原液着色技术在牛仔面料上的开发应用.docx
《原液着色技术在牛仔面料上的开发应用.docx》由会员分享,可在线阅读,更多相关《原液着色技术在牛仔面料上的开发应用.docx(14页珍藏版)》请在冰豆网上搜索。
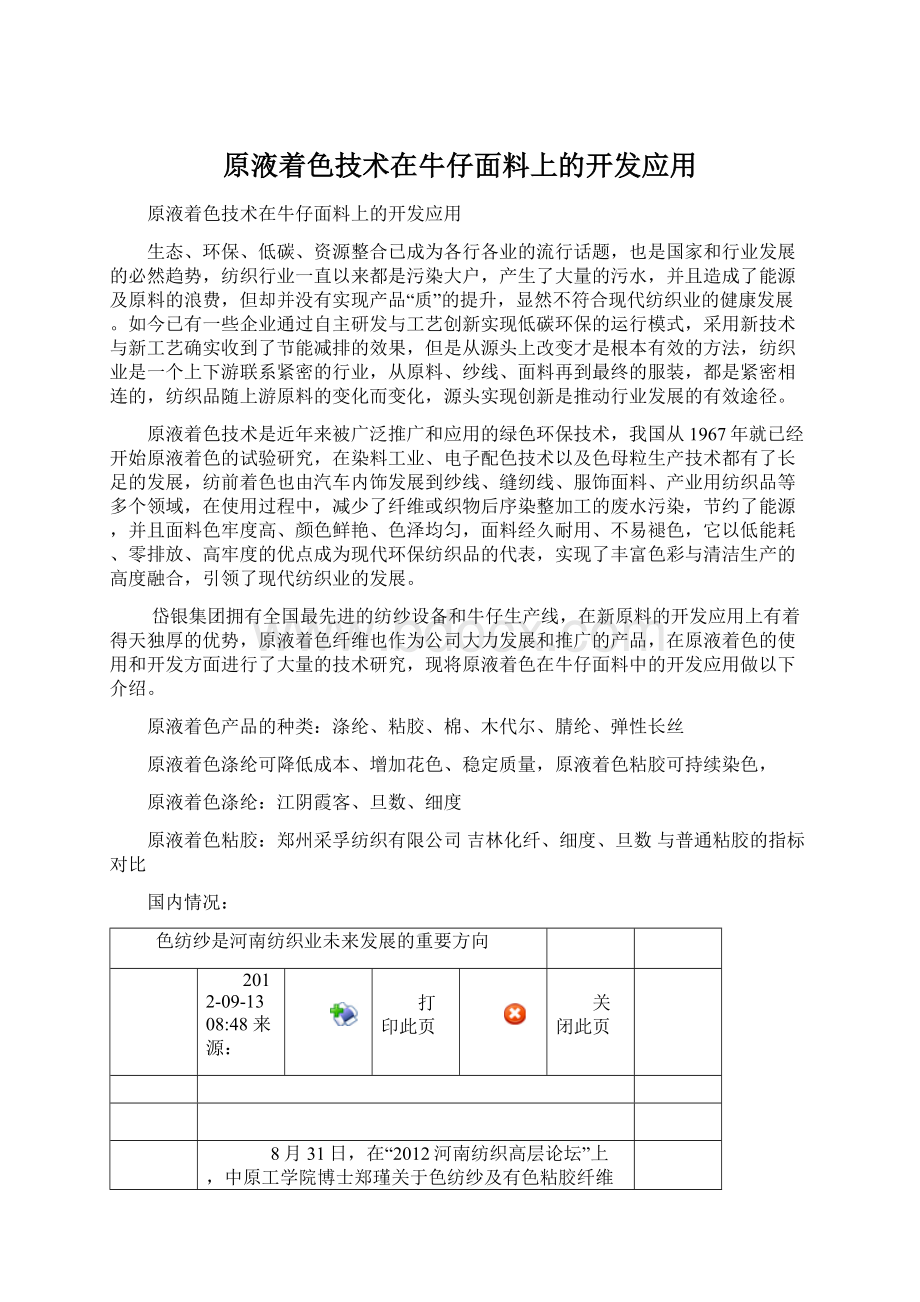
原液着色技术在牛仔面料上的开发应用
原液着色技术在牛仔面料上的开发应用
生态、环保、低碳、资源整合已成为各行各业的流行话题,也是国家和行业发展的必然趋势,纺织行业一直以来都是污染大户,产生了大量的污水,并且造成了能源及原料的浪费,但却并没有实现产品“质”的提升,显然不符合现代纺织业的健康发展。
如今已有一些企业通过自主研发与工艺创新实现低碳环保的运行模式,采用新技术与新工艺确实收到了节能减排的效果,但是从源头上改变才是根本有效的方法,纺织业是一个上下游联系紧密的行业,从原料、纱线、面料再到最终的服装,都是紧密相连的,纺织品随上游原料的变化而变化,源头实现创新是推动行业发展的有效途径。
原液着色技术是近年来被广泛推广和应用的绿色环保技术,我国从1967年就已经开始原液着色的试验研究,在染料工业、电子配色技术以及色母粒生产技术都有了长足的发展,纺前着色也由汽车内饰发展到纱线、缝纫线、服饰面料、产业用纺织品等多个领域,在使用过程中,减少了纤维或织物后序染整加工的废水污染,节约了能源,并且面料色牢度高、颜色鲜艳、色泽均匀,面料经久耐用、不易褪色,它以低能耗、零排放、高牢度的优点成为现代环保纺织品的代表,实现了丰富色彩与清洁生产的高度融合,引领了现代纺织业的发展。
岱银集团拥有全国最先进的纺纱设备和牛仔生产线,在新原料的开发应用上有着得天独厚的优势,原液着色纤维也作为公司大力发展和推广的产品,在原液着色的使用和开发方面进行了大量的技术研究,现将原液着色在牛仔面料中的开发应用做以下介绍。
原液着色产品的种类:
涤纶、粘胶、棉、木代尔、腈纶、弹性长丝
原液着色涤纶可降低成本、增加花色、稳定质量,原液着色粘胶可持续染色,
原液着色涤纶:
江阴霞客、旦数、细度
原液着色粘胶:
郑州采孚纺织有限公司吉林化纤、细度、旦数与普通粘胶的指标对比
国内情况:
色纺纱是河南纺织业未来发展的重要方向
2012-09-1308:
48来源:
打印此页
关闭此页
8月31日,在“2012河南纺织高层论坛”上,中原工学院博士郑瑾关于色纺纱及有色粘胶纤维的演讲引起了与会代表的关注。
365纱线网记者专访了郑瑾,请他详细解读了色纺纱及有色粘胶纤维的发展。
记者:
色纺纱及有色粘胶纤维对减少环境污染、节能环保有哪些好处?
郑瑾:
色纺纱由于纺纱前所用的纤维原料均通过染色或原液着色,故纺成纱后在针织与机织加工成织物后一般不需再经染色加工,既缩短了加工工序又减少了环境污染,符合绿色环保的要求。
色纺纱仅对35%~40%的棉花染色,通过混纺可获得l00%彩色棉纱,全产业链生产成本下降。
而若采用以原液着色技术得到的彩色化纤为色纺原料,能使生产过程“零排放”。
记者:
色纺纱的发展情况如何?
郑瑾:
色纺纱起源于欧洲,最早应用于毛纺,后来逐步在棉纺、麻纺等行业推广应用。
色纺纱行业在国内起步较晚,是纺织行业中一个新兴分支行业。
色纺产品被逐渐引入中国后,色纺产业得到超常发展。
1984,色纺基本空白。
但进入20世纪90年代后,色纺进入高速发展阶段。
色纺纱生产能力从初期的10万锭左右增加到2009年的约300万锭,成为世界色纺纱市场的主导者。
据365纱线网了解,目前,国内色纺纱生产产能已增加至600万锭。
记者:
既然色纺纱发展这么快,它的特点和优势是什么?
郑瑾:
以色纺纱为原料制造产品,有利于下游用户进行环保和节能生产。
从纺纱到织布,用色纺纱生产同其他工艺相比,可以减少将近1/3的废水排放,并在节约电能、蒸汽等方面具有明显优势。
色纺纱产品颜色时尚。
色纺纱的本源就是自然颜色,在纺纱过程中,把不同颜色的纤维经过充分、均匀地混和后,纺制成具有独特混色效果的色纱。
混色纺纱通过色纤维的混和来获得一种独特的色彩,呈现出“空间混合”的效果,色彩透明、丰富,并且有层次的变化,富于立体感,从而产生人们希望的艺术效果。
色纺纱做成服装后颜色含蓄、自然,具有较强的朦胧感。
这种自然的、返璞归真的风格符合现代个性化、多样化、时尚化的服装发展趋势和消费趋势。
色纺纱可以实现多种原料混纺,产品更丰富、更具竞争力。
色纺纱工艺能够做出由棉、麻、毛、丝、化纤等多种原料混纺而成的纱线,结合流行色的演绎,能够提供源源不断的创新产品。
记者:
有色粘胶纤维的技术创新体现在哪里?
郑瑾:
采用传统工艺生产1吨染色布或染色纱通常需要消耗100吨水、500度电、6立方米蒸汽,而有色粘胶纤维的生产工艺相比较于白色粘胶纤维而言,每吨仅增加0.2吨水、5度电,不耗费蒸汽,不产生污水。
对全国200余万吨粘胶短纤维产能来说,该工艺的社会价值、环保效益将不可估量。
其技术创新在于,从粘胶纤维的生产源头开始染色,生产四种单色的粘胶短纤维,代替传统的白色粘胶短纤维。
然后将四种基色纤维按比例组合,在下游色纺纱企业生产出各种颜色的纱线,最后织布、制衣。
该工艺去掉了传统的染色流程,既适合品种单一稳定、生产量大的粘胶纤维企业,也符合品种多、生产量小的下游色纱生产企业生产特点。
而传统上,两者在颜色和产量上一直存在难以调和的矛盾。
有色粘胶纤维在市场上有着明显的优势。
一是节能减排。
“原液着色”型粘胶纤维的着色过程能耗低、污染小,不耗费蒸汽,不产生污水。
二是加工成本低。
纤维“后染”费用平均为7500元/吨,而“原液着色”型有色粘胶纤维仅比白色粘胶纤维增加4000元/吨。
即使不去计算因此而减少的污水排放费用及对环境的影响,也会使色纺纱企业的产品更具有市场竞争力及更大利润空间。
三是色牢度高。
“后染”型有色纤维各项色牢度平均在3级左右,而“原液着色”型有色粘胶纤维各项色牢度均在4级以上。
四是可纺性好。
“后染”型有色纤维染色后强度损失大,不利于纺纱加工,而“原液着色”型有色粘胶纤维能保持与普通粘胶纤维相同的力学性能,可纺性好。
五是混纺面料性能更优。
在纯棉色纺面料中添加10%~30%有色纤维素纤维,可使面料获得更佳的手感、吸湿性、及舒适程度,并使面料的抗折皱能力增强。
记者:
这两种产品对河南纺织调整结构、解决同质化问题有何积极意义?
郑瑾:
河南纺织业应该有自己的特色。
当前河南纺纱企业95%的产品是中低档棉纱,同质化严重,在市场上竞争力不强,河南应该有鲜明的区域产品定位。
色纺纱行业近10年规模增加了10倍,平均每年以22%~30%的速度增长。
色纺纱是未来发展的重要方向。
面料生产一直是河南纺织业发展的短板,而作为内陆省份,河南发展印染业存在着先天不足,缺水以及对环境影响的考虑,导致河南不可能去大力发展印染产能。
河南纺织业必须走出一条有自己特色的发展之路,形成“有色粘胶纤维——粘胶色纺纱——色纺面料”产业链将是不错的选择。
国外情况:
兰精木代尔原液染色纤维,
原液着色的PTT/PET并列复合弹性丝而言,它又解决了白丝后染造成的弹性不匀、颜色不匀、色牢度低和加工费用高的问题;采用原液着色技术可使色丝售价降低到进口白丝后染产品的50%~60%,具有显著的经济效益;PTT/PET复合弹性长丝在面料中的施加技术及弹性控制技术,可赋予面料抗皱性、适体性和舒适性,提高了面料的档次和附加值。
PTT的应用可以降低用毛等级,节约企业原料成本;并且可以降低染色时的能量消耗,原液着色可使色丝成本降低50%,提高了产品的附加值。
PTT的弹性、柔软的手感、耐脏污性能会使得PTT/毛混纺产品比PET/毛混纺产品有更好的服用性能和销售价格。
陈丽芬:
PTT的弹性稳定、手感柔软,提升了毛/聚酯纤维混纺产品的档次。
毛纺行业的国际竞争激烈,现在我们用新型复合面料开发出更多民用功能性产品,既降低成本又可以开拓市场,实实在在地提高了企业的竞争力。
纤维素原液着色技术实现了纤维素制品纺和染的一体化生产,解决了染料染色中存在日晒牢度差、色泽不匀等弊病,省略了下游产品的染色环节,减少了水和能源的消耗,是一项值得推广和发展的纤维染色技术。
本文阐述和分析了纤维素纤维原液着色技术中着色剂、溶解纤维素纤维的溶剂以及着色剂与纺丝原液相容性基础问题的最新研究进展,认为超细颜料或超细包覆颜料是纤维素纤维原液着色着色剂的主要发展方向
新变化催生新期待,催生对创意设计人才的种种“新期待”。
霞客公司技术和产品介绍
我公司现主要产品有:
无染彩纤、无染彩棉和无染彩纱。
我公司主营有色纤维和有色多纤维混纺纱线,集研发、生产、销售、外贸进出口于一体。
公司现经营纱锭40万枚,年产霞客彩纤20万吨,无染彩纱10万吨,无染彩棉20万吨。
员工3600人,是具有6大系列产品,2000多个品种的彩色“超市”。
旗下产品先后获得中国纺织工业协会产品开发贡献奖、改革开放三十年推动纺织产业升级重大技术进步奖,同时远销欧美、日韩、西亚、东南亚等国家和地区,享有较高的知名度。
霞客牌商标是“江苏省知名商标”,荣获中国首批环保质量信得过重点品牌。
公司被授予“中国环保产业协会会员”、“中国流行色应用示范基地”和“中国纺织工程协会环保技术研发中心”。
“国家环保彩纤产品开发基地”。
1、无染彩纤原液着色在线添加技术
霞客彩纤(有色涤纶短纤)是采用“原液着色”技术,在纺丝过程中熔体状态下通过在线添加色母粒混合着色生产的彩色大化纤。
该技术及工艺是纤维生产通过在密封环境下利用“原液着色”技术实现聚酯着色,使用色母粒渗入纤维内部的注射式着色,其生产出的各种环保彩纤产品质量高,牢度好,耐水洗,抗摩擦,无色差。
“熔体直纺在线添加”技术是具有国际领先水平的高新技术和集成性创新工艺,整个过程在完全密封的系统内完成,使纤维的色泽状况和差别化程度更臻于完美。
该技术突破了印染行业的传统工艺,替代了纺织印染生产环节,圆满实现了生产流程中的“零排放”,实现了整个生产过程中的清洁环保,是纺织行业的一次革命性变革。
公司现有涤纶短纤产品规格:
1.33dtex*38mm 1.56dtex*38mm 2.22dtex*38mm
2.22dtex*51mm 2.78dtex*51mm 2.78dtex*65mm
常规颜色有:
本白、特黑、漂白、特白
浅色:
豆绿、果绿、湖兰、水灰、米黄、深米黄、杏黄
中色:
深青灰、烟灰、松子灰、老红烟灰、旦黄、紫罗兰、铁灰
深色:
玫红、桔红、金黄、红咖啡、翠绿、宝兰、桔红
特别色:
大红、深藏青、鲜枣红
无染彩纤色牢度均在3级和3级以上,符合GB18401-2003《国家纺织产品基本技术安全规范》
2、无染彩棉多纤维配置化
以霞客彩纤(有色涤纶短纤)为主体,与其他各种天然和人造纤维进行混合配色,从而形成差别化功能型的“无染彩棉”。
“无染彩棉”实现了全过程的无污染生产和后道企业的无需染色,同时满足了下游企业对色彩以及功能的要求。
我们在此基础上开发了“无染彩纱”,在纺织行业中开辟了一条绿色环保之路。
“无染彩棉”不仅解决了生产过程无污染、多纤维混纺的套色难题,而且后道产业链无需染色,其核心价值主要体现在三个方面:
(1)保护环境、实施环保
从环境效益上讲,常规的纺织品一般经过染整处理,进行着色。
而印染行业不仅需要消耗大量的淡水资源,而且是重污染作业,其废水很难处理,已成为对环境造成严重污染的行业之一。
霞客环保利用“在线添加熔体直纺工艺”生产的差别化环保彩纤,采用“原液着色”技术,在纺丝过程中通过在线添加色母粒,整个过程在完全密闭的系统内完成,从投入到产出整个工艺过程无污染,从根本上规避了纺织产品产业链中污染最严重的印染环节对环境的影响,实现了污染零排放,可以说是纺织行业的一项工艺革命和环保创新。
(2)节能减排、降低成本
无染彩棉的使用,减少了印染工序,节水、节电、节汽、减少设备投入和用工,缩短流程时间,使整个产业链降低成本15%以上。
(3)丰富色彩、美化生活
无染彩棉的诞生赋予了彩色合成纤维特定的内涵,色彩必须以环境保护为第一要义;色彩必须和经济发展紧密结合,必须与社会生活和谐共存;色彩必须用传统文化凸显时尚。
通过“三元无限”配纤配色的组合,可以实现色彩的无限供给,丰富了纺织面料的色彩世界,满足了人们对色彩的追求。
而“天人合一”则通过混纺、交织使不同的纤维原料在性能上得到互补,其独特的立体效应与质感,成为时装、童装、睡衣和家用纺织品的时尚表现。
同时无染彩棉能通过在线添加功能母粒赋予色织面料全新的功能,如免烫、抗菌、防静电、防紫外线等,使无染彩棉有较高的技术附加值。
3、无染彩纱(线)
(1)采用大化纤色纤维纺纱,减少环境污染,节能,价格较染色纱优惠,手感柔软,强力高,色牢度好,色彩鲜艳.适合针织,织布,服饰等用纱.
(2)以彩色涤纶大化为基础,进行多纤维多色彩混配纺纱,减少生产成本,适合针织毛衫和梭织用纱。
(3)常规品种有六大色系上千个品种,主要支数从16S到60支,常规库存产品有21S、32S、40S等。
4、霞客纺料配置中心
霞客纺料配置中心利用无染彩棉,建立“配色、配棉、配功能、配技术、配物流”的新型商业运营模式,实施ERP信息系统整合全过程管理,提升企业效率,为纺织产业链企业提供全方位、一条龙、一站式、一体化、保姆式的专业化服务。
同时也为纺织企业在实际运作中带来了实惠:
(1)减少后道企业生产周期,实现快速反应,比传统流程大约节省2/3的时间
(2)满足了客户对小批量、多品种的需求
(3)解决了客户尾料积压
(4)为客户解决色彩配置、色卡制作和色彩管理
(5)减少了后道企业采购环节、生产环节,从而减少了资金占用等方面的成本
(6)适应集约化、规模化、专业化运作,减少了客户组织生产的时间和费用等
三、原液着色纤维在牛仔面料上的应用情况:
3.1原液着色涤纶牛仔面料的开发
涤纶作为纺织业应用最广的纺织材料,因其价格优势、较好的强力、良好的光泽、面料清晰的纹路,被广泛的应用在各种面料上,但在牛仔面料上的使用数量还有限,由于牛仔面料染色使用的靛蓝和硫化染料对涤纶不上染,因此一直应用在纬纱中,含量也仅仅占25%左右。
随着原液着色技术的发展,涤纶作为可纺性很强的合成纤维,为其应用于牛仔面料的经纱中提供了条件,将原液着色涤纶与棉以混纺或AB纱的方式纺纱,利用靛蓝或硫化染料染棉不染涤的特点,将棉纤维染成与涤纶相同的颜色,实现了涤纶在牛仔经纱上的应用。
1、在原液着色涤纶牛仔面料的开发中,主要从以下几个方面进行研究:
(1)涤纶与棉混纺比例的确定:
在纺纱时涤纶与棉纤维的混纺比例以70/30、60/40、50/50三种比例进行纺纱和染色试验,试验结果为50/50的比例更容易控制染色均匀度,因此最终纱线以原液着色产品以涤纶/棉50/50的比例进行设计。
(2)纺纱形式的确定:
以混纺和AB纱两种纺纱形式进行试验,通过染色试验得出以下结论:
A、染颜色较鲜艳的兰色时,涤纶与棉纤维混纺要比AB纱的形式更容易获得均匀的染色效果,相互混合的结合方式,也有利于提高面料整体的色牢度。
B、染颜色很深的黑色时,由于在后续面料的水洗时基本是保色洗的状态,选择何种纺纱形式影响较小,混纺和AB纱均可。
(3)颜色一致性的控制:
牛仔服装是需要经过水洗来体现风格、满足服用要求的,由于两种原料的水洗色牢度不同,原液着色涤纶色牢度高,而棉纤维所使用的染料色牢度低,容易引起条花、染色不匀等疵点,为保证两种原料着色率的一致性,棉纤维上染率的调整是此类产品开发的重点,因此棉纤维染色的深度,需要根据色母粒涤纶的颜色来确定,考虑到水洗掉色程度的差异,一般是棉纤维的染色深度需偏高掌握,比正常需要达到的染色深度要高5—8%。
(4)面料颜色鲜艳度的问题:
牛仔面料中棉纤维的染色基本都是靛蓝或硫化染料染色,因此其色光不如色母粒涤纶鲜艳,如何根据需要选择合适的颜色,是决定面料档次和开发产品的关键。
为此,我们在颜色的选择上,多以传统的牛仔色蓝色和黑色为主,一方面这两种颜色生产容易控制,另一方面也保持了牛仔的本色。
(5)染色工艺为:
蓝涤/C50/5018环+14.5竹AB纱染色工艺:
精炼槽温度
40℃±1
精炼槽助剂
4g/L渗透剂;3g/L片碱
靛蓝g/L
1.85-1.9
保险粉g/L
0.7-0.8
车速m/min
22
烧碱g/L
2.9-3.1
工艺路线:
1精炼→1水洗→4兰→3水洗
(6)原液着色涤纶牛仔面料投放市场后,无论在价格方面、生产成本还是风格方面,都具有明显的竞争优势,主要表现在以下几个方面:
A、提高了生产效率:
牛仔面料的生产流程长,纱线要经过多道加工,因为涤纶的引用,提高了纱线强力,减少了断头,提高了织造效率。
相同纱支指标对比数据为:
品种
纱线
回潮
重量
强力
断裂强度
断裂伸长率
最低
捻度
捻不匀
%
偏差
CV%
CN/Tex
%
强度
捻/10cm
%
DY1926A
混纺10环
3.5
-0.1
3.3
18.7
11.3
17.1
46
2.6
DY1060
棉10环
5.9
0.9
7.6
13.9
5.8
11.7
49.8
4.1
DY1926
混纺10竹
3.4
0.1
6.5
14.2
8.9
12.5
47.6
3.5
DY1311
棉10竹
7.8
0.5
6.8
13
6.1
11.6
50.2
8.9
DY1933
AB纱16环
3.6
-0.2
4
13.8
8.9
12.6
56.4
2.9
DY1919
棉16环
8.2
0.5
8.1
15.8
6.6
13.4
56.7
2.7
DY1933
AB纱13竹
3.6
0.6
5.3
11.4
7.7
10.2
54
3.5
DY1558
棉13竹
8.4
-0.2
6.6
15.8
6
14.5
54.9
7.6
由以上数据可看出:
原液着色回潮率比棉小、重量偏差接近、强力不匀率小、最低断强高、捻度的不匀率低,因此原液着色纱线质量的综合指标比棉要好,更利于各个环节的质量控制。
B、减少了染化料的消耗:
原液着色涤纶无需再染色,只需对棉纤维进行染色即可,这样可减少50%的染料消耗,同时要达到同样的染色深度,与纯棉纱线相比染料可减少20%的用量,节约了染色成本,减少了污水排放。
C、减少染槽数量:
硫化染料的染色浓度和染色温度都比较高,因此无需很多染槽即可达到设计的染色深度,在这种操作方式下,一方面稳定了染色过程的质量控制,另一方面也减少了排污的数量。
D、节约了处理费用:
原液着色纤维与棉混纺使用,无需经固色处理,即可达到或超越经过固色处理的面料要求。
E、加工工序的简化:
涤纶具有很好的光泽度,因此此类面料无需进行丝光即可达到丝光的效果。
原液着色涤纶引入到牛仔面料的经纱中,突破了牛仔经纱只能为纤维素纤维的现状,同时提高了涤纶在牛仔面料中的含量,可达到了50%以上,且具有超强棉感,不影响牛仔面料使用的舒适性,而且还提高了速干性,从染色费用、原料费用、丝光效果费用、提高色牢度费用等方面都有很大的优势,其成纱质量好、强度高、色泽均匀、光泽度好、免丝光等优点更是传统产品无法具备的,原液着色技术使牛仔面料的开发进入一种高比例涤纶含量的时代。
3.2原液着色粘胶牛仔面料的开发:
粘胶纤维在牛仔面料上的应用很广泛,尤其是其柔软的手感、亮丽的光泽、优良的吸湿性和舒适性,更是奠定它在牛仔原料中的地位,仅次于棉纤维,尤其是近年来高弹牛仔女装的盛行,更是被众多牛仔面料研发人员所青睐。
常规粘棉混纺牛仔面料,虽然能满足手感的需要,但是在色彩方面有局限,粘胶和棉纤维都属于纤维素纤维,因此染色方法、染色效果以及牛仔的水洗效果基本接近,很难实现大的变化。
原液着色粘胶是用专用环保型着色剂,经过特殊的工艺处理后,应用电子配色和纺前注射技术,使色浆均匀地分散在粘胶中而生产出的有色纤维。
原液着色粘胶与棉混纺后,通过套染靛蓝或硫化类染料,赋予面料所需要的表面色,利用硫化染料不耐漂,而原液着色粘胶漂洗后不变色的优点,可通过不同的水洗工艺获得具有多层色彩丰富的水洗风格,原液着色粘胶纤维有以下几方面的特性:
(1)优越的环保性能:
使用的着色剂是一种纯天然碳黑染料,该染料对人体和环境是决对安全的,避免了由于使用其它化学染料对人体皮肤造成损害,为下游用户的生产提供了诸多便利条件,减少了因坯布染色而产生的污染。
(2)优良的色牢性能:
纤维成型过程中直接结合在纤维内部,染料被包裹在纤维壁中,因此与普通后染色纤维相比有较高的色牢度,织物耐洗涤、不褪色、耐干、湿摩擦性能明显提高,也被用户誉为“不退色”纤维。
(3)色泽均匀美观:
减少了因织物染色中出现的泛黄、花染现象,提高了制品品质。
(4)节约能耗:
经济效益可观。
原液着色粘胶纤维与棉混纺,染色方面在操作上不受颜色的限制,并且色牢度高、着色鲜艳、耐水洗和漂洗,而且可运用原液着色纤维色牢度高,而硫化色不耐漂洗的差距,实现一款多色、渐变的、色彩层次感强的牛仔面料,使女装牛仔服装个性鲜明,更加符合流行的主题,主要方案设计要点为:
1、纺纱工序:
女装多以色彩艳丽为主,因此原液着色粘胶的颜色多以鲜艳的红色、黄色、蓝色等为主,因此要求棉纤维的配棉较高,采用精梳配棉,以减少粗细节,提高条干的均匀度、色彩的明亮度。
2、染色方案:
原液着色粘胶与棉纤维混纺,其设计理念是利用原液着色粘胶的高水洗色牢度来实现面料漂洗后的鲜艳风格,因此在制定染色方案时,总体方向为,面料表面为传统的牛仔色,如黑色、深蓝色,并且可通过水洗进行处理掉,最终裸露色牢度高的、鲜艳的原液着色粘胶的颜色,达到不一样的多层色彩的效果,这也是原液着色粘胶最核心的开发重点。
原液着色粘胶渐变牛仔面料的开发,主要是颜色的开发,如何发挥母粒粘胶的作用,选择合适的表面色,保护色母粒粘胶的底色不被沾污,保证漂洗后的鲜艳度是开发的关键,以蓝色和黄色为例,在染色方案的确定上,选择了以下几种:
(1)蓝色:
染靛蓝、染靛蓝后套黑、直接套黑 三种方案
结果表明,蓝色无论深度如何,套染不同染色深度的靛蓝后再以硫化染料作为表面色的补充,是比较合理的,面料颜色从深到浅,且底色鲜艳,是靛蓝打底所不能达到的。
(2)黄色:
黄色色泽鲜艳、明快,因此为了突出漂洗后的颜色,在套染黄色时确定了诸多方案,从深至浅,进行优选,总体方向追求漂洗后能呈现艳丽的黄色。
几种试验方案为:
染料浓度均为8g/L
A、传统牛仔色:
染靛蓝、染靛蓝后套硫化黑、直接套硫化黑三种
B、深色调主题:
染硫化深蓝、染硫化深蓝后套硫化黑两种
C、艳蓝色调:
染硫化蓝2BN、染硫化蓝2BN后套硫化黑
D、清新明快色调:
染硫化新蓝、染硫化新蓝后套黑
E、高贵宝蓝:
染硫化宝蓝、染硫化宝蓝后套黑
经染色后漂洗的试验表明,8g/L中等浓度的浅色硫化新蓝,漂洗后黄色最为鲜艳,浅色调一方面对黄色母粒粘胶起到保护的作用,另一方面比较容易漂洗掉,表面再套染硫化黑,能够满足面料的表面色光。
3、染色工艺设计:
用原液着色粘胶纤维作为底色,比任何浓度的靛蓝或硫化染料都要鲜艳,漂洗后牢度都高,原液着色粘胶与棉混纺,只需赋予其较深的表面色,套染靛蓝后再染硫化染料,或直接用1—2道硫化染料,都能赋予面料较深的表面色,这样不仅可有效减少染槽个数,也可简化染色过程,减少排污。
具体染色工艺为:
棉/兰粘胶70/30(12环+12竹)染色工艺:
精炼槽温度
40℃±1
精炼槽助剂
4g/L渗透剂3g/L片碱
硫化温度
95℃±1
硫化含量g/L
12-12.5