芳烃生产技术进展Word文档下载推荐.docx
《芳烃生产技术进展Word文档下载推荐.docx》由会员分享,可在线阅读,更多相关《芳烃生产技术进展Word文档下载推荐.docx(15页珍藏版)》请在冰豆网上搜索。
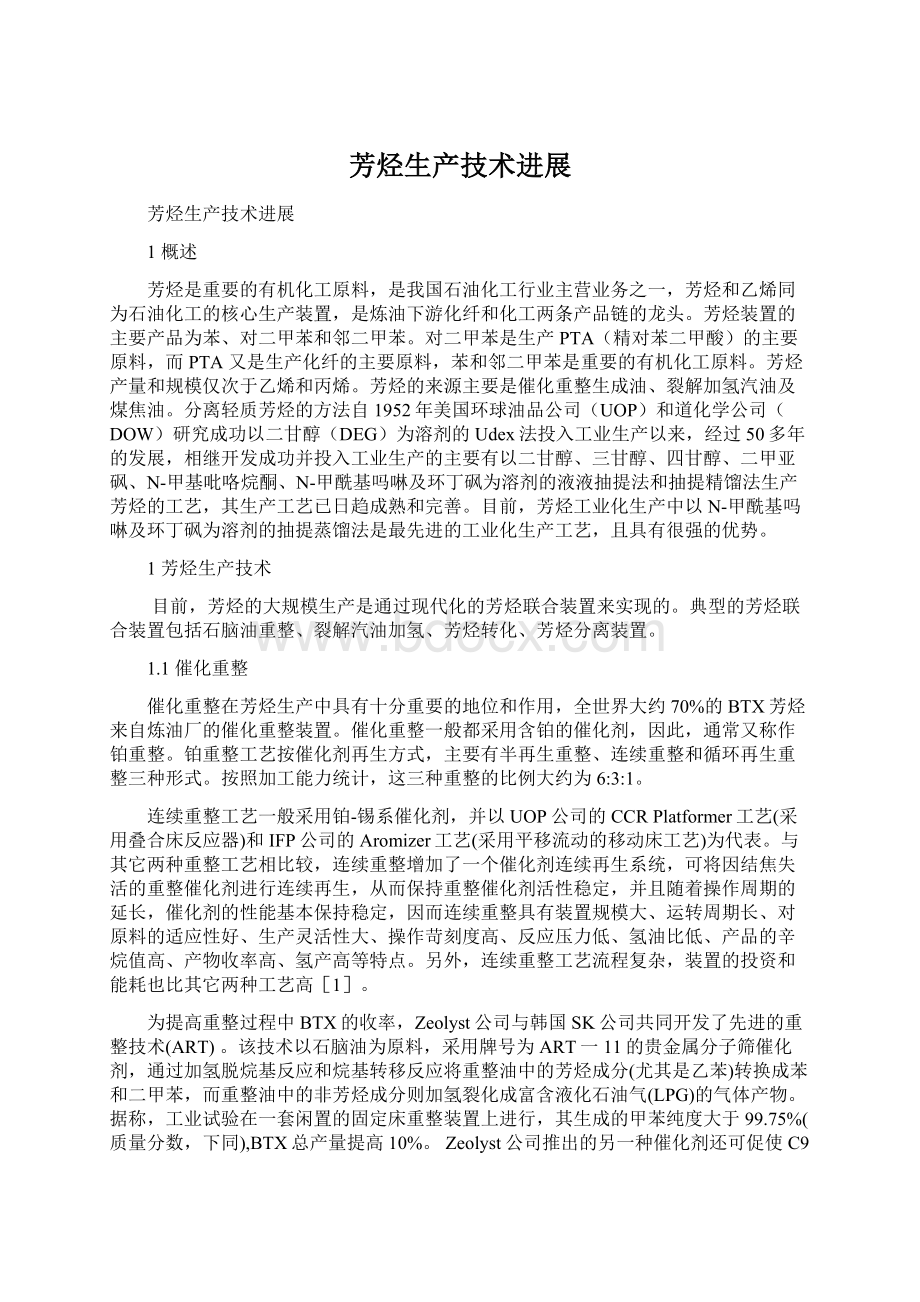
据称,工业试验在一套闲置的固定床重整装置上进行,其生成的甲苯纯度大于99.75%(质量分数,下同),BTX总产量提高10%。
Zeolyst公司推出的另一种催化剂还可促使C9+重芳烃烷基转移成BTX,且这种贵金属改性的催化剂寿命较长,运行两年仍可产出高纯BTX。
ExxonMobil公司开发的多段石脑油重整工艺,在最后一段重整反应器内装填低酸活性分子筛催化剂(即含有加氢功能的徕和ZSM一5分子筛催化剂),苯和甲苯的收率分别增加5%和3%,二甲苯的收率也略有增加[2]。
1.2裂解汽油加氢
烃类高温裂解,以粗汽油为裂解原料时,通常情况下大约每生产It乙烯可副产It裂解汽油,其中苯质量分数可达29.1%,而BTX总质量分数可达58.8%。
从裂解汽油中回收BTX通常需采用两段加氢:
第一段加氢采用贵金属Pd/A1203催化剂,主要对热稳定性差的双烯烃进行加氢;
第二段采用非贵金属Co-Mo/A1203催化剂进行烯烃加氢,并除去包括硫化物在内的多种杂质。
1.3芳烃转换
由于二甲苯衍生物需求的增长速度远远高于苯衍生物的增长速度,目前很多芳烃联合装置以提高二甲苯收率为目的,将需求量相对较少的甲苯和C9芳烃转换为苯和二甲苯,可采用加氢脱烷基工艺、甲苯歧化和烷基转移工艺等。
1.3.1加氢脱烷基工艺
该工艺以苯为目的产物,其优点是苯的收率高。
以甲苯为原料时,苯的收率在99%以上,苯的纯度大于99.99%,仅用白土处理和一般蒸馏就能得到合格产品。
目前在甲苯消费构成中有39.5%用于脱烷基制苯,但由于甲苯歧化制二甲苯装置的增多,联产苯的成本相对较低,因而未来甲苯脱烷基制苯的生产将受到一定的制约。
1.3.2甲苯歧化与烷基转移
随着三大合成材料工业的发展,苯和二甲苯需求量迅速增长,致使石油芳烃供需出现不平衡,其中大约占芳烃总质量50%的甲苯和C9芳烃除用作高辛烷值汽油调合组分外,没有价值较高的用途,在20世纪60年代后甲苯歧化与烷基转移制二甲苯和苯的工艺便应运而生。
与甲苯脱烷基制苯工艺相比,甲苯歧化与烷基转移反应过程中甲基只在苯环间移动,而不是将甲基转化为甲烷,所以氢耗量较少,设备和公用工程消耗也少。
代表性的工艺有Mobil公司的MSTD工艺、UOP公司的Tatoray工艺、IFP/Mobil公司的TranPlus工艺等。
几种主要工艺的操作条件见表1。
表1甲苯岐化与烷基转移工艺
Process
Company
catalyst
Preactioncondition
Temperature/℃
Pressure/MPa
n(H):
n(HC)
WHSV/h-1
Xylene-Plus
Arco
Re-Yzeolite
490-550
0.1
-
0.5-0.1
MTDP-3
Mobil
ZSM-5
400-500
3.0-4.0
0-1.5
4.0
MTPX
460
PX-Plus
UOP
Modifiedzeolite
370-500
1.3-3.0
5.0-12.0
1.0-5.0
Mobil公司开发的MTDP和MTPX是选择性甲苯歧化工艺。
MSTDP工艺于1988年工业化,产物中对二甲苯的质量分数达到82%~90%,MTDP工艺则是MSTDP工艺的改进,其特点是高空速、低氢烃摩尔比。
1997年工业化的MTPX工艺,在甲苯转化率为20%~30%时,对二甲苯选择性在90%以上。
UOP公司开发的PX一Plus工艺也属于选择性甲苯歧化工艺,当甲苯转化率为30%时,二甲苯中对二甲苯的质量分数可超过90%。
甲苯选择性歧化的关键是催化剂。
例如通过表面酸度的调变,可使因分子筛酸性活性中心而引发的异构反应得到抑制,或者是控制分子筛的微孔尺寸,使苯和对二甲苯很容易从狭窄的通道中进出,而间位和邻位二甲苯的扩散就较为困难,从而实现选择性歧化制对二甲苯的目的。
Mobil公司在开发多代选择性甲苯歧化制对二甲苯工艺的基础上,2001年开发了最大化生产对二甲苯的PxMax工艺。
向市场推出的PxMax工艺有两种:
采用EM一2200催化剂,可在现场进行选择性除焦;
采用MTPX催化剂。
两种工艺都比其它选择性歧化工艺有更高的选择性和更长的运行周期,并可在较低的起始和循环温度、较低的氢烃循环比下进行操作。
由于PxMax工艺的对二甲苯浓度很高(质量分数大于90%),所以可以降低下游工艺的操作成本。
Mobil公司还声称,PxMax工艺比MSTDP工艺有重大改进,PxMax工艺不需要高温反应,操作过程也可简化,若用于建设大型装置可降低投资,也可很容易地用于现有装置的改造。
韩国LGCaltex公司已与Mobil公司签订一项协议,在350kt/a的对二甲苯生产装置上采用该技术,并于2003年投人运行[2]。
1.3.3二甲苯异构化
从催化重整油和裂解汽油中获得的C8芳烃,对二甲苯含量仅为混合二甲苯总质量的1/4左右,且乙苯所占比例较大,为最大限度地生产对二甲苯,需将C8芳烃进行异构化反应生成对二甲苯。
典型的工艺有:
UOP公司的Isomer工艺、东丽公司的Isolene(II)工艺、Engelhard公司的Octafining工艺等。
目前工业上应用较多的是UOP公司的Isomer工艺、Engelhard公司的Octafining工艺和Mobil公司的MHAI工艺。
其中,Octafining工艺采用固定床临氢反应;
Isomar工艺在采用第二代催化剂后克服了第一代催化剂带来的腐蚀问题,操作条件虽与Octafining工艺相似,但操作温度略低。
Mobil公司20世纪90年代开发的MHAI工艺采用活性高、选择性好、操作条件温和、催化剂结焦速率慢、运转周期长、再生性能好的分子筛催化剂。
原料中的乙苯还可通过脱烷基、歧化等反应转化为苯和二甲苯。
乙苯转化率可达60%~70%,二甲苯损耗率则降至1.8%,非芳烃转化率达20%,二甲苯的选择性达到平衡值的102%[3]。
2001年Mobil公司向市场推出的最大化生产二甲苯的XyMax工艺,对二甲苯的浓度高于平衡值,且原料中乙苯和非芳烃也可分别转化为苯和低碳烷烃。
乙苯的转化率可高达60%~80%。
Mobil公司开发了两种改进的异构化催化剂:
第一种为高活性异构化(AMHAI)催化剂,与以往采用的异构化工艺相比,采用该催化剂有较高的产物选择性和较低的操作成本。
由于乙苯转化率有较大幅度的提高,所需反应温度又较低,故可改善操作灵活性。
第二种为EM-4500催化剂,也可提高乙苯转化率,有较高的产物选择性,能有效降低二甲苯损失。
AMHAI催化剂已于1999年工业化,EM-4500催化剂则在2000年投人运行。
Mobil公司还开发了较XyMax工艺更具竞争力的XyMax-2工艺。
该工艺使用寿命较长的催化剂,而且这种催化剂可在更宽范围的温度和压力条件下使用。
如对现行装置进行必要的调整,对二甲苯的生产能力可提高40%。
近年来异构化工艺向双层或多层催化剂系统发展,通常第一层催化剂为乙苯转化催化剂,第二层为二甲苯异构化催化剂。
但BP公司发现,由于乙苯转化时生成副产物乙烯使催化剂易失活,所以BP公司开发了3层催化剂系统,即在双层催化剂床中另外加人加氢催化剂(Mo/A1203),乙烯加氢可转化为乙烷,催化剂失活速率可从0.05%下降至0.006%~0.008%,催化剂再生周期超过一年。
UOP公司开发的双层催化剂体系,第一层为磷硅酸铝催化剂(如MgAPSO),第二层为硅酸铝催化剂(如ZSM一5)。
其优点为:
前者乙苯转化率高,后者能提高乙苯生成二甲苯的收率,从而获得较高的乙苯转化率和二甲苯收率,并显著提高工艺的经济性。
Sü
d-Chemie公司开发了一种基于Pt一MFI的催化剂,对混合二甲苯异构化和乙苯脱烷基反应具有较高的活性和选择性。
这种催化剂主要通过晶体尺寸、硅铝比、粘合剂材料和挤条形状的调节而得到优化。
1.3.42,6一二甲基萘的生产
2,6-二甲基萘(2,6-DMN)是生产聚萘二甲酸乙二酯(PEN)和液晶聚合物(LCP)的重要原料。
PEN具有优异的气体阻隔性、耐热性、机械性、尺寸稳定性、抗紫外线性等,可广泛用于工业纤维、薄膜、包装容器、磁片、印刷线路板、电容器隔离板等。
因此,2,6一DMN和PEN已成为高分子材料研究的热点课题之一。
1.3.4.12,6一二甲基萘的制备
Amoco公司、日本三菱瓦斯化学公司、三菱石油公司、芬兰Optatech公司采用邻(或间)二甲苯和丁二烯为原料,用碱金属催化剂等制备2,6一DMN的技术已工业化。
Chevron公司等以甲苯和1-戊烯(或正丁烯)和CO为原料,采用分子筛或酸性催化剂制备2,6一DMN也取得较好的结果。
日本三菱瓦斯化学公司采用间二甲苯、丙烯、CO为原料,HF-BF3为催化剂,可高选择性地直接制备2,6-DMN,不需进行二甲基萘异构体的分离。
以萘和甲基萘为原料,通过与甲醇等烷基化制备
2,6-DMN的研究也取得了较好的结果。
ExxonMobil公司和日本神户制钢所研发了利用催化裂化或乙烯裂解柴油中的混合二甲基萘经异构化、分离生产2,6一DMN的技术,比其它方法投资费用低30%~50%,生产成本低40%左右[4]。
我国炼油工业的催化裂化(FCC)装置的生产能力为100Mt/a,生产FCC柴油40Mt/a,FCC柴油中二甲基萘含量较高。
用这种原料,通过混合二甲基萘异构化、分离生产2,6一DMN,将会有明显的技术经济优势。
1.3.4.22,6一二甲基萘的分离与提纯
混合二甲基萘有10种异构体,这些异构体的沸点相差很小,用精馏方法很难得到纯度较高的2,6一DMN。
已研究过的分离提纯2,6一DMN的方法有:
吸附分离法、直接结晶分离法、共熔结晶分离法、高压结晶分离法、乳化结晶分离法。
用吸附分离法和直接结晶分离法制得高纯度的2,6一DMN比较困难。
共熔结晶分离法采用三硝基芴酮、a-氰基-6-甲基萘、4一硝基邻苯二甲酰亚胺等作为配合剂,可得到纯度为99.0%~100%的2,6-DMN。
ExxonMobil公司和日本神户钢铁公司合作研究的高压结晶分离法,在150MPa压力下可分离得到纯度大于95%的2,6-DMN。
乳化结晶分离法以水为连续相,用特制的乳化剂可制得纯度大于96%的2,6-DMN。
共熔结晶分离法存在着配合剂循环使用等比较繁杂的问题,高压结晶分离法对设备要求非常高,而乳化结晶分离法要求分离液中2,6-DMN的浓度较高。
因此,2,6-DMN的分离提纯方法仍需进一步改进。
1.3.5对二甲苯的分离
二甲苯分离是芳烃生产中难度较大的一个环节。
工业上主要采用模拟移动床吸附分离工艺,也有少数采用结晶(深冷)工艺。
其中UOP公司的Parex液相吸附分离工艺于1971年工业化,其吸附剂由经Ba和K改性的分子筛制得,最新的Parex工艺采用牌号ADS-27作为吸附剂,在对二甲苯纯度为99.9%的情况下,对二甲苯收率可高达97%。
1997年IFP公司也推出Eluxy1吸附分离技术,采用牌号SPX3000作为高效吸附剂,对二甲苯的纯度可达99.9%,1997年12月在韩国一套500kt/a的工业装置上得到应用。
最近IFP公司又推出了两步法模拟移动床工艺:
第一步采用Ba离子交换的X分子筛作为吸附剂,从混合二甲苯中分出对二甲苯,脱附剂为对二乙苯,对二甲苯的纯度和收率分别达99.7%和96.7%;
第二步分离余下的间二甲苯,采用Na离子交换的Y分子筛作为吸附剂,脱附剂为甲苯,间二甲苯的纯度可达99.04%。
在得到高纯对二甲苯的同时还可得到高纯间二甲苯。
早期的结晶(深冷)分离法采用的是可靠性较差的小型设备,维修的工作量很大。
近年来随着设备制造业的发展,结晶分离又重新引起人们的关注。
GTC技术公司推出的CrystPX结晶技术可减少设备数量并能生产高纯对二甲苯。
由于该法采用两级冷冻和结晶,且对流程作了新的改进,投资较低,装置效率更高。
一套400kt/a的对二甲苯生产装置,采用吸附分离的投资费用和生产成本分别为1.7亿美元和441美元/t,但采用CrystPX工艺的投资费用和生产成本分别为1.3亿美元和433美元/t。
随着高新技术的发展,膜分离技术和变压吸附技术也有望进人对二甲苯分离领域。
例如日本NGK绝缘体公司选用了一种AM型分子筛膜,这种膜的孔径为0.5~0.6nm,可以从间二甲苯和邻二甲苯中将分子尺寸较小的对二甲苯分离出来。
但需进一步改善渗透速率,提高气体分离膜的容量。
BP公司推出的技术是将变压吸附技术与模拟移动床分离技术结合在一起的组合工艺。
混合二甲苯首先进人变压吸附装置形成富含对二甲苯的物流和富含邻二甲苯与间二甲苯的物流,然后前者进人模拟移动床吸附装置,分出对二甲苯和富含乙苯的C8芳烃物流,后者进人异构化装置使其转化为对二甲苯。
由于该组合工艺可减少邻二甲苯和间二甲苯进人模拟移动装置的进料量,从而降低了投资费用和能耗。
此外,BP公司还开发了将变压吸附与结晶分离相结合的另一种组合工艺[2]。
1.4芳烃抽提
从催化重整生成油和裂解加氢汽油中分离轻质芳烃的方法主要有溶剂抽提法和抽提蒸馏法。
自1952年美国环球油品公司和道化学公司研究成功了以二甘醇(DEG)为溶剂的Udex法投入工业生产以来,各国又相继研究成功了以环丁砜为溶剂的Sulfolane法,N-甲基吡咯烷酮(NMP)为溶剂的Arosolvan法,二甲亚砜(DMSO)为溶剂的IFP法,以及N-甲酰基吗啉(NFM)为溶剂的Formex法,并陆续投入工业生产。
此外,Udex法也陆续改用三甘醇(TEG)、四甘醇(TETRA)或加入第二组分为新的抽提溶剂,并改进工艺流程等。
70年代以来,研究成功了以NMP为溶剂的抽提蒸馏法(Distapex)和NFM为溶剂的抽提蒸馏法(Morphylane),分离苯或二甲苯。
特别在70年代,为寻找更有效的抽提溶剂,还研究了溶剂分子对选择性和溶解能力的影响,并对近百种有机溶剂或两种以上的有机溶剂混合物的抽提性能进行了考察,对溶剂抽提方法的发展起了重要的作用。
近多年来,中国石化石油化工科学院在以环丁砜为溶剂进行液液抽提法开发成功并投入生产以得到苯、甲苯及二甲苯的基础上,又对环丁砜为溶剂进行芳烃抽提蒸馏进行了大量的研究,并开发出了以环丁砜为抽提溶剂的SED工艺,主要生产苯及甲苯产品[5]。
世界上溶剂抽提轻芳烃的工艺主要有五种[6]。
1.4.1甘醇类溶剂抽提工艺
自1965年底由石油化工科学研究院自己研究、开发和设计的第一套二甘醇为溶剂的芳烃抽提工业装置投产成功以来,石油化工科学研究院又研究和开发了以三甘醇、斯甘醇为溶剂的抽提工艺。
四甘醇抽提简化工艺流程与二甘醇抽提工艺流程对比,具有四个明显的不同:
(1)水洗水与汽提水二个系统简化为一个系统;
(2)抽提蒸馏-汽提塔分成两个独立的塔;
(3)气体水与富溶剂换热改称与贫溶剂换热;
(4)操作条件有明显的变化。
用四甘醇工艺改造二甘醇工艺,投资少,使抽提处理能力提高40%,能耗降低约四分之一,芳烃回收率提高2%~4%,产品质量进一步提高,苯的结晶点可稳定在5.45℃左右,操作简化而易于平稳,容积损耗也有明显减少。
在研究和发展中技术在不断提高,能耗及溶剂损耗也在不断降低。
而以四甘醇为溶剂的四甘醇抽屉工艺在甘醇类溶剂抽屉芳烃工艺中为最佳
1-抽提塔;
2-抽提蒸馏塔;
3-回流芳烃罐;
4-汽提塔;
5-芳烃罐;
6-水汽提塔;
7-抽余油水洗塔;
8-溶剂再生塔
图1简化的斯甘醇抽提工艺流程
1.4.2二甲亚砜溶剂抽提工艺
二甲亚砜溶剂抽提芳烃装置在中国仅有从法国引进的一套,世界上总共也不超过10套,由于二甲亚砜热稳定性差(120℃开始分解),不宜用汽提蒸馏回收溶剂,因此,工艺流程中采用了丁烷反抽提,使得工艺流程(与甘醇类溶剂和环丁砜溶剂抽提相比)变得比较复杂。
除溶剂损耗外又增加了低沸点丁烷的损耗。
2-反抽提塔;
3-反抽出物水洗塔;
4-溶剂蒸馏水塔;
5-抽余物脱丁烷塔;
6-抽出物脱丁烷塔;
7-抽余油水洗罐
图2二甲亚砜抽提流程
1.4.3环丁砜溶剂抽提工艺
关于环丁砜抽提工艺技术,由于此工艺所用的溶剂环丁砜具有较好的热稳定性,优良的选择性和溶解能力,装置能耗和物耗较低,以及其工艺相对较为简单等因素,目前在中国的芳烃生产装置中是一种主流的生产工艺。
但是,环丁砜溶剂的降解问题是多数环丁砜抽提装置面临的一个问题,为保持循环溶剂酸碱度的稳定,防止设备腐蚀,需定期从回流芳烃罐加入一定数量的单乙醇胺。
图3环丁砜溶剂抽提工艺
1.4.4Distapex抽提蒸馏工艺
Distapex是德国Lurgi公司开发的以NMP为溶剂的工艺。
主要用于从煤焦油和裂解加氢汽油中回收纯苯,也用于从催化重整液中回收C8芳烃或甲苯。
Distapex工艺的产品纯度及其它质量都比较好,但NMP是一个含氮的有机溶剂,即使在溶剂分解温度以下操作,产品含有机氮的问题往往也难于避免。
。
如果对芳烃中有机氮含量有严格的限制,需采用常温下的白土精制。
采用Distapex工艺处理苯馏分、甲苯馏分和二甲苯馏分时,公用工程消耗随原料的变重而显著增大,因此该工艺比较适合处理较轻的苯馏分。
图4Distapex工艺流程简图
1.4.5Morphylane抽提蒸馏工艺
德国Koppers公司开发的Morphylane工艺,采用NFM为溶剂。
九十年代,我国科研单位也开展了以NFM为溶剂的抽提精馏工艺的研究,使以N-甲酰基吗啉为溶剂的抽提精馏工艺得到了进一步的发展。
由于NFM溶剂遇水容易水解,生成吗啉和甲酸,吗啉的常压沸点为128.4℃,在气体过程中部分吗啉会随芳烃一起被蒸发出来,从而造成芳烃含碱性氮,生成的甲酸还会腐蚀设备。
因此,Koppers公司回来对流程进行了改进,不采用原料洗涤,而是在ED塔顶设少量非芳烃回流来回收微量溶剂。
NFM溶剂的选择性明显优于NMP,Morphylane法能从相应的馏分中同时获得两种芳烃,如苯/甲苯或甲苯/二甲苯,产品纯度符合要求,但公用工程消耗高于两种芳烃分别抽提精馏方案。
近年来,KruppWood又提出了同时制取苯及甲苯的新流程,其主要做法是:
先将原料进行预分馏,切取苯馏分和甲苯馏分,然后将两个馏分进入同一个抽提精馏系列,苯馏分进入ED塔的下部,甲苯馏分送入ED塔上部,经过抽提精馏和芳烃与溶剂的分离后得到高纯度苯甲苯混合物,再通过精馏分离,得到苯、甲苯产品。
但是此改进后的流程仍然存在苯的回收率偏低的问题。
九十年代以来,我国科研单位对Morphylane工艺的一些弱点,即芳烃回收率偏低、溶剂回收苛刻度高,提出了一种改进的流程,主要是在流程中增加了一台溶剂闪蒸罐,通过闪蒸将贫溶剂中的芳烃进一步净化,从而既降低了溶剂回收的真空度和温度,又提高了芳烃的回收率。
图5Morphylane工艺流程示意图
1.4.6SED抽提蒸馏工艺
Distapex和Morphylane工艺与液液抽提相比,虽然流程简单、操作费用低,但芳烃收率偏低、、溶剂回收条件苛刻,且一般不适用于重整油苯抽提。
重整汽油C6馏分中苯的重量分数一般在30%~490%左右,如果采用单一的极性溶剂如NMP、NFM或环丁砜作为抽提精馏溶剂,在ED塔内容易形成两个液相,造成ED塔内剧烈沸腾甚至冲塔现象,使ED塔难以稳定操作。
为了解决芳烃含量低的原料的抽提精馏问题,中国石油化工科学研究院从增加溶剂的溶解性、降低溶剂回收的苛刻度入手,进行了大量的试验及模拟计算研究,筛选出了一种较为理想的助溶剂(COS),并最终开发了SED工艺。
在SED工艺中,采用环丁砜-COS的复合溶剂,显著增强了溶剂对C6馏分的溶解能力,避免ED塔出现两个液相,ED塔操作稳定,易于控制。
同时由于加入了助溶剂,还有效降低了溶剂回收塔的操作苛刻度,提高了苯的回收率。
而对于用芳烃含量较高的裂解加氢汽油为原料生产芳烃的SED工艺装置,采用单一的环丁砜溶剂既可以达到满意的苯回收率。
由中国石油化工科学研究院开发的用环丁砜为溶剂或SUL-COS符合溶剂进行抽提蒸馏生产轻质芳烃的新工艺(SED),代表了目前最先进的芳烃抽提技术,其工艺主要用来生产高纯度的苯和甲苯产品。
SED工艺的特点是工艺流程简单,物耗能耗低;
加氢汽油经预分馏后,C6、C7馏分进入抽提蒸馏塔(ED塔)进行抽提蒸馏,苯、甲苯产品纯度高;
占地面极少,投资低;
装置运行稳定性高,操作简单。
目前使用SED工艺生产单苯的装置在国内有扬子石化公司苯抽提装置、镇海石化公司苯抽提装置、燕山石化公司苯抽提装置、大连石化公司苯抽提装置、独山子石化公司苯抽提装置、中原石化公司苯抽提装置,而用于同时生产高纯度苯和甲苯的目前只有于2005年3月投产的上海赛科石油化工股份有限责任公司芳烃抽提装置。
SED工艺流程见图6。
图6SED工艺流程简图
1.4.7单塔实现芳烃和非芳烃分离的研究
据文献报道,Unde公司目前在研究开发进一步降低投资和运行费用的高级Morphylane抽提蒸馏工艺。
此工艺旨在根据DWC技术的理念,将此技术应用于芳烃抽提蒸馏工艺中来,将