电机绕组的浸漆工艺.docx
《电机绕组的浸漆工艺.docx》由会员分享,可在线阅读,更多相关《电机绕组的浸漆工艺.docx(6页珍藏版)》请在冰豆网上搜索。
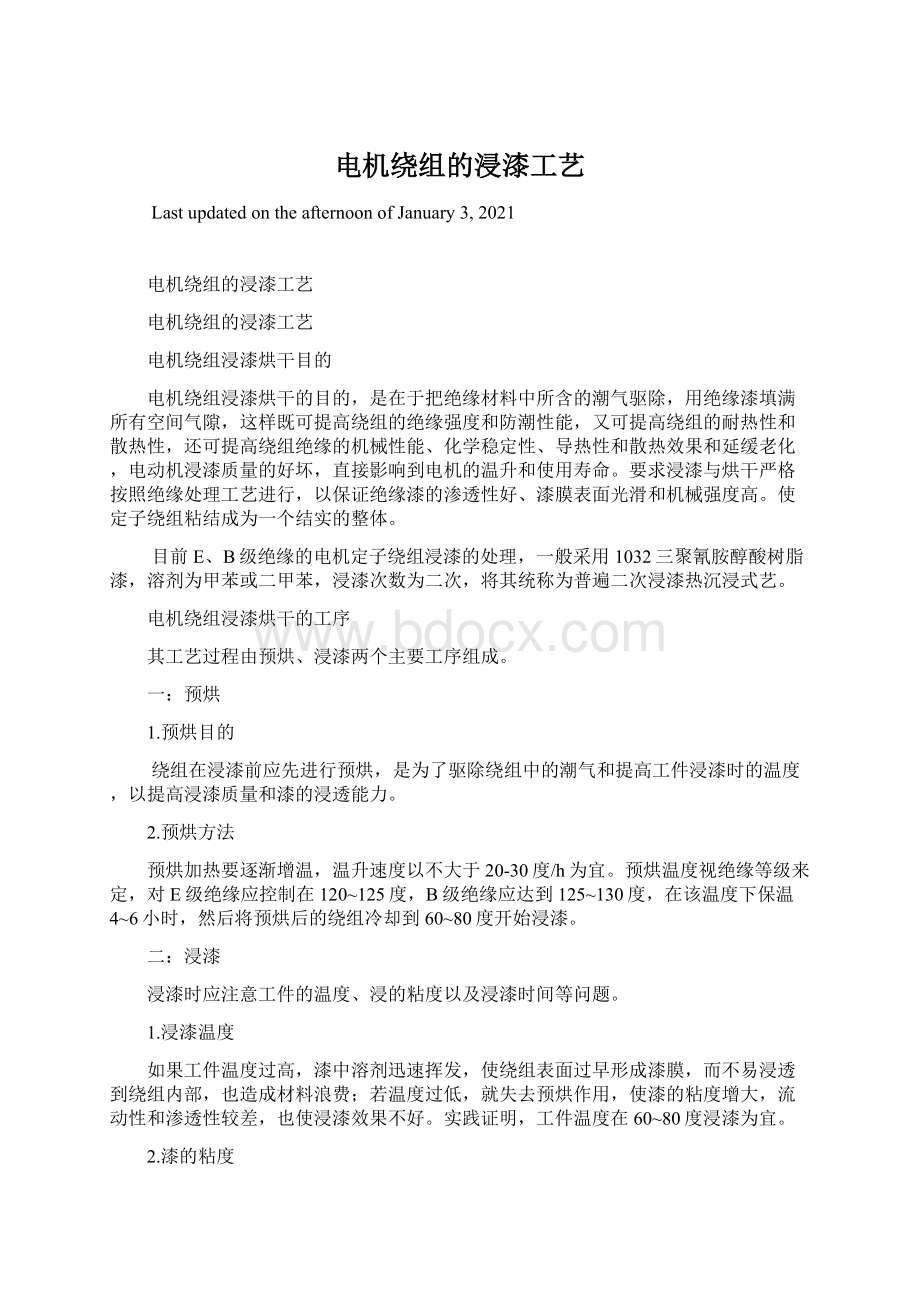
电机绕组的浸漆工艺
LastupdatedontheafternoonofJanuary3,2021
电机绕组的浸漆工艺
电机绕组的浸漆工艺
电机绕组浸漆烘干目的
电机绕组浸漆烘干的目的,是在于把绝缘材料中所含的潮气驱除,用绝缘漆填满所有空间气隙,这样既可提高绕组的绝缘强度和防潮性能,又可提高绕组的耐热性和散热性,还可提高绕组绝缘的机械性能、化学稳定性、导热性和散热效果和延缓老化,电动机浸漆质量的好坏,直接影响到电机的温升和使用寿命。
要求浸漆与烘干严格按照绝缘处理工艺进行,以保证绝缘漆的渗透性好、漆膜表面光滑和机械强度高。
使定子绕组粘结成为一个结实的整体。
目前E、B级绝缘的电机定子绕组浸漆的处理,一般采用1032三聚氰胺醇酸树脂漆,溶剂为甲苯或二甲苯,浸漆次数为二次,将其统称为普遍二次浸漆热沉浸式艺。
电机绕组浸漆烘干的工序
其工艺过程由预烘、浸漆两个主要工序组成。
一:
预烘
1.预烘目的
绕组在浸漆前应先进行预烘,是为了驱除绕组中的潮气和提高工件浸漆时的温度,以提高浸漆质量和漆的浸透能力。
2.预烘方法
预烘加热要逐渐增温,温升速度以不大于20-30度/h为宜。
预烘温度视绝缘等级来定,对E级绝缘应控制在120~125度,B级绝缘应达到125~130度,在该温度下保温4~6小时,然后将预烘后的绕组冷却到60~80度开始浸漆。
二:
浸漆
浸漆时应注意工件的温度、浸的粘度以及浸漆时间等问题。
1.浸漆温度
如果工件温度过高,漆中溶剂迅速挥发,使绕组表面过早形成漆膜,而不易浸透到绕组内部,也造成材料浪费;若温度过低,就失去预烘作用,使漆的粘度增大,流动性和渗透性较差,也使浸漆效果不好。
实践证明,工件温度在60~80度浸漆为宜。
2.漆的粘度
漆的粘度选择应适当,第一次浸漆时希望漆浸透到绕组内部,因此要求漆的流动性好一些,故漆的粘度应较低,一般可取22~26s(20度、4号粘度计);第二次浸漆时,主要希望在绕组表面形成一层较好的漆膜,因此漆的粘度应该大一些,一般取30~38s为宜。
由于漆温对粘度影响很大,所以一般规定以20度为基准,故测量粘度时应根据漆的温度作适当调整。
3.浸漆时间
浸漆时间的选择原则:
第一次浸漆,希望漆能尽量浸透到绕组内部,因此浸漆时间应长一些,约15~20min第二次浸漆,主要是形成较好的表面漆膜,因此浸漆时间应短一些,以免时间过长反而将漆膜损坏,故约10~15min为宜。
但一定要浸透,一直浸到不冒气泡为止,若不理想可适当延长浸漆时间。
每次浸漆完成后,都要把定子绕组垂直放置,滴干余漆,时间应为30min,并用溶剂将其它部位余漆擦净。
浸漆方法
浸漆的主要方法有:
浇浸、沉浸、真空压力浸。
对单台修理的电机浸漆,多采用浇浸,而沉浸和真空压力浸通常用于制造电机,对批量的可考虑沉浸,高压电机才采用真空压力浸。
常用的浇浸工艺方法为:
(a)取出预烘的电机,待温度凉至60~80度,竖直架于漆盘之上;
(b)将无溶剂漆灌入空饮料塑料瓶中,以便把握浇浸漆量;
(c)手拿装有绝缘漆的塑料瓶,斜倾瓶口使绝缘漆流出瓶口呈线状,从绕组上端部浇入绝缘漆,使漆在线圈中渗透并由绕组下端部回流到漆盘;
(d)当停止滴漆约20~30min,把电机定子翻过来,再将绝缘漆浇向绕组上端部(原下端部)直至渗透为止;
(e)再停止滴漆约30min后,用布蘸上煤油,将定子内膛及机座上的余漆清除,然后进行烘干;
(f)若需二次浸漆的,经烘干后取出凉至60~80度再进行二次浇浸,操作同上。
5、真空压力浸漆(简称:
VPI)绝缘工艺
VPI-真空压力浸渍工艺是将工件预烘去潮后冷却,置于真空环境中,排除白坯线圈内部的空气和挥发物,依靠真空中漆液重力和线圈毛细管作用,以及利用干燥的压缩空气或惰性气体,对解除真空后的浸渍漆液施加一定压力的作用,使漆液迅速渗透并充满绝缘结构内层。
在国内,目前VPI还是一种间隙作业的绝缘工艺。
工件的滴干工序在浸漆罐内进行,其干燥工序一般另设容器或烘箱进行,方式有真空干燥、常压静置干燥或旋转干燥。
VPI-工艺流程:
⊙→预烘除湿→入罐→真空排气→真空浸漆→压力浸渍→压力排漆→卸压滴漆→出罐→固化干燥→⊙。
比较:
显然,VPI在漆液渗透方面和浸渍方面,远远优于其它浸漆工艺。
在应用方面,VPI更适合大型高压线圈、多层齐绕磁轭线圈和要求较高的大型绕组、以及其它高压线圈。
理论上,VPI的应用,真空和压力可以做得相当的高,当然成本也高了。
FGH则不然,由于连续作业,以及产量和成本的具体要求,其应用具有一定范围的限制。
在应用试验和实际工作中,我们发现,真空环境对于某一温度条件下的一种浸渍漆液,当其真空度低于某一绝对压力的数值时,亦即达到某一对应的“临界”真空时,会导致该浸渍漆液中大量泡沫和液面大量雾气的产生,,即发生“沫化”和“雾化”现象。
“沫化”造成漆液中大量空穴,会阻碍浸渗。
“雾化”致使溶剂或稀释剂大量逸出,会影响固化。
对于压力,原则上加压是为了使漆液更容易进入填充空隙,输漆过程实际上就有一个大气压。
如果绝缘结构内毛细管的润湿性已经平衡,则增加压力对整个绝缘结构的填充并无明显作用,除非在固化时一直维持增加的压力,所以,增加填充的有效途径,是降低漆的粘度和减小绝缘结构空隙、提高毛细管效应,而不是提高压力。
根据“粘度与压力对渗透速率”的试验,其数据显示:
当漆液粘度较大时,增大压力对填充速度有较大作用,在漆液粘度小时,增大压力对填充速度的作用不显着。
然而,漆液粘度却对填充速度具有十分显着的影响,二者呈反比关系。
由此可见,在VPI工艺的应用中,片面强调和单纯追求高真空或高压力,是盲目和无益的。
其结果会影响浸渍效率,甚至会破坏浸渍质量。
一种工艺对不同的绝缘结构以及不同的技术要求,其实际工艺参数也各不相同。
譬如VPI共有四种工艺参数,即真空Vi、压力Pi、温度Ti、时间ti,其中i为1、2、3、…….,n(n是VP工艺工序的总数,i是工序次序)。
绝缘结构(W)、技术指标(A)、漆液特性(E)是这四种工艺参数的基本函数元素。
6电机、变压器绕组的浸漆绝缘处理工艺
从沉浸即普通浸渍到多次浸渍,又到滴漆,滚浸和真空浸漆,真空压力浸渍发展到工艺连续的普通沉浸,滴漆和滚浸,最后到真空浸漆烘干一体化,形成了一系列多样的机械化连续作业,应用现代计算机技术和PLC技术自动化控制的浸渍工艺,这是不断地通过技术革新,生产需求和社会发展的推动,逐步演变发展,正是这种推动,又产生了新一代真空浸漆烘干机,节能、环保成一体的高新技术产品、名牌产品,国内外近600家用户使用。
新一代真空浸漆烘干机是将工件放入浸烘缸预烘,在真空环境中排除线圈内部的空气和挥发物,再在真空条件下依靠漆液重力和线圈中毛细管作用,真空浸漆,使漆液迅速渗透并充满绝缘结构内层的一种机械作业的绝缘工艺。
FGH工艺流程:
放入工件→白坯预烘→真空去湿→真空浸漆→回漆→滴漆→清洗→回清洗剂→低温干燥至高温固化→保温→出炉全过程,全密封无环境污染一次性完成。
FGH作用优点:
在FGH工艺适用范围中,其作用的优点主要在以下几个方面:
(1)提高整体性,由于真空浸漆使绝缘漆几乎完全填充绝缘内部,加强了整个绕组的整体性,绕组在运行中各部分不会单独移动,减少了因移动磨损引起的故障。
(2)提高耐环境条件,由于真空浸漆,整个浸漆过程包括输漆和浸漆烘干,都是在完全密封容器条件下进行和完成,整个干燥过程采用热风循环加热,产生的废气通过A、B二组冷凝器回收再排放,改善工作环境,符合环保要求。
(3)降低运行温度和温升,由于真空浸漆与干燥成一体完全填充,良好地代替了内部空气隙,提高了导热性能,对电机、变压器一般可降低5-10℃。
(4)提高工件性能,由于真空浸漆干燥整个绕组被浸渍漆严密包封、浸透,表面漆膜光滑亮泽,使污染物、潮湿气体和化学气体不能进入内层,消除了由导电介质架桥引起的故障。
(5)节约能源和降低成本,由于真空浸漆、烘干成一体,干燥时间比烘箱缩短五分之二,干燥温度比烘箱降低10-20℃,进一步实现增产节能和降低成本。
定子绕组浸漆干燥工艺守则
1
本守则适用于中心高≤132mm的电机定子绕组,在LZJ-4自动连续沉浸机中进行B级、F级一次绝缘浸渍处理。
2、材料
浸渍材料:
JF-9801F2级连续沉浸树脂(B级、F级)。
稀释剂:
专用稀释剂。
清洗材料:
苯乙烯。
3、设备工具
LZJ-4自动连续沉浸机,具有工件自动传送系统,配有强迫循环通风、排废风机、控制温度等装置。
酒精温度计(0~100℃)、4号粘度计、秒表、500V兆欧表、时钟(计时监控用)。
毛刷、揩布。
刮漆工具:
铲刀、刮刀等。
4、工艺准备
检查所用材料、设备、装置、计量仪器和有关器具应符合使用要求。
检查有绕组定子铁心,其绕组端部绝缘不应有损伤、污迹,对引出线损伤、线圈碰伤、露铜、槽楔滑出、绑扎松开等工件应退回上道工序予以修整。
配漆:
4.3.1在室温下,将JF-9801F2级连续沉浸树脂按甲、乙两个组份2:
1(重量)比例,倒入贮漆箱,用搅拌工具搅拌均匀。
4.3.2测量绝缘漆的粘度:
先用温度计测量漆温,然后用4号粘度计测量漆的粘度(在漆面下约100mm外取样二次,求平均值),查附表一:
漆的温度与粘度关系,如:
对应23℃时,粘度为~。
5、工艺过程
设定工艺参数:
5.1.1工位状态:
总工位30篮,其中预热3篮、冷却2篮、浸漆1篮、滴干2篮、凝胶10篮、固化10篮、装卸2篮。
5.1.2工艺参数设定及控制:
参数见工艺参数表(附表二),其中“公进时间”由车间主管负责设置。
检查冷却水箱的水位情况,如果水箱内制冷机组蒸发器的盘管没有淹没,则须加入适量的清洁自来水,接通制冷机组的电源,启动压缩机冷却水箱中的水温,水温不低于5℃(防止结冰),这时冷水机的温控仪将切断制冷机组的电源,然后接通冷却水泵的电源,使冷却水在系统中循环(检查各管道及管接头处有无泄漏现象)。
开机前检查各控制开关的位置,“机修-工作”选择开关应拔在“工作”位置上,节拍时间与沉浸时间应符合(附表二)工艺参数表要求。
开启总电源开关,观察电源电压值及三相电源指示灯。
将预置加热开关拔至“非定时”位置,按下“启动”按钮,这时热风循环风机开始运转,相应指示灯亮起。
制冷机工作1小时左右后,开启各烘道加热区的加热控制开关,各相应的指示灯亮起,主管加热器开始加热烘道,根据加热温度的要求,将加热状态选择开关拔至“加热”“恒温”或“停止”,以控制辅助加热器的工作状态。
合上排废风机开关,相应的指示灯亮起,风机开始动转,这时程序控制同时投入动作,如吊篮的位置正确,则隔热门及沉浸槽自动进入起始位置。
开启漆泵开关,相应的指示灯亮起,漆泵把漆液从贮漆箱送往沉浸槽,如需搅拌漆液,开启漆搅拌器开关,搅拌完毕后将开关关闭。
当烘道温度达到预定值时,将工件装入吊篮,开始浸烘作业。
工件卸下后,检查其内外表面漆膜是否均匀,如有漆瘤及漆膜过厚影响装配时,应趁热铲除漆瘤或刮漆,同时将引接线分离。
6、质量检查
漆的粘度按附表一、浸漆时间及烘炉温度按附表二的技术要求,绝缘电阻应大于20MΩ。
烘干后绕组表面漆膜色泽应均匀一致,手触漆膜应不粘手并稍有弹性,表面无裂纹和皱纹,其端部无变形、端部铜线无磕碰、露铜、引接线分离、槽楔无错位。
浸渍漆无变质、无杂质。
每批工件的浸烘处理都应按规定做好记录,交接班时要签字。
工件干燥后应经检验人员检验合格,在浸烘记录上签字后方可转移。
7、注意事项
浸烘场所,严禁烟火及堆放易燃物品,应备有必要的消防器材,注意安全生产。
当漆液接触人体皮肤和眼睛时,用大量清水冲洗,严重时去医院救治。
定期清理活性碳纤维板,设备须按使用说明书要求定期进行维修保养。
工件应均匀地排列在吊篮内,吊篮不得倾斜。
工件装前,先清除吊篮底部的漆瘤,烘道温度未达到预定值时,不得进行浸烘作业。
设备内有工件时不允许停机。
设备运行时,不允许操作人员擅离岗位.要严格监控设备工作情况。
当设备出现故障时,应立即请机修人员修理。
不允许操作人员随意调节炉温及电气控制柜上的时间继电器。
在规定的时间内测量漆温及粘度,漆温最高不得超过40℃,当粘度超过时应在漆液中加入适量稀释剂,使粘度降到附表一(温度、粘度对照表)要求。
JF-9801F2级连续沉浸树脂是分组体系,使用时严格按比例配制,用多少配多少,工作结束后要用专用稀释剂清洗设备和输漆管路。
当停机时间超过2天时,开机前必须用苯乙烯清洗循环系统。
当发生突然停电等情况,恢复通电后,在设备内的定子(指在预烘工位以及正在沉浸的定子)应重新烘浸处理,确保质量。
停机时应先切断加热器的电源,10分钟后切断热风循环电机的电源,当机内从漆中挥发出来的气体基本消除后,再按下停止按钮。
沉浸槽中的漆面应高于绕组200mm以上。
工件在搬运堆放中应注意保护绕组和绝缘部位,以免发生碰伤现象。