包头原料条件下1800立方米高炉本体及渣铁处理系统设计毕业论文设计说明书.docx
《包头原料条件下1800立方米高炉本体及渣铁处理系统设计毕业论文设计说明书.docx》由会员分享,可在线阅读,更多相关《包头原料条件下1800立方米高炉本体及渣铁处理系统设计毕业论文设计说明书.docx(38页珍藏版)》请在冰豆网上搜索。
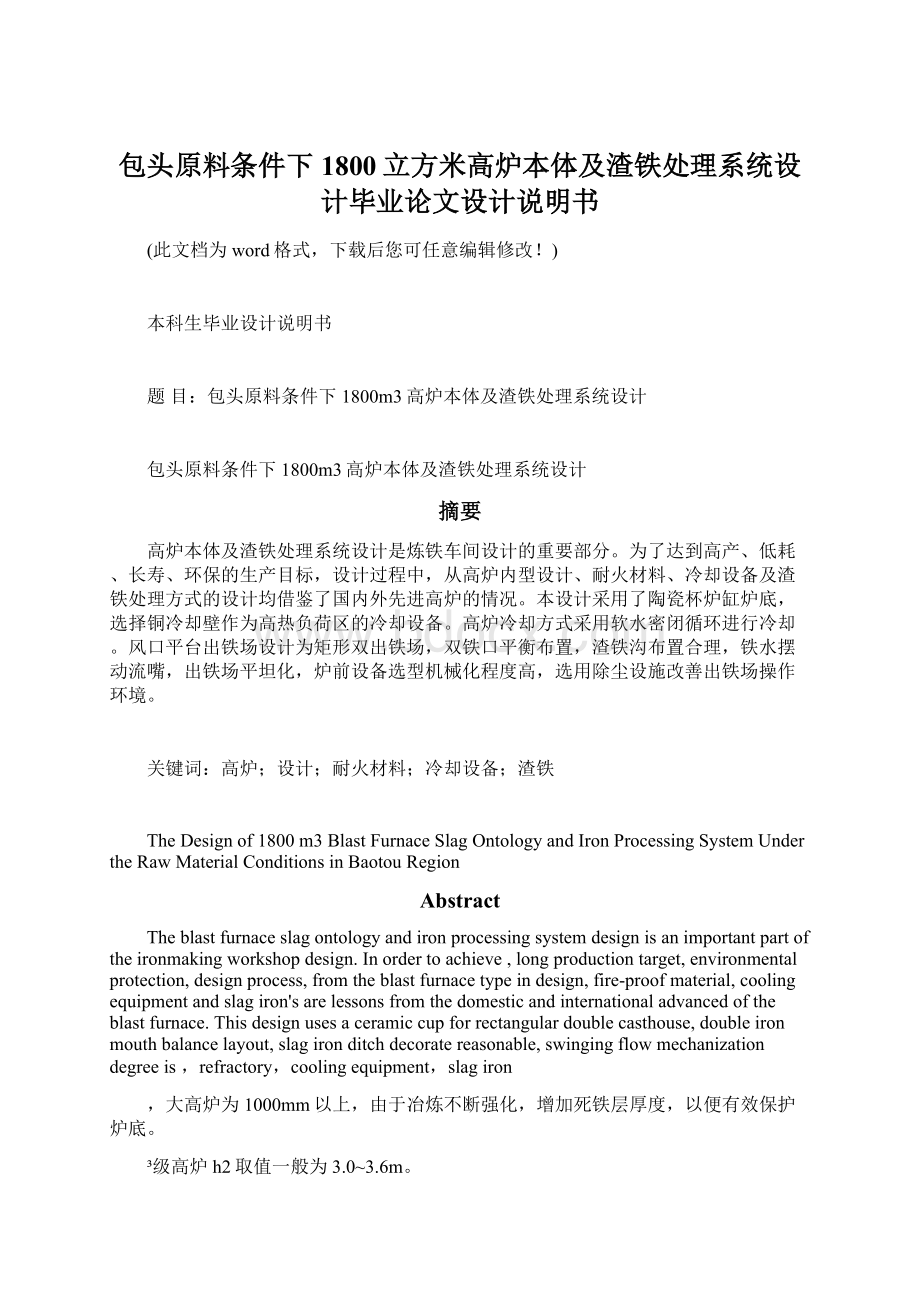
包头原料条件下1800立方米高炉本体及渣铁处理系统设计毕业论文设计说明书
(此文档为word格式,下载后您可任意编辑修改!
)
本科生毕业设计说明书
题目:
包头原料条件下1800m3高炉本体及渣铁处理系统设计
包头原料条件下1800m3高炉本体及渣铁处理系统设计
摘要
高炉本体及渣铁处理系统设计是炼铁车间设计的重要部分。
为了达到高产、低耗、长寿、环保的生产目标,设计过程中,从高炉内型设计、耐火材料、冷却设备及渣铁处理方式的设计均借鉴了国内外先进高炉的情况。
本设计采用了陶瓷杯炉缸炉底,选择铜冷却壁作为高热负荷区的冷却设备。
高炉冷却方式采用软水密闭循环进行冷却。
风口平台出铁场设计为矩形双出铁场,双铁口平衡布置,渣铁沟布置合理,铁水摆动流嘴,出铁场平坦化,炉前设备选型机械化程度高,选用除尘设施改善出铁场操作环境。
关键词:
高炉;设计;耐火材料;冷却设备;渣铁
TheDesignof1800m3BlastFurnaceSlagOntologyandIronProcessingSystemUndertheRawMaterialConditionsinBaotouRegion
Abstract
Theblastfurnaceslagontologyandironprocessingsystemdesignisanimportantpartoftheironmakingworkshopdesign.Inordertoachieve,longproductiontarget,environmentalprotection,designprocess,fromtheblastfurnacetypeindesign,fire-proofmaterial,coolingequipmentandslagiron'sarelessonsfromthedomesticandinternationaladvancedoftheblastfurnace.Thisdesignusesaceramiccupforrectangulardoublecasthouse,doubleironmouthbalancelayout,slagironditchdecoratereasonable,swingingflowmechanizationdegreeis,refractory,coolingequipment,slagiron
,大高炉为1000mm以上,由于冶炼不断强化,增加死铁层厚度,以便有效保护炉底。
³级高炉h2取值一般为3.0~3.6m。
,炉容大向上取值,设计中可调整h3确定炉容。
。
1.2.4α、β角
高炉炉腹角(α)和炉身角(β)一般取值为79°~83°;炉身角有减小的趋势,α和β角对内型合理与否有着重要的影响。
因为炉气在炉内传质传热取决于两个方面:
一是煤气在炉内停留的时间。
它取决于高炉下部容积与高炉有效容积之比;二是取决于煤气在炉内分布。
除操作因素外,对炉型来说就是α和β了。
适宜的减小α和β,利于煤气流上升与分布,且有利于保护炉衬。
而α、β大了不仅影响煤气流分布,中心气不开放,还影响高炉寿命。
炉型设计合理是获得良好技术经济指标,保证高炉操作顺行的基础[3]。
而高炉设计尤为关键,没有科学的设计其他都无从谈起,科学的设计是高炉长寿的基础[4]。
1.3高炉用耐火材料
在侵蚀性因素联合作用下引起高炉炉衬损毁,这些因素包括:
炉渣、碱类物质、铁水、气体介质、炉料磨损、热应力等。
高炉每个部位的使用条件不同,要求区别对待炉衬每个区段用相应耐火材料的选择。
高炉用耐火材料有陶瓷质材料和碳质材料两大类。
陶瓷质材料有粘土砖、高铝砖、刚玉砖和不定形耐火材料等;碳质材料有炭砖、石墨炭砖、石墨碳化硅砖、氮结合碳化硅砖、粘土结合碳化硅砖等[5]。
(1)粘土砖和高铝砖。
粘土砖和高铝砖亦称陶瓷质或粘土质耐火材料,在高炉上使用已有较长久的历史,现在也广泛应用于高炉各个部位。
粘土砖、高铝砖具有良好的机械强度,耐磨性和抗渣性均较好,成本较低。
(2)在高炉上使用的碳质耐火材料是在粘土质耐火材料之后。
近代高炉逐渐大型化,冶炼强度也有所提高,炉衬热负荷加重,碳质耐火材料具有独特的性能,逐渐应用到高炉上来,尤其是炉缸炉底部位几乎普遍采用碳质材料,其他部位炉衬的使用量也日趋增加。
(3)不定形耐火材料。
不定形耐火材料主要有捣打料、喷涂料、浇注料、泥浆和填料等。
按成分可分碳质不定形耐火材料和粘土质耐火材料。
捣打料、喷涂料、浇注料可根据需要和部位的不同,形成各种形状。
泥浆是砌砖不可缺少的填缝粘结剂。
填料一般是两层砌体之间的隔热物质或是粘结物质[6]~[10]。
不定形耐火材料与成型耐火材料相比,具有成型工艺简单、能耗低、整体性好、抗热震性强、耐剥落等优点;还可以减小炉衬厚度、改善热导率等,近年来使用较多[7]。
高炉炉底、炉缸是高炉的重要部位,炉龄的长短,主要取决于这两部位的使用寿命[11]。
因此,近代高炉在此部位均采用炭砖加陶瓷杯的混合结构。
炉底下部全部使用炭砖,上部靠周边冷却壁砌筑环形炭砖,炉缸部位也采用炭砖砌筑,在炉底中央和炭砖内侧砌筑陶瓷质材料的陶瓷标。
采用这种结构形式,其目的是利用炭砖热传导性能好的特点,加强炉底冷却散热,将铁水凝固等温线(1500℃)向上部推移,并把800℃左右的化学反应等温线推至保护层内,从而减缓炉底侵蚀速度,防止环形断层的发生,延长炉底使用寿命,另外,炭砖的最大弱点是抗氧化能力差。
尽管高炉冶炼性属于还原性气氛,但是暴露无遗在与炉气接触的炭砖,仍然非常容易氧化。
因此,采用在炭砖内侧镶砌一层高温理化性能特好的中性陶瓷材料以保护炭砖在烘炉期间和炉役前期不被氧化的陶瓷杯技术,如图1.4。
能够有效地阻止液体炉渣和铁水过早地向炭砖渗透接触,间接地延长高炉的使用寿命。
图1.4陶瓷杯结构及理论等温线分布图
1.4高炉冷却设备
高炉冷却设备是高炉炉体结构的重要组成部分,对炉体寿命起到如下作用:
(1)保护炉壳。
在正常生产时,高炉炉壳只能在低于80℃的温度下长期工作,炉内传出的高温热量由冷却设备带走85%以上,只有约15%的热量通过炉壳散失。
(2)对耐火材料的冷却和支承。
在高炉耐火材料表面的工作温度高达1500℃左右,如果没有冷却设备,在很短的时间内耐火材料就会侵蚀或磨损。
通过冷却设备的冷却可提高耐火材料的抗侵蚀和抗磨损能力。
冷却设备还可以对高炉内衬起支承作用增加砌体的稳定性。
(3)维持合理的操作炉型。
使耐火材料的侵蚀内型接近操作炉型,对高炉内煤气流的合理分布、炉料的顺行起到良好的作用。
(4)当耐火材料大部分或全部被侵蚀后,能靠冷却设备上的渣皮继续维持高炉生产[12]。
由于高炉各个部位热负荷不同,加上结构上的要求,高炉冷却设备有:
外部喷水冷却,风口和渣口冷却,冷却壁,冷却水箱,以及风冷或者水冷炉底等。
(1)喷水冷却装置。
在炉身和炉腹部位设有环形冷却水管,水管直径;φ50~φ150mm,约距炉壳100mm,水管上朝炉壳斜上方钻有φ5~φ8小孔若干,小空间距100mm。
冷却水经由小孔喷射到炉壳上进行冷却。
为了防止水的喷溅,在炉壳上装有防溅板,防溅板与炉壳之间有8~10mm的缝隙,冷却水沿炉壳下流至集水槽返回水池。
喷水冷却装置结构简单,检查方便,造价低廉。
适用于碳质炉衬和小型高炉,对于大型高炉是一种辅助性的冷却手段。
(2)风口和渣口。
宝钢1号高炉风口装置见图1.5,由A-1管、A-2管、伸缩管、异径接头、弯管、直吹管等组成。
伸缩管可吸收热膨胀位移,结构密封性好。
A-2管内衬由耐火材料浇注成文氏管结构,用来测定送风量。
图1.5风口结构
1-风口;2-风口二套;3-风口大套;4-直吹管;5-弯管;6-鹅颈管;7-热风管;8-拉杆;9-吊环;10-销子;11-套环
渣口装置一般由四个套组成,即大套,二套,三套和渣口小套,见图1.6。
渣口小套由紫铜制造,一般为空腔式结构,直径45~60mm;三套由青铜铸成空腔式结构;大套、二套由铸铁铸成,内部铸有蛇形钢管。
图1.6渣口结构
(3)冷却壁。
见图1.7。
冷却壁设置于炉壳炉衬之间,有光面冷却壁和镶砖冷却壁,其基本结构是铸铁板内铸有无缝钢管。
光面冷却壁用于炉底炉缸,风口区冷却壁的块数为风口数目的两倍;渣口周围上下段各两块,由四块冷却壁组成。
镶砖冷却壁用于炉腹、炉腰和炉身下部,镶砖的目的在于易结渣皮,代替炉衬工作。
冷却壁用方头螺栓固定在炉壳上,每块4个螺栓。
同段冷却壁间竖直缝20mm,上下段间水平缝30mm,两段竖直缝相互错开。
冷却壁的优点是不损坏炉壳强度,密封性好,冷却均匀,炉衬表面光滑平整。
图1.7高炉冷却壁
铜冷却壁的特点有[13,14]:
1)铜冷却壁具有导热率高,热损失低的特点。
目前国内外铜冷却壁大多以轧制纯铜为材质,经钻孔加工而成。
这样制作出来的铜冷却壁的冷却通道与壁体是一个有机整体,消除了铸铁冷却壁因水管与壁体之间存在气隙而形成隔热屏障的弊端,再加上铜本身具有高导热性,这样就使得铜冷却壁在实际的使用过程中能保持非常低的工作温度。
2)利于渣皮的形成与重建。
较低的冷却壁热面温度是冷却壁表面渣皮形成和脱落后快速重建的必要条件。
由于铜冷却壁具有良好的导热性,因而能形成一个相对较冷的表面,从而为渣皮的形成和重建创造有利条件。
由于渣皮的导热性极低,渣皮形成后,就形成了炉内向铜冷却壁传热的一道隔热屏障,从而减少了炉内热损失。
研究表明,在渣皮脱落后,铜冷却壁能在15min内完成渣皮的重建,而双排水管球墨铸铁冷却壁至少需要4h。
为了提高冷却壁寿命,日本新日铁公司对冷却壁结构做了多次改进,效果显著,其四代结构情况如图1.8。
第二代较第一代平均寿命提高了3.2年,一代产量提高了1445tm3;而第三代使用寿命可稳定的保持10年;第四代冷却壁砌体厚度减薄至200mm,因而冶炼中有利于维持炉型,稳定了炉容。
第三代冷却壁炉龄后半期容积为开炉时的1.13倍,而四代冷却壁减少到1.05倍。
图1.8四代冷却壁
(4)冷却水箱。
冷却水箱是埋于炉衬内的冷却设备,用于厚壁炉衬,有扁水箱和支梁式水箱两种。
(5)风冷、水冷炉底。
大型高炉炉缸直径较大,径向周围冷却壁的冷却,已不足以将炉底中心部分的热量散发出去,如不进行冷却则炉底向下侵蚀严重。
因此大型高炉炉底中心部分要冷却,冷却的方法是风冷和水冷。
1.5高炉基础
高炉基础是高炉下部的沉重结构,它的作用是将高炉全部载荷均匀的传递到地基。
高炉基础由埋在地下的基座和地面上的基墩组成。
基墩断面为圆形,高度一般为2.5~3m。
基座直径与荷载和地基土质有关[15]。
1.6渣铁处理系统
1.6.1风口平台及出铁场设计
(1)风口平台及出铁场
风口平台是炉前操作人员活动的平台,通过风口观察炉况,更换风口,放渣,维护铁口及渣铁沟和冷却设备,操纵一些阀门等。
风口平台一般比风口中心线低1150~1250mm,应该平坦且留有排水坡度,其操作面积随炉容大小而异[16]。
在铁口侧布置着铁沟和下渣沟的炉前平台叫出铁场。
见图1.9。
铁口是炉缸中最薄弱的部分,出渣出铁是高炉的基本操作。
出铁场和操作平台上设置有以下设备:
渣铁处理系统、主沟铁沟等修理更换设备、能源管道(水、煤气、氧气、压缩空气)、风口装置和更换风口的设备、炉体冷却系统和燃料吹喷系统的设备、起重设备、材料和备品备件堆置场、集尘设备、人体降温设备、照明设备以及炉前休息室、操作室、值班室等。
在出铁场上把这些布置合理,使用方便,减轻体力劳动,改善环境,保证出铁出渣操作的顺利进行是设计时必须考虑的事项。
矩形出铁场有如下的优点[17]:
①矩形出铁场在铁口上方可设置较大面积的除尘罩,铁口除尘效果好。
环形出铁场受到吊车内环梁的限制,铁口上方无法放置较大的除尘罩;
②与环形出铁场相比,矩形出铁场厂房结构钢结构量较小,投资较低;
③矩形出铁场炉体平台检修维护环境较好。
而环形出铁场由于环形吊车内环梁及环形厂房的影响,炉体各层平台面积受到限制,对炉体平台的布置造成一定的困难,环形气楼附近的几层炉体平台。
经常有从出铁场收集的烟尘聚集,平台内积灰较多,炉体平台的检修维护环境差。
图1.9矩形出铁场
(2)出铁场除尘
为了改善炉前高温、多尘的劳动环境,减少烟尘和热辐射对人体的危害,在渣铁沟上方设计有沟盖,在渣、铁罐的上方设计有抽尘罩,除尘管道全部采用侧吸式并埋入沙层中。
由于铁口区烟尘量占出铁场烟尘总量的30%,所以铁口区域设计采用了顶吸式,通过抽风机把烟尘抽走。
未抽尽的烟尘通过出铁场上的排烟气楼自然排出。
1.6.2炉前主要设备
炉前设备主要有开铁口机、堵铁口泥炮、堵渣机、换风口机、炉前吊车等[17]。
1.6.3铁水处理设备
铁水运输是冶金企业关键工艺之一,随着钢铁生产工艺的不断发展,钢铁企业的不断壮大,铁水运输方式也正在不断发展。
铁水罐车是钢铁企业铁水运输的重要工具,目前铁水罐车主要有两种:
一种是敞口式铁水车,一种是鱼雷形混铁车(鱼雷罐车)。
中小型高炉一般采用敞口式铁水车,大型高炉多采用鱼雷罐车。
采用不同的铁水运输车辆,对于钢铁生产节奏和钢铁质量会产生不同的影响。
1.6.4炉渣处理
高炉渣处理方法有炉渣水淬、放干渣及冲渣棉。
目前,国内高炉普遍采用水冲渣处理方法。
(1)图拉法水淬渣(TYNA)
图拉水淬渣工艺的原理是用高速旋转的机械粒化轮配合低转速脱水转鼓处理熔渣,工艺设备简单,耗水量少,渣水比为1:
1,运行费用低,可处理含铁量小于40%的熔渣,不需要设干渣坑,占地面积小,渣中带铁不爆炸等优点。
但也有缺点:
工程投资高,粒化器拆卸、维修难度大、时间长,大直径轮式脱水器运行不稳定,维护费用高,成品渣质量不好,无法处理泡沫渣。
我国唐钢2560m3高炉、济钢1750m3高炉炉渣处理系统采用了该工艺[18]~[19]。
(2)INBA法(英巴法)
INBA法是由卢森堡PW公司开发的一种炉渣处理工艺。
从渣沟流出的熔渣经冲渣箱进行粒化,粒渣和水经水渣沟流入渣槽,蒸汽由烟囱排出,水渣自然流入设在过滤滚筒下面的分配器内。
分配器沿整个滚筒长度方向布置,能均匀的把水渣分配到过滤滚筒内。
水渣随滚筒旋转由搅动叶片带到上方时,脱水后的粒渣滑落在伸进滚筒上部的排料胶带机上,然后由输送胶带机运至粒渣槽或堆场。
滤出的水,经集水斗、热水池、热水泵站送至冷却塔冷却后进入冷却水池,冷却后的冲渣水经粒化泵站送往水渣冲制箱循环使用。
缺点是运行不稳定,故障率高[20]~[21]。
(3)底滤法水淬渣(OCP)
底滤法水淬渣是在高炉熔渣沟端部的冲渣点处,用具有一定压力和流量的水将熔渣冲击而水淬。
水淬后的炉渣通过冲渣沟随水流入过滤池,沉淀、过滤后的水淬渣,用电动抓斗机从过滤池中取出,作为成品水渣外运。
OCP法是较成熟的炉渣处理工艺,过滤水中固体悬浮物少,对设备和管道的磨损少,我国大中型高炉采用较多;但该工艺也存在投资大、占地面积大、用水用电量高等不足。
1.7高炉本体和出铁场的设计方案
根据上述文献资料的分析总结,按照高炉设计先进、合理、可行、经济的原则,本设计拟采用如下方案:
采用陶瓷杯炉缸炉底;出铁场设计为双矩形出铁场,用图拉法水冲渣处理炉渣。
第一章
炼铁工艺计算
2.1高炉物料平衡计算
2.1.1原料条件及平衡计算[22]
1.原料条件
包头地区原料成分见表2.1~2.3
表2.1矿石成分表(%)
成分
TFe
Mn
P
S
F
FeO
CaO
烧结矿
56.05
0.78
0.06
0.06
0.27
7.7
10.59
球团矿
63.57
0.04
0.02
0.01
0.06
1.83
0.94
生矿
65.35
0.17
0.05
0.02
0.03
1.86
0.10
硅矿
1.08
0.00
0.00
0.00
0.00
0.00
0.17
石灰石
0.00
0.00
0.01
0.03
0.00
0.00
56.00
续表
成分
SiO2
MgO
Al2O3
RxOy
K2O
Na2O
CO2
烧结矿
5.15
2.01
0.49
0.98
0.13
0.22
0.00
球团矿
5.56
0.73
0.39
0.17
0.11
0.13
0.00
生矿
2.72
0.13
0.81
0.00
0.013
0.00
0.00
硅矿
96.00
0.08
2.21
0.00
0.00
0.00
0.00
石灰石
0.39
0.09
0.17
0.00
0.00
0.00
43.28
表2.2焦炭成分表(%)
固定碳
(%)
灰分
(13.570%)
83.880
SiO2
Al2O3
CaO
MgO
FeO
FeS
P2O5
6.380
5.400
0.800
0.100
0.830
0.050
0.010
续表
挥发分(1.030%)
有机物(1.520%)
合计
全硫
游离水
CO2
CO
CH4
N2
H2
H
N
S
100.00
0.800
3.700
0.150
0.490
0.150
0.086
0.150
0.500
0.249
0.771
(S全=S有机+FeS×3288=0.771+0.050×32÷88=0.800)
表2.3煤粉成分表(%)
C
H
O
N
S
H2O
78.990
2.390
4.030
0.740
0.580
0.900
续表
灰分(12.370%)
SiO2
Al2O3
CaO
MgO
FeO
合计
5.586
5.290
0.560
0.218
0.716
100.00
(1)原料成分:
采用烧结矿、球团矿、生矿冶炼。
矿比为90:
5:
5。
矿石成分经补齐平衡计算后见表2.4
(2)冶炼制钢生铁,规定生铁成分[Si]=0.5%,[S]=0.03%
(3)炼铁焦比K=410Kgt,煤比M=130Kgt
(4)规定炉渣碱度R=CaOSiO2=1.03
(5)元素在生铁、炉渣与煤气中的分配率见表2.5
(6)选取铁的直接还原度rd=0.45,氢的利用率ηH2=35%
(7)空气湿度为4.298gm3
(8)鼓风湿度为ψ=0.00124×4.298=0.0053,即0.53%
(9)热风湿度为1200℃
表2.4原料成分表(%)
项目
TFe
Mn
P
S
FeO
Fe2O3
CaO
烧结矿
56.050
0.780
0.060
0.060
7.700
71.366
10.574
球团矿
63.570
0.040
0.020
0.010
1.830
88.756
1.340
生矿
65.349
0.170
0.050
0.020
1.860
91.264
0.100
硅矿
1.080
0
0
0
0
1.543
0.170
石灰石
0
0
0.010
0.030
0
0
56.000
混合矿
56.891
0.713
0.058
0.056
7.15
73.230
9.589
续表
项目
MgO
SiO2
Al2O3
MnO
MnO2
P2O5
FeS
烧结矿
1.977
4.900
0.290
1.007
0
0.137
0.165
球团矿
0.888
5.860
0.640
0.052
0
0.046
0.028
生矿
0.130
2.720
0.810
0
0.269
0.115
0
硅矿
0.080
96.000
2.207
0
0
0
0
石灰石
0.090
0.390
0.123
0
0
0.023
0
混合矿
1.830
4.839
0.334
0.909
0.013
0.131
0.150
续表
项目
RxOy
CO2
CaF2
K2O
Na2O
∑n
烧结矿
0.980
0
0.554
0.130
0.220
100
球团矿
0.170
0
0.123
0.110
0.130
100
生矿
0
0
0.062
0.013
0
100
硅矿
0
0
0
0
0
100
石灰石
0
43.280
0
0
0
100
混合矿
0.891
0
0.508
0.123
0.205
100
对于生矿,补齐平衡计算后∑n=100烧损2.619(其中含有结晶水)
对于混合矿,补齐平衡后∑n=100烧损0.131%
表2.5元素在生铁炉渣煤气中的分配率
项目
Fe
K
Mn
Na
P
S
生铁
0.997
0.3
0.5
0.3
1.0
炉渣
0.003
0.7
0.5
0.7
0
煤气
0
0
0
0
0
0.005
2.配料计算
(1)铁矿石用量计算
燃料带入铁量Fef
Fef=焦炭带入+煤粉带入
=410×(0.0083×5672+0.0005×5688)+130×0.00716×5672
=3.50Kg
计算矿石用量A
A=[1000×﹙95.7-0.73×[Si]-[S]﹚-100Fef×η﹙1﹚][η﹙1﹚TFe+0.68P矿+1.03Mn矿η﹙2﹚]
=[1000×﹙95.7-0.73×0.5-0.03﹚-99.7×3.50][0.997×56.891+0.68×0.058+0.5×1.03×0.713]
=1662.19Kg
﹙2﹚生铁成分计算
[Fe]=﹙A×TFe100+Fef﹚×0.99710
=﹙1662.19×0.56891+3.50﹚×0.99710
=94.62
[P]=﹙A×P矿100+焦炭中P带入量﹚10
=﹙1662.19×0.058100+410×0.0001×62142﹚10
=0.10
[Mn]=A×Mn矿100×η﹙2﹚10
=1662.19×0.00713×0.510
=0.59
[C]=100-[Fe]-[Si]-[Mn]-[P]-[S]
=100-94.62-0.5-0.59-0.10-0.03
=4.16
生铁成分表如表2.6
表2.6生铁成分表(%)
项目
Fe
Si
Mn
P
S
C
∑
比例
94.62
0.50
0.59
0.10
0.03
4.16
100.00
(3)熔剂用量计算
矿石燃料带入的CaO量=1662.19×0.09589+4l0x0.008+130×0.0056
=163.40Kg
矿石燃料带入的Si02=1662.19×0.048