立磨工艺2综述.docx
《立磨工艺2综述.docx》由会员分享,可在线阅读,更多相关《立磨工艺2综述.docx(40页珍藏版)》请在冰豆网上搜索。
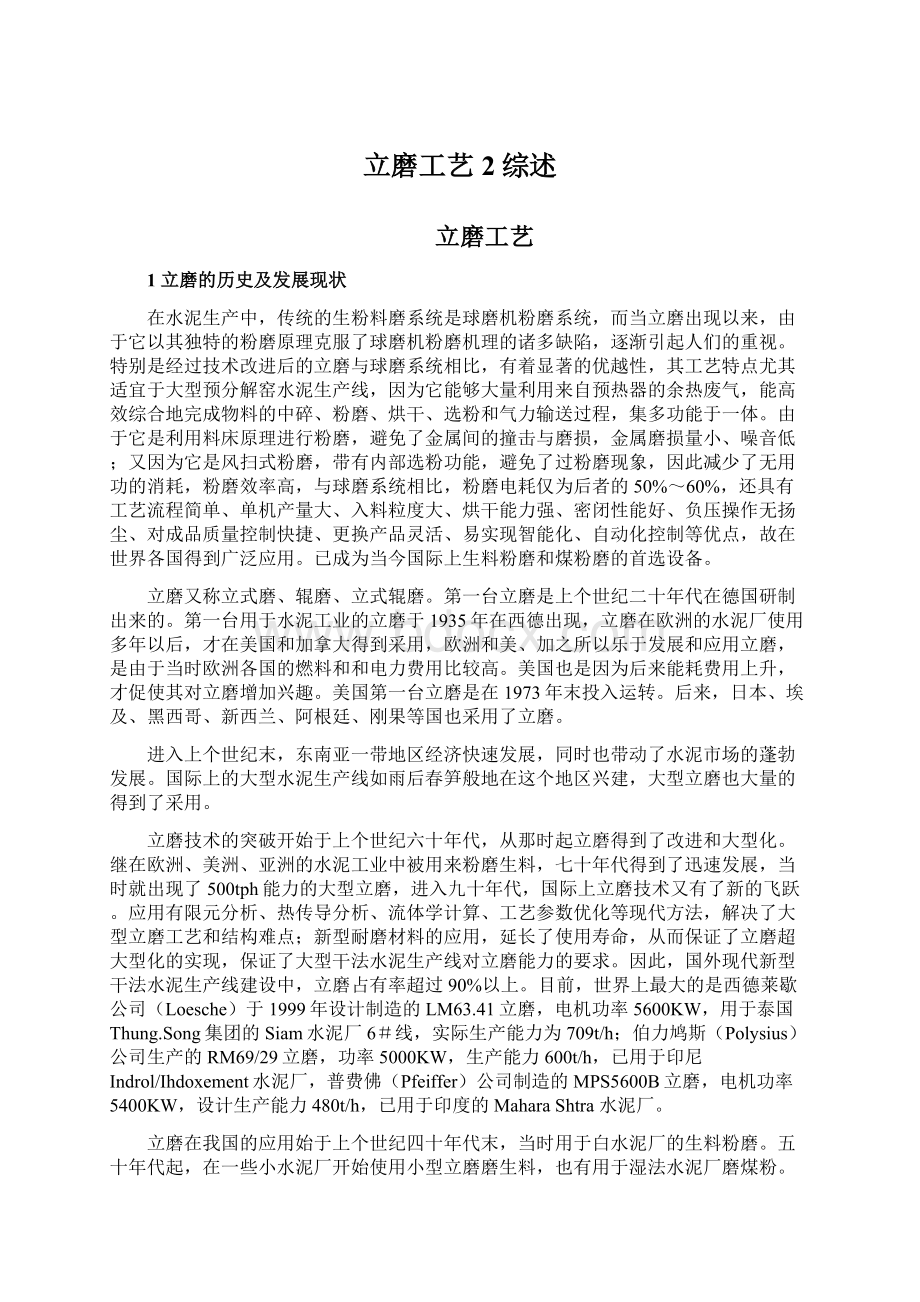
立磨工艺2综述
立磨工艺
1立磨的历史及发展现状
在水泥生产中,传统的生粉料磨系统是球磨机粉磨系统,而当立磨出现以来,由于它以其独特的粉磨原理克服了球磨机粉磨机理的诸多缺陷,逐渐引起人们的重视。
特别是经过技术改进后的立磨与球磨系统相比,有着显著的优越性,其工艺特点尤其适宜于大型预分解窑水泥生产线,因为它能够大量利用来自预热器的余热废气,能高效综合地完成物料的中碎、粉磨、烘干、选粉和气力输送过程,集多功能于一体。
由于它是利用料床原理进行粉磨,避免了金属间的撞击与磨损,金属磨损量小、噪音低;又因为它是风扫式粉磨,带有内部选粉功能,避免了过粉磨现象,因此减少了无用功的消耗,粉磨效率高,与球磨系统相比,粉磨电耗仅为后者的50%~60%,还具有工艺流程简单、单机产量大、入料粒度大、烘干能力强、密闭性能好、负压操作无扬尘、对成品质量控制快捷、更换产品灵活、易实现智能化、自动化控制等优点,故在世界各国得到广泛应用。
已成为当今国际上生料粉磨和煤粉磨的首选设备。
立磨又称立式磨、辊磨、立式辊磨。
第一台立磨是上个世纪二十年代在德国研制出来的。
第一台用于水泥工业的立磨于1935年在西德出现,立磨在欧洲的水泥厂使用多年以后,才在美国和加拿大得到采用,欧洲和美、加之所以乐于发展和应用立磨,是由于当时欧洲各国的燃料和和电力费用比较高。
美国也是因为后来能耗费用上升,才促使其对立磨增加兴趣。
美国第一台立磨是在1973年末投入运转。
后来,日本、埃及、黑西哥、新西兰、阿根廷、刚果等国也采用了立磨。
进入上个世纪末,东南亚一带地区经济快速发展,同时也带动了水泥市场的蓬勃发展。
国际上的大型水泥生产线如雨后春笋般地在这个地区兴建,大型立磨也大量的得到了采用。
立磨技术的突破开始于上个世纪六十年代,从那时起立磨得到了改进和大型化。
继在欧洲、美洲、亚洲的水泥工业中被用来粉磨生料,七十年代得到了迅速发展,当时就出现了500tph能力的大型立磨,进入九十年代,国际上立磨技术又有了新的飞跃。
应用有限元分析、热传导分析、流体学计算、工艺参数优化等现代方法,解决了大型立磨工艺和结构难点;新型耐磨材料的应用,延长了使用寿命,从而保证了立磨超大型化的实现,保证了大型干法水泥生产线对立磨能力的要求。
因此,国外现代新型干法水泥生产线建设中,立磨占有率超过90%以上。
目前,世界上最大的是西德莱歇公司(Loesche)于1999年设计制造的LM63.41立磨,电机功率5600KW,用于泰国Thung.Song集团的Siam水泥厂6#线,实际生产能力为709t/h;伯力鸠斯(Polysius)公司生产的RM69/29立磨,功率5000KW,生产能力600t/h,已用于印尼Indrol/Ihdoxement水泥厂,普费佛(Pfeiffer)公司制造的MPS5600B立磨,电机功率5400KW,设计生产能力480t/h,已用于印度的MaharaShtra水泥厂。
立磨在我国的应用始于上个世纪四十年代末,当时用于白水泥厂的生料粉磨。
五十年代起,在一些小水泥厂开始使用小型立磨磨生料,也有用于湿法水泥厂磨煤粉。
自七十年代末,国内在干法水泥厂开始发展窑外分解新型干法工艺时,才比较重视立磨粉磨生料的研究开发工作。
八十年代初,天津水泥研究设计院开发出了TKM系列立磨。
其中TKM25型立磨用于河南新乡水泥厂1000t/d新型干法生产线上,产能为80t/h,系统电耗15.4KWh/t。
合肥水泥工业设计研究院研究开发出了HRM系列立磨,产能限于1000t/d的生产线配用。
与此同时,我国开始引进国外大型立磨用于新型干法水泥厂。
据统计,国内讫今共引进用于日产2000吨以上生产线配套的大型立磨已超过47台。
沈阳重型机器厂1985年从德国Pfeiffer公司引进了与日产2000吨以下规模生产线配套的MPS立磨制造技术,其产品在琉璃河水泥厂,万年水泥厂采用。
又与海螺集团合作开发制造与2500t/d、5000t/d生产线配套的MPS3424、MPS5000(MLS4531)立磨,目前已在荻港海螺、铜陵海螺和池州海螺等公司投入使用。
其中MLS4531立磨是已投入使用的最大的国产立磨。
由于海螺集团拥有国内最多的大型窑外分解生产线,因此,配用的大型立磨台数也是最多。
目前共拥有各型生料立磨13台,用于磨煤粉的立磨12台以上;海螺集团也是拥有进口大型立磨类型最多的企业,分别有MPS型、ATOX型、RM型、LM型等,其中池州海螺一个基地就分别拥有MPS型一台、ATOX型一台、RM型两台,用于粉磨生料,还有磨煤立磨三台。
预计海螺集团在建和拟建的多条熟料生产线将全部采用大型和特大型立磨用于粉磨生料。
纵观国际国内立磨的应用和演变,立磨正朝大型化和超大型化发展,以适应大型干法水泥生产线的建设,其结构设计更趋向合理,功能更趋向完善。
近年海螺集团采用的立磨,基本是经改进后的第三代立磨。
其选粉功能、细度调节功能、碾磨效率、耐磨性、节能措施、控制水平都大大提升。
立磨在水泥熟料粉磨的应用上也已出现成功的例子,大有在水泥厂取代球磨机系统的趋势,但立磨的技术含量高于球磨机,它是集机(含液压)、电、仪于一体的,功能综合性强的设备,无论是操作或维修的技术要求都超过球磨机,需要在实践中认真总结研究,以尽快管好、用好、维护好立磨,促进生产发展,最大化地提高经济效益。
2立磨工作原理及类型
立磨的类型很多,结构和功能各有特色,但基本结构大同小异,它们都具有传动装置、磨盘、磨辊、喷口环、液压拉伸装置、选粉装置、润滑系统、机壳等,其主要工作原理也基本相同。
2.1立磨主要工作原理
由传动装置带动机壳内磨盘旋转,磨辊在磨盘的磨擦作用下围绕磨辊轴自转,物料通过锁风喂料装置和进料口落入磨盘中央,受到离心力的作用向磨盘边移动。
经过碾磨轨道时,被啮入磨辊与磨盘间碾压粉碎。
磨辊相对物料及磨盘的粉碎压力是由液压拉伸装置提供(适宜的粉碎压力可根据不同物料的硬度进行调整)。
物料在粉碎过程中,同时受到磨辊的压力和磨盘与磨辊间相对运动产生的剪切力作用。
物料被挤压后,在磨盘轨道上形成料床(料床厚度由磨盘挡料环高度决定),而料床物料颗粒之间的相互挤压和磨擦又引起棱角和边缘的剥落,起到了进一步粉碎的作用。
粉磨后的物料继续向盘边运动,直至溢出盘外。
磨盘周边设有喷口环,热气流由喷口环自下而上高速带起溢出的物料上升,其中大颗粒最先降落到磨盘上,较小颗粒在上升气流作用下带入选粉装置进行粗细分级,粗粉重新返回到磨盘再粉磨,符合细度要求的细粉作为成品,随气流带向机壳上部出口进入收尘器被收集下来。
喷口环处上升的气流也允许物料中比重较大的物质落入喷口环下面,从机壳下部的吐渣口排出,由于喷口环处的气流速度高,因此热传递速率快,小颗粒被瞬时得到烘干。
据估算进入立磨的每一颗粒在成为成品之前,平均在磨辊下和上升气流中往复内循环运动达几十次,存在多级粉碎的事实。
从上述可以看出,立磨工作时对物料发挥的是综合功能。
它包括在磨辊与磨盘间的粉磨作用;由气流携带上升到选粉装置的气力提升作用;以及在选粉装置中进行的粗细分级作用;还有与热气流进行热传递的烘干作用,对于大型立磨而言(指入磨粒度在100mm左右),实际上还兼有中碎作用,故大型立磨实际具有五种功能。
上述吐渣口的功能在大型立磨上也发生了变化,利用吐渣口与外部机械提升机配合,将大比例的物料经吐渣口进入外部机械提升机重新喂入磨内粉磨,以减轻磨内气力提升物料所需风机负荷,有利于降低系统阻力和电耗,因为机械提升电耗显著地低于气力提升出现的较高电耗,这种方法称为物料的外循环。
2.2立磨的类型
各型立磨在结构上的差异最突出的是在磨盘的结构和磨辊的形状及数目上。
另一方面,不同类型的立磨在选粉装置上均作了较大改进,现在已经把高效选粉机移置到立磨之中,以取代原来的静态惯性选粉装置,提高了选粉效率,也能更方便地调节成品细度。
还有对磨辊的加压方式也各有不同等。
因此,功能效果上各有千秋。
现将常用的几种立磨主要结构功能与特点分述如下:
MPS型立磨:
MPS型立磨为西德普费佛(Pfeiffer)公司技术,也称非凡磨。
(沈重基于普费佛公司技术开发制造的MLS型磨也属此类)。
该磨采用鼓形磨辊和带圆弧凹槽形的碗形磨盘,粉磨效率较高,磨辊3个,相对于磨盘倾斜安装,相互120°排列。
辊皮为拼装组合式。
由三根液压张紧杆传递的拉紧力通过压力框架传到三个磨辊上,再传到磨辊与磨盘之间的料层中。
该液压张紧杆不能将磨辊和压力框架在启动磨机时同时抬起,故设有辅助传动装置。
启动时先开辅传,间隔一定时间再开启主传动装置。
选粉装置由静态叶片按设定倾角布置,起引导气流产生旋转,以强化分离物料的作用。
由机顶传动装置带动设在选粉装置中部的动态笼型转子转动,并且可方便地实现无级调速。
有强化选粉装置中部旋转风速的作用,增强选粉效率和方便地通过调整转速来调整成品细度(转速越大,细度越细)。
喷口环导向叶片为固定斜度安装,有利于引导进风成为螺旋上升趋势,可使粗粉在进入选粉装置前,促进部分粗粒分离出上升气流回到磨盘。
可在运转前进入磨内用遮档喷口环的截面方法来改变风环通风面积,从而改变风速(总面积越小,风速越大),以适应不同比重物料的风速需要。
检修时液力张紧杆只可将联在辊上的压力框架抬起,但应先拆除压力框架与磨辊支架间的联接板。
并用装卸专用工具将磨辊固定。
喂料口锁风装置采用液压控制的三道闸门,既有锁风功能,又有控制喂料量的作用。
吐渣口锁风采用两道重力翻板阀控制。
ATOX型立磨
该磨为丹麦史密斯(F.L.Smidth)公司设计并制造。
采用圆柱形磨辊和平面轨道磨盘,磨辊辊皮为拼装组合式,便于更换辊皮。
磨辊一般为3个,相互成120°分布,相对磨盘垂直安装。
三个磨辊由中心架上三个法兰与辊轴法兰相联为一体。
再由三根液力拉伸杆分别通过与三个辊轴另一端部相联,将液压力向磨盘与料层传递,该液压张拉伸杆可将磨辊和中心架整体抬起。
因此,不设辅传,启动时直接开动主传动系统。
选粉装置已用SEPAX选粉机来取代原来的静态惯性分离器,SEPAX也是丹麦开发的一种高效选粉机,其结构也分为一圈静态导向叶片和中间一个由窄叶片组成的动态笼形转子,其机理和功能大致类似MPS采用的选粉装置。
不过,在笼型转子上加了水平分隔环构件,该构件有利于旋转气流呈分层水平旋转,气流运动清晰,气流层与层间干扰小,使选粉分级功能更加高效。
静态叶片可预先设定倾角,有辅助调整产品细度的作用。
运转中还可以用机顶外部调整螺栓来调整叶片角度。
喷口环与MPS型类似。
喂料口锁风装置采用机械传动的回转叶轮结构,既锁风又可控制喂料量。
进料溜管底部为通热风的夹层结构,有防堵的作用。
吐渣口采用密闭的电磁振动给料机出料,具有料封功能。
RM型立磨
该磨为西德伯力鸠斯(Polysius)公司技术并制造。
大约于1965年开始生产以来,主要销售欧洲。
RM磨经历了三代技术改造,目前的结构和功能与其它类型立磨有较多的区别。
主要体现在是以两组拼装磨辊为特点,每组辊子由两个窄辊子拼装在一起,两组共4个磨辊,这两个辊子各自调节它们对应于磨盘的速度。
有利于减少磨盘内外轨道对辊子构成的速度差,从而减轻摩擦带来的磨损,可延长辊皮的使用寿命,还削减了辊和盘间物料的滑移,每个磨辊也为轮胎形,磨盘上相对应的是两圈凹槽形轨道,磨盘断面为碗形结构,磨盘上两个凹槽轨道增加了物料被碾磨的次数和时间,有利于提高粉磨效率。
每组磨辊有一个辊架,每个磨辊架两端各挂一吊钩,各吊钩由一个液压拉杆相联,共4根。
拉杆通过吊钩和辊架传递压力到磨辊与料床上,对物料碾压粉碎。
碾压力连续可调,以适应操作要求。
液压拉紧系统可让每组双辊在三个平面上自由移动,如:
垂直面上升下降和相对辊轴轴面偏摆以及少量沿辊子径向的水平移动。
如果靠磨盘中间的内辊被粗料抬高,那么外辊对物料的压力就会加大,反之亦然。
每组磨辊中的每个窄辊的这种交互作用的功能也导致高效研磨。
研磨轨道的形状和棍面经磨损变形后能影响吊钩的偏移量。
可通过测量其磨损量并相应调整吊钩吊挂方位来弥补。
这有利于使提供给双辊的压力均衡,维持粉磨效果。
双辊组的辊面还可在被不均衡磨损后,还可整体调转180o安装使用。
喷口环出风口面积设计成可从机壳外部调整,调整装置为8个定位销档板,通过推进和拉出一定许可量并用插销定位即可改变喷口环面积,从而改变气流在磨内的上升速度(面积小,则气速高)以适应不同的产量的需要。
喷口环导向叶片垂直装设,有利于减少通风阻力。
选粉装置采用了SEPOL型高效选粉机,与史密斯ATOX型采用的SEPAX型不同的地方有:
笼形转子上无水平隔环,但外围的静态叶片倾角可调,调整机构设在机壳顶部。
磨机运转时也可通过人工转动调整机构改变叶片倾角,有利于根据需要辅助动态叶片调整产品细度。
粗粉漏斗出口设分流板,使粗粉朝两个粉尘浓度较低区域下落。
用于磨煤的RMK立磨的选粉装置其粗粉锥斗,还设计成剖分组合式,有利于维修选粉装置时,将两半锥斗绕销轴向两边分开,方便维修操作。
每台立磨由两台外部提升机共同负责提升由吐渣口排出的外部循环物料,然后分别送入机壳顶部两个回料进口,进入选粉装置的撒料盘或直接进入立磨,进行外部再循环粉磨。
进料口锁风喂料装置是由叶轮式机械传动喂料阀均匀喂入物料,该喂料阀既可调节喂料量又可实现泄漏风量的最小化。
并设计成用热风对粗料喂料阀中心加热,和热风通入溜管夹层加热的结构,有利于防止水份大的物料在喂料阀中和溜管中粘结堵塞。
吐渣口装有重力式锁风阀门。
传动装置中设辅助传动,因为磨辊不能由液力拉杆抬起。
LM型立磨
该磨为西德莱歇(Loesche)公司技术并制造。
国内引进使用的莱歇磨分两类:
一类是由日本宇部(UBE)公司和西德莱歇公司通过技术合作而制造的宇部-莱歇磨,即UBE公司制造的LM型系列;另一类是由美国福勒(Fuller)公司与西德莱歇公司订合同,获准生产的莱歇磨,即Fuller公司制造的LM型系列,其主要结构基本相同。
大型莱歇磨为4辊式,(低于150t/h产量的型号为两个辊子)。
是锥台型磨辊和平面轨道磨盘,无辊架。
磨辊与磨盘间的压力由相应辊数的液压拉伸装置提供。
工作时,通过摇臂作为一个杠杆,把油缸对拉伸杆产生的拉力传递给磨辊,进行碾磨。
最大的特点是,液压拉伸杆可通过控制抬起磨辊,使拖动电机所需的起动转矩减至最小值。
因而可使用具有70%或80%起动转矩的普通电动机,无辅传。
还设有液压式磨辊翻出装置以简化维修工作。
检修时,只要与液压装置相连,即可使磨辊翻出机壳外,可使磨辊皮更换在一天内完成。
液压控制杆在磨机外部,不需要空气密封,但是当磨辊在粉磨位置时,辊子的气封必须保持抵住磨内500mmH2O的负压,以防止过量含尘气体渗入轴承。
35000tpd熟料线原料立磨(MLS型)操作管理
3.1操作指导思想
3.1.1在各专业人员及现场巡检人员的密切配合下,根据入磨物料水份、粒度、差压、出入口温度、系统风量等参数状况,及时调整磨机的喂料量和各挡板开度,努力做到立磨运行平稳,提高粉磨效率。
3.1.2树立“安全生产,质量第一”的观念,精心操作,不断总结。
根据生产实际情况,充分利用计量监测仪表,计算机等先进的技术手段整定出最佳操作参数,实现优质、稳产、高效、低耗,长期安全文明生产。
3.2开磨前的准备工作
3.2.1通知PLC人员将DCS投入运行。
3.2.2通知总降做好上负荷准备。
3.2.3通知电气人员给不备妥设备送电。
3.2.4通知质量控制人员及调度准备开机。
3.2.5通知现场巡检工做好开机前的检查工作,并与其保持密切联系。
3.2.6进行联锁检查,对不符合运转条件的,要找有关人员进行处理。
3.2.7检查各挡板,闸阀是否在中控位置,动作是否灵活可靠。
中控显示与现场显示是否一致,若不一致要找相关人员校正。
3.2.8查看配料站各仓料位情况。
3.2.8查看启停组有无报警或不符合启动条件,应逐一找出原因进行处理,直到启停组备妥。
3.3热风炉开磨操作
3.3.1烘磨
联系现场确认柴油罐内要有合适的油位,如果是新磨的首次开磨,烘磨时间要长,一般2小时左右,且升温速度要慢和平稳,磨出口温度控制在80~90℃。
升温前先启动窑尾EP风机,将旁路风阀门关闭,调节EP风机、磨出口和入口挡板,点火后可稍加大抽风。
现场确认热风炉点着后,通过调节给油量、冷风挡板来达到合适的风量和风温。
鉴于生料粉是通过窑尾电收尘进行收集,热风炉点火时,窑尾电收尘不能荷电,火点着后一定要保证油能充分燃烧,不产生CO,这时窑尾电收尘才可荷电。
3.3.2布料
利用热风炉首次开磨时,应对磨盘上进行人工铺料。
具体方法是:
A.可以从入磨皮带上通过三道锁风阀向磨内进料,然后进入磨内将物料铺平。
B.直接由人工从磨门向磨内均匀铺料。
铺完料后,用辅助传动电机带动磨盘慢转,再进行铺料,如此反复几次。
从而确保料床上物料被压实,料层平稳,最终料层厚度控制在80~100mm左右。
同时也要对入磨皮带进行布料。
即先将“取消与磨主电机的联锁”选择项选择,然后启动磨机喂料,考虑到利用热风炉开磨时,风量和热量均低,可将布料量控制在120~140t/d左右,入磨皮带速度以25%运行,待整条皮带上布满物料后停机。
3.3.3开磨操作
当磨机充分预热后,可准备开磨。
启动磨机及喂料前,应确认粉尘输送及磨机辅助设备已正常运行,磨机水电阻已搅拌,辅传离合器已合上等条件满足。
给磨主电机,喂料和吐渣料组发出启动命令后,辅传电机会先带动磨盘转运一圈,时间1分钟58秒,在这期间加大窑尾EP风机阀门挡板至60~70%左右,保证磨出口负压控制在5500~6500Pa左右,磨出口阀门全开,入口第一道热风阀门挡板全关,逐渐开大热风挡板和冷风阀门。
如果系统有循环风阀门应全开,待磨主电机启动后入磨皮带已运转,这时可设定65~75%皮带速度,考虑到热风炉的热风量较少,磨机台时喂料量可控制在250~300t/d左右,开磨后热风炉的供油量及供风量也同步加大,通过热风炉一、二次风的调节,使热风炉火焰燃烧稳定、充分。
由于入磨皮带从零速到正常运转速度需要将近10秒钟时间,导致磨内短时间料子少,具体表现在磨主电机电流下降至很低,料层厚度下降,振动大,处理不及时将会导致磨机振动跳停。
这时可采取以下几种措施解决:
A.磨主电机启动前10~20秒,启动磨喂料,但入磨皮带速度应较低。
B.可先提高入磨皮带速度至85%左右,待磨机
稳定后再将入磨皮带速度逐渐降下来。
C.开磨初期减小磨机通风量,待磨机料层稳定后再将磨机通风量逐渐加大。
3.3.4系统正常控制
磨机运转后,要特别注意磨主电机电流、料层厚度、磨机差压、磨出口气体温度、振动、磨出入口负压等参数。
磨主电机电流在270~320A,料层厚度在80-100mm,磨机差压在5000~6000PA,磨出口气体温度60-80°C,振动在5.5~7.5mm/s,张紧站压力在8.0~9.5Mpa.
3.3.5停机
3.3.5.1停止配料站各个仓的进料程序,如果是长期停机要提前准备,以便将配料站各仓物料尽量用完。
3.3.5.2停止磨主电机、喂料和吐渣组。
3.3.5.3关小热风炉供油量及供风量,如果是长期停机应将热风炉火焰熄灭,减小窑尾EP风机冷风阀,磨进口阀门开度,保证磨内有一定通风即可。
3.4窑尾废气开磨(窑喂料量≥200t/h)
3.4.1烘磨
利用窑尾废气烘磨时,控制两旁路风阀门在60~80%左右,打开磨进出口阀门保证磨内通过一定热风量,烘磨时间控制在30~60分钟左右,磨出口温度控制在80~90°C左右,如磨机为故障停磨时间较短,可直接开磨。
3.4.2开磨操作
开磨前需掌握磨机的工况:
磨内是否有合适的料层厚度,入磨皮带是否有充足的物料,如果料少,可提前布料。
启动磨主电机,磨喂料和吐渣料循环组,组启动命令发出后,加大窑尾EP风机入口阀门至85~95%左右,保证磨出口负压控制在6500~7500Pa左右,逐渐关小两旁阀门至关闭,逐渐打开磨出口阀门和两热风阀门直至全部打开,冷风阀门可调至20%左右开度(以补充风量)。
在磨主电机启动前,上述几个阀门应动作完成。
但不宜动作太早,从而导致磨出口气体温度过高。
立磨主电机,喂料和吐渣循环组启动后,即可给入磨皮带输入65~75%速度,喂料量控制在340~380t/h左右,并可根据刚开磨时磨内物料多少,调节入磨皮带速度,喂料量,选粉机转速,磨机出口挡板等各种控制参数,使磨机状况逐渐接近正常。
根据磨进出口气体温度高低来决定是否需要开启磨机喷水系统。
针对增湿塔工艺布置位置不同,启动磨机时控制磨出口温度方法也有所不同,当增湿塔位置在窑尾高温风机之前,由于进磨热风已经过增湿塔喷水的冷却,故进磨气体温度较低在250°C左右,相应磨进出口气体温度也低。
如果增湿塔位置在高温风机之后,从而导致进磨热气没有经过冷却,气体温度在310~340°C左右,这时需启动磨机喷水来控制磨出口温度。
3.4.3系统正常控制
主要参数控制:
磨主电机电流在300~380A,料层厚度在100~120㎜,磨机差压在6500~7500Pa,磨机出口气体温度在80~95°C,磨机喂料量在380~450t/h,张紧站压力在8.0~9.5Mpa,振动在5.5~7.5mm/s。
磨机正常操作,主要从以下几个方面来加以控制:
A.磨机喂料量
立磨在正常操作中,在保证出磨生料质量的前提下,尽可能提高磨机的产量,喂料量的调整幅度可根据磨机振动、出口温度、系统风量、差压等因素决定,在增加喂料量的同时调节磨内通风量。
B.磨机振动
振动是磨机操作中一重要参数,是影响磨机台时产量和运转率的主要因素,操作中力求振动平稳。
振动与诸多因素有关,单从中控操作的角度来讲注意以下几点:
a.磨机喂料要平稳,每次加减幅度要小,加减料速度中。
b.防止磨机断料或来料不均。
如来料突然减少,可提高入磨皮带速度,关小出磨挡板。
c.磨内物料过多,特别是粉料过多,要及时降低入磨皮带速度和喂料量,或降低选粉机转速,加强磨内拉风。
C.磨机差压
立磨在操作中,差压的稳定对磨机的正常工作至关重要,它反映磨机的负荷。
差压的变化主要取决于磨机的喂料量、通风量、磨机出口温度。
在差压发生变化时,先查看配料站下料是否稳定,如有波动查出原因后通知相关人员处理,并做适当调整,如果下料正常可通过调整磨机喂料量、通风量、选粉装置转速、喷水量来调节。
D.磨机出口温度
立磨出口温度对保证生料水分合格和磨机稳定具有重要的作用,出口温度过高(>95°C),料层不稳,磨机振动加大,同时不利于设备安全运转。
出口温度主要通过调整喂料量、热风阀门、冷风阀门及磨机和增湿塔喷水量等方法控制。
E.出磨生料水份和细度
对于生料水份控制指标<0.5%,为保证出磨生料水份达标同,可根据喂料量、磨进出口温度,入磨生料水份等情况通过调节热风量和磨机喷水量等方法来解决。
对于生料粉细度可通过调节选粉机转速,磨机通风量和喂料量等方法解决。
若细度或水份超标,要在交接班记录本上分析造成原因及纠正措施。
3.4.4停机
正常停机时,可先停止磨主电机、喂料及吐渣组,同时打开旁路风阀门,调小窑尾EP风机入口、磨出口和进口阀门,全部打开冷风阀门,开启或增大增湿塔喷水。
停止配料站相关料仓供料。
3.5故障停窑后磨机维持运行的操作
鉴于大部份生产厂窑的产量受生料供应的影响较大,为延长磨的运转时间,停窑后可维持磨的运行。
当窑系统故障停机时,由于热风量骤然减小,这时应及时打开冷风阀门,适当减小EP风机挡板开度,停止喷水系统,关闭旁路风阀门,大幅度减小磨机喂料量到250~300t/h左右,从而保证磨机状况稳定。
为防止进入窑尾高温风机气流温度过高,可适当打开高温风机入口冷风阀,高温风机入口挡板可根据风机出口温度和出磨温度进行由小到大调节。
保证高温风机入口温度在450°C以下,出磨温度高于40°C。
当窑系统故障恢复投料时,应做好准备,及时调整,避免投料时突然增大的热风对磨机的冲击。
即:
在投料