浅述航空发动机高温蠕变.docx
《浅述航空发动机高温蠕变.docx》由会员分享,可在线阅读,更多相关《浅述航空发动机高温蠕变.docx(7页珍藏版)》请在冰豆网上搜索。
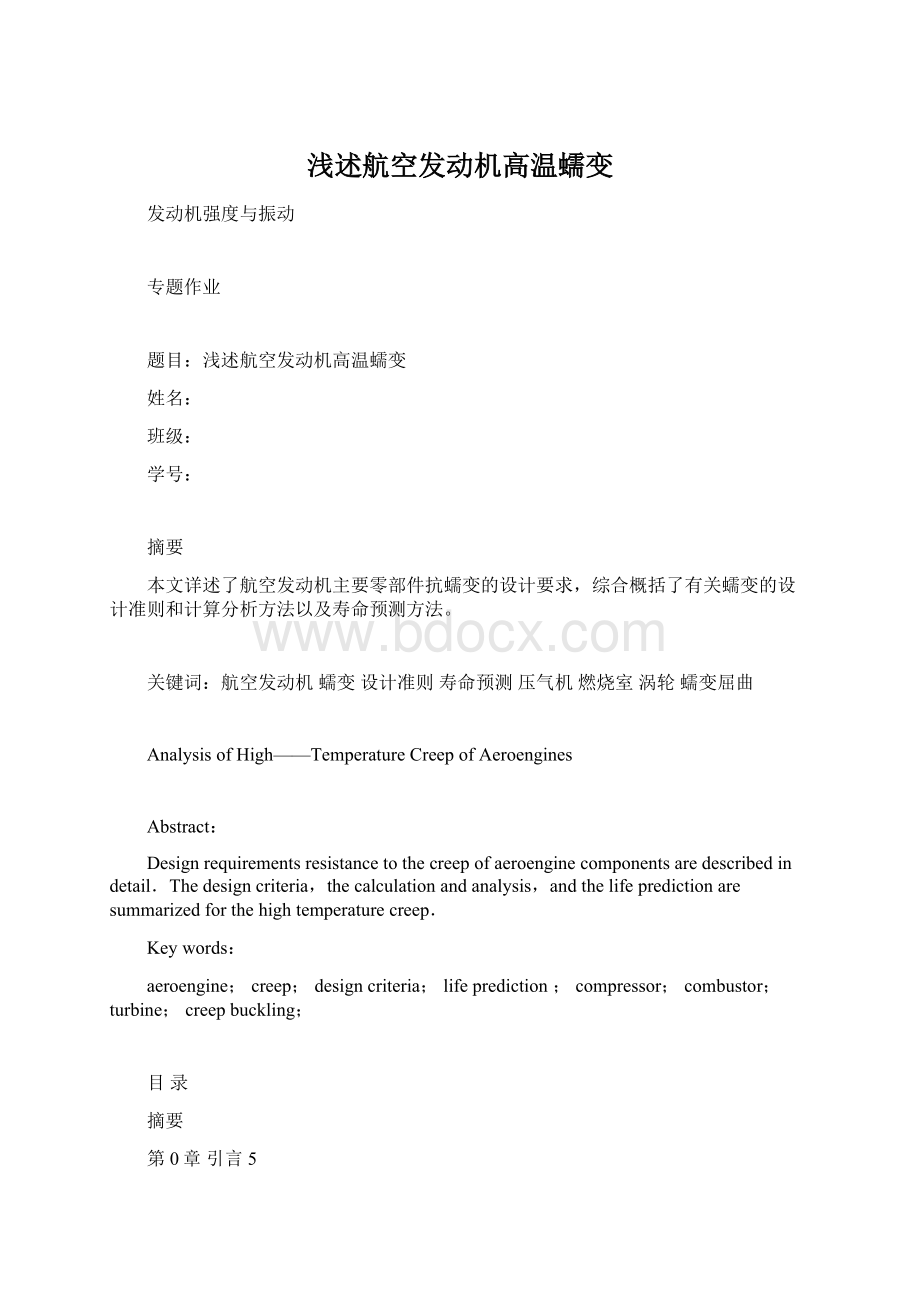
浅述航空发动机高温蠕变
发动机强度与振动
专题作业
题目:
浅述航空发动机高温蠕变
姓名:
班级:
学号:
摘要
本文详述了航空发动机主要零部件抗蠕变的设计要求,综合概括了有关蠕变的设计准则和计算分析方法以及寿命预测方法。
关键词:
航空发动机蠕变设计准则寿命预测压气机燃烧室涡轮蠕变屈曲
AnalysisofHigh——TemperatureCreepofAeroengines
Abstract:
Designrequirementsresistancetothecreepofaeroenginecomponentsaredescribedindetail.Thedesigncriteria,thecalculationandanalysis,andthelifepredictionaresummarizedforthehightemperaturecreep.
Keywords:
aeroengine;creep;designcriteria;lifeprediction;compressor;combustor;turbine;creepbuckling;
目录
摘要
第0章引言5
第1章航空发动机结构抗蠕变设计要求6
1.1轮盘设计的抗蠕变要求6
1.2叶片抗蠕变设计要求6
1.3热端机匣抗蠕变的设计要求6
1.4静子抗蠕变设计要求6
1.5燃烧室和加力燃烧室抗蠕变的设计要求7
第2章有关蠕变的设计准则7
第3章蠕变的计算分析方法9
第4章高温蠕变试验9
第5章蠕变寿命预测方法10
第6章结束语11
参考文献12
引言
蠕变会导致航空发动机高温零部件的塑性变形过大或产生蠕变应力断裂,特别是随着涡轮前温度进一步提高,其矛盾更加突出。
例如,在高温环境下,温度只增加15℃,零件的蠕变寿命就会缩短一半。
蠕变是材料的固有特性之一,金属材料的工作温度超过其熔化温度的40%时都会产生蠕变,当减小应力或降低温度时,稳定蠕变阶段(第2阶段)时间增长,甚至加速蠕变阶段(第3阶段)可能不会发生;当增大应力或升高温度时,蠕变的第2阶段随之缩短,只有起始蠕变阶段(第1阶段)和第3阶段,材料在很短时间内就会断裂。
要求理想的高温抗蠕变材料,蠕变曲线具有很短第1阶段和低速率第2阶段,以便延长产生限定变形量(如1%)的时间,同时也要求有一个明显的第3阶段,这样可以预示材料在断裂时有一定的塑性。
蠕变变形和蠕变断裂萌生于晶粒边界,并随着晶粒滑移和分离而扩展,因此,蠕变断裂是晶间断裂。
虽然蠕变是一种塑性流动现象,但晶间断裂过程却使断口具有脆性断裂的外观。
蠕变断裂通常是在没有颈缩、也没有预兆的情况下发生的。
目前还不能可靠地预测蠕变断裂或持久断裂的特性。
抗蠕变性能良好的材料,必须具有在长期高温作用下保持金相组织稳定的性能。
对于抗蠕变良好的合金,抗氧化和抗腐蚀的能力通常也是它的重要属性。
较大的晶粒对于抵抗蠕变也可能是有利的,因为晶粒越大,大部分蠕变过程赖以发生的晶界长度也就越短。
在航空涡喷涡扇发动机结构设计准则中,蠕变强度的判据一般用蠕变强度极限或持久强度极限来表征。
两种强度极限都是反映材料高温性能的指标,其区别在于侧重点不同。
例如航空发动机高温材料
在900℃,100h时的持久强度为314MPa,而在同样的温度和时间条件下产生0.2%的蠕变应变时,其蠕变强度极限为196MPa。
本文将详述了航空发动机主要零部件抗蠕变的设计要求,综合概括了有关蠕变的设计准则和计算分析方法以及寿命预测方法做一些简单的探讨。
一、航空发动机结构抗蠕变设计要求
提供“足够的蠕变/应力断裂寿命”是发动机主要零部件的设计要求之一。
1.1轮盘设计的抗蠕变要求
在恶劣的应力和温度条件下,轮盘抗蠕变设计要求轮盘关键尺寸的变化不超过规定的允许值。
在预定的检修期内,允许操作者用更换件重新装配转子,以防止出现较严重的松动或过盈。
因为轮盘经受着应力、温度和使用时间的综合作用,所以必须在零件的整个寿命期内保持尺寸稳定性,以避免累积的蠕变变形。
1.2叶片抗蠕变设计要求
叶片蠕变变形能使叶片径向伸长、恢复扭转和弯曲。
为了确保叶片在规定的寿命期内保持良好的性能。
限制蠕变变形量是叶片设计的主要要求。
其变形限制是:
工作中叶尖不应出现严重的磨损;叶型的恢复扭转不致引起叶冠松动或性能恶化;叶片顶部和叶冠的弯曲变形不应使叶冠间的松紧度发生太大的变化;不应使叶片的冷却效果变坏。
叶片设计也不应出现蠕变应力断裂。
在冷却叶片的过程中,应力和温度梯度造成蠕变率在相当大的范围内变化,而应力断裂裂纹仅在局部出现。
非冷却叶片应力断裂开始于整个危险截面上最大的局部蠕变。
经分析,它应与叶片的伸长和一个允许的最大伸长极限值有关,并以应力断裂裂纹刚开始时的蠕变为依据。
1.3热端机匣抗蠕变的设计要求
高压压气机机匣、扩散机匣、高压涡轮机匣和加力燃烧室机匣都可能发生高温蠕变。
为了减少叶片叶尖间隙增加量,使机匣变形减少到机匣部件允许的范围内,必须限制机匣的蠕变量。
例如,直径为60cm的涡轮机匣,产生0.1%的蠕变量。
引起的叶片叶尖间隙的增长量为3mm,这一增长量导致了很大的效率损失。
机匣蠕变对材料温度非常敏感。
机匣抗蠕变设计时,必须充分考虑飞行任务,确定发动机功率水平和在各功率水平的工作时间;还必须求出高压涡轮机匣在各水平的温度,以及在一个飞行任务中各功率水平上产生蠕变量的总和,从而得到
规范中规定的若干飞行任务中的总蠕变量。
如果总蠕变量超标,则通过增加机匣材料厚度或进一步冷却来降低蠕变量。
1.4静子抗蠕变设计要求
静子叶片的挠曲受到叶型蠕变、机匣和连接结构的蠕变变形等因素的综合影响。
应当确定叶型蠕变限度,以使隔圈和盘之间的间隙不低于安全运转限度。
蠕变除了引起尺寸变化外,还能因蠕变应力断裂而造成裂纹,因而必须考虑局部应力。
悬臂导向叶片主要承受弯曲载荷(包括热载荷),导致产生急剧的应力梯度和在局部区域诱发恶劣的蠕变状态。
应力断裂设计应选取当导向叶片材料出现大尺寸裂纹时的蠕变应变,这种裂纹估计出现在材料蠕变曲线第3阶段的开始时。
1.5燃烧室和加力燃烧室抗蠕变的设计要求
火焰筒工作时处于高温、高应力状态下,所以其材料大部分处于蠕变状态。
每个循环中的蠕变变形都缩短了火焰筒产生低循环疲劳裂纹的时间。
因此,必须考虑蠕变和疲劳的交互作用。
燃烧室温度最高时是发生在飞机起飞阶段,但在飞机爬升及巡航阶段也易发生蠕变变形。
大直径全环形火焰筒更容易产生蠕变屈曲。
因此,精确地确定蠕变屈曲寿命就变得很重要。
蠕变屈曲对压力载荷、简体工作温度、直径以及几何形状都很敏感,因此,要根据这些参数确定产生蠕变屈曲的临界变形值。
如简体应力增加10%,屈曲时间就缩短50%,材料温度每降低28℃,蠕变屈曲寿命将增加300%。
二、有关蠕变的设计准则
(1)美国军用标准MIL-STD-1783第4.9节中关于发动机零部件蠕变的设计要求是:
在第4.3节规定的工作状态和寿命期内,发动机的静止和转动件蠕变不能影响发动机外场正常使用;零件蠕变不能影响发动机的分解和再装配,或者在发动机整个规定寿命期内翻修时不得更换零件。
在第5.9节中关于零部件蠕变验证中提出:
发动机的静止和转动件蠕变特性必须满足5.9a、5.9b和5.9c节的要求和验证。
在该标准的第30节中,对“要求和验证”作了说明。
其中指出:
根据第4.3节中的“设计使用寿命”和“设计用法”中指出,在金属工作温度和此温度持续时间内,设计应力不得超过蠕变强度最低允许值的0.2%。
同时建议在“设计用法”和“设计使用寿命”期间设计应力不大于最小应力断裂寿命的50%所对应的应力值。
在蠕变和应力断裂设计分析中应包括设计的极限飞行状况和恶化状态。
每个蠕变的关键件必须完成随设计寿命变化而变化的蠕变、零件伸长量及应力断裂寿命百分比的分析预测。
设计的工作应力根据以往的经验来确定,即在达到满意的蠕变和应力断裂寿命百分比方面(即0.2%塑性蠕变寿命、0.127ram轮缘径向伸长量、50%应力断裂寿命等)有较高的概率。
(2)美国于1995年1月11日颁布的航空涡喷涡扇涡轴涡桨发动机通用规范(JAGS一87231A)中,在结构完整性中对热部件蠕变设计要求的许多细节与MIL-STD-1783相近,只是略有改动,如第4.0,4.1,5.3节,“背景”中指出:
对每个有蠕变限制的零件,应进行随设计用法而变化的蠕变和应力断裂寿命分析预测;应根据指明可以得到满意的高概率蠕变和应力断裂寿命(例如,0.1%塑性蠕变寿命、0.127mm轮缘直径增长、50%断裂寿命等)的以往经验确定设计工作应力。
所有转子的蠕变状态应以每个叶轮的蠕变为准,而不是以每个叶片的蠕变为准等。
这些与MIL-STD-1783不同的提法,是值得研究的。
(3)斯贝MK202发动机应力标准(EGD一3)的第2.1.3节中提出:
只有在要求发动机作连续的或累计的长时间工作时才考虑蠕变,通常将蠕变条件下的应力与材料的0.1%蠕变强度作比较。
但对某些按破坏条件而不是按变形限制来确定工作寿命的部件可与蠕变断裂强度作比较。
该标准的“结构设计准则”提出:
a.压气机。
压气机转子叶片的蠕变应力规定:
叶身弯曲应力和拉伸应力的合成应力应小于规定的蠕变强度;销接固定的叶片根部,销孔边缘的名义拉伸应力不应超过规定蠕变强度的60%;燕尾形榫头根部,所有应力应小于规定的蠕变强度。
压气机静子叶片在所有作用有蠕变应力的条件下,最大弯曲应力不应超过规定的蠕变强度。
b.涡轮。
涡轮盘的平均周向应力、在任意半径上的径向应力的合力(离心力加热载荷)以及盘枞树形榫齿的挤压应力都必须小于规定的蠕变强度。
涡轮转子叶片的叶冠、伸根和叶根颈部的弯曲应力和拉伸应力的合成应力以及枞树形榫齿的挤压应力不应超过规定的蠕变强度。
在所有蠕变应力的条件下,涡轮导向叶片最大弯曲应力不应超过规定的蠕变强度。
c.该准则对主轴及静子结构也都提出了蠕变的设计要求。
(4)高效节能发动机文集第5分册第5.1.4节中的设计准则指出:
蠕变一在一定温度下长时间承受应力的材料会发生某种形式的变形,特别是在转动结构中,蠕变因素是一个重要的设计准则。
在涡轮设计中,总蠕变量限制在0.2%。
(5)有些设计指南在考虑蠕变时,对设计应力是用持久强度作为判别标准。
例如对涡轮盘和叶片(包括叶身、缘板、伸根和榫头)、压气机盘和叶片等都规定了持久强度储备。
将在所研究状态的工作温度和持续时间的条件下相应材料的持久强度极限与该条件下计算点工作应力的比值称为储备系数,对不同零件都规定了不同的储备系数。
三、蠕变的计算分析方法
高温零部件蠕变变形和蠕变应力计算是进行零部件寿命预测的重要组成部分。
蠕变是与时间有关的塑性变形,是非线性问题。
同时,在蠕变过程中应力重新分配,蠕变量与瞬时应力水平有关,而瞬时应力水平又是时间的函数,所以蠕变计算是较复杂的。
用有限元法求解蠕变问题的基本思路是:
把蠕变经历的时间分成有限间隔,△£1、△£2、……,按某种简化方法求得每一时间间隔△£内的蠕变量,所有时间间隔蠕变量的积累即为整个时间的蠕变量。
在计算第i个时间间隔的△£蠕变时,一般采用显式或隐式欧拉法。
曾对涡轮盘和叶片(包括定向结晶和单晶)用ANSYS和MARC等程序进行了大量的计算,得出了可信结果。
计算蠕变时,首先要确定蠕变律,在大多数工程应用中采用Norton的表达式:
,式中A、n和P为不同温度下的材料常数,可由材料的单轴蠕变试验拟合出来。
循环蠕变分析是研究蠕变的重要课题。
发动机是在多种变工况下工作的,因此,预测蠕变寿命时,必须研究发动机在变动温度和变动应力下的循环蠕变特性。
这种循环蠕变特性和恒定温度与恒定应力状态下的静态蠕变特性相比,对于不同材料,其结论也不同。
在简单循环载荷谱下曾对单晶涡轮叶片作过循环蠕变计算,并与静态蠕变作了对比分析。
发动机工作时,部件的应力状态是热弹塑性加蠕变,即产生疲劳和蠕变,需要考虑它们的交互作用,蠕变会降低低循环疲劳寿命。
四、高温蠕变试验
进行蠕变计算分析,需要提供足够的3个阶段的蠕变曲线及其拟合的蠕变常数。
这些数据精确与否,对计算结果影响较大。
蠕变律常数需要对试件在工作温度范围内和应力状态下进行完整的蠕变试验。
据分析,至少要有9条蠕变曲线(3、4个温度,每个温度下取3、4个应力水平)反映出高温材料的蠕变行为,满足蠕变计算的需要。
受冶金、测量等因素影响,试验结果分散性很大,需要分析、校核和修正。
蠕变试验主要有2个难点。
一是蠕变试验是在高温下进行的,而温度越高,则试验结果的分散性越大;其二是要求在试验过程中应力保持恒定,而目前多数蠕变试验机在试验中只能保持载荷不变,这样得出的结果误差较大。
解决的办法是增加子样的容量以及人为地加以修正。
曾对镍基合金进行试验及校正,结果还是令人满意的。
五、蠕变寿命预测方法
由于蠕变寿命受多种因素的影响,所以蠕变寿命预测的方法也有多种。
工程中常用的方法有拉森-米勒(L—M)法。
该方法与寿命一时间分数法结合起来,可计算蠕变累积的损伤。
L—M方程为:
L—M方程参变常数由材料手册中查得。
当需要预测蠕变(
:
0.2%,0.1%),可采用方程:
考虑蠕变因素在材料中占支配地位时,估算蠕变寿命推荐用时间寿命分数法。
定义蠕变作用时间与蠕变断裂时间之比为损伤参数。
若有M级加载,则总损伤公式为:
如已知飞行载荷,可以统计出起飞、爬升、巡航和低速各状态的时间或时间比例。
当给出各状态的时间比例
时,则总寿命公式为:
式中:
L为总寿命(h);
为i状态下的蠕变断裂寿命。
法是预测蠕变寿命的一种新方法。
其基本思想是把蠕变曲线看成由衰减的第1阶段和加速的第3阶段所组成。
因此蠕变方程可以写成:
式中:
是经过t时间的总应变;
是在蠕变试验开始加载时的瞬时应变;
是温度和应力的函数。
一旦求得
即可得到在给定温度和应力下的蠕变曲线,以及由式
可求出在给定应变
下的时间
(蠕变寿命),或给定蠕变断裂应变
下的断裂时间
(蠕变断裂寿命)。
如果有的材料不合乎上述蠕变规律,如中国DD3单晶叶片材料,变形规律只表现出一个加速过程,这时可以利用改进的
法。
六、结束语
结构的蠕变的屈曲实质上是蠕变变形发展的过程,结构蠕变的屈曲是一个非常复杂的非线性问题,材料的蠕变性能、结构的外界约束、工作环境等都对蠕变屈曲有着显著的影响。
随着航空发动机发展,结构抗高温蠕变问题越来越重要,目前而言,还有许多问题须进一步深入研究,如蠕变寿命预测方法、测定标准、循环蠕变问题、蠕变疲劳交互作用,并且单晶和复合材料等新材料的蠕变特性也需提到议程上来。
参考文献
[1]雷友峰、程卫华、徐林耀等,航空发动机燃烧室蠕变屈曲研究.燃气涡轮试验与研究,2001.
[2]陈铁云、沈惠申,结构的屈曲.上海:
科技文献出版社.1993
[3]黎方学,单晶气冷涡轮叶片热弹性蠕变计算及蠕变寿命分析研究.北京航空航天大学研究生院学士学位论文,1999.
[4]饶寿期等,单晶材料涡轮叶片的循环蠕变分析.航空动力学报,1998,13
(1).
[5]孟春玲等.单晶叶片材料蠕变试验研究.北京航空航天大学学报,1998,24
(1).
[6]孟春玲等.涡轮叶片蠕变寿命预测方法研究.中国航空学会第七届航空发动机结构强度振动会议论文集,2000.
[7]美国军用标准,发动机结构完整性大纲(MIL-STD-1783).