砂轮的选用和安全.docx
《砂轮的选用和安全.docx》由会员分享,可在线阅读,更多相关《砂轮的选用和安全.docx(15页珍藏版)》请在冰豆网上搜索。
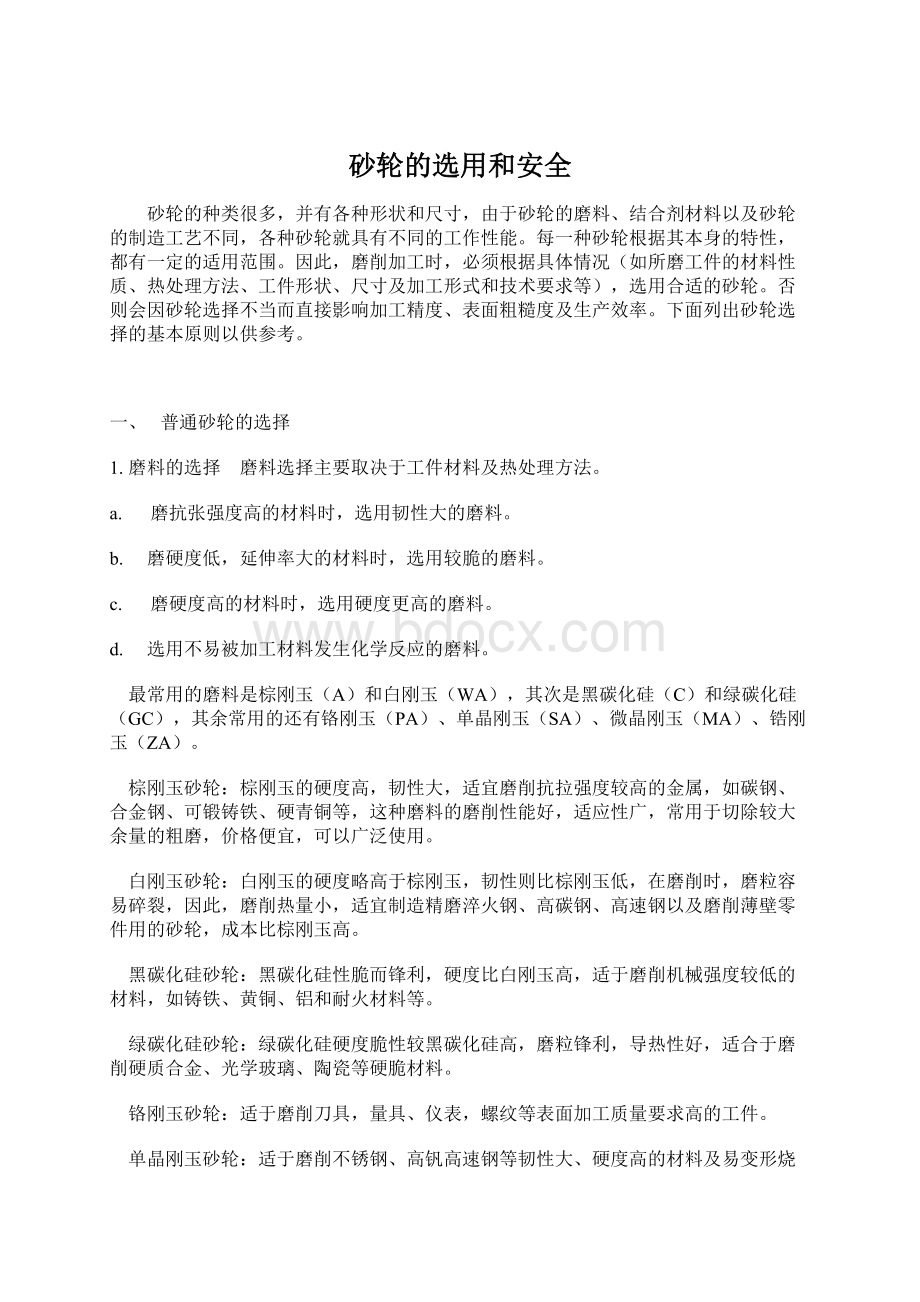
砂轮的选用和安全
砂轮的种类很多,并有各种形状和尺寸,由于砂轮的磨料、结合剂材料以及砂轮的制造工艺不同,各种砂轮就具有不同的工作性能。
每一种砂轮根据其本身的特性,都有一定的适用范围。
因此,磨削加工时,必须根据具体情况(如所磨工件的材料性质、热处理方法、工件形状、尺寸及加工形式和技术要求等),选用合适的砂轮。
否则会因砂轮选择不当而直接影响加工精度、表面粗糙度及生产效率。
下面列出砂轮选择的基本原则以供参考。
一、 普通砂轮的选择
1.磨料的选择 磨料选择主要取决于工件材料及热处理方法。
a. 磨抗张强度高的材料时,选用韧性大的磨料。
b. 磨硬度低,延伸率大的材料时,选用较脆的磨料。
c. 磨硬度高的材料时,选用硬度更高的磨料。
d. 选用不易被加工材料发生化学反应的磨料。
最常用的磨料是棕刚玉(A)和白刚玉(WA),其次是黑碳化硅(C)和绿碳化硅(GC),其余常用的还有铬刚玉(PA)、单晶刚玉(SA)、微晶刚玉(MA)、锆刚玉(ZA)。
棕刚玉砂轮:
棕刚玉的硬度高,韧性大,适宜磨削抗拉强度较高的金属,如碳钢、合金钢、可锻铸铁、硬青铜等,这种磨料的磨削性能好,适应性广,常用于切除较大余量的粗磨,价格便宜,可以广泛使用。
白刚玉砂轮:
白刚玉的硬度略高于棕刚玉,韧性则比棕刚玉低,在磨削时,磨粒容易碎裂,因此,磨削热量小,适宜制造精磨淬火钢、高碳钢、高速钢以及磨削薄壁零件用的砂轮,成本比棕刚玉高。
黑碳化硅砂轮:
黑碳化硅性脆而锋利,硬度比白刚玉高,适于磨削机械强度较低的材料,如铸铁、黄铜、铝和耐火材料等。
绿碳化硅砂轮:
绿碳化硅硬度脆性较黑碳化硅高,磨粒锋利,导热性好,适合于磨削硬质合金、光学玻璃、陶瓷等硬脆材料。
铬刚玉砂轮:
适于磨削刀具,量具、仪表,螺纹等表面加工质量要求高的工件。
单晶刚玉砂轮:
适于磨削不锈钢、高钒高速钢等韧性大、硬度高的材料及易变形烧伤的工件。
微晶刚玉砂轮:
适于磨削不锈钢、轴承钢和特种球墨铸铁等,用于成型磨,切入磨,镜面磨削。
锆刚玉砂轮:
适于磨削奥氐体不锈钢、钛合金、耐热合金,特别适于重负荷磨削。
2.粒度的选择 主要取决于被磨削工件的表面粗糙度和磨削效率。
粒度是指磨料的颗粒尺寸,其大小则用粒度号表示用粗粒度砂轮磨削时,生产效率高,但磨出的工件表面较粗糙;用细粒度砂轮磨削时,磨出的工件表面粗糙度较好,而生产率较低。
在满足粗糙度要求的前提下,应尽量选用粗粒度的砂轮,以保证较高的磨削效率。
一般粗磨时选用粗粒度砂轮,精磨时选用细粒度砂轮。
当砂轮和工件接触面积较大时,要选用粒度粗一些的砂轮。
例如,磨削相同的平面,用砂轮的端面磨削比用砂轮的周边磨削选的粒度要粗些。
3.硬度的选择 主要取决于被磨削的工件材料、磨削效率和加工表面质量。
硬度是指砂轮在外力作用下磨粒脱落的难易程度,为了适应不同工件材料磨加工的要求,制造砂轮时分成不同硬度的等级
不同粒度的砂轮其适用范围砂轮选得过硬,磨钝的磨粒不易脱落,砂轮易堵塞,磨削热增加,工件易烧伤,磨削效率低,影响工件表面质量;砂轮选得过软,磨粒还在锋利时就脱落,增加了砂轮损耗,易失去正确的几何形状,影响工件精度。
所以砂轮硬度的选择要适当,还应根据砂轮与工件接触面积大小、工件形状、磨削的方式、冷却方式、砂轮的结合剂种类等因素来综合考虑。
下列砂轮硬度选择原则供参考:
a. 磨削软材料时要选较硬的砂轮,磨削硬材料时则要选软砂轮;
b. 磨削软而韧性大的有色金属时,硬度应选得软一些;
c. 磨削导热性差的材料应选较软的砂轮;
d. 端面磨比圆周磨削时,砂轮硬度应选软些;
e. 在同样的磨削条件下,用树脂结合剂砂轮比陶瓷结合剂砂轮的硬度要高1~2小级;
f. 砂轮旋转速度高时,砂轮的硬度可选软1~2小级;
g. 用冷却液磨削要比干磨时的砂轮硬度高1~2小级。
4.结合剂的选择 应根据磨削方法,使用速度和表面加工要求等条件予以考虑。
最常用的砂轮结合剂有陶瓷结合剂(V)和树脂结合剂(B)。
陶瓷结合剂是一种无机结合剂,化学性能稳定、耐热、抗腐蚀性好,气孔率大,这种结合剂制造的砂轮磨削效率高、磨耗小,能较好地保持砂轮的几何形状,应用范围最广。
适于磨削普通碳钢、合金钢、不锈钢、铸铁、硬质合金、有色金属等。
但是,陶瓷结合剂砂轮脆性较大,不能受剧烈的振动。
一般只能在35米/秒以内的速度下使用。
树脂结合剂是一种有机结合剂,这种结合剂制造的砂轮强度高,具有一定的弹性,耐热性低,自锐性好,制作简便,工艺周期短。
可制造工作速度高于50米/秒的砂轮和很薄的砂轮。
它的应用范围仅次于陶瓷结合剂,广泛用于粗磨、荒磨、切断和自由磨削,如磨钢锭,铸件打毛刺等。
可制造高速、高光洁度砂轮,重负荷、切断以及各种特殊要求的砂轮。
5.组织的选择 主要考虑工件所受的压力、磨削方法、工件材质等。
组织是指砂轮中磨粒所占砂轮体积的百分比。
砂轮组织等级的划分是以62%的磨粒体积百分数为“0”号组织,磨粒体积每减2%,其组织增加一号,依此类推,共分15个号。
号数越大,组织越松 组织紧密的砂轮能磨出较好的工件表面,组织疏松的砂轮,因空隙大,可以保证磨削过程中容纳磨屑,避免砂轮堵塞。
通常粗磨和磨削较软金属时,砂轮易堵塞,应选用疏松组织的砂轮;成型磨削和精密磨时,为保持砂轮的几何形状和得到较好的粗糙度,应选用较紧密组织的砂轮;磨削机床导轨和硬质合金工具时,为减少工件热变形,避免烧伤裂纹,宜采用松组织的砂轮;磨削热敏性大的材料、有色金属、非金属材料宜采用大于12#组织的砂轮。
6.形状和尺寸的选择 应根据磨床条件和工件形状来选择。
常用砂轮形状有平形砂轮(P)、单面凹砂轮(PDA)、双面凹砂轮(PSA)、薄片砂轮(PB)、筒形砂轮(N)、碗形砂轮(BW)、碟形一号砂轮(D1)等。
每种磨床所能使用的砂轮形状和尺寸都有一定的范围。
在可能的条件下,砂轮的外径应尽可能选得大一些,以提高砂轮的线速度,获得较高的生产率和工件表面质量,砂轮宽度增加也可以获得同样的效果。
现国标砂轮书写顺序:
砂轮代号、尺寸(外径×厚度×孔径)、磨粒、粒度、硬度、组织、结合剂、最高工作线速度。
例示:
P400×150×203A60L5B35
二、 金刚石砂轮的选择
金刚石砂轮比用碳化硼、碳化硅、刚玉等一般磨粒制成的砂轮刃角锋利、磨耗小、寿命长、生产率高、加工质量好,但价格昂贵,因而适用于精磨硬质合金、陶瓷、半导体等高硬度脆性难加工材料。
金刚石砂轮的特征包括磨料种类、粒度、硬度、浓度、结合剂、砂轮形状与尺寸。
磨料:
广泛使用人造金刚石(JR),根据它的结晶形状和颗粒强度,分各种型号,按其特定用途选型号。
粒度:
要以工件粗糙度、磨削生产率和金刚石的消耗三个方面综合考虑。
硬度:
只有树脂结合剂金刚石砂轮才有“硬度”这一特性。
一般采用S(Y1)级或更高。
结合剂:
常用的结合剂有四种,其结合能力和耐磨性以树脂、陶瓷、青铜、电镀金属为序,依次渐强。
树脂结合剂金刚石砂轮磨削效率高,被加工工件粗糙度好,适用范围广,自锐性好,不易堵塞,发热量小,易修整,主要用于精磨工序。
陶瓷结合剂金刚石砂轮主要用于各种非金属硬脆材料、硬质合金、超硬材料等的磨削。
浓度:
浓度选择要根据使用砂轮的粒度、结合剂、形状、加工方法、生产效率及砂轮寿命的要求而定。
高浓度金刚石砂轮保持砂轮形状的能力强,低浓度砂轮磨削时,金刚石的消耗往往更低些,应根据需要酌情选取。
形状和尺寸:
按工件的形状、尺寸和机床条件选用。
三、 立方氮化硼(CBN)砂轮的选择
立方氮化硼(CBN)砂轮的立方氮化硼颗粒粘在普通砂轮表面只有很薄一层,其磨粒韧性、硬度、耐用度是刚玉类砂轮的100倍,最适于加工硬度高、粘性大、高温强度高、热传导率低的难磨钢材及高速或超高速磨削。
其应用范围与人造金刚石起着互相补充的作用。
金刚石砂轮在磨削硬质合金和非金属材料时,具有独特的效果,但在磨削钢料时,尤其是磨削特种钢时,效果不显著。
立方氮化硼砂轮磨削钢件的效率比刚玉类砂轮要高近百倍,比金刚石砂轮高五倍,但磨削脆性材料不及金刚石。
立方氮化硼砂轮的选择和金刚石砂轮的选择相类似。
但在结合剂选用上,大部分是树脂结合剂,次之是电镀,金属结合剂。
陶瓷结合剂CBN砂轮主要用于钛合金、高速钢、可锻铸铁等难加工的黑色金属的磨削,树脂结合剂CBN砂轮适用于磨削铁磁性材料,是加工钢材的理想选择。
CBN砂轮浓度一般在100%~150%间选用较经济合理,它不能用普通切削液,需特殊的切削液。
四、 大气孔砂轮的选择
大气孔砂轮在磨削时具有不易被堵塞、耐用度高和切削能力强等优点。
适用于软金属和塑料、橡皮和皮革等非金属材料的粗、精磨。
同时,它具有散热快的特点,所以在磨削一些热敏性大的材料、薄壁工件和干磨工序中(例如刃磨硬质合金刀具和机床导轨等)有良好的效果。
大气孔砂轮和一般陶瓷结合剂砂轮的制造方法基本一样。
不同点是在配料中外加一定量的增孔剂,它在砂轮烧结前完全挥发或被烧烬,从而产生大气孔。
大气孔砂轮生产范围是:
磨料一般选择碳化物和刚玉等,如常用的有黑碳化硅(C)、绿碳化硅(GC)和白刚玉(WA)等几种,这些磨料的硬度高、性脆而锋利,具有良好的导热和导电性能;磨料粒度(36#~180#);结合剂(陶瓷结合剂);硬度(G~M各级);形状(平形、杯形、碗形或碟形等);气孔尺寸(约0.7~1.4毫米)。
精密磨削中的砂轮修整
砂轮修整是影响精密磨削质量的关键因素之一。
修整方法有单粒金刚石修整、金刚石粉末烧结型修整器修整和金刚石超声波修整等,如图3-3所示。
金刚石修整时砂轮与修整器的相对位置如图3-4所示。
金刚石修整器的位置与砂轮磨削时的工件位置相对应,修整器安装在低于砂轮中心0.5~1.5mm处,并向右上倾斜10˚~15˚,以减小受力。
金刚石超声波修整分为点接触法和面接触法。
砂轮的修整用量有修整导程、修整深度、修整次数和光修次数。
修整导程—般为10~15mm/min;修整深度为2.5μm/单行程;修整时一般分为初修与精修,精修一般为2~3次单行程;光修为无修整深度修整,一般为1次单行程,主要是为了去除砂轮表面个别突出微刃,使砂轮表面更加平整。
磨床工作安全技术
一、磨削的特点
磨削加工是用得最广泛的切削加工方法之一。
它与其它切削加工如车削、铣削、刨削等比较,具有以下一些特点:
1.磨削速度很高,每秒可达30m至50m;切削温度较高,可达1000℃至1500℃;切削过程历时很短,只有万分之一秒左右。
2.磨削加工能获得很高的加工精度和很小的表面粗糙度,通常公差等级可以达到IT5~IT7级,表面粗糙度可以达到Ra0.8μm至Ra0.4μm。
如果采用高精度磨削方法,公差等级可以超过IT5级。
表面粗糙最高可以达到Ra0.05μm。
3磨削时的切削深度较小,在一次行程中所能切除的金属层较薄,只有几个微米。
磨削的安全问题主要有:
工件在磨床上加工时,从砂轮上飞溅出大量细的磨屑,而从工件上飞溅出大量金属屑。
磨屑和金属屑会使磨工眼部遭受危害,尘末吸入肺部对身体有害。
必须采取适当的防护装置。
由于种种原因,磨削时可能造成砂轮的碎裂,从而导致工人遭受严重的伤害。
在靠近转动的砂轮进行某些手工操作时,如