高炉炼铁仿真操作系统操作规程.docx
《高炉炼铁仿真操作系统操作规程.docx》由会员分享,可在线阅读,更多相关《高炉炼铁仿真操作系统操作规程.docx(12页珍藏版)》请在冰豆网上搜索。
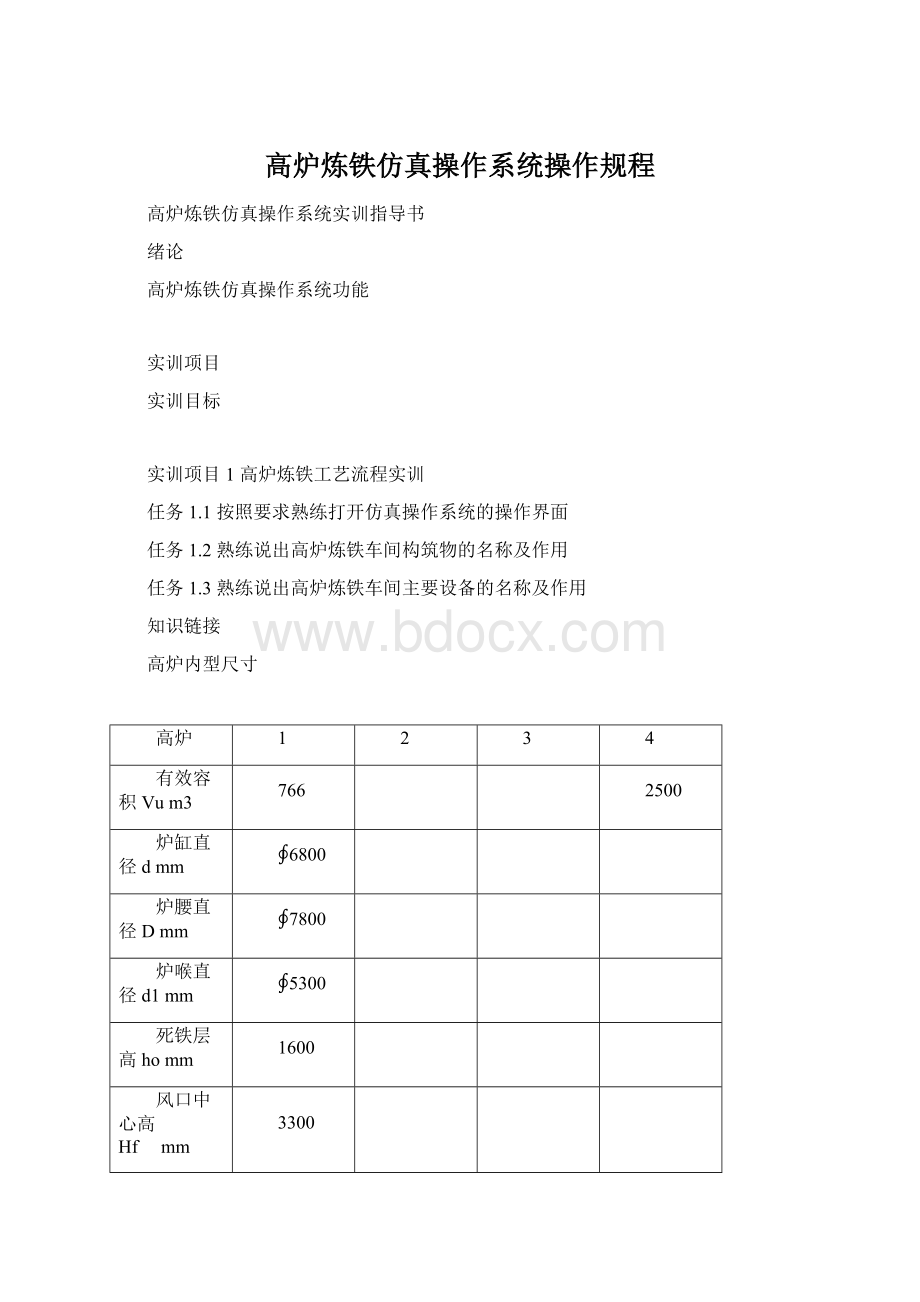
高炉炼铁仿真操作系统操作规程
高炉炼铁仿真操作系统实训指导书
绪论
高炉炼铁仿真操作系统功能
实训项目
实训目标
实训项目1高炉炼铁工艺流程实训
任务1.1按照要求熟练打开仿真操作系统的操作界面
任务1.2熟练说出高炉炼铁车间构筑物的名称及作用
任务1.3熟练说出高炉炼铁车间主要设备的名称及作用
知识链接
高炉内型尺寸
高炉
1
2
3
4
有效容积Vum3
766
2500
炉缸直径dmm
∮6800
炉腰直径Dmm
∮7800
炉喉直径d1mm
∮5300
死铁层高homm
1600
风口中心高Hf mm
3300
炉缸高h1 mm
3800
炉腹高h2 mm
2800
炉腰高h3 mm
1900
炉身高h4 mm
10900
炉喉高h5 mm
2200
有效高hu mm
21600
炉腹角 α
79°15ˊ40″
炉身角 β
83°43ˊ03″
风口数目 个
18
30
风口间距 mm
1169.4
实训项目2高炉上料实训
仿真实训条件:
(一)高炉槽下筛分、称量、运输系统的组成
高炉槽下系统由矿槽、焦槽以及皮带机三部分组成,矿槽采用双排,设有大小矿槽12个,大矿槽测为6个烧结矿槽,小矿槽侧由2个普通球团矿槽、2个块矿槽、2个熔剂或锰矿槽构成设有5个焦槽,各矿槽下均设给料机、振动筛、称量漏斗等设备。
配置一个矿石中间称量漏斗与一个焦炭中间称量漏斗,矿焦通过中间称量漏斗、经皮带上炉顶。
同时拥有小块焦回收系统,1A-6A按烧结矿考虑,1B-6B按球团矿、锰矿熔剂、生矿考虑。
4.1.1 各高炉矿槽、焦槽配备(见表4—1)
表4—1 各高炉矿槽配备情况
项目
炉别 矿槽数(个) 焦槽数(个)
烧结矿槽 球团矿槽 块矿槽 焦丁槽
1、2号高炉 6× m3 2× m3 2× m3 1× m3 4× m3
储存时间(h):
焦炭:
8h;烧结矿:
12h;球团矿:
12h;碎焦:
8h;碎矿:
8h。
4.1.2 槽下筛分、秤量设备(见表4—2,表4—3)
表4—2 筛分设备 表4—3 秤量
类别
规格 焦炭筛 烧结矿筛 类别
名称 矿 焦
型 式 BTS-150-330 BTS-150-330 称量物 烧结矿
球团矿
块矿 焦炭
能力(t/h) 200 250
筛面尺寸(mm) 15003300 15003300
筛分效率 秤容积(m3) 6.9 6.9
装料制度OC或COL(大粒度矿)、OS(小粒度矿)
(二)主要控制功能
矿焦槽所有入炉原料采用分散筛分、分散称量+集中称量流程。
按预先设定的排料程序,将筛分合格后的入炉原料依次给入中间漏斗称量后,再依次排放到相应的胶带机。
槽下设有排料程序控制,根据物料组成与上料要求任意选择,一般情况下焦炭可以选择3-4个称量漏斗同时工作,烧结矿可以每次选择3-4个称量漏斗,杂矿可以选择3-4个称量漏斗进行不同形式的组合供料。
知识链接:
原燃料供给与控制
1)分配原则:
炉况处于非正常状况的高炉,在恢复阶段供给理化性能好的原、燃料。
2)原燃料使用技术要求
(1)矿槽使用由高炉提出,主管副作业长(或生产技术室主任)批准。
(2)矿槽漏嘴必须轮流使用,漏嘴堵塞或故障不能漏料时必须及时处理。
(3)高炉工长按用料规定配料,计算后写料单。
(4)上料PLC的控制程序,必须确保按料单准确漏料,秤量误差规定如下:
矿石<0.5%,焦炭0.3%~0.5%;与此同时,必须保证重量补偿功能工作正常。
(5)临时调剂变料,在5批之内可不用变料通知单,超过时则必须发变料通知单并输入微机内,停止时及时消除。
(6)秤量校对:
每班核对一次焦炭秤、矿石秤的零点。
3)合理炉料结构
高炉冶炼用的原料主要有:
烧结矿、球团矿和块矿,使用时必须合理搭配,最佳方案是:
高碱度烧结矿(R=1.75~1.85),配低碱度球团或块矿(硅石可用以临时调碱度)
特殊情况也可以按下列要求配料:
以块矿为主搭配高碱度烧结矿时,可用石灰石调碱度。
灰石必须装在每批料的中间或一车料的上边,把灰石分布到高炉中心。
准确、及时,为高炉上好每一批精料,全心全意为高炉服务。
二. 目标
1、入炉粉末率≤4%
2、影响高炉上料为0
3、原燃料数据准确率为100%
4、设备点巡检,润滑率为100%
5、安全事故为0
6、设备事故为0
环形布料;工作特点是倾角固定的旋转运动。
(2)定点布料;工作特点是方位角固定的布料。
(3)螺旋布料;工作特点是倾角变化的旋转布料,倾角变化分为倾角渐变的螺旋形布料和倾角跳变的同心圆布料(4)扇形布料,工作特点是方位角在规定的范围反复变化。
4原、燃料
4.1 供料系统的主要设备
4.1.1 各高炉矿槽、焦槽配备(见表4—1)
表4—1 各高炉矿槽配备情况
项目
炉别 矿槽数(个) 焦槽数(个)
烧结矿槽 球团矿槽 块矿槽 焦丁槽
1、2号高炉 6× m3 2× m3 2× m3 1× m3 4× m3
储存时间(h):
焦炭:
8h;烧结矿:
12h;球团矿:
12h;碎焦:
8h;碎矿:
8h。
4.1.2 槽下筛分、秤量设备(见表4—2,表4—3)
表4—2 筛分设备 表4—3 秤量
类别
规格 焦炭筛 烧结矿筛 类别
名称 矿 焦
型 式 BTS-150-330 BTS-150-330 称量物 烧结矿
球团矿
块矿 焦炭
能力(t/h) 200 250
筛面尺寸(mm) 15003300 15003300
筛分效率 秤容积(m3) 6.9 6.9
各高炉内型尺寸
炉别
项 目 1#、2#
有效容积Vu m3 766
炉缸直径d mm ∮6800
炉腰直径D mm ∮7800
炉喉直径d1 mm ∮5300
死铁层高ho mm 1600
风口中心高Hf mm 3300
炉缸高h1 mm 3800
炉腹高h2 mm 2800
炉腰高h3 mm 1900
炉身高h4 mm 10900
炉喉高h5 mm 2200
有效高hu mm 21600
炉腹角 α 79°15ˊ40″
炉身角 β 83°43ˊ03″
炉缸断面积A m2 36.30
炉腰断面积B m2 47.76
炉喉断面积C m2 22.05
Vu/A 21.10
Hu/D 2.769
炉缸容积V1 m3 137.93
炉腹容积V2 m3 117.32
炉腰容积V3 m3 90.74
炉身容积V4 m3 371.55
炉喉容积V5 m3 48.51
工作容积Vg m3 646
风口数目 个 18
风口间距 mm 1169.4
5.1.2高炉冷却结构(见表5—2)
表5—2 各高炉冷却壁段数
冷却壁型
炉别 光面段 带凸台段 炉底冷却形式
1#、2# 1~7段
(120mm) 8~13段
(捣打SiC捣料) ∮76×12mm
水冷
5.1.3 高炉主要阀门直径(见表5—3)
表5—3 各高炉主要阀门直径
阀门(mm)
炉别 1#2#
炉顶
放散阀 ∮650×2
均压阀 ∮200×2
均 压∮300
放散阀 ∮1890
煤气切断阀 ∮1200
放风阀 ∮ ×1
调节阀组 ∮ ×3
5.2 高炉工艺参数
5.2.1 鼓风工艺参数(见表5—4)
表5—4 鼓风工艺参数
项目
炉别 冶炼强度1.60~1.85(t/m3.d)
标准风速140~180(m/s)
鼓风动能104(Mpa/GJ)
炉项压力0.15~0.20(MPa)
压差0.12~0.16(Mpa)
5.2.2 炉渣化学成份(见表5—5)
表5—5 炉渣的化学成份
炉渣的化学成分 (%)
铁种 CaO SiO2 MgO AI2O3 FeO碱度
炼钢铁 40~42 37~39 8.0~8.5 8.0~9.0 <0.60 1.15±0.02
铸造铁 40~41 39~40 8.0~8.5 8.0~9.0<0.50 1.00~1.05
5.2.3 高炉各部位水温差控制范围见(表5—6)
表5—6 高炉各部位水温差控制范围
部位 炉缸 炉腰 炉身
下部 炉身
中部
1~2段 3~5段
水温差范围(℃) <3 <4 6~8 8~10 10~12
热流强度(KJ/m2.h) 34000 37000 35000 ~
5.2.4 生铁含硅量与铁水温度(见表5—7)
表5—7 生铁含硅量和铁水温度
炉 别 生铁含硅[Si]% 标准偏差(σsi) 铁水温度(℃)
1#、2# 0.35—0.85 ≤0.15 1400~1450
5.2.5各高炉冷却水水压规定值(见表5—14)
表5—14 各高炉水压规定数值
部位
炉别 炉 缸
(Mpa) 风 口
(Mpa) 平 台
(Mpa) 中 部(Mpa) 上部 (Mpa)
1#、2# 0.35 1.00 0.35 0.30 0.25
注:
对冷却水质的要求
(1)PH值:
6~8;
(2)悬浮物:
小于200mg/L;
(3)固形物:
小于500mg/L;
(4)进水温度:
20℃~30℃,最高温度不超过35℃。
高炉基本操作制度:
送风制度是根据冶炼条件选择适宜的风口直径和长度、调整风量、维持较高的风速和动能,以达到风口活跃和炉缸工作均匀。
鼓风参数控制见表5—4。
1)风口面积的选择
在一定的原燃料条件和冶炼强度下,要求有一个合适的风口面积。
在生产条件变化较大时,风口面积要相应地调整,特别是炉缸工作变差,上部调剂无效时,要果断地调整风口面积和分布。
(1)有计划地改变冶炼强度、炉顶压力和喷吹数量时,要相应地扩大或缩小风口面积;
(2)冬季冷风温度降低、原燃料质量恶化、渣铁运输困难不能保证按时放渣、出铁时,可根据情况适当缩小风口;
(3)炉况异常、炉缸不活跃、吹不进风、在上部调剂效果不明显时要及时缩小风口(或堵风口);
(4)开炉和长期休风后的复风,为保证送风后炉况稳定和安全出铁,需临时堵部分风口;
2)风量与风压
风量是强化高炉冶炼最积极的因素。
在炉况稳定顺行的条件下,增加风量有利于提高冶炼强度、活跃炉缸。
高炉必须根据原燃料的实际条件(也就是透气性的好坏)确定本炉正常生产时压差和对称的风压与风量。
3)热风温度
风温是鼓风的质量标志。
鼓风带入的热量是高炉主要热源之一。
提高风温有利于活跃炉缸、提高喷吹物数量,降低焦比。
因此,在喷吹煤粉的条件下,热风温度应保持最高水平,正常生产时不能将风温做为调剂手段。
必须时,应遵循下列原则。
降风温时,一次降到所需水平,一般不超过正常风温15%。
恢复时视炉温和炉况接受程度逐步提高至所需水平,其升温速度可控制在每小时50~100℃的水平,每次不大于30℃。
热风炉换炉时,风温波动应小于20℃。
4)喷吹煤粉
高炉喷吹煤粉不仅可以代替焦炭,而且有利于炉况稳定顺行。
在不富氧的条件下,一般喷吹120~150千克/吨铁。
富氧2~3%可喷吹150~180kg/t铁。
喷吹煤粉力求广喷、匀喷,促进炉缸圆周工作均匀。
做为热源调剂时注意其同焦炭的置换比换算和热滞后性。
5)富氧
富氧可提高冶炼强度,提高理论燃烧温度,有利于煤粉的充分燃烧,从而提高喷吹量和置换比。
1%的富氧相当于增加4.76%的风量。
富氧同高风温、大喷吹量同时使用时,节焦增产效果更显著。
现有原料条件下经济富氧率<4%。
5.3.2.3造渣制度
1)技术要求:
(1)具有良好的稳定性和流动性;
(2)具有足够的脱硫能力;
(3)有利于获得稳定充沛的炉温;
(4)有利于维护高炉内型剖面的规整;
(5)根据生产需要,有利于形成较为稳定的渣皮并有利于消除炉缸堆积物和附着物。
2)渣碱度及化学成份(见表5—5)
(1)炉渣碱度应保持在1.15~1.20范围内;
(2)炉况不顺时,可相应选下限碱度;
(3)冶炼中锰制钢铁时,碱度可选中下限;
(4)硫负荷升高至5kg/t·Fe时,应选中上限;
(5)炉缸水温差升高、炉身下部及以下部位炉皮破损、冷却壁损坏严重时,可选中上限碱度;
(6)选择碱度时必须注意同炉温的对称、匹配,不允许长期低碱度、低炉温操作,更不允许高碱度、低炉温操作。
3)熔剂调节
(1)调节炉渣碱度以终渣碱度为依据;
(2)正常情况调节石灰石量一次以30kg为宜,最多不超过60kg。
炉凉出黑石头渣时要果断调整碱度,按规定炉渣碱度的下限操作。
4) 洗炉
洗炉方法分为化学洗炉和物理洗炉两种方法。
提高炉温降低碱度是任何方法的必备条件。
(1)物理洗炉方法
边缘布焦,发展边缘气流,利用煤气流冲刷粘结物,采用此措施时,需要减轻负荷15%~18%。
这种方法对风口区以上较为有效。
净焦洗炉连续不许超过15批(此法处理高炉下部粘结或堆积物)。
(2)化学洗炉方法
各种洗炉剂作用和选用标准:
均热炉渣是含FeO及硅酸盐的洗炉剂,主要是以这些化合物造成熔化温度较低的含FeO较高的初、终渣,清洗碱性粘结物和堆积物比较有效。
锰矿及含Mn的洗炉剂,主要是利用MnO有一定的脱硫作用,故还可降低渣碱度,渣碱度降低后洗炉效果更好。
萤石或含氟矿石,主要利用其造成熔化温度低、流动性好的炉渣参与洗炉过程。
对炉身下部炉墙结厚的洗炉作用较好,但易影响生铁质量、且对消除炉缸石墨碳堆积不太理想。
(3)洗炉注意事项
洗炉都会造成炉温降低,特别是边缘布焦强烈发展边缘气流时,必须按物理洗炉方法的规定进行;
化学洗炉变料时要采用热量换算系数上限。
洗炉过程中风口易破损,注意冷却设备水温变化,当超出规定水平要立即停止洗炉。
洗炉过程中要注意炉喉温度的变化。
控制风压与风量的对应关系,有步骤地恢复到正常炉况。
5.3.2.4冷却制度
合理的冷却制度是延长炉衬寿命及防止炉墙粘结、保证炉况顺行的重要措施,
控制炉腹至炉身下部高温区的水温差尤其重要。
各部水温差控制范围见表5—6。
炉缸和炉基冷却设备水温差超过规定标准时,按设备维护规定处理。
炉腹以上冷却设备水温差较长时间超过规定标准时,要采取下述措施。
(1)清洗冷却设备;
(2)增加水压(水量增加1/3);
(3)减少冷却壁串联数;
(4)采取适当加重边缘的措施;
(5)当炉腹以上冷却设备水温差低于规定水平时,出现炉墙结厚、炉况不顺时,可采取以下措施:
①适当采取发展边缘的措施;
②采取降低炉渣碱度的措施;
③降低冷却强度,炉况好转后,要及时恢复,严禁损坏炉衬;
④确认粘结后应采用洗炉措施。
5.3.2.5热制度
稳定的热制度是高炉生产优质铁水及炉况稳定顺行的基本保证之一。
其稳定性可以采用生铁含硅量的标准偏差和铁水温度来衡量(见表5—7)。
(1)正常生产条件下,750m3的高炉,生铁含[Si]可控制在0.30~0.70%的范围内。
(2)冶炼低锰炼钢铁的高炉,生铁含硅[Si],可控制在中下限。
①计划休风,炉温要控制在上限水平。
②当高炉事故休风率增加时,炉温应控制在中上限水平。
③在高炉冷却设备大量漏水又不能及时查明处理的情况下,必须采用加焦提高炉温的措施,来提高高炉承受波动的能力,避免失常。
④严禁连续低炉温操作。
2)高压、常压转换程序
(1)常压转高压操作的转换程序
①通知布袋除尘主控室、鼓风机站,并发出高压操作指令;
②通知卷扬,恢复均压制度;
③依次逐个关小∮900mm的加压阀,使炉顶压力达到接近的水平;
④将压力定值器调到指定位置;
⑤用手动调节∮450mm或∮900mm的自动调节阀调整到45°的位置;
⑥再次调节∮450mm阀,使炉顶压力达到指定水平;
⑦将∮450mm自动调节阀改为自动;
⑧在改高压的过程中,根据高炉炉况加风,保持或稍低于常压的压差水平。
(2)高压转常压的操作程序
①通知布袋除尘主控室、鼓风机站并发出常压操作指令;
②将∮450mm或∮900mm的自动调节阀改为手动;
③减风,控制压差等于或稍高于高压时压差水平;
④依次逐个地全开∮900mm调压阀。
高炉喷煤操作:
喷煤系统采用了ZGM133中速辊式磨煤机,大布袋一次收粉,四罐交叉并联倒罐喷吹,罐中央氮气流化板和罐底氮气流化装置等设备以及采用了浓相输送技术,烟煤、无烟煤混合喷吹,安全检测,计算机控制等喷吹工艺,设计制粉能力74~78t/h,最大喷吹能力55t/h,煤粉粒度为-200目≥80%,水分<1%,收粉方式为高浓度低压脉冲袋式收集器进行一级收粉,喷吹系统采用浓相输粉技术,固气比不小于30,管道内煤粉流速为4~8m/s。
在总管上设置煤粉流量计和调节阀,其调节和计量精度误差小于4%。
直接喷吹,喷吹能力按200kg/t设计。
喷煤用空压机主要由2台高压力螺杆机供风,干燥气系统为制粉提供300℃的烟气进行干燥的气体。
系统采用计算机控制,喷吹、制粉所有操作均可在主控室通过计算机操作完成。
2.2喷煤工艺流程