制程抽样之品质分析剖析.docx
《制程抽样之品质分析剖析.docx》由会员分享,可在线阅读,更多相关《制程抽样之品质分析剖析.docx(28页珍藏版)》请在冰豆网上搜索。
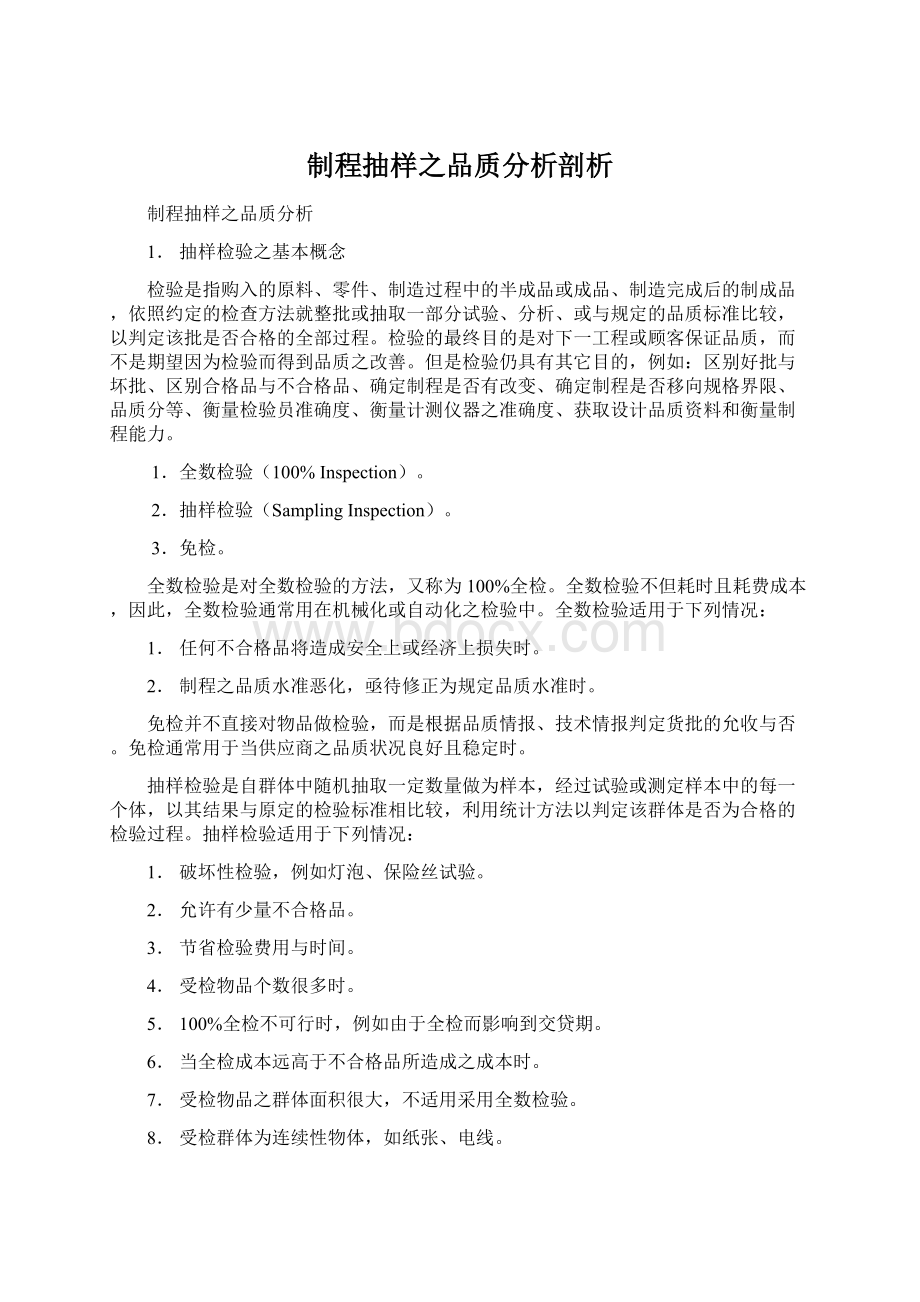
制程抽样之品质分析剖析
制程抽样之品质分析
1.抽样检验之基本概念
检验是指购入的原料、零件、制造过程中的半成品或成品、制造完成后的制成品,依照约定的检查方法就整批或抽取一部分试验、分析、或与规定的品质标准比较,以判定该批是否合格的全部过程。
检验的最终目的是对下一工程或顾客保证品质,而不是期望因为检验而得到品质之改善。
但是检验仍具有其它目的,例如:
区别好批与坏批、区别合格品与不合格品、确定制程是否有改变、确定制程是否移向规格界限、品质分等、衡量检验员准确度、衡量计测仪器之准确度、获取设计品质资料和衡量制程能力。
1.全数检验(100%Inspection)。
2.抽样检验(SamplingInspection)。
3.免检。
全数检验是对全数检验的方法,又称为100%全检。
全数检验不但耗时且耗费成本,因此,全数检验通常用在机械化或自动化之检验中。
全数检验适用于下列情况:
1.任何不合格品将造成安全上或经济上损失时。
2.制程之品质水准恶化,亟待修正为规定品质水准时。
免检并不直接对物品做检验,而是根据品质情报、技术情报判定货批的允收与否。
免检通常用于当供应商之品质状况良好且稳定时。
抽样检验是自群体中随机抽取一定数量做为样本,经过试验或测定样本中的每一个体,以其结果与原定的检验标准相比较,利用统计方法以判定该群体是否为合格的检验过程。
抽样检验适用于下列情况:
1.破坏性检验,例如灯泡、保险丝试验。
2.允许有少量不合格品。
3.节省检验费用与时间。
4.受检物品个数很多时。
5.100%全检不可行时,例如由于全检而影响到交贷期。
6.当全检成本远高于不合格品所造成之成本时。
7.受检物品之群体面积很大,不适用采用全数检验。
8.受检群体为连续性物体,如纸张、电线。
抽样检验是统计品质管制中之一重要领域,它可应用于零件、原料之进料检验。
买方从供应商所送来之贷批中抽取一定数量为样本,在样本中检验一些品质特性,根据样本之情报决定贷批为接受或拒绝。
被接受之贷批可送至生产线加工,而被拒绝之物品将被重新加工或报废。
抽样计划有三点重要之观念需加以说明:
1.抽样计划是用来判定贷批是否可被接受,而非估计贷批之品质。
大部分抽样计划并非设计用来估计贷批之品质。
2.抽样计划无法提供任何型式之品质管制。
抽样计划只是用来接受或拒绝贷批。
即使所有货批具有相同之品质水准,抽样计划有可能接受某些贷批但拒绝其他贷批。
被接受之贷批的品质水准可能并不比被拒绝的贷批好。
制程管制可以有系统地改善品质,但抽样计划无法达成此目的。
3.抽样计划之有效运用是做为确保产品符合规格之查核工具,它并非是用来改善产品品质之工具。
1.1抽样检验之优点和缺点
若与100%全检比较,抽样检验有下列优点:
1.抽样检验之检验次数少,因此较为经济。
2.抽样检验所需之人力较少,因此,人员之训练和监督都较简单。
3.抽样检验可降低搬动过程中所造成之损坏。
4.抽样检验可降低检验误差。
在全检中,检验员可能因疲劳而造成成大量之不合格品被接受。
5.将整批产品拒绝可给予卖方改善品质之压力。
6.可以应用在破坏性检验。
抽样检验也具有一些缺点,这些缺点包括:
1.具有将不好之产品予以允收之风险,同时亦具有将良好之产品予以拒收之风险。
2.发展抽样计划需要时间规划,同时要管理不同之抽样计划。
3.抽样所获得之产品资讯较少。
1.2抽样计划之种类
抽样计划可以用很多种方式来分类,若以数据的性质来分类,可分为计量值抽样计划(variablessamplingplans)和计数值抽样计划(attributessamplingplans)。
计量值数据是指可以量测且必须量测之品质特性,例如长度,重量等。
而计数值数据则是指
(1)可以量测但不需要实际值之数据;或
(2)不可量测之品质特性。
抽样计划如以抽样方式分类,可分为:
1.单次抽样(singlesampling)。
2.双次抽样(doublesampling)。
3.多次抽样(multiplesampling)。
4.逐次抽样(sequentialsampling)。
单次抽样是从批中随机抽取结果,决定
(1)允收;
(2)拒收;或(3)抽第二组样本再作判定。
多次抽样计划是双次抽样之延伸,可能是三次、四次或更多次。
一般而言,双次抽样计划中,每次抽样之样本大小低于单次抽样,而多次抽样中之样本大小则更低于单次抽样。
多次抽样计划最终可延伸成逐次抽样,亦即每次从货批中检验一件,根据检验结果,可采取下列任一种决策:
(1)允收;
(2)拒收;或(3)抽取下一件。
单次、双次、多次、和逐次抽样,可以由妥善设计,以达到相同之结果。
换句话说,这四种抽样方式可以由设计,以使得一货批在这四种程序下,均获得相同之允收机率。
基于下述理由,当我们在选择抽样计划时,必须考虑下列因素:
管理效率、由抽样计划结果所获得的资讯、平均检验件数和对于物流之影响。
表1-1为各种抽样检验形式的比较。
表1-1各种抽样检验形式的比较
项目
单次
双次
多次
对产品品质保证
几乎相同
对供应商心理上的影响
最差
中间
最好
总检验费用
最多
中间
最少
行政费用(含训练、人员、记录及抽样等)
最少
中间
最多
检验负荷的变异性
不变
变动
变动
对每批制品品质估计的准确性
最好
中间
最差
对制程平均数估计决策速度
最快
较慢
最慢
检验人员及设备的使用率
最佳
较差
较差
1.3随机抽样
随机抽样是抽样计划中之一重要观念,受检之样本必须是从货批中随机抽取且要具有代表性。
非随机抽取之样本,将使抽样检验之结果产生偏差。
例如,供应商知道检验员会从货批之上层抽取样本,可能会将好的货品故意排在上层。
随机抽机之一种技巧是将货批中之每一物件加以编号,再以随机化数表自货批中抽取样本。
如果物品本身已有序号或代号,则可省略编号之工作。
另一种方法是以三位数字代表物品在箱中长、宽、高之位置,例如乱数436代表抽取箱中第4层、第3行和第6列之物品。
在有些时候,货品之编号不存在或无法将每一物件编号。
此时可将贷批分成几个层次,每层又分成好几块,再从每一块中抽取样本。
1.4使用抽样计划之指导原则
抽样计划可依设计准则和检验方式区分成下列数项:
1.规准型抽样计划
又称为两定点计式(Two-pointscheme),此抽样计划考虑p1、p2两个货批不合格率及其相对应之货批允收率1-α和β,其中p1〈p2。
当送检验批之不合格率低于p1时,保证经由抽检验后之拒收机率不超过α,一般假设α=0.05%另一方面,当送验批不合格率高于p2时,保证经由抽验以后允收机率不超过β,一般设为β=0.1。
2.选别型抽样计划
当送验批被拒收后,整批全数检验,并将不合格品剔除,以合格品取代。
这种形式之抽样计划又可分成保证送验批平均吕质的AOQL型及保证单独送验批品质的LTPD型。
3.调整型抽样计划
此种抽样计划是由买方根据卖方的产品品质调整检验的方法。
买方先要求卖方送验批的品质不合格率优于AQL值--------,并按数次检验的结果,调整抽样之宽严程度。
抽样之宽严程度可分为正常、加严和减量三种。
4.连续型抽样计划
此种抽样主要是用在当被检验物件无法(或很难)自然形成贷批之情况,例如电视、电脑等以输送带装配之生产过程。
一个抽样计划说明判定贷批所使用之样本大小和允收或拒收货批之条件。
抽样方案(samplingscheme)是由数个抽样计划所组成之一组程序来定义,包含批量、样本大小、接受或拒绝的判定准则。
而抽样系统(samplingsystems)则是由一个或多个抽样方案所构成。
表1.2列举数种主要之抽样程序和其应用。
一般而言,抽样计划之选择需考虑抽样之目的和产品品质之历史资料。
另外,抽样方法之应用并非是静态,我们可能从一抽样计划自然演进到另一层次之抽样计划。
当买方与具有优良品质历史之供应商时,可能会先使用计数值抽样计划。
当抽样结果证明供应讷的品质确实不错时,抽样计划可能转到样本数较少之抽样程序,例如跳批抽样计划。
在长期往来后,如果供应商之产品品质稳定且良好时,买方可考虑停止抽样检验工作。
如果买方对供应之产品品质或品质保证活动一无所知时,可先采用能够确保产品品质不劣于某特定目标之抽样计划。
如果抽样计划成功地使用,而且供应商之产品品质令人满意,则可由计数值检验,转换至计量值检验。
计量值检验之情报可以用来协助供应商建立制程管制。
在供应商阶层有效地运用制程管制,可以改善供应商之制程能力,此时买方可以考虑停止进料之检验。
表1-2各种抽样程序
目的
计数值程序
计量值程序
为顾客/生产者确保品质水准
满足OC曲线特性之抽样计划
满足OC曲线特性之抽样计划
维持品质水准在一目标上
AQL系统
MIL-STD-105E
AQL系统
MIL-STD-414
确保平均出厂品质水准
AOQL系统
AOQL系统
减量检验
连锁抽样计划
窄界限规则
具有良好品质历史下减量检验
跳批抽样计划
双次抽样
跳批抽样计划
双次抽样
保证品质水准不低于目标值
LTPD计划
道奇--洛敏计划
LTPD计划
道奇—洛敏计划
抽样计划之使用具有寿命周期。
在投入品质保证之初,一个组织通常会把重点摆在验收抽样计划。
但随着品质保证组织之发展,一个公司会较少依赖抽样计划,而把重点摆在统计制程管制和实验设计方法。
利用抽样计划区别好批或坏批并无法改善产品品质水准。
产品品质之改善,有赖制程管制和实验设计方法之有效运用。
2.计数值单次抽样计划
2.1单次抽样计划之定义
单次抽样计划是依照样本大小n,允收数(acceptancenumber)c来决定。
假设批量大小N为10000,则单次抽样计划
n=120
c=2
代表从含10000件之批中,随机检验120件。
如果在这120个样本中,检验出之不合格品数等于或小于2件,则判事实上为允收;否则为拒收。
允收数c可视为样本中,允许出现之不合格品数的上限值。
2.2操作特性曲线(OperatingChargingCharacteristicCurve,简称OC曲线)
一、操作特性曲线之定义
操作特性曲线为评估验收抽样计划的一个重要量测。
此曲线描述在不同不合格率下,货在被允收之机率。
在OC曲线上有三个重要的点(参考图1-1)须加以说明。
当产品之不合格率等于p1时,其允收机率Pa=1-α,α称为生产者风险,(producer’srisk),p1称为称为可接受品质水准(AcceptableQualitylevel,简称AQL)。
当不合格率等于p2时,产品被允收之机率为β,β称为消费者风险(consumer’srisk),p2称为界限品质水准(LimitingQualityLevel,LQL)或称为批容许不良率(LotTolerancePercentDefective.LTPD)。
p3称为无差异品质水准(IndifferenceQualityLevel,简称IQL),此时允收机率Pa=0.5。
操作特性曲线的制作过程说明如下。
假设批量为N,今从其中抽出n件样本,发现d件为不合格品之机率为:
P{d}=
允收机率是指当不合格品数d小于或等于允收数c之机率,可计算如下:
Pa=P{d≤c}=
假设各批之平均不合格率为p=0.01,n=120,c=2,则允收机率为:
Pa=P{d≤2}=
=
=0.8804
若将不同p值下之允收机率Pa算出,则可绘出OC曲线。
表11-3为在数个不同p值下的允收机率,图1-2为OC曲线。
表1-3n=120,c=2之单次抽样计划的允收机率
p
Pa
0.005
0.9999
0.010
0.8804
0.020
0.5687
0.030
0.2984
0.040
0.1372
0.050
0.0575
0.060
0.0225
0.070
0.0083
0.080
0.0030
0.090
0.0010
二、样本大小n及允收数C对于OC曲线之影响
理想化之OC曲线(见图1-3)可在100%检验,且无检验误差之情况下获得。
另外,增加样本大小n亦可获得接近理想化之OC曲线。
一般而言,改变允收数c,对于OC曲线之斜率不会造成太大之改变。
允收数c降低,OC曲线将向左移。
当不合格率很小时,较小之c值比较大之c值具有更高之区别能力。
样本大小n及允收数c对于OC曲线之影响为:
1.样本大小n降低,OC曲线将更平缓,当n降低,且n与c之比例保持一定,则生产者风险及消费者风险都将增加(见图1-4)。
2.允收数c降低将造成α增加,但β将减小。
3.当样本大小n固定,但c值改变时,c值愈小,OC曲线愈接近原点(见图1-5)。
三、OC曲线之种类
当样本来自于一很大之批,或自连续数批产品以随机之方式检验,则二项分配是计算货批允收机率Pa之正确机率分配,此种情况下所获得之OC曲线称为B型曲线(typeBOCCurve),A型OC曲线则是用于计算一独立送验批且批量大小为有限之产品。
此时样本中之不合格品是以超几何分配(hypergeometricdistribution)来描述。
一般而言,A型曲线较B型曲线为低(参见图1-6),当n/N≤0.1时,此二种曲线并无太大差别(注:
当n/N≤0.1时,超几何分配可以利用二项分配来逼近。
)
四、OC曲线之特性
在实务上,有两种特殊但并非正确之抽样计划需加以说明。
第一是使用允收数等于0之抽样计划,第二是以批量之固定比例做为样本大小。
以下说明在此两种特殊设计下,OC曲线之变化。
1.允收数c=0之OC曲线与c≠0之曲线有相当大这差别,c=0时,OC曲线为一下凸之曲线(参见图1-7)。
此种特性造成即使p很小时,允收机率仍然很小。
这种情况对于买卖方都不利。
如果将货批退回给卖方,则可能有许多批是不需退回的,此将造成成卖方在生产上之延误。
如果卖方以100%全检不合格之货批,则不少品质不错之货批将被筛选,此时抽样检验将失去意义。
第十三章所介绍之连锁抽样计划,可用来解决上述之问题。
2.若样本大小n为批量N之固定比例,则不同之样本大小将有不同程度之保证(参见图1-8)。
3.双次抽样计划
一、双次抽样计划之定义
单次抽样计划是以第一次样本之检验结果,来判定拒收或允收。
在双次抽样计划中,在检验完第一组样本后之可能情况为:
(1)接受该批;
(2)拒绝该批;或(3)检验第2组样本。
在检验完第二组样本后,可能情形有
(1)拒绝;或
(2)接受。
一个双次抽样计划包含下列参数据:
n1=第一次抽样的样本大小
c1=第一次抽样的允收数
r1=第一次抽样的拒收数
n2=第二次抽样的样本大小
c2=两组样本合并后的拒收数
双次抽样计划之实施过程如图1-12所示。
C2为在第一组样本及第2组样本中,允许存在之不合格数(注:
在实际上,常见之错误是将c2比较)。
其中r2=c2+1以保证在第二次抽样后,能达成决定(不是拒收,就是允收,无第三种情况)。
假设双次抽样计划书为
n1=80,c1=0,r1=3
n2=80,c2=3,r2=4
双次抽样之实施过程为先抽取80件为1样本。
若在此样本中,并无任何不合格品,则允收该批。
若发现多于3件不合格品,则拒收。
如果不合格品数为1或2件,则抽取第2组样本(在此例仍为80件)。
若在第1组样本及第2组样本中发现之总不合格数小于或等于3件,则允收;否则拒收该批产品。
双次抽样计划亦可以由四个参数来定义
n1=第一次抽样之样本大小
c1=第一次抽样之允收数
n2=第二次抽样之样本大小
c2=两次抽样之允收数
假设n1=50,c1=1,n2=100,c2=3。
首先自批中抽取50个样本,并记录其中之不合格品数d1。
若d1≤c1则允收该批,不需第二次抽样。
若d1>c2,则拒收该批。
若c1若d1+d2≤c2=3,则允收该批;若d1+d2>c2=3,则拒收该批。
在上述双次抽样之定义下,r1=r2=c2+1。
二、双次抽样计划之OC曲线
图1-12双次抽样计划之流程
假设双次抽样计划为n1=48,c1=1,n2=96,c2=3。
令P
代表第一次抽样即予允收之机率,P
为第二次抽样才予允收之机率。
Pa为整体之允收率,其中Pa=P
+P
。
若第一次抽样即予允收,则在第一次抽样所发现之不合格品数d1,只能为0或1(亦即小于或等于c1)。
若为合格率为0.05,则
第二次抽样才予允收之可能情形有:
1.d1=2且(d2=0或d2=1)
2.d1=3且d2=0
第一种情形发生之机率为
P{d1=2,d2≤1}=P{d1=2}P{d2≤1}
=
=(0.2664)(0.044)
=0.0117
第二种情形发生之机率为
P{d1=3,d2=0}=P{d1=3}P{d2=0}
=
=0.0016
因此
=P{d1=2,d2≤1}+P{d1=3,d2=0}=0.0117+0.0016=0.0133
在p=0.05之下,货批之允收机率Pa为
Pa=
0.3006+0.0133=0.3139
依照同样之程序,我们可以计算在不同之p值下的Pa值,以绘制OC曲线。
(参见图1-13)。
4.MIL-STD-105E(ANSI/ASQCZ1.4)
4.1MIL-STD-105E之历史背景
计划值这标准抽样程序是在二次大战期间开发出来的。
最原始这版本称为JAN-STD-105(全名为jointarmy-navystandard105),系在1949年设计完成。
在1950年,JAN–STD-105被修订为MIL-STD-105A。
随后在1958、1961和1963年分别推出MIL-STD-105B,MIL-STD-105C和MIL-STD-105D。
在1964年,美国、英国和加拿大三国共同修正MIL—STD—105D,称为ABC-STD-105(注:
ABC代表Ameriba、Britain和Canada)。
MIL-STD-105D的民间版是在1971年推出,由美国国家标准局(AmericanNationalStandardInstitute,ANSI)将其列入美国国家标准。
称为ANSI/ASQCZ1.4。
最近这修订版为1981。
在1974年,国际标准化组织(InternationalOrganizationforStandardization,ISO)将ANSI/ASQCZ1.4稍作修正,将其编列为ISO2859。
我国中央标准局于1970年公布之国家标准CNS2779和日本的JISZ9015国家标准,都与MIL-STD-105标准类似。
目前之最新版本为1989年5月10日,美国军备研究发展工程中心公布之MIL-STD-105E。
105E和过去105D版本相类似,只是在文字部分加以修订,另行编排。
MIL-STD-105E是以可接受品质水准(acceptablequalitylevel,简称AQL)基础之抽样计划(注:
AQL又译为允收品质水准)。
AQL是指买方可接受之品质水准。
在以AQL为基础之检验计划中,货批不是很明确地被拒收就是被允收,并不包含选别检验。
选别检验虽然可使出货之不合格率降低,但必须付出额外之检验成本,如果买、卖双方是属于同一公司或组织,品质与成本间之平衡,可以很容易地获得解决。
但如果属于不同公司,则会产生下列问题。
1.第一个问题是应该由那一方承担选别检验之成本。
卖方(生产者)对于买方实施筛选之额外检验成本,可能不乐意接受,此乃因为卖方无法控制或无法正确评估买方在筛选上之检验成本。
反之,如果筛选工作是由卖方来执行,买方可能不乐意接受卖方检验之结果。
2.如果由买方执行筛选,并只退回不合格品,则无法激励卖方改善品质。
一般而言,以AQL为基础之抽样检验,对于买方较有利,而选别检验则有利于卖方。
4.2MIL-STD-105E之使用
MIL-STD-105E提供三种抽样型式:
单次抽样、双次抽样和多次抽样。
每一种抽样计划又可分为正常检验(normalinspection)、加严检验(tightenedinspection)和减量检验(reducedinspection)。
抽样计划开始时,通常是先使用下沉检验,除非另有规定,加严检验是用在当卖方之品质变差时,而减量检验是用在卖方之品质良好之情况。
MIL-STD-105E之重点为AQL,当AQL≤10%时,可用来表示不合格率或百件中之不合格点数,当AQL大于10%,则仅能用来表示百件中之不合格点数。
MIL-STD-105E使用之AQL是按照几何级数递增,每一级大约是前一级的1.585倍。
AQL通常是在契约中订定,或者由负责当局指定。
不同之不合格点或不合格品可以使用较低之AQL值。
AQL也可依
(1)检验成本与修理成本之比例;
(2)可能发现问题之地方(顾客、终检、制程);(3)不合格品之处理方式(报废、修理、特采);(4)生产方式(全自动、半自动、人工);(5)鉴定不良之难易程度来决定。
当检验成本与修理成本之比例低、可能在顾客处发现问题、不合格品需报废、全自动生产、很难鉴定不良之情况下,适合采用较低AQL值。
在MIL-STD-105E中,样本大小是由批量大小和检验水准来决定(见表1-7)。
检验水准是用来描述检验量之相对大小。
不同之检验水准对于生产者有大约相同之保证,但对于消费者则有不同之保证程度。
MIL-STD-105E提供七种检验水准,分别为一般检验水准(generalinspectionlevel)Ⅰ,Ⅱ,Ⅲ,功能和特殊检验水准(specialinspectionlevel)S-1,S-2,S-3,S-4。
大多数之产品采用一般之检验水准,其中检验水准Ⅱ称为正常检验水准(normalinspectionlevel)。
水准Ⅰ较水准Ⅱ具较低区别能力,而水准Ⅲ较水准Ⅱ有更高之区别能力。
水准Ⅲ之相对检验数大约为水准Ⅱ之两倍,而水准Ⅰ则为水准Ⅱ之一半,特殊检验水准是保留给检验成本昂贵或需破坏性检验之产品。
此种检验水准是用在需要较小样本或者是较大之抽样风险(必须或是可以)容忍时,检验水准需在买、卖双方之合约中注明或由有关决策单位决定。
MIL-STD-105E之使用程序可分为下列步骤:
1.选择AQL。
2.决定检验水准(InspectionLevel)。
3.决定批量大小。
4.求样本大小(查表1-7)。
5.决定适当之抽样计划(单次、双次或多次抽样)。
6.决定适当之抽样计划表。
7.决定采取正常或减量检验。
批量大小
特殊
检验
水准
一般
检验
水准
S-1
S-2
S-3
S-4
Ⅰ
Ⅱ
Ⅲ
2-8
A
A
A
A
A
A
B
9-15
A
A
A
A
A
B
C
16-25
A
A
B
B
B
C
D
26-50
A
B
B
C
C
D
E
51-90
B
B
C
C
C
E
F
91-150
B
B
C
D
D
F
G
151-280
B
C
D
E
E
G
H
281-500
B
C
D
E
F
H
J
501-1200
C