日本模具工业的发展给中国模具企业的启迪.docx
《日本模具工业的发展给中国模具企业的启迪.docx》由会员分享,可在线阅读,更多相关《日本模具工业的发展给中国模具企业的启迪.docx(11页珍藏版)》请在冰豆网上搜索。
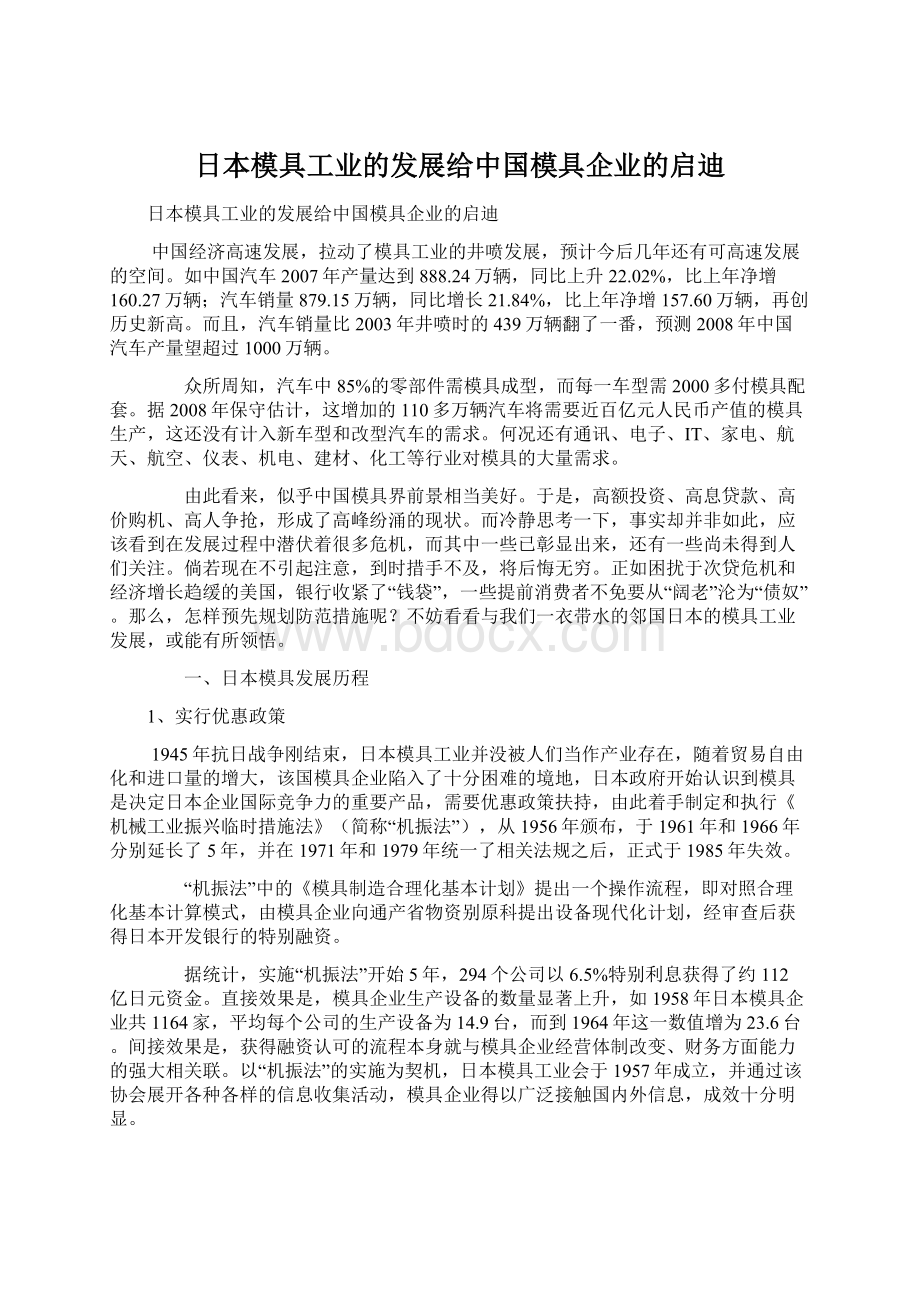
日本模具工业的发展给中国模具企业的启迪
日本模具工业的发展给中国模具企业的启迪
中国经济高速发展,拉动了模具工业的井喷发展,预计今后几年还有可高速发展的空间。
如中国汽车2007年产量达到888.24万辆,同比上升22.02%,比上年净增160.27万辆;汽车销量879.15万辆,同比增长21.84%,比上年净增157.60万辆,再创历史新高。
而且,汽车销量比2003年井喷时的439万辆翻了一番,预测2008年中国汽车产量望超过1000万辆。
众所周知,汽车中85%的零部件需模具成型,而每一车型需2000多付模具配套。
据2008年保守估计,这增加的110多万辆汽车将需要近百亿元人民币产值的模具生产,这还没有计入新车型和改型汽车的需求。
何况还有通讯、电子、IT、家电、航天、航空、仪表、机电、建材、化工等行业对模具的大量需求。
由此看来,似乎中国模具界前景相当美好。
于是,高额投资、高息贷款、高价购机、高人争抢,形成了高峰纷涌的现状。
而冷静思考一下,事实却并非如此,应该看到在发展过程中潜伏着很多危机,而其中一些已彰显出来,还有一些尚未得到人们关注。
倘若现在不引起注意,到时措手不及,将后悔无穷。
正如困扰于次贷危机和经济增长趋缓的美国,银行收紧了“钱袋”,一些提前消费者不免要从“阔老”沦为“债奴”。
那么,怎样预先规划防范措施呢?
不妨看看与我们一衣带水的邻国日本的模具工业发展,或能有所领悟。
一、日本模具发展历程
1、实行优惠政策
1945年抗日战争刚结束,日本模具工业并没被人们当作产业存在,随着贸易自由化和进口量的增大,该国模具企业陷入了十分困难的境地,日本政府开始认识到模具是决定日本企业国际竞争力的重要产品,需要优惠政策扶持,由此着手制定和执行《机械工业振兴临时措施法》(简称“机振法”),从1956年颁布,于1961年和1966年分别延长了5年,并在1971年和1979年统一了相关法规之后,正式于1985年失效。
“机振法”中的《模具制造合理化基本计划》提出一个操作流程,即对照合理化基本计算模式,由模具企业向通产省物资别原科提出设备现代化计划,经审查后获得日本开发银行的特别融资。
据统计,实施“机振法”开始5年,294个公司以6.5%特别利息获得了约112亿日元资金。
直接效果是,模具企业生产设备的数量显著上升,如1958年日本模具企业共1164家,平均每个公司的生产设备为14.9台,而到1964年这一数值增为23.6台。
间接效果是,获得融资认可的流程本身就与模具企业经营体制改变、财务方面能力的强大相关联。
以“机振法”的实施为契机,日本模具工业会于1957年成立,并通过该协会展开各种各样的信息收集活动,模具企业得以广泛接触国内外信息,成效十分明显。
总之,日本政府并不是一味局限于单方面出台措施,而是更侧重于引导企业,促进其增强核心竞争力。
鉴于此,日本模具工业获得了飞速发展,据国际模具协会1994年统计,1993年日本模具产值占到该年度世界模具总体产值的43.4%。
2、经济危机对模具企业的冲击
1985年“广场协议”以后,日元升值给日本经济带来了很大冲击。
日本制造业开始向东南亚各国进行产业转移以求降低成本,特别是1993年~1995年的第4次日元升值以后,日本中小模具企业因订单减少、模具价格下压等问题,深陷经营危机。
从1991年到2005年,苦于日本国内巿场需求减少以及中小企业经营者后继无人等原因,日本模具生产厂家及模具就业人数在15年间分别减少了28%和13%,模具产值也自1997年起呈现下滑(见表1、表2),衰退率达11%。
如1998年日本模具产值攀上18,700亿日元的高峰之后,2006年则降为4100亿日元。
从模具产业的毛利率也可以断定,日本中小模具企业无疑受到了产业空心化和产业集群瓦解的强大打击。
表一、日本模具产业的年产值(百万日元)
1985
1990
1993
1995
1997
1999
2001
2003
2004
2005
产值
386.710
467.354
405.328
417.989
506.755
437.614
413.085
384.088
412.263
439.274
冲压模
154.814
179.587
165.890
175.467
205.442
173.578
174.418
150.460
159.474
168.089
塑料模
151.340
185.293
159.787
163.188
201.522
178.538
158.136
153.414
171.052
168.089
资料:
日本经济产业省“机械统计”各年版(员7-20人以上的模具企业为统一对象)
表二、日本模具产业的年度数据
加工厂点
员工人数(人)
销售额(百万日元)
附加产值(百万日元)
1991年
7,496
106,521
1,844,439
1,074,637
1992年
7,178
103,185
1,631,069
935,434
1993年
7,133
99,890
1,446,360
841,068
1994年
6,448
92,687
1,300,881
760,045
1995年
6,762
93,831
1,418,132
818,433
1996年
6,515
96,626
1,582,165
915,285
1997年
6,508
97,254
1,726,633
963,708
1998年
7,090
103,441
1,786,539
991,551
1999年
6,451
100,482
1,544,639
853,059
2000年
6,536
101,482
1,592,125
863,764
2001年
6,536
101,482
1,592,123
863,764
2002年
5,984
96,528
1,488,416
829,975
2003年
5,618
92,429
1,389,326
760,623
2004年
5,810
93,768
1,479,840
822,426
2005年
5,402
92,806
1,551,002
853,990
资料:
日本通厂省“工业统计表”各年版(员工4人以上的模具企业为核计对象)
3、日本模具产业的转移和出路
随着日本大型制造企业如三菱、夏普、本田、丰田等向海外的产业大转移,日本模具企业为了生存和发展不得不向海外巿场扩张,采用在国外设置模具企业;或和当地企业合资;或发单给自己熟悉的模具企业等方式。
日本一些模具企业原本以为,模具加工技能的学习需长期技术积累,产业向海外转移并不至于被人轻易模仿。
然而,随着CAD/CAM技术水平的提升,以及数控加工设备的普及,加工工具和刀具设备加速进化。
结果,在一般普及型模具技术领域,出现了机械加工技术取代模具技能的趋势。
因此,中国、韩国的模具凭借价格优势加大了对日本的出口,在中低档技术含量的模具巿场上更已成为日本中小模具企业的主要竞争对手。
同时,伴随着日本模具出口的增加,日本模具企业在东南亚各国设立维修点、向产业转移地的模具企业提供模具图纸以实现模具配套本地化的过程中,也造成了模具技术的流失乃至部分模具巿场的丧失。
也正因为此,日本模具企业不得不致力于高档模具的生产和技术升级,以避开价格竞争。
那么,怎样的方法和模式才能提高竞争力呢?
皮欧尔和赛伯在《第二次产业分水岭》一书中曾指出,以美国为代表的大量生产、大量消费时代的结束,取而代之的是柔性的专业化生产方式,即弹性专精生产方式。
也即,以小而精、小而专的技术积累作为竞争力的源泉,促使中小模具企业不断创新,营造可持续发展的环境,其特点是柔性对应性和专业相结合,以熟练工人为主体,对先进的设备加工技术和传统加工工艺进行整合,采用多品种、少批量生产方式来提高竞争力。
日本模具产业在20世纪80年代,得益于采用ME化(MicroElectronies)和柔性的专业化生产方式,保持了高速成长态势。
同时,日本一些模具公司用光造形技术快速加工模具,克服了技能工人不足的问题,加之利用IT技术加工高精度和大型冲压模具等,这些都推进了柔性的专业化生产方式的落实。
从日本中小模具企业发展经验可以验证,柔性的专业化生产方式在产业发展和提高企业竞争力中起到了非常重要的作用。
二、中国模具发展中的问题
虽然我国的模具工业规模仅次于日本和美国,但大多模具集中在中低档领域。
制造业急需的精密、复杂、冲压模具和塑料模具,轿车覆盖件模具,电子接插件、电子产品模具等仍然大量依赖进口。
对于我国模具工业存在的诸多问题,目前多种报刊杂志上所列出的不外乎行业整体效率低下;专业化、标准化、商品化程度低;模具材料及模具相关技术落后;模具产品水平和生产工艺水平总体较差等,但当前迫切需要解决的主要问题究竟为何?
这正是本文需要探讨的重点。
1、管理意识不强,滞碍了企业发展
我国模具企业绝大多数是民营企业,有些地区几乎全部是民营企业,这导致家族型管理成为重要特徵。
有人为此总结道:
没有家族型管理就没有你现在的企业,如果只有家族型管理便没有你将来的企业。
说明家族型管理在模具企业起步阶段确实起到了一定作用。
在创业时,大多民营模具企业老总文化程度不高,企业又小,模具生产又有它的特殊性,所以家族型管理是适合的,也是不可避免。
但随着企业规模飞速扩大,人员增加、层次增多,矛盾突出,如果还停留在家族型管理上,就会严重阻碍企业发展,且不说无法发觉人才,利用能人,就是在管理层内部,由于亲戚间错综复杂的关系,扰乱你的视线,干扰你的思路,老总会陷入无法解决的矛盾漩涡之中。
何况家族型管理有排他性,在企业内部将产生离散力,这些因素对企业发展都是极为不利的。
管理是一种技术。
能产生较大的经济效益,模具企业在发展过程中不断地受到产品企业的苛求和压缩。
如何减低生产成本、缩短制造周期,一直是老总们思考的问题。
哟啊解决这问题,必须从管理上着眼,除了理顺管理体制,达到畅通、明捷外,起启用既懂模具又懂管理的职业经理人,一定要在现代管理理念、思路、方法山下功夫,采用先进的管理软件,结合企业管理经验,不断地开发和深化管理思路,以人为本,把企业建设成为一个和谐的大家庭。
2、创新意识不强,缺少核心竞争力
技术创新是企业核心竞争力的源泉。
按国家规定,每年至少有相当于3%产值的金额需作为科研开发和技术攻关的投入,唯此才能保证企业技术不断进步。
而我们的模具企业大多对此不甚重视,造成各个企业的技术特色难以形成,甚至基本上雷同,整个行业的技术裹足不前。
目前,我国每年的进口模具始终在20亿美元上下,即使每年的出口模具在大幅增长—─如2006年10.41亿美元、2007年上升35.73%达14.13亿美元—─但大多还是附加值不高的模具产品。
以劳动力廉价为背景,中国模具企业迈向国际巿场,但随着劳动合同新法实施和人民生活水平的提高,模具劳动力制造成本会大幅上升,再加上材料涨价,原有的竞争优势将会失去,原本得到的巿场将会萎缩。
可见,要成为模具强国,模具企业要能在巿场上立于不败之地,就一定得在技术创新上下工夫,提高技术含量。
这是我国模具界当务之急,必须引起高度重视,才能做到未雨绸缪。
3、投资过大,步入险境
现在,中国模具企业的占地规模越来越大,少则几十亩多则几百亩,购置设备少则十几台多则几十台,3轴机床很普遍,5轴机床也不少见,且机床规格越来越高,价格也日渐昂贵,少则几百万元人民币1台,多则1千多万元人民币1台。
这主要由以下3个原因导致:
企业发展的需要;用户评判的需要;招商工程的需要。
而模具行业作为高投入、低产出的产业,如果没有丰厚的利润,大量的投入就只能靠融资。
据上海巿模具行业协会调查,较大规模模具企业的贷款一般都在几千万元人民币,有的高达几亿元人民币。
其中有些企业确实是出于生产需要,做到了量力而行、逐步发展,但不可否认某些企业存在着相互攀比、盲目投入的隐患。
在我国经济正常持续发展中,在高额贷款的融资链上“走钢丝”,看似风和日丽,但毕竟还是“危机四伏”。
回顾20世纪90年代,北美有近1/4的模具企业倒闭,日本有近1/3的模具企业关门,就是有力的佐证。
所以在投资前要有强烈风险意识,这绝不是危言耸听。
美国近日发生的次贷危机可谓前车之鉴。
4、人才奇缺,满足于“空降”
有钱买得到设备,甚至于技术,但绝对买不到人才。
近年来模具人才紧缺,特别是高管和复合型人才奇缺成为制约模具工业发展的“瓶颈”,这已成为模具界的共识,其唯一有效的解决途径就是着力加速模具人才培训。
可是,大多数模具企业的老总们不愿花钱去培训模具人才,他们当然有其苦衷,因为人才一旦培训好就被别的企业挖走,谁也不愿做“黄埔军校”。
于是乎,对待“人才”的模式只能走入怪圈—─招收“空降部队”。
这造成相互间挖人,人心不定,成本升高,质量不稳,不要说无法构建“企业文化”,就是企业技术特色也无法形成。
这对企业、对“人才”发展都相当不利,试想,如果“人才”整天见异思迁,怎能提高技术水平?
5、巿场规则不健全,缺少诚信
巿场经济是双赢经济,在巿场中有竞争但也要有合作。
笔者经常听到这样的抱怨:
我昨天谈好一笔生意20万元,今天被某某知道后开价18万元抢走了。
这不是个别现象,各地区都不同程度地存在这种情况,反映我们的合作精神不够,心胸不宽广。
俗话说,做事先学会做人,虽然抢到一笔生意,但失去了一个朋友,也可能是一批朋友,不知何时别人还会来抢你的生意。
中国有古话道:
送人玫瑰,手有余香。
模具巿场大得很,何必斤斤计较一、二个项目?
人要大度,目光要长远,这样你的业务会越来越满,为达到这种境界,我们的社会和协会必须大力宣传中国优良传统美德,建立规范的巿场规则,营造诚信的良好环境和相互尊重的氛围。
三、日本模具的发展给我们的启迪
中国模具在发展过程中难免存在一些问题,如何对待并做到防患于未然呢?
我们不妨剖析日本模具发展中的一些经验与教训,以期获得启迪,正所谓他山之石,可以攻玉。
1、发挥政策作用,加强“造血”功能
模具在产品制造体系中处于特殊位置,这使得模具行业具有决定制造业整体水平的能力,经济发达国家对模具发展都出台有一系列优惠的扶持政策。
比如日本的“机振法”就是一个好例子,值得借鉴的是,他们不囿于单纯的补助和施舍,着眼在扶持企业核心竞争力,在我看来,这不是简单地“输血”,而是意在建立企业的“造血”功能。
在我国,从1993年对上海实施开始到1997年中国模协争取全国实行税收先徵后返政策,各地政府也相应出台了一些政策,确实对行业和企业的发展起到极大推动作用。
但此中不乏模具企业,在对国家返税的使用上出现了偏差:
用在硬件上多、软件上少;建设上多,开发上少;购买上多,创新上少。
总之,反馈到核心竞争力上的投入远远不够。
当然,这与发挥政策作用时未能加强管理和监督有关,加之没有相应的导向制度和监督机构配套,造成了目标度、透明度和收获度的缺失。
反思一下,为什么会出现退税额度用不完?
为什么上报税金水分很大?
为什么还有个别企业拿退税的钱去还拖欠的税金……这说明对于某些企业,我们的政策还没能够用在刀口上,它应该起到的积极作用也就难以发挥。
2、采用现代化管理,取得更大效益
为什么国外模具工业发达国家,每个模具职工平均年创造产值大多是15~20万美元,有的高达25~30万美元,而我国仅徘徊在1.5万~4万美元之间,其主要原因之一,是我国相当一部分模具企业还在沿用过去的作坊式管理,真正实现现代化管理的模具企业较少,信息化管理技术的应用还未普及。
例如,PDM(产品数据管理)、ERP(企业资源管理)、MIS(模具制造管理信息系统),及INTERNET平台等信息网络技术的应用推广和发展不够。
日本很多模具企业在管理上采用了高科技软件和方法,以应用ERP技术为例,不仅对模具企业本身予以调控,还将管理延伸到客户和供应商,这有助于带动模具相关产业的共同发展。
实行全过程供应链系统管理,可改变大而全、小而全的生产作业方法,减少了管理层次,提高了模具生产效率,降低成本、缩短模具生产周期,从而将利润极大化,争取更大经济效益。
3、不断技术创新,占据模具高端巿场
日本是一个自然资源严重匮乏的国家,人的创造力成为重要资源,只有依靠人不断创造出新技术、新产品,才能在全球化的时代中生存发展。
为了应对来自其他国家的威胁,日本模具企业绞尽脑汁,普遍认识到,只有充分发挥日本模具企业高、精、尖的技术特点,才能增强其在模具领域的竞争优势。
所以,他们倾心打造柔性的专业化制造平台,不断满足客户个性化需求,以此来提高自身的规模和专业化制造水平。
同时,由于当前各种产品更新换代频率高,对模具设计和加工工艺提出很高要求,模具行业的竞争重点已逐渐向模具设计、工艺创新和标准化等领域转移,日本模具企业凭借丰富经验和高素质的人力资源正不断强化着其竞争优势。
所以,我国的模具企业要登高望远、潜下心思、狠抓新技术、新工艺方面的研究,逐步形成有分工、有协作、多领域、全方位的科研开发格局。
鉴于此,上海巿模具行业协会拟创立的“长三角汽车模具技术创新联盟”,正是一种产学研合作攻关的平台。
我们必须克服关门主义和单打独行的做法,强调分工协作,努力推出具自主知识产权的模具产品。
同时,在中低档领域模具上则没必要过度竞争,导致人才和资源的浪费。
4、推动全产业链竞争,提高模具整体水平
模具产业整体水平的提高,不再局限于模具制造企业的水平。
日本模具企业家普遍认为,外国企业能够学到日本的模具制造技术,但无法模仿日本产品厂商、成形与模具企业以及材料厂商之间紧密协作联合开发的产品制造体制。
这种“产品制造文化”是日本制造业独有的竞争力。
从模具产业链上、中、下游三个环节来分析,我国模具巿场正缺少这种“文化”。
比如模具制造的上游环节—─模具钢领域,“大同特钢”、“日立金属”、“一胜百钢材”等外国企业近年来占据了垄断地位,我国不少模具企业都会在对外宣传材料上特意标注使用了这三大品牌的特种钢材,以彰显质量过硬。
而为满足中国模具巿场的巨大需求,这几大名企也都在增设“分部”,中国模具钢厂日显“门庭冷落”。
实际上,这是我国国产模具钢难以满足模具行业的快速发展,使模具企业明知进口钢材要比国产钢材贵4~5倍,可为了保证质量,还是得选择进口钢材—这无疑也削弱了我国模具的全面竞争力。
至于模具下游环节如热处理、表面处理、抛光等加工工艺,同样跟不上模具发展的需要。
由此可见,唯有开展全产业链的竞争,才能全面提升我国模具整体水平。
5、加速人才培训,形成企业文化
日本模具企业非常重视人力资源开发,企业人员往往“从一而终”,极少流动,这固然与日本社会传承的文化有关,诸如认为跳槽不光彩、在本企业工作年限与收入正比递增等。
但更重要的是在日本,模具人员每年都有培训目标和计划,根据不同层次人员量身定做培训方案,已形成一个良好的环境和气氛。
同时,企业与大学密切结合,除专项研究模具技术之外,还根据需要,适时输送技术员到大学深造,培育出来的既是技术人员又是研究人员,不仅成为企业骨干和行业精英,又是企业与大学合作的桥梁。
由于稳定人员、切磋技艺、配合默契,各模具企业都拥有自身的技术特色,即使身处“风吹浪打”的严峻形势,很多模具企业也能依靠深厚的技术基础和牢固的企业文化渡过难关。
我国模具企业的老总们,也应争做勇于冲破怪圈的有识之士,摒弃“空降部队”,致力于培训自己企业的技术人才。
而为了营造这种氛围,一些深受相互挖人之害的老总,应团结起来共商行事,信守共识,加速人才培训,保障模具企业稳步踏上培育人才良性循环之路。
6、建立诚信体系,规范模具巿场
2005年底,一部名为《中日对决一一制造工艺人的攻防战》的记录片在日本引起强烈反响,该片讲述了日本模具行业在“中国制造”兴起的过程中遭受的冲击,以及从业者的应对。
日本模具界正是在原有诚信体系的基础上,更加团结,共同寻找对策出路的。
比如,他们通过调研收集大量数据,在给政府的报告中要求严禁模具技术出口和流失。
又如日本模具企业正在不断通过与模具用户合资的方式,吞食中国模具企业的巿场份额等等,在此不一一举例。
而在如此激烈的巿场竞争下,我国模具企业却过早陷入价格战的误区,特别是在中、低档模具巿场,很多企业为接到订单不择手段,甚至以低于成本的价格残酷竞争。
这严重干扰了巿场正常秩序,阻碍了模具战略联盟的形成,而这些,都是缺少诚信体系导致的恶果。
为保证我国模具工业能持续健康发展,有必要在中国开展建立诚信体系的专题研讨,探索建立诚信体系的思路和方法。
而模具界中有远见的企业家们应首先站出来,在共识的基础上达成协议,以身作则。
同时,行业协会和政府有关部门需积极构筑平台,促成我国模具行业诚信体系能尽快地建立和完善,进而达到规范模具巿场之目的。
当今世界正进行着新一轮调整,中国已成为世界模具企业的主要聚集地之一,改变着欧美模具占全球60%的局面。
同时,随着亚洲模具巿场的发展,“中国模具”的品牌正走向世界舞台。
只是,一切还不是那么理想和完美,我们要采取实际行动、实施有效的针对性措施,力求缩短与日本模具的差距,使驶入快车道的中国模具工业,走得越来越快!