重介旋流器.ppt
《重介旋流器.ppt》由会员分享,可在线阅读,更多相关《重介旋流器.ppt(39页珍藏版)》请在冰豆网上搜索。
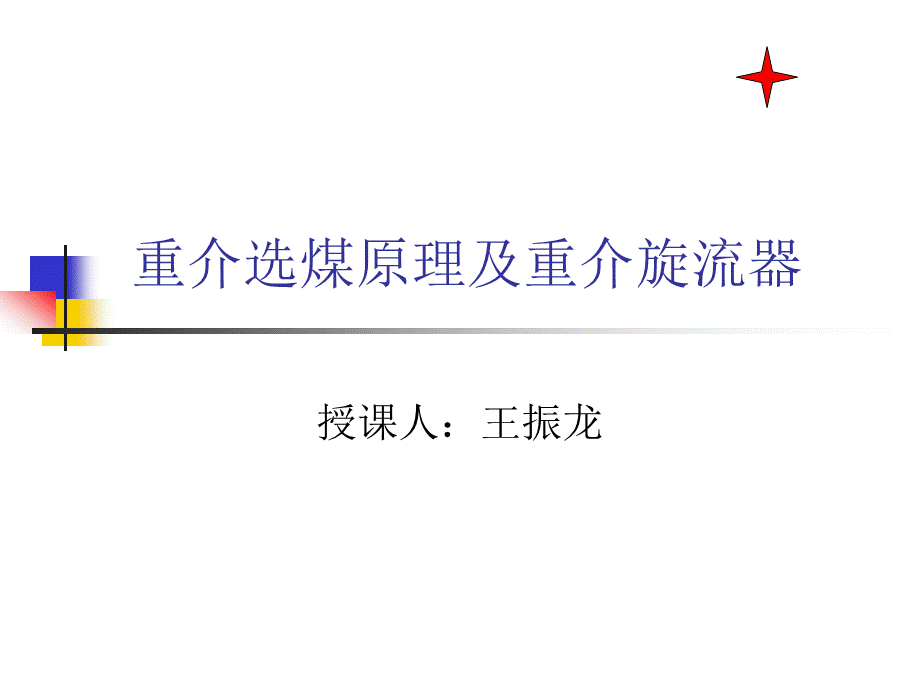
重介选煤原理及重介旋流器,授课人:
王振龙,一、重介质选煤原理,重介质选矿是重力选矿的一种方式,只是所采用的介质不同而已。
通常将密度大于水的介质称为重介质。
在这样的介质中进行的选矿叫做重介质选矿,它是按照阿基米德原理进行的。
通常所选用的重介质密度是介于被选物料中轻产物和重产物两者的密度之间,或者说使介质介等于所需求浮物(或沉物)质量指标的分选密度p,即浮介沉或介p在重介质中,选分过程完全属于静力作用的过程。
此时,介质的运动状态和颗粒在介质中的沉降规律,已不是形成分层的主导因素,而重介质本身的性质(如密度、粘度等)却是影响分选的重要因素。
二、重介质选煤特点及适用范围,重介质选煤特点:
1、分选效率高。
如图所示,各种选煤设备的可能偏差E值的比较。
从图中不难看出,重介质分选机和重介质旋流器的分选效率在各种重力选煤方法中是最高的。
2、分选密度调节范围宽。
重介选煤的分选密度一般是1300-2200kg/m3,而且易于调节,其误差可保持在0.5%范围之内。
3、适应性强,分选粒度范围宽重介质选煤在入选原煤的粒度、数量和质量上允许有较大的波动。
例如,块煤分选机的入料粒限为1000-6mm,末煤重介质旋流器为50-0.15mm,大直径重介旋流器的入料上限可提高到100mm。
4、生产过程易于实现自动化。
重介质选煤所用悬浮液的密度、液位、粘度、磁性物含量等工艺参数能实现自动控制。
重介质选煤的缺点是:
增加了加重质的净化回收工序;设备磨损比较严重;介质损耗增加了生产成本。
重介质旋流器分类方法较多;下面是几种常规的分类方法:
(1)按其外形结构可分为:
(2)按其选后产品的种类可分为:
(3)按给入旋流器的物料方式可分为:
(4)按旋流器的安装方式可分为:
三、重介质旋流器分类,圆柱形重介质旋流器;圆柱圆锥形重介质旋流器。
二产品重介质旋流器;三产品重介质旋流器。
周边(有压给原煤、给介质的重介质旋流器;中心(无压)给原煤、周边(有压)给介质的重介质旋流器。
正(直)立式、倒立式和卧式三种。
重介质旋流器工作机理,与水介质旋流器类似分选流场与水介质旋流器有很大差别,当料浆以一定的速度进入旋流器,遇到旋流器器壁后被迫作回转运动。
由于所受的离心力不同,密度大的颗粒所受的离心力大,能够克服水力阻力向器壁运动,并在自身重力的共同作用下,沿器壁螺旋向下运动,细而小的颗粒及大部分水则因所受的离心力小,未及靠近器壁即随料浆做回转运动。
在后续给料的推动下,料浆继续向下和回转运动,于是粗颗粒继续向周边浓集,而密度小颗粒则停留在中心区域,随着料浆从旋流器的柱体部分流向锥体部分,流动断面越来越小,在外层料浆收缩压迫之下,含有大量细小颗粒的内层料浆不得不改变方向,转而向上运动,形成内旋流,自溢流管排出,成为溢流,而粗大颗粒则继续沿器壁螺旋向下运动,形成外旋流,最终由底流口排出。
2.1、重介旋流器分选机理,2.1、重介旋流器分选机理,2、“矿粒在重介旋流器内受上升、下降液流作用的过程中,是按密度进行分离的,使分离点在重介旋流器的下部,即底流口附近。
因此重介旋流器的底流介质密度是决定矿粒在旋流器内分离密度的主要因素。
”,实际分离密度,-底流介质密度,2.1、重介旋流器分选机理,5、“把染色液体注入透明旋流器中,发现在旋流器锥体上半部出现一个明显的染色液环。
认为这个染色液环的界面代表着垂直零速面,同时也是径向零速面。
染色液环在直径为0.43D(D为旋流器直径),并在0.7D截面下形成矿粒分离锥面,认为轻密度矿粒只有进入锥面内才能从溢流口排出。
否则,从底流口排出。
”,重悬浮液在离心力场作用下,内部形成不同的“等密度面”。
密度自上而下,由内项外增加。
越靠近锥壁和底流口的密度越大越靠近溢流管附近的密度越小,产生原因:
重介质是由高密度固体粒子与水混合成的不均匀两相体系。
在较大的离心力场作用下,悬浮液在旋流器中受到强烈的浓缩作用。
从而造成悬浮液的密度在旋流器中分布不均匀。
底流密度与溢流密度差异、重介质粒度差异决定了煤和矸石的分析密度。
2.2、重介质旋流器等密度面,150圆筒圆锥型旋流器200圆筒型旋流器入料密度为1.43t/m3,2.2、重介质旋流器等密度面,影响因素1、加重质粒度2、重介质密度3、给料压力4、锥角5、底流口尺寸,分选悬浮液形成的密度场对保证物料在重介质旋流器内按密度进行精确分离起决定性作用矿粒进入旋流器中,矿粒逐渐扩散,按矿粒密度不同而处于相应的等密度线上。
在离心力作用下,密度大的矸石很快奔向器壁,在外旋流作用下由底流口排出。
密度轻的精煤在内旋流作用下从溢流口排出。
2.3、矿物分选过程,2.3、矿物分选过程,悬浮液形成密度场对精确分离过程起决定性作用的。
实际生产中对重介质旋流器内密度场检测困难。
只能通过实验室实验,结合旋流器入料点和各排料点悬浮液的流变特性测定,找出它们之间的关系,达到对旋流器内流场的调控。
2.4、分离锥面,分离锥面构想图,分离锥面的形成决定于垂直零速面,并与径向零位面有关,而分离锥面周截面的确定则与旋流器的结构有关。
流场运动特性的实验结果证实了分离锥面的存在。
2.5、重介旋流器分选过程(有压给料旋流器),1、入料管2、锥体3、底流口4、溢流管5、溢流室6、支架,2.5、重介旋流器分选过程(有压给料旋流器),优点:
分选精度高、介质循环量少。
缺点:
系统磨损严重、原料破碎泥化严重、入料上限小。
2.6、重介旋流器分选过程(无压给料旋流器),2.6、重介旋流器分选过程(无压给料旋流器),优点:
入料上限宽、处理能力大、管路磨损轻。
缺点:
分选精度容易受影响。
2.7、重介旋流器分选工艺流程(有压给料旋流器),三产品重介旋流器流程(泵给料),原煤破碎严重;泵磨损严重;入料上限受泵限制;循环量大;厂房低、流程简化;基本建设投资少。
2.7、重介旋流器分选工艺流程(有压给料旋流器),三产品重介旋流器流程(定压给料),厂房高、基建投资多。
原煤破碎轻;管路磨损轻;入料上限不受泵限制;循环量小;生产操作直观。
2.7、重介旋流器分选工艺流程(无压给料旋流器),无压给料(中心给料)三产品重介旋流器流程,工艺复杂;对细粒煤分选效果差。
2.7、重介旋流器分选工艺流程(无压给料旋流器),重介质选矿工作影响因素,3、影响重介质旋流器工作的主要结构因素,1、重介质旋流器的圆柱直径2、旋流器圆柱长度3、旋流器的溢流口直径4、溢流管长度和器壁5、旋流器的底流口直径6、旋流器入料口形状和尺寸7、旋流器的锥比8、旋流器圆锥角9、旋流器的安装角,3.1、结构参数,3.1旋流器的圆柱直径,中心给料:
煤:
2.55m3悬浮液;周边泵给料:
煤:
35m3悬浮液周边定压箱给料:
煤:
2.54m3悬浮液,式中:
直径D影响处理能力和入料上限。
3.2旋流器的长度,旋流器长度和容积主要取决于旋流器的圆柱尺寸,从而保证物料的有效滞留时间。
圆柱部分过短,易造成液流的不稳定,使选煤效率降低。
圆柱部分过长也会使分选效果变坏。
200圆柱圆锥旋流器:
k=(0.60.7)D200圆柱圆锥旋流器:
k=(0.72)D圆柱旋流器:
k=(26)D直径大的选小值,直径小的选大值。
圆柱长度与分离密度及效率的关系,4.3溢流口的直径,溢流口直径在(0.320.4)D一般选取0.4D。
易选煤溢流口可选取大一些。
旋流器直径确定后,溢流口直径与生产能力成正比。
溢流口直径与分离密度、可能偏差的关系,1、溢流管长度对切向速度无明显影响,但对精煤质量和分选精度又较大的影响。
溢流管增长时,溢流管下端至锥体下部距离缩短,促使实际分离密度增大,使分选结果变坏。
溢流管长度=(0.81.0)圆柱长,2、溢流管壁厚对切向速度影响较大,壁厚加大,使溢流管与器壁之间空间变小、流层变薄,从而使相同半径上的切线速度梯度增大。
厚管壁的轴向零速区较宽,速度由向下变向上有缓慢过渡区,使分选精度提高。
过厚的溢流管壁使重量增加,容积变小,对结果也不利。
3.4溢流管长度和器壁的影响,3.5底流口的直径,底流口直径在(0.240.32)D范围内底流口直径3dmax,3.6入料口形状和尺寸,入料口有圆形、矩形、扇形等多种,入料流线有切线、摆线、渐开线等方式。
入料流线对入料压头损失和液流稳定有一定的作用。
入料口形状无较大影响,入料尺寸过大,使流线难以保证,尺寸过少,影响入料上限。
入料速度:
45米/秒当量直径:
(0.20.3)D,3.7锥比,重介质旋流器锥比:
溢流口直径与底流口直径的比值。
锥比越小,分选密度越高。
反之,越低。
入选原煤属于难选煤时,锥比宜选小一点。
一般锥比在0.50.8。
溢流口与底流口直径由于磨损而增大的部分不能超过原来直径的3%。
一般在2%以下。
3.8圆锥角与旋流器安装角,主要出于工艺的需要,以及有利于旋流器给料、排料的方便和顺畅。
一般在1040度。
重介质旋流器圆锥角增大,实际分离密度迅速增大。
锥角增至80度后,变化显著变小,选煤效率迅速下降。
4、影响重介质旋流器工作的主要操作因素,1、入料压力:
定压箱给料:
煤t:
悬浮液m3=1:
(2.54)H=(911)D混合泵给料:
煤t:
悬浮液m3=1:
(35)P=(910)D105(帕),4、影响重介质旋流器工作的主要操作因素,2、悬浮液密度悬浮液密度波动在10kg/m3。
高密度分选可放宽一些,低密度分选要求更严一些(5kg/m3),5、影响重介质旋流器工作的主要操作因素,3、煤泥含量煤泥量小于60%时,随煤泥量增加,可能偏差减小。
随着煤泥量继续增加,10.5mm级煤的可能偏差随之增大。
加重质粒度粗时,可适当增加煤泥含量。
粒度过粗过细均会造成加重质损失,影响分选效果。
分流的作用机理,在悬浮液中泥质物的含量是处于动平衡状态。
进入悬浮液系统中的煤泥有原生煤泥和次生煤泥;而从悬浮液系统排出的煤泥包括产品带走的煤泥及稀介质和分流过来的一部分合格介质,经磁选后以尾矿形式排走的煤泥。
当原煤的数量、质量,选煤工艺流程及分流量等诸因素不变时,按照数质量进出平衡的原则,煤泥既不能在悬浮液系统中无限积存,也不可能在系统中无限减少。
进入系统的煤泥量与从系统中排出的煤泥量始终维持动平衡。
当某一因素变化时,这个动平衡便遭到破坏,其表现是煤泥在合格介质中的增加或减少,但到一定值后,又在新的条件下达到了新的平衡。
例如,若使分流量增大,虽然进入系统的煤泥量没变,但从磁选机排出的煤泥量增多了,也就是说,从系统中排除的煤泥量,大于进入系统的煤泥量,那么合格介质中煤泥含量逐渐减少,合格悬浮液的粘度便逐渐降低,于是脱介筛第一段脱介效果将改善,进入脱介筛第二段后,稀悬浮液中的煤泥量也将减少,最后由产品带走的煤泥量必然也就减少。
于是其结果导致系统中排除的煤泥量,逐渐与进入系统的煤泥量趋于平衡,也就在合格悬浮液中煤泥量减少的基础上,建立了新的平衡关系。
间歇性跑煤的原因,1.原煤在混料桶中按密度分层,当密度较低的原煤累计达一定数量后,集中进入旋流器,一部分精煤就从底流口被排出。
2.旋流器入料压力不稳或固液比不稳定,这样旋流器内部流场紊乱,精煤有可能从底流口排出。
3.底流口磨损,底流口增大,造成部分精煤随底流排出。
4.介质系统内煤泥累积,悬浮液粘度增高,分选精度下降,导致矸石跑煤。
6、悬浮液密度自动控制系统,