减速器传动轴加工工艺.docx
《减速器传动轴加工工艺.docx》由会员分享,可在线阅读,更多相关《减速器传动轴加工工艺.docx(12页珍藏版)》请在冰豆网上搜索。
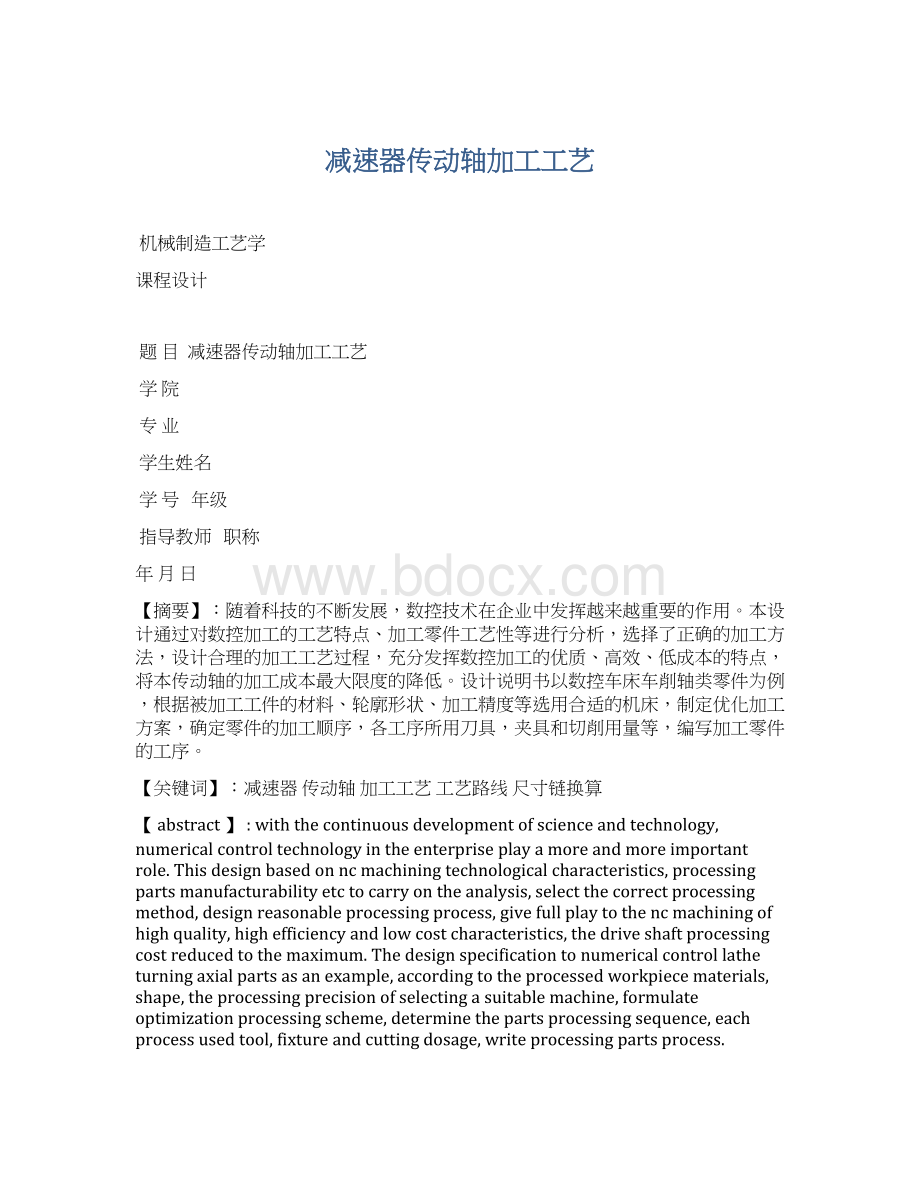
减速器传动轴加工工艺
机械制造工艺学
课程设计
题目减速器传动轴加工工艺
学院
专业
学生姓名
学号年级
指导教师职称
年月日
【摘要】:
随着科技的不断发展,数控技术在企业中发挥越来越重要的作用。
本设计通过对数控加工的工艺特点、加工零件工艺性等进行分析,选择了正确的加工方法,设计合理的加工工艺过程,充分发挥数控加工的优质、高效、低成本的特点,将本传动轴的加工成本最大限度的降低。
设计说明书以数控车床车削轴类零件为例,根据被加工工件的材料、轮廓形状、加工精度等选用合适的机床,制定优化加工方案,确定零件的加工顺序,各工序所用刀具,夹具和切削用量等,编写加工零件的工序。
【关键词】:
减速器传动轴加工工艺工艺路线尺寸链换算
【abstract】:
withthecontinuousdevelopmentofscienceandtechnology,numericalcontroltechnologyintheenterpriseplayamoreandmoreimportantrole.Thisdesignbasedonncmachiningtechnologicalcharacteristics,processingpartsmanufacturabilityetctocarryontheanalysis,selectthecorrectprocessingmethod,designreasonableprocessingprocess,givefullplaytothencmachiningofhighquality,highefficiencyandlowcostcharacteristics,thedriveshaftprocessingcostreducedtothemaximum.Thedesignspecificationtonumericalcontrollatheturningaxialpartsasanexample,accordingtotheprocessedworkpiecematerials,shape,theprocessingprecisionofselectingasuitablemachine,formulateoptimizationprocessingscheme,determinethepartsprocessingsequence,eachprocessusedtool,fixtureandcuttingdosage,writeprocessingpartsprocess.
【keywords】:
reducerdriveshaftprocessingtechnologyprocessroutesizechainconversion
前言5
1.生产纲领及类型5
2.零件的分析5
2.1零件结构工艺性分析5
2.2零件技术要求分析6
3.毛坯的选择6
3.1毛坯的选择6
3.3毛坯形状及尺寸的确定7
4.定位基准的选择7
5.零件表面加工方法的选择7
6.工艺路线的拟定9
7.工序余量和尺寸的确定10
8.设备选择12
9.刀具选择12
10.量具选择12
11.课程设计总结12
12、致谢13
13、参考文献13
前言
机械加工工艺规程,是规定零件机械加工工艺过程和操作方法的重要工艺文件。
它不仅是企业生产中重要的技术文件,也是机械制造过程中用于指导生产、组织加工和管理工作的基本依据,还是新建和改建工厂或车间的基本资料。
本次课程设计是在学习了《机械制造工艺学》课程之后,我综合所学的基础和专业知识,在陈慧老师的悉心指导下进行系统、全面的一次综合性生产实践的检验。
课程设计说明书概括性的介绍了设计过程,对设计中各部分内容作了重点的说明、分析、论证和必要的计算,系统性整理、表达了在机械加工工艺设计过程中涉及到的专业知识和基本要求,有条理的表达了自己对工艺规程作用的见解。
本次设计中,由于生产经验和专业知识有限,设计中一定存在较多的缺点和错误,恳请老师批评指正。
1.生产纲领及类型
由课程设计的给定题目可知该零件为中批生产。
2.零件的分析
2.1零件结构工艺性分析
由实训题目可知,该轴是减速器的一个传动轴。
传动轴与机构中的其他零件通过间隙配合相结合,具有传递力矩,转矩和扭矩等作用。
从零件图上看,该零件是典型的轴类零件,结构比较简单,结构呈阶梯状,属于阶梯轴,形状对称,尺寸精度,形位精度要求均较高。
其主要加工的面有
20mm、
32mm、
40mm、
35mm和
25mm的外圆柱面,及1个键槽。
由于零件悬伸较长,因此刚性较差,在车工件时应充分注意这一点。
2.2零件技术要求分析
从该传动轴零件图可知,两支承轴径分别为
20±0.07mm和
25±0.07mm、配合轴颈
350-0.017是零件的3个重要表面。
该零件的主要技术要求为:
(1)两支轴承径分别为
20±0.07mm和
25±0.07mm,表面粗糙度Ra
0.8um。
(2)配合轴颈
350-0.017mm,表面粗糙度Ra
0.8um,且与支承轴径的同轴度公差为
0.02mm。
(3)键槽8±0.018mm.表面粗糙度Ra
1.6um,键槽深度为310-0.2mm。
(4)键槽对
20mm和
25mm的外圆轴线的对称度为0.03mm。
(5)零件需要调质处理到28HRC~32HRC,保持均匀。
3.毛坯的选择
3.1毛坯的选择
轴类零件最常用的毛坯是棒料和锻件,只有某些大型或结构复杂的轴(如曲轴),在质量允许下采用锻件。
由于毛坯经过加热,锻造后能使金属内部的纤维组织表面均与分布,可获得较高的抗拉,抗弯及抗扭强度,所以除光轴外直径相差不大的阶梯轴可使用热轧棒料或冷轧棒料,一般比较重要的轴大部分都采用锻件,这样既可以改善力学性能,又能节约材料,减少机械加工量。
根据生产规模的大小,毛坯的锻造方式有自由锻和模锻。
自由锻多用于中小批量生产。
模锻适用于大批量生产,而且毛坯制造精度高,加工余量小,生产效率高,可以锻造形状复杂的毛坯。
故综合考虑本设计实际情况,选用冷轧圆钢作为毛坯。
3.3毛坯形状及尺寸的确定
分析零件图可知,轴为阶梯轴,没有斜度,传动轴的外圆直径相差不大(最小端为
20mm,最大端为40mm),故选用棒料。
从生产类型来看为中批生产,因此综合考虑选用
45mm的,长度为160mm的冷轧圆钢作为毛坯。
4.定位基准的选择
(1)粗基准的选择:
按照粗基准的选择原则,应选择次要加工表面为粗基准。
又考虑到台阶轴的工艺特点,所以选择外圆端面为粗基准面。
(2)精基准的选择:
按照基准重合原则及加工要求,故选择两中心孔作为统一的精基准。
5.零件表面加工方法的选择
当零件的加工质量要求较高时,往往不可能用一道工序来满足要求,而要用几道工序逐步达到所要求的加工质量和合理地使用设备、人力,零件的加工过程通常按工序性质不同,可以分为粗加工,半精加工,精加工三个阶段。
(1)粗加工阶段:
其任务是切除毛坯上大部分余量,使毛坯在形状和尺寸上接近零件成品,主要目标是提高生产率,去除内孔,端面以及外圆表面的大部分余量,并为后续工序提供精基准。
此零件即加工
20mm、
32mm、
40mm、
35mm和
25mm的外圆柱面。
(2)半精加工阶段:
其任务是使主要表面达到一定的精加工余量,为主要表面的精加工做好准备。
此零件即加工
20mm、
32mm、
40mm、
35mm和
25mm的外圆柱面、孔等。
(3)精加工阶段:
其任务就是保证各主要表面达到规定的尺寸精度,留一定的精加工余量,为主要表面的精加工做好准备,并可完成一些次要表面的加工。
如精度和表面粗糙度要求,主要目标是全面保证加工质量。
基面先行原则
该零件进行加工时,要将端面先加工,再以左端面、外圆柱面为基准来加工,因为左端面和
20外圆柱面为后续精基准表面加工而设定的,才能使定位基准更准确,从而保证各位置精度的要求,然后再把其余部分加工出来。
先粗后精
即要先安排粗加工工序,再安排精加工工序,粗车将在较短时间内将工件表面上的大部分余量切掉,一方面提高金属切削效率,另一方面满足精车的余量均匀性要求,若粗车后留余量的均匀性满足不了精加工的要求时,则要安排半精车,以此为精车做准备。
先面后孔
对该零件应该先加工圆柱表面,后加工孔,这样安排加工顺序,一方面是利用加工过的平面定位,稳定可靠,另一方面是在加工过的平面上加工孔,比较容易,并能提高孔的加工精度,所以对于传动轴来讲先加工
35外圆柱面,做为定位基准再来加工其余各孔。
工序划分的确定
工序集中与工序分散:
工序集中是指将工件的加工集中在少数几道工序内完成每道工序加工内容较多,工序集中使总工序数减少,这样就减少了安装次数,可以使装夹时间减少,减少夹具数目,并且利于采用高生产率的机床。
工序分散是将工件的加工分散在较多的工序中进行,每道工序的内容很少,最少时每道工序只包括一简单工步,工序分散可使每个工序使用的设备,刀具等比较简单,机床调整工作简化,对操作工人的技术水平也要求低些。
综上所述,考虑到工件是中批量生产的情况,则采用工序分散。
另外根据零件图可以看出,由于两支承轴颈和轴颈配合的精度要求较高,最终加工方法为磨削。
磨外圆前要进行粗车半精车,并完成其他次要表面的加工。
键槽的加工,虽然精度要求不高,但表面粗糙度要求较高,要粗、精铣来达到要求。
辅助工序安排去毛刺,倒棱角,清洗,除锈,退磁,检验等。
6.工艺路线的拟定
根据以上分析,该零件的加工路线为:
下料→车一端面、中心孔,调头车另一端面、中心孔→粗车外圆、车槽和倒角→调质→俢研中心孔→半精车各外圆→铣键槽→粗、精、磨3个主要表面外圆→手工去毛刺→检验。
7.工序余量和尺寸的确定
由《机械加工工艺人员手册》课查得:
(1)调制后半精车余量2.5mm~3mm,本例取3mm.
(2)半精车后
20±0.07mm、
25±0.07mm、
350-0.017mm3段外圆留磨削余量0.4mm,半精车公差取-0.15~0。
根据倒推法,可得半精车工序该3尺寸的相应工序尺寸分别为
20.40-0.15mm、
25.40-0.15mm、
35.40-0.15mm.粗磨后留余量0.1mm,若粗磨公差取-0.1~0,则相应粗磨工序尺寸分别为:
20.10-0.10mm、
25.10-0.10mm和
35.10-0.10mm。
精磨工序尺寸即为设计尺寸,
20±0.07mm、
25±0.07mm和
350-0.017mm。
(3)在
350-0.017mm外圆半精车后铣键槽的深度尺寸的确定,因后续还需要磨削,310-0.2mm的保证涉及多尺寸同时保证必须经过工艺尺寸链计算才能确定。
具体计算如下:
①根据加工过程建立尺寸链如图所示:
②判断组成环的性质
尺寸310-0.2mm是磨削加工后最后得到的,故为封闭环;R170-0.085mm和A为增环,R17.70-0.075mm为减环。
③由尺寸链计算
由式(3.3)得A=17+31-17.7=30.3(mm)
由式(3.6)得ES(A)=0+0-(-0.075)=0.075(mm)
由式(3.7)得E