以风险为基础的质量体系和药品生产的物料管理130831.pptx
《以风险为基础的质量体系和药品生产的物料管理130831.pptx》由会员分享,可在线阅读,更多相关《以风险为基础的质量体系和药品生产的物料管理130831.pptx(87页珍藏版)》请在冰豆网上搜索。
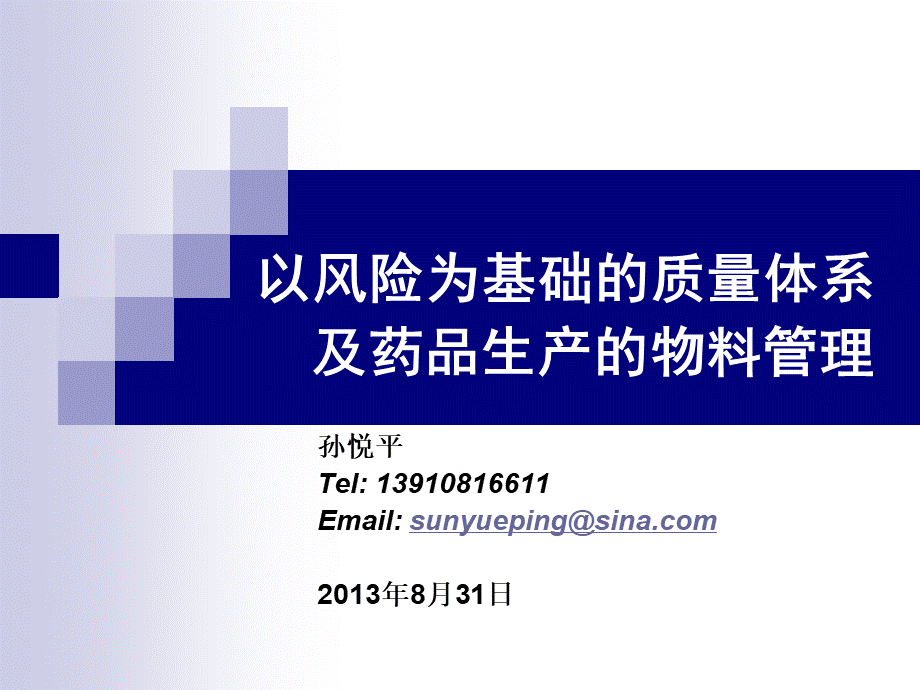
孙悦平Tel:
13910816611Email:
2013年8月31日,以风险为基础的质量体系及药品生产的物料管理,2,2,2023/10/3,自我介绍,孙悦平12年药理学和毒理学研究经历1978-1979:
北京市药检所药理室研究人员1982-1990:
首都医科大学药理学教研室讲师1986-1988:
瑞典皇家医学院毒理部访问学者23年制药企业和医药咨询经历1990-1991:
西安杨森制药有限公司药品注册经理1991-1994:
德国汉姆公司北京办事处原料药欧洲注册经理1994-2010:
医药咨询公司高级咨询师2010-至今:
独立咨询师,WHO外聘顾问,以风险为基础的质量体系及药品生产的物料管理,1.QRM与PQS的一体化建设2.QRM计划和组织实施3.原辅料管理4.物料供应商的管理,1.QRM与PQS的一体化建设,“以风险为基础的”的由来:
GMP发展的第一个里程碑:
1963年美国FDA颁布世界上第一部药品生产质量管理规范,对药品生产过程进行质量控制“好的产品是控制/检验出来的”。
GMP发展的第二个里程碑:
1978年6月,FDAGMP发布的药品工艺检查验收标准,提出了验证的要求。
标志着质量管理从“质量检验”提升至“质量保证”“好的产品首先是验证/生产出来的,然后才是控制/检验出来的”。
然而,要求的“验证”大多是基于GMP要求和行业标准而不是基于风险评估。
上世纪末FDA认识到基于GMP和行业统一要求限制了上市后药品的质量提升、技术创新和行业发展。
因此必须为GMP寻找新的基础,以适应、鼓励和促进技术创新和使企业形成质量体系不断完善和提升的管理机制。
4,2023/10/3,5,2023/10/3,1.QRM与PQS的一体化建设,2002年,FDA发布基于风险的21世纪的cGMP,提出在风险评估的基础上将质量设计到产品中,继而ICH根据这一指导思想起草了指导文件Q8、Q9和Q10:
Q8药品研发:
CTPP和CQAsCPP和设计空间QbD和PATQ9质量风险管理(QRM):
QRM的原则和程序规范的评估方法和应用Q10药品质量体系(PQS):
药品生命周期知识管理体系不断完善,1.QRM与PQS的一体化建设,欧盟修订了EUGMP的第一章药品质量体系:
为了与ICHQ10的理念和用词相匹配用药品质量体系(PQS)全面替代了质量保证(QA),将ICHQ10纳入EUGMP的第三部分,作为GMP第一章的补充说明。
(2013年1月30日生效),7,2023/10/3,1.QRM与PQS的一体化建设,PQS与传统GMP的差别:
为完善质量体系的行动提供一种新的思维逻辑:
传统GMP:
因为发现与GMP条款有差距,我们不得不进行改进。
被动地去符合指南的要求:
实践中会走形式甚至感觉迷茫PQS:
因为发现了新的影响产品质量的风险,我们需要制定新的控制措施和可接受标准。
主动地设计和完善质量体系:
实践中感觉受激励和有成就感PQS要求对所有影响药品质量的关键因素进行控制,但没有也不可能提出哪些是关键因素,因此这一体系必须建立在风险评估的基础上。
如果GMP仅关注那些与产品关键质量特性和工艺无关的条款要求,那么这种符合性是不能保证产品质量的。
因此,GMP要求只是最低标准,是PQS的一部分。
“为了可靠地实现质量目标,企业必须全面系统地设计并正确地执行PQS并与GMP和QRM相互融合”(见新修订的EUGMP第一章)。
1.QRM与PQS的一体化建设,PQS的设计始于生产工艺的研发:
首先建立产品质量目标档案(QTPP,QualityTargetProductProfile)识别药品的关键质量特性(CQAs)研究原辅料成分的质量特性选择一种适合的生产工艺,并设置关键工艺参数(CPPs)制定适合的质量控制战略将生产工艺的技术解决方案、物料和产品的质量标准和控制策略写成注册文件,申请上市许可证书,8,2023/10/3,1.QRM与PQS的一体化建设,1.QRM与PQS的一体化建设,研发资料向生产场地转移后,应识别和研究可能对工艺和产品特性产生影响的所有因素,以形成新的控制战略。
10,1.QRM与PQS的一体化建设,影响药品质量的所有因素可概括为人、机、料、法、环:
人员操作:
关键岗位的人员标准、关键操作的标准、监控标准等厂房与设备维护:
关键设备的使用、校准、清洁和维护标准等仓储与物料管理:
关键物料的质量标准、供应商标准、仓储运输环境标准、控制标准和检测方法等生产工艺过程控制:
各种过程控制标准,如关键步骤和关键控制参数的控制范围、中间产品和成品的质量标准和检测方法等药品生产环境的控制:
空气中尘埃粒子和微生物的控制标准、压差和气流控制标准、温湿度标准等所有关键因素的控制标准都必须要符合。
1.QRM与PQS的一体化建设,关键影响因素控制方法和可接受标准的确认和验证:
应通过审慎的战略思考建立关键因素的可接受标准或控制范围,所有这些因素和相关的可接受标准应包含在验证总计划之中。
应在科学技术基础上制定出能够满足可接受标准要求的控制方法。
这些技术方法和可接受标准应通过验证和确认程序的检验。
12,2023/10/3,第一百三十八条企业应当确定需要进行的确认或验证工作,以证明有关操作的关键要素能够得到有效控制。
确认或验证的范围和程度应当经过风险评估来确定。
1.QRM与PQS的一体化建设,1.QRM与PQS的一体化建设,因此,以风险为基础的PQS的设计过程可以表示如下:
1.QRM与PQS的一体化建设,在PQS建立和验证之后,大家都希望不会出现变化,但变化总是通过两种方式出现:
计划的变化(变更):
包括厂房、设备、物料、工艺及监控方法等关键因素做出变更。
特点是变化原因清楚,影响和后果不清楚,所以风险评估重点在于变更可能的影响的识别。
非计划的变化(偏差):
包括任何形式的系统失效,偏差、缺陷或不合格产品,以及其他问题。
特点是后果清楚,变化的原因不一定清楚,因此风险评估的重点在于根本原因调查。
当一种变化是重大的,不论是计划的或非计划的,都有必要重新进行验证或确认。
15,1.QRM与PQS的一体化建设,严格的变更控制程序是新版GMP中的最基本理念:
要有程序保证对计划变更进行预先的评估,其批准要先于实施,必要时应考虑向法规当局备案和获得批准。
在进行任何变更后,应进行评估以确认实现了质量目标并没有出现对产品质量的非预期的有害影响。
1.QRM与PQS的一体化建设,不断完善的机制是GMP符合性的关键:
在偏差、产品质量缺陷和其他问题的调查过程中,可以采用质量风险管理原则进行适当水平的根本原因分析。
(将在后面详述),17,2023/10/3,1.QRM与PQS的一体化建设,2.QRM计划和组织实施,新版GMP对质量管理体系的定义:
第二条企业应当建立药品质量管理体系。
该体系应当涵盖影响药品质量的所有因素,包括确保药品质量符合预定用途的有组织、有计划的全部活动。
问题:
贵企业是否有“影响药品质量的所有因素”的清单呢?
如何确定“影响药品质量的所有因素”?
“有组织、有计划的全部活动”包含了哪些活动?
你们的质量部门是否安排的计划了足够的这些活动?
2.QRM计划和组织实施,“影响产品质量的所有因素”是QRM的管理对象:
对“所有因素”的识别是质量管理的基础,因此质量部门应当有一份“所有因素”的清单。
随着药品知识的不断增加,这份清单会越来越长,因此这份清单是在整个药品生命周期中知识管理的结果。
这份风险清单中或许只有少部分因素是需要严格控制的,而对于一个因素是否需要进行控制的评判取决于风险评估。
在系统的评估之后,会形成一份从所有影响因素中筛选出的关键影响因素清单以下是风险评估的几项原则。
2.QRM计划和组织实施,质量风险管理的基本原则(中国新版GMP):
第十三条质量风险管理是在整个产品生命周期中采用前瞻或回顾的方式,对质量风险进行评估、控制、沟通、审核的系统过程。
问题:
如何通过前瞻或回顾的方式系统地实施质量风险管理?
如何对整个产品生命周期中的风险进行管理?
2.QRM计划和组织实施,质量风险管理的基本原则(中国新版GMP):
第十四条应当根据科学知识及经验对质量风险进行评估,以保证产品质量。
问题:
如何对科学知识和经验进行管理,并将其应用于风险评估?
在风险评估活动中,如何保证参与评估的人员能覆盖所有必要的知识?
2.QRM计划和组织实施,质量风险管理的基本原则(中国新版GMP):
第十五条质量风险管理过程所采用的方法、措施、形式及形成的文件应当与存在风险的级别相适应。
问题:
如何按风险级别制定差异化的质量管理程序?
如何针对对于不同的风险级别建立不同的文件系统?
2.QRM计划和组织实施,2012年3月,PIC/S发布了评估质量风险管理执行情况的GMP检查员助手备忘录此检查员手册有助于理解怎样的QRM能够被接受。
2.QRM计划和组织实施,上述QRM评估的检查员手册多次提出“风险管理计划”的概念:
要有一份高层的文件描述企业的QRM政策,其中包含范围、方案和组织QRM活动的时间表QRM系统应保证对质量风险的评估是基于对风险的系统识别,并包含所有可能发生的风险能证明QRM的运用是有计划的,而且清晰的定义了QRM的关键要素并形成文件在QRM开始执行之后,企业应将定期回顾风险管理计划中风险评估和输出的准确性,并形成文件,2.QRM计划和组织实施,应制定一份高级别文件,QRM主文件,作为计划的和系统的QRM活动的依据,它应包含以下内容:
公司的QRM的方针政策QRM的适用范围和模块划分QRM的组织结构和评估团队职责划分和决策程序风险评估的程序和相关工具文件体系和相关表格下层文件:
QRM年度计划,2.QRM计划和组织实施,有组织、有计划的质量风险管理活动:
ICHQ10体系的设计应适当地结合风险管理原则,包括采用适当的工具。
质量体系的有些方面可以是全公司的,另一些方面可能是产品导向的,。
为了方便管理,可将总体风险划分若干个模块,所有模块之和应能够覆盖所有质量风险,如分为:
厂房和环境设备设施物料和供应商岗位与人员生产工艺QA/QC监控,27,2.QRM计划和组织实施,将QRM融入PQS:
有计划的QRM活动是PQS建立过程的重要环节。
QA部门应按照模块组织和计划前瞻的和回顾的风险评估,这些活动的结果将成为PQS不断完善的基础。
2.QRM计划和组织实施,风险评估计划的实施:
QA部门应当有一名人员负责QRM,按照年度计划组织QRM活动。
每个月针对一个专门的模块。
每项活动都应召集风险管理团队以及有相关知识的技术人员参加,并准备好相关的资料和文件。
要引导参加评估的人员通过头脑风暴识别所有有可能发生的风险,做出各种假设:
什么可能出错?
可采用一些风险评估工具,如:
流程图平面图核查表鱼骨图(寻找根本原因),2.QRM计划和组织实施,通过风险分析制定风险控制计划:
在第一阶段的风险识别之后,可采用FMEA对清单中的所有风险因素进行风险分析,并得到风险的评分(风险优先数值,RPN)。
将每一项风险因素的得分与预先在FMEA方法SOP中设定的风险可接受限度相比较,可以做出是否需要采取风险降低措施的决定。
可以将需要控制的风险单独形成一个主要风险的清单,而其他不需要采取措施的风险形成残留风险的清单。
然后风险评估人员开始转入下一个步骤,针对每一项主要风险因素讨论采取何种措施来降低风险。
QA人员可以与每一个部门一起,通过措施类型筛选出各自的风险降低项目的列表,并按照这一项目列表制定出各自的工作计划。
2.QRM计划和组织实施,以下表格可适用于系统的风险评估:
-名称:
风险评估对象的名称或编码-系统失效:
指风险的现象描述,通常与风险可能性(P)的评判相关联-失效模式:
指失效如何对产品质量产生影响的描述,通常与风险严重性(S)的评判相关联-当前控制:
指当前已有的控制措施,通常与可监测性(D)的评判相关联-RPN:
风险优先数值,是上述三个评估数值,S,P和D的乘积,2.QRM计划和组织实施,不良事件引发的风险评估:
非计划的风险评估通常由各种不良事件所引发,例如投诉、偏差、官方检查或自检中发现的缺陷、不合格或退回的产品等。
应当针对不同级别的风险建立不同的程序,正式的、较正式的和非正式的。
正式的风险评估程序应当始于风险识别(与Q9相似),即根本原因的调查。
如果无法确定真实的根本原因时,可给提出最可能的根本原因的考虑(可以是多个),并将其填写到表格中。
当用人员失误作为原因时,应当论证其他基于工艺、程序或系统的失误或问题(如果存在的话)没有被忽略。
2.QRM计划和组织实施,不良事件引发的风险评估(续):
只有在根本原因得到确定后,才有可能对风险的严重性做出评估和制定风险的预防措施。
FMEA的工具也可以用于此类风险评估,而RPN数值可以为是否进入CAPA程序的决策提供参考。
应针对调查结果制定出适当的纠正预防措施(CAPAs),并跟踪和评估这些措施的效果。
如果风险级别较低,可采用非正式的程序。
相关责任人可以根据其的经验,以及与其他技术人员的交流(或没有交流)做出决策。
然而,此类决策应当填写一张简单的表格并归档,以说明风险决策背后的考虑。
2.QRM计划和组织实施,在日常工作会议中的风险评估:
除了前瞻性和事件触发的风险评估之外,制药企业各部门处理日常管理问题的工作例会也属于QRM活动。
这样的会议通常会处理小的风险或不良趋势,这些问题或趋势一般不会启动偏差报告。
然而,这些会议的记录只存在于参会人员的记录本上。
考虑到大部分日常管理经验是在这些工作会议上积累起来的,存在于参会人员之间的讨论之中。
基于知识管理系统的理念,这些信息也应当通过合适的方式进行管理。
公司应当拟定一份与前一张幻灯片相似的标准的会议记录表格,将会议沟通内容的记录从记录本转移到表格上,并将其归档到QRM文件体系之中。
2.QRM计划和组织实施,在日常工作会议中的风险评估(续):
通常每个车间(或其他部门)每周都会召开工作总结会,会议一般由车间主任主持,各个班组长和QA监督员参加。
这样的会议流程一般也是与ICHQ9规定的标准程序是一致的。
大部分工作总结会都从风险识别开始,通过提问和汇报,将上一周每个人发现的问题或不良趋势进行汇总。
然后通过风险分析决定是否采取风险降低措施。
而这些措施和下一周的相关工作计划成为会议的输出。
在下一周的工作例会上,上一周制定的风险降低措施将会得到评估,如果问题还没有解决,就应制定进一步的措施和计划。
部门的QA监督员应当对上述内容记录在标准的表格上,会后对发现的问题按照固定的风险模块进行分类,最后提交给QA部门。
2.QRM计划和组织实施,风险回顾或回顾性风险评估:
在下一年度的风险管理计划中,风险评估团队应当对每一个风险模块进行回顾。
回顾的范围包括前瞻性评估中识别的风险清单,上一年度中所有由不良事件触发的风险,由于变更引发的风险,以及每个部门在工作例会上讨论的风险等等。
高层管理人员(包括总经理)应当参与到质量风险回顾和PQS运行状况的回顾活动中,以抓住产品、工艺和体系不断完善的机会。
企业应当制定一种机制,当体系出现明显改变或得到新的信息(如投诉、偏差调查、变更控制等)时,可以随时启动对风险评估和管理计划的回顾。
2.QRM计划和组织实施,风险回顾或回顾性风险评估(续):
风险回顾的一个重要目标是审核风险降低措施的有效性,这类审核通常会与风险事件的审查相结合。
重要的是将调查到的风险事件的根本原因与预先识别的风险清单进行对比,如果根本原因没有出现在清单里,应当将其增加到清单。
而如果已经在清单中,就应当对相关风险进行重新评估,核查该风险是否被低估或降低措施的效果是否不足。
应设计一个耐用的质量风险的文件管理系统,保证所有时候识别的不同级别的风险、所有的风险降低措施、其执行情况和结果都能很好的归档(分别归档于不同的模块),并且容易进行定期的回顾。
37,2023/10/3,2.QRM计划和组织实施,风险回顾或回顾性风险评估(续):
所有单独的风险评估及其输出的结果的都应当得到回顾分析,并要有定期的控制措施和再评估以确保其有效性,即与当前的状况和控制相对应。
残留风险的清单也应进行回顾,确保这些风险在当前的知识和经验下仍然是可接受的。
风险管理计划回顾的有效性也应当受到关注,例如回顾的频率要经过论证,跟进措施的职责要明确,回顾性风险评估的结果应当下达到在适合的范围内。
3.原辅料管理,质量管理部在供应商审计中的责任起草和批准供应商的质量评估和现场审计程序;制订“内控标准”;对每一个物料供应商进行质量评估;组织实施对主要物料(关键物料)供应商的现场审计;供应商的批准或否决;保存供应商审计档案、文件和记录;定期对物料及供应商的状况进行回顾性审查;下达批准供应商的清单,及时更新,监督执行情况。
39,2023/10/3,3.原辅料管理,WHOGMP:
第8.8条:
质量管理负责人有义务协同其他部门批准能提供符合要求的起始物料和包装材料的供应商;第8.9条:
在批准供应商并将其列入合法供应商名单之前,首先要评估供应商。
评估要特别重视供应商的历史和所供应物料的性质。
如果需要进行现场审计,首先要确定供应商符合GMP的能力。
40,2023/10/3,3.原辅料管理,质量管理负责人与物料相关的职责(新版GMP第23条):
1.确保原辅料、包装材料、中间产品、待包装产品和成品符合经注册批准的要求和质量标准;3.确保完成所有必要的检验;4.批准质量标准、取样方法、检验方法和其他质量管理的操作规程;5.审核和批准所有与质量有关的变更;11.评估和批准物料供应商;14.确保完成产品质量回顾分析;15.确保质量控制和质量保证人员都已经过必要的上岗前培训和继续培训,并根据实际需要调整培训内容。
41,2023/10/3,3.原辅料管理,原辅料的前瞻性风险评估:
应根据上述风险评估程序确定哪些属于关键物料(主要物料)。
确定每一个关键物料的关键质量特性和控制范围。
列出影响关键物料的关键质量特性的所有可能的影响因素,并对其中关键的影响因素建立风险降低措施(如列入质量评估或现场审计项目清单)。
42,2023/10/3,3.原辅料管理,关键物料的风险管理:
风险识别:
根据制剂的技术要求制定关键物料的“用户标准”风险评估:
收集资料,评估潜在风险,收集的资料包括供应商资质证明文件质量标准与URS的差距供应商现场GMP审计报告(起草风险为基础的审核清单)其他:
如原料药杂质档案风险评定:
供应商的批准或否决风险降低:
关键项目的检测,增加备用供应商等风险接受:
合格供应商目录的发放风险审核:
建立供应商档案,定期对关键物料进行质量回顾审核,43,2023/10/3,3.原辅料管理,44,2023/10/3,风险评估,风险降低,回顾跟踪,不接受,沟通:
信息收集、评估、管理、调查、报告等,工具:
问卷表、流程图、鱼骨图、FMEA等,接受,关键物料的筛选和控制方案的制定,3.原辅料管理,关键物料(主要物料):
物料:
原料+辅料+包装材料关键物料:
经过风险评估确定的能够对产品的质量特性产生关键影响的物料,一般是指起始物料+内包装材料起始物料:
原料药+辅料核心物料:
活性物料(原料药)原料药是能够保证药品有效性和安全性的核心物料,必须严格控制。
原料药,关键物料,物料,起始物料+内包装材料,3.原辅料管理,关键物料:
原料药、部分辅料和内包装材料为什么关键?
(以片剂为例)对含量和杂质含量的影响主要取决于原料药(核心物料)对含量均一度的影响对原料药分散度有影响的部分辅料对生物利用度的影响原料药:
粉体性质、晶型辅料:
特殊理化性质,影响溶出度包装材料的影响密闭度透气性:
微生物污染、光照、氧化、受潮,46,2023/10/3,3.原辅料管理,关键物料的风险管理:
列出物料影响制剂质量的所有可能的模式(物料的潜在风险);根据收集的供应商资料,评估潜在风险的危害性、危害的可能性和可监测性,确定每一个物料潜在风险的风险值;将具有不可接受风险的物料纳入关键物料,并将需要控制的影响因素、控制范围或方式纳入URS或内控标准;关键项目的检测,供应商的现场审计,增加备用供应商等;合格供应商的批准;合格供应商档案,合格供应商目录的发放;定期对关键物料及其供应商进行回顾性审查。
47,2023/10/3,3.原辅料管理,仓储的现场管理,包括以下内容:
物料的接收:
接收环境、物料核查和清洁、物料接收档案物料的储藏环境:
温、湿度控制,昆虫和啮齿动物的控制,控制措施的有效性评估,相关设备的性能确认问题,门窗的管理物料的分区存放:
注意高敏感药物的隔离存放问题物料的标识:
标识应跟随每一个包装物料的取样:
取样环境和捕尘存在的问题物料的发放:
称重的问题仓储信息的记录、归档和回顾:
仓储信息应具备可回顾性物料的使用和中间产品的管理:
称重和配料前的审核,中间产品的储存环境,48,2023/10/3,3.原辅料管理,原辅料取样应根据对物料的风险分级和供应商的风险评估确定取样计划(见WHOTRS929有关取样计划的指南):
49,2023/10/3,3.原辅料管理,原辅料的质量回顾审核:
可以单独进行或与产品质量回顾报告合并进行,每年至少评估一次;根据积累的检测数据,评估是否存在不良的质量变化趋势;对于原料药,应当对杂质情况进行专项审查,考察是否出现新的未知杂质;应重点考察对产品有关键影响的原辅料参数,对积累的数据进行统计学分析,考察不合格的概率,进行风险评估;可根据质量回顾分析报告和风险评估报告调整原辅料质量控制的策略;如果在评估中发现异常趋势,应及时调查,必要时应对供应商进行现场审计。
50,2023/10/3,3.原辅料管理,原辅料的检测:
原辅料质量标准和检测项目应基于真正影响质量的参数。
一些影响产品质量的关键项目,即使药典标准没有规定,也应逐批检测。
可以根据风险评估的原则对某些非关键项目逐步加大监控周期。
3.原辅料管理,“应当制定相应的操作规程,采取核对或检验等适当措施,确认每一包装内的原辅料正确无误”。
逐个包装取样的主要考虑:
可能存在包装或标识错误。
如果原辅料供应商通过GMP认证,且经质量体系的现场审计确认不可能存在包装或标识错误时,可免于逐批取样,但在接收程序中应核实每一包装的原辅料上的标签,以及包装的完整性和密闭性(GMP第229条)。
如需每个包装取样做鉴别试验,可采用NIR技术,或对每个包装的样品进行混合,进行半定量分析,也可在每一包装的原辅料初次打开用于生产之前进行鉴别分析。
此外,批准放行的原辅料应在每个包装上附带标识,以便于核对。
3.原辅料管理,有效期和复验期:
新版GMP只规定贮存期内有不良状况时进行复验,但未规定超过复验期且复验合格是否可以使用。
按照药品管理法,超过有效期的药品属于劣药,而该法也将原料药纳入药品范畴。
原料药在国外一般采用复验期而不是有效期,超过复验期的原辅料经检验合格后,可以使用,但不可延长复验期。
使用接近复验期或超过复验期经检验合格的原料药时应进行风险评估,必要时应留样进行稳定性考察。
3.原辅料管理,第223条物料和不同生产阶段产品的检验应当至少符合以下要求:
(一)企业应当确保药品按照注册批准的方法进行全项检验;
(二)符合下列情形之一的,应当对检验方法进行验证:
1.采用新的检验方法;2.检验方法需变更的;3.采用中华人民共和国药典及其他法定标准未收载的检验方法;4.法规规定的其他需要验证的检验方法。
(三)对不需要进行验证的检验方法,企业应当对检验方法进行确认,以确保检验数据准确、可靠;药典未收载的方法必须要验证,收载的要确认。
3.原辅料管理,55,2023/10/3,分析方法的类型和验证项目(根据ICHQ2):
化学药物分析中需要验证的主要是色谱学、光谱学方法。
4.物料供应商的管理,第255条质量管理部门应当对所有生产用物料的供应商进行质量评估,会同有关部门对主要物料供应商(尤其是生产商)的质量体系进行现场质量审计,并对质量评估不符合要求的供应商行使否决权。
主要物料的确定应当综合考虑企业所生产的药品质量风险、物料用量以及物料对药品质量的影响程度等因素。
企业法定代表人、企业负责人及其他部门的人员不得干扰或妨碍质量管理部门对物料供应商独立作出质量评估。
56,2023/10/3,4.物料供应商的管理,第256条应当建立物料供应商评估和批准