《机床机械零部件检测维修与调整》教案四.docx
《《机床机械零部件检测维修与调整》教案四.docx》由会员分享,可在线阅读,更多相关《《机床机械零部件检测维修与调整》教案四.docx(31页珍藏版)》请在冰豆网上搜索。
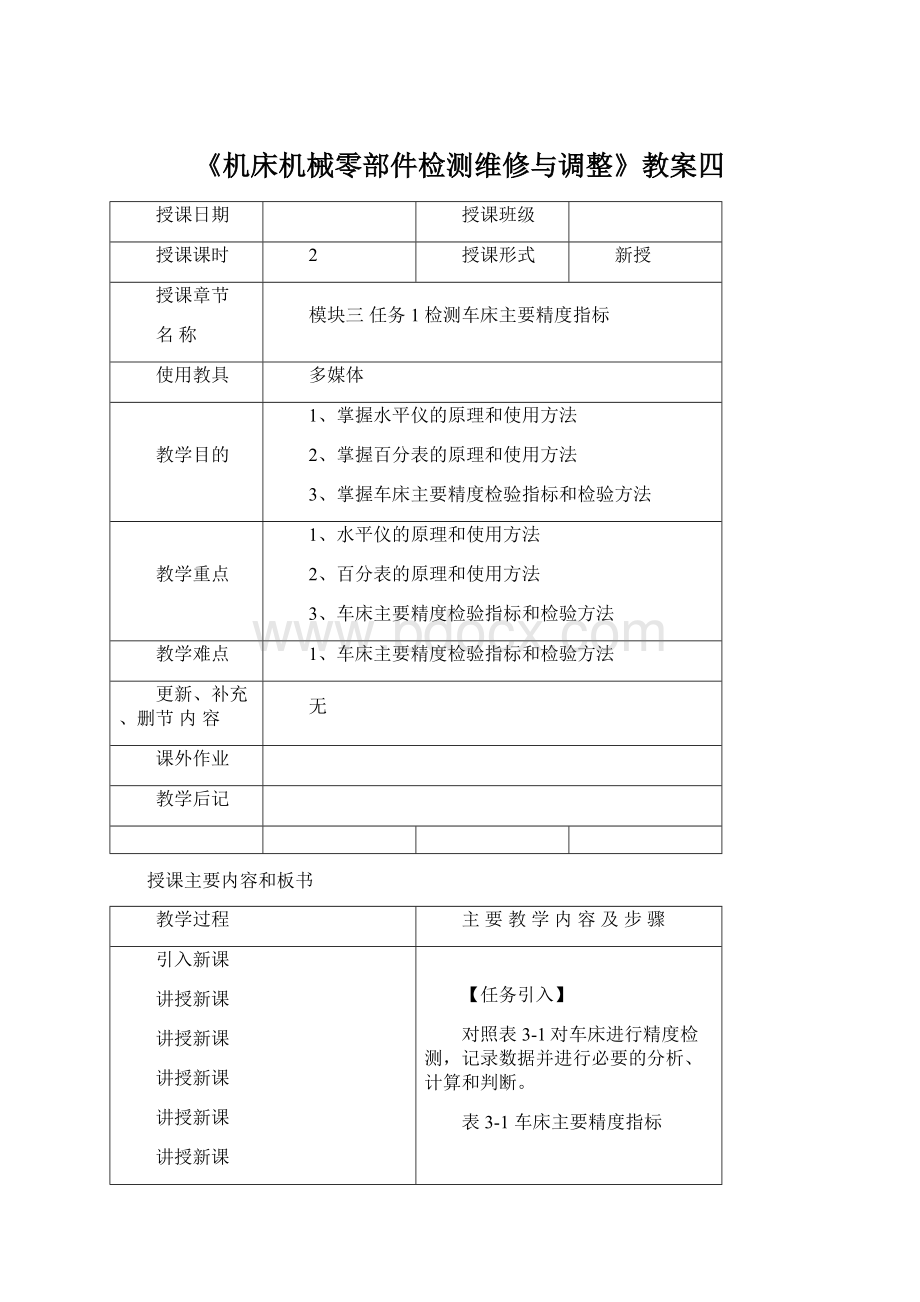
《机床机械零部件检测维修与调整》教案四
授课日期
授课班级
授课课时
2
授课形式
新授
授课章节
名称
模块三任务1检测车床主要精度指标
使用教具
多媒体
教学目的
1、掌握水平仪的原理和使用方法
2、掌握百分表的原理和使用方法
3、掌握车床主要精度检验指标和检验方法
教学重点
1、水平仪的原理和使用方法
2、百分表的原理和使用方法
3、车床主要精度检验指标和检验方法
教学难点
1、车床主要精度检验指标和检验方法
更新、补充、删节内容
无
课外作业
教学后记
授课主要内容和板书
教学过程
主要教学内容及步骤
引入新课
讲授新课
讲授新课
讲授新课
讲授新课
讲授新课
讲授新课
课堂小结
作业布置
【任务引入】
对照表3-1对车床进行精度检测,记录数据并进行必要的分析、计算和判断。
表3-1车床主要精度指标
【任务分析】
表3-1节选自《卧式车床精度》(GB4020-88),是车床的常规精度检测项目。
在新机床验收或旧设备的维修维护中,为了验证机床的精度是否达到要求,通常要检测这些项目。
任务要求采用水平仪、百分表以及心棒等必要的检测工具,按表3-1中图示的方法检测,做好记录,并进行数据分析。
【相关知识】
一、水平仪
水平仪是机修工作中最基本的测量仪器之一,常用来测量导轨在垂直面内的直线度、工作台台面的平面度及零件间的平行度、垂直度等。
常用的水平仪有条式水平仪、光学合像水平仪等(见图3-1)。
1、水平仪的结构与工作原理
水平仪是测量与自然水平面所形成倾斜角度的测角量仪,主要工作部分是水准器。
水准器是内壁磨成所需要的曲率并带有刻度的玻璃管,在管内装入酒精或乙醚,使管内留下不大的空气泡。
如图3-2所示为水平仪工作原理。
若被测面为一自然水平面时,气泡的位置为A,连接4点与玻璃管曲率中心0,必垂直于水平面。
当被测面与水平面倾斜成a角时,由于地心引力作用,气泡将由4点移至B点,则-定垂直于水平面。
倾角越大,图中AB弧长也越大。
以刻线标示弧长,根据它们的几何关系,就可以精确计算出每偏移一格倾角的大小。
2、水平仪的读数
读数时,以零线为基准,在两个方向上分别读出气泡停止的格数,取其平均值。
如图3-3a所示读数为2格,图3-3b所示读数为2.5格。
二、百分表
1、百分表
百分表是应用很广的万能量具,用它可以检验机床精度和测量工件的尺寸、形状和位置误差。
百分表
1)百分表的结构
百分表的结构如图3-6所示。
图中1是淬硬的触头,用螺纹旋入测量杆2的下端,测量杆的上端有齿。
当测量杆上升时,带动齿数为16的小齿轮3?
在小齿轮3的同轴上装有齿数为100的大齿轮4,再由大齿轮4带动中间的齿数为10的小齿轮5。
在小齿轮5的同轴上装有长指针6,因此,长指针就随着一起转动。
在小齿轮5的另一边装有大齿轮7,在其轴下端装有游丝,用来消除齿轮间的间隙,以保证其精度。
该轴的上端装有短指针8,用来记录长指针的转数(长指针转一圈时短指针转一格)。
拉簧11的作用是使测量杆2能回到原位。
在表盘9上刻有线条,共分100格。
转动表圈10,可调整表盘刻线与长指针的相对位置。
2)百分表的刻线原理
百分表内的测量杆和齿轮的齿距为0.625mm。
当齿杆上升16齿时(即上升0.625×16=10mm),16齿小齿轮转一周,同时齿数为100的大齿轮也转一周,就带动为10的小齿轮和长指针转10圈。
当测量杆移动lmm时,长指针转一圈。
由于表盘上共刻100格,长指针毎转一格表示测量杆移动0.01mm。
为提髙可视精度,也可使用千分表,即长指针每转.格表示测量杆移动0.001mrn,但一般使用在要求测量精度非常髙的场合。
3)百分表的测量范围
百分表的测量范围是指测量杆的最大移动量,有0~3mm、0~5mm、0~10mm三种规格。
2、杠杆式百分表结构
杠杆式百分表如图3-7a所示。
这种百分表小巧灵活,常用于车床、磨床上校正工件的安装位置,或用于普通百分表不便使用的地方。
杠杆式百分表的结构原理如图3-7b所示。
触头1与扇形齿板2用板11连接,当触头向上或向下摆动时,扇形齿板就带动小齿轮3转动,与小齿轮3同轴的端面齿轮4也随之转动,从而带动小齿轮5。
当小齿轮5转动时,同轴的指针6也随之转动,即可在表盘上读出读数。
转动表圈7,可调整表盘刻线与指针的相对位置。
3、百分表的使用
【任务实施】
一、准备工作
1、普通车床
2、千分表、百分表、磁力表座、条式水平仪、钢卷尺各一件。
3、长检验棒(见图3-12)、带莫氏锥度的短检验棒(见图3-15)、前后顶尖、钢珠各一件。
2)数据处理
参照“使用水平仪测量导轨垂直面内的直线度误差”分别用作图法和计算法求出全程直线度误差和1m内的最大误差。
计算得实测误差后对照精度指标判别精度是否符合要求。
2、检测溜板移动的倾斜度
检验溜板移动在垂直面内的直线度合格后,将水平仪原位转动90°和导轨垂直(见图3-10)。
移动溜板,每隔200mm记录一次水平仪的读数。
在溜板的全部行程上至少记录3个读数。
水平仪在每米行程上和全部行程上读数的最大代数差即为本项检测的实测误差,计算得误差后对照精度指标判别精度是否符合要求。
3、检测溜板移动在水平面内的直线度
1)操作
在前后顶尖间,顶紧一根长检验棒,将千分表固定在溜板上,使千分表触头顶在长检验棒的测母线上(见图3-11),调整尾座,使千分表在长检验棒两端的读数相等,然后,转动千分表表圈,调整表盘的“0”刻线与长指针对齐。
移动溜板,在溜板的全部行程上检验。
记下每一次测量的读数。
长检验棒的结构如图3-12所示,尺寸见表3-4,堵头和检验棒体均采用T10A制造(检验棒体也可用无缝钢管),经过热处理硬度达56~62HRC。
外径D的圆度公差为0.001mm,圆柱度公差为100mm:
0.001mm。
表3-4长检验棒的规格系列
序号
L
D
D2
d
1
300
50
35
30
2
1000
60
45
40r
3-
1500
75
55
50
可以画出溜板的运动曲线,求出千分表在每米行程上的读数的最大差值和全部行程上的最大差值,就是每米直线度误差和全程最大误差。
例如,检验棒长1500mm,每隔150mm测量一次,在全长上测量11次,测得数据见表3-5。
表3-5千分表读数
位置/mm
0
150
300
450
600
750
900
1050
1200
1350
1500
读数/µm
0
+8
+10
-8
-15
-20
0
Vf
+8
+5
0
将测得的数据标示在坐标纸中,如图3-13所示,从图可以看出,两端点的坐标均为0。
它们的连线为经过坐标原点的水平线,全程上的最髙点或最低点的坐标差值就是全程误终,即0.03mm。
求每米误差则需从第一点开始量起1m为第一段,第二点开始为第二段……每段的首尾两端连成直线,测出该段内各点到该直线的正、负两方向的距离最大值之和即为该段内的误差。
各段误差相比较,误差最大的那段的值就是每米误差。
4、检测左轴的轴向窜动、径向跳动、轴肩跳动
1)主轴轴向窜动检査(见围3-14)
以百分表在1位置做测量,将锥度标准的短检验棒放人主轴孔中,在短检验棒中心孔中置一个钢珠,然后用百分表测得运动中主轴轴向窜动的误差。
允差0.01mm。
2)主轴轴颈径向跳动检查(见图3-14)
百分表在2的位置,测头触在主轴颈部定心圆柱表面上,旋转主轴,百分表即可测得径向跳动的误差。
允差0.01mm。
3)主轴轴肩支撑面跳动检验(见图3-l4)
百分表在3的位置,即可测得轴肩支撑面跳动的误差。
允差0.02mm。
1、水平仪的原理和使用方法
2、百分表的原理和使用方法
3、车床主要精度检验指标和检验方法
练习题
1、水平仪是测量的测角量仪。
2、水平仪测量导轨垂直面内的直线度时,一般用哪几种方法进行数据处理?
3、使用百分表测量时应该注意哪些事项?
授课日期
授课班级
授课课时
2
授课形式
新授
授课章节
名称
任务2车床主要部件的拆卸
使用教具
多媒体
教学目的
1、掌握车床的基本结构和各大部件的结构和功能
2、掌握大零部件拆卸方法
教学重点
1、车床的主要部件和功能
2、机床部件拆卸时的吊挂吊离方法
3、主轴箱、溜板箱、刀架拖板、尾座等部件的拆卸
教学难点
1、主轴箱、溜板箱、刀架拖板、尾座等部件的拆卸
更新、补充、删节内容
无
课外作业
教学后记
授课主要内容和板书
教学过程
主要教学内容及步骤
引入新课
讲授新课
讲授新课
讲授新课
讲授新课
课堂小结
作业布置
【任务引入】
C620型车床结构如图3-25所示,请将主轴箱、刀架拖板、溜板箱、尾座四大部件从床身上拆卸下来。
【任务分析】
由于机床部件质量一般比较大,拆卸时除了要遵守前面两个模块所讲的机床零部件拆卸原則外,还要注意査看部件的承重部位在哪里,分析拆离承重部位后,部件将会停靠在哪里,要不要使用支撑,如何拆卸相关约束,如何搬走或吊离等问题。
本任务主要通过对车床主要部件的拆卸,掌握如何拆卸机床主要部件,同时进一步了供车床整体结构以及各部件的结构和功能,为下一步的装配和调整做好准备。
【相关知识】
一、车床的主要部件
1、床身部分
床身(见图3-26)是保证各部件装配在所需位置的基体零部件,它支撑和连接车床其他多郤件并保证各零部件间的正确位置和相互运动关系。
床身导轨在水平面内的直线度、在垂直面内的直线度、导轨的扭曲度、导轨的平行度以及导轨与导轨之间、导轨与平面之间的度对车床的精度有很大的影响。
2、主轴箱部分
主轴箱由箱体、摩擦式离合器、各传动轴、主轴、变速操纵机构、制动器和润滑装置等组成。
主要用于安装主轴和主轴的变速机构,主轴前端安装卡盘以夹紧工件,并带动工件旋转实现主运动。
主轴箱是加工时的主运动部件,主轴的精度即主轴径向跳动和轴向窜动,以及主轴回转中心线对床身导轨的平行度等对加工质量有很大影响。
3、进给箱部分
进给箱是车床的进给调整机构,进给箱的作用是把从主轴经挂轮机构传来的运动传给光杠或丝杠,取得不同的进给量和螺距。
进给箱中装有进给运动的变速机构,调整其变速机构,可得到所需的进给量或螺距,通过光杠或丝杠将运动传至刀架就可以实现不同进给速度的切削。
操纵杠可控制主轴正转、反转和停止。
4、溜板箱部分
溜板箱是车床进给运动的操纵箱’内装有将光杠和丝杠的旋转运动变成刀架直线运动的机构,通过光杠传动实现刀架的纵向进给运动、横向进给运动和快速移动,通过丝杠带动刀架做横向直线运动,以便车削螺纹。
5、刀架拖板部分
刀架拖板结构如图3-27所示,它主要用于装卡刀具,并使之实现纵向和横向切削加工,主要机件由大托板、中托板、回转底座、小拖板及装卡刀具组成。
6、尾座部分
尾座是车床的辅助支撑机构。
主要机件有尾座体、尾座底板及尾座顶。
尾座用于安装支承叫床工件,还可以安装中心钻、钻头、铰刀等其他切削工具。
二、机床部件拆卸时的吊挂吊离方法
由于机床部件往往比较重,拆卸时,往往用到吊装设备。
使用到吊装设备时,应注意以下的安全措施:
1、部件的挂吊点必须选择能使部件保持稳定的位置
首先应当使用原设计的挂吊位置。
在没有专用挂吊装置时,应充分估计部件的重心,如图3-28所示,主轴箱在吊离时,应将a、b两处同时挂住,如果只挂a处或b处,主轴箱起吊时将发生偏转。
2、要充分考虑拆卸过程中挂吊点的受力变化
如图3-29a所示,拆卸C620型车床进给箱时,一般首先拆下两个定位销,接着用吊绳将箱体两端挂住,在紧固螺钉拆松之前吊绳不能挂得太紧,只要吊绳稍微受力即可。
当拆卸紧固螵钉时,由于进给箱是安装在床身垂直面上的部件,其拆卸顺序应由下而上,即先拆螺钉1、2,然后才能拆卸螺钉3、4。
如先拆螺钉3、4,则当松开螺钉1、2时,即会发生如图3-29b所示的情况,因其重心高于支撑点,部件会发生突然偏转,可能别坏螺钉或箱体边缘,甚至发生人身事故。
对于垂直面上安装的重型部件,都应当注意这一情况。
3、要充分估计挂吊处的强度,是否足以承受部件的重量,同时挂吊点应尽可能靠近箱壁、法兰等处,因为这些地方刚度较强。
4、部件吊离时,吊车应使用点动起吊,并用手试推部件,观察其是否完全脱离紧固装置,或被其他件挂住。
如图3-28所示,C620型车床主轴箱的定位螺钉较为隐蔽,易于漏拆,随便起吊容易发生事故。
5、对于具有垂直滑道面的部件,如图3-30所示的镗床主轴箱,在拆卸时,一般应将其降到最低位置,把滑道面锁住,下面用枕木垫实,防止部件在拆卸过程中突然下滑。
6、部件在吊运移动过程中,应保持部件接近地面的最低位置行走一般不允许从人头或机床上空越过。
7、部件在吊放时,要注意强度较弱的尖角、边缘和凹凸部分,防止碰伤或压溃,如图3-31所示主轴箱放置时要注意枕木髙于螺母的高度。
【任务实施】
一、准备
1、切断所有电源。
2、准备工具:
扳手、旋具、拉出器、锤子、铜棒衬垫、弹性卡簧钳、油池、毛刷等。
3、准备材料:
棉纱、柴油。
4、清理、清洗车床外表面。
二、拆卸主轴箱部件
步骤如下:
1、结合图样查看主轴箱实物,分析主轴箱通过哪些连接零件与床身、刀架拖板等零部件相连接。
制定一个拆卸方案。
2、卸下主电动机皮带。
3、卸下主轴箱所有的紧固螺栓和销钉。
4、将主轴箱吊运到指定的地点,用木板垫住。
三、拆卸溜板箱
步骤如下:
1、结合图样查看溜板箱实物,分析溜板箱通过哪些连接零件与床身、刀架拖板等零部件相连接。
制定一个拆卸方案。
2、放溜板箱的油。
3、溜板箱下放千斤顶支架,高度到溜板箱底部。
4、卸下“三杠”链接套、销及“三杠”托架。
5、卸下溜板箱所有的紧固螺栓和销钉,使千斤顶支架下滑一定距离,卸下溜板箱。
6、将溜板箱吊运到指定的地点,用木板垫住。
四、拆卸刀架拖板
步骤如下:
1、结合图样查看刀架拖板实物(见图3-27),分析刀架拖板通过哪些连接零件与床身、溜板箱等零部件相连接。
制定一个拆卸方案。
2、卸下刀架拖板与导轨连接的锁紧压块。
3、将刀架拖板吊运到指定的地点,用木板垫住。
五、拆卸尾座
步骤如下:
1、结合图样査看尾座实物,分析尾座通过哪些连接零件与床身相连接。
制定一个拆卸方案。
2、卸下尾座与床身导轨连接的锁紧压块。
3、将尾座吊运到指定的地点,用木板垫住。
1、车床的主要部件和功能
2、机床部件拆卸时的吊挂吊离方法
3、主轴箱、溜板箱、刀架拖板、尾座等部件的拆卸
练习题
1、说出车床主要部分名称及用途?
2、使用吊装设备拆卸部件时应该注意哪些事项?
授课日期
授课班级
授课课时
2
授课形式
新授
授课章节
名称
任务3床身的检测、调整
(一)
使用教具
多媒体
教学目的
1、掌握机床导轨的检测方法
2、掌握刮削调整技能
教学重点
1、车床导轨直线度要求
2、床鞍导轨与尾座导轨的平行度
3、刮削的一般工艺过程
4、刮刀种类
教学难点
1、刮削的一般工艺过程
2、刮刀种类
更新、补充、删节内容
无
课外作业
教学后记
授课主要内容和板书
教学过程
主要教学内容及步骤
引入新课
【任务引入】
查阅相关技术标准获取车床床身(见图3-26)导轨精度指标,检测车床床身是否符合指标要求。
如果不符合,分析原因并进行必要的调整,使之完全符合指标要求。
【任务分析】
床身是保证各零部件装配在特定位置的基本零部件,它的精度直接或间接影响车床的整体精度。
检测床身导轨的精度对掌握机床状况和为下一步的
讲授新课
讲授新课
讲授新课
讲授新课
讲授新课
讲授新课
课堂小结
作业布置
维修调整都具有重要的意义。
车床导轨面的局部维修调粮主要是研刮。
研刮调整是机床维修钳工必备的技能之―,本任务通过对车床导轨的调整使学生掌握研刮的基本要领。
【相关知识】
1、床身导轨的技术要求
床身导轨是床鞍、尾座等移动的导向面,是保证刀具直线移动的关键。
如用3-32所示为卧式车床床身导轨的截面图。
其中,2、6、7为床鞍用导轨,3、4、5为尾座用导轨,1、8为压板用导轨。
床身装配是机床装配的基础,床身导轨的精加工是在床身与床脚用螺栓连接后进行的,最终达到如下要求。
1、床身导轨的几何精度
1)车床导轨直线度要求
车床导轨直线度主要指导轨面水平面内的直线度和垂直面内的直线度。
对矩形导轨,水平表面控制导轨在垂直平面内的直线度(见图3-33a)。
矩形导轨的两侧面控制导轨在水平面内的直线度(见图3-33b)。
对V形导轨,因为组成导轨的是两个斜表面,所以两个斜表面既控制垂直平面内的直线度(见图3-33c),同时也控制水平面内的直线度(3-33d)。
车床导轨直线度一般要求如下:
在垂直平面内,全长上为0.03mm,在任意500mm测量长度上为0.015mm,只许中间凸;在水平面内,全长上为0.025mm。
2)床鞍导轨的平行度
对于每条导轨的表面形状,除了在水平面内和垂直平面内有直线度要求外,为了保证导轨和运动部件相互配合良好,提高接触率,还要求控制导轨表面的扭曲,这对大型导轨特别重要。
在刮研时,为了测量导轨间的平行度,作为基准测量用的导轨,更要防止有严重扭曲。
车床导轨表面扭曲的检验方法如图3-34所示,V形导轨用V形水平仪垫铁,平导轨用平垫铁,从导轨的任一端开始,移动水平仪垫铁,每隔200~500mm读数一次,水平仪读数的最大代数差值,即为导轨的扭曲误差。
该项误差要求在机床精度标准中都未规定,主要规定于刮研或配磨工艺中。
图3-33导轨的直线度
车床床鞍导轨平行度一般要求在全长上为0.04mm/1000mm,通常使用专用桥形平板放于床鞍两条导轨上,在桥形平板上横向放置水平仪,在导轨全长上每隔200~500mm读数一次,用计算或在网格纸上绘出曲线图的方法算出导轨的平行度误差。
3)床鞍导轨与尾座导轨的平行度
在垂直平面与水平面全长上均为0.04mm,任意500mm测量长度上为0.03mm。
通常采用拉表的方法测量。
4)床鞍导轨对床身齿条安装面的平行度
全长上为0.03mm,在任意500mm测量长度上为0.02mm。
通常也采用拉表的方法进行测量。
2、接触精度
刮削导轨的接触点应不少于10点/(25mm×25mm)。
磨削导轨则以接触面积大小来评定接触精度的髙低。
3、表面粗糙度
刮削导轨表面粗糙度值一般在Ra1.6μm以下,磨削导轨表面粗糙度值一般在Ra0.8μm以下。
‘
4、硬度
一般导轨表面硬度应在170HB以上,并且全长硬度一致,与之相配合件的硬度应比导轨硬度稍低。
5、导轨稳定性
导轨在使用中应不变形。
除采用刚度大的结构外,还应进行良好的时效处理,以消除内应力,减少变形。
二、刮削技术
刮削是钳工的基本操作方法之一,使用各种不同形状的刮刀,在工件表面上刮去一层薄薄的金属层,以提高工件的加工精度。
刮削的劳动强度比较高,尤其是在机床制造的装配工序,刮削的工作量对于整个装配工作量来说,占有很大的比例。
通常,工件经过刨、铣等机械加工后,达不到工艺图样的要求,往往要凭借刮削的方法来保证和进一步提离工件的精度。
例如:
1)相互运动着的导轨副,它的两个摩擦面要求有良好的接触率,接触面积大,承受的压力也就大,耐磨性就好。
2)相互连接的两个工件中,结合表面质量高,连接的刚度就强,能使部件的几何精度更趋于稳定,不易产生变形。
3)对有密封性要求的表面,如果表面质量差,就会产生漏油、漏气等不良现象。
4)要求有准确的尺寸和公差配合的工件,而且这些相配工件的尺寸都必须保证在允许的公差范围内。
5)机床在装配过程中,要求达到理想的几何精度,需通过调整封闭环的尺寸来实现。
以上所述各项质量要求,一般都需要通过刮削来达到。
因此,要求对刮削工作予以足够的重视。
1、刮削原理和一般刮削过程
1)刮削原理
刮削也是金厲切削的一种形式,伹和车、刨、铣等机械加工的连续切削不同,由车、刨、铣等加工出来的工件表面精度,主要依靠工作母机本身的精度。
由于在连续切削过程中,不可避免地会产生各种因素引起的振动、刀具的磨损以及热变形等情况,使加工出来的工件表面精度受到不同程度的影响。
而刮削主要是运用显示凸点和微踱切削来提高工件的精度和表面质量。
刮削的要点有二:
(1)通过显示凸点法,能够准确地显示出工件表面上不合格的部位,即将工件平面上较高的部位显示出来,并加以分析,有助于刮除。
(2)选择合适的刮刀,进行微量切削,刮去较高部位的金属层。
这样经过反复地显示凸点和合理地进行刮削,能使工件的加工精度达到预期的要求。
2)刮削前的准备
工件在刮削前,要清理表面的锈迹,倒钝棱边和去掉毛刺,然后进行调整。
如被刮工件的面积较小,又只要求表面的直线度误差时,可由推磨的标准平板根据显点来保证,像这类大的平面,直线度误差不能单纯地由推磨的标准平板获得,需要通过测量,则被刮工件应采用可调垫铁支撑,以便于测量时调整。
3)刮削的一般工艺过程
刮削的一般工艺过程可分为粗刮、细刮和刮花纹等。
(1)粗刮。
首先要通过测量和显点以确定刮削部位,并要知道这个部位该刮去多少金属,粗刮的刮削量很大,可集中在这个部位重刮数遍,但刀纹要交错进行,才能保证每遍的刮量均匀,防止刮出一个个深凹。
用这种方法进行粗刮能减少显点次数,从而提高了工效。
(2)细刮与精刮。
经过粗刮后的工件表面,其直线度误差基本上已达到要求,显点也稀稀落落地分布于整个平面。
因此,进行细刮时,只挑选大而亮的显点,而且每刮一次,显点一次,显点也逐渐地由稀到密,由大到小,直至达到每25mm×25mm内显点若干的要求。
精刮在细刮的基础上进行,刮削方法与细刮相同,仍旧是挑选磨得最亮的点子来刮削,刀纹要短要细,以达到更髙的精度。
(3)刮花纹。
工件经过刮削后,其表面已经形成了花纹,但这种花纹是不规则的,而且不美观。
所以一般对刮削后的工件表面,或经过精刨、精磨以后的表面,还要再刮一层花纹,这样对导轨来说,能够增加其表面的润滑条件,减少摩擦阻力,从而提高了它的耐磨性能,延长了使用寿命。
并且在维修时,可根据花纹的消失情况来判断导轨表面的磨损程度。
如在非运动表面或外露表面上刮一层花纹,则可提高机床的外观质量。
2、花纹的种类及其刮削方法
常见的花纹有如图3-35所示的几种:
图3-35a、b所示的地毡花纹与斜花纹常刮在仪器仪表上,也可刮在其他外露表面作为装饰。
图3-35c、d所示的月牙花纹和链条花纹常刮在滑动导轨面。
在生产实践中,根据操作者的不同技巧,还可刮削出更多的花纹,如鱼鳞花纹、燕子花纹等。
刮削花纹时,除了掌握刮削的基本功以外,还需具有一定的技巧,才能使刮出的花纹整齐、美观、光滑。
刮削地毡花纹和斜花纹:
刮刀在一定的点上,平行往复推刮2~3次,使其出现有规则的方块。
刮削月牙花纹:
左手按住刮刀前部,起着压和掌握方向的作用,右手握住刮刀中部并做适当扭动,交叉成46°方向进行,在光线的反射下能显示出明暗、美观的月牙花纹。
刮削链条花纹:
先刮出一条半圆花纹,又像连续的月牙花纹,刮时,刮刀右角先落,左角稍抬,在综合作用下,刮刀连推带扭