电泳涂装的漆膜弊病及其防治.docx
《电泳涂装的漆膜弊病及其防治.docx》由会员分享,可在线阅读,更多相关《电泳涂装的漆膜弊病及其防治.docx(5页珍藏版)》请在冰豆网上搜索。
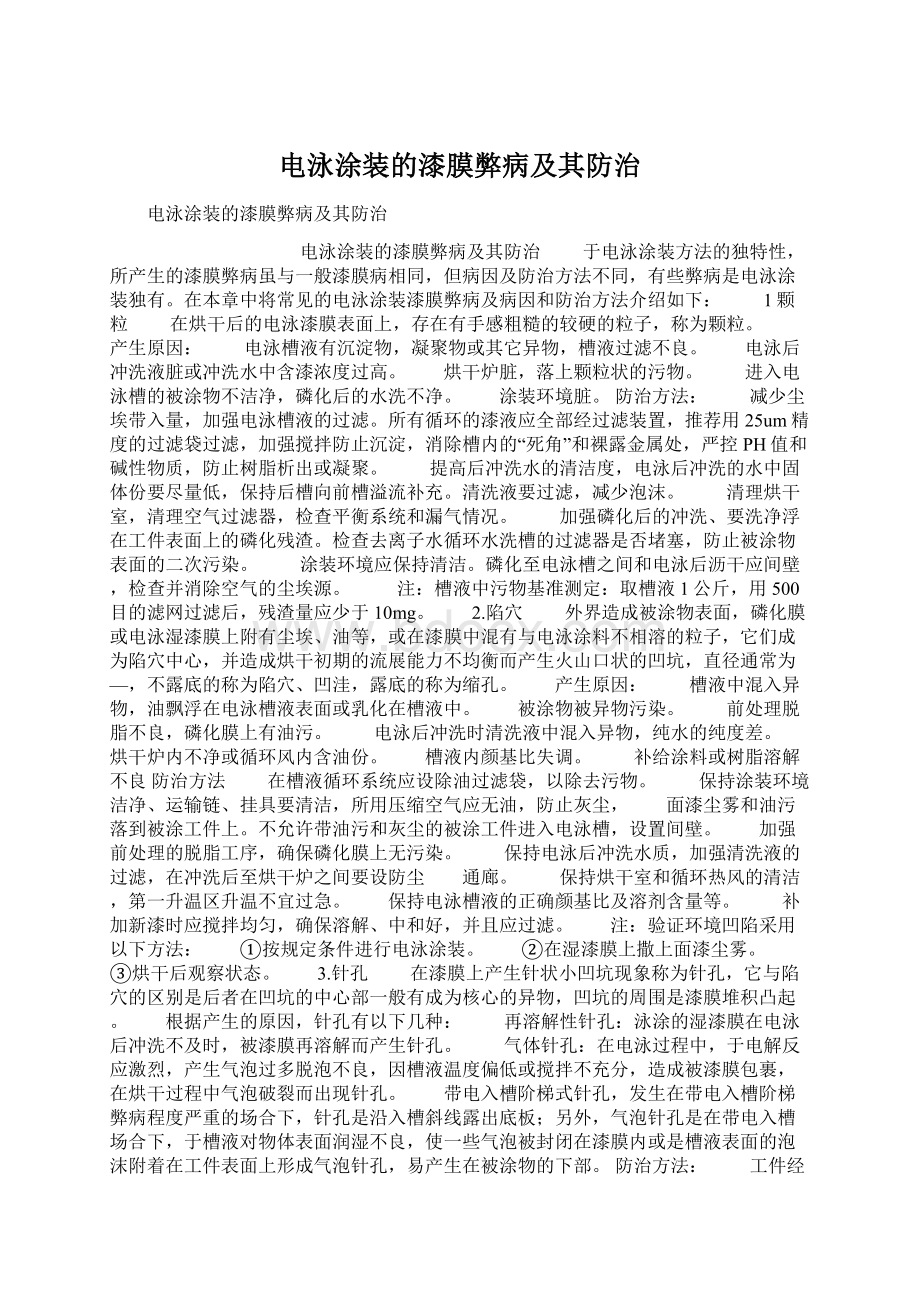
电泳涂装的漆膜弊病及其防治
电泳涂装的漆膜弊病及其防治
电泳涂装的漆膜弊病及其防治 于电泳涂装方法的独特性,所产生的漆膜弊病虽与一般漆膜病相同,但病因及防治方法不同,有些弊病是电泳涂装独有。
在本章中将常见的电泳涂装漆膜弊病及病因和防治方法介绍如下:
1颗粒 在烘干后的电泳漆膜表面上,存在有手感粗糙的较硬的粒子,称为颗粒。
产生原因:
电泳槽液有沉淀物,凝聚物或其它异物,槽液过滤不良。
电泳后冲洗液脏或冲洗水中含漆浓度过高。
烘干炉脏,落上颗粒状的污物。
进入电泳槽的被涂物不洁净,磷化后的水洗不净。
涂装环境脏。
防治方法:
减少尘埃带入量,加强电泳槽液的过滤。
所有循环的漆液应全部经过滤装置,推荐用25um精度的过滤袋过滤,加强搅拌防止沉淀,消除槽内的“死角”和裸露金属处,严控PH值和碱性物质,防止树脂析出或凝聚。
提高后冲洗水的清洁度,电泳后冲洗的水中固体份要尽量低,保持后槽向前槽溢流补充。
清洗液要过滤,减少泡沫。
清理烘干室,清理空气过滤器,检查平衡系统和漏气情况。
加强磷化后的冲洗、要洗净浮在工件表面上的磷化残渣。
检查去离子水循环水洗槽的过滤器是否堵塞,防止被涂物表面的二次污染。
涂装环境应保持清洁。
磷化至电泳槽之间和电泳后沥干应间壁,检查并消除空气的尘埃源。
注:
槽液中污物基准测定:
取槽液1公斤,用500目的滤网过滤后,残渣量应少于10mg。
2.陷穴 外界造成被涂物表面,磷化膜或电泳湿漆膜上附有尘埃、油等,或在漆膜中混有与电泳涂料不相溶的粒子,它们成为陷穴中心,并造成烘干初期的流展能力不均衡而产生火山口状的凹坑,直径通常为—,不露底的称为陷穴、凹洼,露底的称为缩孔。
产生原因:
槽液中混入异物,油飘浮在电泳槽液表面或乳化在槽液中。
被涂物被异物污染。
前处理脱脂不良,磷化膜上有油污。
电泳后冲洗时清洗液中混入异物,纯水的纯度差。
烘干炉内不净或循环风内含油份。
槽液内颜基比失调。
补给涂料或树脂溶解不良防治方法 在槽液循环系统应设除油过滤袋,以除去污物。
保持涂装环境洁净、运输链、挂具要清洁,所用压缩空气应无油,防止灰尘, 面漆尘雾和油污落到被涂工件上。
不允许带油污和灰尘的被涂工件进入电泳槽,设置间壁。
加强前处理的脱脂工序,确保磷化膜上无污染。
保持电泳后冲洗水质,加强清洗液的过滤,在冲洗后至烘干炉之间要设防尘 通廊。
保持烘干室和循环热风的清洁,第一升温区升温不宜过急。
保持电泳槽液的正确颜基比及溶剂含量等。
补加新漆时应搅拌均匀,确保溶解、中和好,并且应过滤。
注:
验证环境凹陷采用以下方法:
①按规定条件进行电泳涂装。
②在湿漆膜上撒上面漆尘雾。
③烘干后观察状态。
3.针孔 在漆膜上产生针状小凹坑现象称为针孔,它与陷穴的区别是后者在凹坑的中心部一般有成为核心的异物,凹坑的周围是漆膜堆积凸起。
根据产生的原因,针孔有以下几种:
再溶解性针孔:
泳涂的湿漆膜在电泳后冲洗不及时,被漆膜再溶解而产生针孔。
气体针孔:
在电泳过程中,于电解反应激烈,产生气泡过多脱泡不良,因槽液温度偏低或搅拌不充分,造成被漆膜包裹,在烘干过程中气泡破裂而出现针孔。
带电入槽阶梯式针孔,发生在带电入槽阶梯弊病程度严重的场合下,针孔是沿入槽斜线露出底板;另外,气泡针孔是在带电入槽场合下,于槽液对物体表面润湿不良,使一些气泡被封闭在漆膜内或是槽液表面的泡沫附着在工件表面上形成气泡针孔,易产生在被涂物的下部。
防治方法:
工件经泳涂成膜后,离开槽液立即用UF液冲洗,以消除再溶解性针孔。
在电泳涂装时,从工艺管理上应控制漆液中杂质离子的浓度,对各种离子的含量要控制在规定的范围之内,要求定期化验槽内各种离子浓度,如超标要排放超滤液,对极液也要控制在规范之内。
在磷化膜孔隙率高的情况下也易含气泡,因此应遵守工艺规定的温度。
为消除带电入槽的阶梯式针孔,要求槽液表面的流速大于米/秒,以消除堆积泡沫,在带电入槽的通电方式生产时,防止运输链速度过低。
为消除水洗针孔,首先要保证漆膜电渗性好,控制槽内溶剂含量及杂质离子的含量,以获得致密的漆膜,后冲洗的水压不可高于。
4.膜厚太薄 泳涂后工件表面的干漆膜厚度低于所采用电泳涂料技术条件或工艺规定的膜厚。
产生原因:
槽液的固体份过低。
泳涂电压偏低,泳涂时间太短。
槽液温度低于工艺规定的温度范围。
槽液中的有机溶剂含量偏低。
槽液老化,使湿漆膜电阻过高,槽液电导率低。
极板接触不良或损失,阳极液电导太低,被涂物通电不良。
电泳后冲洗过程中UF液清洗时间过长,产生再溶解。
槽液的PH值太低防治方法:
提高固体份,保证固体份稳定在工艺规定的范围内,固体份的波动最好控制在%以下。
提高泳涂电压和延长泳涂时间,使它们控制在合适范围内。
注意定期清理热交换器,检查是否堵塞,加热系统及示温元件是否出了故障,槽液温度控制在工艺规定的范围内或上限。
添加有机溶剂调整剂,使其含量达到工艺规定的范围。
加速槽液更新或添加调整剂,提高槽液电导和降低湿涂膜电阻。
检查极板是否有损失或表面有结垢,一定要定期清理或更换极板,提高阳极液电导,检查被涂工件通电是否良好,挂具上是否有涂料附着。
缩短UF液冲洗时间,防止再溶解。
添加中和度低的涂料,使槽液PH值达到工艺范围内。
5.漆膜过厚 被涂工件表面的干漆膜厚度超过所采用电泳涂料技术条件或工艺规定的膜厚。
产生原因:
泳涂电压偏高。
槽液温度偏高。
槽液的固体份过高。
泳涂时间过长 槽液中的有机溶剂含量过高,槽液熟化时间太短。
工件周围循环效果不好。
槽液电导率高。
阴/阳极比不对,阳极位置布置不当。
防治方法:
调低泳涂电压 槽液温度绝对不能高出工艺规定,尤其是阴极电泳漆,当漆温过高将会影响槽液的稳定性,维持槽液温度在工艺规定的温度范围的下限下生产。
将固体份降到工艺规定之内,固体份过高不仅使漆膜过厚而且表面带出槽液多,又增加后冲洗的困难。
控制泳涂时间,在连续生产时应尽可能避免停链。
控制槽液中的有机溶剂含量,排放超滤液,添加去离子水,延长新配槽的熟化时间。
通常因泵、过滤器及喷嘴堵塞而造成,应维修调整之。
排放超滤液,添加去离子水,降低槽液中的杂质离子的含量。
调整极比和阳极布置的位置 6.水滴迹 电泳漆膜烘干后局部漆面上有凹凸不平的水滴斑状的弊病。
产生原因:
湿电泳漆膜上有水滴,在烘干时水滴在漆膜表面上沸腾,液滴处产生凹凸不平的涂面。
在烘干前,湿电泳漆膜表面上有水滴,水洗后附着的水滴未挥发掉或未吹掉。
烘干前从挂具上滴落的水滴。
电泳水洗后,被涂物上有水洗液积存。
最终纯水洗的纯水量不足。
所形成的湿电泳漆膜的抗水滴性差。
进入烘干室后温升过急。
防治方法:
在烘干前吹掉水滴,降低晾干区的温度,将晾干区的温度调整到30~40℃。
采取措施防止挂具上的水滴落在被涂物上。
吹掉积存的清洗水或开工艺孔,或改变装挂方式解决被涂物上的积水问题。
提供足够量的纯水。
改变工艺参数或涂料组成来提高湿漆膜的抗水滴性。
在进入烘干室时避免升温过急,或增加予加热。
注:
水滴迹试验方法 ① 按规定条件电泳后吹干 ② 在试验样板的水平面上滴上试验液③ 照原水平状烘干后观察表面状态7.异常附着 被涂物表面或磷化膜的导电性不均匀,在电泳涂装时电流密度集中于电阻小的部分,引起漆膜在这部位集中成长,其结果在这部位呈堆积状态附着。
产生原因:
被涂物表面导电不均匀,致使局部电流密度过大。
磷化膜污染被涂物表面污染 前处理工艺异常:
脱脂不良,水洗不充分,有脱脂液和磷化液残留;磷化膜有发兰、黄锈斑。
此因产生的异常附着称为前处理异常附着。
槽内杂质离子污染,电导过大,槽液中有机溶剂含量过高;灰分太低。
泳涂电压过高,槽液温度高,造成漆膜破坏。
注:
验证前处理不良或前处理异物附着有以下两种方法。
A:
用100号砂纸将试验样板打磨一半表面,擦净后按规定条件进行电泳涂装,烘干后观察表面状态和膜厚。
B:
在试验样板上滴落几滴试验液,照原样按规定的条件进行电泳涂装,烘干后观察表面状态。
防治方法:
严格控制被涂物表面的质量,应无锈迹、焊药等。
要严格控制前处理各道工序,改进前处理工艺,确保脱脂良好,磷化膜均匀,水洗充分,应无黄锈、兰色斑。
严格控制槽液中杂质离子含量,防止杂质离子混入,排放超滤液,加去离子水来控制杂质离子含量和有机溶剂含量。
如果灰分过低则添加色浆。
泳涂电压不能超过工艺规定,尤其要控制被涂物入槽初期电压,降低槽液温度,采用较为缓和的电泳涂装条件,避免极间距太短。
8.泳透力低 复杂的被泳工件的箱形结构或背离电极部分泳不上漆或者涂得过薄的现象称为泳透力低。
产生原因:
所选用电泳漆的泳透力本身就差或泳透力变差。
泳涂电压过低。
槽液的固体份偏低。
槽液搅拌不足。
防治方法:
为使箱式结构能泳涂上漆,最根本的措施是选用泳透力高的材料,起码要选用75%的泳透力,严格检测进厂电泳漆和槽液的泳透力。
适当升高泳涂电压。
及时补加漆,确保固体份在工艺规定的范围。
加强槽液的搅拌。
9.干漆迹 于被涂物出电泳槽后至电泳后清洗之间时间过长,或电泳后清洗不充分,致使附着在湿电泳漆膜上的槽液干结,在烘干后涂膜表面产生斑痕,称为干漆迹。
产生原因:
电泳至水洗区之间的时间太长*。
0次水洗不完全,电泳后水洗不充分。
槽液温度偏高。
环境湿度低防治方法:
在工艺设计时应注意,被涂物从电泳槽出槽到0次电泳后清洗之间的时间宜选在1分钟之内。
强化0次水洗,使被涂物清洗完全。
适当降低槽液温度。
提高泳涂环境湿度。
注:
验证方法:
① 按规定的条件进行电泳涂装。
② 电泳后先不水洗,晾干一定时间。
③ 水洗、烘干后观察状态 10.二次流痕 按正常工艺电泳泳涂,水洗液有靠近被涂物的夹缝结构处在烘干后产生漆液流痕,这种现象称之为二次流痕。
产生原因:
电泳后水洗不良。
槽液的固体份过高,水洗水的含漆量也偏高。
被涂物的结构所造成。
进入烘干室时升温过急。
防治方法:
强化电泳后的水洗,增加浸式清洗工序,提高循环去离子水洗水的温度。
适当调低槽液的固体份,降低水洗水中的含漆量。
改进被涂物的结构,开供排液的工艺孔。
强化晾干的功能,为改善漆液的流动性将晾干室的温度调到30~40℃,并在被涂物进入烘干室之前进行加热,以避免夹缝中的水分在急剧升温中沸腾将漆液挤出。
11.再溶解 泳涂沉积在被涂物上的湿漆膜,被槽液或超滤清洗液再次溶解,产生使漆膜薄。
失光、针孔、露底等现象。
这种电泳涂装的漆膜弊病称之为再溶解。
产生原因:
被涂物电泳后在电泳槽或水洗液中停留时间过长。
槽液的PH值偏低,溶剂含量偏高,水洗水的PH值偏低;冲洗压力过高,冲洗时间过长。
防治方法:
在间歇式生产场合,断电后被涂物应立即从槽中取出,在连续式生产场合应带电出槽,水洗槽中停留时间不宜超过1分钟。
将槽液和水洗液的PH值严格控制在工艺规定范围内。
每次冲洗时间应控制在40秒左右,冲洗压力不应超过。
12.涂面斑印 底材表面污染,在电泳涂装后,干漆膜表面仍有可见的斑纹或地图状的斑痕,这种电泳漆膜称之为涂面斑印。
它与水迹和漆迹斑痕的不同之处是涂面仍平整。
产生原因:
* 磷化后的水洗不充分。
磷化后的水洗水的水质不良。
前处理过的被涂面再次被污染,如挂具上的污水滴落在前处理过的表面上。
防治方法:
强化磷化后的水洗,检查喷嘴是否有堵水洗塞。
加强磷化后水洗水的管理;新鲜去离子水洗后的滴水电导不应超过50us/cm。
注意涂装环境,保持清洁,防止前处理过的表面再污染,防止挂具上滴水。
注:
涂面斑印的验证方法 ① 将用纯水稀释过的前处理液滴落在前处理过的样板上,晾干10分钟。
② 在100℃下烘干10分钟。
③ 按规定的条件电泳、烘干、观察状态。
13.漆面不匀、粗糙 烘干后的电泳漆涂膜表面光泽、光滑度等不匀,有阴阳面。
这种电泳漆膜弊病称为漆面不匀或漆面粗糙。
轻者光泽不好或失光,漆膜外观不丰满,重的手感不好。
如果在电泳过程中处在垂直面的漆膜光滑有光泽,而处在水平面的电泳沉积漆膜粗糙无光泽,这种现象称为“L”效果不好。
*产生原因:
被涂物表面的磷化膜不均和过厚,磷化后的水洗不充分。
槽液的固体份过低,槽液中有细小的凝聚物,不溶性的颗粒,槽液过滤不良。
槽液的颜基比过高。
槽液中混入不纯物,如杂质离子等不纯物混入,槽液电导太高。
槽液中的溶剂含量过低。
在被涂物周围槽液的流速太低或不流动。
槽液的温度低。
防治方法:
改进磷化工艺,选用致密薄膜型磷化膜,加强磷化后的水洗及水洗水的水质 管理。
提高槽液的固体份,控制其在工艺规定的范围内,加强槽液的全过滤,尤其要除去易沉降的重的小颗粒。
通常减少色浆的补加量,来降低槽液的颜基。
排放超滤液,添加去离子水,来降低槽液中杂质离子含量和电导。
添加溶剂,来提高槽液中有机溶剂含量。
在电泳过程中加强槽液的循环和搅拌。
将槽液的温度严格地控制在工艺规定的范围内。
注:
参见第六章的“L”效果的试验方法。
14.带电入槽阶梯弊病 在连续式生产被涂物带电进入电泳槽的场合,涂面上产生多孔质的阶梯条纹状的漆膜弊病,这种弊病一般为带电入槽阶梯弊病。
产生原因:
入槽部位液面有泡沫浮游,泡沫吸附在被涂物表面上被沉积的漆包裹。
被涂物表面不湿不均或有水滴。
入槽段电压过高,造成强烈的电解反应,在被涂物表面产生大量的电解气体。
运输链速度太慢或有脉动防治方法:
加大入槽部位液面的流速,消除液面的泡沫。
吹掉被涂物表面的水滴,确保被涂物全干状态进入电泳槽。
降低入槽段的电压,在入槽段减少或不设电极。
加快运输链速度,一般链速在2米/分以下易产生带电入槽阶梯弊病,链速应均 匀脉动。
发生漆膜弊病时的检查要点NO现象确认事项 检查确认内容1膜厚不足 电压通电不良槽液温度加热残分 溶剂含量 检查电压是否适当检查挂具上是否有涂料附着,测极罩电阻槽液温度是否保持在工艺规定范围内 加热残分是否偏低槽液中的溶剂含量是否偏低2漆膜过厚 电压槽液温度加热残分通电时间 溶剂含量 检查电压是否适当槽液温度是否保持在工艺规定范围内加热残分是否偏高运输链速度是否变慢了槽液中的溶剂含量是否偏高3涂膜的缩孔、凹坑、针孔涂料、槽液环境纯水前处理 颜料分检查槽液中有无混入异物的痕迹被涂物是否有被油分,面漆雾污染纯水的水质是否合格脱脂是否不良颜料分是否偏低* 4涂膜有颗粒涂料、槽液水洗水被涂物 环境检查槽液内有无沉淀物,凝聚物或异物混入电泳后的清洗水是否太脏被涂物不清洁或磷化后水洗不充分涂装环境是否不清洁5二次流痕 涂料水洗加热残分是否过高
电泳后水洗是否不充分6涂面的异常附着电压灰分溶剂量设备、操作 磷化涂装电压适当否灰分过低*溶剂含量过高否极间距是否过近磷化药品未清洁干净7水滴迹挂具 被涂物在电泳水洗后的晾干过程中从挂具上有无水滴落在电泳水洗后被涂物上的积水排除干净否8不均匀的干痕迹水洗运输链的速度槽液温度 环境电泳后的水洗充分否电泳和水洗之间的时间是否过长槽液温度是否过高涂装环境的湿度太低9再溶解槽液水洗水 运输链槽液的PH值低水洗水的PH值低或冲洗压过高运输链速度变低或停止 10涂面斑印 磷化后的水洗环境 挂具上的污物水洗不充分被涂物在电泳前又被污染否 有无挂具上的污物滴落在被涂物上或槽液中11涂膜粗糙 磷化加热残分纯水前处理 颜料分磷化膜是否均匀,前处理后水洗是否充分槽液的加热残分是否过低纯水的水质是否合格脱脂是否不良颜料分是否偏低*