mm
h/D=0.31在0.31—0.33范围内,符合要求。
(3)炉帽尺寸计算:
①炉口直径d
d口=0.45D
d口=0.45D=0.45×4.985=2.243m=2243mm.
由于采用水冷炉口,有关系式d口+200—400mm=d水,本设计取400mm,即各边大出200mm.
②炉帽倾角取62°,所以炉帽高度为:
为了维护炉口的正常形态,防止因砖衬蚀损使其迅速扩大,在炉口上部设有高度为H口=300—400的直线段
取H口=0.36m=360mm
H帽=(D-d)tanθ/2+H口=0.5×(4.985-2.243)×tan62°+0.36=2.732m=2732mm
炉帽总容积V帽
V帽=π/12(H帽-H口)(D2+Dd+d2)+π/4d2H口=26.9m3
(4)出钢口尺寸计算:
出钢口中心线水平倾角取0°
出钢口尺寸d出=(63+1.75T)1/2=(63+1.75×150)1/2=180.4mm
出钢口水平倾角取0°使钢流对钢包内的金属冲击力变小。
、
出钢口外径一般为出钢口内径的6倍左右,即
d外=6d出=1082.4mm
出钢口长度LT
出钢口长度一般为出钢口内径的7~8倍,即
LT=(7~8)d出
本设计取为7,则LT=1262.8
(5)炉子内型高度:
本设计中炉容比选0.95
转炉有效容积Vt=150×0.95=142.5m3
H身=4V身/πD2=4(Vt-V帽-Vc)/πD2=4.793m=4793mm
H内=H帽+H身+h=2.732+4.793+1.547=9.072m=9072mm
(6)炉子的高径比:
炉壳总高H总=H帽+H身+h+71.38+1170=10313.38
炉壳外径D壳=4985+1030+980+2×71.38=7137.76
H总/D壳=1.44,在1.25~1.45之间,所以符合设计要求。
(7)转炉炉衬的设计:
表3.1转炉炉衬耐火材料厚度
炉帽炉身(加料侧)炉身(出钢侧)炉底
合计
绝热层厚度(mm)
20202020
80
永久层厚度(mm)
110160160420
750
填充层厚度(mm)
100100100100
400
工作层厚度(mm)
560750700630
2640
合计
79010309801170
炉壳钢板厚度的选择
炉帽钢板取c1=0.8c2=57.10mm
炉身钢板取c2=0.01D壳=71.38mm
则应有(D+1030+980+2c2)×0.01=c2
解得c2=71.38mm
炉底钢板取c3=1.0c2=71.38mm
C.氧枪的设计
(1)氧枪喷头设计
①原始条件:
根据本设计物料平衡的计算,知每吨钢耗氧量为52.5m3/t,吹炼时间为14.5min。
输氧管测压点氧气最高压力为1.18MP,氧气平均温度为17℃。
氧枪枪位高度:
化渣枪位1.5~1.8m,吹炼枪位0.9~1.2m。
②计算氧气流量:
Q=52.5×150/14.5=543Nm3/min
③综合考虑,马赫数M=2.0最佳。
④设计工况氧压和喉口直径:
查等熵流表,当M=2.0时,P/P0=0.1278,取P=0.099Mpa,则P0=0.775Mpa,每孔氧流量:
q=543/5=108.6Nm3/min
P0=0.775Mpa=0..775/9.8×100=7.9kg/cm3
根据公式
q=17.64CDP0A喉/To0.5式(3.7)
式中:
CD—喷管流量系数,0.95~0.96,本设计取为0.95
A喉—喉口面积
To—入口处氧气的温度,取为273+17°C
则有108.6=17.64×0.95×[7.9/(290)0.5]×π/4×d喉2
解,得d喉=42.19mm
⑤确定喷孔出口直径:
依据M=2.0,查等熵流表,得:
A出/A喉=1.688,即π/4×d出2=1.688π/4×d喉2
d出=(1.688)0.5×42.19=54.81mm
⑥确定喷孔其它几何尺寸:
(54.81―42.19)/2L=tan4°
解,得L=90.23mm最后确定L=90mm
⑦多孔喷头的各个流股发生汇交和不汇交以效应角θ为界,大于θ各个流股就很少汇交,小于θ就必定汇交。
得出β=12.8°~15.4°,综合考虑取孔倾角15°。
操作枪位为35~40倍的出口直径,即54.81×35~40=1918.35~2192.4mm
(2)氧枪水冷系统设计
氧枪枪身尺寸的确定
氧枪枪身有三层同心无缝钢管组成。
a.已知条件:
吹炼过程氧枪冷却水量200t/h,冷却水进水压力位1.2MPa冷却水进水温度19℃
b.中心钢管直径的确定:
已知氧流量Q=543Nm3/min,氧气流在中心管内的流速按60m/s考虑,依据气体状态方程,在中心管内的实际状态下的氧流量为:
Q实=(1×543×290)/(273×7.9×60)=1.22m3/s
则中心管直径为d内=[(4×1.22)/(3.14×60)]1/2=0.161m=161mm;取为160mm
中心钢管的壁厚及直径根据标准无缝钢管产品规格选定为φ180×10mm
c.中层钢管和外层钢管直径的确定
对150t转炉冷却水耗量取200t/h的条件下:
进水环缝截面积:
F1=Q水/V进=200/(6×3600)=0.0093m2进水速度取6m/s
出水环缝截面积:
F2=Q水/V出=200/(7×3600)=0.0079m2出水速度取7m/s
已知中心钢管外径为187mm,则中层钢管的内径为
d中=[(4×0.0093)/3.14+0.182]1/2=0.21m=210mm;取为205mm
根据标准无缝钢管产品规格选定为φ219×7mm
同理,外层钢管内径为:
d外=[(4×0.0079)/3.14+0.2192]1/2=0.241m=241mm
根据标准无缝钢管产品规格选定为φ273×16mm
3.2原材料的供应及设备
A.散状料的供应
地下料仓容积的计算
本设计中:
轻烧白云石以及铁矿石为本地产,储存时间分别为3和3.5天;而石灰和萤石为外运,储存时间分别为0.4天和8天。
根据物料平衡计算,每炉钢分别需要白云石、铁矿石、石灰、萤石的质量分别为3.71t、1.48t、5.15t、0.45t。
由于该转炉冶炼周期为33min,故每天可以冶炼1440/33=44炉钢
白云石地面料仓容积为
根据公式
V=Qt/0.8Ύ
式中
Q:
一天需要的原料量;
t:
贮存天数;
0.8:
装满系数;
Ύ:
堆比重。
其中各种散状料的Y值由相关设计手册查出。
经计算可得
白云石的地下料仓容积为:
V白=3.71×44×3/(0.8×1.7)=360m3
可以设计为三个容积为120m3的料仓;
矿石地下料仓容积为:
V矿=1.48×44×3.5/(0.8×2.4)=119m3
可以设计为一个容积为120m3的料仓;
石灰地下料仓容积为:
V石=5.15×44×0.4/(0.8×1.0)=113m3
可以设计为一个容积为120m3的料仓;
萤石地下料仓容积为:
V莹=0.45×44×8/(0.8×1.7)=116m3
可以设计为一个容积为120m3的料仓;
故对于散状料共需要安排六个容积为120m3的料仓。
B.废钢的供应
(1)废钢料斗的尺寸
废钢料槽容积决定于每炉废钢装入量,大型转炉废钢加入量大,可分多个料斗加入,但最好一料斗加入.废钢料斗容积计算如下:
V=q/nρf(式3.10)
式中:
V:
废钢料斗容积,m3
q:
每炉加入废钢量,t
有前面的物料平衡可计算得150×7.31%=10.98t
N:
料斗装满系数,取0.8
ρ:
废钢堆积密度,采用轻废钢,取1.2t/m3
f:
每炉加入废钢的斗数,取1
代入上式可得料斗容积为
V=10.98/(0.8×1.2×1)=11.4m3,取12m3
废钢料斗参数:
废钢槽容积:
12m3
废钢槽最大载重:
40t
吊耳轴中心距:
2200mm
前后耳轴距:
4500mm
废钢槽外形尺寸:
7200×2000×2000mm
料槽重量25t
(2)废钢料坑容积计算
根据公式料坑容积
V=Qx/1.2Ύ(式3.11)
式中:
Q—车间日需废钢量。
1.2—装满系数。
Ύ—废钢堆比重,采用轻废钢,取1.2t/m3
x—废钢储存定额,本设计中内部废钢约占30%,储存2.4天,外购废钢占70%,储存7.5天。
故x=0.3×2.4+0.7×7.5=6
计算得:
Q=44×10.98×6/1.2×1.2=2013m3
故可以设置1个2000m3的废钢坑。
4.转炉车间烟气净化
OG法:
按经验公式
=G(
)×
式(4.1)
式中:
—炉气量(N
/h);
G—转炉后期铁水装入量(Kg),超装20%;
—铁水中含碳量(%);
—钢水最终含碳量(%)
=148000×1,2×(4.15-0.10)%×22.4/12×60/14.5×1.8=100004N
/h
②参数计算:
烟气量的计算:
采用未燃法,烟气量主要取决空气燃烧系数
。
本设计取
=0.08
根据物料平衡计算出燃烧后的烟气量:
V=[1+1.88α(CO%)]
(N
/h)式(4.2)
所以V=(1+1.88×0.8824×0.08)×100004=113276N
/h
假定燃烧后烟气仍残留氧气,则烟气成分为;
CO=(1-α)CO%V0/V=(1-0.08)×0.8824×100004/113276=71.7%;
CO2=(αCO%+CO2%)V0/V=(0.08×0.8824+0.098)×100004/113276=14.9%
N2=(1.88αCO%+N2%)V0/V=(1.88×0.08×0.8824+0.0065)×100004/113276=12.3%
O=0.5%V0/V=0.45%
烟气浓度修正:
根据回收中期,烟气量为炉气量的113276/100004=1.133倍,故进口烟气浓度应作修正,C0=0.106/1.133=0.094Kg/Nm3,
回收煤气量计算:
每吨钢产生的炉气量为:
1000×(4.15-0.1)%×22.4/12×1/(0.8824+0.1)=76.95/Nm3,
按烟气成倍率为1.133倍,则每吨钢产生的煤气量为1.133×76.95/=87.18Nm3,,考虑到前后期不回收煤气,定回收率为70%,则每吨钢可回收的煤气量为70%×87.18=61.03Nm3
5.主厂房的布置设计
转炉跨在车间中厂房最高、设备最多,多平台布置,是建筑结构复杂和投资最多的跨间。
主要布置转炉及其倾动机构、氧枪付枪系统、散料和铁合金加入系统、除尘系统等。
转炉横向位置的确定
计算转炉中心线与靠近原料跨的厂房纵向柱列中心线的距离a,a值应能保证原料跨吊车顺利向转炉加入废钢和兑入铁水,同时应满足布置氧枪升降机构的要求。
a值的计算式如下:
a=L1+L2-L3-L4式(5.1)
式中:
a—转炉中心线与厂房纵向柱列中心线的距离mm,
L1—转炉倾动到受铁位置(倾动角α=45°)时,转炉炉口内缘(新炉衬)与转炉中心线的距离,mm。
L1可以粗略计算如下:
L1=(10313.38-4900)×sin45o=3827mm,取为3830mm
L2—铁水罐内铁水全部兑入转炉(转炉倾角为104°左右)时,铁水罐嘴前沿到铁水罐耳轴中心线的水平距离,1200mm。
L3—吊车主钩的移动极限及安全距离,取600mm。
L4—吊车轨道中心线与厂房柱子中心线的距离mm。
本设计采用水泥立柱约1.830m。
故a=L1+L2-L3-L4
=3830+1200-600-1830=2600mm
转炉跨在炉后配置两台10t吊钩桥式起重机,以对设备进行检修。
为满足更换氧枪的需要,在转炉跨的厂房上部布置了一台10t吊钩桥式起重机,还配备一台280t铸造起重机,轨面标高54.000米。
在加料跨内主要完成兑铁水、加废钢和转炉炉前的工艺操作。
一般在加料跨的两端分别布置铁水和废钢工段。
铁水系统作业区进行高炉铁水的转运、向转炉兑铁水、铁水包的修砌和烘烤、铁水的脱硫和扒渣。
铁水系统主要设备有混铁炉、铁水吊车、铁水包运输称量车、脱硫和扒渣等设备。
废钢的供应有两种方式:
①在原料跨的一端设立废钢工段,废钢由火车或汽车运入,用电磁盘吊车装入废钢漏斗,称量后待用;
②当加入转炉的废钢量大时,特别是大型炼钢厂,在原料跨一段的外侧另建废钢间,在废钢间内加工处理后的废钢装入料斗并称重,然后料斗有地面或高架台车送入原料跨待用。
加料跨长度为炉前作业区、铁水系统作业区和废钢料斗吊运加料所需的长度总和。
加料跨的长、宽、高综合炉前、铁水、废钢三个系统工艺操作和设备布置,设计长度为240米。
加料跨厂房高度决定于其吊车的轨面标高,由于同一轨面要进行两个不同作业区的作业即要完成向转炉兑铁水、加废钢操作,加料跨吊车轨面标高在二者所需高度中取最高。
由于加料跨同一轨面要进行向转炉兑铁水、加废钢两种操作,所以应该取二者中较高的,因此加料跨轨道高度为25043mm
加料跨,取为25.5m,厂房全长240米,跨度27米,分三个区域,1~7号柱间为废钢存放配料区,配备一台100t电磁起重机,用于转炉加废钢作业,轨面标高为25.5米。
7~11号柱间设+9.065米平台,为转炉主操作区;11~21柱间为铁水准备区,设有铁水倒罐站铁水预处理设施。
加料跨配备1台280/80t铸造起重机和1台50t桥式吊钩起重机,担负铁水罐的吊运及铁水加入转炉的任务,加料跨9.065米转炉生产主操作平台为混凝土平台。
参考文献
[1]张凤泉,刘贵江,康永林,等.汽车用低合金钢的现状与发展[J],特殊钢,2003,24(4):
1~4.
[2]刘浏.复吹转炉强化冶炼工艺研究[J],钢铁,2004,39:
9~14.
[3]戴云阁:
现代转炉炼钢[M].沈阳:
东北大学出版社,1999,33~65.