低温球铁方面资料.docx
《低温球铁方面资料.docx》由会员分享,可在线阅读,更多相关《低温球铁方面资料.docx(32页珍藏版)》请在冰豆网上搜索。
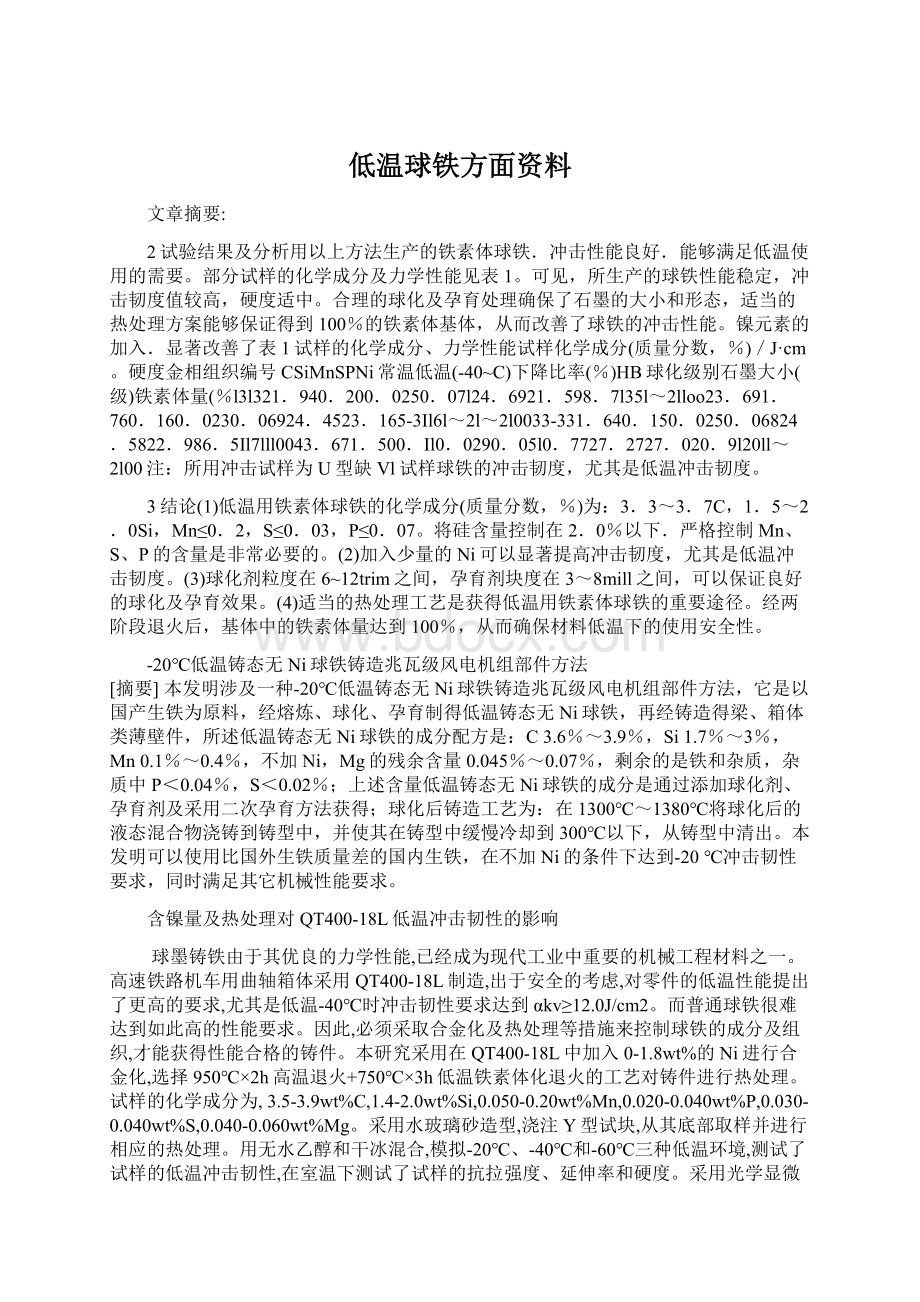
低温球铁方面资料
文章摘要:
2试验结果及分析用以上方法生产的铁素体球铁.冲击性能良好.能够满足低温使用的需要。
部分试样的化学成分及力学性能见表1。
可见,所生产的球铁性能稳定,冲击韧度值较高,硬度适中。
合理的球化及孕育处理确保了石墨的大小和形态,适当的热处理方案能够保证得到100%的铁素体基体,从而改善了球铁的冲击性能。
镍元素的加入.显著改善了表1试样的化学成分、力学性能试样化学成分(质量分数,%)/J·cm。
硬度金相组织编号CSiMnSPNi常温低温(-40~C)下降比率(%)HB球化级别石墨大小(级)铁素体量(%l3l321.940.200.0250.07l24.6921.598.7l35l~2lloo23.691.760.160.0230.06924.4523.165-3Il6l~2l~2l0033-331.640.150.0250.06824.5822.986.5Il7lll0043.671.500.Il0.0290.05l0.7727.2727.020.9l20ll~2l00注:
所用冲击试样为U型缺Vl试样球铁的冲击韧度,尤其是低温冲击韧度。
3结论
(1)低温用铁素体球铁的化学成分(质量分数,%)为:
3.3~3.7C,1.5~2.0Si,Mn≤0.2,S≤0.03,P≤0.07。
将硅含量控制在2.0%以下.严格控制Mn、S、P的含量是非常必要的。
(2)加入少量的Ni可以显著提高冲击韧度,尤其是低温冲击韧度。
(3)球化剂粒度在6~12trim之间,孕育剂块度在3~8mill之间,可以保证良好的球化及孕育效果。
(4)适当的热处理工艺是获得低温用铁素体球铁的重要途径。
经两阶段退火后,基体中的铁素体量达到100%,从而确保材料低温下的使用安全性。
-20℃低温铸态无Ni球铁铸造兆瓦级风电机组部件方法
[摘要]本发明涉及一种-20℃低温铸态无Ni球铁铸造兆瓦级风电机组部件方法,它是以国产生铁为原料,经熔炼、球化、孕育制得低温铸态无Ni球铁,再经铸造得梁、箱体类薄壁件,所述低温铸态无Ni球铁的成分配方是:
C3.6%~3.9%,Si1.7%~3%,Mn0.1%~0.4%,不加Ni,Mg的残余含量0.045%~0.07%,剩余的是铁和杂质,杂质中P<0.04%,S<0.02%;上述含量低温铸态无Ni球铁的成分是通过添加球化剂、孕育剂及采用二次孕育方法获得;球化后铸造工艺为:
在1300℃~1380℃将球化后的液态混合物浇铸到铸型中,并使其在铸型中缓慢冷却到300℃以下,从铸型中清出。
本发明可以使用比国外生铁质量差的国内生铁,在不加Ni的条件下达到-20℃冲击韧性要求,同时满足其它机械性能要求。
含镍量及热处理对QT400-18L低温冲击韧性的影响
球墨铸铁由于其优良的力学性能,已经成为现代工业中重要的机械工程材料之一。
高速铁路机车用曲轴箱体采用QT400-18L制造,出于安全的考虑,对零件的低温性能提出了更高的要求,尤其是低温-40℃时冲击韧性要求达到αkv≥12.0J/cm2。
而普通球铁很难达到如此高的性能要求。
因此,必须采取合金化及热处理等措施来控制球铁的成分及组织,才能获得性能合格的铸件。
本研究采用在QT400-18L中加入0-1.8wt%的Ni进行合金化,选择950℃×2h高温退火+750℃×3h低温铁素体化退火的工艺对铸件进行热处理。
试样的化学成分为,3.5-3.9wt%C,1.4-2.0wt%Si,0.050-0.20wt%Mn,0.020-0.040wt%P,0.030-0.040wt%S,0.040-0.060wt%Mg。
采用水玻璃砂造型,浇注Y型试块,从其底部取样并进行相应的热处理。
用无水乙醇和干冰混合,模拟-20℃、-40℃和-60℃三种低温环境,测试了试样的低温冲击韧性,在室温下测试了试样的抗拉强度、延伸率和硬度。
采用光学显微镜观察试样组织,用X-ray衍射仪分析试样物相组成,用扫描电子显微镜观察试样断口形貌...Ductileironhasbeensignificantengineeringmaterialsforitsexcellentmechanicalproperties.Crankcasesofengineusedinhigh-speedrailwayaremadeofQT400-18L.Onaccountofsafety,ahigherpropertyatlowtemperatureisnecessary.Especially,itsimpacttoughnessαkvat-40℃isrequiredtoexceed12.0J/cm2.Butacommonnodulargraphitecastironcannotmeetthisrequirement.Forthisreason,appropriatemeasuresshouldbetaken,suchasalloyingandheat-treatmenttocontrolcomponentsand..
耐低温冲击球墨铸铁
和常温球墨铸铁相比,耐低温冲击球墨铸铁的生产还是有一定的难度,应该说有一定的技术含量。
对球化剂、孕育剂、生铁、废钢等原附材料,球铁成分、过程控制及检测诸多方面都提出了全新的要求。
1生产条件
采用0.5T中频感应电炉熔炼铁液,呋喃冷硬树脂砂造型,主要生产如图一所示箱体铸件,牌号要求为GJS-350-22-LT,铸件单重为117kg。
2生产过程
主要炉料为低碳、低锰废钢和回炉料,采用增碳剂,增硅剂调整铁液成份,控制原铁液及铸件化学成份到表1要求范围。
升温至1510℃~1530℃,进行球化和孕育处理
分析与探讨
如何获得较高低温冲击韧性的球墨铸铁件呢?
冲击韧性反映材料断裂时吸收的能量,也反映快速形变条件下,材料抵抗裂纹萌生、发展和断裂的能力。
低温冲击韧性是一个材料的韧性指标,也就是说具有较高低温冲击韧性的球墨铸铁件在-20℃或-40℃时具有较高冲击韧性,脆--韧性能转变温度较低,能够较好的克服冷脆。
因此,如下的一些措施都能有效的提高球墨铸铁的低温冲击韧性指标
4.1提高球墨铸铁材质的铁素体含量
研究表明不同温度下不同基体组织对低温冲击韧性有较大的影响,塑性较高的铁素体球铁能获得较高的冲击韧性指标
4.1.1化学成份
降低促进或稳定珠光体形成元素如:
Mn、V、Zr、Nb、Ti、Cr、Mo、W、Cu、Pb、Sb等元素,其中值得一提的两个元素,一个是锰,它对球墨铸铁的冲击韧性和脆性转变温度都有特别不利的影响,每提高0.1%的锰含量,球铁的脆性转变温度提高10℃~12℃,所以,尽量选择低锰生铁和废钢作为原材料;另一个元素是Cu,他虽然是中性元素,提高珠光体含量的作用不明显,但是,随着含Cu量的增加,球墨铸铁的脆性转变温度升高,并且冲击韧度也下降。
适量提高铁素体形成元素,如:
C、Si、Ca、Ba、Al、Bi等元素,其中值得一提的是Si元素,众所周知,Si是强烈促进石墨化元素,有利于提高铁素体含量,但Si量增加,冲击韧性明显下降,Si含量每提高01.%脆性转变温度就提高5.5℃~6℃,含Si量在4%左右的球墨铸铁,虽具有全部的铁素体基体,但脆性很大,就是常温下也难于在有冲击载荷的条件下使用,因此,具有低温冲击性能要求的球铁中Si含量一般控制在1.6~2.0%。
4.1.2降低铸件随型冷却速度
一定成份的球铁,改变其共晶阶段冷却速度,可在较大范围内改变其基体组织,也就是说铸件随型冷却速度愈慢,其基体组织中铁素体含量愈高,铸件越厚,冷却速度越慢,铁素体含量越高。
但应防止出现晶粒及石墨球粗大;造型材料不同,导热能力不同,导致随型铸件冷却速度也不同,应选用干型砂或树脂砂等导热较慢的造型材料,同时应适当放宽铸型厚度(俗称加大吃砂量),尽量减少或不用冷铁,对于薄壁件来说,适当提高浇铸温度的措施来减缓铸件冷却速度,尽量延长开箱时间,有条件的可将随型铸件集中摆放,减缓散热。
4.1.3热处理
从图4、图5可看出,通过热处理工艺后,提高了铁素体含量,延伸率、冲击韧性都得到了较大幅度的提高,通过退火处理部分元素在高温下能得以扩散,铸件基体组织的晶格变细、晶粒细化,铁素体量和性能得以稳定提高。
同时,通过热处理的方法,可适当放宽对原辅材料中部分元素的苛刻要求。
对于达不到要求的或中小铸件可通过热处理的措施来祢补。
4.2细化晶粒、增加共晶团数量
随着材料晶粒尺寸的增大,材料的断裂应力显着降低,当晶粒尺寸大于某一临界尺寸时,既出现脆性断裂,细化及减小晶粒尺寸可降低脆性转变温度,从而提高球墨铸铁低温冲击韧性指标。
4.2.1合成铸铁熔炼工艺
采用废钢和回炉球铁作为主要原料,采用石墨增C,硅铁或碳化硅增Si的方式熔炼球铁铁液。
由于C、Si的熔点比铁液的温度高,主要是靠扩散溶解的方式进入铁液,在铁液中存在着大量的[C]的微晶,这种微晶是先共析或共晶石墨很好的外来形核基底,有利于细化晶粒。
4.2.2多次孕育
孕育的实质是脱氧、脱硫形成外来晶粒,其目的是增加石墨形核能力,细化晶粒,增加石墨球数量,增加铁素体含量,经过三次孕育,尤其是浇铸过程中采用0.3~1mm的含Ba孕育剂进行瞬时孕育,孕育量虽少,但孕育效果显着。
4.3净化铁液,减少晶粒内部、晶粒间的夹渣及夹杂物
材料断裂往往是穿晶或沿晶断裂,材料晶粒内部或晶粒间有夹杂或夹杂物,削弱了材料的键合力,在冲击载荷作用下,经常形成为裂纹源,或裂纹传播的途径,降低材料的耐低温冲击能力。
4.3.1铁液预处理
4.3.1.1脱氧、脱硫处理
对于采用冲天炉--电路双联熔炼的厂家,可采取摇包方式冲入方式或气动脱硫方式进行脱硫,使原铁液中的硫含量降至0.02%一下,不过,现在用的脱硫剂大部分为CaO或CaC2成份,这种脱硫剂脱氧能力较差,能适当辅助以一些脱氧元素如Ca、Ba、Al等元素就更好。
对于采用电炉直接熔炼也有必要采取铁水的脱氧、脱硫处理。
4.3.1.2铁液的过热及静置
提高铁液熔炼温度,可以使原材料中带入的夹杂物,以及在熔炼过程中形成的夹渣及夹杂物上浮至铁液表面,尤其是对于采用废钢增碳工艺更要适当提高熔炼温度≥1500℃,增加保温时间,不然,碳不能完全溶到铁液中,形成夹渣。
对球化后的铁液进行1~3min的静置,有利于活泼金属如Mg、Ba、Al、Fe的氧化物及硫化物上浮,从而净化铁液。
4.3.1.3多覆盖勤扒渣
多覆盖有利于熔炼过程,浇铸过程中减少铁液和空气的接触时间,降低铁液中的氧含量;勤扒渣,有利于聚集在熔炼过程或球化过程中形成的残存氧化物、硫化物,从而使铁--渣分离,保证进入型腔前的铁液得到良好的净化。
4.3.1.4铁液过滤
结合浇铸系统在型上或型内设置一个带有过滤器的集渣包,一是阻止固、液态渣的通过;二是有利于铁液平稳注入型腔,减少二次氧化渣的形成;三是在集渣包中上浮一些集渣物,尽量减少一次渣进入型腔。
4.4降低晶界偏析元素
Mn、Sb、Sn、As、Ti等元素为晶界偏析元素,应尽量降低其含量。
4.5降低氧化物、硫化物形成元素
Ca、Ba、Al、Mg、稀土元素易形成氧化物、硫化物,应尽量降低其含量
4.6专用球化剂、孕育剂
用于生产耐低温冲击球铁的球化剂、孕育剂应注意如下三原则
一是:
高的稳定的球化及孕育效果:
这一方面取决于球化剂本身的成分稳定,主要元素如Mg、Re、Ca、Ba等偏差范围应小于±0.3%;另一方面是铁水质量的稳定,如出铁温度,S、O含量的稳定;再次就是操作工艺的稳定,如出铁速度及除铁位置的控制,防止出铁过慢使铁水直冲球化剂。
二是:
较强的墨化能力,Mg、Re是主要