化工事业部芳烃生产与资源调研 精品.docx
《化工事业部芳烃生产与资源调研 精品.docx》由会员分享,可在线阅读,更多相关《化工事业部芳烃生产与资源调研 精品.docx(18页珍藏版)》请在冰豆网上搜索。
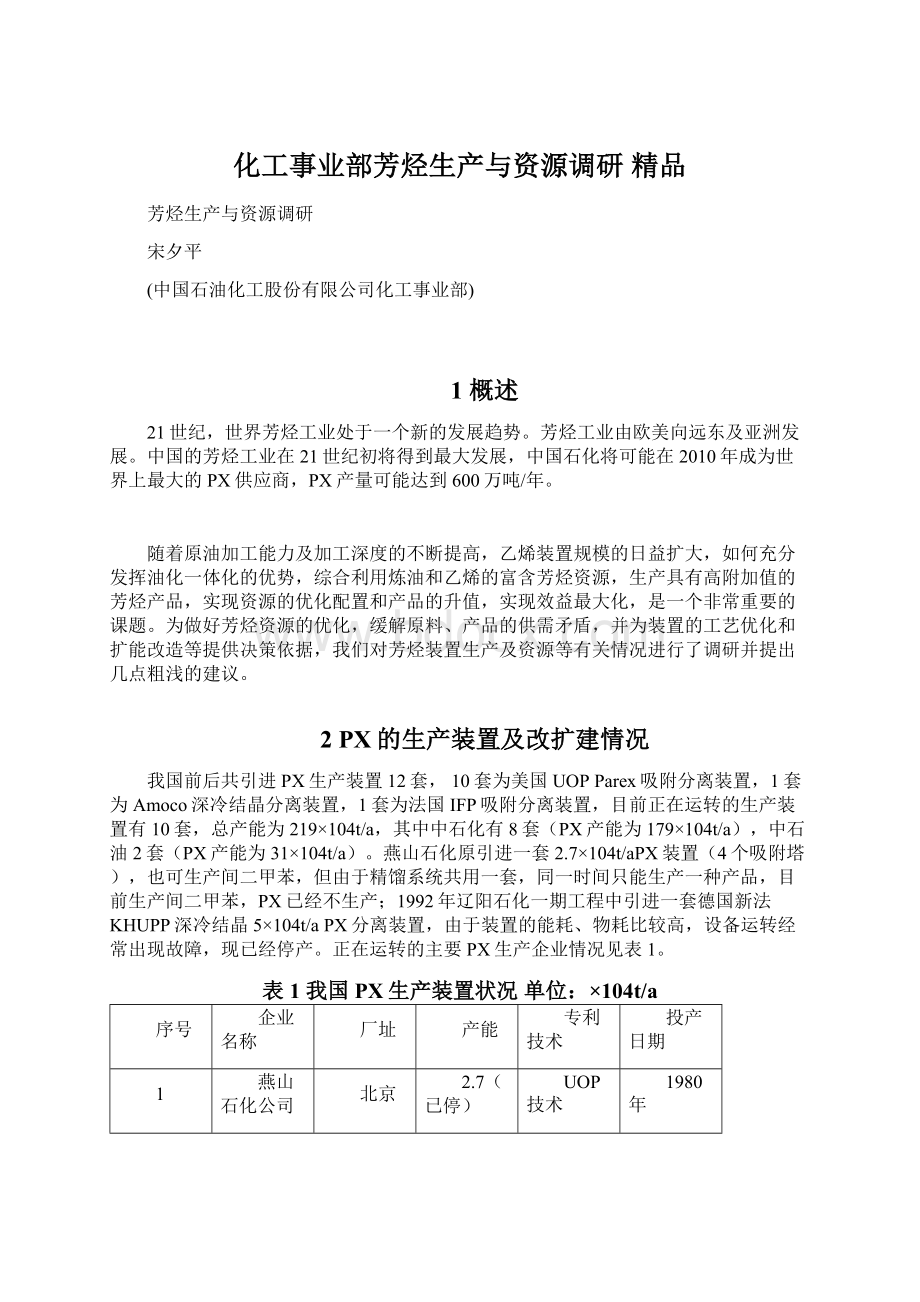
化工事业部芳烃生产与资源调研精品
芳烃生产与资源调研
宋夕平
(中国石油化工股份有限公司化工事业部)
1概述
21世纪,世界芳烃工业处于一个新的发展趋势。
芳烃工业由欧美向远东及亚洲发展。
中国的芳烃工业在21世纪初将得到最大发展,中国石化将可能在2010年成为世界上最大的PX供应商,PX产量可能达到600万吨/年。
随着原油加工能力及加工深度的不断提高,乙烯装置规模的日益扩大,如何充分发挥油化一体化的优势,综合利用炼油和乙烯的富含芳烃资源,生产具有高附加值的芳烃产品,实现资源的优化配置和产品的升值,实现效益最大化,是一个非常重要的课题。
为做好芳烃资源的优化,缓解原料、产品的供需矛盾,并为装置的工艺优化和扩能改造等提供决策依据,我们对芳烃装置生产及资源等有关情况进行了调研并提出几点粗浅的建议。
2PX的生产装置及改扩建情况
我国前后共引进PX生产装置12套,10套为美国UOPParex吸附分离装置,1套为Amoco深冷结晶分离装置,1套为法国IFP吸附分离装置,目前正在运转的生产装置有10套,总产能为219×104t/a,其中中石化有8套(PX产能为179×104t/a),中石油2套(PX产能为31×104t/a)。
燕山石化原引进一套2.7×104t/aPX装置(4个吸附塔),也可生产间二甲苯,但由于精馏系统共用一套,同一时间只能生产一种产品,目前生产间二甲苯,PX已经不生产;1992年辽阳石化一期工程中引进一套德国新法KHUPP深冷结晶5×104t/aPX分离装置,由于装置的能耗、物耗比较高,设备运转经常出现故障,现已经停产。
正在运转的主要PX生产企业情况见表1。
表1我国PX生产装置状况单位:
×104t/a
序号
企业名称
厂址
产能
专利技术
投产日期
1
燕山石化公司
北京
2.7(已停)
UOP技术
1980年
2
上海石化股份有限公司
上海
23.5
UOP技术
1985年
3
辽阳石油化纤公司
辽阳
25
UOP技术
1996年
辽阳
5(已停)
Khupp技术
1992年
4
天津石化公司
天津
8
UOP技术
1980年
天津
25
UOP技术
2000年
齐鲁石化公司
山东
6.5
UOP技术
1987年
6
乌鲁木齐石化总厂
新疆
6.0
UOP技术
1989年
7
扬子石化公司
南京
45
UOP技术
1989年
10
UOP技术
1997年
8
洛阳石化公司
洛阳
18
UOP技术
2000年
9
镇海炼化股份有限公司
镇海
45
IFP技术
2003年
合计
212(219.7)
3芳烃联合装置简介
3.1芳烃联合装置构成
芳烃联合装置一般由苯抽提或苯/甲苯抽提或苯/甲苯/二甲苯抽提、PX吸附分离、二甲苯分馏、甲苯歧化及烷基转移、甲苯择型歧化、C8A异构化等单元组成。
也有的联合装置配套设施还包括裂解汽油加氢、直馏石脑油加氢精制、连续重整及用于生产重整用石脑油的加氢裂化装置,本报告中的芳烃联合装置是指至少含有PX吸附分离单元的联合装置,详细情况见表2。
在芳烃联合装置中,核心装置是生产PX的吸附分离单元,其它单元的设置、OX是否作为产品采出以及PX与OX比例,将会影响PX的成本和联合装置的技术经济指标,但PX产能主要取决于PX装置本身的规模,更确切地说主要取决于旋转阀或吸附塔本身的大小。
目前,UOP已设计和建设了73套装置,其中投产了71套,总PX产量超过1500×104t/a,装置规模从2.1×104t/a到120×104t/a不等。
90年代法国IFP推出了新的吸附分离工艺技术(Eluxyl),是目前世界上第二家拥有生产PX全套技术的专利商,并与Mobil的二甲苯异构化技术合作,形成了生产PX的成套技术。
已投产的装置有3套,在建5套,单套生产装置的最大规模达到75×104t/a
。
国内PX的吸附分离技术仅有镇海炼化是法国研究院(IFP)的Eluxyl
专利技术,在2003年8月投入生产,其余均为美国环球油品公司(UOP)的专利技术。
法国IFP的Eluxyl工艺与美国UOP的Parex工艺也是采用模拟移动床,吸附塔24床层,立式、床层互通,但没有旋转阀,利用微机控制144台遥控阀的顺序切断和开启来分离PX,操作简单维修容易,内构件简单不需反洗,同时采用拉曼光谱快速测量塔中各剖面物流浓度与微机控制相连。
现吸附剂吸附容量及选择性已作改进,与UOP吸附剂水平相当。
典型的芳烃联合装置一般包括芳烃抽提(苯抽提、苯/甲苯抽提、苯/甲苯/二甲苯抽提)装置、二甲苯分离装置、吸附分离装置、二甲苯异构化装置、甲苯歧化及烷基转移装置,产品有PX和(或)OX和(或)苯甲苯和(或)混合二甲苯等。
图1为一典型的芳烃联合装置的简单示意图。
加氢裂解汽油
裂化石脑油
C6~C7
重整单元
抽提单元
C7A
C8A
C9A
C8A以上
二甲苯
分馏单元
混合
二甲苯
重芳烃
抽余液
吸附分离单元
异构化
单元
产品苯
歧化单元
其它C7A
抽余油
产品OX
产品PX
图1芳烃联合装置流程框图
表2芳烃联合装置组成单元状况表
公司名称
裂解汽油加氢
连续重整
抽提
分馏
吸附分离
歧化
异构化
天津分公司
√
半连续
√
√
√
√
√
上海石化
—
连续
√
√
√
√
√
齐鲁石化
√
—
√
√
√
√
√
扬子石化
√
连续
√
√
√
√
√
镇海炼化
—
连续
√
√
√
√
洛阳石化
—
—
√
√
√
√
√
天津石化
√
连续
√
√
√
√
√
乌石化
—
—
—
√
√
√
√
辽阳化纤
√
连续
√
√
√
√
√
3.2PX装置用吸附剂
吸附剂的制造技术是吸附分离PX的关键技术,UOP自1972年开发成功后,其吸附剂几乎垄断世界上所有的PX吸附生产装置,且吸附剂的价格昂贵,绝大多数PX生产装置也都是UOP的Parex吸附分离装置。
1995年法国IFP成功开发出PX吸附剂SPX3000,并在美国旧金山的雪可龙公司推出第一套组合式PX分离工艺,即第一段PX吸附分离至90~95%纯度,第二段PX结晶分离,年产量为45×104t/a,之后几年分别在韩国、伊朗、集团公司的镇海炼化共有8套工业化装置投入运行,单线能力为75×104t/a,从而打破UOP多年PX吸附分离技术的垄断地位。
中国石化集团公司的石油化工研究院(RIPP)开发的RAX2000A吸附剂,目前通过集团公司组织的技术鉴定,也正准备工业化应用,吸附剂技术的研制成功预示着在不久的将来,集团公司有能力提供出自己的成套芳烃联合装置工艺技术。
表3为国内芳烃联合装置目前正使用的吸附剂情况。
表3PX装置吸附剂使用情况一览表
企业名称
在用吸附剂情况
PX纯度(%)
PX收率(%)
型号
装填量(t)
投用时间
设计
实际
设计
实际
天津分公司
ADS-7
234
1996年9月
≮99.2
≮99.5
≮92
≮92
上海石化
ADS-7
500
1985年3月
≮99.2
≮99.5
≮92
≮98
齐鲁石化
ADS-7
180
1987年10月
≮99.2
≮99.2
≮92
85
扬子石化
ADS-7
1162
1990年3月
≮99.2
≮99.5
≮92
≮92
洛阳石化
ADS-27
343
2000年4月
≮99.8
≮99.7
≮95
≮92
天津石化
ADS-27
475
2000年9月
≮99.7
≮99.7
≮97
≮97.5
镇海炼化
SPX3000
995
2003年7月
≮99.8
≮99.8
≮96
中石化总计
3889
乌鲁木齐
ADS-7
118
1995年9月
≮99.7
≮
≮
≮
辽阳石化
ADS-27
475
1996年7月
≮99.8
≮
≮
≮
中石化/中石油总计
4482
3.3芳烃联合装置的技术经济指标
在芳烃联合装置中,一般设有芳烃抽提装置和PX吸附分离装置,石脑油重整装置有的设在炼油装置区,加氢裂解汽油装置有的设在乙烯装置区。
不同的配套装置使用的原料不同,可以用于生产PX的原料主要有:
直馏重石脑油、加氢裂化重石脑油、重整生成油、混合二甲苯、加氢裂解汽油、轻质化重芳烃,但直接原料一般为混合二甲苯、重整生成油、轻质化重芳烃等,不同的原料,不同的配套装置,不同的产品结构,生产PX的能耗、物耗相差非常大,用各装置设计数据估算,各种原料在芳烃联合装置上的使用情况如表4。
表4芳烃装置物耗表
序号
原料
原料消耗(吨PX)
副产品
1
重整用石脑油(芳潜大于45%)
消耗石脑油2.5吨
苯、重芳烃、抽余油、氢气、液化汽、戊烷油、石油醚、燃料气
2
混二甲苯(其中EB小于14%)
消耗混苯1.22吨
苯、重芳烃、燃料气
3
加氢裂解汽油
C6:
NA+A+N、
C7:
NA+A+N、
C8:
NA+A+N
消耗乙烯裂解油4.24吨
苯、抽余油、石油醚、甲苯、燃料气
4
重整生成油:
芳烃含60%以上,辛烷值大于100
重整生成油1.8吨
苯、抽余油、石油醚、甲苯、重芳烃
备注:
①本表只是装置的综合平均状况。
②重整生成油是以芳烃重整后的物料来衡量比较的。
由于芳烃联合装置的配套装置不一样,产品结构不同,PX的能耗、物耗水平差异较大。
理论上当芳烃联合装置二甲苯系统的PX与OX的比例在2.3~2.5:
1时的产品结构,整体效益要优于只生产PX或只生产OX或PX与OX的比例过高、过低的产品结构。
但由于各家芳烃装置的下游配套装置不一样,产品结构也就有所区别。
例如,下游设有苯酐装置的,一般都将OX作为产品采出。
3.4芳烃联合装置中其它装置简介
芳烃联合装置的其它主要配套装置只介绍芳烃抽提装置、二甲苯异构化装置、甲苯歧化及烷基转移装置。
其中,芳烃抽提技术包括液液抽提工艺技术、抽提蒸馏工艺技术、抽提组合工艺技术,这包括采用不同溶剂的抽提装置如N-甲酰吗林、四甘醇、环丁砜等;最近几年比较热门的甲苯择型歧化装置,国内也有大的突破,目前由石油化工科学研究院提供技术,扬子石化芳烃厂首套67×104t/a甲苯择型歧化工业化装置的建设正在进行中。
重整装置、裂解汽油加氢装置由于在炼油和乙烯装置中一般有介绍,本文不再叙述。
3.4.1芳烃抽提装置
由于中石油的部分装置尤其炼油行业的装置无法了解,所以统计数据可能有出入,但包括正在建设中的装置和已经准备建设的装置,国内抽提装置至少有45套。
目前,中石化有32套(包括合资2套)。
3.4.2二甲苯异构化装置
国内二甲苯异构化装置总计12套,现正常运行的有9套,其中中石化系统6套,中石油系统3套,详情见表5二甲苯异构化装置概况。
全国二甲苯异构化催化剂的总装量大约为350吨,平均每年的换剂量为50吨左右,中石化系统内使用的都为乙苯转化型催化剂,而中石油系统内使用的全部为乙苯脱乙基型催化剂。
表5二甲苯异构化装置概况
生产企业
目前催化剂牌号
装置规模*(万吨/年)
首次开车时间
扬子石化
SKI-400-40
45(55)
1990
齐鲁石化
SKI-400-40
9
1987
上海石化
SKI-400-40
23
1998
天津石化
SKI-400C
25
2000
天津石化
SKI-400-40
8
1981
吉林化纤
SKI-100
12
2002
镇海炼化
SKI-400
45
2003
辽阳化纤
SKI-100
25(29)
1999
辽阳化纤
SKI-100
20
1996
乌鲁木齐石化
SKI-100
*指PX规模
3.4.3甲苯歧化及烷基转移装置
中国甲苯歧化与烷基转移工业成套技术引进从20世纪70年代初开始,1973年上海石油化工总厂(现上海石油化工股份公司)从日本东丽公司引进了第一套2.5×104t/a聚酯成套技术
,其中包括4.5×104t/a甲苯歧化与烷基转移(以下简称歧化)装置,之后中国又引进了10套歧化装置,见表6。
中国开展甲苯歧化催化剂和工艺的开发研究工作也是70年代初,于1978年10月在湖南长岭炼油厂设计并建成了规模为3×104t/a的第一套工业试验装置,采用复旦大学的技术生产了一批DFC-1甲苯歧化与烷基转移催化剂用于试运转。
1987年上海石油化工研究院开发的ZA-3催化剂在引进装置上工业应用成功,随后有ZA-和HAT-两个系列6个牌号的催化剂先后工业化应用成功。
至2003年,中国的歧化装置全部使用国产HAT-催化剂,有近20项中国专利和美国专利获得授权,形成了自主知识产权,为中国石化出口成套技术和催化剂提供了条件。
1998年上海石油化工研究院的该项技术出口德国,用于中东87×104t/a装置设计,催化剂为HAT-95催化剂,预计2004年投产
。
表6甲苯歧化装置[1]
工厂名称
工艺路线
技术来源
规模[2],×104t/a
投产年份
备注
中石化上海石化一期
Tatoray
东丽公司
4.5
1977
1996年关闭
中油辽化化工一厂
Xylene-Plus
ARCO
12.3
1979
1996年关闭
中石化天津石化化工厂
Tatoray
UOP
12.5
1981
中石化上海石化二期
Tatoray
UOP
39.8(56)
1985
1999年扩能
中石化齐鲁石化烯烃厂
Tatoray
UOP
21
1987
中石化扬子石化芳烃厂
Tatoray
UOP
100.7(123.2)
1990
1997年扩能
中石化长岭炼油厂
/
长岭炼油厂
3
1978
1979年关闭
中石化乌石化炼油厂
Tatoray
UOP
13
1995
中油辽化公司聚酯一厂
Tatoray
UOP
48
1996
中油吉化炼油一厂
Tatoray
UOP
34.2
1996
中油抚顺公司石油三厂
STDT
上海石化院
40
1997
中石化洛阳石化总厂
Tatoray
UOP
37
2000
中石化天津石化化工厂
Tatoray
UOP
55.6
2000
中石化镇海炼化公司
STDT
上海石化院
100
2004
中国大陆
540.5
[1]:
含循环料;
[2]:
()括号内为已扩能后的规模。
由表6可以看出,镇海装置建成后,全国11套装置处理能力达到540.5×104t/a。
就装置数量而言,我国歧化装置约占全球的1/6,但目前只有2套装置规模达到100×104t/a,大多数装置的规模已经偏小,有3套明显偏小。
3.4.4甲苯择型歧化装置
石油化工科学研究院于1996~1998年,完成甲苯择型歧化催化剂的实验室研究工作,确定催化剂的配方、制备工艺、完成工艺条件试验、稳定性试验和再生试验,1998年9月在抚顺石化公司催化剂厂完成吨级工业放大试生产。
1998年10月~1999年1月在齐鲁石化烯烃厂完成1500小时工业侧线稳定性试验。
1999年5月通过公司技术开发部组织的技术鉴定。
2003年完成该技术的工艺包设计和编制工作,预计2005在扬子石化实现工业应用。
上海石化研究院研制的MXT-01催化剂用于苯-碳九芳烃烷基转移新工艺,目前通过了中石化组织的技术鉴定并提出了与甲苯选择歧化工艺组合使用的路线,这种组合工艺不失为芳烃联合装置扩能改造的一个优选方案。
目前,该催化剂1000小时寿命试验结果表明,在高空速WHSV2.5h-1、氢烃摩尔比4.0、反应原料甲苯/C9A=50/50(wt)的反应条件下,其总转化率在46%以上,总选择性甾6%以上,C8A/苯摸摩尔比在3.7以上。
在相同工况下。
具有高的混合二甲苯收率。
4芳烃装置原料状况
4.1芳烃装置的原料结构
2002年中石化集团公司的芳烃联合装置共使用芳烃原料356.27×104t,其中石脑油243.24×104t占68.28%,混合二甲苯25.26×104t占7.09%,加氢裂解汽油53.25×104t占14.95%,重整生成油34.52×104t占9.69%。
4.2中石化芳烃资源的地域分布
由于所用原料不同,每生产1吨PX,需要的原料量是不同的。
对PX有贡献的原料主要为甲苯、碳八芳烃(C8A)、碳九芳烃(C9A)三种和少量的碳十芳烃(C10A)。
而这三种原料的上游原料为加氢裂解汽油、重整生成油(C6~轻质油和C8~C10重质油)。
当然,随着新工艺技术的不断开发与工业化应用,也有其它原料成为PX的潜在原料,如上海院的甲苯歧化与烷基转移催化剂可以将3~4%C10A转化为二甲苯,国外有的甲苯歧化与烷基转移催化剂可以将30%左右的C10A转化为二甲苯,北京石化院的重质芳烃轻质化技术、上海石化院的苯和C9A生成二甲苯催化剂也已经研制成功。
国外关于轻烃转化为芳烃以及重芳烃转化为苯、甲苯、二甲苯的新工艺技术进展与工业化更是进展迅速,芳烃资源变的越来越广。
5芳烃装置及资源存在的主要问题及分析
5.1下游需求强劲,上游发展滞后
由于民营企业的介入,PTA、聚酯行业的生产能力增长幅度很大,而且增长过程是下游拉动上游,PX生产能力的增长远远滞后于PTA产能的增长,使PX进口的增长率大大高于产能增长率。
到2003年达2338万吨/年,其中,亚洲地区PX的产能居首,达1420万吨/年,其次是北美地区,为514万吨/年,其中国内产量达163.2万吨,较2002年增长了10%,PX的自给率从1997年的92.2%下降到2003年的63.7%。
5.2部份芳烃资源没有合理利用
齐鲁石化60万吨/年催化重整装置,可提供51.6×104t/a芳烃原料,其中5万吨/年作为汽油调和组份,富余PX原料约29×104t/a。
2004年后富余加氢裂解汽油14×104t/a,可富余3.5×104t/aPX原料。
齐鲁石化2004年后总富余32.5×104t/aPX原料。
赛科90×104t/a乙烯,可提供加氢裂解汽油55×104t/a,富余26×104t/aPX原料。
另外,考虑到汽油标准的提高,重整生成油用于汽油调合的量将减少,同时中石化的小乙烯装置都在考虑新上苯或(和)甲苯或(和)二甲苯芳烃抽提装置,各炼油厂也准备新上芳烃抽提装置,可利用的PX原料会有所增加。
2004年后,集团公司富余PX原料将至少达到120.2×104t/a。
5.3芳烃原料的优化仍有较大的余地
中石化加工原油中,胜利原油含东兴有约19.6%,不是含东兴有约19.2%,而胜利原油是环烷基的原油,其生产的石脑油的芳潜指数一般都在60以上,是芳烃生产的优良原料。
目前中石化重整原料的芳潜指数虽大部份是在60以上,但也有部分较低。
同时中石化重整原料没有一个统一的标准,企业标准中也仅有微量杂质的指标,而没有芳潜指数等指标。
集团公司目前重整装置能力1121×104t/a,其中炼油型重整装置的能力为702×104t/a,目前平均负荷约70%,平均三苯收率37.42%。
如果重整装置满负荷运行,增加三苯量约150×104t/a。
5.4部份PX装置吸附剂已进入使用寿命的后期
除洛阳、天津大芳烃外,中石化的上海、扬子、齐鲁、天津小芳烃等都是1990年前投运的,PX装置吸附剂的型号都是ADS-7,而且都已进入吸附剂的使用后期,齐鲁、扬子、上海都存在吸附剂性能下降,收率达不到设计指标的现象,整体效益在逐渐下滑。
5.5ADS-27在不同的装置出现相同的问题
目前,国内共有3家企业使用UOP新型PX吸附剂ADS-27,按照UOP的介绍,在处理能力、PX纯度与收率等方面,ADS-27与ADS-7相比具有很大的优势。
从3家企业的运转情况看,PX纯度和收率没有多大出入,但在处理能力方面各家企业在运转2年左右之后,均表现出床层压差大的问题,进而影响到吸附分离单元的负荷,其中天津石化于2000年9月投产,2003年4月发现压差开始增大,虽然经过多方努力查找原因,无法判断问题所在,现在运转负荷仅83%左右;洛阳石化于2000年4月投产,2002年6月28日因吸附剂进入乙二醇而失去活性,经过再生复活于2002年10月16日恢复正常生产,停产3个月,但吸附塔的压差已达到操作上限0.35MPa,开工后装置负荷最高只能达到94%;中石油的辽阳石化于1996年7月投产,开车时吸附塔的压差在0.15MPa左右,目前压差在0.3MPa,虽然可以达到100%负荷,但吸附塔压差相比ADS-7增长速度明显,使用ADS-2的企业,运转时间较长的齐鲁石化、上海石化吸附塔的压差,基本在0.1MPa,没有什么明显的变化。
使用ADS-27的企业在操作中可能有过这样或那样的操作不当之处,但相同的问题却应该引起我们正在使用ADS-27吸附剂和将要引进ADS-27吸附剂的企业足够的重视。
6对芳烃生产及资源优化的若干建议
6.1加强管理,保证装置稳定的前提下,高负荷运转
最近几年国内使用的UOP新型ADS-27的企业频繁出现问题,大多是我们因为操作不当、管理不严造成的,当然也可能有PX吸附剂本身的问题。
在使用ADS-7时吸附塔的压力控制系统波动范围较大对吸附塔影响很小,但UOP的ADS-27的强度远小于ADS-7,且空速大,相同压力下的破碎率大,在操作中要严格控制吸附塔本身的压差,避免由于吸附剂的破碎而造成吸附床层间压差增大并影响吸附高负荷运转的情况出现,不可仍延续ADS-7时的操作习惯;同时今后引进ADS-27的企业,在签定技术协议时应该考虑增加相应的条款,以保护企业自身的利益。
6.2从源头抓起,做到宜芳则芳,宜烯则烯
乙烯和芳烃的生产都利用石脑油做原料,但二者对石脑油原料品质有完全不同的要求,前者要求链烷烃含量高,后者要求环烷烃含量高。
在生产实践中已总结出“宜烯则烯、宜芳则芳”的乙烯与芳烃原料的优化选择原则,但实际运行中总有一部分不适合乙烯原料的石脑油组分进入裂解炉,一部分不适合做芳烃原料的石脑油进入重整反应器。
这就要求原油必须分贮分炼,从源头抓起,特别是芳烃原料不仅要求芳烃含量高,更重要的是对硫、氮、氯、砷、铅、铜、溴等微量杂质都有很高的要求,为此对于有PX生产的企业来说,首先应保证芳烃原料的优化供应。
同时,应加强对石脑油中芳烃与乙烯原料组分分离的研究,即把适合乙烯生产的直链烷烃和适合芳烃生产的环烷分开,将能真正实现乙烯与芳烃原料的最优化。
随着国家颁布的新汽油标准,为满足高标号清洁汽油生产的需要,炼油企业重整已陆续开满。
然而更高要求的成品油标准对芳烃含量要求控制在40%标准之下,以后还要降低。
因此炼油重整装置在满足调合高标号清洁汽油的同时,通过适当的工艺,把高芳含量(主要是C7A/C8A/C9A)的重整生成油用