风机叶片.docx
《风机叶片.docx》由会员分享,可在线阅读,更多相关《风机叶片.docx(14页珍藏版)》请在冰豆网上搜索。
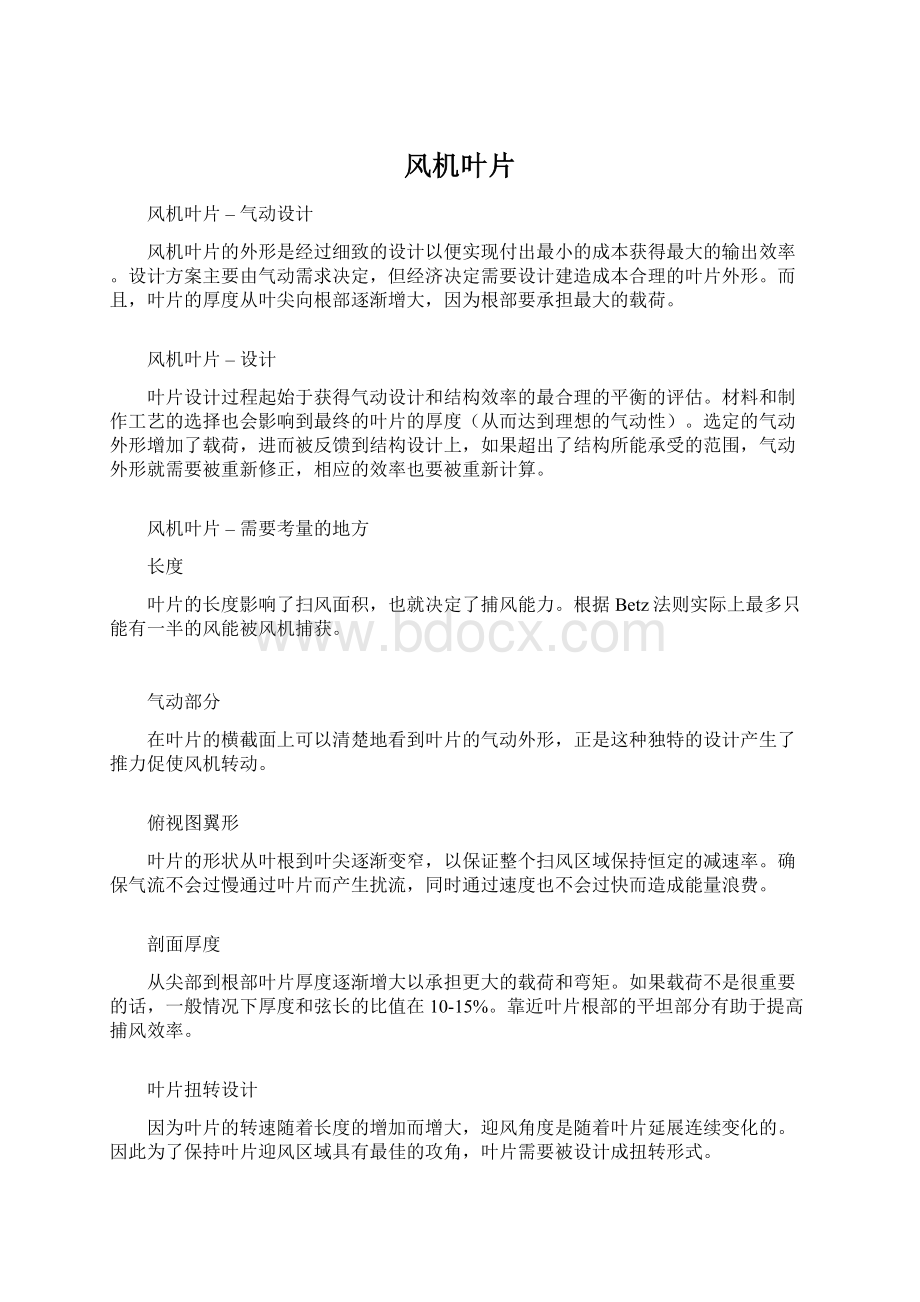
风机叶片
风机叶片–气动设计
风机叶片的外形是经过细致的设计以便实现付出最小的成本获得最大的输出效率。
设计方案主要由气动需求决定,但经济决定需要设计建造成本合理的叶片外形。
而且,叶片的厚度从叶尖向根部逐渐增大,因为根部要承担最大的载荷。
风机叶片–设计
叶片设计过程起始于获得气动设计和结构效率的最合理的平衡的评估。
材料和制作工艺的选择也会影响到最终的叶片的厚度(从而达到理想的气动性)。
选定的气动外形增加了载荷,进而被反馈到结构设计上,如果超出了结构所能承受的范围,气动外形就需要被重新修正,相应的效率也要被重新计算。
风机叶片–需要考量的地方
长度
叶片的长度影响了扫风面积,也就决定了捕风能力。
根据Betz法则实际上最多只能有一半的风能被风机捕获。
气动部分
在叶片的横截面上可以清楚地看到叶片的气动外形,正是这种独特的设计产生了推力促使风机转动。
俯视图翼形
叶片的形状从叶根到叶尖逐渐变窄,以保证整个扫风区域保持恒定的减速率。
确保气流不会过慢通过叶片而产生扰流,同时通过速度也不会过快而造成能量浪费。
剖面厚度
从尖部到根部叶片厚度逐渐增大以承担更大的载荷和弯矩。
如果载荷不是很重要的话,一般情况下厚度和弦长的比值在10-15%。
靠近叶片根部的平坦部分有助于提高捕风效率。
叶片扭转设计
因为叶片的转速随着长度的增加而增大,迎风角度是随着叶片延展连续变化的。
因此为了保持叶片迎风区域具有最佳的攻角,叶片需要被设计成扭转形式。
叶片数量和转速
通常情况下风机叶片的转速大约是风速的7到10倍,目前的设计叶片最多为3个。
转速越高,叶片数量越多也就意味着叶片尺寸要做的更窄,更薄,从而很难保证叶片具有足够的强度。
而在转速过快的时候叶片的捕风效率也有所降低,噪音增大,更易受到环境侵蚀和飞鸟撞击的伤害。
转速过低时捕风效率也会降低,同时增加了施加给其他部件的轴向负荷。
桨距控制
因为风能资源的多变性,必须确保风机在低风速时能够持续产能,在高风速时能够承担高负荷。
因此在风速超过理想风速时,风机可以通过调整桨距以产出能量,并降低外部载荷,比如可以顺桨迎风而上,或者主动停转以远离强风。
风机叶片–复合材料设计
材料和制作工艺的选择会影响到叶片的成本及最终的叶片厚度(从而达到理想的气动性)。
因此结构设计过程在如何将设计原则和制造工艺相结合工作中扮演着重要角色,必须找出可以保证高性能与低成本,同时具有最优气动性的方案。
风机叶片–制造工艺
叶片的结构设计与制造工艺紧密相关,目前叶片的制造工艺主要有预浸料工艺和灌注工艺两种。
两者都需要生产出低成本高可靠性的叶片。
关于两种工艺的选择在业界已经争论了很多年,灌注工艺成本低廉,被广泛接受。
而预浸料工艺产出的叶片具有更高的性能,易于实现自动化生产,质量更加稳定,可以进一步降低叶片重量。
叶片重量的降低也就降低了叶片本身和发电机的负荷,从而进一步降低了成本和风机其他部件的磨损。
风机叶片制造–材料供应
固瑞特自从1995年就已开始面向风机叶片市场提供材料,以生产复合材料叶片,随着叶片尺寸的加大,叶片设计也日趋复杂,固瑞特一直致力于向叶片制造商提供高性价比的先进复合材料。
固瑞特的产品包括了目前叶片制造的全部工艺所需的全套材料,包括了手糊成型,真空灌注和预浸料工艺。
在供应手糊树脂的同时,我们更加关注于真空灌注和预浸料工艺技术及相关材料的开发。
结构工程
叶片设计过程起始于获得气动设计和结构效率的最合理的平衡的评估。
材料和制作工艺的选择会影响到叶片的成本及最终的叶片厚度以及可以达到的理想的气动性。
因此结构设计过程在如何将设计原则和制造工艺相结合工作中扮演着重要角色,必须找出可以保证高性能与低成本的最优方案。
结构设计–流程
翼面向弯曲
由于风推力产生的翼面向弯曲是最早被认知的也通常是最重要的加载形式,叶片结构中的梁帽和腹板就是为了承担这种载荷而设计的,如上所述设计需要在气动外形和结构效率之间找到一个平衡点,两者都会对发电成本产生影响。
因此设计中就需要通过研究厚度变化对发电效率和重量的影响规律,找到最优化的厚度分布。
叶片重量
翼弦向的疲劳载荷取决于叶片的重量,这样在结构设计过程中会产生一个迭代循环。
在叶片被制造出来之前,我们无法确切知道它的重量,只能进行估算。
在得到叶片重量的较准确数字后,我们会对铺层结构进行优化改进以弥补可能的重量增加带来的附加载荷。
此时,可以通过降低材料需用应力来解决疲劳性能的问题,在没有疲劳测试结果的情况下GL提供了确保安全性的强度安全因子,在循环次数为1千万次的情况下,玻璃纤维的安全系数是5,而碳纤维是3,。
抗扭刚度
在叶片基本的抗弯性能(翼面向和翼弦向)确定下来后,接下来需要考虑的就是叶壳的抗扭刚度和抗屈曲强度。
叶根的设计要求是能够承担叶片经过螺栓传递给中心转子和粘合剂结点的载荷,使得结点上承受的载荷不超过其承受范围。
有限元分析
在进行有限元分析以前,设计分析主要是通过一些数据表格或简单的分析方法进行,只能提供大致的不是十分准确地分析结果。
有限元分析可以使分析结果更为精确,我们可以采用软件将一个虚拟三维叶片分割成几千个细小单元,就像瓦片一样。
通过计算机的分析,我们可以得到每一片的受力情况和力传递过程,从而可以模拟整体受到外力时叶片的反应。
结构设计–流程
∙首先获得所用材料的性能数据,并根据材料和选用的工艺设定安全因子,得到优化后的设计材料性能。
∙通过翼面向的弯曲载荷设计铺层结构,确认结构设计符合气动设计的要求。
∙有了基本的铺层设计后,可以通过叶片重量对疲劳载荷进行预估。
∙测试壳体的抗扭刚度和抗屈曲强度
∙制定材料和工艺要求,确保重量和成本符合要求。
∙进一步通过有限元分析对结构设计结果进行验证,包括刚度,强度和疲劳性能等。
∙完成样机制作并进行实际测试,以验证叶片的极限翼向面可承受负荷和极限疲劳性能,从而修正设计。
叶片制造工艺
叶片的结构设计与实际生产制造方法息息相关,两者都需要兼顾生产成本和叶片的可靠性。
两种主要的叶片制造方法有:
预浸料法和灌注法。
尽管两种方法都适用于两种常见设计的叶片结构,但预浸料主要用于箱式粱的叶片结构。
制造成本
为了提供高性能低成本的产品,在风力发电工业中,叶片制造工艺的选择是一直是有许多争论的主题。
灌注工艺被认为是低成本的制造方案其主要原因是原材料(BOM)的低成本。
而预浸料所具有更高的材料性能,易操作实现自动化,同时减小叶片总重。
更轻的叶片意味着较低叶片自身载荷同时也减小作用在叶轮毂和发电机(WTG)齿轮箱上的载荷。
所以,在考虑成本的时,不仅仅要看到原材料的价格,同时要考虑整体的性能和成本因素。
叶片长度
叶片的长度是材料和生产技术的选择时最主要的考虑因素之一。
根据历史数据,随着叶片的增长,重量增量与发电增量比约为2.5.但由于运输条件、实际载荷作用在叶片和塔架上,这个增量比并不稳定.所以需要运用不同的材料和设计理念为叶片增长提供多种解决方案。
减轻叶片重量
一种在增加叶片长度的同时并减小叶片重量的方法是使用更高强度和刚性的碳纤维材料代替玻纤材料。
碳纤维刚性大约为玻纤的3倍,而密度仅为分别180kg/m3(玻纤为240kg/m3)。
尽管碳纤维具有更优越的性能,但其高成本和更精确的工艺要求使使用碳纤维设计和生产成为挑战。
较大叶片的疲劳特性
当叶片变的更长,其失效机理也会随之改变。
20-35m较小叶片设计主要围绕材料满足刚性需求,所以增强纤维的性能主导的材料设计。
如果叶片变得更长,它对疲劳的敏感度对显著增加。
这些疲劳负载更多的与复合材料中的树脂有关.当疲劳压应力主导设计时,复合材料的整体质量就变的尤为重要了。
为满足叶片制造的需要,原材料的选择对工艺设计至关重要,同时也整合了制造工艺于工艺设计中。
叶片制造工艺–树脂灌注技术
灌注工艺的基本原则就是通过真空压力将树脂吸入预先铺好的增强纤维或纤维布中,真空操作降低纤维一面的压力后,大气压力会驱使树脂浸润增强纤维,纤维灌注的速度和距离取决于以下因素:
∙树脂系统的黏度
∙增强纤维的渗透性
∙灌注树脂的压力梯度
树脂黏度
在相同的压力梯度下,黏度越小的树脂,所产生的"拖曳"现象越少,从而浸润效果越好。
这样有助于减少大型部件的注胶口,使灌注过程更加简便。
树脂的黏度取决于其化学成分。
对于环氧树脂——风机叶片最为常用的灌注树脂而言,通常采取加入稀释剂的办法降低黏度。
稀释剂的量需要严格控制,否则会降低环氧树脂的机械性能和物理性能(如耐热性)
另外一个提高灌注速度的办法是提高树脂温度,黏度与温度成反比。
根据经验法则温度每升高10-15度,树脂黏度就会降低一半。
当树脂开始固化时,黏度会以指数级的速度升高,形成凝胶状,最终形成一种呈玻璃态的固态产物。
渗透性
纤维或者层合板的渗透性的影响因素有以下几点:
∙纤维直径
∙纤维定型
∙织物类型
玻璃纤维和碳纤维的渗透性明显不同,碳纤维难以被树脂浸润。
这是因为碳纤维的单丝直径要小于玻璃纤维,平均在5-10μm,而玻璃纤维平均直径在16-24μm。
所以碳纤维可以形成更加密实的织物,渗透性也相应降低。
对纤维进行化学定型的目的在于在后续工艺如编织中,对其加以保护,同时起到加大其与树脂系统的结合力,从而使层合板拥有最强的机械性能。
增强结合的一个关键在于表面需要有良好的浸润性,因此许多表面处理剂针对浸润性能进行了针对性地改良。
在灌注工艺中这一点尤为重要,良好的浸润性可以有效的缩短灌注时间。
压力梯度
在模具和真空袋不存在漏气的情况下,灌注工艺中的压力梯度取决于灌注时的大气压和真空泵压力。
在灌注树脂进入纤维层后,在树脂前端产生的"拖曳"效应开始加剧。
这种牵引力的大小与灌注的纤维体积和其渗透性成正比。
灌注过程中的最大的压力梯度取决于大气压力,为了增加压力梯度可以选择高渗透性的织物或在重要的注胶口处安装管道。
因为部件的结构和厚度多变,从而使注胶口和真空出口的位置和数量的选择变得非常复杂,这种情况下可以采用计算机模拟办法进行辅助设计。
真空和模具要求
对于真空灌注工艺而言,生产中最为重要的一点就是真空系统及模具所能够提供的真空环境的完整性。
即使是最细微的漏气也会导致复合材料成品中夹杂气泡,同时因为存在压力梯度,气泡会在织物层中迅速扩散,这将使孔隙率增高,需要进行比较大的修复工作,并降低了产品质量。
因此在开始灌注前必须严格检查真空环境和模具,以确保真空袋中没有漏气现象存在。
在很多叶片制造过程中经常用到胶衣底漆,这