层压工艺.docx
《层压工艺.docx》由会员分享,可在线阅读,更多相关《层压工艺.docx(12页珍藏版)》请在冰豆网上搜索。
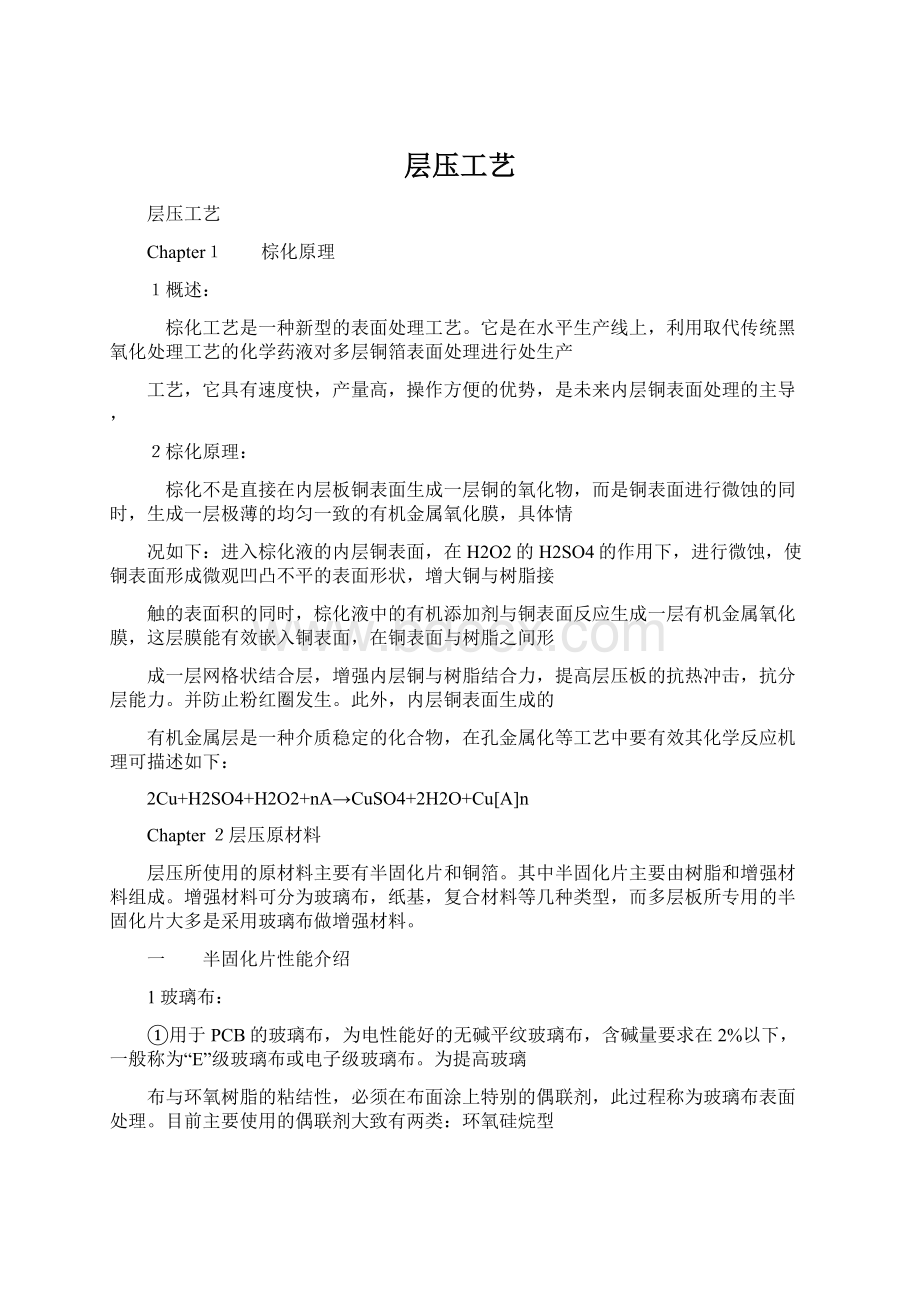
层压工艺
层压工艺
Chapter1 棕化原理
1概述:
棕化工艺是一种新型的表面处理工艺。
它是在水平生产线上,利用取代传统黑氧化处理工艺的化学药液对多层铜箔表面处理进行处生产
工艺,它具有速度快,产量高,操作方便的优势,是未来内层铜表面处理的主导,
2棕化原理:
棕化不是直接在内层板铜表面生成一层铜的氧化物,而是铜表面进行微蚀的同时,生成一层极薄的均匀一致的有机金属氧化膜,具体情
况如下:
进入棕化液的内层铜表面,在H2O2的H2SO4的作用下,进行微蚀,使铜表面形成微观凹凸不平的表面形状,增大铜与树脂接
触的表面积的同时,棕化液中的有机添加剂与铜表面反应生成一层有机金属氧化膜,这层膜能有效嵌入铜表面,在铜表面与树脂之间形
成一层网格状结合层,增强内层铜与树脂结合力,提高层压板的抗热冲击,抗分层能力。
并防止粉红圈发生。
此外,内层铜表面生成的
有机金属层是一种介质稳定的化合物,在孔金属化等工艺中要有效其化学反应机理可描述如下:
2Cu+H2SO4+H2O2+nA→CuSO4+2H2O+Cu[A]n
Chapter2层压原材料
层压所使用的原材料主要有半固化片和铜箔。
其中半固化片主要由树脂和增强材料组成。
增强材料可分为玻璃布,纸基,复合材料等几种类型,而多层板所专用的半固化片大多是采用玻璃布做增强材料。
一 半固化片性能介绍
1玻璃布:
①用于PCB的玻璃布,为电性能好的无碱平纹玻璃布,含碱量要求在2%以下,一般称为“E”级玻璃布或电子级玻璃布。
为提高玻璃
布与环氧树脂的粘结性,必须在布面涂上特别的偶联剂,此过程称为玻璃布表面处理。
目前主要使用的偶联剂大致有两类:
环氧硅烷型
和氨基硅烷型。
上述两类偶联剂经不同的化学处理后,其性能会有较大的差异,各玻璃布厂家在新型偶联剂的研究,开发方面都投资大
量的人力、物力、财力。
因为这是玻璃布性能好坏的关键所在。
②玻璃纤维布的组成:
SiO2:
%Al2O3:
%CaO:
%MgO:
%Na2O:
%B2O3:
8%
③玻璃纤维的性能,玻璃纤维作为增强材料与其它常用材料相比有以下优点:
拉伸强度与弹性模量高。
伸长率小,尺寸稳定性好,无蠕变现象。
不着火,而温达550℃。
耐微生物侵蚀,耐各种化学试剂和溶剂腐蚀,耐蚀性好。
不吸潮,电性能好。
应用广泛。
2环氧树脂:
①环氧树脂俗称万万能胶,可想而知其粘结性能特别好,用于覆铜箔层压板的环氧树脂是阻燃性的溴化环氧树脂,其化学结构如下:
BrCH3BrCH3
CH2—CH—CH2—O——C——O————CH2—CH—CH2—O——C——O—CH2—CH—CH2
OBrCH3BrnOHCH3O
②环氧树脂溶解:
用于覆铜板的环氧树脂,在使用前其本身是线型体,必须借助于固化剂,将树脂的环氧基[-CH-CH2]打开,使线型环氧树脂分子交联成
空间网状结构,从而形成不溶不熔的固化物,才能达到使其交联,环氧树脂按一定配比溶于溶剂中,作用是:
把所有配料按一定比例均
匀的混在一起。
环氧树脂原材料粘度太高,必须降低其粘度才能达到在生产过程中对玻璃布的浸润性。
3半固化片的型号:
目前使用的主要有四种:
型号
7628#
2116#
1080#
106#
厚度
4半固化片的存在状况:
A阶段:
环氧树脂处于液体状态,在室温下,能自由流动。
B阶段:
玻纤布用树脂浸渍固化至中间阶段,处于固态,即从A阶段到B阶段,加热条件下,又能恢复到液体状态。
C阶段:
树脂再次熔化,浸渍玻璃布,最后固化,即从B阶段到C阶段。
三种状态的取应性:
A→B→C。
B与C之间不可逆性,至C
阶段后,固化后不再熔化。
5半固化片的特性指标:
多层板所用半固化片的主要外观要求有:
布应平整、无油污、无污迹、无外来杂质或其它缺陷、无破裂和过多的树脂粉末,但允许有微
裂纹。
半固化片四种性能指标:
含胶量(RC)、流动度(RF)、凝胶时间(GT)、挥发物含量(VC)。
①树脂含量:
指树脂在半固化片中所占重量百分数,一般树脂含量为45~~65%之间,其含量随玻璃布厚度增加而减小,对于半固化片,
其含量大小直接影响半固化片的介电常数、击穿电压等电气性能及尺寸稳定性,一般含量高的、介电常数低、击穿电压高,但尺寸稳定
性差、挥发物含量高。
②树脂流动度:
树脂中能流动的树脂占树脂总量的百分数。
树脂流动度一般在25~~40%之间,其含量随玻璃布厚度增加而减小,流动度高,在层压过
程中树脂流失多,容易产生缺胶、贫胶现象;流动度低,容易造成填充图形间隔困难,产生气泡,空洞等现象。
③凝胶时间:
指树脂在加热情况下,处于液态流动的总时间,凝胶时间一般为140~~190s之间,凝胶时间长,树脂有充分时间来润湿图形,并能有效
地填满图形,有利于压制参数的控制。
④挥发物含量:
挥发物含量通常是指浸渍玻璃布时树脂所用的一些小分子溶剂在预固化时残余物,挥发物与半固化片的百分重量称为挥发物含量,一般
挥发物含量≤%。
挥发物含量高,在层压时易形成气泡,造成树脂泡沫流动。
6半固化片性能介绍:
①树脂材料:
Tg(玻璃化转变温度)高的树脂其固化前熔融状态粘度大,固化在固化阶段收缩较大,但是一旦固化完成之后,其整体尺寸稳定性好,
易于控制。
树脂是作为绝缘物填充各粘结作用物质而存在于覆铜箔层压材料和B阶段粘结片之中,这就是说树脂是填充并粘结玻璃纤维
的主格细缝中,如果残留在玻璃纤维布上很薄,仅起层间粘结作用时,在这种情况下,尽管树脂尺寸收缩较大,但它受到玻璃布机械阻
挡或束缚作用,这样玻璃纤维伸缩是主要的,所以层压材料尺寸稳定性在很大程度上是取决于玻璃纤维布。
②玻璃布材料:
玻璃丝直径和捻线越粗,其刚性越好,抗树脂伸缩变化越强,因而其组成的层压板基材的尺寸稳定性越高。
玻璃布和经、纬方向其尺寸稳定性也不同,由于形成玻璃布过程中经线方向受到强力伸展作用而使尺寸变长,而纬线受拉伸作用要小得
多,通常经线方向尺寸收缩要比纬线方向收缩大30~~50%。
7半固化片的选用原则及规律:
①使用半固化片的原则:
在层压时树脂能填满印制导线间的间隙。
能在层压中排除叠片间空气和挥发物。
能为多层板提供必须的树脂/玻璃布比率。
②如果树脂预固化程度低(凝胶时间长),层压时树脂流失就多,如果树脂中挥发物含量高,层压时树脂含量高,树脂的流失也相应多,
如果树脂含量高,层压中流失也多。
预固化程度低的树脂,其原始粘度也小,受压后易外溢。
层压时挥发物将因受热而从树脂中逸出,并推动树脂一起外流。
层压时树脂流失(B%)与半固化片的原始树脂净厚度(ho)和层压时某一瞬间的树脂净厚度h有如下关系:
B=(1-h/ho)*100%
B随ho增大而增大。
③选用不同半固化片对生产问题的预防性。
选用树脂含量高的半固化片,可以预防基板白斑。
选用树脂含量高的半固化片,可以预防板面凹坑产生。
选用树脂含量,流动度小的半固化片,可以预防层间滑移。
8半固化片的存放:
①温度的影响:
目前采用的半固化片是一种潜伏性固化剂和固化促进剂的树脂体系构成,在常温下较稳定。
温度过低,空气中水分在半固化片上凝聚成
吸附水,这种吸附水能促进存放的半固化片进一步的聚合,使用时导致层压或热风整平中分层起泡。
实践证实,在10~~21℃范围内存
放一个月或更长一段时间,半固化片未见有明显的特性变化。
②湿度变化:
存放环境的湿度会使半固化片的特性明显的变化。
半固化片明显吸湿。
半固化片历经高低温度循环,未能除尽水分,证明在半固化片上存在着物理和化学的吸附水,吸附水先是抑制
固化,后是加速树脂固化。
水主要是入侵树脂体系中各种不同物质之间的界面,存在着水对界面的冲击。
③湿度对半固化片各特性的影响如下:
对挥发物含量的影响,在大气环境中存放将会使半固化片的挥发物含量增加。
对流动性的影响:
在相对湿度为20~~40%存放时,流动性稍有增加。
在相对湿度为40~~70%存放时,流动性大幅度增加。
在相对湿度为70~~90%存放时,流动性仅有轻微增加趋势。
半固化片相对湿度为90%时只需15min,流动就显著增加,再继续存放较长时间,增加就不明显了。
另外,粘性时间短(B阶段程度高)的半固化片,其流动性对湿度的敏感性也大,粘性时间长的半固化片湿度对其影响也小。
在半固化片中树脂的B阶段程度较高,玻璃布的编织密度愈高,流动性受湿度的影响也愈大,因为界面的水分起着“润滑剂”作用,增加了流动性。
对凝胶时间的影响。
湿度对凝胶时间的影响不大,常为±5s测量误差所掩盖。
9使用半固化片的注意事项:
①在进行层压时,操作者必须戴上洁净的棉纱手套或尼龙手套,以防止手沾污粘合面。
②操作中,如果发现半固化的树脂层中有白色的毛状裂纹,这种裂纹一般是在搬运和操作中产生的,在层压时,会在树脂融化,流动过程中自然消失,因此不会影响产品质量。
折良、痕处玻璃布未断裂或损坏,该折痕也会因树脂融化,流动而完全消失。
如果折痕处,玻璃布已断裂,层压中半固化片将会由于树脂的高压流动而从断裂处被整个撕裂,从而该区域成为仅有树脂而无玻璃布的隐患区,这种半固化片严禁使用。
③通常批量不同的半固化片不能混合使用,除非它们具有相同的预固化流动性能。
然而当压制件很厚,加热板又大时,可在层压时预先选定的半固化片来插入使用。
二铜箔
铜箔可分为压延铜箔和电解铜箔两大类。
1压延铜箔:
就是将铜板经过多次重复辊轧制成的,一般毛箔生产完成后,还要进行粗化处理,压延铜箔在刚性覆铜箔板上使用极少,其优点为
耐折性和弹性系数大于电解铜箔,适用于挠性覆铜箔板,它的铜的纯度(99。
9%)高于电解铜箔(98%),在毛面上比电解铜箔平滑,有利于电信号的快速传递。
2电解铜箔:
①电解铜箔是通过专用电解机,在图形阴极滚筒上上生产出来的。
对电解铜箔主要有以下技术性能要求:
厚度、抗拉强度、剥离强度、抗高温氧化性、铜箔的电阻系数。
其它要求:
延伸率、耐折性、硬度、弹性系数、高温延伸性、表面粗糙度、蚀刻性、可焊性、UV油墨的附着性等。
②常用铜箔标准厚度为18um、35um、70um三种。
3牛皮纸:
牛皮纸在层压过程中起缓冲作用,其目的是确保层压过程中温度传递压力分布的均匀性。
牛皮纸放在上下加热板和上下模钢板之间,通
常热放、一次、二次各8张,每层压一次换8张,新鲜的牛皮纸紧靠模钢板。
Chapter3层压对位
一定位原理
1概述:
电路图形的对位系统贯穿多层照相底版制作、图形转移、层压、钻孔等工艺步骤的一个共性问题。
影响多层板层间定位精度的因素很多,主要的因素有:
照相底版的尺寸稳定性。
基材的尺寸稳定性。
定位系统的精度。
加式设备精度、操作条件(温度、压力)和生产环境(温度和湿度)。
电路设计结构,布局的合理性。
层压模板与基材的热性能的匹配。
参考数据:
FR-4的热膨胀系数为13~~15ppm/℃。
不锈钢A1S1300或A1S2400热膨胀系数为11~~16ppm/℃。
42CrMo4不锈钢热膨胀系数为20~~300℃时为12。
9ppm/℃。
2定位原理:
即两点定线、三点可定面、多层板的定位有销钉定位和无销钉定位。
3有销钉定位法:
①两孔定位法:
利用预制在各单层印制板上的两个圆孔,插入销钉实现图形转移、层压、钻孔等工序的定位,最终完成多层板的定位。
这种方法由于在X方向上受到限制,往往在Y方向上产生尺寸“飘移”,造成层间对位有较大的误差,因此,此法对于较厚板基、层数少、板面积小、档次不高的多层板来说是可取的。
②一孔一槽定位:
针对两孔定位存在的缺点,提出了一孔一槽定位法。
此法在X方向上一端留有余隙,以便于覆铜箔基材在此方向上有一个小的伸缩余量,从而避免了Y方向上尺寸的无序“飘移”。
对档次不高的多层板来说,这是比两孔定位更为可取的定位方法。
③三孔或四孔定位:
为了防止在生产过程中在X方向和Y方向上的尺寸变化,推出了三孔(呈三角板分布)和四孔(呈十字形)定位。
但是由于销钉和孔的紧密配合而使芯片基材在“锁定”状态下成型,由此产生的内应力会造成多层板的锅底和翘曲。
④四槽孔定位:
在照相底版、覆铜箔基材的四个周边的中心处内侧,制出四个槽孔,并利用相应的四个槽形销钉来实现图像转移、叠层、层压和钻孔等一系列工序的定位。
四槽孔定位是以槽孔的中心线为定位基准,因此由诸种因素造成的定位误差可以均匀在中心线的两边,而不是积累在一个方向上,显然这是一种比较合理的方法,也是当今世界上多层板生产企业广为采用的方法。
四槽孔定位的工艺过程可简述如下:
用冲槽孔设备分别在粘结片和内层薄板及照相底版上冲四个定位槽孔→在四销钉位桌上将底版套在内层薄板上作图形转移→蚀刻→黑化→在叠层台上用四个销钉将内层、粘结片、脱模膜(离型纸)按设计要求装于层压模板中→层压→去销钉→裁毛边→多层叠合物置于数控钻孔机上的四槽工具上钻孔→转后续工序。
采用销钉定位法虽然产品合格率高,工艺容易控制,但操作复杂,工作效率低,成本高,难以适应企业量产的需要。
因此,无销钉定位法脱颖而出。
4无销钉定位法:
①X射线打靶定位:
在多层板照相底版的图形外设置三个定位标靶并用数字化编和编入钻孔程序数据内(底版准备)→底版冲定位孔→制底版书夹→内层板无销钉图象转移→蚀刻→黑化→以铜箔作外层内置预先叠放好的粘结片和黑化内层板→无销钉层压→裁毛边→显露定位标靶后用X射线扫靶优化后自动钻出定位孔→定位钻孔→转后续工序。
此法特别适用生产3~~4层的多层板。
②熔合定位法:
多层板无销钉定位法中目前对六层以上采用铆钉定位外,还有一种熔合定位法,这种方法在多层板制造中逐步推广应用。
利用熔合定位机,在多层板叠层后,通过该机熔合头所产生的200~~500℃的瞬时同高温,在1~~1。
5min内,粘结片把各层之间粘合、固化、定位。
定位点根据需要而设定。
一般在6个熔合点之内。
该熔合定位法比铆钉定位准确,偏移小,从而重合精度提高,避免铆钉铆合后,本身的厚度给层压带来影响。
另外该机可双台面移动,一面叠层一面进行熔合,生产效率高,不仅适合大拼版24*24生产,还能适应小尺寸,小批量生产。
二多层板层间偏位及其影响因素
1多层板层间偏位:
①多层板层间对位偏差包含着层与层之间重合度和内、外层环宽两个概念,两者既密切相关又有区别。
但我们最关心的是环宽的问题,除了外层环宽保证外,特别是内层环宽的保证问题,这是关系到多层板内层电气互边的可靠性问题,也是本文讨论多层板层间偏差的重要依据。
②有关内层环宽的规定和意义:
对于多层板内层功能性(即指与导线相连接)连接盘在钻孔后可能出现的情况有三种情况:
第一,为理想情况,即环宽处处相等尺寸,第二,为最小环宽处≥0。
05mm的情况,第三,为最小处为0(相切)情况,也即破盘情况。
③根据ANSI/IPC-ML-950C和MIL-P-55110等有关规定,为了确保多层印制板内层电气互边的可靠性,多层板内层(特别是功能性连接盘)的环宽最小处应≥0。
05mm,对于重要的电子设备和军用品不允许破盘或钻孔与连接盘相切的情况出现。
这是因为一旦破盘或相切处于功能性连接盘的内边导线处时,将会严重影响多层板电气互边的可靠性问题。
其理由是:
内连导线仅以其导线的截面积而显露于孔壁上,然后通过金属化孔的电镀与镀通孔孔壁直接连接。
由于原基材铜箔层上的铜和镀层上的铜在特性上(物理上和化学上)产生差异,如化学沉积铜层较疏松、延展性较差等,这些将会造成该处电气互连的薄弱环节,再加上接触面少得多,会经不起热冲击和作用条件的要求而易于发生断裂,造成多层内层电气互连开路。
这是电子设备的“要命”问题。
2多层板生产过程对位偏差的分配控制:
①限定多层板对位偏差本质上是整个生产过程中其尺寸变化的分配和控制问题。
因此首先要分析和掌握多层板生产过程中影响尺寸变化的因素;并找出哪些因素是主要矛盾和哪些因素是矛盾的主要方向,然后针对主要影响因素和影响因素的主要方面采取措施,严加控制来达到目的。
②各种因素的影响:
从多层板生产角度和长期实践经验的结果来看,多层板整个生产过程中影响其尺寸变化因素有:
多层板线路设计的合理性,内层覆铜箔层压尺寸稳定性,照相底片制作和作用过程中尺寸稳定性,多层定位系统的精确度,多层以层压过程尺寸的变化,数控钻床和钻孔精度的控制,多层板尺寸大小,环境条件(主要是温、湿度)和操作者水平等一系列因素。
3多层板设计合理性:
①对于高密度、小孔、高层、薄板的多层板(≥10层)来说,设计者通常是把电源层地层和信号层分开独立地占有某一整层或几层,由于内层各种功能性导体面积有相等,加上每一层上导体部分分布不均,形成局部区域导体密度很高而另一部分区域导体密度稀疏,甚至电、地层上留有局部大面积的铜箔区,而基材厚度很薄(如0。
01mm),这些都会造成各层尺寸变化不一致和每一层上局部尺寸变化不相同(如引起X、Y方向收缩差异等)。
以上种种导体不均匀设计结果会造成各层尺寸的差异而导致多层板层间对位的偏差,尽管完全布设是不现实的,但是更合理的布设是能做到的。
②合理或理想的多层板导体布设主要是:
各层面上铜导体的分布应尽量分配均匀,避免局部导体疏密差别悬殊过大,电、地层面上导体形成“网状”结构,不采用大面积或局部大面积铜箔结构,这样做还有利于层间结合力,为了改善薄片基材的刚性(利于表面处理)和层压时层间气体均匀流动填满导体间的间隔,从而改善层压时基材尺寸变化均匀性,每层面上四周边(成品加工框线外)应设计成交叉或“梅花状”而不是四周包围着整片铜箔,相邻层面的导线走向成90℃角或整体图形倾斜45℃角后互为垂直等等。
4层压材料尺寸稳定性:
多层板层压材料是指制造内层用的覆铜箔基材(芯材)和用于内层间既起绝缘作用又起层间粘结作用的B-阶段粘结片等两种材料为主。
前者是由铜箔、玻璃布和固化(C-阶段)了的树脂组成复合材料,后者是由玻璃布和B-阶程度的树脂组成的复合材料。
为了掌握和控制这些层压材料尺寸稳定性情况必须了解各种材料的性能。
5树脂材料:
Tg(玻璃化转变温度)高的树脂其固化(C-阶)前熔融状态粘度大,因此在固化阶段收缩较大,但是一旦固化完成之后,其整体尺寸稳定性好,易于控制。
所以Tg高的聚酰亚胺、氰酸脂树脂的BT树脂比下Tg较低的环氧树脂来说,尽管进行固化过程中引起较大的尺寸收缩,但不会象环氧树脂那样常常引起(特别是内层线路制造和层压过程及以后加工过程,如HAL)不规则的局部尺寸不均匀收缩。
树脂的热膨胀系数小于Tg温度下,膨胀一般为40~~80ppm/℃。
由于树脂是作为绝缘填充和粘结作用物质而存在于覆铜箔层压材料B-阶粘结片之中,这就是说树脂是填充度粘结玻璃纤维布提方格细缝中,如果残留在玻璃纤维布上很薄仅起层间粘结作用时,在这种情况下,尽管树脂尺寸收缩较大,但它受到玻璃布机械阻隔挡式束缚作用,这样玻璃纤维布伸缩是主要的。
对于铜箔来说,由于一般采用的为“ED”得到的并经过一系列处理,加上又薄(作为多层板用的一般为≤35um厚度)其尺寸变化是很小的,一般为5~~7ppm/℃。
所以层压材料尺寸稳定性在很大知名度上是取决于玻璃纤维布。
6玻璃纤维布材料:
玻璃纤维布对层压板基材尺寸稳定性有很大影响,对于同一类型玻璃纤维布(如E-玻璃纤维)来说有如下规律:
玻璃丝直径和捻线越
粗,其刚性越好,抗树脂伸缩变化越强。
因而其组成的层压板基材的尺寸稳定性越高,如“7628”玻璃纤维布(厚度为0。
173mm)比起“1080”玻璃布(厚度为0。
056mm)其尺寸稳定性约提高7~~8倍,玻璃布的经、纬向其尺寸稳定性也不同,由于形成玻璃布过程中经线方向受到强力拉伸作用而合尺寸伸长,同时组成布后一系列处理和浸渍树脂、烘烤等过程中一直受到强力拉伸着,而纬线受拉伸作用要小得多,因而在形成覆铜箔板和B-阶粘结片并用于制造多层板时便引起经线与纬线方向尺寸收缩不一致,一般来说,经线方向尺寸收缩要比纬线方向收缩大30~~50%。
同时,玻璃纤维布厚时,由于抗拉作用强,其经纬方向的尺寸稳定性要好得多。
7B-阶段粘结片:
多层板层间对位的偏差是指各个层面上铜导体图形位置变化(参照布设理想位置)的情况,而B-阶段粘结片表面无铜箔层,仅由玻璃纤维布和树脂来组成的,因而在多层板层压过程中对相邻铜箔导体图形仅起绝缘隔离填充和粘结作用。
所以B-阶段粘结片与覆铜基板最大区别是:
(一)表面无覆铜箔层,在层压过程中本身不存在着铜导体图形位移和尺寸变化问题。
(二)玻璃布的树脂处于B-阶段而不是处于C-阶段状态的树脂,这种树脂在多层板层压加热过程中会形成熔融状态并在一定压力而流动,排挤掉相邻层上导体间的间隙中的空气并填满把相邻的层粘结起来。
总之在加热加压下完成固化反应和控制多层板厚度,很显然,B-阶段粘结片对多层板层间对位偏差的影响主要是通过树脂固化反应前流动和玻璃布尺寸变化影响,但是对于已固化(C-阶段)了的粘结力很强的覆铜箔基材形成的铜导体图形内层来说,B-阶段粘结片这种作用对相邻的导体图形层尺寸变化(含位移)的影响相对是很小的。
正因为这样,冲制B-阶段粘结片的定位孔精度不必提出严格要求也不必冲制成相应的四槽位也进行“紧配合”形式,一般是制成比销钉孔尺寸更大的圆孔,以便装模叠层时轻松的套进四槽销钉上便可。
8覆铜箔基材:
覆铜箔基材是用B-阶段粘结片和经处理过去时铜箔在加热加压下形成并固化了的芯材。
它是形成多层板内层导体图形的基材。
多层板层间对位度就是指这些内层导体位置变化程度。
在形成多层板过程中它除了受B-阶段粘结片影响外,最主要的是取决于覆铜箔基材本身尺寸稳定性情况。
影响覆铜箔基材尺寸稳定性因素很多,很复杂,主要是
(一)覆铜箔基材中树脂固化程度,在固化时与固化后由于树脂收缩大和玻璃布收缩中玻璃布经、纬线方向收缩差异等引起内应力和尺寸的变化。
为了克服这些缺陷,剪裁后的覆铜箔基材在还没有表面处理前必须进行严格的烘烤。
对于环氧树脂玻璃布的铜箔板材应在160~~170℃*4~~6h处理,为便于移转和防止损伤铜表面以及保证烘烤的均匀性,首先平放一光洁的钢板(或铝合金板)叠放覆铜箔基材至25~`30mm厚度,再盖上一块光洁的钢板,然后再叠放覆铜箔基材,这样重复3~`5层,最上面要压上钢板,平放于烘箱内烘烤。
这种处理方法可使基材内部树脂进一步充分固化,充分消除内应力和提高尺寸稳定性。
通过试验和长期生产实践表明可大大改善基材尺寸稳定性,一般其尺寸稳定性可提高1~~3倍。
(二)覆铜箔基材中绝缘材料的厚度和结构,即玻璃布厚度(或类型)和树脂的含量问题。
一般说来,玻璃布越厚、树脂含量越少,其尺寸稳定性越高,因此采用较厚的玻璃布和较低含量的树脂尺寸稳定性、提高层间对位度是有好处的。
因此,在满足多层板厚度和可靠性要求下,覆铜箔基材的厚度尽量选取厚些(即用厚玻璃布),而B-阶段粘结片可选取薄些、树脂含量相对高些(保证填满相邻铜导体图形间隙并粘结牢固),这样既便于调节多层板厚度又有利于主体基材尺寸稳定性。
9照相底片尺寸稳定性:
从照相底片结构可清楚地知道,照相底片尺寸稳定性是由基材尺寸稳定性来决定的,而不是由银盐、乳胶层等等来决定的,因此照相底片基材一般选用尺寸稳定性较好的聚酯(PET)材料为基体,而较厚的聚酯薄膜比较薄的聚酯薄膜尺寸稳定性好。
同时,为了提高聚酯薄膜尺寸稳定性,聚酯薄膜要进行特殊处理,因为聚酯薄膜尺寸变化受温度、湿度变化的影响很大。
温度控制可以通过房间温控(±1℃或更小到±0。
5℃)和冷光源(如控温的曝光机或平行光曝光机)等达到较好的控制效果,而湿度要在小范围内(±3%RH)控制就困难得多,因此在聚酯薄膜表面进行“防潮”处理以提高其尺寸稳定性是一种有效的方法。
如杜邦(Dupont)公司已提供的Dimension naster高稳定性的底片,具有保护的乳胶层,