文献综述.docx
《文献综述.docx》由会员分享,可在线阅读,更多相关《文献综述.docx(6页珍藏版)》请在冰豆网上搜索。
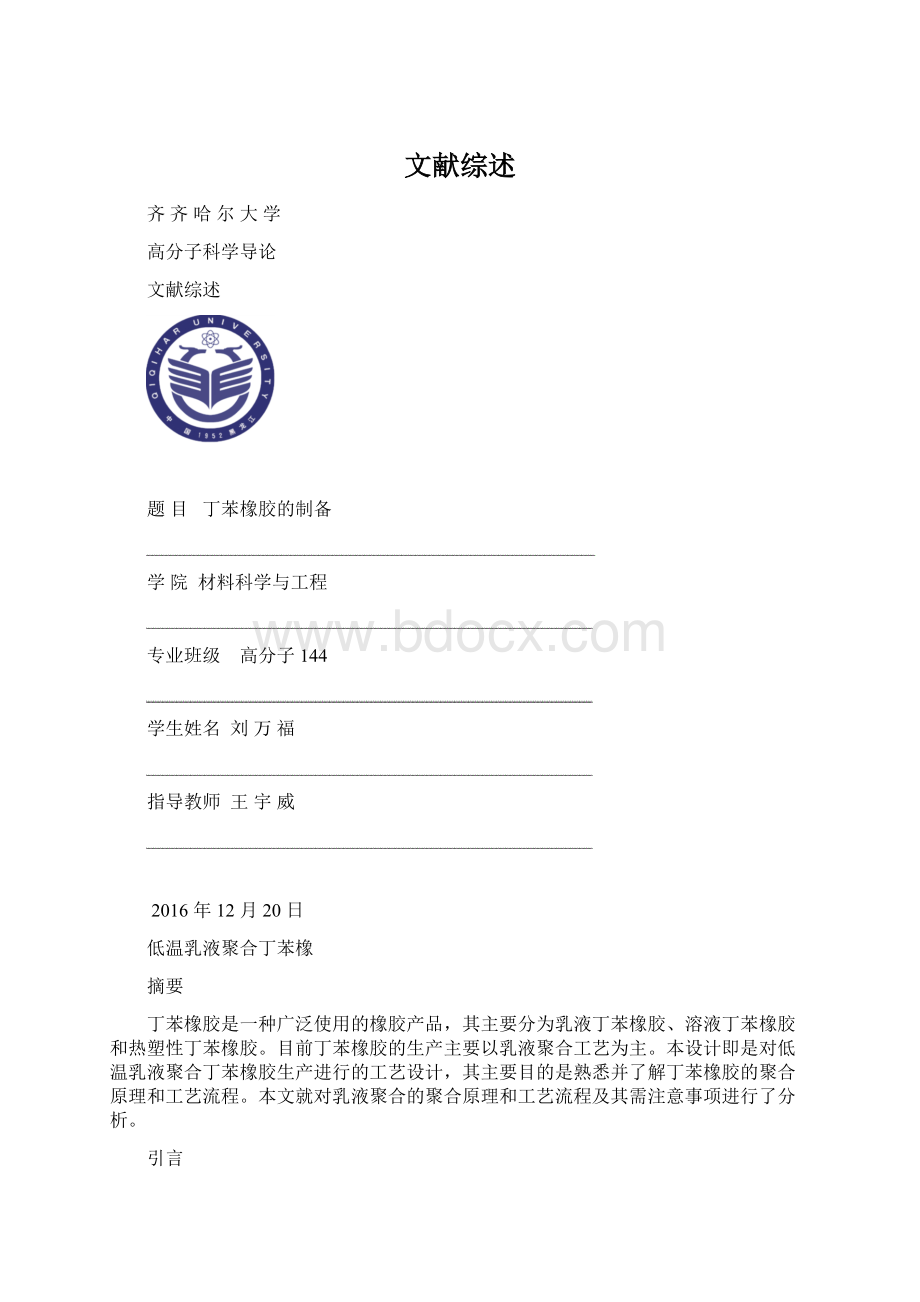
文献综述
齐齐哈尔大学
高分子科学导论
文献综述
题目丁苯橡胶的制备
学院材料科学与工程
专业班级高分子144
学生姓名刘万福
指导教师王宇威
2016年12月20日
低温乳液聚合丁苯橡
摘要
丁苯橡胶是一种广泛使用的橡胶产品,其主要分为乳液丁苯橡胶、溶液丁苯橡胶和热塑性丁苯橡胶。
目前丁苯橡胶的生产主要以乳液聚合工艺为主。
本设计即是对低温乳液聚合丁苯橡胶生产进行的工艺设计,其主要目的是熟悉并了解丁苯橡胶的聚合原理和工艺流程。
本文就对乳液聚合的聚合原理和工艺流程及其需注意事项进行了分析。
引言
丁苯橡胶( SBR) 是丁二烯和苯乙烯的无规共聚物, 是合成橡胶中工业化最早、产耗量最大的胶种,被大量用于制造各种汽车轮胎、胶管、运输带及胶鞋制品。
目前, 工业上丁苯橡胶的生产方法主要采用乳液聚合和溶液聚合两种方法。
乳液聚合生产工艺成熟, 生产规模大, 其生产能力约占 SBR 总生产能力的 80% 以上。
而低温乳液聚合方法又占乳聚丁苯橡胶生产的 90% 以上 。
20世纪60年代中后期,乳液聚合丁苯橡胶(E-SBR)的生产技术日臻成熟,生产工艺基本定型。
尔后朝着改进工艺、提高自动控制水平和生产装置大型化方向发展,目前已达到相当先进的水平。
本文综述了 E-SBR的制备技术及其改性与延伸加工技术。
1.E-SBR的制备
1.1调整聚合配方
引入第三单体 美国Goodyear轮胎与橡胶公司不用溶剂,通过内含抗降解剂、金属失活剂、 光敏剂、 颜料、增效剂、催化剂和促进剂的官能化苯乙烯与(氯化) 丁二烯在2%~3%(以有机组分计)离子型表面活性剂和10%~70%(以单体总量计)增塑剂存在下,于0~25℃ 乳液共聚,可制得含酰氨基的官能化E-SBR。
所用增塑剂有羧酸、磷酸酯、缩甲醛和N-丁基苯基磺酰胺等。
增塑剂在此起双重作用:
既是官能化共聚单体的助溶剂和分散剂,又是官能化E-SBR的增塑剂。
由于这种第三单体具有抗氧化性,所以该官能化E-SBR具有优异的抗氧化性能。
日本Zeon公司用p-N,N-二甲基氨基甲基苯乙烯作第三单体,开发出一种生热低且耐磨、可填充SiO2或炭黑、门尼粘度为10-200的E-SBR。
该E-SBR由大于40%的丁二烯单体单元、小于50%的苯乙烯单体单元和小于20%的含叔氨基 (部分叔氨基已被烃基季胺化)的苯乙烯单体单元组成。
Zeon 公司开发出一种由大于45%的丁二烯单体单元、小于20%的-甲基丙烯酸基氧三丙氧基硅烷单体单元和小于50%的苯乙烯单体单元组成的新型E-SBR和一种由大于45%的丁二烯单体单元、小于20%的-甲基丙烯酸基氧三丁氧基硅烷单体单元、小于20%的甲基丙烯酸羟乙酯单体单元和小于50%的苯乙烯单体单元组成的四元共聚E-SBR。
在合成E-SBR时加入0.01%-5%(以丁二烯计)的丙烯参与共聚,可使单体转化率在6.1h时达到70%,产物门尼粘度[ML(1+4)100℃]为72,而无丙烯存在时, ML(1+4)100℃只有46。
1.2聚合工艺的改进 用丙烯腈作亲水单体,过硫酸钾作引发剂进行苯乙烯与丁二烯的无皂乳液共聚合,获得最高转化率的条件是pH值为5和单体/水(质量比)为0.5。
用这种方法制得的E-SBR的拉伸强度、300%定伸应力和扯断伸长率均比常规E-SBR的差, 但其熟化速率却比常规E-SBR的快。
日本JSR公司发明了一种用两步聚合工艺生产中苯乙烯含量E-SBR的新方法。
该方法为:
先使44份丁二烯与51份苯乙烯在乳化剂和0.07份叔十二碳硫醇存在下乳液共聚,单体转化率达到63%时加入5份丁二烯和0.1份叔十二碳硫醇,继续聚合到转化率为80%,可得到结合苯乙烯质量分数为45%、门 尼粘度为93.5的E-SBR。
美国Xerox公司通过将单体加入聚合釜,引发聚合,待反应相开始放热后用惰性气体净化反应器,同时将聚合温度升到规定指标的方法制取了残余单体含量低的E-SBR。
德国Buna化工厂在由10个聚合釜组成的聚合釜系列合成E-SBR的过程中,将第一台聚合釜用作预混釜,预混料通过过滤器进入以后各釜进行聚合, 并将C10H7SO3H-HCHO缩合物、丁二烯-苯乙烯-马来酸酐共聚物或马来酸的Diels-Alder加合物之稀水溶液洗涤过滤器时形成的洗涤液回流入聚合系统,减少了釜内的挂胶量
2.E-SBR的改性与延伸加工
2.1共混改性
日本住友化学工业公司发明了一种以乙丙橡胶/E-SBR为基料的压缩永久变形性能优异的胶料。
其基本组成为:
20-50份乙烯--烯烃-非共轭二烯烃三元共聚橡胶,碘值8-40,特性粘数(在二甲苯中,70℃)大于1.5dL/g,80-150 份E-SBR;0-1.7份硫磺和0.2-5份给硫体(以弹性体总量为100份计)。
美国Goodyear轮胎与橡胶公司发明了一种在2%-35(以有机组分计)离子型表面活性剂和10%-70%(以单体总量计)增塑剂[如磷酸三 (丁氧基乙基)酯]存在下,使含抗降解官能团的乙烯基化合物 :
如[N-(4-苯氨基苯基)甲基丙烯酰胺] 与共轭二烯烃于40-100℃下共聚,制得稳定性弹性体,然后将其与普通E-SBR共混,制备聚合物分子链上结合有抗降解官能团母炼胶的方法。
2.2化学改性
Bridgestone日本公司在甲苯溶液中用-溴基苯基乙酸和叔丁氧基氯处理E-SBR,制得了耐热性能得到改善、适用于生产轮胎的卤化E-SBR,其硫化胶100%定伸应力、拉伸强度和伸长率均有大幅度提高。
该公司还在叔丁氧基氯存在下用四唑化合物(如1-苯基-5-硫基-1,2,3,4-四唑)改性E-SBR, 其硫化胶拉伸强度有较大提高,抗湿(干)滑性亦有所改善。
该公司还用丙烯酸或甲基丙烯酸接枝改性E-SBR,以生产耐热性和路面抓着力良好的充气轮胎。
接枝改性剂通式为R1R2C=CR3COOH[R1-3为氢、卤素、 取代或非取代烷基或链烯基(碳原子数不大于5)],用量为0.1-5.0份。
改性在有机卤试剂存在下进行。
3.环保型乳液聚合橡胶
所谓环保型丁苯橡胶(SBR)就是指在生产、加工和使用过程中不产生亚硝胺化合物等有毒物质,对环境无污染,对人体无毒害的SBR。
因此,在SBR的生产、加工过程中需实现稳定剂、防老剂、硫化促进剂、调节剂、终止剂等助剂的环保化,即使用“绿色助剂”。
20世纪80年代以来,国外对环保型SBR的开发非常活跃,主要是通过开发不产生亚硝胺化合物的环保型助剂或添加抑制剂的途径来控制橡胶制品中亚硝胺化合物的产生。
3.1使用不含亚硝基的聚合终止剂
目前,工业上用低温乳液聚合法生产SBR的工艺中多以二乙基羟胺(DEHA)、二硫代氨基甲酸盐(SDD)、亚硝酸钠等或其混合物为聚合终止剂。
其中SDD或DEHA在胶乳凝聚过程的酸性环境条件中易形成仲胺,仲胺可与硝基化试剂如亚硝酸钠以及空气中存在的氮氧化物反应生成亚硝胺化合物(如N-亚硝基二甲基胺、N-亚硝基甲乙胺、N-亚硝基二乙胺、N-亚硝基二正丙胺、N-亚硝基二异丙胺、N-亚硝基哌啶、N-亚硝基二正丁胺、N-亚硝基二乙醇胺等)。
因此,开发新的聚合终止剂以替代能够形成仲胺的SDD和DEHA,最大限度地减少或消除亚硝胺化合物的产生成为实现SBR环保化的主要目标之一。
在典型的低温乳液聚合SBR(苯乙烯与丁二烯的质量比为23:
77)生产过程中,以单体总质量分数4%的脂肪酸皂与松香酸皂(质量比50:
50)混合物为乳化剂,叔十二碳硫醇为相对分子质量调节剂,在5℃下进行聚合反应,转化率达到60%时加人多硫化钠(如Na2S4)终嗑该聚合反应。
该研究不仅考察了分别采用多硫化物与传统终止剂混合物作终止剂时,终止聚合反应后0.12 h时胶乳的门尼黏度以及总固物含量的变化情况,而且分析了这2种终止剂所生成的亚硝基化合物的情况。
结果表明,采用混合终止剂(0.100份SDD/0.015份Na2S4/0.040份NaNO2)与单独使用0.050份Na2S,终止剂时,虽然终止剂均具有良好的终止作用,即0.12 h时胶乳的门尼黏度和总固物含量变化很小,但在使用前者的体系中,每千克橡胶中亚硝基二甲胺含量高达500μg,而在使用后者的体系中,每千克橡胶中亚硝胺化合物的含量小于10μg。
3.2使用不产生亚硝胺化合物的聚合终止剂
2003年,中国石化齐鲁石化分公司发明了一种不产生亚硝基化合物的乳液聚合制备SBR的方法,其工艺主要是选用新化合物替代传统乳聚工艺中由SDD、DEHA和亚硝酸钠组成的聚合终止剂,生产出门尼黏度合格的环保SBR。
该研究开发的终止剂包括以下组分:
单芳基或单烷基二硫代氨基甲酸盐(D)、盐酸羟胺(E)、Na2S4或Na2S·9 H2O(S)。
终止剂的配合组成由D、E、S中的1种、2种或3种组成,但不包括单独的S组分。
在带有搅拌、夹套以及温度和压力指示的10 L聚合釜中,以脂肪酸皂/松香酸皂(质量比2.5/2.5)为乳化剂,过氧化氢二异丙苯(DIP)、过氧化氢蒎烷(PHP)或对盖烷过氧化氢(PMHP)为引发剂,将1,3-丁二烯/苯乙烯(质量比68/32)进行乳液聚合。
在5℃下聚合8-12h,当转化率达到62%-75%时,加入组合终止剂。
当传统组合终止剂中SDD为0.40份,DEHA为0.15份,NaNO2为0.08份时,终止效果良好,转化率从聚合终止时的70.32%经24 h后只变化到70.85%,但亚硝基化合物含量(以橡胶计)却达到了10μg/kg;而使用0.36份D、0.10份E与0.04份S组合的新型终止剂时,转化率从63.65%只变化到24h后的64.01%,亚硝基化合物含量为0,不仅完全达到了终止聚合的目的,而且环保特征明显。
且从橡胶的物理机械性能来看,在使用传统组合终止剂体系中,所得橡胶的门尼黏度为46.5,300%定伸应力(50 s)为17.0MPa,拉伸强度为24.5 MPa,扯断伸长率为471%;在使用新组合终止剂体系中,所得橡胶的门尼黏度为47.0,300%定伸应力(50 s)为16.6 MPa,拉伸强度24.6 MPa,扯断伸长率为475%,可以看出,两者所得橡胶的物理机械性能基本相同。
3.3添加亚硝胺化合物抑制剂
在乳液聚合SBR胶乳生产过程中,采用N-异丙基羟胺(NiPHA)、单乙胺和多乙胺为亚硝胺化合物抑制剂,其原料配方(质量份)为:
苯乙烯28,1,3-丁二烯72,脱离子水200,表面活性剂4.5,电解质0.3,Na、Fe盐0.02,甲醛次硫酸钠、0.08,叔十二碳硫醇0.3,有机过氧化物0.05-0.10,由KOH调节反应体系pH值到10.5-10.9,聚合反应温度为10-12℃,当转化率达到60%时,将NiPHA终止剂以及亚硝胺化合物抑制剂加入反应器中,脱除未反应单体,回收SBR胶乳,分析胶乳中亚硝胺化合物,经过凝聚后再分析SBR产品中亚硝胺化合物的含量,同时在聚合体系中添加高含量的亚硝胺母体物以考察这种抑制剂对抑制亚硝胺化合物生成效果。
例如,NiPHA质量分数为400×10-6,当不加亚硝胺化合物抑时,虽然胶乳中未测出亚硝胺化合物,但胶乳中可测出质量分数为7×10-9的N-亚硝基二甲胺;以质量分数为200×10-6的二乙基羟胺与质量分数为200×10-6的二丁基羟胺为终止剂,并添加质量分数为1125×10-6的多乙胺为抑制剂,所得胶乳(已脱除单体)中的亚硝胺化合物为无效量,橡胶产品中也未检出亚硝胺化合物;如果不加亚硝胺化合物抑制剂,橡胶产品中含有质量分数为6×10-9的N-亚硝基二丁胺和质量分数为3×10-9的N-亚硝基二甲胺。
以质量分数为400×10-6的DEHA为终止剂,不添加亚硝胺化合物抑制剂,同时在终止剂中加入亚硝胺母体物(如质量分数为1900×10-6的二乙胺与质量分数为400×10-6的三乙胺),不仅在胶乳(已脱除单体)中测出含有质量分数为1.3×10-9的N-亚硝基二乙胺,而且在橡胶产品中可检出6种亚硝胺化合物;如果在此终止剂配方中添加了亚硝胺化合物抑制剂(如质量分数为1%的单乙胺、质量分数为1%的单丁胺与质量分数为1%的单戊胺或质量分数为0.8%的多乙胺),即使加入了亚硝胺母体物(如质量分数为1900×10-6的二乙胺与质量分数为400×10-6的三乙胺),结果不仅在胶乳中未检出亚硝胺化合物,而且在橡胶产品也未测出亚硝胺化合物。
因此,即使在体系中添加了大量各种亚硝胺母体物的情况下,常规聚合终止剂与亚硝胺抑制剂(单乙胺和多乙胺类化合物)复合使用,也具有卓越的抑制亚硝胺化合物生成的作用,所得SBR中未测出亚硝胺化合物,实现了SBR的环保化。
3.4应用其他助剂
在SBR生产中,防老剂是用量较大、对环境污染较重的助剂。
目前,曾广泛使用的萘胺类及酚类化合物等已被淘汰,二胺类、喹啉类等化合物的发展迅速。
防老剂的持久性是生产环保型SBR的重要保障。
近年来,为了提高防老剂的持久性,开发高相对分子质量防老剂和反应性防老剂成为研究的热点。
高相对分子质量防老剂分为2种,一种称为大分子防老剂,一般相对分子质量为500-1000;另一种是由带抗氧基团的单体聚合而成,也称齐聚物防老剂。
反应性防老剂,也称键合型防老剂,它们带有反应性基团,能与聚合物反应,以化学键与之相连,可提高其耐迁移性、耐挥发性和耐抽出性,长期保持防护效能,达到环保作用。
在硫化促进剂中,过去用量最大、综合性能较好的次磺酰胺类促进剂N-氧联二亚乙基-2-苯并噻唑次磺酰胺(NOBS)已被美国和欧洲一些国家禁用,此外,如二乙基二硫代氨基甲酸锌、N-氧联二亚乙基硫代氨基甲酰-N′-氧联二亚乙基次磺酰胺、二硫化四甲基秋兰姆、二硫江苏南通申花化工公司是目前我国最大的丁苯橡胶生产厂家,生产能力约占全国丁苯橡胶总生产能力的25.95%;其次是中石油吉林石油化工公司,生产能力约占总生产能力的21化四乙基秋兰姆、一硫化四甲基秋兰姆等也属于有毒促进剂,应逐步淘汰。
我国正大幅度地削减NOBS的用量,其用量已由原来占次磺酰胺类促进剂的30%下降为2004年的19%,其产量基本上得到控制,同时不含亚硝胺化合物的N-叔丁基-2-苯并噻唑次磺酰胺促进剂产量已达到7.2kt/a。
4.国内需求量和年均增长率
我国丁苯橡胶的研究开发始于20世纪50年中期,自2003年我国对原产于俄罗斯、韩国和日本丁苯橡胶进行反倾销取得胜利以来,国内有多套丁苯橡胶新建或扩建项目建成投产。
截止到2006年底,我国丁苯橡胶的生产厂家有7家,总生产能力为65.5万t/a,其中乳聚丁苯橡胶的生产厂家有中石化齐鲁石油化工公司、中石油吉林石油化工公司、中石油兰州石油化工公司以及江苏南通申花化工公司4家,生产能力合计为49.5万t/a,约占我国丁苯橡胶总生产能力的75.57%;溶聚丁苯橡胶的生产厂家有中石化北京燕山石油化工公司、中石化茂名石油化工公司和中石化高桥石油化工公司3家,生产能力合计为16.0万t/a,约占我国丁苯橡胶总生产能力的24.43%。
其中.37%;再次是中石化齐鲁石油化工公司,生产能力约占总生产能力的19.85%。
随着生产能力的不断增加,我国丁苯橡胶的产量也不断增加。
1999年我国丁苯橡胶的产量只有29.32万吨,2001年增加到34.87万吨。
2003年由于国内市场的强劲需求和反倾销的实施,抑制了俄罗斯及日本、韩国等国家资源的进口,全国丁苯橡胶的产量首次突破40万吨,达到40.97万吨,比2002年增长15.6%。
2005年我国丁苯橡胶的产量进一步增加到51.42万吨,比2004年增长约9.46%。
2006年我国丁苯橡胶的产量约为54.00万吨,同比增长约5.02%,2001-2006年产量的年均增长率约为9.14%。
近年来我国丁苯橡胶产品品种牌号不断增加,尤其是充油产品的产量不断提高。
目前中石化齐鲁石油化工公司、中石油兰州石油化工公司、申花化工公司和中石化茂名石油化工公司的装置都可以生产充油产品。
中石化齐鲁石油化工公司开发的充油丁苯橡胶是含苯乙烯40%、充高芳烃油37.5份,特别适合用作轮胎的胎面胶和三角胶,其各项性能指标与国外产品基本一致。
参考文献;
1.Schule G O,Parker D K.Manufacture of rubbers having polymer-bound functionality[P].US,US 5 284 906.1994
2.王志勇. 高增亮. 李迎.不含亚硝基化合物的乳液聚合橡胶的制备方法[P] 中国发明专利, CN 1 429 847 A, 2003
3.吕百龄. 姜明辉.橡胶助剂手册 ( 第2章 ) :
硫化体系助剂[M] 北京:
化学工业出版社, 2000
4.Syrinek A R, C leverH A.Shortstop agents for vinyl polymerizations[ P] U S, U S 5 880 230, 1999
5.胡金生. 曹同玉. 乳液聚合[ J].北京:
化学工业出版社, 1987. 26 6.佐伯康治. 聚合物制造工艺[J].北京:
石油化学工业出版社, 1977. 250 7.王久芬.高聚物合成工艺 [M]. 北京:
国防工业出版社,2005.
8. 李克友. 张菊华. 向福如.《高分子合成原理及工艺学》.科学出版社
9.赵德仁. 张慰盛.高聚物合成工艺学(第二版)[M]. 北京:
化学工业出版社,1997. 10.于红军.高分子化学及工艺学[M]. 北京:
化学工业出版社,2000. 11.侯文顺. 杨宗伟.高聚物生产技术[M]. 北京:
高等教育出版社,2007.
12.崔小明. 国内外丁苯橡胶的供需现状及发展前景[J].化学工业,2008,26
(2):
23-30