轮毂加工实用工艺设计.docx
《轮毂加工实用工艺设计.docx》由会员分享,可在线阅读,更多相关《轮毂加工实用工艺设计.docx(16页珍藏版)》请在冰豆网上搜索。
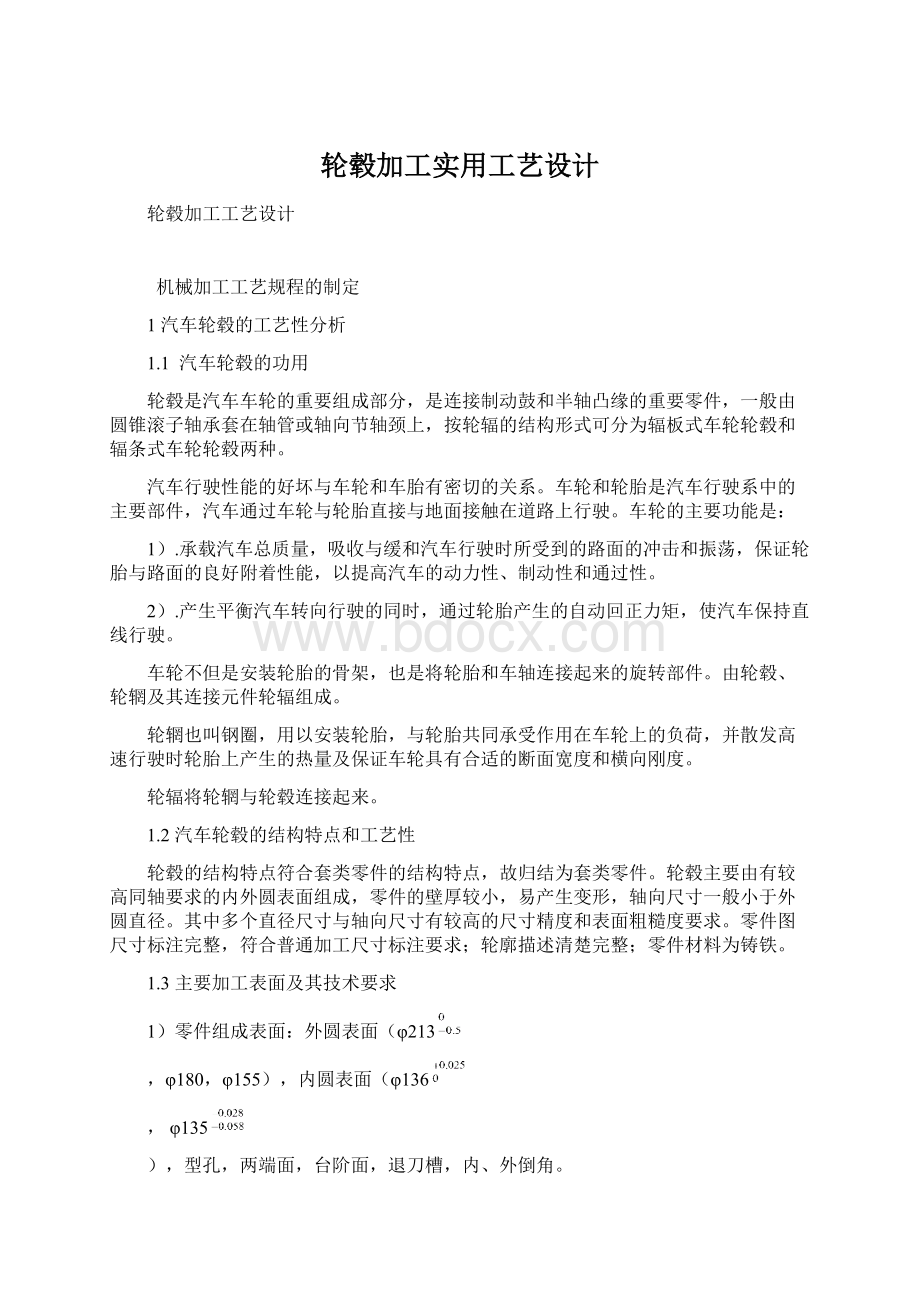
轮毂加工实用工艺设计
轮毂加工工艺设计
机械加工工艺规程的制定
1汽车轮毂的工艺性分析
1.1汽车轮毂的功用
轮毂是汽车车轮的重要组成部分,是连接制动鼓和半轴凸缘的重要零件,一般由圆锥滚子轴承套在轴管或轴向节轴颈上,按轮辐的结构形式可分为辐板式车轮轮毂和辐条式车轮轮毂两种。
汽车行驶性能的好坏与车轮和车胎有密切的关系。
车轮和轮胎是汽车行驶系中的主要部件,汽车通过车轮与轮胎直接与地面接触在道路上行驶。
车轮的主要功能是:
1).承载汽车总质量,吸收与缓和汽车行驶时所受到的路面的冲击和振荡,保证轮胎与路面的良好附着性能,以提高汽车的动力性、制动性和通过性。
2).产生平衡汽车转向行驶的同时,通过轮胎产生的自动回正力矩,使汽车保持直线行驶。
车轮不但是安装轮胎的骨架,也是将轮胎和车轴连接起来的旋转部件。
由轮毂、轮辋及其连接元件轮辐组成。
轮辋也叫钢圈,用以安装轮胎,与轮胎共同承受作用在车轮上的负荷,并散发高速行驶时轮胎上产生的热量及保证车轮具有合适的断面宽度和横向刚度。
轮辐将轮辋与轮毂连接起来。
1.2汽车轮毂的结构特点和工艺性
轮毂的结构特点符合套类零件的结构特点,故归结为套类零件。
轮毂主要由有较高同轴要求的内外圆表面组成,零件的壁厚较小,易产生变形,轴向尺寸一般小于外圆直径。
其中多个直径尺寸与轴向尺寸有较高的尺寸精度和表面粗糙度要求。
零件图尺寸标注完整,符合普通加工尺寸标注要求;轮廓描述清楚完整;零件材料为铸铁。
1.3主要加工表面及其技术要求
1)零件组成表面:
外圆表面(φ213
,φ180,φ155),内圆表面(φ136
,φ135
),型孔,两端面,台阶面,退刀槽,内、外倒角。
2)主要加工表面:
套类零件的主要表面为内孔。
内孔加工方法很多。
孔的精度、光度要求不高时,可采用扩孔、车孔、镗孔等;精度要求较高时,尺寸较小的可采用铰孔;尺寸较大时,可采用磨孔、珩孔、滚压孔;生产批量较大时,可采用拉孔(无台阶阻挡);有较高表面贴合要求时,采用研磨孔;加工有色金属等软材料时,采用精镗(金刚镗)。
3)主要技术要求:
孔与外圆一般具有较高的同轴度要求;端面与孔轴线(亦有外圆的情况)的垂直度要求;内孔表面本身的尺寸精度、形状精度及表面粗糙度要求;外圆表面本身的尺寸、形状精度及表面粗糙度要求等。
2确定生产类型
轮毂的生产类型为大批量生产。
3零件毛坯的选择
套类零件的毛坯主要根据零件材料、形状结构、尺寸大小及生产批量等因素来选。
孔径较小时,可选棒料,也可采用实心铸件;孔径较大时,可选用带预孔的铸件或锻件,壁厚较小且较均匀时,还可选用管料。
当生产批量较大时,还可采用冷挤压和粉末冶金等先进毛坯制造工艺,可在提高毛坯精度提高的基础上提高生产率,节约用材。
汽车后轮轮毂的最大孔径为φ194mm,孔径较大,因此毛坯选择为铸铁。
铸造是常用的制造方法,优点是:
制造成本低,工艺灵活性大,可以获得复杂形状和大型的铸件,在机械制造中占有很大的比重。
铸件的质量直接影响着产品的质量,因此,铸造在机械制造业中占有重要的地位。
4零件加工工艺规程的制定
4.1选择加工方案
φ136
mm、φ135
mm内孔,采用精镗达到精度及粗糙度要求;φ114mm孔以及外圆没有精度要求,因此铸面即可;台阶面及端面采用车削加工;圆周槽在立铣上完成;八个安装孔以及14个螺纹孔采用钻削。
考虑宝马M3轮毂的结构工艺特点,按照编制工艺规程的一些基本原则,同时考虑各种设备和加工方法的经济程度和不同精度要求表面的适当加工方法。
拟定了如下的加工工艺方案:
方案
工序号、工序名称和加工要求(尺寸及公差单位:
mm;表面粗糙度单位:
μm)
工序1、铸造毛坯
工序2、退火
工序3、粗车上端面。
粗车阶梯面。
保证:
两面的距离为130.75。
工序4、粗镗锥孔φ144-φ194孔。
保证:
两直径之间的垂直距离为32。
粗镗φ194孔。
保证镗削长度为15。
粗镗锥孔φ144-φ194孔。
保证:
两直径之间的垂直距离为32。
粗镗φ144孔。
粗镗φ136孔。
粗镗φ135孔。
保证:
镗削长度为34。
工序5、精镗φ136孔。
保证:
表面粗糙度为R1.6,上极限为+0.025,下极限为0。
精镗φ135孔。
保证:
表面粗糙度为R1.6,上极限为-0.028,下极限为-0.058。
切内外倒角2×45°。
工序6、粗车下端面。
保证:
上下端面距离为236。
上极限为0,下极限为-0.6。
工序7、粗镗φ144孔。
粗镗φ135孔。
粗镗φ136孔。
粗镗锥度为5的孔。
工序8、精镗φ136孔。
精镗φ135孔。
表面粗糙度为R1.6,上极限为-0.028,下极限为-0.058。
精镗φ136孔。
表面粗糙度为R1.6,上极限为+0.025,下极限为0。
精镗锥度为5的孔。
车外倒角4×45°。
车内倒角4×30°。
工序9、铣槽。
保证:
槽宽23,槽截面中心距为275。
工序10、钻8-φ20H8的通孔。
绞8-φ20H8的通孔。
保证:
倒角0.5×45°。
保证:
中心孔到定位中心距离137.5。
工序11、钻14-M12的螺纹孔。
保证:
加工孔中心到定位面距离77.5;
保证:
孔深36。
工序12、铣凸台。
保证:
与台阶面的距离为26,对称极限为±0.26
工序13、去除毛刺
工序14、清洗零件
将零件放入温度80-90摄氏度,含1.8-2.0%的苏打水中清洗并吹千。
工序15、热处理表面高频淬火及低温回火
工序16、对热处理后的零件进行磁粉探伤检查,检查热处理部位是否有裂纹等缺陷。
方案Ⅱ
工序1、备料。
工序2、铸造毛坯。
工序3、退火。
工序4、镗:
工位1.粗镗轴承孔φ131。
工位2.粗镗轴承孔φ132。
工位3.半精镗上轴承孔至φ135.5。
工位4.半精镗下轴承孔至φ134.5。
工位5.精镗。
保证:
表面粗糙度为R1.6,上极限为+0.025,下极限为0。
保证:
表面粗糙度为R1.6,上极限为-0.028,下极限为-0.058。
工序6、工位1.粗镗φ135孔。
工位2.粗镗锥孔至下端面,锥度为5°。
工位3.粗镗轴承底端面。
工位4.粗车上端面。
工位5.粗车凸台外圆。
工位6.粗车凸台小平面。
工序5、车:
工位1.粗车上端面。
工位2.粗车外圆。
工位3.粗车上法兰端面。
工位4.半精车上端面。
工位5.倒角。
工位6.半精车外圆。
工位7.半精车法兰端面。
保证:
上下端面距离为236。
上极限为0,下极限为-0.6。
保证:
凸台与台阶面的距离为26,对称极限为±0.26。
工序7、铣:
工位1.粗铣宽23的圆周槽。
工位2.精铣宽23的圆周槽。
保证:
槽宽23,槽截面中心距为275。
工序8、钻:
工位l.钻φ20孔。
工位2.绞φ20孔,倒角。
保证:
倒角0.5×45°。
保证:
中心孔到定位中心距离137.5。
工序9、钻:
钻φ10孔,攻螺纹。
保证:
加工孔中心到定位面距离77.5;
保证:
孔深36。
工序10、去毛刺及所有锐边倒钝。
工序11、清洗零件(退火处)
工序12、表面淬火保证硬度为HBS120~163
工序13、探伤:
保证热处理部位无裂纹等缺陷
工序14、清洗零件
工序15、最终检查
4.2确定加工顺序
加工顺序的确定按由内到外、由粗到精、由近到远的原则确定,在一次装夹中尽可能加工出较多的工件表面。
结合本零件的结构特征,可先加工内孔各表面,然后加工外轮廓表面。
由于该零件为单件小批量生产,走刀路线设计不必考虑最短进给路线或最短空行程路线,外轮廓表面车削走刀路线可沿零件轮廓顺序进行
4.3定位基准的选择
套类零件的主要定位基准毫无疑问应为内外圆中心。
外圆表面与内孔中心有较高同轴度要求,加工中常互为基准反复加工保证图纸要求。
零件以外圆定位时,可直接采用三爪卡盘安装;当壁厚较小时,直接采用三爪卡盘装夹会引起工件变形,可通过径向夹紧、软爪安装、采用刚性开口环夹紧或适当增大卡爪面积等方面解决;当外圆轴向尺寸较小时,可与已加工过的端面组合定位,如采用反爪安装,工件较长时,可采用“一夹一托”法安装。
4.4零件的热处理
考虑套类零件的结构工艺等特点,其材料可以为铸铁。
本零件的材料为铸铁HT250,铸造毛坯。
为了保证零件上配合和接触表面所需要的硬度,加工前应对这些表面进行退火以增加其硬度。
4.5拟订工艺路线
备坯→去应力处理→孔加工粗加工→孔半精加工→基准面加工→外圆等粗加工→外圆等半精加工→孔加工粗加工→基准面加工→安装空加工→螺纹孔加工→去毛刺→零件最终热处理→清洗→终检。
4.6选择各工序加工机床设备及工艺装备
表1.1工序流程表
工
序
号
工序名称
设备名称及编号
夹辅具
及编号
切削工具及编号
量具及编号
1
备料
2
铸造毛坯
3
退火
4
镗:
粗镗轴承孔φ131。
粗镗轴承孔φ132。
半精镗上轴承孔至
φ135.5。
半精镗下轴承孔至
φ134.5。
精镗。
镗床
专用夹具
镗刀
塞规
5
粗镗φ135孔。
粗镗锥孔至下端面,锥度为5°。
粗镗轴承底端面。
粗车上端面。
粗车凸台外圆。
粗车凸台小平面。
立式车床
专用夹具
镗刀
45°车刀
塞规
6
车:
粗车上端面。
粗车外圆。
粗车上法兰端面。
半精车上端面。
倒角。
半精车外圆。
半精车法兰端面。
转塔式
车床
专用夹具
车刀
游标尺
7
铣:
粗铣宽23的圆周槽。
精铣宽23的圆周槽。
铣床
专用夹具
立铣刀
游标尺
8
钻:
钻φ20孔。
绞φ20孔,倒角。
钻床
专用夹具
麻花钻
绞孔钻
卡尺
塞规
9
钻:
钻φ10孔,攻螺纹。
钻床
专用夹具
麻花钻
塞规
10
去毛刺及所有锐边倒钝
11
清洗零件(退火处)
12
表面淬火保证硬度为HBS120~163
13
探伤:
保证热处理部位无裂纹等缺陷
14
清洗零件
15
最终检查
我们通过查选刀具,可初步确定钻孔时的直径D,D可以使标准刀具最好,钻孔的切削余量我们可以在手册中查出。
因为属于大批量生产,所以量具选择卡尺,塞规较多,卡尺用来测轴或两面间距,塞规可测孔,槽等,详细情况量具设计中有介绍。
4.7确定各工序机械加工余量,工序尺寸及表面粗糙度
4.7.1加工余量的选择原则:
1)加工余量的选择原则应完全保证图纸的全部精度,光洁度等技术要求。
2)为了缩短工时,降低成本,应尽量采用最小的加工余量。
3)决定余量应考虑热变形等带来的尺寸变化。
4)综合考虑机床与夹具的精度及变形。
5)加工零件的尺寸大小及刚性好坏。
4.7.2确定加工余量的方法:
1)查表法。
2)经验估算法:
常用于单件小批量生产。
3)分析计算法:
材料十分贵重或少数大批量生产的工厂采用。
4.7.3公差的选择原则:
1)公差不应超出机床的经济加工精度。
2)零件的最后精度高的选小值。
3)批量大选小值。
采用查表法查文献[1]中表5-8确定的φ20的安装孔工序尺寸及公差如下:
表1.2φ20安装孔工序尺寸及公差表
工序名称
工序基本余量
工序经济精度
工序尺寸
工序尺寸及工差
钻孔
0
+0.2
19
φ19RA=12.5
铰孔
20.05~20.15
RA=3.2
4.8确定典型工序的切削用量及工序基本工时定额
4.8.1粗加工切削用量的选择原则
1)背吃刀量的选择:
依据加工余量和机床——夹具——刀具——工件系统的刚性来确定在保留半精加工,精加工必要的余量前提下应在工艺系统刚性和机床功率允许的情况下,尽可能取较大的背吃刀量,以减少进给次数。
2)进给量的选择:
选择进给量时应考虑机床进给机构的进给强度,刀杆尺寸,刀片厚度,工件直径和长度,在工艺系统的刚度和强度允许下可选大一些的进给量。
3)切削速度的选择:
粗加工的切削速度主要受刀具耐用度和机床功率的限制,合理的切削速度一般不需要精确计算,而根据生产实践经验和有关资料确定。
4.8.2精加工时切削用量的选择原则
1)背吃刀量的选择
精加工时,为保证零件表面粗糙度要求,背吃刀量一般取0.1~0.4㎜较为合适。
2)进给量的选择
精加工限制进给量提高的主要因素使表面粗糙度,走刀量f增大,虽有利于切屑,但残留面积高度增大,表面质量下降。
3)切削速度V的选择
切削速度提高时,切削变形减小,切削力有所下降,由此可见,精加工时应选择较小的吃刀深度和进给量f,并在保证合理刀具耐用度的前提下,选用尽量高的切削速度V。
4.8.3各工序的工艺卡片如下:
表1.3镗削加工工艺卡片
序
号
工艺说明
加工规定
夹辅具
刀具
量具
转速
(r/min)
进给量
(mm)
背吃刀量
(mm)
走刀次数
名称
名称
名称
1
粗镗轴承孔φ131
710
0.5
2
1
专用夹具
镗刀
塞规
2
粗镗轴承孔φ132
710
0.5
2.5
1
专用夹具
镗刀
塞规
3
半精镗上轴承孔至
φ135.5
1120
0.3
1.5
1
专用夹具
镗刀
塞规
4
半精镗下轴承孔至
φ134.5
1120
0.3
1.5
1
专用夹具
镗刀
塞规
5
精镗
1440
0.15
0.5
1
专用夹具
镗刀
塞规
表1.4车削加工工艺卡片
序
号
工艺说明
加工规定
夹辅具
刀具
量具
转速
(r/min)
进给量
(mm)
背吃刀量
(mm)
走刀次数
名称
名称
名称
1
粗车上端面。
710
1.2
3
1
专用夹具
车刀
游标
2
粗车外圆
710
1.2
3
1
专用夹具
车刀
游标尺
3
粗车上法兰端面
710
1.2
3
1
专用夹具
车刀
游标
4
半精车上端面。
1120
0.6
1
1
专用夹具
车刀
游标
5
倒角
1120
0.6
2
1
专用夹具
车刀
游标
6
精车外圆。
1440
0.6
1
1
专用夹具
车刀
游标
7
半精车法兰端面
1120
0.6
1
1
专用夹具
车刀
游标
表1.5铣削加工工艺卡片
序
号
工艺说明
加工规定
夹辅具
刀具
量具
转速
(r/min)
进给量
(mm)
背吃刀量
(mm)
走刀次数
名称
名称
名称
1
粗铣宽23的圆周槽。
710
0.1
3
1
专用夹具
立铣刀
游标
2
精铣宽23的圆周槽。
1120
0.07
1
1
专用夹具
立铣刀
游标
表1.6钻削加工工艺卡片
序
号
工艺说明
加工规定
夹辅具
刀具
量具
转速
(r/min)
进给量
(mm)
背吃刀量
(mm)
走刀次数
名称
名称
名称
1
钻φ20孔
1100
0.5
--
1
专用夹具
麻花钻
塞规
2
绞φ20孔,倒角
1100
0.5
--
1
专用夹具
麻花钻
塞规
4.8.4工时定额的确定
工序消耗的单件时间分为基本时间Tb,辅助时间Ta,布置工作地时间Ts,休息和生理需要时间Tr和准备终结时间Te
。
1.基本时间Tb,指直接切除工序余量所消耗的时间,可计算得出。
2.辅助时间TaTB=Ta+Tb(1.1)
3.布置工作地时间Ts:
取Ts=2%~7%TB
4.休息与生理需要时间Tr:
Tr=2%~4%TB
∴单位时间为:
Tp=Ta+TB+TS+Tr+Te(1.2)
5.基本时间的计算。
第一道工序根据实际加工情况切削用量取n=710r/minV=43/minf=0.5mm/r
由文献[1,123-128]表7-5得
Tb=L/fn=L1+L2/fn(1.3)
L1=(D-d1/2)ctgkr+(1~2)(1.4)
其中毛坯无孔时d1=0L2=1~4又
∵D=φ135mmd1=0
∴L1=(D1/2)ctgkr+1.5=135/2ctg710+1.5=8.14
L2=3
∴Tb1=L1+L2/fn=11.14/120=0.0928(min)
∴Tb1=5.6s
同理,可以算出其余工序的工时定额。
1.4.9工艺过程的技术经济性分析
拟定工艺路线的出发点,应当是在保证零件质量的前提下,力求提高生产率和降低生产成本。
因此,宜采用高效率机床组成的流水线或自动线。
在零件加工工艺规程制定中,两种方案都可将轮毂加工成型,但对于我们来说高效而经济的方案是我们的首选。
比较两种工艺方案的特点在于:
方案I整个加工过程比较复杂,具体工序分的不是很清楚。
方案II整个加工过程比较细致,在加工过程中,粗加工,精加工分的也比较细,保证了加工质量,提高了加工精度。
方案II对轮毂内孔的加工进行了粗精加工,保证了在使用过程中的质量精度,且对安装孔的加工也很细,保证了安装孔的精度。
综上各种条件因素的比较,选择II方案为最优方案。
结论
这次的毕业设计是检验我们四年所学知识的一个过程,培养我们动手能力,我们即将迈向社会,面对新的挑战,我们不仅要冷静下来用脑思考,而且要动手去做更是不可分离的一个部分。
学无止境,机械这门课验证了这句话,它适用丁那些不怕吃苦,勇住直前的人,不断的钻研才会有成就。
这次的设计是我们充分发挥自己想象力的一个好机会。
在这三个月的毕业设计中,我除了熟练掌握了CAD、CATIA绘图,还知道了如何设计能提高生产率,当然是以保证产品质量的前提下,还要涉及及到降低生产成本。
这次的设计只是一个开端,经过努力终于完成了该工艺设计,当中还有很多不足之处,希望老师给予指正,我会虚心的接受各位老师的意见。
谢辞
接近个一月工艺设计已结束,在这一个多月的设计过程中,遇到许多非常棘手的问题,我就去找专业课老师,经过老师给我细心的指导、讲解,使我闯出一道道难关,完成了这篇设计;我真心地谢谢你!
老师。
经过一个多月的设计,不但锻炼了自己独立思考,解决问题的能力,同时也加深了与同学之间的协作关系,未来的科研工作光靠一个、两个人是不行的,需要有一种协作精神,共同解决问难,完成课题。
通过这次设计,使我认识到一个设计人员的责任,事业心是非常重要的,同时也对自己所学的专业知识有了更深的理解,得到了巩固和发展。
设计过程是一个“三边”过程,即“边设计”,“边计算”,“边修改”的过程,这对我们查阅资料,手册的能力也大大提高了。
总之,这次设计无论是从心理素质上,还是从实践能力上都有一定提高,为今后走上工作岗位打下了良好的基础。
设计者:
袁文强
参考文献
[1]张耀辰.《机械加工工艺设计手册》.第1版.航空工业出版社.1987年12月
[2]陆剑中孙家宁.《金属切削原理与刀具》.第3版.机械工业出版社.1998年1月
[3]袁长良.《机械制造工艺装备设计手册》.第1版.中国计量出版社.1992年2月
[4]张玉刘平.《几何量公差与测量技术》.第3版.东北大学出版社.2006年8月
[5]李益民.《机械制造工艺设计简明手册》.第1版.机械工业出版社.1994年7月
[6]陈宏钧.《实用机械加工工艺册》.第1版.机械工业出版社.1996年12月
[7]双语教学研究组.《机械工程/双语教学》.第1版.辽宁民族出版社.2002年12月
[8]陈家瑞.《汽车构造》(下册).第1版.机械工业出版社.2000年5月
[9]任立昭,何人可.设计语义学探讨[J].广西工学院学报,2003,14(4).
[10]马学良.产品语义研究在工业设计的应用[J].山东大学,2008年
[11]姚贵升.汽车金属材料应用手册.北京理工大学出版社,2000年
[12]崔树平.汽车发动机构造与维修.武汉理工大学出版社,2008年08月
[13]汽车发动机与设计生产新工艺新技术与质量检验标准规范实用手册.
北方工业出版社,2007年07
[14]张平格.液体转动与控制.冶金工业出版社,.2009年01月
[15]余永宁.材料科学基础.高等教育出版社,2006年05月
[16]胡俊红,产品设计定位观[B],株洲工学院包装设计艺术学院,
2001.22
[17]祁娜,杨随先.面向产品个性化的设计方法初探[A],机械设计与
制造2010,
(2).
[18]]盛尚雄.工业产品造型设计中的直线分割【J].甘肃科学学报,2006,
(8)
[19陈览月.商品造型设计的抽象美与工艺美[J].包装世界,2000.
[20]姜斌,魏琳.轻工机械类产品形象设计的研究与实用[J].轻工机械,
2005,23(3):
17—19.
[21]王兴,基于用户知识的按键设计研究[D]合肥工业大学,20090301.
[22]刘志峰,刘光复.绿色设计[M].北京:
机械工业出版社,2000.