机床传动系统设计.docx
《机床传动系统设计.docx》由会员分享,可在线阅读,更多相关《机床传动系统设计.docx(19页珍藏版)》请在冰豆网上搜索。
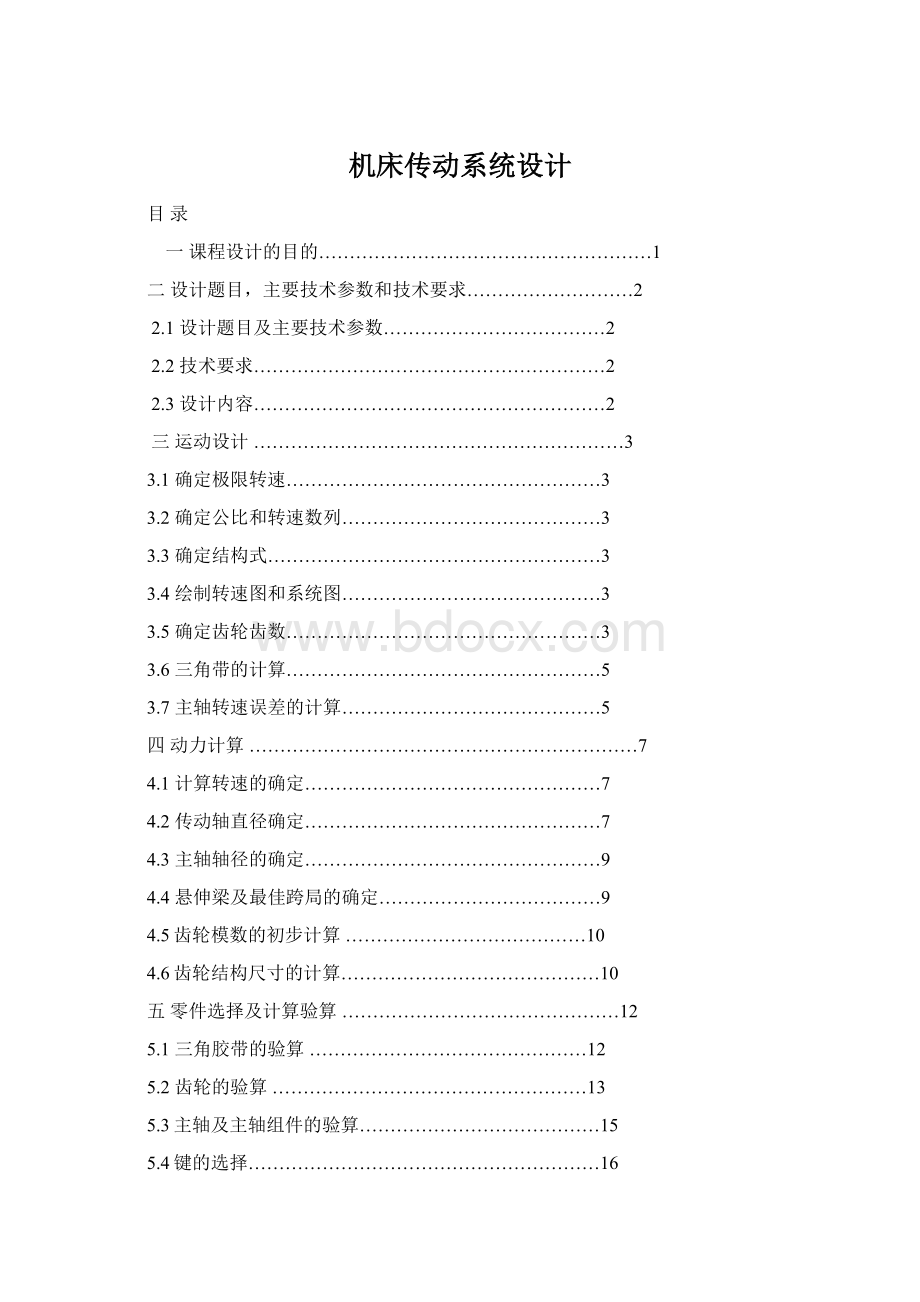
机床传动系统设计
目录
一课程设计的目的………………………………………………1
二设计题目,主要技术参数和技术要求………………………2
2.1设计题目及主要技术参数………………………………2
2.2技术要求…………………………………………………2
2.3设计内容…………………………………………………2
三运动设计……………………………………………………3
3.1确定极限转速……………………………………………3
3.2确定公比和转速数列……………………………………3
3.3确定结构式………………………………………………3
3.4绘制转速图和系统图……………………………………3
3.5确定齿轮齿数……………………………………………3
3.6三角带的计算……………………………………………5
3.7主轴转速误差的计算……………………………………5
四动力计算………………………………………………………7
4.1计算转速的确定…………………………………………7
4.2传动轴直径确定…………………………………………7
4.3主轴轴径的确定…………………………………………9
4.4悬伸梁及最佳跨局的确定………………………………9
4.5齿轮模数的初步计算…………………………………10
4.6齿轮结构尺寸的计算……………………………………10
五零件选择及计算验算………………………………………12
5.1三角胶带的验算………………………………………12
5.2齿轮的验算……………………………………………13
5.3主轴及主轴组件的验算…………………………………15
5.4键的选择…………………………………………………16
5.5主轴轴承的选择…………………………………………16
5.6滚动轴承验算……………………………………………16
六参考文献………………………………………………………17
一课程设计的目的
《机械系统设计》课程设计是在学习完本课程后,进行一次学习设计的综合性练习。
通过课程设计,使我们能够应用学过的基础课、技术基础课和专业课的有关理论知识,及生产实习等实践技能,达到巩固、加深和拓展所学知识的目的。
通过课程设计,分析比较机械系统同的某些典型机构,进行选择和改进;结合结构设计,进行设计计算并编写技术文件;完成系统主传动设计,达到学习设计步骤和方法的目的。
通过设计,掌握查阅相关工程设计手册,设计标准资料的方法,达到积累设计知识和设计技巧,提高我们设计能力的目的。
通过设计,使我们获得机械系统基本设计技能的训练,提高分析和解决工程技术问题的能力,并为进行机械系统设计创造一定条件。
二设计题目、主要技术参数和技术要求
2.1设计题目及主要参数
题目:
分级变速主传动系统设计
主要参数:
n=40r/min,n=900r/min,z=8级,公比Φ=1.41,电动机功率P=2.5/3.5kw,电动机转速n=710/1420r/min。
工件材料:
铸铁、钢
刀具材料:
高速钢、硬质合金
设计部件:
主轴箱
2.2技术要求
1.利用电动机完成换向和制动。
2.各滑移齿轮块采用单独操作机构。
3.仅给传动系统采用单独电动机驱动。
2.3设计内容
1.理论分析与设计计算
⑴机械系统的方案设计。
设计方案的分析,最佳功能原理方案的确定。
⑵根据总体设计参数,进行传动系统运动设计和计算。
⑶根据设计方案和零部件选择的情况,进行有关动力计算与校核。
2.图样设计计算
⑴选择系统中的主要机件
⑵工程技术图样的设计与绘制
三运动设计
3.1确定极限转速
nmin=40r/mim,nmax=900r/min则Rn=
3.2确定公比及主轴转速数列
公比:
=1.41,
=1.41
,采用混合公比。
由z=8级,考虑混合公比,查文献[1]表2.12,得转速数列40r/min,80r/min,112r/min,160r/min,224r/min,315r/min,450r/min,900r/min。
3.3确定结构式
传动方案为Z=8=22×23×24。
对于24变速组,r
满足要求。
3.4绘制转速图和传动系统图
1.选定电动机
一般金属切削机床的驱动,无特殊要求,多采用Y系列封闭冷式鼠
笼型三相异步电动机,根据要求选取双速电动机,其功率P=2.5/3.5kw,转速n=710/1440r/min。
2.绘制转速图
根据升速imax≦2,降速imin≧
的条件,分配各传动组的传动比,绘制转速图如图1:
3.5确定齿轮齿数
根据设计要求zmin≧18,齿数和Sz≦100~120,而且为给设计制造提供方便,主传动链中最好采用较少种类的模数,在运动计算中取变速组内模数相同,在传动链中传动比i均取标准公比Ф=1.41的整数次方,查文献
(1)表4.4确定齿轮齿数和sz及小齿轮齿数zi
各齿轮齿数及传动比见下表:
传动比
i1=1/2.8
i2=1/1
i3=1/4
i4=1
齿轮号
z1
z1,
z2
z2,
z3
z3,
z4
z4,
齿数
18
50
34
34
18
72
45
45
图1转速图
绘制系统图如图2
图2系统图
3.6三角带的计算
1.确定计算功率pc
Pc=ka×p,按两班制工作查文献5表11.5取Ka=1.2,p=3.5kw
Pc=1.2×3.0=4.2kw
2.选三角带型号
据Pc及转速图所给皮带轮转速1420r/min,查文献5图11.15得为A型三角胶带。
3.确定带轮直径D0及D0‘
查文献表11.6,Dmin=100mm,则:
D0,=D0×
=75×
=158mm
3.7核算主轴转速误差
实际传动比所造成的主轴转速误差,一般不应超过
10(
-1)%,即,
×100%≦10(
-1)%=4.1%
算得各级转速误差如下
转速
理论转速
实际转速
转速误差
结果
n1
40
40.45
1.13%
合格
n2
80
80.9
1.13%
合格
n3
112
112.4
0.36%
合格
n4
160
161.8
1.13%
合格
n5
224
224.7
0.31%
合格
n6
315
323.5
2.70%
合格
n7
450
449.4
0.13%
合格
n8
900
898.7
0.14%
合格
四动力计算
4.1计算转速的确定
主轴从计算转速nj到最高转速之间的全部转速都传递全功率。
因此使主轴获得上述转速的传递件的转速也应该传递全部功率,传递件的这些转速中的最低转速,就是传动间的计算转速,当主轴的计算转速确定后就可以从转速图上确定各传动件的计算转速。
1.确定主轴的计算转速
由于设计机床采用混合公比,其主轴计算转速可用下式计算:
nj=nmin×
即nIIIj=40×
=102r/min
取nj=112r/min
2.传动轴计算转速的确定
各轴计算转速如下表:
轴序号
0
Ⅰ
Ⅱ
Ⅲ
nj(r/min)
710
450
160
112
3.确定齿轮副的计算转速
计算各齿轮副计算转速如下表:
齿轮序号
Z1
Z1.
Z2
Z2,
Z3
Z3,
Z4
Z4,
nj(r/min)
450
160
450
450
450
112
160
160
带轮的直径与转速分别是:
D0=100mm,D0,=158mm,n0=710r/min
n0,=450r/min
4.2传动轴直径初定
由文献[4]查得各部件得到传动效率:
带:
η1=0.95
轴承:
η2=0.99
齿轮:
η3=0.97
1.各轴传递的功率与扭矩:
电机轴(0轴):
P0=3.5kw
T0=9.55×106×
=47077(N·mm)
Ⅰ轴:
p1=p0×η1=3.5×0.95=3.325kw
T1=9.55×106
=9.55×106×
=70564(N·mm)
Ⅱ轴:
p2=p1·η2·η3=3.325×0.99×0.97=3.193kw
T2=9.55×106
=9.55×106×
=190582(N·mm)
Ⅲ轴:
p3=p2·η2·η3=3.193×0.99×0.97=3.066kw
T3=9.55×106
=9.55×106×
=261431(N·mm)
列表如下:
轴序号
功率N(kw)
转速n(r/min)
转矩(N·mm)
0
3.5
710
47077
Ⅰ
3.325
450
70564
Ⅱ
3.193
160
190582
Ⅲ
3.066
112
262431
传动轴直径的确定
由文献[2]查得:
传动轴直径按扭转刚度用下式计算:
d=1.64
(mm)
式中Tn—该轴传递额定扭矩(N.mm)[
]—该轴每米长度允许扭转角(deg/m),对传动轴,这里取[
]=
Ⅰ轴直径d1=1.64
=28.2mm取d1=30mm
Ⅱ轴直径d2=1.64
=36.2mm取d1=40mm
据机床传动特点,均定为花键轴,查机械零件设计手册,确定花键尺寸如下:
Ⅰ轴选花键8×32×36×6
Ⅱ轴选花键8×42×46×8
4.3主轴轴径的确定
主轴前轴径D1尺寸,按文献[1]表3.20所列的数据确定,取D1=80mm,后轴颈D2可按D2=(0.7~0.9)D1=(56~72)mm取D1=65mm
内孔径:
d=d2×(50~70%)=42mm
4.4主轴最佳跨距的确立
(1)悬伸梁a:
选择前轴承为NN3016K型
后轴承为NN3013K型,根据结构定悬伸梁长度a,由于a/D1=1.25~2.5,则取a=120mm。
(2)由最佳跨距:
求轴承刚度,主轴最大输出转矩T:
T3=262431N·mm
该系统用于φ400的车床上,床身上最常用的最大加工直径即经济加工直径约为最大回转直径的60%,即240mm,故半径为0.12m。
切削力:
Fc=262.431/0.12=2187N
背向力:
Fp=0.5Fc=1094N
则F=
=
=2445N
此力作用于顶在顶尖间的工件上,主轴和尾架各承受一半,故主轴端受力为F/2=1223N
在估算时,假设初值L/a=3(取2~3.5之间),L=360mm.
前后支承反力RA和RB分别为:
RA=F/2×(L+a)/L=1631NRB=F/2×(a/L)=408N
根据文献[1]表3.11查得:
前支承:
La=9,iz=52
后支承:
La=8,iz=50
求出前,后轴承的刚度分别为:
KA=3.39RA0.1la0.8(iz)0.9cosa1.9
=3.39×16310.1×90.8×520.9×11.9=1443N/um
KB=3.39×4080.1×80.8×500.9×11.9=1104N/um
=
=1.31
初步计算时,可假设主轴的当量外de为前,后轴经的平均值,
De=(80+65)/2=72.5mm
故惯性矩:
I=0.05×(0.07254-0.044)=125.2m4
=0.10
式中取E=2.1×1011,查文献[1]图3.38可知l0/a≈1.5。
计算的与原假定不符。
根据l0/a=2再求最佳跨距。
这时算出的KA=1460N/um,KB=1149N/um,η=0.11,l0/a仍接近于1.5。
可以看出,这是一个迭代过程,很快收敛于正确值。
最佳跨距是l0≥120×1.5mm=180mm。
4.5齿轮模数的初步计算
一般同一变速组中齿轮取同一模数,选择负荷最重的小齿轮,按简化的接触疲劳强度计算:
mj=1638
mm
式中,mj——按接触疲劳强度计算的齿轮模数(mm);
Nd——驱动电动机功率(kw),取Nd=3.5kw;
nj——计算齿轮的计算转速(r/min);
u——大齿轮与小齿轮齿数比u≧1,外啮合取“+”,内啮合取“-”;
Z1——小齿轮齿数;
φm——齿宽系数,φm=
(B为齿宽,m为模数),取φm=8;
[σf]——许用接触应力(MPa),由文献[5]图12.17c)取[σf]=500MPa
可得各齿轮模数按参考文献取其值如下表:
组别
第一扩大组
第二扩大组
齿轮计算转速(r/min)
450
450
齿数比
50/18
72/18
小齿轮齿数
18
18
计算模数(mm)
4.14
4.03
标准模数(mm)
5
5
4.6齿轮结构尺寸的计算
分度圆直径d=mz,齿顶高ha=ha*m(ha*=1,c*=0.25),齿根高hf=(ha*+c*)m,齿宽b=φm×m,b`=b+(8~10)mm,则分别计算出各齿轮分
度圆直径,齿顶圆直径,齿根圆直径,中心距及齿宽如下表:
齿轮序号
Z1
Z1`
Z2
Z2`
Z3
Z3`
Z4
Z4`
齿数
18
50
34
34
18
72
45
45
模数(mm)
5
5
中心距(mm)
170
225
分度圆直径(mm)
90
250
170
170
90
360
225
225
齿顶圆直径(mm)
100
260
180
180
100
370
235
235
齿根圆直径
(mm)
77.5
23.7
157.5
157.5
77.5
347.5
212.5
212.5
齿顶高(mm)
5
5
5
5
5
5
5
5
齿根高(mm)
6.25
6.25
6.25
6.25
6.25
6.25
6.25
6.25
齿宽(mm)
48
40
48
40
48
40
40
48
五零件选择及计算验算
5.1三角胶带传动的计算和选定
定带号:
由文献[2]表11.5查得KA=1.1
计算功率:
PC=P×KA=3.85kw
由文献[2]图11.15选A型V带。
(1)计算三角胶带速度
V=
=3.7m/s
(2)初定中心距a
取a=500mm。
(3)三角胶带带长Ld
由参考文献知:
L=
×Dm+2×a+
/a
式中Dm=(D1+D2)/2=(100+158)/2=129mm;
=(D2-D1)/2=29mm;
初步求得L=1407mm
查文献[5]图11.4,取标准长度Ld=1400mm。
(4)计算实际中心距a
a=(L-
×Dm)/4+
=496mm
(5)计算小带轮包角
=1800-(D2-D1)/a×600=173.00≧1200,,故满足要求。
(6)确定胶带根数z
由文献[5]式11.22知
z=
查表得计算知:
Z=5.2根取Z=5根
(7)张紧力:
F0=500×
=135.86N
(8)作用在轴上的力Q
Q=2F0Zsin
=2×146.97×3×sin
=1627N
5.2齿轮验算
(1)直齿圆柱齿轮应力验算
在验算变速箱中的齿轮应力时,选相同模数中承受载荷最大的,齿数最小的齿轮进行接触应力和弯曲应力验算。
接触应力验算公式为
弯曲应力验算公式为
式中,N——传递的额定功率(kw),
;
nj——计算转速(r/min);
m——初算的齿轮模数(mm);
B——齿宽(mm);
z——小齿轮齿数;
u——大齿轮与小齿轮齿数比u≧1,外啮合取“+”,内啮合取“-”;
Ks——寿命系数;
Ks=KTKnKNKq
KT——工作期限系数:
T——齿轮在机床工作期限(Ts)内的总时间(h);对于中型机床的齿轮取Ts=15000~20000h,同一变速组内的齿轮总工作时间可近似地认为T=Ts/p,p为该变速组的传动副数。
这里取T=10000h;
n1——齿轮最低转数(r/min);
Cv——基准循环次数,接触载荷取
,弯曲载荷取
;
m——疲劳曲线指数,接触载荷取m=3,弯曲载荷取m=6;
Kn——转数变化系数,查文献[3]表5-6;
KN——功率利用系数,查文献[3]表5-7;
Kq——材料强化系数,查文献[3]表5-8;
高速传动件可能存在Ks>Ksmax的情况,此时取Ks=Ksmax;大载荷低速传动件可能存在Ks此时应取KsK3——工作状况系数,考虑载荷冲击的影响,主传动(中等冲击)取K3=1.2~1.6;
K2——动载荷系数,查文献[3]表5-1;
K1——齿向载荷分布系数,查文献[3]表5-2;
Y——齿形系数,查文献[3]表5-3;
——许用接触应力,查文献[3]表5-11,取
;
——许用弯曲应力,查文献[3]表5-11取
;
直齿圆柱齿轮的应力验算如下表:
接触应力验算
接触应力验算
第一扩大组
第二扩大组
第一扩大组
第二扩大组
N
3.325
3.193
3.325
3.193
nj
450
450
450
450
m
5
5
5
5
B
48
48
48
48
z
18
18
18
18
u
50/18
72/18
Ks
(计算值)
3×0.71
×0.58×0.64
2.13×1.03
×0.58×0.60
1.05×0.71
×0.78×0.77
0.88×1.03
×0.78×0.75
KS
0.6
0.6
0.45
0.53
K3
1.5
1.5
1.5
1.5
K2
1.5
1.5
1.5
1.5
K1
1.04
1.04
1.04
1.04
Y
0.378
0.378
600
600
220
220
398
374
18
21
结论
合格
合格
合格
合格
(2)齿轮精度的确定
首先计算出齿轮的圆周速度,然后按文献查表选取。
V=
(m/s)
列式如下表
nmax(r/min)
z
d(mm)
v(m/s)
精度等级
Ⅰ轴齿轮
900
18
90
4.24
8
Ⅱ轴齿轮
900
18
90
4.24
8
5.3主轴及主轴组件的验算
(1)主轴刚度验算
前支撑为双列圆柱滚子轴承,后支撑为深沟球轴承和止推轴承,跨距L=180mm.
当量外径
de=
=
主轴刚度:
因为di/de=40/72.5=0.55<0.7,所以孔对刚度的影响可忽略;
ks=
=170N/um
刚度要求:
主轴的刚度可根据机床的稳定性和精度要求来评定
5.4键的选择
根据机床传动特点和经济性考虑,
轴采用平键连接,所以
轴键公称尺寸:
圆头普通平键(A型)。
b=20mm,h=12mm,L=160mm.
5.5主轴轴承的选择
前轴承选用:
NN3016K,双列圆柱滚子轴承。
后轴承选用:
NN3013K。
5.6滚动轴承验算
主轴的前轴承NN3016K双列圆柱滚子轴承,精度等级为P4级,适用于一般机床,由于主轴较粗,载荷相对来说不大,往往磨损后精度下降而失效。
所以这时规定主轴滚动轴承寿命是精度,失效的原因是磨损。
这种精度寿命目前还难以计算,只有依靠经验来估计。
对于后轴承来说,中窄系列一般能够满足要求,故前后轴承均能满足要求。
参考文献
文献[1]:
机械系统设计修订版,侯珍秀编,哈尔滨工业大学出版社
文献[2]:
机械设计,第四版,邱宣怀主编,高等教育出版社
文献[3]:
金属切削机床设计概论与设计习题及课程设计指导,机械制造委员会编,北京科学技术出版社