生产光纤光缆工艺流程.docx
《生产光纤光缆工艺流程.docx》由会员分享,可在线阅读,更多相关《生产光纤光缆工艺流程.docx(53页珍藏版)》请在冰豆网上搜索。
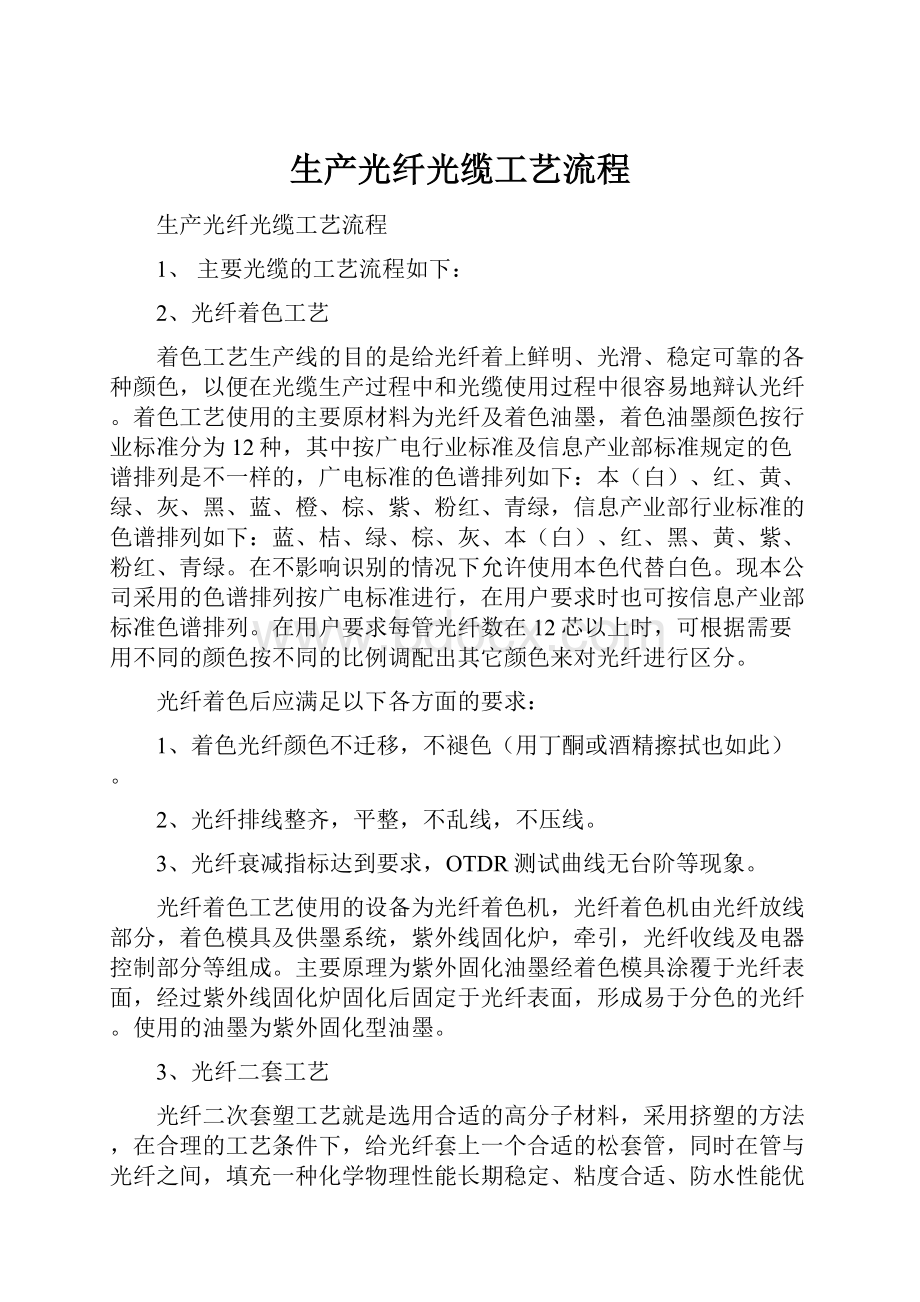
生产光纤光缆工艺流程
生产光纤光缆工艺流程
1、主要光缆的工艺流程如下:
2、光纤着色工艺
着色工艺生产线的目的是给光纤着上鲜明、光滑、稳定可靠的各种颜色,以便在光缆生产过程中和光缆使用过程中很容易地辩认光纤。
着色工艺使用的主要原材料为光纤及着色油墨,着色油墨颜色按行业标准分为12种,其中按广电行业标准及信息产业部标准规定的色谱排列是不一样的,广电标准的色谱排列如下:
本(白)、红、黄、绿、灰、黑、蓝、橙、棕、紫、粉红、青绿,信息产业部行业标准的色谱排列如下:
蓝、桔、绿、棕、灰、本(白)、红、黑、黄、紫、粉红、青绿。
在不影响识别的情况下允许使用本色代替白色。
现本公司采用的色谱排列按广电标准进行,在用户要求时也可按信息产业部标准色谱排列。
在用户要求每管光纤数在12芯以上时,可根据需要用不同的颜色按不同的比例调配出其它颜色来对光纤进行区分。
光纤着色后应满足以下各方面的要求:
1、着色光纤颜色不迁移,不褪色(用丁酮或酒精擦拭也如此)。
2、光纤排线整齐,平整,不乱线,不压线。
3、光纤衰减指标达到要求,OTDR测试曲线无台阶等现象。
光纤着色工艺使用的设备为光纤着色机,光纤着色机由光纤放线部分,着色模具及供墨系统,紫外线固化炉,牵引,光纤收线及电器控制部分等组成。
主要原理为紫外固化油墨经着色模具涂覆于光纤表面,经过紫外线固化炉固化后固定于光纤表面,形成易于分色的光纤。
使用的油墨为紫外固化型油墨。
3、光纤二套工艺
光纤二次套塑工艺就是选用合适的高分子材料,采用挤塑的方法,在合理的工艺条件下,给光纤套上一个合适的松套管,同时在管与光纤之间,填充一种化学物理性能长期稳定、粘度合适、防水性能优良、对光纤有长期良好保护性能、与套管材料完全相容的光纤专用油膏。
二套工艺作为光缆工艺中的关健工序,控制的主要指标有:
1、光纤余长控制。
2、松套管的外径控制。
3、松套管的壁厚控制。
4、管内油膏的充满度。
5、对于分色束管,颜色应鲜明,一致,易于分色。
光纤二次套塑工艺使用的设备为光纤二次套塑机,设备组成由光纤放线架,油膏填充装置,上料烘干装置,塑料挤出主机,温水冷却水槽,轮式牵引,冷水冷却水槽,吹干装置,在线测径仪,皮带牵引,储线装置,双盘收线及电器控制系统等组成。
4、成缆工艺
成缆工艺又称绞缆工艺,是光缆制造过程中的一道重要工序。
成缆的目的是为了增加光缆的柔软性及可弯曲度,提高光缆的抗拉能力和改善光缆的温度特性,同时通过对不同根数松套管的组合而制造出不同芯数的光缆。
成缆工艺主要控制的工艺指标有:
1、成缆节距。
2、扎纱节距,扎纱张力。
3、放线、收线张力。
成缆工艺使用的设备为光缆成缆机,设备组成由加强件放线装置,束管放线装置,SZ绞合台,正反扎纱装置,双轮牵引,引线及电器控制系统等组成。
5、护套工艺
根据光缆不同的使用敷设条件,缆芯外加上不同的护套,以满足不同条件下以光纤的机械保护。
光缆护套作为光缆抵御外界各种特殊复杂环境的保护层必须具有优良的机械性能、耐环境性能、耐化学腐蚀性能。
机械性能指光缆在铺设、使用过程中,必然受到各种机械外力的拉伸、侧压、冲击、扭转、反复弯曲、弯折作用,光缆护套必须能经受这些外力的作用。
耐环境性能指光缆在使用寿命中,要能经受住外界正常的此外线辐射、温度变化、潮气的侵蚀。
耐化学腐蚀性能指光缆护套能耐受特殊环境中的酸、碱、油污等的腐蚀。
对于阻燃等特殊性能则必须采用特殊的塑料护套来保证性能。
护套工艺要控制的工艺指标有:
1、钢、铝带与缆芯的间隙合理。
2、钢、铝带的搭接宽度满足要求。
3、PE护层的厚度满足工艺要求。
4、印字清晰,完整,米标准确。
5、收排线整齐,平整。
护套工艺使用的设备为光缆护套挤塑机,设备组成由缆芯放线装置,钢丝放线装置,钢(铝)纵包放带轧纹成型装置,油膏填充装置,上料烘干装置,90挤塑主机,冷却水槽,皮带牵引,龙门收线装置及电器控制系统等组成。
着色工序工艺控制;着色工序:
所谓着色是在裸纤(本色光纤)外在涂覆一;着色工序是光缆生产控制的第一道工序,同时也是光缆;在着色工序生产过程中,经常遇到的质量问题主要有以;影响断纤因素主要有以下几点:
模具尺寸合理选用;;光纤导轮的部位有杂质或硬块,将高速运行的光纤刮;光纤本身有质量问题:
如本色纤强度较差、有裂点、;着色模具的大小与光纤断纤有着直接的关系,选
着色工序工艺控制
着色工序:
所谓着色是在裸纤(本色光纤)外在涂覆一层颜色涂料,其涂料成份中含有光引发剂,通过吸收紫外光产生自由基从而引发聚合反应,将涂料由液体变成固态,从而紧密牢固地附着在光纤上,以便光纤的颜色识别和工程接续。
光纤收线张力
光纤本身有质量问题:
如本色纤强程中因断纤产生高速摔打模具合格度较差、有裂点、夹丝等。
1.1模具合格选用
着色模具的大小与光纤断纤有着直接的关系,选择合适大小的着色模具可以降低光纤因模具配比不合适产生断纤的情况。
着色模具根据光纤外径进行选择,在实际生产中选择合适进出口模具尺寸。
一般情况进口模具比出口模具大10υm左右,因为在进口模处光纤入模口时有轻微高频震荡,进口模太小时容易导致光纤因震动而刮伤产生断纤。
实际生产中参考模具配比
1.2着色模口有杂质堵塞
同种颜色着色光纤长时间着色生产,会在模具口堵塞着色料硬块或杂质,光纤生产过程中可能导致光纤刮伤断纤。
同种颜色着色光纤长时间着色生产,会在模具口堵塞着色料硬块或杂质,光纤生产过程中可能导致光纤刮伤断具。
1.3光纤导轮部位有杂质等赃物。
光纤高速生产过程中,可能产生漏料等情况将各部位导轮弄脏或堆积杂质以及在高速生产过程中产生静电将灰尘杂物吸附到导轮等光纤走线部位,造成光纤受伤产生断纤。
在实际生产中,应对着色车间进行除尘、封闭,并定期清洁光纤走线部位。
1.4光纤收线张力
着色工序光纤生产过程中,收线张力需要合理控制,若张力不足时,容易导致光纤松弛排线不良(抛线、压线、跳线等),最终可能会导致着色光纤在二次套塑工序的放线端容易被拉断。
但收线张力太大时,光纤内部应力比较大,容易产生1550波长衰减大。
1.5光纤本身质量问题
因光纤本身质量问题(强度差张力筛选不合格、有裂点)等情况属于原材料质量问题,此问题不在本次论述范围之内。
本文主要讨论因光纤运输等原因造成光纤内部存在跳线等原因而产生的断纤情况。
现阶段光纤运输多为航空运输,运输过程可能经过多次搬运,搬运过程中大多存在不注意轻拿轻放和不按光纤包装标识进行搬运情况,造成光纤在运输过程中受力,使光纤内部产生跳线、压线等情况,从而在着色生产过程中产生断纤。
光纤生产公司虽然不能控制光纤运输等环节,但光纤到厂后应注意轻拿轻放,严格按照光纤包装标识进行搬运,防止光纤再次受力,降低着色生产过程中断纤的几率。
1.6着色过程中因断纤产生高速摔打。
主要发生在光纤收线盘上,着色结束时收线盘未能及时停止而导致光纤末端突然断纤并打伤光纤盘上的光纤;同样,在放线盘上突然发生断纤时也可能会发生光纤摔打问题
在实际生产中,着色设备控制系统至光纤着色生产前设定长度前250m左右时开始降速生产,线速降至150m/min时开始上下盘,防止光纤产生摔打。
发生摔打的光纤末端某个部位光纤可能已受伤,所以在投入二次套塑生产前,进行外观检查,在白炽灯下检查明显就看到光纤表面存在白色的亮点,通常1500m/min线速生产时发生断纤摔打时外端500m光纤可能会受伤。
(具体情况具体分析)
2固化
着色光纤固化不合格表现出来的现象通常有:
光纤收线很紧,整盘光纤特别硬;在用酒精棉擦拭光纤时出现掉色情况;并带时光纤剥离性不好,光纤粘带。
光纤固化度检测方法:
用脱脂棉蘸溶剂(95%医用酒精)来回擦拭100次,擦拭力度应均匀适中,已能够听见“吱吱”的摩擦声为宜,固化测试过程中着色光纤不发生颜色迁移。
影响光纤固化不良原因有以下几点:
氮气流量;油墨搅拌;清洁石英管;清洁反射板。
紫外灯灯管最大工作功率,固化炉温度控制。
氮气流量控制。
氮气在固化过程中的作用,由于氧气会阻止液体油墨中高分子聚合物链的交联,使油墨固化不完全,而氮气的作用是隔绝空气中氧气成分,其纯度要保持在%以上,且流量应控制在适当范围,过小的流量不能阻隔氧气,过大则会产生真空效应,反而将固化区进口处的空气吸进去。
实际生产中,氮气流量应保持在~h,液氮罐体使用极限压力应在左右,以避免因压力不足影响着色光纤的固化和防止外界空气混入影响液氮纯度。
油墨生产前应搅拌均匀
着色油墨黏度会随温度和压力的变化而相应改变。
当黏度越大时,油墨的流动速率就越小,表面附着力就越大。
当光纤从模口处快速移动时,由于液面的粘滞,油墨并不跟光纤一起运动,而是保持相对静止,从而造成着色时会引起颜色深浅不一,甚至着不上色和着色层固化不好等问题。
可以看出通过找到速度与黏度的平衡点来克服着不上色或着色固化不好等现象发生。
在实际操作中,我们可以通过提高涂覆压力、适当升高涂覆温度以降低油墨黏度或降低生产线速来实现平衡,从而解决着色过程中出现固化或着不上色等问题。
可以看出温度越高,油墨黏度越小,油墨黏度与温度成反比。
由于油墨中的颜色颗粒是一种无机矿物质,密度较大,经长时间放置后,会出现沉淀现象,这会严重影响油墨的黏度,色度和均匀性。
所以着色油墨在使用之前,必须被充分搅拌均匀,应放置在以8转/分的速度的滚料器上滚动6小时以上或用不锈钢棒手动搅拌5分钟(若用其它材料会催化油墨的反应而引起胶化)。
手动搅拌时应顺着一个方向搅拌,尽量避免产生汽泡;且每搅拌一周后,应将不锈钢棒轻轻的从油墨瓶底提起来,以便将底部的颜料带到表面,使之达到均匀的效果。
实际生产过程中涂杯温度应控制在50℃左右。
定期清洁石英管
石英管应干净透亮、无水珠、水斑、无指纹印。
石英管内外表面的洁净度对紫外光的透过率影响极大,表面有灰尘的石英管在紫外波段的透过率低于干净的石英管,表面非常脏石英管的透过率大约是干净石英管透过率的20%。
采用国内某品牌的油墨,在着色速度一样和不同氮气流量下,着色固化情况。
注:
生产过程中应根据实际情况更换石英管。
酒精棉测试固化度(擦拭次数)
氮气流量
16㎡/h
0㎡/h
干净石英管
100>
20>
有点脏石英管
80>
10>
非常脏石英管
20>
5>
定期清洁反射板
定期擦拭固化炉反射罩,保证其良好的镜面效果;
紫外灯光管工作功率及固化炉温度控制
通过配置智能电源,改变传统电源始终最高功率工作方式,通过对灯管功率的由低逐级调整至最高的工作方式,以达到延长灯管使用寿命、节约电量和提高生产速度的目的。
配置高精度单体固化炉,对光源反射聚焦精度严格控制。
改变原配置的双体固化炉,以达到减少灯管数量、减少氮气充气流量、提高着色固化质量的目的。
智能电源功率增大与线速度关系为:
W=Kv;K值越;图1智能电源功率调整关系示意图;在实际生产过程中应将紫外灯灯管提前预热,避免因固;光纤着色是光缆制造过程中的第一道工序,着色质量。
智能电源功率增大与线速度关系为:
W=Kv;K值越大,对应线速度的固化模块输出功率越大,光纤的固化也越高。
生产人员只需根据智能不功率情况及当前功率下光纤固化程度设定合适的K值,就可得到符合工艺性能的光纤固化。
在实际生产过程中应将紫外灯灯管提前预热,避免因固化炉温度不够而产生光纤固化不合格情况,同时注意控制风机流量及频率,将固化炉温度控制在100℃~120℃为宜。
3结束语
光纤着色是光缆制造过程中的第一道工序,着色质量的好坏不仅直接影响到光纤的传输性能和温度性能,同时也会影响到光缆的性能和质量。
在实际生产中,只有严格按照工艺要求生产出符合标准要求的产品,从而确保光纤、光缆产品质量要求。
摘要:
本文主要介绍着色工序常见的一些不合格现象及对其产生原因进行分析,并根据个人实践经验提出了相应解决的办法,以期与广大生产技术人员共同探讨。
关键词:
着色问题原因分析解决
一、前言
光缆系统中的光纤是用色标来识别的,在光纤进入用户环的系统中,对光纤芯数的要求越来越多,尤其是在大芯数光缆系统和带状光缆系统中,对光纤的识别变得越来越重要。
为了便于连接和维修,必须对光纤进行着色。
在着色工序中,除了要求具有较高的生产速度外,还要求不能对光纤本身的质量产生任何的影响。
1550nm窗口对光纤的状态如微弯、应力等非常敏感,如光纤着色后受到应力或产生微弯,就会使光纤产生附加损耗。
因此,在着色过程中如何避免光纤产生内应力和有效地解决微弯问题,是保证光纤着色质量的关键。
另外,为了保证光纤在使用过程中着色层不脱落、颜色不迁移,保证光纤具有较高的固化度也是极其重要的。
因此,着色工序作为光缆生产的第一个工序,保证着色光纤的着色质量对后续工序显得尤为重要。
二、着色过程中的常见问题及原因解析
1.光纤着色后衰减偏大
光纤在着色后会通过OTDR测试仪进行衰减测试,来测试光纤在着色后的传输性能,主
要是针对1310nm窗口和1550nm窗口,当测试结果偏大于标准所规定的值时,我们通常称之为衰减偏大,由于光纤在1550nm窗口对微弯和应力等因素较敏感,如果在着色过程中不注意的话,很容易会产生衰减偏大的现象。
而产生这种现象排除人为的因素外,主要有以下几方面的原因:
空气中的粉尘颗粒在机器高速运转过程中可能通过粘附或通过静电作用吸附在光纤
上进入到模具,或者像立式着色机所用的开口杯模具,灰尘可以直接掉落在模具中,经过积累会堆积在模具口,在光纤高速通过时产生摩擦应力,造成着色光纤下盘后衰减偏大,所以针对这种现象需保证着色车间的洁净度和干湿度,如果着色车间的洁净度和干湿度达不到要求的话,必须提高着色模具清洗的频率。
收放线张力过大或不稳会造成光纤衰减偏大。
通常在光纤着色过程中,如果收放线张力过大,会使光纤产生较大的内应力,造成着色光纤在1550nm窗口产生较大的附加损耗,如果张力不稳定、不均匀或者张力轮跳动则会产生跳线、压线现象,使光纤反射衰减曲线出现台阶,而影响光纤的传输性能。
2.着色光纤表面脱色
在着色生产过程中,经常会遇到光纤表面脱色问题,就是着色后发现不同长度的本色光纤未着上色,其长度从几厘米到几公里不等。
究其原因在于:
光纤在着色过程中,本色光纤以一定的速度被拉入到紫外固化涂料中,由于着色涂料的粘性且着色涂料液与本色光纤表面无相对滑动,所以在着色涂料和本色光纤接触的液面形成动态的
弯液界面,同时粘性流会在受限制的模具出口处驱动一流体压力,此液体压力会形成回流。
由于压力、粘度和线速度等条件的变化时,可能会引起弯液面不稳定或消失,此时会造成着色缺陷甚至会引起脱色。
以常见的某着色机所使用的开口杯模具为例,当油墨在模具内形成回流时,光纤正常涂覆,如图1所示;当油墨液面由于压力、粘度和线速度等条件的影响,使之消失或者不稳定时,就会产生脱色现象,如图2所示。
若是着色油墨未充分搅拌或者搅拌后静置时间过长,则会使油墨产生分层现象,在生产时,着色料会从下模具口漏出,并积聚在下模具口周围,在UV光长期的照射下形成树枝状,造成运行中未固化的着色光纤被该积聚物刮掉或擦掉,导致着色光纤脱色。
3.着色层同心度不良问题
着色生产过程有时会出现着色同心度不良的问题,即我们俗称的着色偏心现象(如图3),而引起这种问题的原因有以下几种:
放线张力过小,高速运动的本色光纤在进入模具后会产生抖动,使得油墨涂覆不均,会造成偏心现象。
模具与模座之间的同心度有偏差,使得本色光纤在进入模具后,与模座所在的平面不是呈垂直状态,从而造成油墨涂覆不均匀,产生偏心问题。
着色模具磨损或者有缺陷也会使得油墨涂覆不均匀,产生偏心问题(如图4)。
4.光纤着色层偏淡甚至着不上色问题
在着色生产过程也经常会遇到着色后光纤颜色偏淡甚至着不上色的情况,产生这种问题
的原因在于:
模具没有清洗干净,使得模具孔径被灰尘颗粒堵住,当本色光纤从模具孔径高速拉
出的时候,只有少量的油墨甚至没有油墨粘附在光纤上,从而造成颜色偏淡甚至着不上色。
着色油墨的使用不当也会造成着色光纤颜色偏淡甚至着不上色的问题。
由于油墨的
黏度对温度非常敏感,以国内普遍使用的上海飞凯油墨为例,其温度黏度如表1所示,由此表可以看出,油墨的黏度和温度是成线性关系的。
油墨中的颜料含有机物质,密度较大,经长时间放置后,会出现沉淀分层现象,这会严重影响油墨的黏度、色度和均匀性,在着色时会产生颜色偏淡甚至着不上色情况。
根据经验保存油墨在恒温25~30度左右,滚动搅拌4~6小时最为合适,时间不宜过长,且在搅拌前需将瓶子上下颠倒数次。
表1油墨温度黏度表
产品型号
颜色
(飞凯)温度粘度数据(cps)
15℃
25℃
35℃
45℃
55℃
60℃
KI1000
无色
7256
2684
1003
KI1001
蓝色
7730
2702
1090
KI1002
橙色
7021
2597
1077
KI1002
橙色
7021
2597
1077
KI1003
绿色
7110
2630
1048
KI1004
棕色
7145
2643
1095
KI1005
灰色
7029
2600
1039
KI1006
白色
7110
2630
1052
KI1007
红色
7232
2675
1087
KI1008
黑色
6862
2538
1064
KI1009
黄色
7529
2785
1149
KI1010
紫色
6819
2522
1077
KI1011
粉红色
7002
2590
1075
KI1012
青绿色
6762
2501
1023
5.着色光纤固化不良问题
着色光纤固化不良的的问题在着色生产过程中应该是屡见不鲜,通过对固化原理的分析很容易能找到产生固化不良问题的原因。
众所周知,UV固化的反应机理是自由基聚合反应,如果环境中有氧气存在,氧气会与自由基反应,产生过氧自由基,会极大的降低固化速度。
因此对氮气流量的控制显得尤为重要。
石英管的质量和洁净度对着色固化影响非常明显,因此使用的石英管必须是由杂质含量很低,透光率很高的石英玻璃制成,而且需保证石英管内外的洁净度。
反光罩的质量和洁净度也对着色固化影响极其明显,反光罩的反射原理图如图5所示,因此在生产过程中要严格保证反光罩的洁净度。
三、结束语
越来越多的光缆厂家把套塑和护套工序定为特殊工序或者关键工序,却越来越忽视光纤着色质量对后续工序的影响作用,而光纤着色作为光缆制造过程中的第一道工序,着色质量的好坏有些可通过下盘检测直接测出,有些可能不会直接测出,如一切应力、裂纹,但会对光纤长期寿命有影响即影响到光缆的性能和质量。
本文从工艺的角度列举了光纤着色生产过程中常见的技术问题,并对这些问题进行深入的分析,提出相应的解决办法。
各公司在生产中均摸索了一套适合本公司特点的生产工艺,只要严格按照工艺要求认真操作,就能生产出合格的着色光纤,满足光缆的技术要求。
袁巍 谢鸿志
中国电子科技集团公司第八研究所 淮南 232001
【摘要】本文主要介绍了ZS04型着色复绕机的组成和工作原理,并着重讲述在光纤着色复绕生产过程中比较重要的几个环节及解决办法。
关键词:
着色 自动控制
1 引言
光纤着色复绕机是缆化工艺中关键的第一步工序。
随着需求量的日益增加,目前光纤着色机已经成为大中型光缆生产厂家必备的专用设备之一,为了适应国内市场的需要,提高设备的机械自动化,降低生产成本,满足国内外光缆生产厂家不断对设备提出的更高要求,我所研制出第四代光纤着色复绕机——ZS04型光纤着色复绕机。
该机具有以下特点:
(1)结构速度高达:
1500m/min
(2)自动化程度高,具有放线、张力控制、UV固化炉、收排线各部分工作失效即自动报警、停机功能。
2 设备组成
ZS04型着色复绕机主要由以下几个部分组成:
(结构示意图如图1)ZS04光纤着色复绕机工艺流程框图如图2所示。
3 组成及功能
在ZS04型着色复绕机中,我们根据生产工艺实际情况出发,同时吸取了国外同类产品的优点,采用典型两极监控的系统控制方案。
上位机和下位机之间通过PPI协议进行通讯,上位机作为生产管理级,主要面向生产操作人员。
下位机作为数据采集和生产现场监控级,主要完成生产过程参数的数据采集,执行控制算法及控制输出等任务,面向生产过程。
3.1 上位机
上位机采用西门子人机界面产品OP27图型操作员面板,配有5.7寸单色液晶,组态软体是基于PC的可视化监控软件otool.。
它的功能如下:
1)显示工艺流程和各参数实时测量值;2)可实时修改下位机和需要的控制参数值;3)能实时显示故障报警画面。
3.2 下位机
下位机采用西门子微型可编程控制器S7200,体积小巧,功能全面,适合于各行各业、各种场合中的检测、监测及控制的自动化,且有高速、多功能、系统化、模块化、可靠性高的特点。
以模块为基础组成分布集散控制系统,对光纤放线、牵引控制和收排线等部分进行有效的控制。
PLC系统选用了CPU226和电源模块,另外还扩展了三个模块,其中两个是模拟量输出模块EM232,共有四路输出,主要提供放线、牵引、收线及收线排线的给定。
另外一块是四输入一输出模块EM235,其中一路输入用于灯管电流的检测、一路用于检测放线盘位置传感器的信号,以达到放排线自动跟踪的目的、另外两路输入用于检测收放线舞蹈轮的位置、一路输出用于提供放线排线的给定。
4 控制过程及特点
限于篇幅本文只给出ZS04型光纤着色机的控制框图,上位机的控制过程如图3所示,下位机的控制过程如图4所示。
ZS04型是在ZS03型光纤着色机以及消化吸收国外同类产品的基础上进行的。
它在以下几个方面作了较大的修改:
1)把光纤放线和收排线部分放入机柜内,并使机械电气分开,减少干扰;2)采用移动式光纤放线架,使放线抖动减小;3)采用一个大功率UV光固化炉,是光纤着色速度提高;4)除去以往零散的用于输入输出各种参数的控制部件,改用可通讯的人机界面产品替代,提高了整机的自动化控制;5)在光纤进入涂复系统前以及在光纤收排线装置之前增加了除静电装置。
5 重要环节的处理
比较上一代着色机,ZS04型着色复绕机在工艺上及自动控制上采取了许多的新思路,对其生产过程中的光固化灯管的自动控制、张力恒定性的控制、排线精度的控制以及除静电的利用,都保证了着色后的光纤附加损耗不致超标。
5.1 生产过程中光纤着色前后张力的恒定
ZS04着色复绕机的着色速度为1200m/min左右,并且收、放线部分要满足50km整盘的放线和收线过程。
在生产过程中,由于收放线盘径是渐渐发生变化,而生产速度恒定,就需要不停地修改收放线速度使张力趋于恒定。
以往着色机采用人工电位器调整改变收放线速度实现,这种方法既不安全也不可靠。
为了确保整个着色过程放线和收线舞蹈轮的稳定性,我们首先在硬件方面对放线、牵引、收线、排线全部选用了松下交流系统MINAS,保证了过程的一致性。
在这个基础上,采用S7-200的闭环控制,再根据着色过程中收放线长度即盘径的变化规律,在软件上编制算法来自动地修改收放线盘的快慢而使上下舞蹈轮在50km整盘的过程中始终能稳定在适中的位置而无须人工干预,保证了张力的稳定性。
经现场调试,用这种方法完全满足光纤着色中的工艺要求。
5.