作业指导书高速公路减水剂.docx
《作业指导书高速公路减水剂.docx》由会员分享,可在线阅读,更多相关《作业指导书高速公路减水剂.docx(16页珍藏版)》请在冰豆网上搜索。
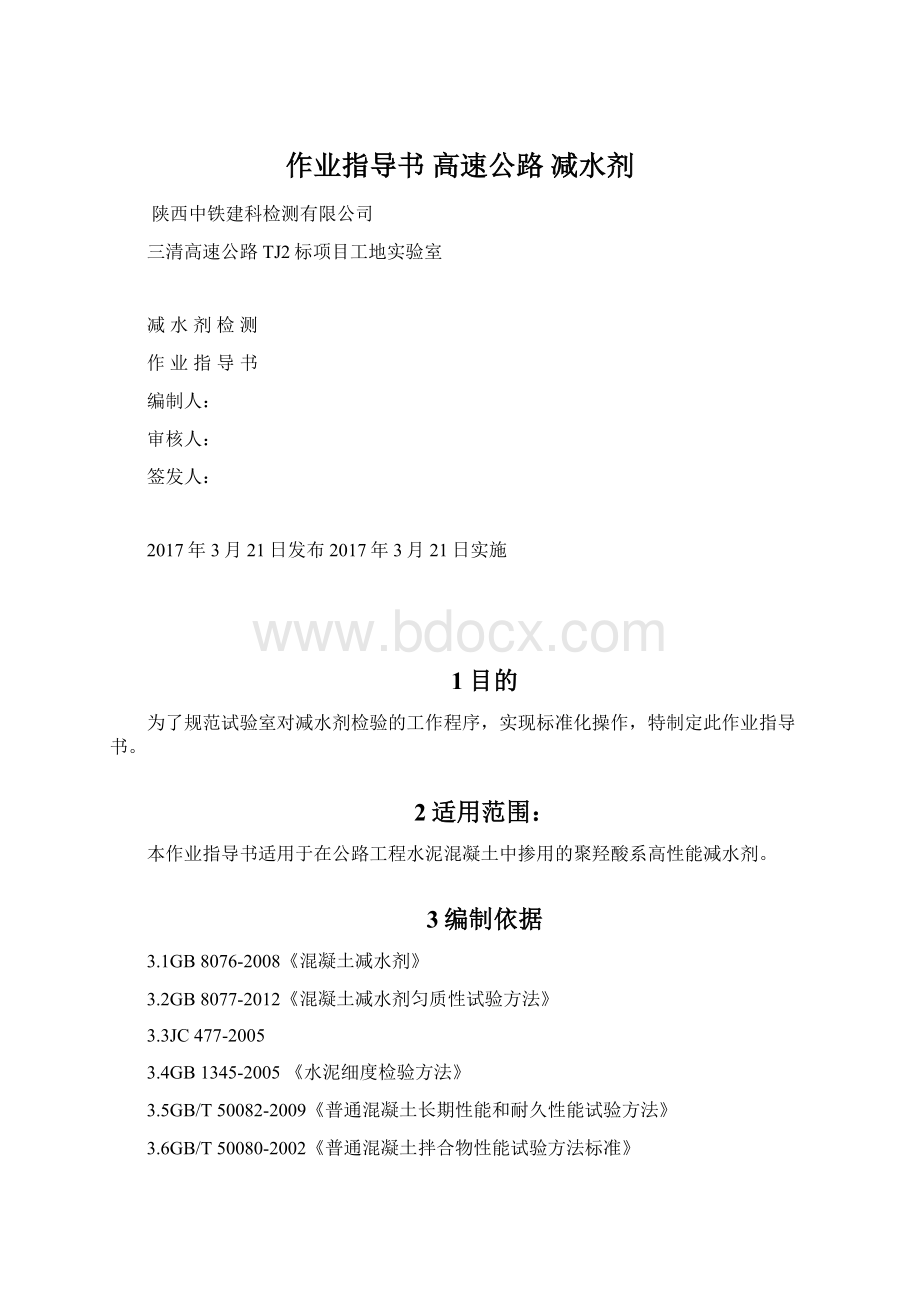
作业指导书高速公路减水剂
陕西中铁建科检测有限公司
三清高速公路TJ2标项目工地实验室
减水剂检测
作业指导书
编制人:
审核人:
签发人:
2017年3月21日发布2017年3月21日实施
1目的
为了规范试验室对减水剂检验的工作程序,实现标准化操作,特制定此作业指导书。
2适用范围:
本作业指导书适用于在公路工程水泥混凝土中掺用的聚羟酸系高性能减水剂。
3编制依据
3.1GB8076-2008《混凝土减水剂》
3.2GB8077-2012《混凝土减水剂匀质性试验方法》
3.3JC477-2005
3.4GB1345-2005《水泥细度检验方法》
3.5GB/T50082-2009《普通混凝土长期性能和耐久性能试验方法》
3.6GB/T50080-2002《普通混凝土拌合物性能试验方法标准》
3.7GB/T2419-2005《水泥胶砂流动度测定方法》
4检测项目概述
5检测准备
5.1人员配备:
5.2一般工作条件下,要求应配备试验人员3人,有专人负责,均必须持证上岗。
5.3负责人员必须持有中级证以上的资格证书。
5.4仪器、设备:
强制式搅拌机、2000kN压力试验机
坍落度筒、台秤100kg、感量50g
电子天平:
500g、感量0.01g;1000g、感量1g
混凝土贯入阻力仪、混凝土含气量测定仪
容量筒:
内径18.5cm、高20cm,容积为5L。
带塞量筒、水泥净浆搅拌机、玻璃板:
直径350~400mm
载锥圆模:
上口直径36mm,下口直径64mm,高度60mm。
负压筛析仪
6检测条件
7检测顺序和方法
7.1材料
7.2水泥:
应采用GB8076-2008附录A规定的基准水泥。
7.2.1砂:
采用GB/T14684-2011《建筑用砂》中Ⅱ区规定的中砂,细度模数为2.6~2.9,含泥量小于1.0%。
7.2.2石子:
采用质量符合GB/T14685-2011《建筑用卵石、碎石》中规定的公称粒径为5mm~20mm的碎石或卵石,采用二级配,其中5mm~10mm占40%,10mm~20mm占60%,满足连续级配要求,针片状物质含量小于10%,空隙率小于47%,含泥量小于0.5%。
如有争议,以碎石结果为准。
7.2.3水:
应符合JGJ63规定的混凝土拌合用水要求。
7.2.4减水剂:
需要检测的聚羟酸系高性能减水剂。
7.3配合比:
配合比基准配合比按普通混凝土JGJ55-2011进行设计。
配合比设计应符合以下规定:
7.3.1水泥用量:
混凝土单位水泥用量360kg/m3
7.3.2砂率:
基准砼、掺减水剂的砼的砂率均为40%~47%。
7.3.3用水量:
基准砼、掺减水剂的砼坍落度控制为(210±10)cm,用水量为坍落度(210±10)cm时最小用水量,用水量包括液体外加剂、砂、石材料中所含水量。
7.3.4外加剂掺量:
按生产厂家推荐掺量。
7.4减水率测定:
减水率为坍落度基本相同时基准混凝土和掺减水剂混凝土单位用水量之差与基准混凝土单位用水量之比。
坍落度按(GBJ180)测定。
减水率按式(1)计算:
——
(1)
式中:
WR───减水率,%;
W0───基准混凝土单位用水量,kg/m3;
W1───掺减水剂混凝土单位用水量,kg/m3。
WR以三批试验的算术平均值计,精确到小数点后一位。
若三批试验的最大值或最小值中有一个与中间值之差超过中间值的15%时,则把最大值与最小值一并舍去,取中间值作为该组试验的减水率。
若有两个值与中间值之差均超过15%时,则该试验结果无效,应该重做。
7.5凝结时间差测定:
凝结时间差按式下式计算:
式中:
ΔT──凝结时间之差,min;
Tt──掺减水剂混凝土的初凝或终凝时间,min;
Tc──基准混凝土的初凝或终凝时间,min。
7.6坍落度、坍扩度
坍落度测定按SD105-82中第4.0.2条[104-80]之规定,坍落度测定在按上述方法测定坍落度后,当混凝土不再向四周流动时,测量互相垂直的两个直径,取其平均值精确至1mm。
对掺泵送剂的混凝土除测定初始坍落度外尚应测定间隔30min和60min时的坍落度。
其测试方法是当测定初始坍落度SL0后把全部混凝土料装入铁桶或塑料桶内,用盖子或塑料布密封,存放30min后将桶内物料倒入拌料板上,用铁锹翻两次,进行坍落度试验得出坍落度保留值SL30,再将全部混凝土料装入桶内,密封再存放30min,用上法再测定一次,得出60min坍落度保留值SL60。
然后计算不同存放时间的坍落度损失率,其计算方法按下列公式进行:
SLB=(SL0-SLt)/SL0×100
式中:
SLB-坍落度损失率,%;
SL0-初始坍落度,mm;
SLt-存放时间t(min)后的坍落度,mm。
7.7抗压强度比测定:
抗压强度比以掺减水剂混凝土与基准混凝土同龄期抗压强度之比表示,按下式计算:
式中:
Rs──抗压强度比,%;
St──掺减水剂混凝土的抗压强度,MPa;
Sc──基准混凝土的抗压强度,MPa。
掺减水剂与基准混凝土的抗压强度按(GBJ81)进行试验和计算。
试件用振动台振动15s~20s,用插入式高频振捣器(Φ25mm,14000次/min)振捣时间为8s~12s。
试件预养温度为(20±5)℃。
试验结果以三批试验测值的平均值表示,若三批试验中有一批的最大值或最小值与中间值的差值超过中间值的15%,则最大及最小值一并舍去,取中间值作为该批的试验结果,如有两批测值与中间值的差均超过中间值的15%,则试验结果无效,应该重做。
7.8抗渗压力(或高度)比
试验步骤:
基准混凝土标养到28d,受检验负温混凝土-7+56d时进行抗渗试验,抗渗压力按0.2MPa、0.4MPa、0.6MPa、0.8MPa、1.0MPa加压,每级恒压8h,加压到1.0MPa为止,若试件透水,则按公式计算透水压力比,精确至1%:
式中:
Pr───透水压力比,%;
Pt───受检验负温混凝土(-7+56d)的透水压力,MPa;
PC───标养28d基准混凝土的透水压力,MPa。
若试件未透水则将劈开,测量试件10个等分点透水高度并取其平均值,以一组6个试件的平均值作为试验结果,透水高度比按公式计算,精确至1%:
式中:
Hr───透水高度比,%;
Ht───受检验负温混凝土6个试件水高度平均值,mm;
HC───基准混凝土6个试件透水高度平均值,mm。
7.9水泥净浆流动度
7.9.1将玻璃板放置在水平位置,用湿布将玻璃板、截锥圆模、搅拌锅均匀擦过,待其表面湿而不带水渍。
7.9.2将截锥圆模放在玻璃板中央,并用湿布覆盖待用。
7.9.3称取水泥300g,倒入搅拌锅内。
7.9.4加入推荐掺量的减水剂及87g或105g水,搅拌3min。
7.9.5将拌好的净浆迅速注入截锥圆模内,用刮刀刮平,将截锥圆模按垂直方向提起,同时开启秒表计时,任水泥净浆在玻璃板上流动,至30s,用直尺量取流淌部分互相垂直的两个方向的最大直径,取平均值作为水泥净浆流动度。
7.9.6结果表达
表达净浆流动度时,需注明用水量,所用水泥的强度等级、名称、型号及生产厂和减水剂掺量。
试样数量不应少于三个,结果取平均值,误差为±5mm。
7.10压力泌水率比
7.10.1将混凝土拌合物装入1.66L试料筒内,用捣棒由外围向中心均匀插捣25次,将仪器按规定安装完毕。
尽快给混凝土加压至3.5Mpa,立即打开泌水管阀门,同时开始计时,并保持恒压,泌出的水接入量筒内。
加压10s后读取泌水量V10,加压140s后读取泌水量V140。
7.10.2结果计算与评定:
7.10.2.1压力泌水率Bp按下式计算:
式中:
Bp───压力泌水率,%;
V10───加压10s时的泌水量,ml;
V140───加压10s时的泌水量,ml。
结果以三次试验的平均值表示,精确至0.1%。
7.10.2.2压力泌水率比Rb按下式计算,精确至1%:
式中:
Rb——压力泌水率比,%;
BPo——基准混凝土压力泌水率,%;
BPA——受检混凝土压力泌水率,%。
7.11含气量测定:
在进行拌和物含气量测定之前,应先测定拌和物所用骨料的含气量:
按下式计算每个试样中粗、细骨料的质量:
式中:
mg、mS───分别为每个试样中的粗、细骨料质量,kg;
m´g、m´S───分别为每立方米混凝土拌和物中的粗、细骨料质量,kg;
V───含气量测定仪容器容积,L。
在容器先注入1/3高度的水,然后把通过40mm网筛的粗、细骨料称好、拌匀,慢慢倒入容器。
水面每升高25mm左右,轻轻插捣10次,并略予搅动,以排除夹杂进去的空气,加料过程中始终使液面高出料的顶面,骨料全部加入后,浸泡约5min,再轻敲容器外壁,排净气泡,然后除去水面泡沫,加入至满,擦净容器边缘。
装好密封圈,加盖拧紧螺栓,关闭操作阀和排气阀,打开排水阀和加水阀,通过加水阀向容器内注水,当流出的水不含气泡时,在注水状态下关闭加水阀和排水阀。
开启进气阀,用打气筒打气,使气室的压力略大于0.1MPa,待压力表指针稳定后,微开排气阀,调整压力至0.1MPa,关紧排气阀。
开启操作阀,轻扣表盘,使指针稳定。
打开排气阀,并用操作阀调整压力。
使压力计指针刚好指在0.1MPa,然后关紧所有的阀门。
打开操作阀,使气室里的压缩空气进入容器,待指针稳定后记录表值,以此按压力与含气量关系曲线查得骨料的含气量值(精确至0.1%)。
含气量测定按该仪器说明进行操作:
用湿布擦净量钵与钵盖内表面,并使其水平放置,将新拌混凝土拌和物一次装入量钵内并稍高于容器,用振动台振实15s~20s刮去表面多余的混凝土拌和物,用镘刀抹平,并使其表面光滑无气泡。
擦净钵体和钵盖边缘,将密封圈放入钵体边缘地凹槽内,盖上钵盖,用夹子夹紧,使之气密良好.打开小龙头和排气阀,用注水器从小龙头处往量钵中注水,直至水从排水阀出口流出再关紧小龙头和排水阀.关好所有的阀门,用手泵打气加压,使表压稍大于0.1MPa,用微调阀准确地将表压调到0.1MPa.按下阀门杆1-2次,待表压指针稳定后,测得压力表读数,并根据仪器标定地含气量与压力表读数关系曲线,得到所测混凝土样品的仪器测定含气量A0值.
A=A0-Ag
式中:
A──混凝土拌和物含气量,%;
A0──含气量测定的平均值,%;
Ag──骨料含气量,%。
以两次测值的平均值作为试验结果,如两次含气量测值相差0.2%以上时,应进行第三次测定,如第三次与以上两次的最接近的值差仍大于0.2%时,此试验无效。
7.12收缩率比测定:
收缩率比以龄期28d掺混凝土与基准混凝土干缩率比值表示,按下式计算:
式中:
Rε──收缩率比,%;
εt──掺加减水剂的混凝土的收缩率,%;
εC──基准混凝土的收缩率,%;
掺减水剂及基准混凝土的收缩率按《混凝土试验作业指导书》中7.9测定和计算,每批混凝土拌和物取一个试样,以三个试样收缩率的算术平均值表示。
7.13抗冻性(50次冻融强度损失率比)
参照GBJ82-85进行试验并计算强度损失率。
基准混凝土在标养28d后进行冻融试验。
受检负温混凝土在龄期为-7+28d进行冻融试验。
根据计算出的强度损失率再按下式计算受检混凝土与基准混凝土损失率之比,计算精确至1%。
式中:
Dr──50次冻融强度损失比,单位为百分数%;
ΔfAT──受检负温混凝土50次冻融强度损失率,单位为百分数%;
ΔfC──基准混凝土50次冻融强度损失率,单位为百分数%。
7.14相对耐久性试验:
按《混凝土试验作业指导书》中7.7进行。
每批混凝土拌合物取一个试样,冻融循环次数以三个试件动弹性模量的算术平均值表示。
相对耐久性指标是以掺减水剂混凝土冻融200次后的动弹性模量降至80%或60%以上评定减水剂质量。
7.15含水率试验:
将洁净带盖的称量瓶放入100~105℃烘箱中干30min,取出置于干燥器内,冷却30min后称重,重复上述步骤至恒温(两次称量的质量差小于0.3mg),称其质量。
再称试样10g±0.2g,装入已烘干至恒温的称量瓶内盖上盖,称出试样及称量瓶总质量。
将盛有试样的称量瓶放入烘箱中,开启瓶盖升温至100~105℃,恒温2h取出,盖上盖然后置于干燥器内,冷却30min后称重,重复上述步骤至恒温,称其质量。
按下式计算:
式中:
──含水率,%;
m0──称量瓶的质量,g;
m1──称量瓶加干燥前试样质量,g;
m2──称量瓶加干燥后试样质量,g。
取三个试样测定数据的平均值为试验结果,精确至0.1%。
7.16细度:
试样在试验前应充分拌匀并经100~105℃烘干,称取10g倒入筛内,用人工筛样,将近筛完时,必须一手执筛反复摇动,一手拍打,摇动速度每分钟120次,并且筛子应向一方向旋转数次,使试样分散在筛布上,直至每分钟通过质量不超过0.05g时为至。
称量筛余物,称准至0.001g。
按下式计算:
式中:
m1──筛余物质量,g;
m0──试样质量,g
重复性限为0.001g/mL;
再现性限为0.002g/mL。
7.17比表面积
7.17.1
用水银排代法先测试料层体积:
将二片滤纸沿圆筒壁放入透气圆筒内,用一直径比透气筒略小的细长长棒往下按,直到滤纸平整地放在金属的穿孔板上,然后装满水银,用一小块薄玻璃片轻压水银表面,使水银面与圆筒平齐,并须保证在玻璃板和水银表面之间没有气泡或空洞存在。
从圆筒口中倒出水银称量,记录水银质量P1,精确至0.05g。
重量几次测定,到数值基本不变为止。
然后从圆筒中取出一片滤纸,试用约3.3g的试样,按照要求压实水泥层。
再在圆筒上部空间注入水银,同上述方法除去气泡压平,倒出水银称量P2,重复几次,直到试样称量值相差小于50mg为止。
计算试料层的体积:
V=(P1-P2)/ρ水银
式中:
V—试料层体积(mm3)
ρ水银—试验温度下水银的密度(g/cm3)
试料层体积的测定至少应进行两次,每次应单独压实,取两次值差不超过0.005cm3的平均值,并记录温度。
在不同温度下水银密度空气粘度n和n
室温(℃)
水银密度(g/cm3)
空气粘度n(Pa.s)
n
8
13.58
0.0001749
0.01322
10
13.57
0.0001759
0.01326
12
13.57
0.0001768
0.01330
14
13.56
0.0001778
0.01333
16
13.56
0.0001788
0.01337
18
13.55
0.0001798
0.01341
20
13.55
0.0001808
0.01345
22
13.54
0.0001818
0.01348
24
13.54
0.0001828
0.01352
26
13.53
0.0001838
0.01355
28
13.53
0.0001847
0.01359
30
13.52
0.0001857
0.01363
32
13.52.
0.0001867
0.01366
34
13.51
0.0001876
0.01370
7.17.2将110±5℃下烘干并在干燥器中冷却到室温的标准试样,倒入100mL的密闭瓶中,用力摇动2min,将结块成团的试样振碎,时试样松散。
静置2min后,打开瓶盖,轻轻搅拌,使在松散过程中落到表面的细粉,分布到整个试样中。
7.17.3试样应预先通过0.90mm方孔筛,在110±5℃温度下干燥1h,并在干燥器内冷却室温。
7.17.4校正试验用的标准样量和被测定试样的质量,应达到在制备的试料层中孔隙率为0.500±0.005。
计算式为:
W=ρV(1-e)
式中:
W—需要的试样量,g
ρ—试样的密度,g/cm3
V—测定的试料层体积,cm3
e—试料层孔隙率
7.17.5试料层制备:
将穿孔板放入透气圆筒的突缘上,用一根直径比圆筒略小的细棒把一片滤纸送到穿孔板上,边缘压紧称取上式中确定的试样量,精确到0.001g,倒入圆筒。
轻敲筒边,使水泥表面平坦。
再放入一片滤纸,用捣器均匀捣实直至捣器的支持环紧紧接触筒顶边并旋转两周,慢慢取出捣器。
7.17.6透气试验:
把装有试料层的透气圆筒接到压力计上,要保证不漏气,并不振动所制备的试料层。
先关闭压力计臂上之旋塞,开动抽气泵,慢慢打开旋塞,平稳地从U形管压力计一臂中抽出空气,直达液面升到最上面的一条刻线时关闭旋塞和气泵。
当压力计的液面的凹面达到第二条刻线时开始计时,当页面的凹面到第三条刻线时停止计时,记录液体通过第二、第三条刻度时的秒数并记下试验时温度。
7.17.7结果计算:
7.17.7.1当被测物料的密度、试料层孔隙率与标准试样相同,试温差≤3℃时,按下式计算:
试温大于±3℃时,按下式计算:
式中:
S—被测试样的比表面积,g/cm3
Ss—标准试样的比表面积,g/cm3
T—被测试样试验时,压力计中液面降落测得的时间,s
Ts—标准试样试验时,压力计中液面降落测得的时间,s
η—被测试样试验温度下的空气粘度Pa.s
ηs—标准试样试验温度下的空气粘度Pa.s
7.17.7.2当被测试样的试料层中孔隙率与标准试样试料层中孔隙率不同,试温差≤3℃时,按下式计算:
试温大于±3℃时,按下式计算:
式中:
ε—被测试样试料层中的孔隙率
ε3—标准试样试料层中的孔隙率
7.17.7.3当被测试样的密度和孔隙率均与标准试样不同,试温差≤3℃时,按下式计算:
试温大于±3℃时,按下式计算:
式中:
ρ—被测试样的密度,g/cm3
ρs—标准试样的密度,g/cm3
7.17.7.4试样比表面积应由二次透气实验结果的平均值确定。
如二次试验结果相差2%以上时,应重新试验。
计算应精确至10cm2/g,10cm3/g以下的数值按四舍五入计(以cm2/g为单位算得的比表面积值换算为m2/g时需乘以系数0.1)。
7.18碱含量:
试样用约80℃的热水溶解,以氨水分离铁、铝;以碳酸钙分离钙、镁。
滤液中的碱(钾和钠),采用相应的滤光片,用火焰光度计进行测定。
7.18.1试剂与仪器
7.18.1.1盐酸(1+1)。
7.18.1.2氨水(1+1)。
7.18.1.3碳酸氨溶液(100g/L)。
7.18.1.4氧化钾、氧化钠标准溶液:
精确称取已在130℃~150℃烘过2h的氯化钾(KCl光谱纯)0.7920g及氯化钠(NaCl光谱纯)0.9430g,置于烧杯中,加水溶解后,移入1000mL容量瓶中,用水稀释到标线,摇匀,转移至干燥的带盖的塑料瓶中.此标准溶液第毫升相当于氧化钾及氧化钠0.5mg。
7.18.1.5甲基红指示剂(2g/L乙醇溶液)。
7.18.1.6火焰光度计。
7.18.2试验步骤
7.18.2.1工作曲线的绘制
分别向100mL容量瓶中注入0.00;1.00;2.00;4.00;8.00;12.00mL氧化钾、氧化钠标准溶液(分别相当于氧化钾、氧化钠0.00;0.50;1.00;2.00;4.00;6.00mg),用水稀释至标准线,摇匀,然后分别于火焰光度上按仪器使用规程进行测定,根据测得的检流计读数的浓度关系,分别绘制氧化钾及氧化钠的工作曲线。
7.18.2.2准确称取一定量的试样置于150mL的瓷蒸发皿中,用80℃左右的热水润湿并稀释至30mL,置于电热板上加热蒸发,保持微沸5min后取下,冷却,加1滴甲基红指示剂,滴加氨水(1+1),使溶液呈黄色;加入10mL碳酸铵溶液,搅拌,置于电热板上加热并保持微沸10min,用中速滤纸过滤,以热水洗涤,滤液及洗液盛于容量瓶中,冷却至室温,以盐酸(1+1)中和至溶液呈红色,然后用水稀释至标线,摇匀,以火焰光度计按仪器使用规程进行测定。
称样量及稀释倍数见下表。
总碱量,%
称样量,g
稀释体积,mL
稀释倍数n
1.00
0.20
100
1
1.00~5.00
0.10
250
2.5
5.00~10.00
0.05
250或500
2.5或5
大于10.00
0.05
500或1000
5或10
7.18.2.3结果表示
氧化钾与氧化钠含量计量:
氧化钾X1含量按下式计算:
式中:
X1——减水剂中氧化钾含量,%
C1——在工作曲线上查得每100mL被测定氧化钾的含量,mg;
n——被测溶液的稀释倍数;
m——试样质量,g;
氧化钠X2含量按下式计算:
式中:
X2——减水剂中氧化钠含量,%
C2——在工作曲线上查得每100mL被测定氧化钠的含量,mg;
n——被测溶液的稀释倍数;
m——试样质量,g;
总碱量按下式计算
总碱量(%)=0.658×X1+X2
7.19钢筋锈蚀试验
7.19.1仪器:
钢筋锈蚀测量仪
7.19.2试验步骤
7.19.2.1制作钢筋电极:
将I级建筑钢筋加工制成直径7mm,长度为100mm,表面粗糙度Ra的最大值为1.6µm的试件,用汽油、乙醇、丙铜依次浸擦除去油脂,并在一端焊上长130mm~150mm的导线,再用乙醇仔细擦去焊油,钢筋两端浸涂热溶石蜡松香绝缘涂料,使钢筋中间报暴露长度为80mm,计算其表面积。
经过处理后的钢筋放入干燥器内备用,每组试件三根。
7.19.2.2拌制新鲜砂浆:
在无特殊要求时,采用水灰比0.5,灰砂比1:
2配制砂浆,水为蒸馏水,砂为检验水泥强度用的标准砂,水泥为基准水泥(或按试验要求的配合比配制)。
干拌1min,湿拌3min。
检验减水剂时,减水剂按比例随拌和水加水。
7.19.2.3砂浆及电极入模:
把拌制好的砂浆浇入试模中,先浇一半(厚20mm)。
将两根处理好经检查无锈痕的钢筋电极平行放在砂浆表面,间距40mm,拉出导线,然后灌満砂浆抹平,并轻敲几下侧板,使其密实。
7.19.2.4连接试验仪器:
按操作规程交三个夹子分别接阳极钢筋、阴极钢筋和甘汞电极即可。
7.19.2.5测试:
未通外加电流前,先读出阳极钢筋的自然电位V(即钢筋阳极与甘汞电极之间的电位差值)。
7.19.2.6接通外加电流,并按电流密度50×10-2A/m2(即50µA/cm2)调整µA表至需要值。
同时,开始计算时间,依次按2、4、6、8、10、15、20、25、30、60min,分别记录阳极极化电位值。
7.19.2.7试验结果处理:
以三个试验电极测量结果的平均值,作为钢筋阳极极化电位的测定值,以时间为横坐标,阳极极化电位为纵坐标,绘制电位-时间曲线。
7.19.2.8根据电位-时间曲线判断砂浆中的水泥、减水剂等对钢筋锈蚀的影响。
7.20固体含量
7.20.1将洁净带盖称量瓶放入烘箱内,于100℃~105℃烘30min,取出置于干燥器内,冷却30min后称量,反复上述步骤直至恒温,其质量为m0。
7.20.2将被测试样装入已经恒重的称量瓶内,盖上盖称出试样及称量瓶的总质量m1。
试样称量:
液体产品:
3.0000g~5.0000g。
将盛有试样的称量瓶放入烘箱内,开启瓶盖,升温至100℃~105℃(特殊品种除外)烘干,盖上盖置于干燥器内冷却30min后称量,重复上述步骤直至恒重,其质量为m2。
7.20.3结果表示
固体含量X固按下式计算:
7.21密度
7.21.1仪器:
比重瓶法
7.21.2测试条件:
液体样品直接测试;固体样品溶液的浓度为10g/L;被测溶液的温度为20℃±1℃;