产品质量控制程序.doc
《产品质量控制程序.doc》由会员分享,可在线阅读,更多相关《产品质量控制程序.doc(15页珍藏版)》请在冰豆网上搜索。
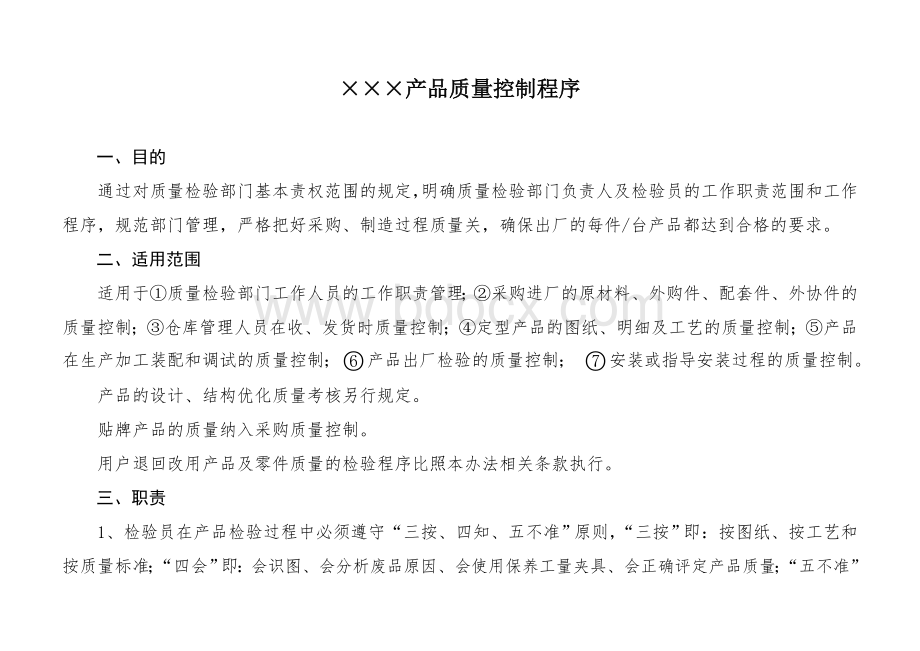
×××产品质量控制程序
一、目的
通过对质量检验部门基本责权范围的规定,明确质量检验部门负责人及检验员的工作职责范围和工作程序,规范部门管理,严格把好采购、制造过程质量关,确保出厂的每件/台产品都达到合格的要求。
二、适用范围
适用于①质量检验部门工作人员的工作职责管理;②采购进厂的原材料、外购件、配套件、外协件的质量控制;③仓库管理人员在收、发货时质量控制;④定型产品的图纸、明细及工艺的质量控制;⑤产品在生产加工装配和调试的质量控制;产品出厂检验的质量控制;安装或指导安装过程的质量控制。
产品的设计、结构优化质量考核另行规定。
贴牌产品的质量纳入采购质量控制。
用户退回改用产品及零件质量的检验程序比照本办法相关条款执行。
三、职责
1、检验员在产品检验过程中必须遵守“三按、四知、五不准”原则,“三按”即:
按图纸、按工艺和按质量标准;“四会”即:
会识图、会分析废品原因、会使用保养工量夹具、会正确评定产品质量;“五不准”即:
不合格的原料不准投入、不合格的毛坯不准加工、不合格的零件不准装配、不合格的产品(成品)不准出厂、不合格的产品(成品)不准计算产值产量。
2、检验员要熟悉产品的主要性能和特点、技术标准,了解零件加工的工艺流程,重点加强对关键零件的形位公差及部件、组件、整机的装配质量检查,督促加工人员使用工装夹具,全面掌握产品的质量要求和岗位中所使用的技术资料。
3、合理维护、正确使用通用计量器具,以及专用验具、夹具、试验仪器或装置。
预防检验器具在检验过程中发生锈蚀、碰伤、形变等现象。
4、为确保检验人员的正常检验工作,检验员原则上不被抽调到供方进行质量检验,或被安排到厂外处理其它业务。
如有特殊情况需抽调检验员到厂外处理其它业务,须经质量部经理批准并做好人员调配工作,此时段出现的质量差错应由接替人员负责。
5、上道工序的零件在工序转移前须经检验员检验确认合格后方可转入下道工序的车间,同时提供详细的调度单(包括图号、数量等)。
下道工序的车间有权退回无检验合格标识和详细调度单的零件,若接收了不合格或没有调度单的零件,则由接收的车间承担不合格零件的质量责任。
6、检查过程中检验员应按规定填写检验记录等质量证明凭据,做好检验标识。
各部门负责人是产品质量的第一责任人,检验员无权对不合格品提出降级意见,均由产生不合格品的车间(部门)提出处置申请,在申请前连同纠错或补救方案及处理意见同时报技术部,由技术部提出处理意见。
7、在采购、生产、安装等过程中技术资料有改动,申请部门需要办理相关更改手续,经技术部具体经办人确认后,需审核人签字方可生效。
8、对已经确定为废品的进行标识和隔离。
四、程序
(一)原材料、外购件、配套件的质量检验
1、采购物品进厂后,采购人员应对照技术部门下达的采购联系函于12小时内自检完毕,自检合格后,提供送检单(注明送检数量型号、接口、尺寸、用户名称、供应商名称等信息)并附图纸(特殊结构定制)、技术参数,以及材质检验报告、合格证等质量证明文件的原件或复印件。
2、检验员按图纸或技术部门下达的采购联系函及有关检验标准对采购物品进行检测,根据检验规定确定全检或抽检的方式并做好记录,对照质量证明文件的内容进行检查验收,合格后签字确认。
抽检要求的检验规定:
送检数量小于20件时采用全检方式;送检数量大于20件时采用抽检方式,按送检数量的20%进行抽检,但不得小于20件。
3、对检验不合格的采购物品,检验员须在送检单上注明不合格标识,采购部门不得办理入库手续。
不合格的采购物品由采购员办理退货手续并及时填写不合格品处置单。
4、检验完毕后,检验员应将送检单及质量证明文件在24小时内交质量文员保存,质量文员对送检结论及质量证明文件进行分类汇总及质量统计。
5、未经检验或无检验合格标识的外购物品保管人员不得发放,各车间不得领用,若接收了不合格的零件,则由接收的车间承担不合格的零件的质量责任。
6、未经检验人员签字的原材料、外购件、配套件不得入库,财务部不得付款;对暂时无法检测的项目,检验人员应在送检单上注明。
(二)齿轮、铸件、锻件、热处理件等外协件的质量检验
1、半成品外协加工件,外协加工前须经检验合格后方可送出外协。
按产品图纸采购的外协物品进厂后,采购人员应于12小时内自检完毕,自检合格后,提供送检单(注明外协类型,送检数量、外协件代号、用户名称、供应商名称等信息)并附图纸,以及材质检验报告、合格证等质量证明文件的原件或复印件。
2、检验员按图纸及有关检验标准对采购物品进行检测,根据规定确定全检或抽检方式并做好记录,对照质量证明文件的内容进行检查验收,合格后签字确认。
抽检要求的检验规定:
送检数量小于20件时采用全检方式;送检数量大于20件时采用抽检方式,按送检数量的20%进行抽检,但不得小于20件。
3、对检验不合格的外协物品,检验员须在送检单上注明不合格标识,生产部门不得办理入库手续。
不合格的外协物品由采购员负责处置(返修或退货)并及时填写不合格品处置单。
4、检验完毕后,检验员应将送检单及质量证明文件在24小时内交质量文员保存,质量文员对送检结论及质量证明文件进行分类汇总及质量统计。
5、未经检验或无检验合格标识的外协件保管人员不得发放,各车间不得领用,若接收了不合格的零件,则由接收的车间承担不合格的零件的质量责任。
6、未经检验人员签字的外协件不得入库,财务部不得付款;对暂时无法检测的项目,检验人员应在送检单上注明。
(三)生产加工及组装调试的质量检验
1、各生产车间在零件加工或总装时,应严格执行“三按”、“五不准”要求,按工装工艺进行加工,执行自检、互检、交检制度,对自检合格的零件,由车间开出送检单,交检验员进行检验。
下道工序在接到上道工序转来的零部件时应根据工艺、图纸要求复核尺寸,确认是否预留加工余量,如发现尺寸问题,将追究上道工序质检员责任,如上道工序未送检将追究操作者责任。
2、对检验中发现的质量问题或违背工艺纪律情况或不按工装加工,检验员有权要求停止加工并及时向质量部和生产部反映,责任车间应及时纠正;对已经发生的不合格产品,检验员应及时开具不合格处理单,产生不合格品的车间(部门)提出处置申请并报送技术部,由技术部经办人提出处理意见,经审核人签字判定是否能降级回用或报废,车间收到技术部对不合格品的处理意见后,应及时采取纠正措施,返工后的产品检验员应重新检验,检验员无权对不合格品提出降级使用意见。
3、检验员应重点加强对关键件的形位公差及部件、组件、整机的装配质量检查,督促加工人员使用工装夹具。
对批量生产的零件,必须坚持首检、巡检、终检制度,检验员在首件检查后须做好标识。
检验员按图纸及有关检验标准对加工零部件进行检测,根据规定确定全检或抽检方式。
抽检要求的检验规定:
送检数量小于20件时采用全检方式;送检数量大于20件时采用抽检方式,按送检数量的20%进行抽检,但不得小于20件。
4、检验员在检验完毕后须在被检零件上做出“合格”或“不合格”标识,按规定要求填写检验记录。
检验单一式三份,一份交送检部门,一份交生产部,一份交质量部汇总、统计、存档。
5、产品在部件组装、拼装、焊接前,车间主任、调度员(工艺员)要认真阅读图纸、工艺后再进行装配、试机。
产品在装配时,如发现上道工序转来的零件有明显的质量问题,应查看是否有上道工序的检查记录,及时退回并做好记录。
检验员必须按图纸和产品质量标准要求检验产品,确保组装、拼装及整机装配达到形位公差的要求,准确判定产品是否合格,并做好记录。
6、产品的试车必须按产品(部颁、企业)标准进行,检验人员按标准中检验规则规定的出厂检验内容进行检验,发现不符标准的指标,允许调整修复,但必须重新进行检验,判定是否合格,并做好试车检验记录。
对带机出厂前整机的试机、检验按技术部制订的调试大纲进行,检验人员依调试大纲进行检验,并做好记录。
7、与产品配套的电控箱(柜),调试人员须进行通电空载试验,做好试验记录,避免产品发往用户出现质量问题。
检验员必须按图纸和产品质量标准要求检验产品,准确判定产品是否合格,并做好记录。
(四)产品出厂的质量检验
1、产品装箱发货前,发货人员根据技术部门下发的发货明细表逐一核对清点,对错发、漏发承担全部责任。
检验员对装箱物品的质量负有完全责任,同时按规定填写出厂记录。
2、产品出厂的质量均由质量检验部负责。
3、每批产品出厂后,质量文员应及时做好产品的档案整理工作。
(五)质量管理部是此程序的监督管理部门,并负责对相关部门执行情况进行考核。
附件:
车间、部门产品质量控制程序流程图
采购件产品质量控制程序流程图
接口尺寸、外观、标识、转动、文件等的检验。
合格
入库或领用
检验员检验
提供送检单、合格证、质保书等。
送检单中须注明送检数量、型号、接口尺寸、用户名称
符合
是否符合图纸或技术要求
采购人员自检
一、基本流程
采购件
不合格
不符合
重点记录接口尺寸的检验结果
红漆标识
批量大时按抽检规定抽检
退回
二、检验项目
材料尺寸应符合标准
须提供质保书或材质检验报告
外观平整厚薄均匀
材料标识与定货要求一致
退回
原材料
底脚安装孔尺寸检验
输出轴及键槽尺寸检验
电机安装孔尺寸检验
外观色泽均匀,安装面无锈蚀、裂纹等缺陷,输出轴转动灵活
须提供质保书或合格证及使用说明书
减速机
填写测量结果记录
整机噪声检测
绝缘电阻检测
电机类
须提供性能测试报告、合格证及使用说明书
抽检数量为每批数量的5%,且不少于5件
泵类
转动件应转动灵活
外观无锈蚀、裂纹等缺陷
轴承及螺栓螺母
外形尺寸应符合标准
轴承的防锈油须完好
须提供合格证
若有1件不合格,再抽检一批,仍有不合格则判整批不合格。
机械密封粗糙度检测
油封外观应光滑、不起泡等
油封及机械密封
阀门的接口尺寸检测
机械密封的密封面平整光滑
阀门类
产品质量控制程序流程图
发货前
核对各道工序的主件主项检验记录
入库
或领用
注明合
格标识
合格
检验员检验
采购人员自检
原材料
入库
质量统计文件存档
填写质量记录
外购件
发货人员根据技术部发货明细逐一核对名称、品种、数量、包装。
合格
调试试机
产品总装
退回
不合格
配套件
外协人员自检
不合格
检验员检(抽)查装箱、待发物品是否符合质量要求。
检验员检验
半成品外协件
外协加工
合格
加工人员自检
返修
入库或转工序
注明合
格标识
合格
加工人员自检
零部件加工
产品出厂
质量统计文件存档
检验员检验
填写质量记录
操作人员自检
组装及调试
技术部制定处理意见
标识、检验员开不合格单
责任车间申请处置
返修
检验员复检
不
合格
产品质量控制程序一览表
工序
各工序生产人员的质量控制
各工序检验人员的质量控制
不合格品处置
备注
原材料
外购件
配套件
1、采购物品进厂后,应于24小时内自检完毕,
2、提供送检单(注明送检数量)
附:
相关图纸、技术参数,以及材质检验报告、合格证等质量证明文件的原件或复印件
3、必要时,封存1件外购件样品
1、按图纸及有关检验标准对采购物品进行检测
2、确定全检或抽检的方式并做好记录
3、对照质量证明文件内容进行查验,合格后签字确认。
附:
抽检规定:
送检数量小于20件时采用全检方式;送检数量大于20件时采用抽检方式,按送检数量的20%进行抽检,但不得小于20件。
1、不合格品退回供应厂家
2、检验员须在送检单上注明不合格
3、采购部门不得办理入库手续
4、各车间不得领用
5、财务人员不得付款
齿轮、铸件