模具毕业设计71糖果盒盖模具设计.docx
《模具毕业设计71糖果盒盖模具设计.docx》由会员分享,可在线阅读,更多相关《模具毕业设计71糖果盒盖模具设计.docx(26页珍藏版)》请在冰豆网上搜索。
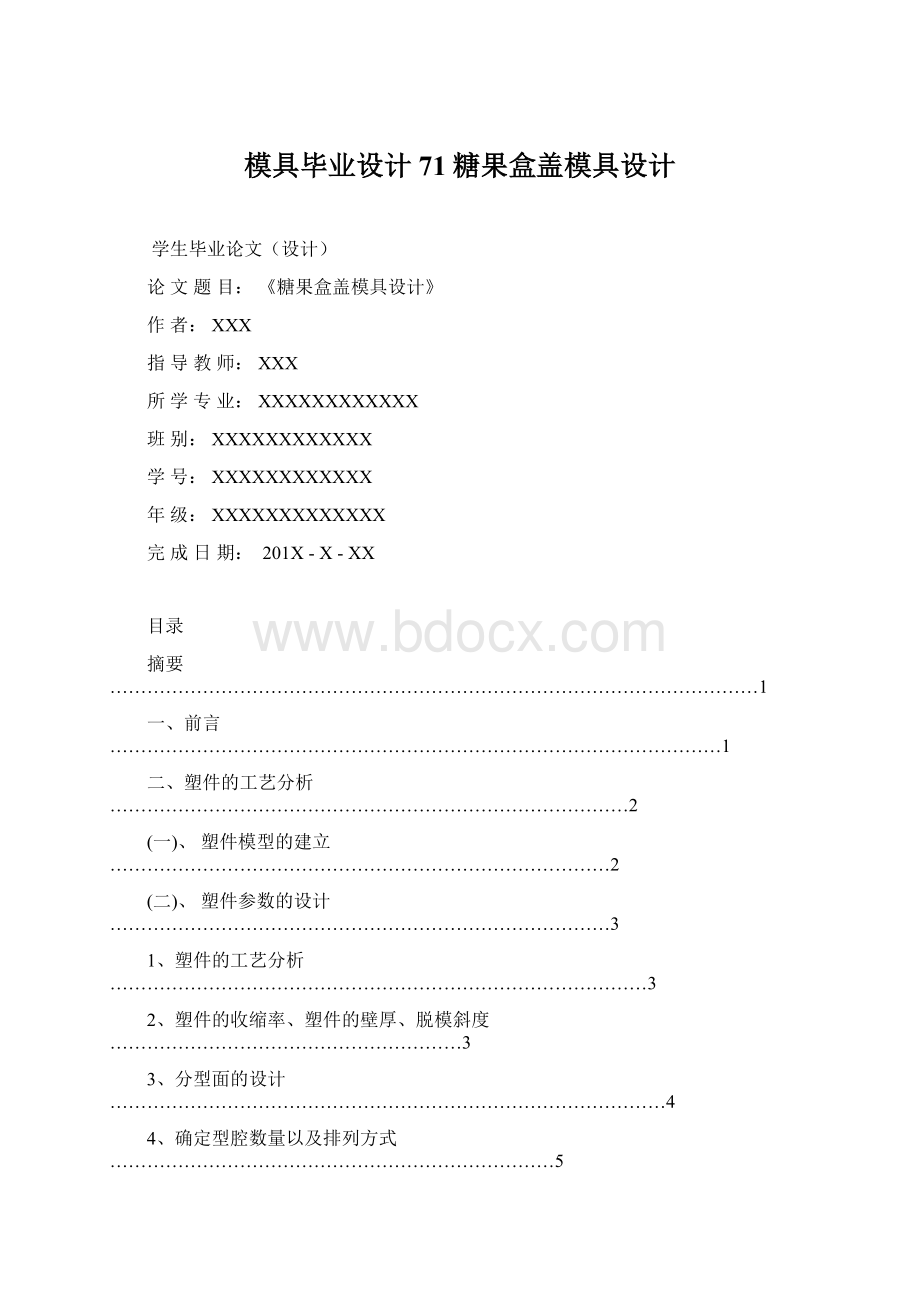
模具毕业设计71糖果盒盖模具设计
学生毕业论文(设计)
论文题目:
《糖果盒盖模具设计》
作者:
XXX
指导教师:
XXX
所学专业:
XXXXXXXXXXXX
班别:
XXXXXXXXXXXX
学号:
XXXXXXXXXXXX
年级:
XXXXXXXXXXXXX
完成日期:
201X-X-XX
目录
摘要……………………………………………………………………………………………1
一、前言………………………………………………………………………………………1
二、塑件的工艺分析…………………………………………………………………………2
(一)、塑件模型的建立………………………………………………………………………2
(二)、塑件参数的设计………………………………………………………………………3
1、塑件的工艺分析……………………………………………………………………………3
2、塑件的收缩率、塑件的壁厚、脱模斜度…………………………………………………3
3、分型面的设计………………………………………………………………………………4
4、确定型腔数量以及排列方式………………………………………………………………5
三、塑料工艺参数的编制………………………………………………………………………6
(一)、塑件注射工艺参数的确定………………………………………………………………6
1、查表填写原材料的注射工艺参数…………………………………………………………7
2、查表填写塑件模塑的工艺卡………………………………………………………………7
四、模具的结构设计………………………………………………………………………………8
(一)、浇注系统的设计……………………………………………………………………………8
(二)、成型零件的设计……………………………………………………………………………11
(三)、顶出机构设计………………………………………………………………………………11
(四)、冷却系统设计………………………………………………………………………………14
(五)、导向机构设计………………………………………………………………………………17
(六)、排气系统设计………………………………………………………………………………18
五、注塑成型设备的选择……………………………………………………………………………18
(一)、计算塑件、浇注系统的体积………………………………………………………………18
(二)、塑件质量的计算……………………………………………………………………………18
(三)、选择注塑机的类型和型号…………………………………………………………………19
六、模架的选择及校核……………………………………………………………………………20
七、模具装配图和零件图…………………………………………………………………………23
致谢…………………………………………………………………………………………………24
参考文献……………………………………………………………………………………………24
摘要本文是通过对糖果盒盖进行形状尺寸分析、工艺分析以及工艺方案的确定;根据这些分析来进行注射模具的设计,确定注塑方案和模具结构形式,工作零件设计与模架选择;并对成型工艺等多方面分析,通过对工艺计算,制定正确加工方案,并对模具的所有成型零部件进行验证及校核;最后根据设计来进行选择注塑机以及绘制模具零件图和装配图。
关键词注塑模成型工艺形状尺寸注塑
一、前言
中国是制造业大国,产品是制造业的主体,模具是制造业的灵魂,模具的发展水平决定了制造业的发展水平。
随着塑料的广泛使用直接带动了注塑模的飞速进步和发展。
从市场情况来看,塑料模具生产企业应重点发展那些技术含量高的大型、精密、复杂、长寿命模具,并大力开发国际市场,发展出口模具。
随着世界的塑料工业,特别是工程塑料的高速发展,可以预见,塑料模具的发展速度仍将继续高于模具工业的整体发展速度,未来几年年增长率仍将保持上升的水平。
根据国内和国际模具市场的发展状况,有关专家预测,未来我国的模具经过行业结构调整后,将呈现十大发展趋势:
一是模具日趋大型化;二是模具的精度将越来越高;三是多功能复合模具将进一步发展;四是热流道模具在塑料模具中的比重将逐渐提高;五是气辅模具及适应高压注射成型等工艺的模具将有较大发展;六是模具标准化和模具标准件的应用将日渐广泛;七是快速经济模具的前景十分广阔;八是压铸模的比例将不断提高,同时对压铸模的寿命和复杂程度也将提出越来越高的要求;九是塑料模具的比例将不断增大;十是模具技术含量将不断提高,中高档模具比例将不断增大,这也是产品结构调整所导致的模具市场未来走势的变化
由于塑模生产领域计算机应用的独特优势,以三维模型为基础的以CAD/CAM/CAE技术为代表的模具计算机应用的集成化生产模式获得了快速的发展和进步。
模具CAD/CAM/CAE技术的广泛应用,显示了用信息技术带动和提升模具工业的优越性。
在欧美,模具CAD/CAM/CAE技术已成为模具企业普遍应用的技术。
在CAD的应用方面,已超越了甩掉图板、二维绘图的初级阶段,目前3D设计已达到了70%~89%。
PRO-E、UG、CIMATRON等软件的应用很普遍。
应用这些软件不仅可完成2D设计,同时可获得3D模型,为NC编程和CAD/CAM/CAE的集成提供了保证。
应用3D设计,还可以在设计时进行装配干涉的检查,保证设计和工艺的合理性。
CAE技术在欧美已逐渐成熟。
在塑料模设计中应用CAE分析软件,模拟塑料的充模过程,分析冷却过程,预测成形过程中可能发生的缺陷。
因此,在未来的模具市场中,塑料模具在模具总量中的比例将逐步提高,且发展速度将高于其他模具。
1
二、塑件的工艺分析
(一)、塑件模型的建立
塑件2D如图1所示:
塑件名称
糖果盒盖
材料
PS
厚度
上壁2侧壁1
工件精度
5
图1
塑件3D如图2所示
2
(二)、塑件参数的设计
1、塑件的工艺分析
(1)、塑件的质量,不仅与模具结构和成型工艺参数有很大的关系,而且还取决与塑件本身和结构设计是否符合工艺要求。
该塑件规定采用PS材料,化学和物理特性大多数商业用的PS都是透明的、非晶体材料。
PS具有非常好的几何稳定性、热稳定性、光学透过特性、电绝缘特性以及很微小的吸湿倾向。
它能够抵抗水、稀释的无机酸,但能够被强氧化酸如浓硫酸所腐蚀,并且能够在一些有机溶剂中膨胀变形。
密度为1.04g/cm3。
典型用途产品包装,家庭用品(餐具、托盘等),电气(透明容器、光源散射器、绝缘薄膜等)。
(2)、塑件的尺寸分析
这里尺寸是指塑件的总体尺寸,而不是指避厚,孔径等结构尺寸。
塑件的尺寸精度是指所获得的塑件与产品图中的尺寸行使程序,即所获得的尺寸的准确度。
塑料尺寸的大小与塑料的流动性有关。
注射成型的塑件尺寸还要受到注射机的注射量、锁模力和模板模板尺寸的限制。
(3)、塑件的精度分析
根据使用要求确定尺寸公差,一般配合部分尺寸精度高于非配合部分尺寸精度。
该工件精度为5,该标准塑件尺寸公差的代号为M5公差等级为5级。
(4)、塑件的表面粗糙度分析
塑件的外观要求越高,表面粗糙度值越低。
塑件表面粗糙的高低,主要取决于模具型腔表面粗糙度。
一般来模具表面粗糙度值比塑件的粗糙度值低1~2级。
塑件的表面粗糙度可参照《GB/T14234-1993塑料件表面粗糙度标准》选取,一般Ra1.6~0.2um之间,而PS的粗糙度值为Ra3.2。
2、塑件的壁厚、塑件的收缩率、脱模斜度。
塑件壁厚大小主要取决于塑料品种、制品大小以及注塑工艺条件。
热塑性塑料易于成型薄壁制品,壁厚可小至0.25mm,但一般不宜小于0.6~0.9mm,常选取2~4mm。
塑件要求厚度:
上外壁2,侧壁为1。
查表可得PS的收缩率为1.0060。
,PS的脱模斜度为35’~1°。
3
3、分型面的设计
为将塑件从密闭的模腔内取出,以及为了安放嵌件或取出浇注系统等,必须将模具分成两个或几个部分,一般将分开模具能取出塑件的面称为分型面。
分型面的选择是一个比较复杂的问题,因为它受到塑件的形状、壁厚、尺寸精度、表面粗糙度、嵌件位置几其形状、塑件在模具内的成型位置、顶出方法、浇注系统的设计,模具排气,模具制造及操作等各种因素的影响。
因此,在选择时要认真分析、综合比较,从几个方案中找出一个比较合理的方案。
分型面是模具动模和定模的结合处,在塑件最大形处,是为了塑件和凝料取出而设计的。
分型面的方向尽量与注塑成型机开模方向垂直的方向,特殊情况下采用与注塑成型机开模方向平行的方向。
分型面有单分型面和双分型面之分。
分型面选择的原则:
分型面应选择在塑件外形的最大轮廓处;分型面的选取应有利于塑件的留模方式,便于塑件顺利脱模,一般都应尽可能留在动模部分;保证塑件的精度要求;满足塑件外观的要求;便于模具的制造;减少成形面积;增强排气效果。
由于本产品的分型面简单,所以采用单分型面。
分型面如图3所示
图3
4
4、确定型腔数量以及排列方式。
本产品是要大量生产,设计是采用多型腔注射模具的,所以采用了一模两腔的方式。
多型腔模具型腔的分布有平衡式排布和非平衡式排布两种,其中平衡式排布的要求是从主流道到各个型腔分流道的长度、形状、断面尺寸分布对称性对应相等,可实现各型腔均匀进料和达到同时充满型腔的目的;而非平衡式与之相反,一般以平衡式排布。
排布如图4所示。
图4
5
三、塑料工艺参数的编制
(一)、塑件注射工艺参数的确定
(1)、查表填写原材料的注射工艺参数(以下参数是根据《注塑模具设计》表1-1)
`
ABS
注射机类型
螺杆式
螺杆转速/(r/min)
30~60
喷嘴
形式
直通式
温度/oC
170~180
料筒温度/oC
前段
150~170
中段
165~180
后段
180~200
模具温度/oC
50~80
注射压力/Mpa
60~100
保压压力/Mpa
50~70
注射时间/s
20~90
保压时间/s
0~5
冷却时间/s
20~120
总周期/s
50~220
6
(2)、查表填写塑件模塑的工艺卡
塑料注射成型工艺卡
资料编号
车间
共页
第页
零件名称
椭圆瓶盖
材料牌号
ABS
设备型号
装配图号
材料定额
每模件数
零件图号
单件重量
4.54g
工装号
材料干燥
设备
温度/ºC
80~85
时间/h
2~3
料筒温度
(ºC)
后段/ºC
180~200
中段/ºC
165~180
前段/ºC
150~170
喷嘴/ºC
170~180
模具温度/ºC
50~80
时间
注射
20~90
保压
0~5
冷却
20~120
压力
注射压力
/Mpa
60~100
背压
/Mpa
后处理
温度/ºC
70
时间定额
辅助/min
时间/h
2~4
单件/min
检验
编制
校对
审核
组长
车间主任
检验组长
主管工程师
7
四、模具的结构设计
(一)、浇注系统的设计
浇注系统是指模具中从喷嘴开始到型腔为止的塑料熔体的流动通道。
它的作用是将塑料溶体顺利地充满到型腔的各个深处,并在填充及凝固过程中,将注射压力传递到型腔的各个部位,以获得外形清晰的内在质量优良的塑件。
浇注系统其组成部分有:
主流道、分流道、浇口和冷料穴等四部分。
注射模浇注系统的组成如图5所示。
图5
浇注系统的设计是注塑模设计的一个很重要的环节,它对注塑成型的效率和塑件质量都有直接的影响,因此,在设计浇注系统时必须注意几项原则。
1.了解塑料的成型特性;
2.防止型芯和塑件的变形;
3.排气良好;
4.减少流程及塑料消耗;
5.修整方便,保证塑件外观质量。
主流道是指从喷嘴起至分流道入口处止的一段通道,它与注塑机喷嘴在同一轴心线上,熔料在主流道中并不改变方向。
主流道是熔体最先经流模具的部分,它的形状与尺寸对塑料熔体的流动速度和充模时间有较大的影响,因此,必须使熔体的温度降和压力损失最小。
其作用是其截面尺寸直接影响到塑件的流动速度和填充时间。
8
为了便于塑料从主流道中拉出,主流道设计成圆锥形,其锥角a=2°~6°,内壁粗糙度Ra应为0.36,主流道大端处呈圆角,其半径常取r=1~3mm,以减小料流转向过度时的阻力。
主流道要和注塑机的喷嘴紧密对接,主流道对接处设计成半球形凹坑,其半径R2=R1+(1~2mm),其小端直径d1=d2+(0.5~1mm),凹坑深度常取3~5mm.所以需对塑件的成形过程及对选用的模架分析,选择主流道。
其衬套的固定用定位圈配合固定在模具的定模座板上。
主流道衬套和注塑机喷嘴的配合如图6所示。
图6
分流道是指主流道与浇口之间的部分,是指塑料熔体从主流道进入多腔模的各个型腔多处进料的通道,起分流和转向的作用。
分流道的要求是塑料熔体在流动中热量和压力损失最小,同时是流道中的塑料量最小。
分流道的长度应尽量可能短,且弯折少,以便减少压力损失和热量损失,节约塑料的原材料和能耗。
常用的分流道的截面形状有圆形、梯形、U形、和六边形等。
流道的截面积越大,压力的损失越小;流道的表面积越大,热量的损失越小。
可知截面形状为圆形的分流道热量损失小、流动阻力小、效果最佳。
圆形截面分流道的直径一般在2~12mm的范围内变动,但对多数塑料来说,分流道直径在5~6mm以下时,对流动性影响较大。
ABS的流动性属于中等,受温度变化较大,分流道直径取5mm。
分流道表面粗糙度一般为1.25即可,分流道只设计在型腔的一面,故采用截面形状为对半圆形的分流道。
对半圆分流道其深度为0.45d=0.45×5=2.25mm。
9
分流道如图7所示。
图7
浇口是指流道末端与型腔之间的细短通道,亦称内浇口,它是浇注系统中断面尺寸最小且最短的部分。
其作用是:
浇口通过截面积的突然变化,使分流道送来的塑料熔体提高注射压力,使塑料熔体通过浇口的流速有一突变性增加,提高塑料熔体的减切速率,降低黏度,使其成为理想的流动状态,从而迅速均衡地充满型腔。
对于多型腔模具,调节浇口的尺寸,还可以使非平衡布置的型腔达到同时进料的目的;浇口还起着较早固化、防止型腔中熔体倒流的作用;浇口通常是浇注系统最小截面部分,还有利于在塑件的后加工中塑件与浇口凝料的分离。
设计里使用侧浇口,侧浇口又称边缘浇口,一般开在分型面上,从塑件侧面进料。
它方便的调整冲模的剪切速率和浇口封闭时间,因此国外称之为标准浇口,它是广泛使用的浇口形式。
侧浇口使用于一模多件,能大大提高效率,减少浇注系统的消耗量。
侧浇口是典型的矩形浇口,一般取宽1.5~5mm,厚0.5~2mm,长0.7~2mm。
冷料穴是用来储藏注塑间隔期内由于喷嘴端部温度低造成的冷料,因冷料进入型腔会影响塑件质量。
注塑模的冷料穴,一般都设置在主流道的末端,即主流道正对面的模板上,直径宜稍大于主流道大端直径,以利于冷料流入。
冷料穴并非所有注塑模都需要开设。
有时由于塑料的性能和注塑工艺的控制,很少产生冷料,或是塑件要求不高,以及模具本身结构即浇注系统的不同形式,可以不设置冷料穴。
10
(二)、成型零件的设计
构成模腔的成型零件包括型腔和型芯以及各种活动镶件等。
成型零件工作时,直接与塑料接触,承受塑料熔体的高压、料流的冲刷,脱模时与制品间还要发生摩擦。
因此,成型零件要求有正确的几何形状,较高的尺寸精度和较低的表面粗糙度;此外,成型零件还要求结构合理,有较高的强度、刚度及较好的耐磨性能。
(1)型腔
型腔是成型塑件制品外表面的主要零件,按其结构不同,可分为整体式和组合式两类。
所以,此处采用式组合式凹模。
型腔设计见凹模零件图附件
(2)型芯
型芯是成型塑件内表面的零件。
主要有主型芯和小型芯。
对于简单的容器,如壳、罩、盖之类的塑件,成型其主要部分内表面的零件称主型芯,而将成型其他小孔的型芯称为小型芯或成型杆。
按结构主型芯可分为整体式和组合式两种。
此处采用组合式。
型芯设计见凸模零件图附件
(三)、顶出机构设计
在塑料成型模具中,完成将塑件从模具型腔或型芯上完整的取出的装置称为顶出机构,即脱模机构。
顶出机构一般由顶出、复位和顶出导向等三大零部件组成。
顶出机构的设计规则:
1、尽量设法使塑件留于动模;
2、保证塑件不变形不损坏完整脱出;
3、尽量不损坏塑件的外观;
4、结构可靠;
5、每副模具的推杆的直径相同,方便加工;
6、塑件推出模具10mm左右,对型腔斜度较大者,顶出塑件深度2/3即可。
11
顶出力的计算:
将塑件从抱紧的芯上推出所需克服的阻力称为脱模力。
脱模力主要是由于塑件收包紧型芯而造成的塑件与型芯的摩擦阻力,而对于不带通孔的壳体类塑件,脱模时,大气压力也是脱模阻力的一大组成部分,而本次设计有通孔,故可不计
大气压力。
单个塑件所需的脱模力为:
F
=AP(
cos
-sin
)
=0.013x1.2x107x(0.2-0.017)
=28548N
所以两个塑件所需的脱模力为57096N
式中:
F
——脱模力(N);
——塑料对模具钢的摩擦系数,约为0.1~0.3,此处
取0.2
——脱模斜度,
为30′~1°,此处取1°;
A——塑件包容型芯的面积(m
);
P——塑件对型芯单位面积上的包紧力,一般情况下,模外冷却
塑件P约取(2.4~3.9)×10
Pa;模内冷却的塑件P约取(0.8~1.2)×10
Pa。
推出机构的类型分为一级顶出机构、二级顶出机构。
其中一级顶出机构又可分为顶杆顶出机构、顶管顶出机构、推板顶出机构、顶块顶出机构、气压顶出机构、成型镶件和型腔顶出。
本次设计是使用单分型面,且塑件可一次推出,所以采用一级顶出机构中的顶杆顶出机构。
顶杆顶出机构是顶出机构中最简单、最常见的一种形式。
由于顶杆截面多为圆形,制造、修配方便、顶出效果好,因此在生产中广泛应用。
有于设置推杆的自由度较大,而且推杆截面大部分为圆形,容易达到推杆与模板或型芯上推杆孔的配合精度,推杆推出时阻力小,推出动作灵活可靠。
而推出零件固定板即推杆固定板,则与推杆一起运动,将塑件顶出型芯。
12
单个塑件推杆的根数及直径可通过以下公式计算并校核。
D=K[64F脱(uL)2/Nπ2E]0.25
式中:
D——推杆直径,mm;
K——安全系数,可取1.4~1.8,此处取1.6;
F脱——脱模力,N;
u——摩擦系数,一端固定时u为0.7,两端固定时u为0.5,此处取0.7;
L——推杆长度,mm;
N——推杆根数;
E——稳定系数,此处取5×106。
若N为2,则
D=K[64F脱(uL)2/Nπ2E]0.25
=1.6×[64×28548×(0.7×128)2/2×3.142×5×106]0.25
=4.6mm
所以本设计中推杆直径采用5mm符合要求。
若D为5,则
N=64F脱(uL)2/[(D/K)4π2E]
=64×28548×(0.7×128)2/[(5/1.6)4×3.142×5×106]
=1
所以本设计中单个塑件所需的推杆根数为2符合要求,所以总共有4根推杆。
推杆应力校核:
[б]=4K2F脱/D2Nπ=4×1.62×28548/62×2×3.14=1293N/cm2。
而推杆的许用应力为32000N/cm2。
故符合要求。
13
推出机构的导向与复位
为了保证推出机构在工作过程中灵活、平稳,推出机构需要设计导向装置;而在每次合模后,推出机构要回到原来的位置上,以组成完整的型腔,推出机构需要设计复位装置。
导向机构可以保证推板在座板和动模垫板之间的推出和复位,防止推板的重量全由推杆来承受而使推杆变形和折断。
设计复位装置是因为推出机构在开模推出塑件后,为下一次的注射成型座准备,以便恢复完整的模腔。
复位装置的类型有复位杆复位装置和弹簧复位装置。
本次设计采用复位杆复位装置。
(四)、冷却系统设计
模具冷却装置的设计与使用的的冷却介质、冷却方法有关。
冷却介质最普遍的是用水冷却,因为水的热容量大,传热系数大,成本低廉。
冷却回路的设计应做到回路系统内流动的介质能充分吸收成形塑件所传导的热量,使模具成形表面的温度稳定地保持在所需的温度范围内,并且要做到使冷却介质在回路系统内流动畅通,无泄留部位。
(1)、冷却回路所需的总表面积计算
冷却回路所需总面积可按下式计算
A=Mq/3600
(θ1-θ2)
式中
——冷却回路总表面积,
——单位时间内注入模具中树脂的质量,kg/h;
——单位质量树脂在模具所内释放的热量,J·kg,
值查表得4×105J·kg;
——冷却水的表面传热系数,
/(
·k);
θ1——模具成形表面的温度,ºC;
θ2——冷却水的平均温度,ºC。
14
(2)、冷却水的表面传热系数
可以以下公式计算
=
(pv)0.8/d0.2
式中
——冷却水的表面传热系数,
/(
·k);
——冷却水在该温度下的密度,kg/m3;
v——冷却水的流速,m/s;
d——冷却水孔直径,m;
——与冷却水温度有关的物理系数。
经查表及计算可得,单位时间内注入模具中树脂的质量
为77.76kg/h,模具成形表面的温度θ1为50ºC,冷却水的平均温度为25ºC,冷却水在该温度下的密度
为1000kg/
,冷却水的流速v为2m/s,冷却水孔直径d为0.006m,
为7.95。
所以
=
(
v)0.8/d0.2
=7.95X(1000X2)0.8/0.0060.2
=9673
/(
·k)
A=(77.76X4X105)/3600X9673X(50-25)=0.0357
3)、冷却回路的总长度计算
冷却回路总长度可用下式计算
=1000A/πd=1000x0.0357/3.14x6=1.895m
在设计和制造冷却系统的时候一般大于理论数值就可以了,而无需按照计算出来的尺寸来制造。
15
在设计冷却系统时,应遵循以下原则:
序号
原则
简图及说明
1
冷却水道可设计成单回路或多回路
冷却水道必须是一个回路,使水道中的水循环。
当水道较长时,随着水温的升高,模具的温度不均匀,可设计成多个回路
2
冷却水道应尽量多、截面尺寸应尽量大
图a的冷却水道为五个,直径较大,型腔的表面温度较均匀,温度在60~60.5°C之间;图b的冷却水道为两个,直径较小,型腔的表面温度不均匀,温度在53.33~58.38°C之间
3
冷却水道与型腔表面之间的距离应尽量相等
当塑件壁厚较均匀时,冷却水道与型腔表面之间的距离应相等;当塑件壁厚不均匀时,厚的地方,冷却水道与型腔表面之间的距离应近些,冷却水道的间距也应小些。
冷却水道的孔边与型腔表面之间的距离一般应大于10mm,常用12~15mm
4
冷却水道的入