1000万吨常减压装置标定报告常减压装置标定核算报告.docx
《1000万吨常减压装置标定报告常减压装置标定核算报告.docx》由会员分享,可在线阅读,更多相关《1000万吨常减压装置标定报告常减压装置标定核算报告.docx(36页珍藏版)》请在冰豆网上搜索。
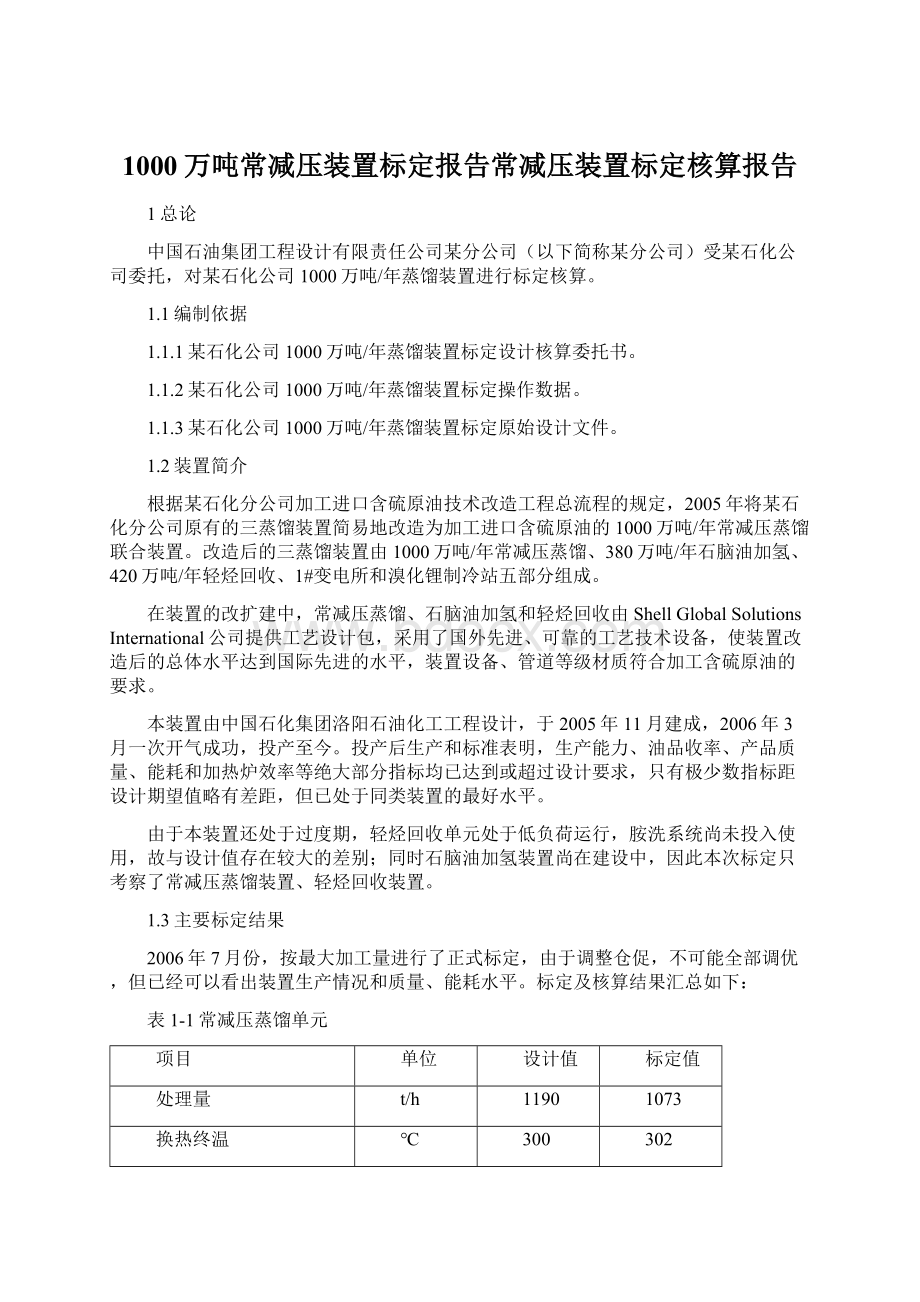
1000万吨常减压装置标定报告常减压装置标定核算报告
1总论
中国石油集团工程设计有限责任公司某分公司(以下简称某分公司)受某石化公司委托,对某石化公司1000万吨/年蒸馏装置进行标定核算。
1.1编制依据
1.1.1某石化公司1000万吨/年蒸馏装置标定设计核算委托书。
1.1.2某石化公司1000万吨/年蒸馏装置标定操作数据。
1.1.3某石化公司1000万吨/年蒸馏装置标定原始设计文件。
1.2装置简介
根据某石化分公司加工进口含硫原油技术改造工程总流程的规定,2005年将某石化分公司原有的三蒸馏装置简易地改造为加工进口含硫原油的1000万吨/年常减压蒸馏联合装置。
改造后的三蒸馏装置由1000万吨/年常减压蒸馏、380万吨/年石脑油加氢、420万吨/年轻烃回收、1#变电所和溴化锂制冷站五部分组成。
在装置的改扩建中,常减压蒸馏、石脑油加氢和轻烃回收由ShellGlobalSolutionsInternational公司提供工艺设计包,采用了国外先进、可靠的工艺技术设备,使装置改造后的总体水平达到国际先进的水平,装置设备、管道等级材质符合加工含硫原油的要求。
本装置由中国石化集团洛阳石油化工工程设计,于2005年11月建成,2006年3月一次开气成功,投产至今。
投产后生产和标准表明,生产能力、油品收率、产品质量、能耗和加热炉效率等绝大部分指标均已达到或超过设计要求,只有极少数指标距设计期望值略有差距,但已处于同类装置的最好水平。
由于本装置还处于过度期,轻烃回收单元处于低负荷运行,胺洗系统尚未投入使用,故与设计值存在较大的差别;同时石脑油加氢装置尚在建设中,因此本次标定只考察了常减压蒸馏装置、轻烃回收装置。
1.3主要标定结果
2006年7月份,按最大加工量进行了正式标定,由于调整仓促,不可能全部调优,但已经可以看出装置生产情况和质量、能耗水平。
标定及核算结果汇总如下:
表1-1常减压蒸馏单元
项目
单位
设计值
标定值
处理量
t/h
1190
1073
换热终温
℃
300
302
加热炉出口温度
常压炉
℃
370
365
减压炉
℃
408
411
加热炉出口效率
常压炉
%
90
93
减压炉
%
90
91
热回收率
%
69
轻油收率
%
53.51
36.88
总拔出率
%
70.4
能耗
Kg标油/t原料
13.84
14.33
2装置采用的主要技术及特点
2.1常减压蒸馏单元
1初馏塔提压操作,采用无压缩机回收液化气。
2抑制原油及初底油在换热器中汽化。
为保证单元的长周期远行,减轻油品在换热器中的结垢,在原油进初馏塔前设置了调节阀以抑制原油出现汽化。
3原油进初馏塔前设置蒸汽加热器
为稳定原油进初馏塔的温度,进行稳定初馏塔的操作,在原油进初馏塔前设置蒸汽加热器,以补偿换热网络的温度变化,并可缩短单元开工时原油升温的时间。
4原油进初馏塔温度较低,塔底吹入一定量的汽提蒸汽。
原油进初馏塔的设计温度为190℃。
为保证塔顶石脑油的质量及收率,塔底吹入17t/h汽提蒸汽。
5常压塔不设置冷回流
常压塔设置常顶循、常一中和常二中三个取热段,塔顶不设置冷回流。
为提高换热效果,中段回流采用小温差、大流量的方式。
6常二线油设置减压真空干燥
常二线油设置减压真空干燥,控制柴油的含水量不大于80ppm(wt),以满足柴油加氢装置对原料中含水量的要求。
7常压塔强化汽提效果
常压塔底采用内缩径,以强化塔底汽提效果。
8换热网络
对常减压和轻烃回收一起进行热整合,优化换热网络。
9换热器设置旁路控制
为稳定换热网络,增加换热网络的弹性,对重沸器、原油加热器、中段回流换热器以及部分原油换热器的热流侧设置控制旁路。
10先进的HSE设置
SGSI对重要的工艺参数均设置链锁保护系统、事故报警及紧急停车链锁系统,大大提高了单元安全运转的可靠性。
2.3主要设备说明
2.3.1塔类
1初馏塔
1)进料温度211℃/206℃,塔顶操作压力为0.33MPa,初馏塔不设进料加热器,塔底不吹气。
2)初馏塔进料段以上直径为3.4M,设20层塔盘;进料段以下直径为5.7M,设5层塔盘,总塔盘25层。
塔盘采用高性能塔盘。
3)初馏塔采用热回流,回流温度为96℃。
4)壳体第五层塔盘以上材质采用16MnR+alloy400,其余为16MnR;顶部5层塔盘材质采用alloy400,其余为0Cr13。
2常压塔
1)常压塔进料温度367℃/356℃;塔顶操作压力为0.06MPa。
常压塔设顶循、一中和二中三个取热中段。
常压塔塔顶不设冷回流。
2)常压塔塔径分3段,常顶循段(1至4层塔盘)直径为6.1M,其余进料段以上塔径均为8M,共45层塔盘。
塔底汽提段设8层塔盘,采用内缩径,直径为4.25M。
3)常压塔设4个部分抽出塔盘,分别是3个中段回流抽出和1个常二线抽出。
设2个全抽出塔盘,分别是常一线和常三线抽出。
4)塔盘采用高性能塔盘。
5)壳体在300℃以上材质采用16MnR+316L,其余为16MnR+405和16MnR+304L。
塔盘材质根据不同温度,分别采用0Cr13、304L和316L。
4减压塔
1)减压塔进料温度为384℃(设计工况)/383℃(灵活工况);塔顶操作压力为16mbar。
减压塔的设计压力为0.15MPa。
2)减压塔设计四个侧线,减一,减二,减三混合作为蜡油,减四线为洗涤油,返回至减压炉入口循环。
3)减压塔塔径分为三段,减一中塔径为7.8M,减二中段塔径为11.8M,其余段塔径为13.8M。
4)减压塔塔内采用SGSI设计结构。
各中段回流取热段采用空塔喷淋取热技术。
减压塔内主要有两段填料,分别为柴油分离段和洗涤段。
5)减压塔上部简体材料为20R,中部简体以及过度段材料为20R+304L,下部简体材料为20R+316L,减压塔填料采用316L材料。
2.3.2加热炉
(1)设计负荷
常压加热炉的设计热负荷,工况一(阿拉伯轻油)为104654KW;工况二(俄罗斯轻油)为103924KW。
减压加热炉的设计热负荷,设计工况(阿拉伯轻油,VG0T95=555℃)为80641KW;灵活工况(阿拉伯轻油,VG0T95=575℃)为74488KW,加热炉设计弹性为操作工况的50%~110%。
(2)加热炉炉型
两台加热炉炉型均为三辐射室十二辐射单元立管式炉,每个辐射单元设置一台低氧化氮燃烧器,共用一个对流室。
油品介质分十二程从对流段上部进炉,经对流加热后进入辐射段,从辐射顶出炉。
2.3.3机泵
由于原油泵、初底泵、常一中泵、常二中泵、减二线及减二中泵、减三泵及减三中泵等扬程较高或流量过大,对以上机泵采用2开1备的运行方式,以节省投资。
对于大流量机泵采用效率较高、NPSH较低的双吸两端支撑式化工流程泵,高电压电机采用隔爆型电机。
2.4设计主要指标
2.4.1加工量及操作弹性
CDU3规模为1000万吨/年,设计弹性为50%~100%。
HVU3规模为630万吨/年,设计弹性为50%~100%。
石脑油加氢单元规模为380万吨/年,设计弹性为50%~100%。
2.4.2装置能耗
常减压单元能耗不大于13.8Kg标油/t原油。
石脑油加氢单元能耗不大于6.71Kg标油/t原油。
2.4.3产品质量
产品
性质
指标
说明
燃料气
总硫,mg/Num3
<22
液化气
≤C2,mole%
5
≥C5,mole%
3
VPat37.8℃,kap
<1380
铜片腐蚀
通过
轻石脑油
RVPat40℃
<12.5psia
重石脑油
ASTMD86,IBP
℃
ASTMD8695%
160℃
沙轻原油
煤油
凝点
闪点
ASTMD8695%
≤-47℃
≥43℃
≤230℃
当作喷气燃料产品时,闪点不大于38℃
柴油(LGO+HGO混合物)
ASTMD8695%
闪点
凝点
≤365℃
≥60℃
冬季<-10
夏季<+5
混合LGO+HGO
混合蜡油
ASTMD116095%
C7沥青质(%wt)
Ni+V(ppmwt)
CCR(%wt)
总氮ppmwt
≤575
≤0.05
≤2.0
≤0.9
<1500
设计工况
混合蜡油
ASTMD116095%
C7沥青质(%wt)
Ni+V(ppmwt)
CCR(%wt)
总氮ppmwt
≤555
≤0.05
≤2.0
≤0.8
<1500
灵活工况
3标定情况及说明
3.1原油及标定方案
(1)加工原油为卡宾达原油,本标定及核算是根据2006年7月14日标定数据整理核算的,日炼油量为25752吨。
(2)标定生产方案
初、常顶石脑油重整原料
常一线3#航空煤油
常二、三线;减一线0#柴油
减二、三线混合蜡油,按减压深拔工况操作
95%点不大于575℃
减压塔底渣油催化裂化原料
3.2检测说明
(1)物料平衡均以装置油表计量为准,参考罐区检尺计量,并根据实际的温度进行密度校正。
(2)对装置所有计量一次指示在标定前进行了回零校正。
(3)初馏塔、常压塔、常压汽提塔的注汽量均以各自孔板计量为准。
(4)各冷却器水分支流采用脉冲流量测量仪测定。
(5)冷去系统中,冷热流无热偶处的温度值是由水银温度计测得。
(6)冷换系统及辅助系统无压力变送指示均采用就地指示弹簧管式压力计测得,并在测量前经过校验。
3.3标定目的
(1)考察装置的运行情况及装置的技术经济指标是否达到设计要求,为装置考核验收提供依据。
(2)考察产品质量情况。
(3)考察减压系统抽真空专利设备水环真空泵和蒸汽喷射泵实际抽真空的能力。
(4)考察减压塔喷头喷淋效果,检验减压空塔喷淋技术,进而考察减压深拔技术的实际运行效果。
(5)考察装置塔内构件的水力学性能,并验证其适用性。
(6)考察加热炉专利火嘴的运行能力。
(7)考察装置物料平衡、热平衡情况。
(8)考察装置换热网络实际运行情况。
(9)考察装置各换热器换热效率。
(10)考察装置加热炉运行情况及效率。
(11)考察电脱盐运行情况。
(12)考察装置能耗水平及技术指标,确定本装置在国内、国际上所处地位。
(13)摸清目前装置存在影响正常生产、处理能力、物耗、能耗、产品收率及产品质量的不利因素,为进一步调整优化操作及今后整改指明方向。
(14)考察各单位单体设备处理能力和效果。
(15)考察装置各计量表的精度、DCS控制系统的准确性和稳定性。
3.4标定时间
2006年7月13日9:
30至2006年7月14日9:
30时共计24小时。
4原油及产品分析数据
4.1原油性质
本次标定的原油为卡宾达原油,其主要性质见下表
表4-1卡宾达原有性质
分析项目
成绩
分析项目
成绩
密度(20℃),kg/m3
872.6
胶质+沥青质,m%
5.74
粘度,m㎡/s
50℃
15.67
蜡含量,m%
13.88
100℃
4.748
馏程,V%
初馏点℃
65
凝点,℃
-1
100℃
30
康氏残碳m%
4.75
120℃
4.5
硫含量,m%
0.22
140℃
6.5
氮含量,m%
0.41
160℃
8.0
水含量,m%
0.04
180℃
10.5
盐含量,mgNaCl/L
25.46
200℃
12.5
金属含量,ppm
Fe
1.32
220℃
15.0
Ni
3.07
240℃
17.0
Cu
0.038
260℃
20.0
Na
0.39
280℃
24.0
Ca
0.12
300℃
27.0
Pb
0.03
全馏出
28.0
V
1.41
API
30.10
酸值,mgKOH/g
0.36
原油类别
低硫中间基
灰分,m%
0.016
4.2产品分析数据
4.2.1蒸顶、常顶、减顶不凝气
表4-3塔顶干气分析化验成绩
干气采样点
初顶气
常顶气
减顶不凝气
硫化氢,mg/m3
2574.6
560.7
2978.5
组成,%(v/v)
氢气
55.21
5.27
二氧化碳
2.12
0.95
0.52
丙烷
29.29
3.04
7.28
丙烯
0.08
1.33
6.78
异丁烷
7.93
1.31
1.21
正丁烷
14.15
1.81
5.51
丁烯-1
2.13
异丁烯
0.01
2.12
反丁烯-2
0.44
异戊烷
2.02
0.74
1.31
顺丁烯-2
0.23
正戊烷
1.59
0.65
2.39
乙烯
4.08
4.64
乙烷
29.84
11.51
14.65
氧气
0.10
0.14
0.38
氮气
6.13
6.66
4.40
甲烷
6.74
12.19
39.68
一氧化碳
0.39
1.05
由于胺洗系统未投用,轻烃干气未经精制,导致干气中硫化氢含量严重超标。
4.2.3初顶、常顶、石脑油分离塔轻重石脑油:
表4-5塔顶石脑油分析化验成绩
采样点
初顶
常顶
C-1211顶
C-1211底
密度(20℃)kg/m3
780.1
727.1
716.3
722.2
馏程
初馏点,℃
29.0
41.9
43
51
10%℃
39.5
76.5
68
78
50%,℃
74.3
141.1
109
116
90%℃
116.0
147.1
151
156
干点,℃
139.4
172.4
176
178
全馏出,ml
95.5
98.2
97
97
残油,ml
1.0
1.0
1.0
1.0
S含量,%(m/m)
0.001
0.02
0.01
0.01
N含量,μg/g
0.5
1.29
0.71
0.71
Cl含量,μg/g
0.7
0.6
0.7
0.6
As含量,μg/kg
9
19
24
21
Pb含量,μg/kg
<10
<10
<10
<10
Cu含量,μg/g
10
12
11
10
Hg含量,μg/kg
3.2
2.4
2.1
2.2
含水量,%(m/m)
0.0150
0.0139
0.032
0.011
族组成,%(m/m)
环烷烃
23.75
33.90
31.08
31.84
异构烷烃
42.17
31.58
34.25
33.29
正构烷烃
42.17
31.58
34.25
33.29
芳烃
2.50
8.09
6.84
7.54
标定期间初、常顶石脑油质量完全符合工艺指标要求的数值,并且标定期间各馏出点温度也比较稳定,这说明常压塔采用常顶循环回流来控制塔顶温度是可行的。
但重石脑油的初馏点比设计值低30℃,与设计值有较大的偏差,这主要是石脑油分离塔塔底重沸器热量不够造成的,在以后生产中需要调整操作参数。
4.2.4常一线:
表4-6常一线航煤产品化验分析成绩
采样点
常一线
密度(20℃)kg/m3
785.6
馏程
初馏点
170
10%,℃
178
20%,℃
182
50%,℃
181
90%,℃
干点,℃
212
234
全馏出,ml
98.5
残油,,ml
1.0
损失,ml
0.5
冰点,℃
-53
实际胶质,mg/100ml
2.0
闪电,℃
54
运动粘度(-20℃),mm2/s
3.700
运动粘度(20℃),mm2/s
1.608
铜离子,μg/g
18
硫醇性酸,%(m/m)
0.00245
S含量,%(m/m)
0.02
赛氏色,号
7
Ag片腐蚀,级
0
铜片腐蚀,级
1a
总酸值mgKOH/g
0.026
芳烃,%(v/v)
10.1
烯烃,%(v/v)
0.7
饱和烃,%(v/v)
89.2
烟点,mm
27.0
净热值,Mj/kg
安定性:
压力降,kpa管壁评级
1.9/不合格
水应反应:
界面情况,级分离程度,级
1b/2级
电导率(20℃)
3
固体颗粒污染物含量,mg/l
2.55
标定期间常一线航煤质量完全符合工艺卡片的指标要求。
同时,常顶KK平均值与常一线HK平均值之差为14℃,满足常压产品煤油与石脑油脱空度大于5℃的分离要求。
4.2.5常二线/常三线/减一线:
表4-7柴油产品化验分析成绩
采样点
常二线
常三线
减一线
密度(20℃)kg/m3
813.4
830.9
842.9
十六烷值
50
62
56.5
实际胶质mg/100ml
4.4
40.0
40.0
闪点,℃
92
62
83
运动粘度,(20℃),mm2/s
3.312
7.160
6.549
冷滤点,℃
-22
4
-2
凝点,℃
-26
3
-3
S含量,%(m/m)
0.04
0.07
0.10
水溶性酸碱
无
无
无
铜片腐蚀,级
1a
1a
1a
灰分,%(m/m)
0.002
0.003
0.002
10%蒸余物残炭,%(m/m)
0.02
0.03
0.03
酸度mgKOH/100ml
5.01
8.59
9.74
水分,%(V/V)
无
无
无
硫醇硫,%(m/m)
0.0256
0.00251
0.00504
色度,号
<0.5
<0.5
<3.0
氧化胺定性,总不容物,mg/100ml
0.6
0.9
1.8
馏程
初馏点,℃
216.0
148
218
10%,℃
228.2
263
265
50%,℃
233.7
321
312
90%,℃
257.1
354
347
95%,℃
298.6
361
357
干点,℃
310.4
369
369
标定期间常二线产品质量完全符合0#柴油的质量要求,且产品质量稳定;尽管常三线初馏点较低,但与常二线、减一线混合后完全满足0#柴油的质量要求。
常三线初馏点低的主要原因是常三线抽出层塔盘为全抽出塔盘,且汽提塔无汽提蒸汽。
标定期间减一线产品质量完全符合柴油指标要求,可见,该减压塔在只有两段填料的前提下,减一线产柴油是完全可行的。
常二线HK平均值与常一线KK平均值之差为1℃,不满足常压产品煤油与石脑油脱空度>5℃的分离要求,在生产中需优化操作条件以满足产品质量的要求。
4.2.6混合蜡油
表4-8混合蜡油产品化验分析成绩
采样点
混合蜡油
混合蜡油
密度,kg/m3
(20℃)
882.1
2%,℃
342
(70℃)
848.2
5%,℃
354
粘度(100℃),mm2/s
6.103
10%,℃
368
残碳%(m/m)
0.19
20%,℃
391
S含量,%(m/m)
0.13
30%,℃
404
总氮,%(m/m)
0.12
40%,℃
420
含盐量,mgNaCl/L
1.50
50%,℃
436
碳/氢比
60%,℃
452
Ni+V
70%,℃
468
族组成:
%(m/m)
饱和烃
80%,℃
486
芳香烃
90%,℃
509
胶质
95%,℃
523
C7沥青质
97%,℃
531
全馏出,ml
98
从上表馏程分析可以看出,减压蜡油还未达到设计深拔的要求,但已经达到灵活性工况(95%不大于555℃)要求。
标定期间减压蜡油的氮含量满足设计要求,低于1500ppm;残碳平均为0.19%,远低于设计值0.9%。
1)塔顶真空度还未达到设计值12~16mbar,即99kpa以上,主要是因为水环真空泵未投用。
2)由于减压系统部分流量部分孔板不指示值,造成减压系统操作未达到设计值。
3)加压系统符合略低,部分操作条件与设计值相差较大。
4.2.7常压渣油:
表4-9常压渣油产品化验分析成绩
采样点
常压渣油
常压渣油
密度,kg/m3
(20℃)
908.9
2%,℃
322
(70℃)
875.0
5%,℃
345
粘度(100℃),mm2/s
20.90
10%,℃
370
残碳%(m/m)
5.59
20%,℃
400
S含量,%(m/m)
0.16
30%,℃
426
总氮,%(m/m)
0.28
40%,℃
454
含盐量,mgNaCl/L
10.34
50%,℃
484
碳/氢比
60%,℃
524
Ni+V
70%,℃
族组成:
%(m/m)
饱和烃
68.95
80%,℃
芳香烃
18.31
90%,℃
胶质
12.00
95%,℃
C7沥青质
0.74
97%,℃
常压渣油中小于350℃馏分含量大于5%,尚未达到设计指标,其主要原因常压塔进料温度低于设计值5℃左右,小于350℃馏分蒸发不完全所致。
4.2.8减压渣油:
表4-10减压渣油产品化验分析成绩
采样点
减压渣油
减压渣油
密度,kg/m3
(20℃)
963.9
2%,℃
(70℃)
931.3
5%,℃
粘度(100℃),mm2/s
457.5
10%,℃
残碳%(m/m)
14.24
20%,℃
S含量,%(m/m)
0.20
30%,℃
总氮,%(m/m)
0.56
40%,℃
含盐量,mgNaCl/L
10.31
50%,℃
碳/氢比
60%,℃
Ni+V
29.96
70%,℃
族组成:
%(m/m)
饱和烃
80%,℃
芳香烃
90%,℃
胶质
95%,℃
C7沥青质
97%,℃
全馏出,ml
由于分析仪器的原因,减压渣油的蒸馏数据暂时无法提供,故对于减压深拔的效果暂时无法评价。
4.2.9脱盐前后油品性质
表4-11电脱盐成绩
一级脱盐原油
二级脱盐原油
水含量,%(V/V)
0.45
0.50
盐含量,mgNaCl/L
14.82
8.06
原油的含盐量为25.46mgNaCl/L,一级脱后盐含量为14.82mgNaCl/L脱盐率为41.8%;二级后脱盐含量为8.06mgNaCl/L,脱盐率为68.3%,水含量为0.5%,此数值与设计有较大的差距,由于电脱盐系统尚处于调整期,其操作条件还需要继续摸索。
项目
单位
设计值
实际操作值
一、初馏塔