毕业设计论文衬板冲压工艺及模具设计全套图纸.docx
《毕业设计论文衬板冲压工艺及模具设计全套图纸.docx》由会员分享,可在线阅读,更多相关《毕业设计论文衬板冲压工艺及模具设计全套图纸.docx(25页珍藏版)》请在冰豆网上搜索。
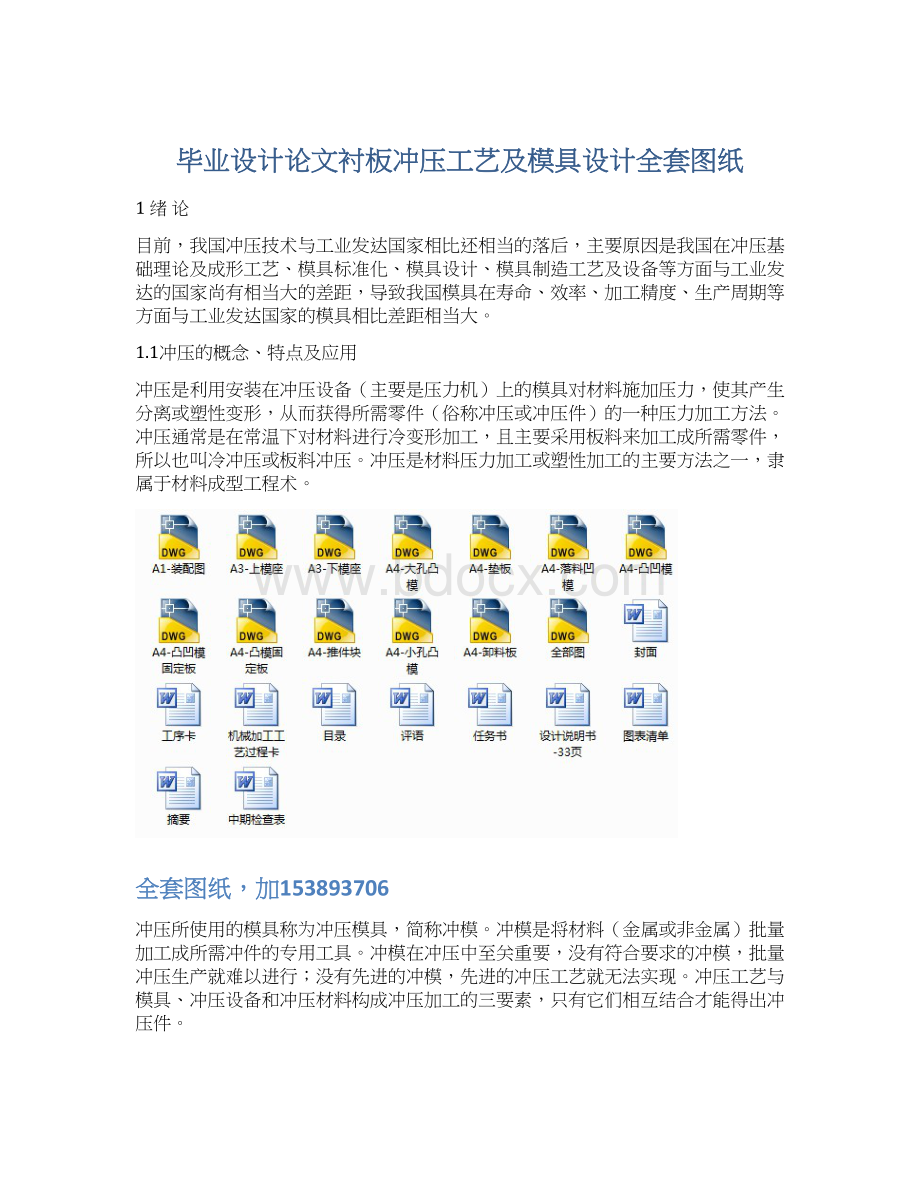
毕业设计论文衬板冲压工艺及模具设计全套图纸
1绪论
目前,我国冲压技术与工业发达国家相比还相当的落后,主要原因是我国在冲压基础理论及成形工艺、模具标准化、模具设计、模具制造工艺及设备等方面与工业发达的国家尚有相当大的差距,导致我国模具在寿命、效率、加工精度、生产周期等方面与工业发达国家的模具相比差距相当大。
1.1冲压的概念、特点及应用
冲压是利用安装在冲压设备(主要是压力机)上的模具对材料施加压力,使其产生分离或塑性变形,从而获得所需零件(俗称冲压或冲压件)的一种压力加工方法。
冲压通常是在常温下对材料进行冷变形加工,且主要采用板料来加工成所需零件,所以也叫冷冲压或板料冲压。
冲压是材料压力加工或塑性加工的主要方法之一,隶属于材料成型工程术。
全套图纸,加153893706
冲压所使用的模具称为冲压模具,简称冲模。
冲模是将材料(金属或非金属)批量加工成所需冲件的专用工具。
冲模在冲压中至关重要,没有符合要求的冲模,批量冲压生产就难以进行;没有先进的冲模,先进的冲压工艺就无法实现。
冲压工艺与模具、冲压设备和冲压材料构成冲压加工的三要素,只有它们相互结合才能得出冲压件。
与机械加工及塑性加工的其它方法相比,冲压加工无论在技术方面还是经济方面都具有许多独特的优点。
主要表现如下。
(1)冲压加工的生产效率高,且操作方便,易于实现机械化与自动化。
这是因为冲压是依靠冲模和冲压设备来完成加工,普通压力机的行程次数为每分钟可达几十次,高速压力要每分钟可达数百次甚至千次以上,而且每次冲压行程就可能得到一个冲件。
(2)冲压时由于模具保证了冲压件的尺寸与形状精度,且一般不破坏冲压件的表面质量,而模具的寿命一般较长,所以冲压的质量稳定,互换性好,具有“一模一样”的特征。
(3)冲压可加工出尺寸范围较大、形状较复杂的零件,如小到钟表的秒表,大到汽车纵梁、覆盖件等,加上冲压时材料的冷变形硬化效应,冲压的强度和刚度均较高。
(4)冲压一般没有切屑碎料生成,材料的消耗较少,且不需其它加热设备,因而是一种省料,节能的加工方法,冲压件的成本较低。
冲压地、在现代工业生产中,尤其是大批量生产中应用十分广泛。
相当多的工业部门越来越多地采用冲压法加工产品零部件,如汽车、农机、仪器、仪表、电子、航空、航天、家电及轻工等行业。
在这些工业部门中,冲压件所占的比重都相当的大,少则60%以上,多则90%以上。
不少过去用锻造=铸造和切削加工方法制造的零件,现在大多数也被质量轻、刚度好的冲压件所代替。
因此可以说,如果生产中不谅采用冲压工艺,许多工业部门要提高生产效率和产品质量、降低生产成本、快速进行产品更新换代等都是难以实现的。
1.2国内模具发展现状方向以及冲压技术的现状及发展方向
1.2.1国内模具的现状
我国模具近年来发展很快,据不完全统计,2003年我国模具生产厂点约有2万多家,从业人员约50多万人,2004年模具行业的发展保持良好势头,模具企业总体上订单充足,任务饱满,2004年模具产值530亿元。
进口模具18.13亿 美元,出口模具4.91亿美元,分别比2003年增长18%、32.4%和45.9%。
进出口之比2004年为3.69:
1,进出口相抵后的进净口达13.2亿美元,为净进口量较大的国家。
在2万多家生产厂点中,有一半以上是自产自用的。
在模具企业中,产值过亿元的模具企业只有20多家,中型企业几十家,其余都是小型企业。
近年来, 模具行业结构调整和体制改革步伐加快,主要表现为:
大型、精密、复杂、长寿命中高档模具及模具标准件发展速度快于一般模具产品;专业模具厂数量增加,能力提高较快;"三资"及私营企业发展迅速;国企股份制改造步伐加快等。
虽然说我国模具业发展迅速,但远远不能适应国民经济发展的需要。
我国尚存在以下几方面的不足:
第一,体制不顺,基础薄弱。
“三资”企业虽然已经对中国模具工业的发展起了积极的推动作用,私营企业近年来发展较快,国企改革也在进行之中,但总体来看,体制和机制尚不适应市场经济,再加上国内模具工业基础薄弱,因此,行业发展还不尽如人意,特别是总体水平和高新技术方面。
第二,开发能力较差,经济效益欠佳.我国模具企业技术人员比例低,水平较低,且不重视产品开发,在市场中经常处于被动地位。
我国每个模具职工平均年创造产值约合1万美元,国外模具工业发达国家大多是15~20万美元,有的高达25~30万美元,与之相对的是我国相当一部分模具企业还沿用过去作坊式管理,真正实现现代化企业管理的企业较少。
第三,工艺装备水平低,且配套性不好,利用率低.虽然国内许多企业采用了先进的加工设备,但总的来看装备水平仍比国外企业落后许多,特别是设备数控化率和CAD/CAM应用覆盖率要比国外企业低得多。
由于体制和资金等原因,引进设备不配套,设备与附配件不配套现象十分普遍,设备利用率低的问题长期得不到较好解决。
装备水平低,带来中国模具企业钳工比例过高等问题。
第四,专业化、标准化、商品化的程度低、协作差.由于长期以来受“大而全”“小而全”影响,许多模具企业观念落后,模具企业专业化生产水平低,专业化分工不细,商品化程度也低。
目前国内每年生产的模具,商品模具只占45%左右,其馀为自产自用。
模具企业之间协作不好,难以完成较大规模的模具成套任务,与国际水平相比要落后许多。
模具标准化水平低,标准件使用覆盖率低也对模具质量、成本有较大影响,对模具制造周期影响尤甚。
第五,模具材料及模具相关技术落后.模具材料性能、质量和品种往往会影响模具质量、寿命及成本,国产模具钢与国外进口钢相比,无论是质量还是品种规格,都有较大差距。
塑料、板材、设备等性能差,也直接影响模具水平的提高。
1.2.2国内模具的发展趋势
巨大的市场需求将推动中国模具的工业调整发展。
虽然我国的模具工业和技术在过去的十多年得到了快速发展,但与国外工业发达国家相比仍存在较大差距,尚不能完全满足国民经济高速发展的需求。
未来的十年,中国模具工业和技术的主要发展方向包括以下几方面:
1)模具日趋大型化;
2)在模具设计制造中广泛应用CAD/CAE/CAM技术;
3)模具扫描及数字化系统;
4)在塑料模具中推广应用热流道技术、气辅注射成型和高压注射成型技术;
5)提高模具标准化水平和模具标准件的使用率;
6)发展优质模具材料和先进的表面处理技术;
7)模具的精度将越来越高;
8)模具研磨抛光将自动化、智能化;
9)研究和应用模具的高速测量技术与逆向工程;
10)开发新的成形工艺和模具。
1.2.3冲压标准化及专业化生产方面
模具的标准化及专业化生产,已得到模具行业和广泛重视。
因为冲模属单件小批量生产,冲模零件既具的一定的复杂性和精密性,又具有一定的结构典型性。
因此,只有实现了冲模的标准化,才能使冲模和冲模零件的生产实现专业化、商品化,从而降低模具的成本,提高模具的质量和缩短制造周期。
目前,国外先进工业国家模具标准化生产程度已达70%~80%,模具厂只需设计制造工作零件,大部分模具零件均从标准件厂购买,使生产率大幅度提高。
模具制造厂专业化程度越不定期越高,分工越来越细,如目前有模架厂、顶杆厂、热处理厂等,甚至某些模具厂仅专业化制造某类产品的冲裁模或弯曲模,这样更有利于制造水平的提高和制造周期的缩短。
我国冲模标准化与专业化生产近年来也有较大发展,除反映在标准件专业化生产厂家有较多增加外,标准件品种也有扩展,精度亦有提高。
但总体情况还满足不了模具工业发展的要求,主要体现在标准化程度还不高(一般在40%以下),标准件的品种和规格较少,大多数标准件厂家未形成规模化生产,标准件质量也还存在较多问题。
另外,标准件生产的销售、供货、服务等都还有待于进一步提高。
1.3 衬板冲孔落料模具设计与制造方面
1.3.1衬板冲孔落料模具设计的设计思路
冲裁是冲压工艺的最基本工序之一,它是利用模具使板料沿着一定的轮廓形状产生分离的一种冲压工序。
它包括落料、冲孔、切边、修边、切舌、剖切等工序,其中落料和冲孔是最常见的两种工序。
冲裁在冲压加工中应用极广。
它既可直接冲出成品零件,还可以对已成形的工件进行再加工。
普通冲裁加工出来的制件的精度不高,一般情况下,冲裁件的尺寸精度应在IT12级以下,不宜高于IT10级。
只有加强冲裁变形基础理论的研究,才能提供更加准确、实用、方便的计算方法,才能正确地确定冲裁工艺参数和模具工作部分的几何形状与尺寸,解决冲裁变形中出现的各种实际问题,从而,进一步提高制件质量。
衬板是典型的冲压件,该模具工作过程很简单就是冲孔和落料,根据零件图的结构和尺寸精度以及材料的性能确定完成该冲件所需要的模具类型.因此,综合考虑各种因素后采用复合模。
根据计算的结果和选用的标准模架,判断此次冲裁能不能采用标准的模架。
为了保证制件的顺利加工和顺利取件,模具必须有足够高度。
要改变模具的高度,只有从改变导柱和导套的高度,改变导柱和导套的高度的同时,还要注意保证导柱和导套的强度.导柱和导套的高度可根据冲裁凸凹模与落料凹模工作配合长度决定.设计时可能高度出现误差,应当边试冲边修改高度。
1.3.2衬板冲压模具设计的进度
1.了解目前国内外冲压模具的发展现状,所用时间10天;
2.确定加工方案,所用时间5天;
3.模具的设计,所用时间30天;
4.模具的调试.所用时间5天.
2衬板冲压工艺性的分析
工件名称:
衬板
生产批量:
大批量
材料:
30
材料厚度:
2mm
工件图:
如图1
图1零件图
该零件是衬板,该零件对材料的性能要求不是很高,30钢该零件的材料满足使用要求。
外形落料的工艺性:
衬板料厚2mm,外形复杂程度一般,尺寸精度要求一般。
因此,可采用落料工艺获得。
冲孔工艺性:
四个直径6.4的圆孔和一个直径17的大圆孔,这两类孔的形状均较规则,尺寸精度要求一般,可采用冲孔获得。
此工件只有外形落料和冲孔两个工序,图1所示零件尺寸均为未标注公差的一般尺寸,按GB1804—79规定取IT14级,符合一般复合模的经济精度要求。
综上分析可知,图1零件具有较好的冲压工艺性,适合冲压生产。
3分析比较和确定工艺方案
垫片零件所需的基本冲压工序为冲孔和落料,可拟定以下三种工艺方案。
方案一:
采用单工序模分三次工序进行冲压。
工序1:
冲出衬板的外形轮廓。
工序2:
冲出直径17的大圆孔。
工序3:
冲出四个直径6.4的圆孔。
方案二:
采用冲孔落料复合模。
方案三:
采用冲孔落料级进模。
各个方案优缺点的分析比较:
方案一的特点是化整为零,将原先很复杂的工件形状分解成两类形状规则的内孔和一个外形轮廓,三个形状较简单的单元从而简化了模具刃口形状,使模具制造简便。
另外,各次工序所需的冲压力小了,可以解决冲压设备吨位不够的问题。
这个方案的缺点是需要两次冲压工序,多工序冲裁时,生产效率低累积误差大,与本零件生产批量大相矛盾。
此外,该方案在完成冲压生产过程中,增大冲压工人的劳动强度。
方案二的优点是冲压件内外形相对位置及零件尺寸和一致性非常好,制件精度高;制件表面平直;适宜冲制薄料,模具结构紧凑,要求压力机工作台面的面积较小,缺点是凸凹模壁厚受到限制,尺寸不能太小。
方案三的特点是构成连续模的零件数量多,结构复杂。
模具制造与装配难度大,精度要求高,步距控制精确,且要求刃磨,准修方便。
刚性大,对有关模具零件材料及热处理要求高,仅适合中小型零件的大批量生产。
衬板零件的空间距离和孔边距离远大于此零件要求的最小壁厚1mm。
该冲压件的料厚为1mm,属于薄料,切尺寸较大,综合考虑模具结构和模具生产经济性等因素,该冲压件采用方案二较为合理。
4模具结构型式的选择
4.1模具结构型式
根据上述分析,该零件采用复合模。
若采用倒装式复合模,冲孔废料可以通过凸凹模,从压力机工作台孔中漏出,工件由上面的凹模带上后,由推件装置推出。
板料由下模的卸料装置脱出,这样操作方便而且安全能