装置检修无损检测施工方案.docx
《装置检修无损检测施工方案.docx》由会员分享,可在线阅读,更多相关《装置检修无损检测施工方案.docx(21页珍藏版)》请在冰豆网上搜索。
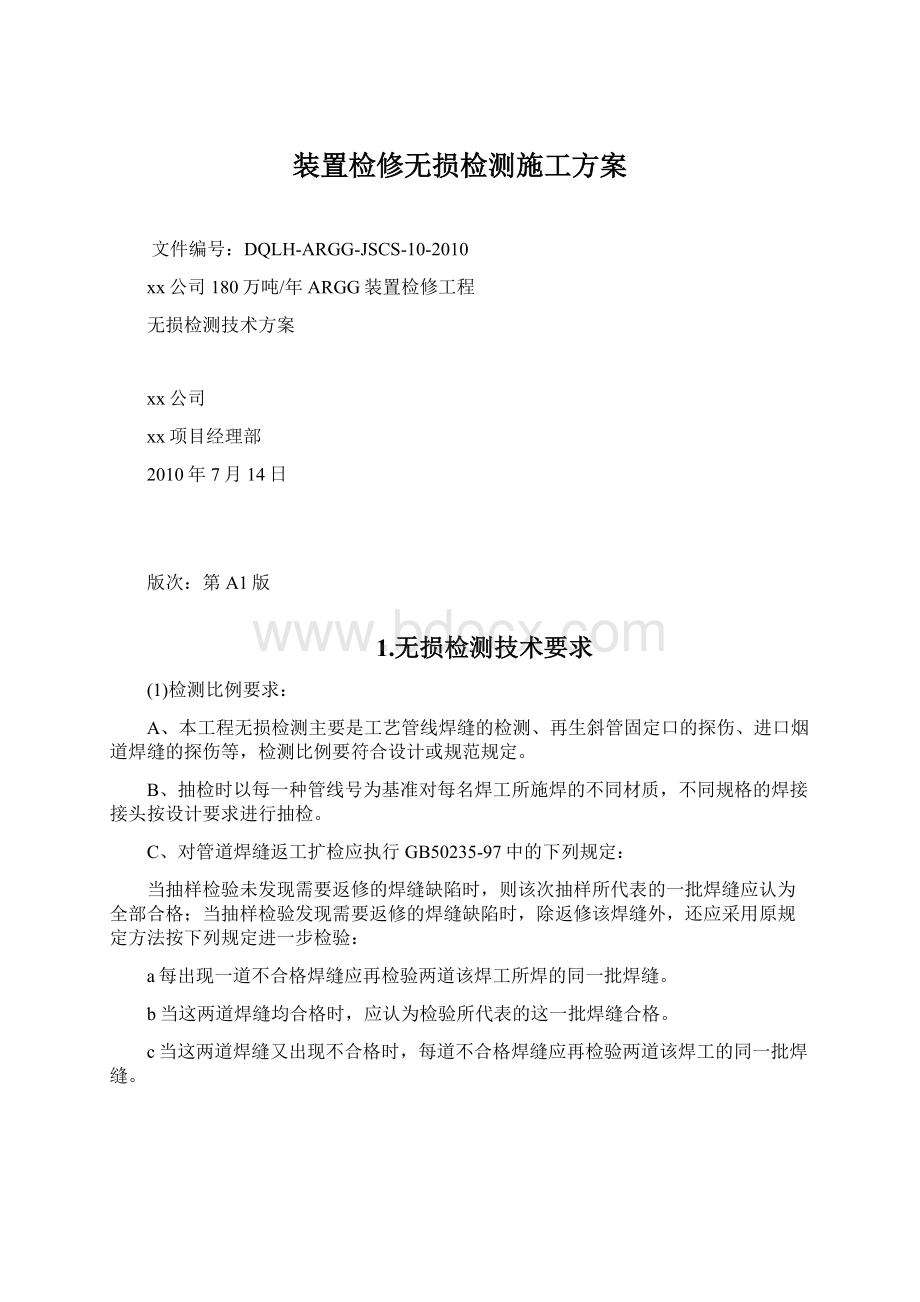
装置检修无损检测施工方案
文件编号:
DQLH-ARGG-JSCS-10-2010
xx公司180万吨/年ARGG装置检修工程
无损检测技术方案
xx公司
xx项目经理部
2010年7月14日
版次:
第A1版
1.无损检测技术要求
(1)检测比例要求:
A、本工程无损检测主要是工艺管线焊缝的检测、再生斜管固定口的探伤、进口烟道焊缝的探伤等,检测比例要符合设计或规范规定。
B、抽检时以每一种管线号为基准对每名焊工所施焊的不同材质,不同规格的焊接接头按设计要求进行抽检。
C、对管道焊缝返工扩检应执行GB50235-97中的下列规定:
当抽样检验未发现需要返修的焊缝缺陷时,则该次抽样所代表的一批焊缝应认为全部合格;当抽样检验发现需要返修的焊缝缺陷时,除返修该焊缝外,还应采用原规定方法按下列规定进一步检验:
a每出现一道不合格焊缝应再检验两道该焊工所焊的同一批焊缝。
b当这两道焊缝均合格时,应认为检验所代表的这一批焊缝合格。
c当这两道焊缝又出现不合格时,每道不合格焊缝应再检验两道该焊工的同一批焊缝。
2.主要检测方案
(1)对于本装置中工艺管道对接焊缝射线检测一般采用常规χ射线检测为主的检测方法。
(2)工艺管道检测有困难的固定焊口、容器类焊缝等可采用γ射线进行双壁单影或双壁双影透照。
(3)对于大壁厚(单壁≥25mm)工艺管道对接焊缝可采用下列检测方法:
A、周向χ射线或γ射线周向一次曝光。
B、γ射线双壁单影透照。
3.检测部位表面质量要求
(1)进行检测作业前,必须对被检焊缝的表面质量进行确认,符合标准要求后方可进行检验。
(2)射线检测部位表面的不规则状态以不掩盖或不影响内部缺陷显示作为是否修磨处理的限度。
4.检测时机
(1)检测对象应经形状尺寸和外观质量检查合格后,方可进行检测。
(2)设计文件有要求的,按规定的时机进行无损检测。
(3)对于返修部位应在返修后及时复探。
(4)材质为合金钢的对接焊缝必须焊接完成24h后,才能进行检测。
5.检测工艺流程
(1)射线检测工艺流程
(2)渗透检测工艺流程图
6.射线检测(RT)工艺
(1)射线照相质量等级:
选用AB级
(2)检测设备与器材
检测设备:
250/300kV定向、250kV/300kV周向X射线机
机胶片类型:
柯达胶片AA400
象质计灵敏度:
按JB/T4730-2005中要求进行选择。
增感屏:
铅箔增感屏(χ射线前后屏为0.02~0.2mm,根据不同的电压kV值进行选择)。
(3)透照方式、象质计的选用和摆放位置(见表23)
规格(mm)
透照方式
象质计选用
摆放部位
Φ≤100
T≤8mm,b≤D0/4
双壁双影
R10系列象质计
胶片侧或射源侧均可
T>8mm,b>D0/4
垂直透照
100<Φ≤711
双壁单影或周向
胶片有效长度1/4处或在圆周上等间隔地放置3个象质计
Φ>711
活动口
单壁单影或周向
胶片有效长度1/4处或在圆周上等间隔地放置3个象质计
固定口
双壁单影
胶片有效长度1/4处
(4)训机要求:
必须按照设备使用说明书进行规范训机,严禁违章操作,每次训机必须达到满幅的80%以上。
(5)曝光参数的选择:
依照JB4730—2005中的要求,当焦距为700mm时,曝光量不得低于15mA·min。
当焦距改变时可按平方反比定律对曝光量的推荐值进行换算。
(6)透照方法的选择
A、对于管径≤100mm以下的管道焊缝,且T≤8mm,b(焊缝宽度≤D0/4)时采用双壁双影法透照,分两次相互垂直方向透照,椭圆间距应在1倍焊缝宽度左右为宜;
椭圆成像方法:
采用位移法,其位移计算公式:
L=
式中:
L——位移距离
L1——焦点到工件表面距离
L2——工件表面到胶片距离
b——焊缝宽度(b≤D0/4)
q——椭圆开口宽度
B、对于管径≤100mm以下的管道焊缝,若T>8mm,b(焊缝宽度>D0/4)时,采用垂直透照方式重叠成像,此时一般应相隔120°或60°透照3次;
C、对于100mm<Φ≤711mm的管道焊缝和Φ>711mm的固定焊口,采用双壁单投影法透照。
其每次透照长度计算见下式:
L3=πD0/N
式中:
D0——环焊缝外径
N——每道焊口透照底片张数(既可查表又可计算)
D、对于Φ>711mm的活动焊口,可利用周向X射线机,采用中心透照方式周向曝光;
(7)射线照相质量等级及透照厚度比:
JB4730—2005规定,射线照相质量等级为AB级,管径为100到400之间时,透照厚度比K为1.2,管径大于400时,透照厚度比K为1.1。
(8)焊缝透照底片张数的计算方法:
ADN≧500执行SH3501-2002规范,抽查比例和检验长度按每条焊缝的长度计算。
B500>DN≥100,每道焊缝的透照次数N的计算方法及过程如下:
依据JB4730-2005规定和上图,其计算公式见下式:
N=1800/a=1800/η+θ
η=Sin-1(D0Sinθ/F-D0)
θ=Cos-1〔1+(K-1)T/D0〕/K
a=η+θ
式中:
N——透照底片张数η——射线束半辐射角
θ——横向裂纹检出角K——透照厚度比
F——焦点到胶片距离(mm)
D0——环焊缝外径(mm)T——壁厚(mm)
当D/T≧1/30时
可使公式θ=Cos-1〔1+(K-1)T/D0〕/K简化为:
θ=Cos-11/K
透照方式和透照焦距如表24:
序号
检件规格
透照方式
透照焦距(mm)
1
DN≧500
双/单壁单影
≧650
2
500>DN≥100
单壁单影
D0+150
3
DN≦80
双壁双影
600
C工艺管道各种规格每道焊口的拍片数量:
序号
管径
张数
有效长度(mm)
1
设备
\
n
200~260
2
管道
Φ813
10
256
3
管道
Φ711
9
249
4
管道
Φ660
8
260
5
管道
Φ630
8
247
6
管道
Φ530
7
238
7
管道
Φ478
6
250
8
管道
Φ426
6
222
9
管道
Φ377
6
197
10
管道
Φ325
6
170
11
管道
Φ273
6
143
12
管道
Φ219
6
115
13
管道
Φ168
6
88
14
管道
Φ159
6
84
15
管道
Φ141
6
74
16
管道
Φ114
6
60
17
管道
Φ108
6
57
18
管道
Φ≤89
2
\
注:
以上数值为采用双壁单影法透照时计算出的透照张数和有效长度,采用垂直透照方式重叠成像时一般应相隔120°或60°透照3次,采用单壁单影法周向曝光时,此时K=1,底片有效长度可依片长而定。
(9)RT编号方法如图20、图21、图22所示:
注:
1.底片示意图中各字母的含义:
A:
区号B:
管号D:
焊口号
E:
片位号RX:
返工标记X:
返工次数
H:
检测日期KY:
扩探标记Y:
扩探次数
W:
焊工号中心标记(小管径用):
2.识别标记包括区号、管号、焊口号、片位号、返工标记、扩探标记、返工次数、扩探次数和检测日期。
定位标记包括定位中心标记、搭接标记。
3.标记摆放要求齐全、规范,距离焊缝边缘5mm以上,紧贴于工件表面与胶片之间。
若业主对此有特殊要求,则另行约定、执行。
4.检测状态的标识符号○——合格×——返工——复验合格
位置:
距焊缝边缘100mm范围内。
方法:
有色记号笔标注。
(10)暗室处理
暗室处理采用自动洗片机为主,手洗为辅。
手洗操作方法见下面的操作程序。
A、显影
显影方法:
手工槽洗;
显影温度20±2℃;
显影时间4~6min。
注意事项:
显影前,测量显影液温度;充分搅动显影液;显影中,应不时作垂直方向的抖动。
B、停显或漂洗
停影液(水)停影时间2~3min强力抖动
C、定影
定影温度16~24℃;
定影时间10~15min;
注意事顶:
a定影前,测量定影液温度;充分搅拌定影液。
定影刚开始,要多次抖动,之后,每隔一定时间抖动一次;
b使用的定影液与新液相比,当定影时间为新液所需时间的两倍,视为失效,更换新液。
D、水洗
水洗温度:
16℃~22℃;
水洗时间:
15~30min;
水质要求:
流动、清洁;
水洗程序:
后水洗的底片放在流动水的后面。
E、干燥
干燥方法:
视环境温度选用自然干燥;
干燥程序:
润湿—→滴离—→干燥;
润湿液:
洗洁精水溶液;
润湿时间:
1min;
注意事项:
底片之间保持一定的间距。
(11)底片评定
A、设备环境条件:
评片室单独设置,室内光线暗淡。
室内照明不在底片上产生反射光。
冷光源强光观片灯应有足够亮度(观察黑度>4.0),且亮度可调;
B、底片质量要求:
a灵敏度检查:
象质计影象、型号、规格、摆放位置。
象质指数(Z)达到JB4730—94的表5-3规定的要求。
射线种类
底片黑度(D)
灰雾度(D0)
X射线
2.0~4.0
<0.3
γ射线
2.0~4.0
b黑度(D)检查:
c标记检查:
齐全、规范,位置适当,距焊缝边缘大于5mm;
d伪缺陷检查:
有效评定区域不允许有伪缺陷影象;
e背散射的检查:
较黑背景上,不得出现较淡的“B”的影象。
C、底片评定:
严格按照JB/T4730—2005标准对底片进行正确质量等级评定。
D、检测信息反馈:
以返工通知单形式及时、准确地与委托单位、相关部门反馈检测结果,以委托形式按规定进行扩探、复验。
E、资料整理
底片整理:
先排序后装袋。
同一焊口的底片,按检测位号由小到大的顺序;同管号的底片,按焊口号由小到大的顺序;同区的底片,按管号由小到大的顺序;依次排序、填袋、装袋、捆扎、归箱。
报告签发:
按容器编号、管号、规格、分区域出具报告;
报告摆放次序:
射线探伤一览表 →射线探伤综合报告→射线探伤报告
资料审核:
对照底片袋上记录的内容,审核底片的质量;审核焊缝质量等级评定。
依据检测委托单要求,审核检测比例、扩探比例执行情况;返工复验片与一次片位置的一致性;报告、底片的符合性;资料内容的准确性;签字人员资质的符合性。
报告发放必须及时准确,真实可靠,字体清晰,专业术语规范,报告内容符合JB/T4730—2005中的规定。
7.渗透检测(PT)工艺
(1)渗透检测方法:
采用溶剂去除型着色渗透剂—快干湿式显像剂。
(VC—S)
(2)检测设备:
A检测剂:
渗透剂(DH-RS)清洗剂/丙酮(HD-BS)显像剂(HD-EV)
B对比试块:
镀铬试块
(3)检测环境:
当被检部位温度低于15℃时,应先做对比试验;检测剂易燃、易爆,严禁明火;检测剂有毒,采取必要的通风措施;观察迹痕在被检表面可见光照度大于500lx条件下,应有充足的光线和照明。
(4)操作工艺
操作步骤
方法
温度℃
时间min
范围
喷距
mm
注意事项
预处理
表面清理;
预清洗。
—
—
检测部位四周外扩25mm
—
1.干燥;
2.检测面不被污染。
渗透
喷涂
刷涂
15~50
≥10
—
—
1.检测部位完全被渗透剂覆盖;
2.渗透过程中,保持润湿状态。
3.环温低于15℃,用对比试块修正时间。
清洗
擦拭
—
检测面全部擦净为止
—
—
1.不得往复擦拭;2.不得用清洗剂冲洗检测面;
3.防止过度清洗或清洗不足。
干燥
自然干燥
—
5~10
—
—
—
显象
喷涂
—
7~30
—
300~400
1.施加前摇均;
2.依次薄而均匀喷涂;
3.喷涂方向与检测面夹角30~
40°
4禁止在检测面上倾倒显象剂。
观察
肉眼(借助5~10倍放大镜)
—
0~30
—
—
1.观察时机在显象施加后;
2.检测面可见光照度大于500lx;
复验
同上
—
—
—
—
1.操作方法有误;2.返工部位.
后处理
布、纸擦除
—
—
检测面操作环境
—
1.残余显象剂;
2.检测废弃物。
(5)PT编号方法:
区号——容器编号、管号——焊口号
(6)检测状态标识:
○——合格×——返工——复验合格
(7)缺陷显示迹痕的判别
A、缺陷显示迹痕:
除确认外界因素或操作不当造成的显示迹痕之外,其它任何大于等于0.5mm的显示迹痕;
B、线性缺陷:
长宽比大于3的缺陷显示迹痕;
C、圆形缺陷:
长宽比小于等于3的缺陷显示迹痕;
D、横向缺陷:
缺陷显示迹痕长轴方向与被检件轴线或母线的夹角大于等于30°;
E、纵向缺陷:
缺陷显示迹痕长轴方向与被检件轴线或母线的夹角小于30°;
F、一条缺陷:
同一直线、间距≤2mm、至少2条缺陷显示迹痕视为一条缺陷,长度为各条缺陷之和加间距。
(8)缺陷显示迹痕等级评定
A、不允许存在的缺陷:
任何裂纹、白点;
B、不允许超标的缺陷:
单位mm
缺陷显示累积长度等级评定
Ⅰ
Ⅱ
Ⅲ
Ⅳ
评定区(35×100)(圆形缺陷)
≤1.5
≤4.5
≤8
大于Ⅲ级
线性缺陷
不允许
不允许
L≤4
大于Ⅲ级
C、执行标准JB/T4730.5—2005;
D、合格级别Ⅰ级;
E、检测记录:
依据检测批次,分区按管号填写,在管段图上标注检测位置,草图示意缺陷位置。
(9)检测报告的签发
依据检测委托单、记录,按管号分区出具检测报告,一式四份,交甲方2份原件、施工部和QA/QC部1份复印件,检测自留1份复印件。
由PT-Ⅱ、Ⅲ级人员签发、审核渗透检测报告。
摆放次序:
PT委托单——PT综合报告——渗透报告
8.磁粉检测(MT)工艺
(1)检测对象:
容器、管道焊缝表面或其它需要做磁粉检测的部位
(2)探伤仪:
磁轭式磁粉探伤仪(MP—A3)
(3)灵敏度试片:
A1-30/100
(4)磁化方法:
交流电磁轭式纵向磁化
(5)通电方式:
连续法
(6)通电时间:
1~3s
(7)磁化方向:
每一检测区域独立磁化次数≥2次,磁化方向相互垂直。
(8)磁悬液:
A、磁悬液配制:
按磁膏使用说明检测前,现场配制,搅拌均匀;
B、磁悬液组分:
黑磁膏+水+防锈剂;
C、磁悬液浓度:
10~20g/l;
D、磁悬液施加方法:
喷涂法;
E、施加磁悬液注意事项:
磁悬液在通电时间内施加完毕;磁悬液流速以不破坏成形的磁痕显示为度;先停施液,后断电,时差1s。
(9)有效磁化区域:
两磁极连线两侧各50mm范围内。
多次磁化,相邻磁化区域应有至少15mm重叠。
(10)磁粉检测灵敏度的校验:
将试片有人工缺陷的一面紧贴检测面摆放在磁化区域中,用透明胶带四周固定,但不覆盖人工缺陷。
一边磁化被检工件,一边施加磁悬液,试片上人工缺陷磁痕能清晰显示,说明检测灵敏度符合规定的要求。
(11)现场检测操作
按MT工艺流程进行。
(12)磁痕的观察、识别
A、观察方法:
肉眼或借助5~10放大镜观察。
B、环境要求:
检测面可见光照度≥500lx
C、缺陷磁痕:
除确认磁痕是非相关磁痕显示外,其它长度大于等于0.5mm磁痕显示均为缺陷磁痕;
D、线性缺陷:
长宽比大于3的缺陷磁痕;
E、圆形缺陷:
长宽比小于等于3的缺陷磁痕;
F、横向缺陷:
缺陷磁痕长轴方向与被检件轴线或母线的夹角大于等于30°;
G、纵向缺陷:
缺陷磁痕长轴方向与被检件轴线或母线的夹角小于30°;
一条缺陷:
同一直线、间距≤2mm、至少2条缺陷磁痕视为一条缺陷,长度为各条缺陷之和加间距。
(13)缺陷磁痕等级评定
A、不允许存在的缺陷:
裂纹和白点
B、不允许超标的缺陷:
单位mm
缺陷显示累积长度等级评定
Ⅰ
Ⅱ
Ⅲ
Ⅳ
评定区(35×100)(圆形缺陷)
≤1.5
≤3.0
≤4.5
大于Ⅲ级
线性缺陷
不允许
不允许
L≤3
大于Ⅲ级
C、执行标准JB/T4730—2005
D、合格级别Ⅰ级
(14)检测记录:
按检件类型、检测批次,记录所有缺陷磁痕的尺寸、数量、产生部位并图示。
采用胶带法对缺陷磁痕做永久性记录。
(15)复验
A、复验时机
检测结束时,验证检测灵敏度不符合要求;
检测中,操作方法有误;
返工部位;
有疑义或认为需要。
B、复验方法:
同原方法。
(16)检测报告的签发
依据检测委托单、记录,按检测批次、检件类型出具MT报告,一式四份,交甲方2份原件、施工部和QA/QC部1份复印件,检测自留1份复印件。
由MT-Ⅱ级人员认真规范地签发、审核磁粉检测报告。
摆放次序:
MT委托单——MT情况一览表——MT报告
9.无损检测人员资格要求
(1)无损检测人员应具备国家锅炉压力容器安全监察部门颁发的检测资格证书。
(2)Ⅰ级检测资格人员只能在Ⅱ级或Ⅱ级以上资格人员指导和监督下从事检测操作,检测结果评定和报告签发及审核由Ⅱ级或Ⅲ级人员承担。
(3)检测人员应认真做好设备的维护、保养工作,执行安全防护制度。
(4)检测人员的校正视力不低于1.0,并要求评片人员距离400mm能读出高为0.5mm,间隔0.5mm的一组印刷体字母。
(5)无损检测人员要牢固树立“质量第一”的观念,做到不漏检、不误判,严格执行检测标准。
(6)无损检测人员在实施检验前,须了解和熟悉有关监察规程、验收标准、技术文件要求,熟悉被检工件的规格、材质及其制造工艺、焊接工艺、检测工艺。
10、质量保证措施
10.1实行质量责任制:
项目经理是本工程施工质量的第一责任人,施工队队长是本队施工质量的第一责任人,无损检测责任工程师是本专业质量责任人员,各部门负责人要按分工认真履行质量职责,施工中严格按国家、行业、地方强制性标准规范要求进行管理与验收。
10.2“技术交底”制。
对关健工序的施工,在开工前,必须由技术质量部门组织对施工队进行交底,一般工序由施工队技术员对施工班组进行交底,并做好技术交底记录。
10.3贯彻质量“三检制”及“质量大检查”制度。
检查前,先明确检查内容、抽查数量、检测方式、检查量具及允许偏差值。
10.4为认真贯彻“质量第一,奖优罚劣”的方针政策,把工程质量好坏与经济效益有机结合起来,项目部除按照本工程成本核算计奖外,另设专项质量奖,用于奖励对提高工程焊接质量有贡献的单位和个人,并坚持以教育为主,以精神鼓励为辅的原则。
10.5贯彻“质量分析会”制度。
每月定期召开质量分析会,认真分析从施工现场收集到的各种不合格信息,及时采取纠正和预防措施,排除质量隐患。
10.6贯彻“工序交接”制度。
工序交接时,必须由相应专业的专职质检员与上、下道工序的负责人到现场进行交接品的质量验收,避免上道不合格品转入下一道工序。
10.7实行“全过程监督”制。
本专业的专职质检员每天挂牌在施工现场巡视,加大监督力度。
10.8实行“质量一票否决”制。
对于质量低劣的产品,质检人员可独立行使质量否决权,对施工责任单位发出“黄牌”或“红牌”警告,并责令其整改,直至合格为止。
10.9认真执行业主和监理公司下发的质量管理及监督制度。
对业主及监理代表检查发现的质量问题均应不折不扣进行整改,直到合格为止。
11风险识别及预防措施
作业内容和正确程序说明
1、管道检测;2、再生斜管焊缝检测;3、进口烟道检测;4、2个余锅膨胀节焊缝检测;5、1个小旁路膨胀节焊缝检测。
作业活动过程中可能发生的事故
事故名称
触发原因
削减和控制措施
物 体
打 击
高处不稳妥物体坠落
作业中工具脱手坠落
清理高处废弃物
安全使用工具
设置警戒标识
起重伤害
起重吊物坠落,绑扎不合格;违章指挥;吊装物上配件没有固定,坠落伤人
吊装应进行技术方案和安全注意事项交底;决不允许超负荷使用吊装绳索和吊装滑轮
高空坠落
作业人员未系安全带或安全带系挂不符合安全要求;作业现场有孔、坑、洞,防护措施不完善、没有警示标示
安全带系挂要符合安全要求;完善作业现场有孔、坑、洞,防护措施、设警示标示
触电
施工破坏电气线路,电缆接头土埋、水泡;电气设备外壳未接地,保护接地接零不合格
线路架空或电缆麦蒂铺设符合要求,电缆接头应抬高,做隔离措施;所有用电设备金属外壳均应有可靠接地保护
机械、伤害
倒链、千斤顶内在缺陷或使用方法不正确;设备材料表面或地面有突出物;机械设备试运转发生异常损伤伤人
倒链、千斤顶使用前要进行检查,按规范正确使用,作业前及时处理设备材料表面缺陷,设备试运转时设置警戒区
针对违反法律法规标准规章的不符合及可能发生的事故,准备采取的风险削减和控制措施
1.施工要严格遵守操作规程,发现隐患及时报告,始终安全第一位。
2.施工人员进入现场必须佩带安全帽,高空作业要带安全带,并把挂扣锁到牢固的构件上。
3.严禁高空落物或抛物,带上高处的物品要妥善保管。
4.吊装作业要进行联合检查,设置区域警戒范围。
事故发生后准备采取的应急补救措施
疏散无关人员,抢救受伤人员,防止二次事故发生,调集救助力量,控制事态发展。
迅速向上级报告,保持通讯畅通,随时掌握险情动态
12、安全措施
12.1现场施工安全应符合业主有关规定,并按公司《安全管理标准》严格执行。
12.2安全管理实施一票否决制,“谁主管,谁负责”,责任承包,奖罚分明。
12.3安全部门负责对施工人员进行纪律和安全教育,并对施工生产过程实施检查和监督。
12.4施工现场设置明显的标志,防止火种窜动及无关人员进入施工现场。
12.5安全标志:
本工程项目部在施工现场设立工序、分区等标示牌,设立安全生产和操作规程牌,在有潜在危险的地方设立明显的安全警示标志。
12.6对施工作业区域内,各种防护设施、安全标志齐全,未经监理和业主批准,不得移动或拆除。
12.7按业主指定的通道进出厂,并保持施工现场道路畅通。
12.8照明:
若必须在晚上工作时,应有足够的照明强度,以使工作能够安全、顺利完成。
12.9个人防护设备:
所有施工人员必须正确使用个人防护设备。
12.10现场易燃、易爆、有毒物质的存放(如汽油、柴油、油漆、酸等)必须设专库专人保管,并设置明显的标记
12.11人员管理:
无损检测人员应持有效证件上岗。
12.12高空作业应佩带安全带和设置安全网。