课程设计(论文)-逻辑无环流直流可逆调速系统建模与仿真.doc
《课程设计(论文)-逻辑无环流直流可逆调速系统建模与仿真.doc》由会员分享,可在线阅读,更多相关《课程设计(论文)-逻辑无环流直流可逆调速系统建模与仿真.doc(32页珍藏版)》请在冰豆网上搜索。
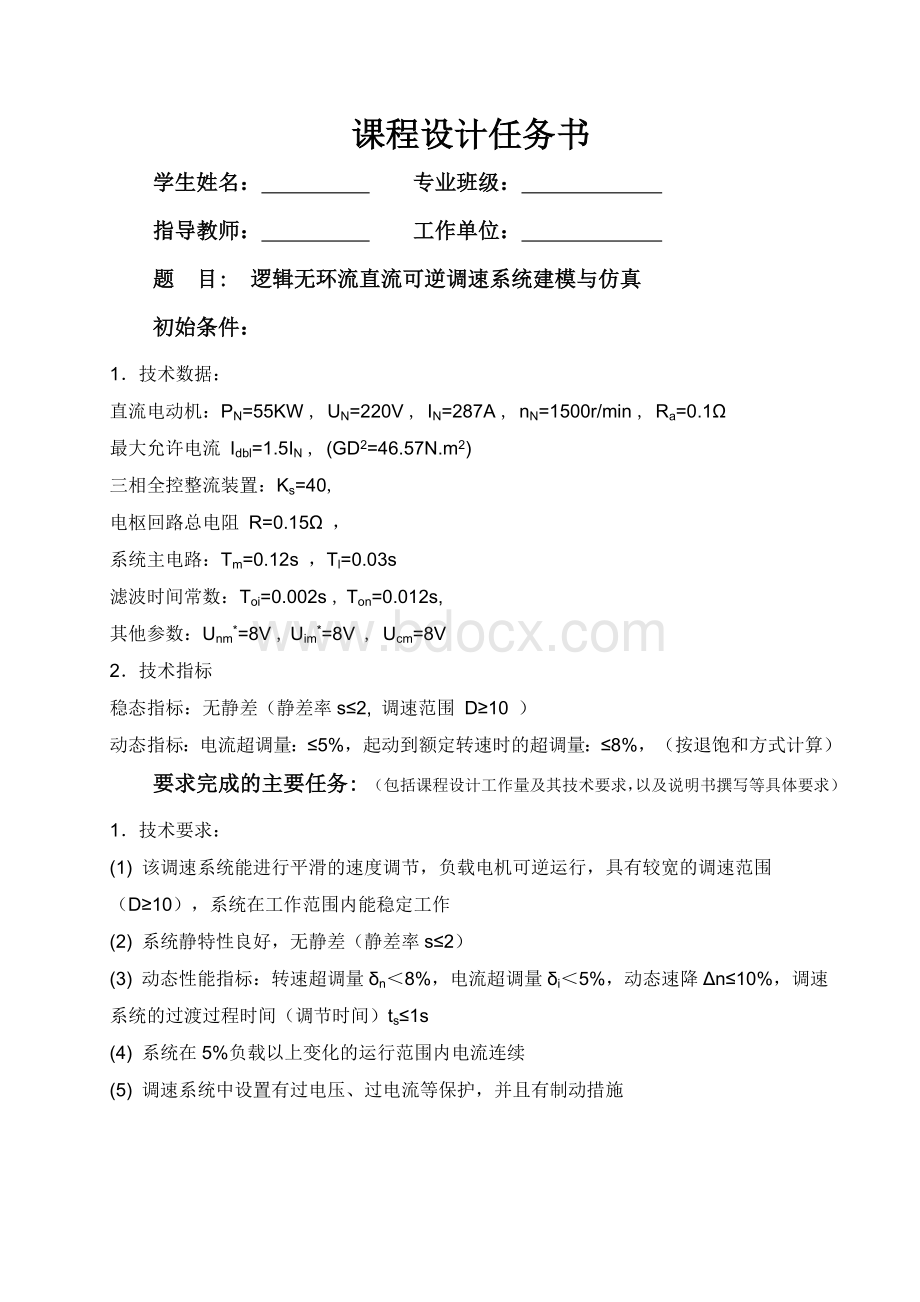
课程设计任务书
学生姓名:
专业班级:
指导教师:
工作单位:
题目:
逻辑无环流直流可逆调速系统建模与仿真
初始条件:
1.技术数据:
直流电动机:
PN=55KW,UN=220V,IN=287A,nN=1500r/min,Ra=0.1Ω
最大允许电流Idbl=1.5IN,(GD2=46.57N.m2)
三相全控整流装置:
Ks=40,
电枢回路总电阻R=0.15Ω,
系统主电路:
Tm=0.12s,Tl=0.03s
滤波时间常数:
Toi=0.002s,Ton=0.012s,
其他参数:
Unm*=8V,Uim*=8V,Ucm=8V
2.技术指标
稳态指标:
无静差(静差率s≤2,调速范围D≥10)
动态指标:
电流超调量:
≤5%,起动到额定转速时的超调量:
≤8%,(按退饱和方式计算)
要求完成的主要任务:
(包括课程设计工作量及其技术要求,以及说明书撰写等具体要求)
1.技术要求:
(1)该调速系统能进行平滑的速度调节,负载电机可逆运行,具有较宽的调速范围(D≥10),系统在工作范围内能稳定工作
(2)系统静特性良好,无静差(静差率s≤2)
(3)动态性能指标:
转速超调量δn<8%,电流超调量δi<5%,动态速降Δn≤10%,调速系统的过渡过程时间(调节时间)ts≤1s
(4)系统在5%负载以上变化的运行范围内电流连续
(5)调速系统中设置有过电压、过电流等保护,并且有制动措施
2.设计内容:
(1)根据题目的技术要求,分析论证并确定主电路的结构型式和闭环调速系统的组成,画出系统组成的原理框图
(2)根据双闭环直流调速系统原理图,分析转速调节器和电流调节器的作用,
(3)通过对调节器参数设计,得到转速和电流的仿真波形,并由仿真波形通过MATLAB来进行调节器的参数调节。
(4)绘制V-M双闭环直流可逆调速系统的电气原理总图(要求计算机绘图)
(5)整理设计数据资料,课程设计总结,撰写设计计算说明书
时间安排:
查阅资料12月21-12月23
任务设计12月24-12月30
校正打印12月31
指导教师签名:
年月日
系主任(或责任教师)签名:
年月日
摘要
晶闸管反并联的电枢可逆线路是可逆调速系统的典型线路之一。
这种线路有能实现可逆运行、回馈制动等优点,但也会产生环流。
为保证系统安全,必须消除其中的环流。
所谓逻辑无环流系统就是在一组晶闸管工作时,用逻辑电路封锁另一组晶闸管的触发脉冲,使该组晶闸管完全处于阻断状态,从根本上切断环流通路。
这种系统不仅能实现逻辑无环流可逆调速,还是交一交变频的基础。
本文采用Matlab的Simulink和PowerSystem工具箱,介绍如何实现逻辑无环流可逆调速系统的建模与仿真。
逻辑无环流可逆直流调速系统省去了环流电抗器,没有了附加的环流损耗,节省变压器和晶闸管装置的附加设备容量。
和有环流系统相比,因换流失败造成的事故率大为降低。
本文对逻辑无环流可逆直流调速系统进行了仿真研究,对DLC(逻辑控制器)、ACR和ASR的参数进行了设计,给出了仿真结果和分析。
关键词:
无环流可逆直流调速系统逻辑控制器MatlabSimulinkPowerSystem
目录
1设计任务与方案 1
2逻辑无环流可逆直流调速系统分析 2
2.1可逆V-M直流调速系统的环流问题 2
2.2移相方法a=b配合控制 2
2.3逻辑无环流可逆直流调速系统的组成与工作原理 4
2.4无环流逻辑控制器 5
3逻辑无环流可逆直流调速系统设计 6
3.1主要参数计算 6
3.2主电路设计 7
3.3DLC(逻辑控制器)设计 7
3.4电流调节器设计 10
3.4.1电流环结构框图的化简 10
3.4.2确定时间常数 11
3.4.3选择电流调节器结构 11
3.4.4计算电流调节器参数 11
3.4.5校验近似条件 12
3.4.6计算调节器电阻电容 12
3.5转速调节器设计 12
3.5.1确定时间常数 13
3.5.2选择转速调节器结构 13
3.5.3计算转速调节器参数 13
3.5.4检验近似条件 13
3.5.5计算调节器电阻和电容 14
3.5.6校核转速超调量 14
4系统建模与仿真 15
4.1逻辑控制器的建模 15
4.2总系统建模 16
4.2.1各部分的传递函数 16
4.2.2传递函数建模 17
4.2.3利用PowerSystem工具箱的物理模型建模 19
4.3仿真结果 21
4.3.1逻辑控制器(DLC)仿真 21
4.3.2电机正反转仿真 22
4.4仿真结果分析 22
5总结 24
5.1心得体会 24
5.2改进意见及展望 24
参考文献 25
附录电气原理图 26
武汉理工大学《电力拖动自动控制系统》课程设计说明书
逻辑无环流直流可逆调速系统建模与仿真
1设计任务与方案
在可逆调速系统中,往往采用既没有直流平均环流,又没有脉动环流的无环流可逆系统,无环流可逆系统省去了环流电抗器,没有了附加的环流损耗,节省变压器和晶闸管装置的附加设备容量。
和有环流系统相比,因换流失败造成的事故率大为降低。
因此,逻辑无环流可逆调速系统在生产中被广泛运用。
本文通过对逻辑无环流可逆直流调速系统仿真分析,研究了逻辑无环流可逆直流调速系统各个重要环节的设计,仿真结果证明了设计的正确性。
在两组反并联供电的直流电动机可逆调速系统中,如果在一组整流器工作时,封锁状态另一组整流器,即切断这组整流器的触发脉冲,使这组整流器不工作,这样两组整流器之间就没有环流通道,既不会产生直流环流也不会产生脉动环流。
这种系统一般由逻辑控制器来判断在正反转或制动过程中那组整流器应该工作(包括整流和逆变两种状态),那组整流器应该封锁,故称为逻辑控制无环流可逆调速系统。
逻辑无环流可逆系统的思路简洁,并且由于不存在环流和没有环流带来的损耗,整流器的容量可以减少,也不需要限制环流的电抗器,是目前晶闸管—直流电动机可逆调速系统常用的控制方案。
设计要求逻辑无环流直流可逆调速系统能进行平滑的速度调节,负载电机可逆运行,具有较宽的调速范围(D≥10),系统在工作范围内能稳定工作;系统静特性良好,无静(静差率s≤2);动态性能指标要求转速超调量δn<10%,电流超调量δi<5%,动态速降Δn≤10%,调速系统的过渡过程时间(调节时间)ts≤1s;系统在5%负载以上变化的运行范围内电流连续;调速系统中设置有过电压、过电流等保护,并且有制动措施。
本设计采用MATLAB进行建模与仿真,文中将采用传递函数和PowerSystem工具箱分别进行建模和仿真。
控制系统传统的计算机仿真是用传递函数方法来完成的,各环节的传递函数是将实际模型经过一定的简化而得到的,较容易实现,但是很多重要细节会被忽略。
而利用PowerSystem工具箱提供了利用物理模型仿真的可能,其仿真建模方法与构建实际电路相似,仿真结果非常接近于实际,但是仿真难度较大。
2逻辑无环流可逆直流调速系统分析
2.1可逆V-M直流调速系统的环流问题
采用两组晶闸管反并联的可逆V-M系统,如果两组装置的整流电压同时出现,便会产生不流过负载而直接在两组晶闸管之间流通的短路电流,称作环流。
一般地说,这样的环流对负载无益,徒然加重晶闸管和变压器的负担,消耗功率,环流太大时会导致晶闸管损坏,因此应该予以抑制或消除。
只要合理的对环流进行控制,保证晶闸管的安全工作,可以利用环流作为流过晶闸管的基本负载电流,使电动机在空载或轻载时可工作在晶闸管装置的电流连续区,以避免电流断续引起的非线性对系统性能的影响。
在不同情况下,会出现下列不同性质的环流。
第一种是静态环流,它是两组可逆线路在一定控制角下稳定工作时出现的环流,其中它又可以分为两类:
1)直流平均环流——由晶闸管装置输出的直流平均电压所产生的环流称作直流平均环流。
2)瞬时脉动环流——两组晶闸管输出的直流平均电压差为零,但因电压波形不同,瞬时电压差仍会产生脉动的环流,称作瞬时脉动环流。
其中直流平均环流可以采用a=b配合控制来消除,瞬时脉动环流可以使用电抗器来抑制。
第二种是动态环流——仅在可逆V-M系统处于过渡过程中出现的环流。
2.2移相方法a=b配合控制
在两组晶闸管反并联的可逆V-M系统中,如果让正组VF和反组VR都处于整流状态,两组的直流平均电压正负相连,必然产生较大的直流平均环流。
为了防止直流平均环流的产生,需要采取必要的措施,比如:
采用封锁触发脉冲的方法,在任何时候,只允许一组晶闸管装置工作;采用配合控制的策略,使一组晶闸管装置工作在整流状态,另一组则工作在逆变状态。
为了防止产生直流平均环流,应该当正组处于整流状态时,强迫让反组处于逆变状态,且控制其幅值与之相等,用逆变电压把整流电压顶住,则直流平均环流为零。
于是
由于,
其中和分别为VF和VR的控制角。
由于两组晶闸管装置相同,两组的最大输出电压是一样的,因此,当直流平均环流为零时,应有
或
如果反组的控制用逆变角表示,则
由此可见,按上式来控制就可以消除直流平均环流,这称作配合控制。
为了更可靠地消除直流平均环流,可采用
为了实现配合控制控制,可将两组晶闸管装置的触发脉冲零位都定在,即当控制电压时,使,此时,电机处于停止状态。
增大控制电压移相时,只要使两组触发装置的控制电压大小相等符号相反就可以了。
配合控制系统的移相控制特性如图2-1所示。
图2-1配合控制系统的移相控制特性
为了防止晶闸管装置在逆变状态工作中逆变角太小而导致换流失败,出现“逆变颠覆”现象,必须在控制电路中采用限幅作用,形成最小逆变角保护。
与此同时,对角也实施保护,以免出现而产生直流平均环流。
通常取。
2.3逻辑无环流可逆直流调速系统的组成与工作原理
逻辑无环流可逆直流调速系统的电气原理图如图2-2所示。
系统主电路也采用两组整流器反并联方案,由于没有环流,不用设置环流电抗器,但为了保证稳定运行时电流波形连续,仍应保留平波电抗器。
控制系统采用典型的转速、电流双闭环系统,由转速调节器、电流调节器、逻辑控制器等组成。
为了得到不反映极性的电流检测方法,在图2-2中画出了交流互感器和整流器,可以为正反向电流分别各设一个电流调节器,1ACR用来控制正组触发装置GTF,2ACR用来控制正组触发装置GTR,1ACR的给定信号经反号器AR作为2ACR的给定信号。
为了不出现环流,设置无环流逻辑控制器DLC,这是系统中的关键环节,它按照系统的工作状态指挥正反组的自动切换。
其输出信号用来控制正组触发脉冲的封锁或开放,用来控制反组触发脉冲的封锁或开放。
在任何情况下,两个信号必须是相反的,决不允许两组晶闸管同时开放脉冲,以确保主电路没有出现环流的可能。
但是,和自然无环流系统一样,触发脉冲的零位仍整定在,移相方法仍采用配合控制。
图2-2逻辑无环流可逆直流调速系统的电气原理图
2.4无环流逻辑控制器
无环流逻辑控制环节是逻辑无环流控制系统的关键环节,无环流逻辑控制器的任务是当需要正组晶闸管工作时,则封锁反组晶闸管,当需要反组晶闸管工作时,则封锁正组晶闸管。
采用数字逻辑电路、PLC、微机等,可以使其数字输出信号0和1来执行封锁与开放晶闸管的功能,为了确保正反组不会同时开放,应使两者不能同时为1。
逻辑控制器的切换动作应该根据电流环给定信号来指挥。
因为当系统在反转时当然应该开放反组晶闸管封锁正组晶闸管;但当系统正转运动中要制动或减速时,也要用反组晶闸管的逆变状态来实现回馈制动。
在这两种情况下都要开放反组,封锁正组。
由此可以发现,ASR的输出信号满足这项工作,反转运行和正转制动都需要电动机产生负的转矩;反之,正转运行和反转制动都需要电动机产生正的转矩,的极性恰好放映了电机电磁转矩方向的变化。
但是,仅用ACR给定信号去控制DLC还是不够。
因为,当的极性改变时,实际电流方向不能立即变化,此时逻辑控制器不能进行切换动作;只有在实际电流降到零的时候,才应该给DLC发出命令。
所以,在改变极性后,还有等待“零电流检测”信号,才能发出正反组切换。
逻辑切换指令发出后还不能马上执行,还要经过关断等待延时和触发等待延时,确保可靠工作。
另外,逻辑控制器应具有逻辑连锁保护功能,以保证在任何情况下,两个信号必须是相反的,决不容许两组晶闸管同时开放脉冲,确保主电路没有出现环流的可能。
那么,根据以上分析逻辑控制器应具有以下结构,如图2-3所示。
图2-3逻辑控制器结构图
3逻辑无环流可逆直流调速系统设计
设计课题给出的技术数据如下:
直流电动机:
PN=55KW,UN=220V,IN=287A,nN=1500r/min,Ra=0.1Ω;最大允许电流Idbl=1.5IN,(GD2=46.57N.m2);三相全控整流装置:
Ks=40;电枢回路总电阻R=0.15Ω;系统主电路:
Tm=0.12s;滤波时间常数:
Toi=0.002s,Ton=0.012s;其他参数:
Unm*=8V,Uim*=8V,Ucm=8V。
要求的技术指标为:
稳态指标:
无静差(静差率s≤2,调速范围D≥10);动态指标:
电流超调量:
≤5%,起动到额定转速时的超调量:
≤8%,(按退饱和方式计算)。
3.1主要参数计算
由电力电子技术知识可知,三相桥式整流电路带阻感负载时输出电压平均值为
可知此设计的负载为电机负载,则在额定负载运行时
,取
则有整流变压器二次侧相电压
系统要求在5%负载以上变化的运行范围内电流连续,则
平波电抗器,取4.5mH;
电枢回路电磁时间常数
电动势系数
转速反馈系数
电流反馈系数
还有,系统要求调速范围,静差率
则闭环系统的稳态速降
系统的开环额定速降
闭环系统的开环放大系数应满足
3.2主电路设计
晶闸管-电动机调速系统(V-M系统)主电路原理图如图3-1所示。
图中由晶闸管组成三相全控桥式整流电路,同时设有过电压和过电流保护电路。
通过调节触发装置的控制电压来移动脉冲的相位,即可改变平均整流电压,从而实现平滑调速。
图3-1V-M双闭环直流可逆调速系统主电路原理图
3.3DLC(逻辑控制器)设计
逻辑无环流可逆调速系统通常采用典型的转速电流双闭环系统结构,关键是设置了一套无环流逻辑切换装置(DLC)。
DLC装置的任务:
在正组晶闸管整流桥工作时开放正组脉冲,封锁反组脉冲;在反组晶闸管整流桥工作时开放反组脉冲,封锁正组脉冲。
DLC的工作要求包括:
(1)DLC根据转矩极性信号和零电流检测信号,经逻辑运算后发出逻辑切换指令。
当改变极性,且零电流检测器发出零电流信号时,允许封锁原工作组,开放另一组。
(2)DLC发出切换指令后需经过封锁延时时间后才能封锁原导通组脉冲,再经开放延时时间后才能开放另一组脉冲。
通常,。
(3)在任何情况下,两组晶闸管不允许同时加触发脉冲。
根据分析,可逆调速系统各种运行状态时逻辑控制器输入与输出各量之间的关系见表3-1。
在表3-1中归纳合并重复项后,可以得到逻辑判断的真值表,见表3-2。
表3-1逻辑控制器输入与输出各量之间的关系
逻辑控制器输入
逻辑控制器输出
说明
电机转矩
电枢电流
正组整流器 VFUblf
反组整流器VRUblr
正向转矩
反向转矩
正向电流
反向电流
Ublf=0正组整流器工作
Ublf=1正组整流器封锁
Ublr=0反组整流器工作
Ublr=1反组整流器工封锁
正向启动零电流
>0
=0
0
1
正向启动有电流
正向运行有电流
>0
>0
0
1
本桥逆变有电流
<0
>0
0
0
本桥逆变零电流
<0
=0
1
0
它桥逆变有电流
<0
<0
1
0
反向启动零电流
<0
=0
1
0
反向启动有电流
反向运行有电流
<0
<0
1
0
正向制动
本桥逆变有电流
>0
<0
1
0
本桥逆变零电流
>0
=0
0
1
它桥逆变有电流
>0
>0
0
1
表3-2逻辑控制真值表
1
1
1
0
1
0
1
0
0
0
1
0
0
1
0
1
0
0
0
1
1
0
0
1
根据表3-2可以得到逻辑控制器输入和输出的逻辑关系表达式为(用与非门实现)
逻辑判断由与非门组成,其输入为转矩极性和零电流信号、;输出为逻辑切换信号、。
延时电路的设计:
前面的逻辑运算电路保证零电流切换,但仅仅采用零电流切换是不够的。
因为零电流检测装置的灵敏度总是有限的,零电流检测装置变成“0”态的瞬间,不一定原来开放组的晶闸管已经断流。
因此必须在切换过程中设置两段延时即封锁延时和开放延时,避免由于正反组整流装置同时导通而造成短路。
根据这个要求,逻辑装置在逻辑电路后面接有延时电路。
逻辑保护电路的设计:
逻辑电路正常工作时,两个输出端总是一个高电位,一个低电位,确保任何时候两组整流一组导通,另一组则封锁。
但是当逻辑电路本身发生故障,一旦两个输出端均出现低电位时,两组整流装置就会同时导通而造成短路事故。
为了避免这种事故,设计有逻辑保护环节。
逻辑保护环节截取了逻辑运算电路经延时电路后的两个输入信号作为一个或非门的输入信号。
当正常工作时,两个输入信号总是一个是高电位,另一个是低电位。
或非门输出总是低电位,它不影响脉冲封锁信号的正常输出,但一旦两个输入信号均为低电位时,它输出一个高电位,同时加到两个触发器上,将正反两组整流装置的触发脉冲全部封锁了,使系统停止工作,起到可靠的保护作用。
设计中采用单片机实现逻辑控制器的功能,设计的逻辑控制器如图3-2所示。
图3-2逻辑控制器电气原理图
3.4电流调节器设计
含给定滤波与反馈滤波的PI型电流调节器如图3-3所示:
图3-3含给定滤波与反馈滤波的PI型电流调节器
其中为电流给定电压,为电流负反馈电压,为电力电子变换器的控制电压。
3.4.1电流环结构框图的化简
在按动态性能设计电流环时,可以暂不考虑反电动势变化的动态影响,即≈0。
这时,电流环如下图3-4所示。
忽略反电动势对电流环作用的近似条件是
(3-1)
图3-4忽略反电动势的电流环动态结构框图
如果把给定滤波和反馈滤波两个环节都等效地移到环内,同时把给定信号改成,则电流环便等效成单位负反馈系统,如图3-5所示:
图3-5等效成单位负反馈的电流环动态结构框图
最后,由于和一般都比小得多,可以当作小惯性群而近似地看作是一个惯性环节,其时间常数为
(3-2)
则电流结构框图最终简化成图3-6。
简化的近似条件为
(3-3)
图3-6小惯性环节近似处理的电流环动态结构框图
3.4.2确定时间常数
1)整流装置滞后时间常数。
查表可知,三相桥式电路的平均失控时间。
2)电流滤波时间常数。
三相桥式电路每个波头的时间是3.3ms,为了基本滤平波头,应有(1~2),因此取。
3)电流环小时间常数之和。
按小时间常数近似处理,取。
3.4.3选择电流调节器结构
根据设计要求,并保证稳态电流无差,可按典型I型系统设计电流调节器。
电流环控制对象是双惯性型的,因此可用PI型电流调节器,其传递函数为
检查对电源电压的抗扰性能:
,查找典型I型系统动态抗扰性能与参数的关系表,各项指标都是可以接受的。
3.4.4计算电流调节器参数
电流调节器超前时间常数:
。
电流环开环增益:
要求时,查表可知,应取,因此
于是,ACR的比例系数为
3.4.5校验近似条件
电流环截止频率:
(1)晶闸管整流装置传递函数的近似条件
(2)忽略反电动势变化对电流环动态影响的条件
(3)电流环小时间常数近似处理条件
满足近似条件。
3.4.6计算调节器电阻电容
按运算放大器取,各电阻和电容值为
,取
,取
,取
按照上述参数,电流环可达到的动态跟随性能指标为,满足设计要求。
3.5转速调节器设计
含给定滤波与反馈滤波的PI型转速调节器如图3-7所示:
图3-7含给定滤波与反馈滤波的PI型转速调节器
其中为转速给定电压,为转速负反馈电压,:
调节器的输出是电流调节器的给定电压。
3.5.1确定时间常数
1)电流环等效时间常数,可知,则
2)转速滤波时间常数。
根据所用测速发电机纹波情况,取。
3)转速环小时间常数。
按小时间常数近似处理,取
3.5.2选择转速调节器结构
按照设计要求,选用PI调节器,其传递函数为
3.5.3计算转速调节器参数
按跟随和抗扰性能都较好的原则,取,则ASR的超前时间常数为
可求得转速环开环增益
满足系统的调速范围和静差率要求。
于是可得ASR的比例系数为
3.5.4检验近似条件
由式得转速环截止频率为
1)电流环传递函数简化条件
,满足简化条件。
2)转速环小时间常数近似处理条件
,满足近似条件。
3.5.5计算调节器电阻和电容
按运算放大器取,各电阻和电容值为
,取
,取
,取
3.5.6校核转速超调量
当时,查表可得,,不能满足设计要求。
实际上,由于该表是按线性系统计算的,而突加阶跃给定时,ASR饱和,不符合线性系统的前提,应该按ASR退饱和的情况重新计算超调量。
按退饱和超调量的计算方法计算调速系统空载起动到额定转速时的转速超调量,并校验它是否满足设计要求。
,满足设计要求。
4系统建模与仿真
4.1逻辑控制器的建模
(1)电平检测器建模。
电平检测的功能是将模拟量换成数字量供后续电路使用。
它包含电流极性鉴别器和零电流鉴别器。
在用Matlab建模时,可用Simulink的非线性模块组中的继电器模块Relay来实现。
(2)逻辑判断电路建模。
逻辑判断电路的功能是根据转矩极性鉴别器和零电流检测器输出信号和的状态,正确发出切换信号和封锁原来的脉冲,开放另一组脉冲。
(3)延时电路建模。
在逻辑判断电路发出切换指令后,必须经过封锁延时和开放延时才能封锁原导通组脉冲和开放另一