旋窑操作手基础知识.docx
《旋窑操作手基础知识.docx》由会员分享,可在线阅读,更多相关《旋窑操作手基础知识.docx(20页珍藏版)》请在冰豆网上搜索。
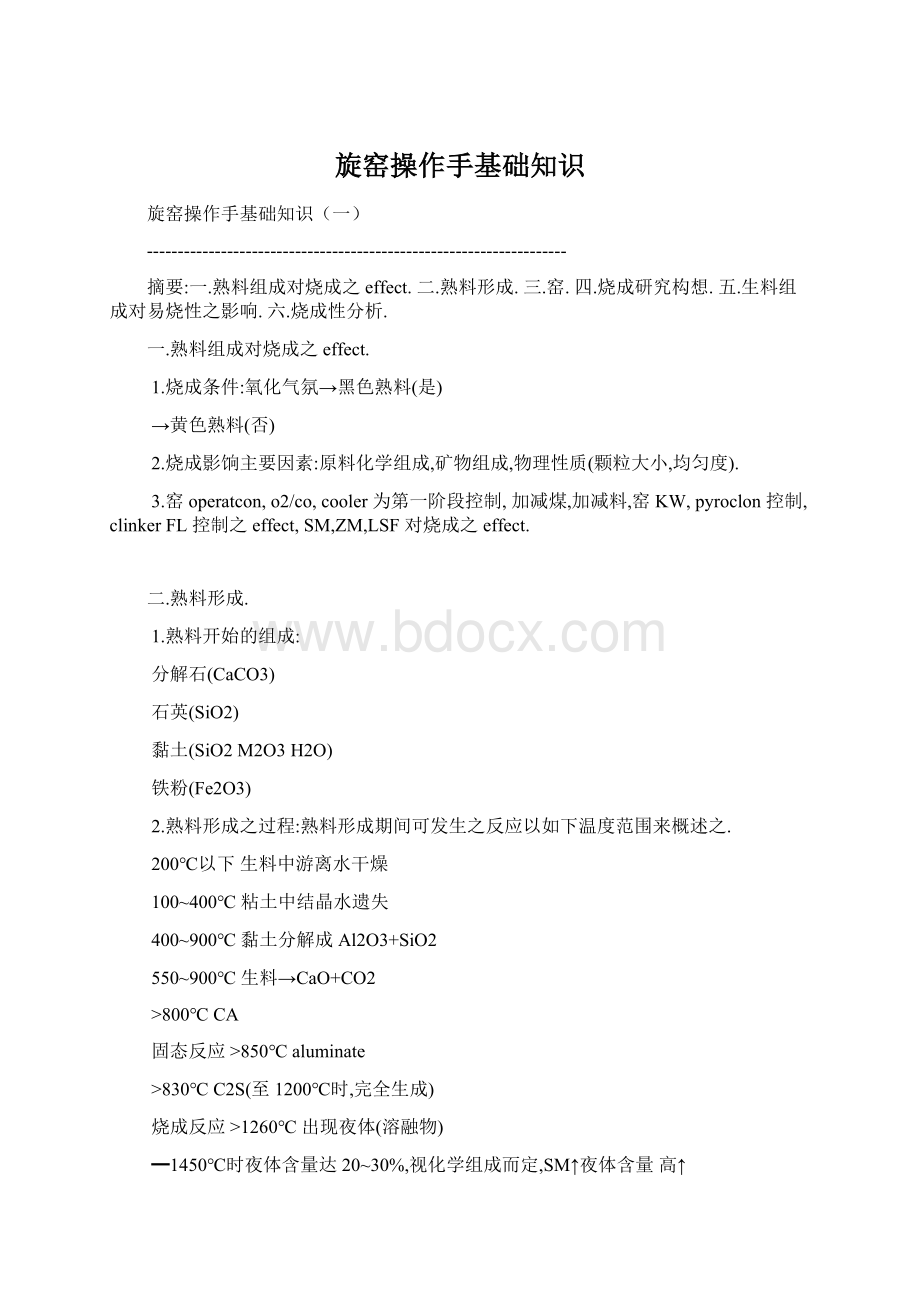
旋窑操作手基础知识
旋窑操作手基础知识
(一)
--------------------------------------------------------------------
摘要:
一.熟料组成对烧成之effect.二.熟料形成.三.窑.四.烧成研究构想.五.生料组成对易烧性之影响.六.烧成性分析.
一.熟料组成对烧成之effect.
1.烧成条件:
氧化气氛→黑色熟料(是)
→黄色熟料(否)
2.烧成影饷主要因素:
原料化学组成,矿物组成,物理性质(颗粒大小,均匀度).
3.窑operatcon,o2/co,cooler为第一阶段控制,加减煤,加减料,窑KW,pyroclon控制,clinkerFL控制之effect,SM,ZM,LSF对烧成之effect.
二.熟料形成.
1.熟料开始的组成:
分解石(CaCO3)
石英(SiO2)
黏土(SiO2M2O3H2O)
铁粉(Fe2O3)
2.熟料形成之过程:
熟料形成期间可发生之反应以如下温度范围来概述之.
200℃以下生料中游离水干燥
100~400℃粘土中结晶水遗失
400~900℃黏土分解成Al2O3+SiO2
550~900℃生料→CaO+CO2
>800℃CA
固态反应>850℃aluminate
>830℃C2S(至1200℃时,完全生成)
烧成反应>1260℃出现夜体(溶融物)
━1450℃时夜体含量达20~30%,视化学组成而定,SM↑夜体含量高↑
━1260℃烧成反应开始,料中主要含固体C2S,游离CaO及夜体,固体在夜体中形成溶液,使扩散反应加速,C2S+CaO→C3S.C3S是水泥中的主要矿物.
>1400℃液体组成,几乎生料中所有之Al2O3+Fe2O3皆在液体中了,CaO56%,SiO27%,Al2O323%,Fe2O314%.冷却期间液体熔融物结晶成C3A及C4AF.
3.烧成后的熟料矿物组成(具有水硬性)
硅酸三钙C3S━3CaO·SiO2
硅酸二钙C2S━2CaO·SiO2
铝酸三钙C3A━3CaO·Al2O3
铁铝酸四钙C4AF━4CaO·Al2O3·Fe2O3
它们的生成量视温度,滞留时间,冷却速度而定.
三.窑.
1.窑中各带之长度.
分解带过渡带烧成带冷却带
L/D━14~173~4D5D5~5.5D1.5D
L/D━10~111.5~2D4.5D3.5~4D1D
物料停留时间2"6"10"2"━20"
2.短窑脱酸度,应该保持90~95%,避免窑内废气温度过高造成进料室及C4下料筛结皮堵塞.脱酸度超标会造成窑内温度分布波动,引起结圈,结皮.而且,将缩短分解带长度,使过渡带长度过长,窑速上不去,形成懒火焰烧成,失去快速锻烧之优势,产量,品质无法达标.
3.熟料中MgO为2%时,熟料烧成温度降50℃,熟料中碱及硫也会降低.
>1260℃时,应该让绝大部份液相生成,以补快速锻烧.
4.短窑采用快速锻烧,烧成带相对较短,火焰温度较高,但较短.故熟料粉形成温度要高,原料必须能“吃火”.
5.RF:
(1).Labahn,otto.andB.KohihaascementEngineers′Handbook.
BauverlagGmbhWiesbadenandBerlin.4thed.1983.
(2).H.F.W.Tsylor.Cementchemistry.AcademilPremLtd.1990.
(3).Peray,KurtE.THERotaryCementKiln,2nded.ChemicalPublishing1986N.F.
6.影响预锻窑产量和品质的因素友有许多,如:
操作水平,原料及燃料品质,生料成份及预均化程度.
生料LSF高,窑内物料松散,不易燃烧及结窑皮,熟料f-CaO高使须提高温度,降低窑速及产量.
生料LSF低,窑内物料紧贴,易形成长厚窑皮,窑皮和结大球使窑的操作状态恶化.
所以保持生料的均衡稳定是保持旋窑易燃烧平衡的关键.
SM低的生料,熔剂性矿的总量增加,即物料的夜体量增加,易造成窑内结圈结球,使窑内操作恶化,破坏热平衡.
采用SM(2.50+-0.10),ZM(1.50+-0.10),LSF(91.5+-1.0)之配料,稳定声料品质,降低标准偏差.
SM高,使物料易燃性降低,因Al2O3+Fe2O3含量降低,不利CaO+SiO2燃结,但预锻窑中需热量少,而热量供应很充分,故可胜任熟料烧成.
IM高,使夜体黏度提高,但由于窑中火焰温度高,故也没有问题.
LSF高,生料中碳酸盐矿物含量低,减少熟料的形成热,可降低热耗量.MgO在燃结温度下是一种助燃剂,使烧成反应易于进行,但含量过高易使烧成带结球.SO3来自原料及燃料,其在1000℃时形成SO2气体,并在窑系统中生成CaSO4,K2SO4,易在窑后段造成结圈及结料.Na2O及K2O对熟料品质及窑操作均有不良影响,它们在烧成带开始处挥发,随窑气飘到预热机底段,在900℃下凝结下来与SO2,CO2及氯反应,碱份循环易在窑内造成结料及结圈.氯来自原料及煤炭,氯也会在高温下挥发与碱份形成氯化碱在窑中循环,造成预热机底段及窑尾结圈.适合燃煤用的生料若突然改燃油时,会造成难烧,这是因为缺少煤灰中的Al2O3及Fe2O3助燃剂之故.
四.烧成研究构想.
1.
(1).脱酸度一天一次,adj.煤量ofpyrodon.
(2).onomlthod一天一次,adj.窑operation.
2.配料方向:
(1).确保入窑生料一致稳定.
(2).熟料品质高,易燃性好,烧成带易结皮.
(3).连续一致的入窑生料成份,是窑适当操作的最重要因素.
五.生料组成对易烧性之影响.
生料易烧性:
生料在窑中转变成熟料之相对难易程度.可标示将生料烧成良好品质熟料所需之燃料量.
生料易烧性视生料组成而定,可用如下来表示:
1.硅率系数(SM).
SM=SiO2/Al2O3+Fe2O3
硅率系数增加将使易燃性变差,因为Al2O3及Fe2O3含量使得CaO及SiO2可在较低温度下化合.
名词定义 易烧:
生料须较少之燃料即可烧成熟料.
难烧:
生料须较多之燃料才可烧成熟料.
2.铝率系数(IM).
IM=Al2O3/Fe2O3
铝率系数越高,生料越难烧.当其它成份固定时,铝含量越高越容易烧,因铝可促进CaO及SiO2之‘反应速率’.熟料IM=1.4~1.6之间最佳,易烧性好,偏高时,会产生易烧性变差.
3.石灰石饱和系数(LSF).
LSF=CaO/(2.8SiO2+1.18Al2O3+0.65Fe2O3)
熟料LSF在0.99以上时,将相当难烧,且即使升高窑温,熟料中游离石灰含量也舞法降低,反而会损失及窑皮及火砖.LSF在一般值时,窑温升高,熟料中F.L.降低,此时可从F.L.含量来判断窑中temp是否适当,熟料F.L.以控制在0.8%较佳,一般0.4?
1.2%.LSF0.90以下将使熟料F.L.偏太低.
4.水硬系数(HM):
目前不常用了.
HM=CaO/(SiO2+Al2O3+Fe2O3)
5.液体含量:
熟料在1450℃烧成时将形成半液体状态,此熟料床粘稠外观是窑操作手观察烧成带时一项很重要的控制参数.液体%(1450℃)=3.0Al2O3+2.25Fe2O3+MgO+Na2O当量总碱份.或=1.13C3A+1.35C4AF+MgO+Na2O当量总碱份,其中MgO含量最高计至2%.熟料中液体含量通常介于25?
27.5%之间,与温度成正比观系.液体含量较高时,烧成带熟料床外观较粘,将使熟料较易烧成.
六.烧成性分析.
1.生料成份之改变对窑操作有很大的影响,故窑操作手应预先掌握入窑的生料之成份变化情况,如Ⅰ型生料改换成Ⅱ型生料.
2.入窑生料之粒度分布状况应尽量均一,减少变化.尤其粗颗粒的生料对烧成性及窑操作稳定性有很大影响.
*.Kuehls烧成指数(BI)=C3S/(C4AF+C3A)值越高表示越难烧.
*.Peray烧成参数(BF)=100(LSF)+10(SM)-3(MgO+Na2O当量总碱份).值越高表示越难烧.
*.经验烧成参数(BF)=x(LSF)+y(SM)-j(MgO+Ma2O当量总碱份).(针对各窑,然后用多重回归分析决定x,y,j值).
例:
熟料参数计算:
(%)
烧失量0.160.16
SiO222.0022.15
Al2O35.405.40
Fe2O33.403.40
CaO65.0064.75
MgO2.852.85
Na2O当量0.750.75
总碱份
SO30.300.30
总计99.8699.86
C3S55.3552.43
C2S21.4124.33
C3A8.568.56
C4AF10.3410.34
HM2.112.09
SM2.502.53
ZM1.591.59
LSF92.691.3
液体含量(%)26.3826.38
Kuehls烧成指数2.932.77
Peray烧成参数106.8105.8
旋窑操作手基础知识
(二)
--------------------------------------------------------------------------------
作者:
水泥网单位:
水泥网[2003-3-25]
关键字:
升重-过烧-脱酸度
摘要:
七.升重试验.八.熟料显微学.九.窑中反应带十.窑中结皮及结晶.十一.操作条件.十二.水泥化学上一些重要之计算式.
七.升重试验.
升重及游离石灰石含量可显示熟料的烧成温度是否适当,不过升重试验较迅速只须5分钟,而滚压则约1小时.熟料升重以6m~12mm,熟料颗粒在1L铁杯中之重量表示之.当熟料成份相同时,过烧熟料的升重高于正常熟料,烧成不良熟料的升重则低于正常熟料,烧成良好之熟料升重通常介于1.25Kg至1.35Kg之间,视成份而定
八.熟料显微学.
1.目的:
用来诊断窑烧成及冷却之变化.
Onomethocl:
窑烧成状况及预测水泥强度.
2.C2S+游离CaO+液体→C3S+缓慢冷却→C2S+CaO
过烧的熟料:
烧成带过长,熟料在烧成temp下暴露时过长,将使液体量增加,生成过多大颗粒C3S结晶,不列于水泥强度.相反地,烧成temp不够,将生成较小的C3S结晶且量较少,过量的C2S及f-CaO,也不利于水泥强度.
九.窑中反应带
1.生料组成份对易烧性之影响.
1.1烧成理想状况:
如Ono所述.
1.2生料参数介绍.
1.3生料参数与易烧性之关系.
2.煅烧带反应:
CaCO3→CaO+CO2
MgCO3→MgO+CO2
将生料完全锻烧脱酸是确保适当烧成熟料之必要条件.定期(如每日)测定C4F料脱酸度,有助烧窑控制.
3.过渡带:
在火焰尾端,料呈暗色,温度突升至烧成temp.
4.烧成带:
直接在火焰下端,熟料矿物生成,C3S,C2S,C3A,C4AF,此时中间区域由于热反应,其中料流temp最高且最粘稠.
5.冷却带:
通常在窑出口3?
6mm内.冷却带长度应适中,使窑落口熟料temp保持在约1370℃,则高温度熟料落入冷却机第一室中将料快速冷却,有利于熟料品质及研磨性.
十.窑中结皮及结晶.
控制烧成带的结皮良好,有助延长耐火砖寿命,增加窑运转效益.
*.窑皮的平衡条件:
熟料液体固化温度
(1)=窑皮表面温度
(2).
当
(1)<
(2)时窑皮熔解脱落
(1)>
(2)时继续生成窑皮
*.液体含量高的熟料较容易生成窑皮.
*.热传导好的耐火砖较容易生成窑皮.(因窑皮的temp较低)
*.火焰形状将影响窑皮表面temp,对窑皮的形成有决定性的影响:
1.火焰过短,有力且宽,会在短截面中释放出大量热熔蚀窑皮.
2.长焰有利于生成窑皮.
3.短焰有利于烧成操作,故应控制适当的短焰,以不熔蚀窑皮为原则.
十一.操作条件.
*.熟料烧成指针:
在一给予的生料量时,藉改变窑速,用煤量及ID风车转速或三者的组合来维持适当的烧成带温度及固定的进料室温度.
依重要性,可列为下述四项基本定律.
1.随时保持设备及人员安全.
2.制造烧成良好的熟料(FL及升重正常).
3.连续稳定的操作旋窑(不须或仅略微改变控制条件).此时窑速,烧成带temp及进料室temp在长时间内变动甚微.
4.以最佳的燃料效率获得最高产量.
*.在Kiln运转顺利期间,每半小时观察烧成带一次,应在Kiln条件变化发生时就作出调整.
*.观察Clinker外观:
良好烧成之熟料是黑色,且烧成温度越高,熟料颗粒越大.
过烧之熟料颗粒较大,升重较高,FL较低,较密实少孔隙,较黑.烧成不良之熟料则相反,较小多砂.
*.火焰颜色应为橘黄色,若变动时应找出原因且调整之.
暗红=======》冷
橘黄=======》正常
白=======》热
注:
1.暗料与亮料在火焰下分界点之改变是烧成带条件变化之先兆.在正常操作下,分界点在火焰下距焰尖约1/4处,若它往窑出口移动表示生料较难烧,料量增加,烧成带温度降低,火焰长度变短.若它往窑进口移动表示生料易烧,料量减少,烧成带温度上升,火焰长度变长且有充分温度.窑操作手可籍稍微调整窑用煤量使分界点维持在适当位置.此分界点不得超过火焰下1/2长度,当太靠近窑出口时,窑操作手应改变火焰长度(若必要时)使分界点与火焰恢复至原来关系.
2.来自冷却机之燃烧空气.当烧成不良之clinker进入cooler后,二次空气中将夹杂大量粉末入窑而干扰烧成带视觉,此时二次空气温度较低会使煤粉燃点更深入kiln中,窑操作手应设法观察火焰下方及尾端来作调整措施,而不因烧成带前端颜色受粉末影响变暗就断定烧成带温度不足.
3.窑皮颜色.在正常操作下,窑皮颜色介于黄,白之间,当变成橘红色或黄色表示烧成带温度降低.当大量生料粉使窑皮温度快速降低时窑操作手应减慢窑速,避免烧成不良clinker.维持或重建窑皮以保护耐火砖及窑壳,避免过热受损是窑操作手之重要责任.
观察烧成带下述项目w之变化对温度之影响:
(1).熟料颜色;
(2).熟料大小;
(3).火焰附近熟料之行进状况;
(4).火焰尾端生料床外观;
(5).暗料与亮料之分界点位置;
(6).二次空气外观;
(7).窑皮状况;
(8).火焰形状及颜色.
及早侦测任何变化并逐步渐进式的采取调整对策是烧窑的准则.
三次管及窑尾O2含量应介于0.7-3.5%之间,而1-1.5%O2是最理想的操作状况.
注:
1.砂料使烧成带变亮时之对策:
略增O2含量,略减用煤量,以提高烧成带temp,降低窑速.
2.煤灰软化温度低及煤灰中铁份含量高之煤较易结圈,故应磨得较细.
3.窑尾温度过高之微兆:
(1).窑在连续操作中,排气中O2含量偏高.
(2).烧成带过长,烧成容易,熟料在火焰端很远就形成.
(3).耗煤量偏高.
4.窑尾温度过低之微兆:
(1).窑长期操作时,排气中O2偏高.
(2).因生料锻烧不完全就进入烧成带,使烧成不易.
十二.水泥化学上一些重要之计算式.
1.水硬系数(HM).
HM=CaO/SiO2+Al2O3+Fe2O3
2.铝率系数(IM).
IM=Al2O3/Fe2O3
3.石灰饱和度(LSF).
(1).生料及熟料适用.
LSF=CaO*100/2.80SiO2+1.18Al2O3+0.65Fe2O3
(2).水泥适用.
LSF=(CaO-0.70SO3)*100/(2.80SiO2+1.18Al2O3+0.65Fe2O3
4.液体含量.
当熟料在1450℃烧成时,将有以下的液体含量:
液体(%)=1.13C3A+1.35C4AF+MgO+Na2O+K2O
5.Bogue公式.
水泥中化合物成份计算:
IM>0.64
C3S=4.07CaO-7.6SiO2-6.72Al2O3-1.43Fe2O3-2.85SO3
C2S=2.87SiO2-0.754C3S
C3A=2.65Al2O3-1.69Fe2O3
C4AF=3.04Fe2O3
6.Na2O当量总碱份(TotalAlkaliesasNa2O).
总碱份=Na2O+0.658K2O
7.预热机脱酸度(PercentofDecomposition)
C=100(A-B)/A(100-B)
其中A=预热机称量机上生料烧失量百分比.
B=预热机某段旋风筒下料管生料烧失量之比.
C=该段旋风筒之脱酸度百分比.
新型干法生产线中央控制操作人员理论培训提纲
1、水泥生产的基本理论:
熟料煅烧看火的基本原理,窑速控制与熟料质量;
2、新型干法水泥生产线的操作规程,中央控制操作人员技能知识。
3、预分解窑与传统回转窑的区别,中控操作原理及各种工艺参数的控制范围,
如何做到精细化操作等。
4、预分解窑正常窑况的操作与故障处理:
(1)新型干法水泥生产线的重点设备:
立磨、预分解系统、篦冷机等的工作原
理及操作与维护;
(2)、如何提高预分解窑产、质量、降低能耗以及采取的相应措施;
5、中控操作团队的建设,如何做好信息的及时传递、指挥、协调各工种之间的配合工作等。
一、预分解窑与传统回转窑的区别,中控操作原理及各种工艺参数的控制范围,
如何做到精细化操作等。
预分解窑的特点是在悬浮预热器与回转窑之间增设一个分解炉或利用窑尾上升烟道,原有预热器装设燃料喷入装置,使燃料燃烧的放热过程与生料的碳酸盐分解的吸热过程,在其中以悬浮态或流化态下极其迅速地进行,从而使入窑生料的分解率从悬浮预热窑的30%左右提高到85%~95%。
这样,不仅可以减轻窑内煅烧带的热负荷,有利于缩小窑的规格及生产大型化,并且可以节约单位建设投资,延长衬料寿命,有利于减少大气污染。
预分解窑是在悬浮预热窑基础上发展起来的,是悬浮预热窑发展的更高阶段,是继悬浮预热窑发明后的又一次重大技术创新。
1悬浮预热技术
悬浮预热技术是指低温粉状物料均匀分散在高温气流之中,在悬浮状态下进行热交换,使物料得到迅速加热升温的技术。
1.1悬浮预热技术的优越性
悬浮预热技术的突破,从根本上改变了物料预热过程的传热状态,将窑内物料堆积态的预热和分解过程,分别移到悬浮预热器和分解炉内在悬浮状态下进行。
由于物料悬浮在热气流中,与气流的接触面积大幅度增加,因此传热速度极快,传热效率很高。
同时,生料粉与燃料在悬浮态下均匀混合,燃料燃烧产生的热及时传给物料,使之迅速分解。
所以,由于传热、传质迅速,大幅度提高了生产效率和热效率。
1.2 悬浮预热器的构成及功能
目前在预分解窑系统中使用的悬浮预热器主要是旋风预热器,构成旋风预热器的热交换单元主要是旋风筒及各级旋风筒之间的连接管道(换热管道),图6-3。
悬浮预热器必须具备使气、固两相能充分分散均布、迅速换热、高效分离三个功能。
1.3旋风预热器是主要的预热设备
旋风预热器是由旋风筒和连接管道组成的热交换器。
现在一般为五级预热器,也有六级预热器。
换热管道是旋风预热器系统中的重要装备,它不但承担着上下两级旋风筒间的连接和气固流的输送任务,同时承担着物料分散、均布、锁风和气、固两相间的换热任务,所以,换热管道除管道本身外还装设有下料管、撒料器、锁风阀等装备,它们同旋风筒一起组合成一个换热单元。
一次换热是达不到充分回收废气余热的目的,必需进行多次换热,即预热器要多级串联。
旋风筒的作用主要是气固分离,传热只占6%~12.5%。
气固间的热交换80%以上是在入口管道内进行的,热交换方式以对流换热为主。
当dp=100µm时换热时间只需0.02~0.04s,相应换热距离仅0.2~0.4m。
因此,气固之间的换热主要在进口管道内瞬间完成的,即粉料在转向被加速的起始区段内完成换热。
最高一级旋风筒的分离效率决定着预热器系统的粉尘排出量,提高它的分离效率是降低外部循环的有效措施,因此一级旋风筒一般为并联的双旋风筒。
由于在换热管道中,生料尘粒与热气流之间的温差及相对速度都较大,生料粉被气流吹起悬浮,热交换剧烈,因此从理论计算及实践均证明,生料与气流的热交换主要(约80%以上)在连接管道内进行。
各种类型的旋风预热器的换热管道风速,一般选用12~18m/s。
为了使生料能够充分的分散悬浮于管道内的气流中,加速气固之间的传热。
必须采取以下措施:
(1)在生料进入每级预热器的上升管道处,管道内应有物料分散装置,一般采用板式撒料器(如图6-4所示)和箱式撒料器。
撒料装置的作用在于防止下料管下行物料进入换热管道时的向下冲料,并促使下冲物料冲至下料板后飞溅、分散。
装置虽小,但作用极大。
(2)选择生料进入管道的合适方位,使生料逆气流方向进入管道,以提高气固相的相对速度和生料在管道内停留时间。
(3)两级旋风筒之间的管道必须有足够的长度,以保证生料悬浮起来,并在管道内有足够的停留运行距离,充分发挥管道传热的优势。
(4)旋风筒下料管道上设有锁风翻板排灰阀,要求结构合理、轻便灵活不漏风,生料能连续卸出,有料封作用。
锁风翻板排灰阀(简称锁风阀)是预热器系统的重要附属设备。
它装设于上级旋风筒下料管与下级旋风筒出口的换热管道入料口之间的适当部位。
其作用在于保持下料管经常处于密封状态,既保持下料均匀畅通,又能密封物料不能填充的下料管空间,最大限度地防止由于上级旋风筒与下级旋风筒出口换热管道间由于压差容易产生的气流短路、漏风,做到换热管道中的气流及下料管中的物料“气走气路、料走料路”,各行其路。
这样,既有利于防止换热管道中的热气流经下料管上窜至上级旋风筒下料口,引起已经收集的物料再次飞扬,降低分离效率;又能防止换热管道中的热气流未经同物料换热,而经由上级旋风筒底部窜入旋风筒内,造成不必要的热损失。
2预分解技术
预分解(或称窑外分解)技术是指将已经过悬浮预热后的水泥生料,在达到分解温度前,进入到分解炉内与进入炉内的燃料混合,在悬浮状态下迅速吸收燃料燃烧热,使生料中的碳酸钙迅速分解成氧化钙的技术。
预分解技术发明后,熟料煅烧所需的60%左右的燃料转移到分解炉内,并将其燃烧热迅速应用于碳酸盐分解进程,这样不仅减少了窑内燃烧带的热负荷,并且入窑生料的碳酸盐分解率达到85%~95%左右,从而大幅度提高了窑系统的生产效率。
2.1分解炉的作用
分解炉的作用是完成燃料的燃烧、换热和碳酸盐分解。
由于生料与燃料在炉内充分分散混合和均布,使得燃料能在炉内迅速完全燃烧,并把燃烧热及时传递给物料,生料中的碳酸盐组分能迅速吸热、分解,放出的二氧化碳能及时排除。
所有这些要求,取决于炉内气、固流动方式,即炉内流场的合理组织。
分解炉内气流运动的基本形式有旋涡式、喷腾式、悬浮式及流化床式。
在这四种形式的分解炉内,生料及燃料分别依靠“涡旋效应”、“喷腾效应”、“悬浮效应”和“流态化效应”分散于气流中。
由于物料