电厂培训资料.docx
《电厂培训资料.docx》由会员分享,可在线阅读,更多相关《电厂培训资料.docx(15页珍藏版)》请在冰豆网上搜索。
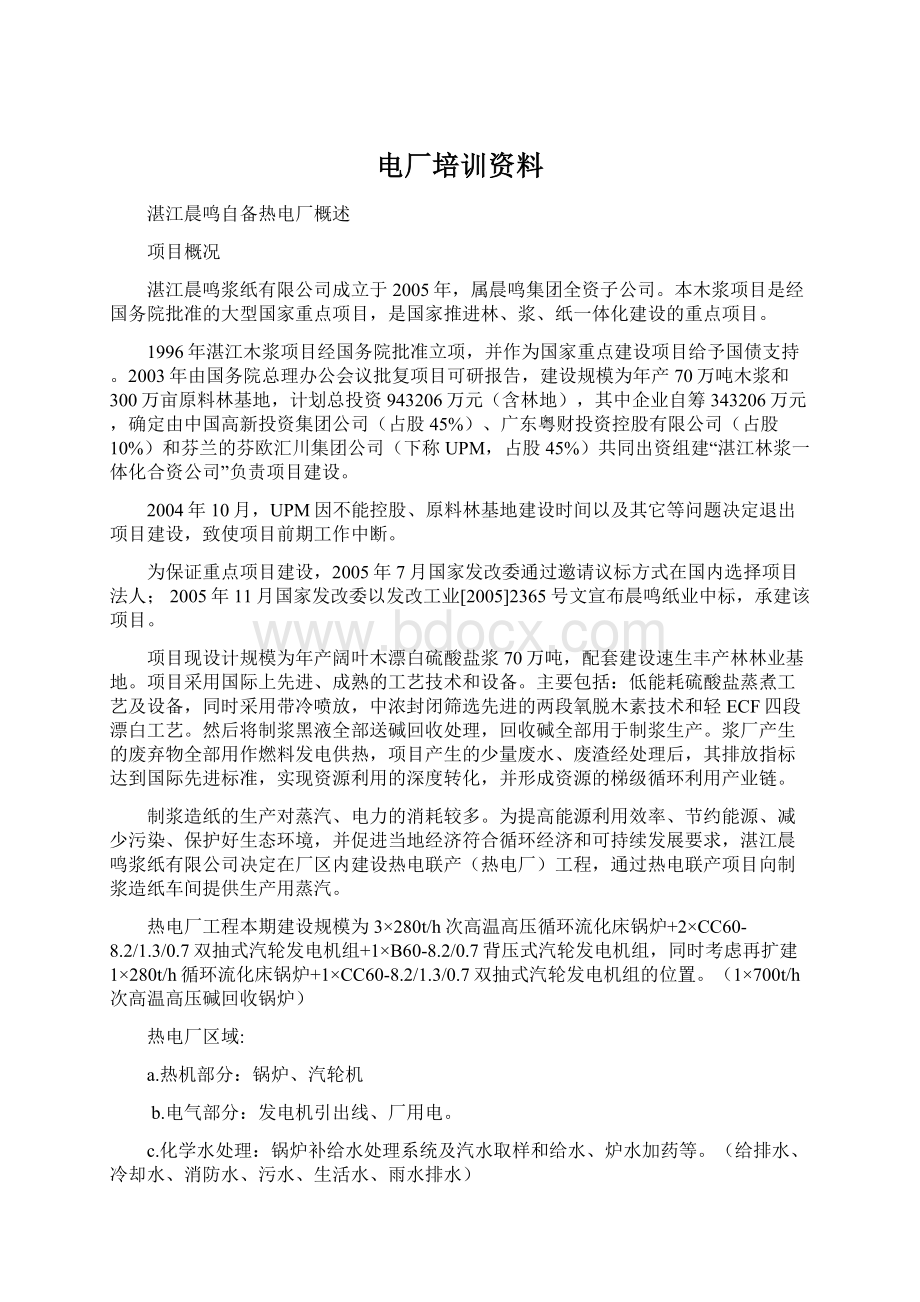
电厂培训资料
湛江晨鸣自备热电厂概述
项目概况
湛江晨鸣浆纸有限公司成立于2005年,属晨鸣集团全资子公司。
本木浆项目是经国务院批准的大型国家重点项目,是国家推进林、浆、纸一体化建设的重点项目。
1996年湛江木浆项目经国务院批准立项,并作为国家重点建设项目给予国债支持。
2003年由国务院总理办公会议批复项目可研报告,建设规模为年产70万吨木浆和300万亩原料林基地,计划总投资943206万元(含林地),其中企业自筹343206万元,确定由中国高新投资集团公司(占股45%)、广东粤财投资控股有限公司(占股10%)和芬兰的芬欧汇川集团公司(下称UPM,占股45%)共同出资组建“湛江林浆一体化合资公司”负责项目建设。
2004年10月,UPM因不能控股、原料林基地建设时间以及其它等问题决定退出项目建设,致使项目前期工作中断。
为保证重点项目建设,2005年7月国家发改委通过邀请议标方式在国内选择项目法人;2005年11月国家发改委以发改工业[2005]2365号文宣布晨鸣纸业中标,承建该项目。
项目现设计规模为年产阔叶木漂白硫酸盐浆70万吨,配套建设速生丰产林林业基地。
项目采用国际上先进、成熟的工艺技术和设备。
主要包括:
低能耗硫酸盐蒸煮工艺及设备,同时采用带冷喷放,中浓封闭筛选先进的两段氧脱木素技术和轻ECF四段漂白工艺。
然后将制浆黑液全部送碱回收处理,回收碱全部用于制浆生产。
浆厂产生的废弃物全部用作燃料发电供热,项目产生的少量废水、废渣经处理后,其排放指标达到国际先进标准,实现资源利用的深度转化,并形成资源的梯级循环利用产业链。
制浆造纸的生产对蒸汽、电力的消耗较多。
为提高能源利用效率、节约能源、减少污染、保护好生态环境,并促进当地经济符合循环经济和可持续发展要求,湛江晨鸣浆纸有限公司决定在厂区内建设热电联产(热电厂)工程,通过热电联产项目向制浆造纸车间提供生产用蒸汽。
热电厂工程本期建设规模为3×280t/h次高温高压循环流化床锅炉+2×CC60-8.2/1.3/0.7双抽式汽轮发电机组+1×B60-8.2/0.7背压式汽轮发电机组,同时考虑再扩建1×280t/h循环流化床锅炉+1×CC60-8.2/1.3/0.7双抽式汽轮发电机组的位置。
(1×700t/h次高温高压碱回收锅炉)
热电厂区域:
a.热机部分:
锅炉、汽轮机
b.电气部分:
发电机引出线、厂用电。
c.化学水处理:
锅炉补给水处理系统及汽水取样和给水、炉水加药等。
(给排水、冷却水、消防水、污水、生活水、雨水排水)
d.运煤系统:
运煤、破碎系统。
e.热控部分:
DCS、PLC、现场仪表;
f.除灰渣部分:
灰渣排放,灰渣库的装车出料。
g.环境保护:
烟尘、SO2、废水、噪声的排放测算及防止措施。
本工程为自备热电厂,同时处理制浆造纸车间生产产生的树皮、木屑和污泥。
h.热力管道:
供热管线至热电厂厂区外。
锅炉
型式:
次高温高压循环流化床锅炉。
主要参数
锅炉额定蒸发量280t/h
锅炉最大蒸发量308t/h
数量3台(两用一备)
过热蒸汽出口压力8.5MPa(g)
过热蒸汽出口温度480℃
锅炉给水温度186℃
锅炉排烟温度140℃
锅炉设计热效率90%
锅炉点火及助燃燃料
点火用油采用0#轻柴油。
每台锅炉配用两台点火器,冷态点火时间燃油每次持续时间约4~5小时,每台锅炉设置2台床下点火装置和3台床上点火装置。
每台床下点火装置耗油量为800kg/h;每台床上点火装置耗油量为300~400kg/h。
一台锅炉一次点火耗油量约为14000公斤。
燃烧
给料系统
直径小于10mm的原煤从煤仓间的煤仓落至称重式皮带给煤机,送至炉膛前墙的播煤口进入锅炉燃烧。
树皮、木屑从煤仓间的生物质仓经螺旋拨料器给料至螺旋给料机,送至炉膛前墙的溜管内,再由螺旋给料机直接送入锅炉炉膛进行燃烧。
造纸污泥通过污泥输送泵送至锅炉炉膛顶部的污泥给料口。
石灰石粉直接通过气力连续输送方式从石灰石粉贮仓送到锅炉炉膛。
排渣系统
炉渣排入冷渣机冷却后,采用输渣皮带输送至渣仓。
每台锅炉配3台冷渣机,1个事故排渣口。
冷渣机采用除盐水冷却。
排渣系统每两台锅炉共用一条输渣皮带,直接由皮带输送至渣库。
一次风系统
每台锅炉配备1台100%容量的高压一次离心风机。
通过冷一次风管,经一次风机升压后的冷一次风进入空气预热器加热,成为热一次风,部分冷风经一次风机加压后送至给煤口作密封风。
风道上设置有风量测量装置。
热一次风再分为3路分支:
第1路热风,进入炉膛底部风室,通过风室布风板上的定向风帽,为床料提供均匀的流化风。
第2路热风,分别为气力播料口提供播料风。
位于锅炉前墙播料风由一次风机提供,在空预器和风量测量装置之间引出,作为播煤风,每支播煤风管布置一只风门,以调节送煤风量。
采用气力播料方式有能使落料顺畅、防止堵塞的优点。
第3路热风,作为床下油枪的点火风。
二次风系统
每台锅炉配备1台100%容量的离心式二次风机,二次风经过空气预热器后,通过二次风配风管和二次风联箱进入炉膛内。
返料风系统
炉膛内的大量物料在高温烟气的携带下,进入旋风分离器内,烟气中的粗颗粒被分离出来,分离下来的高温物料从返料阀返回炉膛作为床料继续燃烧。
由于物料温度较高,难以采用机械输送,因此,设置专门的高压返料风机,供给两路飞灰回送装置,以保证返料系统连续可靠地运行。
烟气系统
锅炉炉膛内采用平衡通风,烟气通过旋风分离器分离出大部分粉尘后,进入锅炉尾部竖井,经过各过热器、省煤器和空气预热器排出锅炉本体。
含尘烟气进入高效布袋除尘器、引风机和湿法脱硫塔,最终通过烟囱排入大气。
脱硝处理系统
本工程采用次高温高压循环流化床锅炉,可有效的抑制NOx的生成。
能够使烟气中氮氧化物的排放浓度小于200mg/Nm3。
同时,本工程在锅炉本体订货时已要求锅炉设备厂在锅炉本体上预留SNCR脱氮系统接口,在锅炉和除尘器中间预留SNCR脱氮系统设备的位置。
布袋除尘器系统
当空预器出来的含尘气体进入布袋除尘器进风口,布袋除尘器内部结构上增设了沉降室,起到预分离的作用,进一步加强布袋预收尘,并保证布袋除尘器安全运行。
布袋除尘器本体设有旁路烟道,当温度或差压超过设定值时,旁路自动运行,以保证系统安全平稳工作。
除尘器的底部灰斗中的灰部分经气力输灰排出。
考虑到烟气的组分特殊,酸露点较高,故在除尘器灰斗上设有电加热保温,仅在冷态情况下启动或临时停运时使用,保证布袋除尘器本体内壁不至于出现酸结露。
烟气经布袋除尘器除尘后,经引风机和湿法脱硫塔后被排入大气。
布袋除尘器的除尘效率能够保证在99.95%以上,能够保证烟囱出口烟尘排放浓度小于30.0mg/Nm3。
湿法脱硫处理系统
为有效降低烟气中SO2的排放浓度,在引风机后设置一套烟气湿法脱硫处理装置对锅炉烟气进行脱硫。
脱硫工艺采用造纸白泥脱硫工艺,吸收剂制浆采用白泥。
造纸碱回收车间黑液浓缩焚烧后,从燃烧炉底部流出的熔融物主要成分是碳酸钠和硫化钠,溶于稀白液后,称为绿液。
在苛化工段,往绿液中加硝石灰,使碳酸钠转化为氢氧化钠。
澄清后的液体称为白液,即蒸煮用的碱液,沉淀出的碳酸钙称为白泥。
湿法工艺采用白泥(CaCO3)作吸收剂,在吸收塔内,吸收浆液与烟气接触混合,烟气中的SO2溶于水,与浆液中的碳酸钙反生成亚硫酸钙,然后在塔底与鼓入的氧化空气发生化学反应,最终反应产物为石膏。
系统中的石膏浆液经排出泵抽出打入石膏脱水系统,脱水后回收成品石膏,同时借此维持吸收塔内浆液密度。
由于吸收浆的循环利用,脱硫吸收剂的利用率很高。
该工艺适用于任何含硫量的煤种的烟气脱硫,脱硫效率较高。
灰输送储存系统
布袋除尘器下的外排灰由连续输送泵通过管道输送至灰库。
自控系统
湿法烟气脱硫除尘系统的自动监测与控制采用PLC系统,实现对湿法烟气脱硫除尘处理系统的顺序自动启停,运行参数自动检测和储存,并对关键参数实行自动调节,使湿法烟气处理系统实现自动控制。
为保证烟气脱硫除尘效率和脱硫除尘设备安全经济的运行,将设置完整的热工测量、自动调节、控制、保护及热工信号报警装置。
为节省投资,又能方便运行,烟气净化监控系统采用控制室PLC系统集中监控和现场监视相结合的控制方法。
烟囱
采用单管烟囱,上口径为5.30m,烟囱高度150m。
汽轮机
抽汽凝汽式汽轮机
型式:
次高温高压抽汽凝汽式汽轮机
数量2台
额定功率:
60MW
最大功率:
66MW
主蒸汽阀前额定压力:
8.2(±0.29)MPa(a)
主蒸汽阀前额定温度:
475(±5)℃
主蒸汽额定/最大流量:
341/392t/h
额定工况I抽汽压力:
1.3(±0.29)MPa(a)
额定工况I抽额定/最大抽汽量:
70/120t/h
额定工况II抽汽压力:
0.7(±0.1)MPa(a)
额定工况II抽额定/最大抽汽量:
100/180t/h
额定工况排汽压力:
0.0062MPa(a)
额定转速:
3000r/min
旋转方向:
从汽机端向发电机端看为顺时针
c背压式汽轮机
型式:
次高温高压背压式汽轮机
数量1台
额定功率:
60MW
最大功率:
66MW
主蒸汽阀前额定压力:
8.2(±0.29)MPa(a)
主蒸汽阀前额定温度:
475(±5)℃
主蒸汽额定/最大流量:
437/479.5t/h
额定工况排汽压力:
0.7(±0.1)MPa(a)
额定工况排汽温度:
187℃
非调整抽汽压力:
1.9(±0.2)MPa(a)
非调整抽汽流量:
15t/h
额定转速:
3000r/min
旋转方向:
从汽机端向发电机端看为顺时针
汽机本体控制与保护
汽机本体控制与保护主要包括数字电液控制系统(DEH)、汽机本体监测系统(TSI)和危急遮断系统(ETS)等
汽轮发电机组运行方式:
定压运行。
主蒸汽
主蒸汽系统采用单母管制。
在锅炉过热器出口至母管前设置电动隔离门,母管至汽机设置电动隔离门,主汽门前设置电动隔离门。
主蒸汽管上设置流量测量装置。
主蒸汽管道材质为12Cr1MoVG。
汽机旁路系统
汽机旁路系统采用启动旁路系统。
即在锅炉出口至主蒸汽母管的电动隔离门前设置一路管道。
当锅炉启动时,关闭锅炉与主蒸汽母管间的电动隔离门,使锅炉启动产生的蒸汽通过启动母管引至减温减压器,经减温减压器减温减压后向外供热。
设置汽机启动旁路系统后,机组的启、停工况得到了改善,且回收了部分工质和热量,提高了机组运行的经济性,减少了噪音污染。
主给水系统
主给水系统采用单母管制
机组配3台容量为110%BMCR最大给水量的电动给水泵,为了节约厂用电,电动给水泵选用了高压变频电机,正常情况下运行两用一备。
正常运行时,锅炉给水调节完全依靠高压变频泵调节流量。
并设30%负荷给水管路调节阀,用于低负荷工况。
另设一小给水管路调节阀,用于锅炉启停。
回热系统
抽汽凝汽式汽轮机的回热系统采用一级高压加热器,一级除氧器和两级低压加热器组成的4级回热系统,汽轮机设有4段抽汽,其中一段抽汽用于高压加热器加热,并向厂区管网供应高压蒸汽;二段抽汽用于中压除氧器加热和外网低压蒸汽供热;三段抽汽用于二号低压加热器加热;四段抽汽用于一号低压加热器加热;其中一、二段抽汽为可调整抽汽,向厂区管网供应高、低压蒸汽。
一段抽汽作为低负荷时除氧器的备用加热蒸汽。
背压式汽轮机不设回热系统。
给水除氧系统
本工程设中压除氧器三台,一台高压除氧器,两台低压除氧器,除氧器采用定压方式运行,热网的疏水先进入疏水扩容器,再由水泵打入除氧器。
低压给水系统采用单母管制系统。
供热系统
高压对外供热参数为:
1.9MPa.a,15t/h;
中压对外供热参数为:
1.3MPa.a,123.5t/h(平均),136t/h(最大);
低压对外供热参数为:
0.7MPa.a,548t/h(平均),602t/h(最大)。
供热系统采用母管制,供热系统供出的高压蒸汽正常运行工况来自抽汽凝汽式汽轮机一段抽汽;低压蒸汽正常运行工况来自抽汽凝汽式汽轮机二段抽汽和背压式汽轮机的背压排汽;在汽轮机检修或故障停运的情况下,由主蒸汽经减温减压后供给高、低压蒸汽,设减温减压器两台,其中减压到1.3MPa.a的减温减压器一台,出力为90t/h;减压到0.7MPa.a的减温减压器两台,单台出力为200t/h。
加热器疏水系统
加热器的疏水系统的设计原则是保证机组在各种工况下都能使加热器通畅的排除疏水,保证加热器及机组的安全,并尽可能的回收疏水的热量,以提高机组的热经济性。
加热器疏水为逐级自流系统。
高加疏水流入除氧器。
高压加热器设高加危机放水管,接至高加疏水扩容器内。
低加疏水由二号低加自流入一号低加,由一号低压自流入凝汽器。
汽封加热器的疏水直接进入凝汽器。
凝结水系统
凝结水系统为单元制(在除氧器前设有母管),每台双抽凝汽式汽轮机组设3台55%容量的凝结水泵,两用一备。
凝汽器抽真空系统
凝汽器抽真空系统选用两台水环真空泵,正常运行时一用一备,启动时可以两台同时运行。
补给水系统
来自化学水处理间的除盐水经冷渣器后全部进入主厂房疏水箱,通过疏水泵送至除氧器。
经化学水处理间处理过的生产返回水直接送至除氧器。
循环冷却水
循环冷却水由厂区循环水系统供给,由工业水泵房打至主厂房。
汽机润滑油储存和油净化装置。
每台机组设置一个主机润滑油箱,油箱容积15m3。
三台机组设置一套移动式滤油机。
除氧间布置
除氧间跨度为9m,柱距为8m,除氧间全长共121.82m。
除氧间各层的布置:
±0.000m层:
布置电气设备间及蓄电池室。
+4.500m层:
为汽水管道夹层。
+8.000m层:
为运行层,布置集中控制室及热控电子设备间。
+12.500m层:
为管道夹层。
+16.000m层:
为除氧间层,布置除氧器、除氧水箱和连续排污扩容器。
煤仓间布置
煤仓间跨度为8m,柱距为8m,固定端布置上煤皮带,每台锅炉所配置的原煤仓占用1个柱距,除氧煤仓间全长共49m。
煤仓间各层的布置:
±0.000m层:
布置电气设备间及蓄电池室。
+4.500m层:
为电缆夹层。
+8.000m层:
为运行层,布置集中控制室及热控电子设备间。
+12.500m层:
为管道夹层。
+16.000m层:
为给料层,布置称重式皮带给煤机和垃圾给料螺旋给料机。
+30.000m层:
为输煤皮带层,布置两台输煤皮带机及通风除尘装置。
原煤仓布置于+1600m层与+30.000m层之间。
发电机
型号:
50WX18Z-054XXT
数量:
3台
额定功率:
60MW
最大功率:
66MW
额定电压:
10.5kV
功率因数:
0.8
额定频率:
50Hz
冷却方式:
空冷
励磁方式静止可控硅励磁
本工程全厂用电负荷为190MW(含自备电站厂用电)。
正常运行时,全厂发电量为180MW,需从电网购电10MW。
当一台发电机停运(不停汽)时,正常运行的两台发电机以最大功率运行,发电量为132MW,需从电网购电48MW,此时63MVA主变负荷率84.66%。
电厂接入系统
全厂设一台SFZ10-63000,110±8X1.25%/38.5kV主变,两回110KvLGJ-300架空线路分别接入太平变电站110kV母线两段。
电气主接线
110kV系统采用单母线接线。
35kV系统采用单母线分段接线,共分两段。
主变35kV侧设两个分支,分别接于35kV系统Ⅰ段、Ⅱ段。
发电机采用发-变组单元接线,经升压变接入35kV系统。
其中1#、2#发电机接于35kV系统Ⅰ段,3#发电机及启/备变接于35kV系统Ⅱ段。
补给水处理系统
锅炉补给水采用的流程如下:
总厂工业水处理站清水池→原水泵→纤维束过滤器→活性碳过滤器→强阳离子交换器→脱碳器→强阴离子交换器→混合离子交换器→除盐水水箱→返水水水箱→除盐水泵→除氧器
↑
合格返回水
除盐水箱→除盐水泵(冷却水用)→冷渣器→疏水箱→除氧器
→汽水取样→
一级除盐+混床系统采用串联连接方式设置,过滤器按母管制设置。
系统的反洗、再生等操作采用PLC控制,同时设置必要的水质在线检测装置。
热网凝结回水处理
由于本项目机组为次高温高压参数,锅炉对补给水水质要求较高,生产返回水(热网凝结回水)较容易受到污染,因此设置一套生产返回水精处理系统:
利用板式换热器、锰砂过滤器、混床对回水进行处理,保证水质达到锅炉补给水水质要求,其中混床、除盐水箱、除盐水泵与补给水处理系统合用。
其处理流程如下:
不合格返回水→凝结水箱→一级板式换热器→二级板式换热器→锰砂过滤器→混合离子交换器→返回水水箱→除盐水泵→除氧器
↑
除盐水箱
合格返回水→返回水水箱→除盐水泵→除氧器
↑
除盐水箱
燃料输送系统
按4×280t/h循环流化床锅炉机组容量一次建成。
燃料输送系统包括:
由汽车卸煤装置至主厂房煤仓间皮带层的整个卸煤、储煤、破碎、上煤系统及辅助设施、防尘设施等;(树皮、木屑输送系统)。
卸煤装置
本工程燃煤全部为自卸汽车公路来煤,本期工程锅炉年耗煤量约66万t/a,终期工程锅炉年耗煤量约100万t/a(3台炉,纯燃贫煤设计煤种工况),
运煤车型选用30t自卸汽车,采用缝式煤槽卸煤装置。
煤槽设6个卸车车位,煤槽上部每个车位设置1台振动平煤箅,煤槽下部配置双路带式输送机和2台叶轮给煤机,叶轮给煤机出力200~600t/h,带式输送机出力600t/h,带宽1m,带速2m/s,一台运行,一台备用,亦可双路同时运行。
贮煤场及其设备
本工程设置斗轮堆取料机贮煤场(干煤棚)一座,跨度74m,长度160m,两侧挡煤墙高度7m,煤堆高度12m,总储煤量50000t;满足一期规模2台运行锅炉机组25d耗煤量,终期规模3台运行锅炉机组17d耗煤量。
筛碎设备
选用出力为300t/h的粗、细碎煤机各2台;互为备用。
带式输送机系统
带式输送机系统分为厂外输送系统(缝式煤槽至煤场)、煤场带式输送机系统和厂内输送系统(煤场至主厂房煤仓间皮带层);厂外输送系统具备切换直接进入厂内输送系统的功能,可实现厂外来煤的直供,将汽车卸煤直接运往碎煤机房。
厂外输送系统从汽车卸煤装置到干煤棚共设2段带式输送机,出力Q=600t/h,带宽B=1m,带速V=2m/s,双路布置,一台运行,一台备用,亦可双路同时运行。
厂内输送系统从干煤棚到主厂房煤仓间皮带层共设4段带式输送机,出力Q=300t/h,带宽B=0.8m和B=1.0m(碎煤机房之前2段带宽为0.8m,碎煤机房之后2段带宽为1.0m),带速V=1.6m/s,双路布置,一台运行,一台备用,也可双路同时运行。
由系统外接入的输送树皮、木屑带式输送机接入碎煤机房之后的运煤带式输送机上,经备用运煤带式输送机直接运至煤仓层的树皮、木屑储仓。
控制方式
控制方式为DCS控制,在控制室(脱硫综合楼)和就地均能实现设备启停。
带式输送机设有:
打滑监测装置;纵向撕裂保护装置;跑偏信号;双向拉绳开关;煤流信号;堵煤信号等。
监视方式采用工业电视。
系统设有下列保护信号:
A)煤流信号:
监测胶带载煤情况。
B)速度信号:
用以监测胶带运行速度以控制带式输送机的启停;
C)防跑偏信号:
当带式输送机跑偏时发出报警信号,仍继续跑偏至过限时立刻停机。
D)拉线开关:
当带式输送机沿线发生设备或其它事故时,可在胶带沿线任何位置拉线停机。
E)堵煤信号
F)纵向防撕裂信号
除灰渣系统
除灰渣系统按干灰、干渣分排分贮存方式。
除灰采用浓相正压气力输送系统,一台炉为一个单元,全厂设容积1000m3灰库2座。
除渣采用干式机械除渣方式,本期2台炉为一个单元,全厂设容积300m3渣库2座。
灰渣全部综合利用。
除尘器的形式
采用6灰斗布袋除尘器。
灰渣堆场
灰渣全部综合利用,运灰渣汽车能及时将灰库、渣库贮存的灰渣装车外运,不设专门的灰渣堆场。
除渣系统
除渣系统采用干式机械除渣方案,本期工程2台炉排渣用一套输渣带式输送机将炉渣运至渣仓。
每台锅炉设有四个排渣管,其中叁个排渣管下接叁台冷渣机,当一台冷渣机故障时,另两台冷渣机仍可满足锅炉正常运行的需要。
本工程采用水冷滚筒式冷渣机,炉底渣经冷渣机冷却,冷渣机能将950℃以上高温炉渣降到100℃以下,再采用耐高温阻燃型带式输送机将渣送到锅炉间外钢渣仓,然后采用专用自卸汽车运至综合利用厂。
输送量可随锅炉床压进行无级调速,并能实现锅炉连续排渣。
冷渣机冷却水选用除盐水,换热后冷却水水温可达80℃,热量可全部回收,节约能源。
单座渣仓直径Φ8m,容积300m3,可贮存2×280t/h循环流化床锅炉燃用贫煤设计煤种(纯燃煤工况)24小时的排渣量。
工艺流程如下:
冷渣机
锅炉排渣口
1#带式输送机
2#带式输送机
渣仓
综合利用
密闭专用汽车
手动插板门
汽车散装机
除灰系统
锅炉除尘系统采用布袋除尘器,收集的飞灰采用正压浓相气力输送装置送至灰库贮存。
飞灰输送系统按一台运行锅炉一个单元设计,布袋除尘器排灰进入各灰斗下的仓泵后,采用压缩空气将灰送到灰库。
全厂设灰库2座,单座灰库直径Φ12m,容积1000m3。
可贮存本期工程2×280t/h运行锅炉燃用贫煤设计煤种(纯燃煤工况)额定负荷运行52小时排灰量。
灰库下分两路卸灰,一路经干灰散装机卸至罐车后运至综合利用厂。
另一路根据需要采用湿式搅拌机将飞灰加湿后装车外运。
为了保证灰库下灰流畅,系统内设有灰库气化风机和电加热器提供灰库气化用气。
正压气力输送系统工艺流程(单台炉):
灰库1000m3
仓泵
(3台)
手动插板
(3台)
布袋除尘器
密闭罐车
汽车散装机
综合利用厂
双侧库底卸料器
灰渣场
密闭专用汽车
加湿搅拌机
工业水
热工自动化部分
本期工程热工自动化控制范围包括:
3台280t/h循环流化床锅炉、2台60MW抽凝式汽轮发电机组、1台60MW背压式汽轮发电机组及相应辅机的控制系统、辅助车间控制系统、烟气在线监测系统、热电厂工业电视监视系统等。
热工自动化主要原则以减员增效、节约投资、提高生产管理及自动化水平为核心目的
1)采用先进实用的控制技术与网络技术,锅炉、汽机采用DCS控制、辅助车间采用远程I/O或PLC控制,使全厂的控制系统构成一个有机的整体。
2)采用机组控制一体化,将发变组和厂用电系统纳入机组DCS控制。
3)设置全厂辅助车间控制系统,对全厂辅助车间分区进行集中监控,以减少运行人员,提高电厂的经济效益。
热工自动化水平
1)本期工程锅炉、汽机采用DCS控制,辅助车间采用远程I/O或PLC控制。
2)机组设分散控制系统(DCS),以LCD、专用键盘、鼠标、BTG盘为单元机组主要监视和控制手段,仅在BTG盘和DCS控制台上配置紧急停机按钮及少量控制开关,并纳入机组DCS,真正实现炉、机、电的监控一体化。
3)机组的启动、停止、正常运行和异常工况的处理均可在中央控制室完成。
4)除燃烧调节在最低稳燃负荷以上投入自动外,其他自动调节系统按全程调节和程序自动投入调节系统;保护联锁逻辑能自动完成主辅机在各种运行和事故工况下的各种事故处理。
电厂设置一个中央控制室,中央控制室位于主厂房8m标高运行层,中央控制室分机柜室与操作室,采用炉、机、电集中控制方式。
机组炉、机、电采用DCS实现监控。
在操作室内布置有本期机组的运行操作员站、值长站、电气仪表BTG盘、工业电视视频操作台、工业电视监视系统显示器等设备。
机柜室布置机组DCS工程师站、打印机、机组的D