立式铣床加工拨叉的课程设计.docx
《立式铣床加工拨叉的课程设计.docx》由会员分享,可在线阅读,更多相关《立式铣床加工拨叉的课程设计.docx(16页珍藏版)》请在冰豆网上搜索。
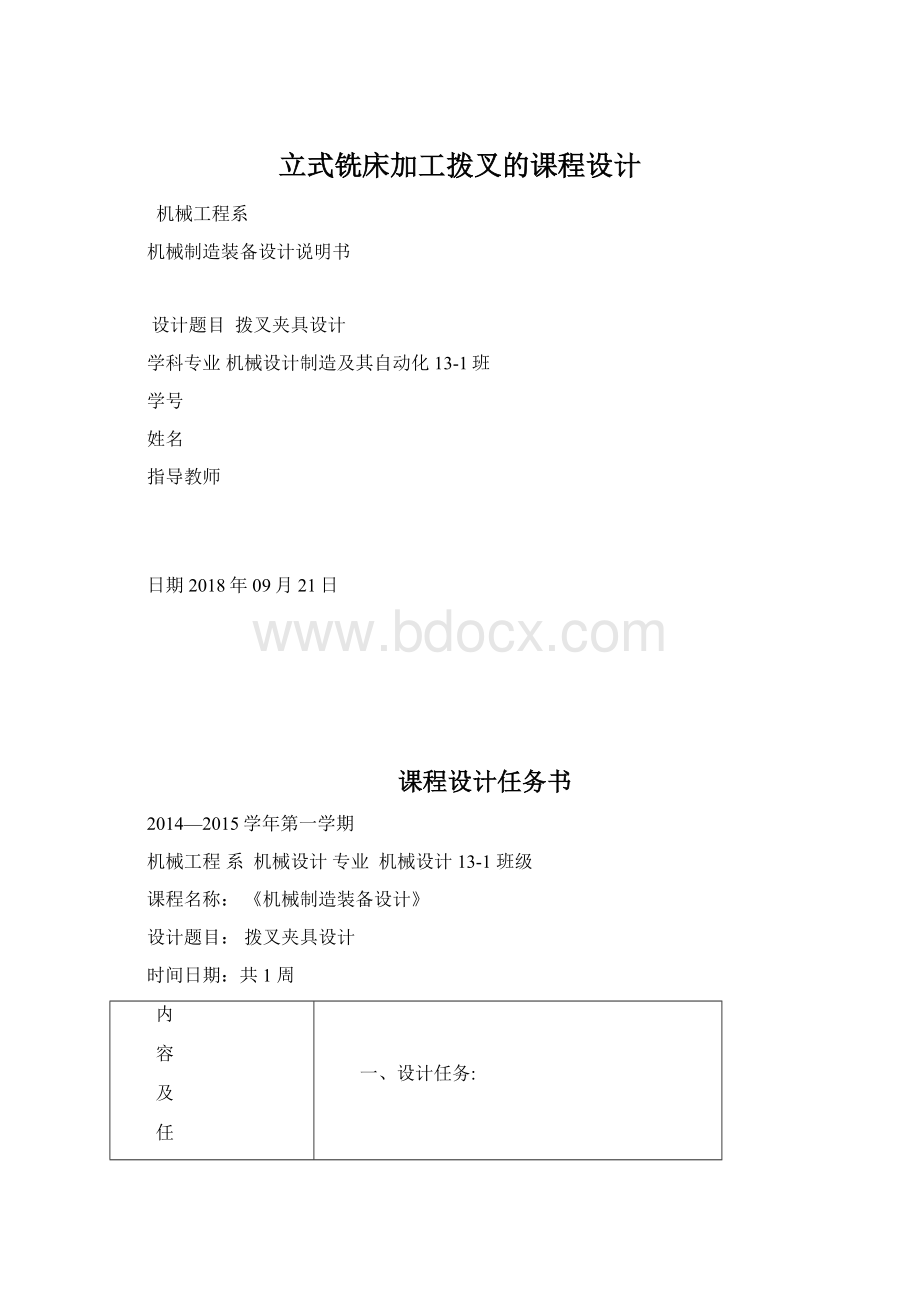
立式铣床加工拨叉的课程设计
机械工程系
机械制造装备设计说明书
设计题目拨叉夹具设计
学科专业机械设计制造及其自动化13-1班
学号
姓名
指导教师
日期2018年09月21日
课程设计任务书
2014—2015学年第一学期
机械工程系机械设计专业机械设计13-1班级
课程名称:
《机械制造装备设计》
设计题目:
拨叉夹具设计
时间日期:
共1周
内
容
及
任
务
一、设计任务:
1.加工条件
孔
、尺寸28的端面、
已加工出
采用立式铣床加工
2.加工要求
加工出尺寸
的两个端面,要求:
(1)与定位基准
轴线垂直度为0.15
(2)距离
其中一端面
3.提交任务要求
(1)拨叉零件图(2D电子版&纸质版);
(2)拨叉铣床夹具装配图(2D电子版&纸质版);
(3)拨叉铣床夹具装配3D,并呈现爆炸视图;
(4)拨叉零件3D
(5)拨叉铣床夹具设计说明书零件图、装配图装订成册
要求内容:
1拨叉零件图;
2拨叉铣床夹具装配图;
3夹具定位基准误差分析;
4夹具零件3D截图展示,及设计说明;
二、设计工作量
1、设计计算说明书一份,非标准零件图1-2张,专用夹具装配总图1张,夹具爆炸图1张(3D图);图纸工作量应大于一张A0图;
2、设计说明书及图纸必须为计算机输出稿;
上交作业应包括电子稿以及打印稿,设计说明书文件格式为word2003版本,平面工作图纸文件格式为Autocad2008或以下版本文件dwg格式,3D图可采用任何一种三维造型软件绘制。
进度安排
起止日期
工作内容
2015.1.5
1、设计准备工作:
熟悉设计任务书,明确设计的内容与要求;2、熟悉设计指导书、有关资料、图纸等
3、结构方案分析;
2015.1.6
机构(夹具)草图设计;机构(夹具)分析计算;
2015.1.7-1.9
装配图绘制草图;夹具零件图绘制;
2015.1.10
编写设计计算说明书;
2015.1.11
答辩
主要参考资料
1.《机械制造装备设计》冯辛安等著机械工业出版社
2.《机械制造装备设计课程设计》陈立德编高等教育出版社
3.《机械制造装备设计》陈立德编高等教育出版社
4.《金属切削机床夹具设计手册》浦林详等编机械工业出版社
5.《金属切削机床设计》戴曙著机械工业出版社
指导教师(签字):
2014年12月22日
系(教研室)主任(签字):
年月日
目录
1分析零件图纸并确定其生产类型1
1.1零件的作用1
1.2零件的工艺分析1
1.3零件的生产类型2
2.总体方案的确定2
2.1定位方案2
2.2定位基准的选择3
2.3加工中心上加工
的两个端面的工艺步骤4
2.4机械加工余量、工序尺寸及毛坯尺寸的确定4
2.5定位元件和定位装置的设计和选择7
2.5.1长圆柱销7
2.5.2支撑钉7
2.5.3螺母7
2.6夹紧方案8
2.7夹具体的设计8
3.定位误差9
4.绘制夹具装配总图9
5.夹具精度设计10
参考文献11
1分析零件图纸并确定其生产类型
1.1零件的作用
题目所给的零件是CA6140车床的拨叉。
它位于车床变速机构中,主要起换档,使主轴回转运动按照工作者的要求工作,获得所需的速度和扭矩的作用。
零件上方的φ14mm孔与操纵机构相连,二下方的φ40mm半孔则是用于与所控制齿轮所在的轴接触。
通过上方的力拨动下方的齿轮变速。
零件如图1-1所示。
图1-1拨叉夹具实体
1.2零件的工艺分析
该拨叉形状特殊、结构简单,属典型的叉杆类零件。
为实现换档、变速的功能,其叉轴孔与变速叉轴有配合要求,因此加工精度要求较高。
叉脚两端面在工作中需承受冲击载荷,为增强其耐磨性,该表面要求高频淬火处理,硬度为48~58HRC;为保证拨叉换档时叉脚受力均匀,要求叉脚两端面对叉轴孔
mm的垂直度要求为0.15mm。
拨叉头两端面和叉脚两端面均要求铣加工,并在轴向方向上均高于相邻表面,这样既减少了加工面积,又提高了换档时叉脚端面的接触刚度;该零件除主要工作表面(拨叉脚两端面、变速叉轴孔
mm,其余表面加工精度均较低,不需要高精度机床加工,通过铣削、钻床、攻丝的粗加工就可以达到加工要求;而主要工作表面虽然加工精度相对较高,但也可以在正常的生产条件下,采用较经济的方法保质保量地加工出来。
由此可见,该零件的工艺性较好。
该零件的主要工作表面为拨叉脚两端面和叉轴孔
mm的孔表面,在设计工艺规程时应重点予以保证。
在本次课程设计中,已知加工条件孔
、尺寸28的端面、
已加工出,采用立式铣床加工。
要加工要求加工出尺寸
的两个端面,要求:
与定位基准
轴线垂直度为0.15,距离其中一端面
。
有图知拨叉零件的材料为ZG45。
孔
、尺寸28的端面、
已加工零件如图1-2所示。
图1-2拨叉零件图
1.3零件的生产类型
根据设计任务已知拨叉夹具零件,要求加工出尺寸
的两个端面,进行夹具设计,生产批量为中批量生产。
2.总体方案的确定
2.1定位方案
根据零件图要求可知,本道工序的内容是铣削
两端的平面,所选用的是立式铣床,在手动的专用夹具中加工完成。
根据工序图给出的定位元件方案,按有关标准正确选择定位元件或定位的组合。
在机床夹具的使用过程中,工件的批量越大,定位元件的磨损越快,选用标准定位元件增加了夹具零件的互换性,方便机床夹具的维修和维护。
利用过度配合将长圆柱销定位在夹具体上,并用短支撑钉辅助支撑作用,工件被完全定位。
分析工序简图可知,拨叉锁销孔
mm,孔的轴线对
mm的两端面垂直度为0.15,
mm的一端面距离拨叉轴孔面的尺寸为
mm。
从基准的重合原则和定位的稳定性、可靠性出发,定位装置选用一个支撑钉销和两个长圆柱销,长圆柱销与工件定位孔配合,限制四个自由度(x,y的转动,x,y的移动),定位销轴肩小环面与工件定位端面接触,限制一个自由度(z的转动),一个支撑钉起辅助支撑作用,限制一个自由度(z的移动),实现工件正确定位。
定位孔与定位销的配合尺寸取为
(在夹具上标出定位销配合尺寸
)。
根据本次夹具设计的零件,由于铣削拨叉的两个弧状端面,故我设计的定位方案如图2-1所示,一次同时加工两个零件,有利提高加工效率,采用长销和可换支撑钉进行定位加工。
定位示意图如下2-1:
图2-1定位示意图
2.2定位基准的选择
1.粗基准选择
该拨叉其他主要表面都加工完成,为保证零件加工相对于已加工表面具有一定位置精度的原则,选叉轴孔外轮廓表面作为粗基准。
2.精基准选择
根据该拨叉零件的技术要求,选择拨叉头叉轴孔
作为精基准,零件上的加工表面都可以采用它作基准进行加工,即遵循了“基准统一”原则。
拨叉轴孔
的中心线是设计基准,选用其作精基准定位加工拨叉脚两侧
圆弧面,实现了设计基准和工艺基准的重合,保证了被加工表面的垂直度要求。
2.3加工中心上加工
的两个端面的工艺步骤
在加工过程中,采用一个工序两次安装的方法对拨叉脚的两个圆弧端面进行加工,在加工工程中,更换不同高度的支撑钉对工件进行支撑,减少误差其表面加工方案如表1。
表1拨叉零件各表面加工方案
加工表面
加工经济精度IT
加工情况
表面粗糙度
备注
铣拨叉脚
mm上端圆弧面
IT14
粗铣端面
6.3
铣拨叉脚
mm下端圆弧面孔
IT14
粗铣端面
6.3
2.4机械加工余量、工序尺寸及毛坯尺寸的确定
(1)零件材料为ZG45,硬度156~217HB,生产类型中批量。
按以上原始资料及加工路线,分别确定各家工表面的机械加工余量、工序尺寸及毛坯尺寸如下:
外圆表面延轴线方向长度方向的加工余量及公差(φ40端面)。
查《机械制造工艺设计简明手册》(以下称《工艺手册》)表2.2.4~2.2.5,取φ40端面长度余量均为2.5(均为双边加工)。
铣削加工余量为:
粗铣2.0mm;精铣0.5mm
(2)确立切削用量及基本工时
工序:
粗、精铣
的下端面
1)加工条件
工件材料:
ZG45。
=0.34GPaHBS=156~217,铸件
机床:
立式铣床
刀具;W18Cr4V硬质合金端铣刀
W18Cr4V硬质合金端铣刀,牌号为YG6,由《切削用量简明手册》〉后称《切削手册》表3.1查得铣削宽度ae≤60mm,深度ap≤4,齿数Z=10时,取刀具直径do=80mm。
又由《切削手册》表3.2选择刀具的前角ro=+5o;后角ao=8o;副后角a'o=
刀齿斜角λs=-10o,主刃Kr=60o,过渡刃Krε=30o,副刃Kr’=5o,过渡刃宽bε=1mm。
2).切削用量
粗铣
的下端面
a)切削深度因切削用量较小,故可以选择ap=1.5mm,一次走刀即可完成所需尺寸。
b)每齿进给量:
由《切削手册》表3.30可知机床的功为7.5KW,查《切
削手册》表3.5可得f=0.14~0.24mm/z,由于是对称铣,选较小量f=0.14mm/z。
c)查后刀面最大磨损及寿命
查《切削手册》表3.7,后刀面最大磨损为(1.0~1.5)mm
查《切削手册》表3.8,寿命T=180min
d)计算切削速度按《切削手册》表3.27中的公式:
也可以由表3.16查得
=98mm/sn=439r/minvf=490mm/s又根据铣床参数,选n=475r/minvf=600mm/s,则实际的切削速度为:
即
=
=119.3m/min,实际进给量为:
即
=
=0.13mm/z
e)校验铣床功率查《切削手册》表3.24,Pcc=1.1KW,而铣床所提供的功率Pcm为1.7KW,所以Pcm>Pcc,故校验合格。
最终确定ap=1.5mmnc=475r/minvfc=600mm/minvc=119.3m/minfz=0.13mm/z
f)计算基本工时
公式中:
L=l+y+Δ;根据《切削手册》表3.26,可得l+Δ=0所以L=l+y+Δ=72mm。
故
=72/600=0.12min
精铣
的下端面
a)切削深度因切削用量较小,故可以选择ap=1.0mm,一次走刀即可完成所需尺寸。
b)每齿进给量:
由《切削手册》表3.30可知铣床的功为7.5KW,查《切削手册》表3.5可得f=0.5~0.7mm/r,由于是对称铣,选较小量f=0.7mm/r。
c)查后刀面最大磨损及寿命
查《切削手册》表3.7,后刀面最大磨损为(1.0~1.5)mm
查《切削手册》表3.8,寿命T=180min
d)计算切削速度按《切削手册》表3.27中的公式:
也可以由表3.16查得
=124mm/svf=395mm/minn=494r/min,根据铣床参数,选n=475r/minvf=375mm/min,则实际的切削速度为
所以
=
=119.3m/min,实际进给量
所以
=
=0.08mm/z。
e)校验铣床功率查《切削手册》表3.24,Pcc=1.1KW,而铣床所提供的功率Pcm为1.7KW,所以Pcm>Pcc,故校验合格。
最终确定ap=1.0mmnc=475r/minvfc=375mm/minvc=119.3mm/min
f)计算基本工时
公式中:
L=l+y+Δ;根据《切削手册》表3.26,可得l+Δ=80mm,所以L=l+y+Δ=32+80=112mm。
故
=112/375=0.3min
2.5定位元件和定位装置的设计和选择
2.5.1长圆柱销
材料:
45钢热处理35-40HRC,本次设计中采用长销钉用于工件的定位,通过开槽沉头螺钉和4个圆柱销将长销固定在夹具体上,长销与工件的孔
进行配合。
配合尺寸为
,限定了工件的四个自由度。
长圆柱销如图2-2所示。
图2-2长圆柱销
2.5.2支撑钉
材料:
45钢热处理30-35HRC,按GB/T2160-91查得,在设计中采用了可换支撑钉,支撑高度都进行了严格的限制,保证了支撑的高度,本设计中采用两次安装加工,要换不通知称高度的支撑钉。
其形状如图2-3所示。
图2-3支撑钉
2.5.3螺母
材料:
45钢热处理35-40HRC,按GB/T41查得,选用标准件六角螺帽M12。
2.6夹紧方案
车床夹具的夹紧装置必须安全可靠。
夹紧力的方向和作用点应按以下要求进行选择:
(1).主要夹紧力应朝向主要定位基准,作用点应靠近支承面的几何中心;
(2).夹紧力的方向应有利于减少夹紧力,尽量垂直于工件的主要定位基面,尽量和切削力、重力方向一致;
(3).夹紧力的方向和作用点应施于工件刚性较好的方向和部位;
(4).夹紧力的作用点应适当靠近加工表面。
由于工件为中等批量生产,产量不大,宜用简单的手动夹紧装置。
采用长圆柱销通过开槽沉头螺钉连接夹具体,并采用支撑钉支撑,通过螺帽夹紧工件来实现夹紧。
长圆柱销夹紧工件主要是为了防止工件在加工过程中受力的作用产生倾覆和振动,手动夹紧是可靠的,可以免去夹紧力的计算。
图2-6夹紧方案图
2.7夹具体的设计
本夹具加工的是
的两个端面,因此在底板上设置支撑板、长圆柱销、支撑钉,将定位、夹紧装置连接成一体,并能正确地安装在铣床上。
如下图2-7所示。
图2-7夹具体
3.定位误差
本工序采用两个支撑钉,支撑定位,工件的一面通过支撑钉支撑。
但是,由于加工是自由公差,故应当能满足定位要求。
4.绘制夹具装配总图
夹具由底板、长圆柱销,支撑钉、螺母、垫圈、圆柱销开槽沉头螺钉零件组成。
(见附图4-1、4-2、4-3)
图4-1总装配图
图4-2爆炸图
图4-3总装配图
5.夹具精度设计
为确使夹具能满足工序要求,在夹具技术要求指定以后,还必须对夹具进行精度分析。
加工过程中厚度为
的板,此项要求由刀具精度保证,与夹具精度无关。
所以,该铣平面夹具能满足铣面工序要求,可行。
参考文献
【1】.《机械制造装备设计》冯辛安等著机械工业出版社
【2】.《机械制造装备设计课程设计》陈立德编高等教育出版社
【3】.《机械制造装备设计》陈立德编高等教育出版社
【4】.《金属切削机床夹具设计手册》浦林详等编机械工业出版社
【5】.《金属切削机床设计》戴曙著机械工业出版社