断口分柝及处理.docx
《断口分柝及处理.docx》由会员分享,可在线阅读,更多相关《断口分柝及处理.docx(36页珍藏版)》请在冰豆网上搜索。
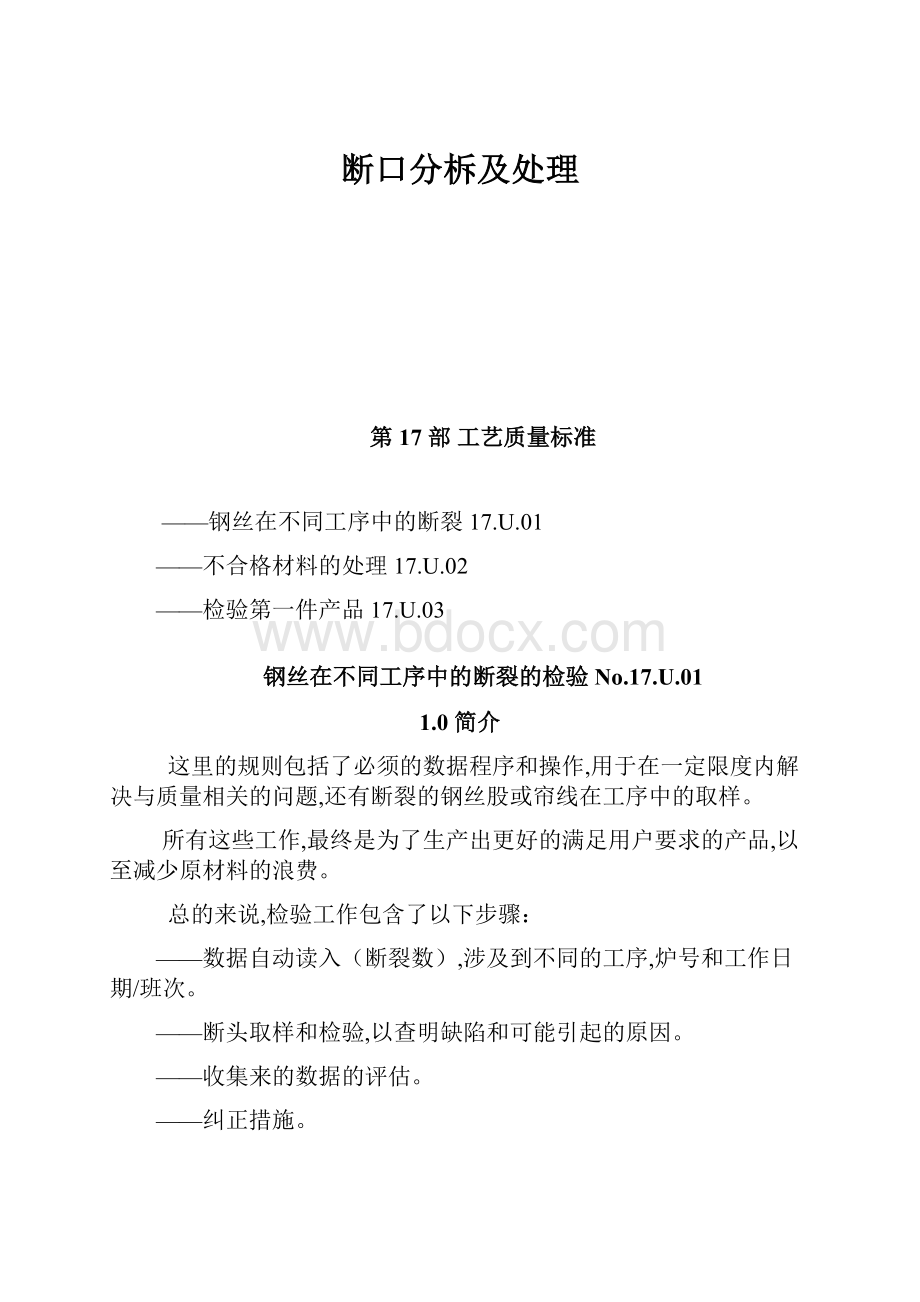
断口分柝及处理
第17部工艺质量标准
——钢丝在不同工序中的断裂17.U.01
——不合格材料的处理17.U.02
——检验第一件产品17.U.03
钢丝在不同工序中的断裂的检验No.17.U.01
1.0简介
这里的规则包括了必须的数据程序和操作,用于在一定限度内解决与质量相关的问题,还有断裂的钢丝股或帘线在工序中的取样。
所有这些工作,最终是为了生产出更好的满足用户要求的产品,以至减少原材料的浪费。
总的来说,检验工作包含了以下步骤:
——数据自动读入(断裂数),涉及到不同的工序,炉号和工作日期/班次。
——断头取样和检验,以查明缺陷和可能引起的原因。
——收集来的数据的评估。
——纠正措施。
2.0断头取样用以查明缺陷
钢丝或帘线断头的取样由生产操作工完成。
操作工必须给样品挂上标签并放在适当的容器内。
质检部门在每班结束时取样:
——粗拉钢丝:
所有收集来的样品
——中拉钢丝:
所有收集来的样品
工序缺陷类型
湿拉/并线(双捻)——发生在湿拉开始的表面缺陷
——发生在湿拉过程中的表面缺陷
——缩丝(逼细)
——在湿拉过程中的焊接引起的缺陷
——杯锥状缺陷
——表面起瘤
——夹渣
——扭转缺陷
对于每一种引起钢丝断裂的缺陷,提供以下信息:
——可能的原因
——缺陷的特征
——采取的措施。
4.0大拉:
断裂原因:
轧钢缺陷
断裂起因:
4a—表面嵌入钢瘤
缺陷特征:
嵌入盘元表面的钢瘤独立于其余的材料,它的尺寸相对较大,完全镶嵌在钢
中。
这种结构的造成往往是不规则的高度脱碳或过热。
钢瘤的硬度与其它材料的硬度相同。
进一步拉伸,缺陷就形成一种折叠状。
随着拉伸的继续进行,缺陷的变形量更大,拉伸得更长。
产生缺陷的大致原因:
在轧制盘条的过程中,“钢屑”或“冷滴”落到钢材的表面。
4b—WC碎片(从轧辊上来)
缺陷特征:
这种瘤有一个尖锐的边缘,在其基体内不变形。
这种碎片的硬度远远高于钢的硬度,而且,它的结构不能用一般的钢材腐蚀液(NITAL)浸蚀。
为了确证这种材料的结构,需要用Murakani试剂。
这是一种专门用于碳化钨WC烧结材料的腐蚀液。
经过进一步的拉伸,WC瘤不变形,但它会破碎,小碎片分布在一个基面上,通过一个小折叠连在一起。
产生缺陷的大致原因:
在轧钢过程中,从轧辊上脱落的烧结材料小片嵌入钢材的表面。
4c—扁平身
缺陷特征:
一个或多个对称隆起(耳朵)以一定的长度出现在盘条上,隆起部分常常很大。
如果这个缺陷经过第一道拉丝不断,那么就形成一种折叠状。
产生缺陷的大致原因:
轧到盘条最后一道的轧辊位置不规则。
4d—折叠
缺陷特征:
盘条表面看上去在一根母线上发生折叠。
折叠面引起高脱碳。
如果缺陷非常大且易以发现,那么经过第一道拉丝就断裂。
折叠可能会出现在整个盘条卷上,这种情况下只要把材料样品作一个扭转试验就能显现缺陷。
产生缺陷的大致原因:
表面折叠是由于轧判盘条时溢流造成的。
4e—不规则结构:
缺陷特征:
钢丝在断裂区域,没有通常所能见到的任何收缩现象。
断裂通常发生在第一步拉伸,或者在进入拉丝前的收线过程中。
金相分析显示出:
珠光体结构非常粗大(在第一步拉伸时断裂)或者有马氏体结构(在进入第一只模子前)
产生缺陷的大致原因:
轧判后的盘条冷却不均匀。
采取的措施:
对于缺陷4a,4b,4c,4d,4e;记录下来,并就盘条卷的缺陷问题向供货商投诉。
断裂原因:
由于表面擦伤而产生马氏体结构
4f—局部擦伤
缺陷特征:
长度方向上出现一些短的擦伤,有时呈现深暗蓝色。
金相试验显示,在断裂部位存在马氏体结构,有时会出现微小的横白裂纹。
产生缺陷的大致原因:
在钢厂包装盘条或在盘条的运输过程中出现强烈磨擦。
4g—在一条母线上的连续擦伤
缺陷特征:
沿盘来的长度方向,在一条母线上出现长而窄的擦伤。
在擦伤区域,有马氏体结构。
产生缺陷的大致原因:
在拉丝机收、放线路程上,钢丝与牵引部件、卷筒或磨损的回转部件产生磨擦。
采取措施:
缺陷4f:
记录下来,就有缺陷的盘条向供货商投诉。
缺陷4f:
检查拉丝机上从放线到收线钢丝路径上所有的零部件的磨损情况及正常工作情况。
断裂原因:
收缩
断裂方式:
拉断
4f局部擦伤
4g在一个基面上出现连续的擦伤
4h—拉断
缺陷特征:
在折裂面出现典型的截面收缩
引起缺陷的大致原因:
a—不规则的模具轮廓线。
b—盘条预处理不当。
c—钢丝表面润滑不足。
d—拉丝机不正常的拉拔条件。
采取的措施:
a—确认模具直径正确,其轮廓规则。
b—确认预处理正确
c—确认在皂盒中硬脂酸钠的有效性。
d—检查各个拉丝步骤中,张力自动调节装置的反拉调节情况。
断裂原因:
过拉引起的表面的缺陷:
断裂形式:
表面的微小裂纹(因润滑不充分)
4i—表面微小裂纹
缺陷特征:
a)表面微小而频繁的撕裂(肉眼看不到)集中在光滑的母线上。
金相试
验显示裂纹部份过硬(但不是马氏体)。
光滑的母线有时是大部份的
圆周,有时是狭窄的和不连续的区域。
这种缺陷通常产生在大拉工序,
但它会对后通工序带来不良影响。
b)仅在母线上严重发亮和裂纹很集中时才易于发现。
金相试验显示出基
体是一个马氏体结构。
产生缺陷的大致原因:
a)1—盘条表面的涂硼层完全或部分脱落。
2—缺少润滑剂
3—模具过份磨损(磨损环)
b)1一只模具断裂
2—拉丝过程中卷筒上或旋转部件上出现吊滞现象。
采取的措施:
a—确认盘条的预处理,润滑和模具更换时间附合说明书的规定。
b—更换破损的模具
c—确认钢丝路径上旋转部件的有效性。
断裂原因:
焊接
断裂形式:
焊接缺陷(因为两端接触不规则或回火错误)
4l—焊接缺陷
缺陷特征:
这种断裂在断裂区往往没有任何颈缩迹象和不规则的外形。
表面可见锉
磨的痕迹,并随着拉丝的步骤的增加而变得不太明显。
金相试验显示中此区脱碳(当断裂发生在焊接区时),这是一个典型的焊接问题。
产生缺陷的大致原因:
盘条焊接时,两端面对接不好,或者回火不好。
采取的措施:
严格遵守焊接操作规程。
4l焊接缺陷(因为两端接触不规则或回火错误)
4m焊接缺陷(在夹头处出现电火花)
4m—焊接缺陷
缺陷特征:
在断头的末端出现孤立的马氏体瘤,上面还有铜的痕迹。
产生缺陷的大致原因:
在焊接操作过程中夹头上起电火花。
采取的措施:
正确夹紧钢丝。
清洁焊机夹头和钢丝两端头。
断裂原因:
杯锥状缺陷
断裂形式:
形成轴向开裂
4n—形成轴向开裂
缺陷特征:
丝断头的一端形成一个锥形,另一端形成一个同样形状的杯形。
金相试验
常常会显示在长度方向截面上的中心经常有许多裂口。
产生缺陷的大致原因:
a)在中心和周围区域之间,由于偏折或珠光体颗粒尺寸不均匀而造成材料结构不规则。
这种情况在金相试验中很容易观察到。
b)因为模具的轮廓线不好(工作锥角太大)或模具过度磨损(磨损环)
而造成不规则拉伸。
在这种情况下,金相分析只能看到轴向的开裂,
而看不到结构上的不规则。
采取的措施:
情况a)通知和投诉供货商
情况b)确保模具的轮廓及换模符合说明书要求。
5.0中拉
断裂原因:
在中拉开始时出现的表面缺陷。
断裂形式:
表面开裂或折叠
5a—表面开裂或折叠
缺陷特征:
断头常常象一把刀尖。
沿着钢丝的一根母线频繁地出现表面缺陷。
金相分析显示,在引起断裂或折叠部分,常常出现脱碳现象。
而且它的硬度
低于其它的区域。
随着拉丝过程的进行,钢丝截面积进一步减少,缺陷部分
越来越呈折叠状,在里面可找到残余的氧化物。
产生缺陷的大致原因:
a)在前道工序开始时的焊接,看不出任何的锉磨痕迹(在这种情况下,表面
缺陷出现的频次不当,出现缺陷的区域很有限。
金相分析显示有扁豆状
脱碳的痕迹)。
b)因为前道工序中润滑不佳,造成过拉导致表面划伤(缺陷4i)。
在这种情况下,缺陷出现的频次很高,而且在钢丝很长的一段区域内均能找到这种缺陷。
采取的措施:
情况a)确保中拉开始时的焊接操作正确
情况b)与缺陷4i(粗拉)处理方法相同。
断裂原因:
缩丝逼细
断裂形式:
拉断
5b—拉断
缺陷特征:
在拉断部位出现典型的截面收缩现象。
产生缺陷的大致原因:
a)不规则的模具轮廓线
b)半成品钢丝预处理不好
c)钢丝上润滑不足
d)拉丝机拉丝条件不良
采取的措施
a)确认模子的直径符合工艺规格要求,其轮廓线正确
b)确保供给的钢丝预处理正确
c)确保皂盒内的硬脂酸钠有效
d)检查并调节各个拉丝步骤中调节器的反拉作用。
断裂原因:
过份拉伸引起的表面缺陷
断裂形式:
表面微小开裂(因为润滑失效)
5c—表面微小开裂
缺陷特征:
a)小而频繁的表面撕裂(裸眼看不到),集中在光滑的母线上,金相分析往往显示该部分过硬,但很少出现马氏体结构。
光滑的母线有时包容大部分周围,有时仅是狭窄和不连续的区域。
这种缺陷常常发生在中拉工序,但其不良影响却大多地表现在后通工序中。
b)一根母线严重发亮,而且裸眼可见密集的裂纹。
这种情况,金相分析显示马氏体结构。
产生缺陷的大致原因:
a)1—钢丝表面的涂层部分或全部脱落或末粘附在钢丝表面。
2—缺少润滑
3—模具的过度磨损(磨损环)
b)1一只模具断裂
2—拉丝过程中,钢丝通道上的辊或稳转部件的吊滞卡死现象。
采取措施:
a)—确认钢丝的预处理,润滑和模具的更换时间与说明书一致。
b)—更换破损的模具:
c)—确认钢丝路径上旋转部件的动作。
断裂原因:
焊接
断裂形式:
焊接缺陷(在中拉开始处焊接)
焊接缺陷(因为两端接触不好或回火不好)
焊接缺陷(在夹头处出现电火花)
5d—焊接缺陷:
缺陷特征:
断口象一把刀尖,钢丝表面的涂层覆盖得很好,没有任何发亮现象。
除非焊接是在大拉的最后一道完成的,否则表面看不到锉削痕迹。
金相分
析显示出典型的中心区脱碳(如果断裂发生在焊点处)除了脱碳区,在断
口的周围区域看不到其它形式的不同结构。
产生缺陷的大致原因:
在中拉工序开头处的焊接,钢丝两端接触不好,或者表面涂层不够。
5e—焊接缺陷
缺陷特征:
在断头部位看不到颈缩任何迹象或不规则的外形。
表面可见锉削的痕迹,
随着拉丝工序的进行,锉削痕迹变得不太明显。
金相分析显示出在焊点和
周围区域具有扁立状脱碳这种典型的焊接不规则结构(当断裂发生在焊接
点时)。
产生缺陷的原因:
在中拉工序的焊接,钢丝两端接触不好或不回火正确。
5f—焊接缺陷
缺陷特征:
在断裂端有孤立的马氏体瘤,其表面还有痕量铜。
产生缺陷的大致原因:
焊接过程中焊机夹头上出现电火花。
采取措施
缺陷5d和5e:
按焊接操作规程进行焊接。
缺陷5f:
焊接时,夹紧钢丝。
清洁焊机的夹头和钢丝被焊部分的表面。
断裂原因:
杯锥状缺陷
断裂形式:
形成轴向的开裂。
5g—形成轴向的开裂
断头的一端象一个锥形,另一个端具有一个同样形状的杯形。
在长度方向
的截面中心,金相分析常常发现很频繁的轴向开裂。
产生缺陷大致原因:
a)因为偏析或珠光体颗粒尺寸不均匀而造成在中心和周围区域的结构不均
匀。
这很容易在金相测试中观察到。
b)因为模具的轮廓线不规则(工作锥角太大)或者模具磨损过度磨损环)而造成不规则的拉伸。
在这种情况下,金相分析只能看到轴向的开裂,而看不到任何的结构不规则。
金相分析可发现的热处理不规则。
(拉伸后的结构有点象纤维并有成束趋向)
采取措施:
情况a):
记录下来并就盘条缺陷问题投诉供货商。
情况b):
确认模具的轮廓线和模具的更换时间符合工艺规范要求。
情况c):
确保半成品热处理工艺规范要求。
6.0湿拉
断裂原因:
在湿拉开始处的断裂
断裂形式:
表面开裂或折叠
6a—表面开裂或折叠
缺陷特征:
断头通常象一把刀尖,在钢丝上沿着一根母线频繁地出现表面缺陷。
在断裂
的裂缝内或引起断裂的折叠内,可用放大镜看到铜或黄铜的痕迹。
金相分析
显示断裂部分(刀尖处)的硬度低于周围的区域。
产生缺陷的大致原因:
在前道工序中因为拉丝或润滑不均匀造成过度拉伸。
(缺陷4i和5c)
采取措施:
按缺陷4i和4c的方法处理。
断裂原因:
缩丝逼细
断裂形式:
拉断
6b—拉断
缺陷特征:
在断头部位出现典型的截面收缩(颈缩)现象。
断点位于模具的工作锥,钢丝直径(d’)与模具的直径(d)相同。
产生缺陷大致的原因:
1)发生断丝的模具直径超公差。
2)发生断丝的模具工作锥大小或定径带太长。
3)模具过度磨损,形成一个磨损环。
4)由于模具堵塞而出现卡丝。
5)因为钢丝的减面率小于机器的系数K,所以钢丝不能在拉丝卷筒上滑动。
采取措施:
1),2),3),5):
更换不符合要求的模具,确认模具的更换周期。
4):
检查表面镀层的结合力。
6c—拉断(因为钢丝被拉伸)
缺陷特征:
在拉断部位截面出现典型的颈缩现象。
断裂发生在模子外面
钢丝的直径(d’)小于模具的直径(d)
产生缺陷大致原因:
1)黄铜镀层的含铜量、重量和结合力不合格。
2)黄铜镀层的热扩散程度不合要求。
3)镀层下氧化物过多。
4)润滑不充分。
采取措施
1),2),3):
使黄铜镀层合格
2)确认润滑槽液的效率。
断裂原因:
因为过度拉伸引起的表面缺陷。
断裂形式:
表面微小裂纹(因为润滑不足引起)
6d—表面微小裂纹
缺陷特征;
在断裂样品上有一根或多根严重发亮的母线(无黄铜),上面有细小而又频
繁的撕裂。
断裂有一个不规则的“隙缝”据此或多或少可以判别出与缺陷
母线是一致的。
这种形式的断裂仅仅发生在最后一道拉丝。
金相分析显示
发亮的母线过硬。
产生缺陷的大致原因:
a—热处理镀铜钢丝在生产线上由于通过破损的导套或导辊而出现部分
或全部磨去黄铜的基面。
b—黄铜镀层的结合力不好。
b—一个或多个模具的轮廓线不规则(出现锐边)或出现过度磨损(磨
损环),特别是开头的几道拉丝。
采取措施
检查热处理镀铜线上钢丝路径,特别注意导向和回转部件。
确认电解酸洗工艺正确槽液工作有效。
更换不规则或磨损的模子。
断裂原因:
焊接
断裂形式:
焊接缺陷(在热处理电镀工序)
6e—焊接缺陷(在热处理电镀工序中)
缺陷特征:
断头截面处变形,表面可见明显的锉削痕迹,表面黄铜镀层覆盖良好。
这种
断裂常常发生在开头的几道拉丝中。
产生缺陷的大致原因:
热处理镀铜工序中上线焊接缺陷。
6f—焊接缺陷(在湿拉放线工序中)
断裂部位完全没有黄铜,锉削痕迹没有或不很明显。
这种断裂往往发生在
中间或最后几道拉丝步骤。
产生缺陷的大致原因:
在湿拉上丝时的有缺陷的焊接。
采取措施:
缺陷6e—6f
确认焊接操作符合操作规程。
断裂原因:
杯锥状缺陷
断裂形式:
形成轴向开裂
缺陷特征:
断头的一端象一个锥形,这一端常常是留在模子里的一端(常常取出这一
段作为检验断头的样品)。
另一端形成一个杯状穴。
在锥形的中心,金相
分析显示以下特征:
6g-1)断裂处没有变硬的结构(纤维没有被拉伸)
6g-2)断裂处具有完全的变硬结构(钢丝被拉伸)
6g-3)类似于6g-1和6g-2的断裂,但结构不均匀。
产生缺陷的大致原因:
6g-1)由于大拉操作不良,造成在热处理镀铜前产生轴向开裂。
6g-2)因为湿拉模具的轮廓线不规则(工作锥太宽)或过度磨损(磨损环)
而造成轴向和开裂。
6g-3)因为中心部位碳的偏析或者热处理镀铜线上不规范操作而产生轴
向的开裂。
采取措施
6g-1)确保大中拉模子的轮廓及更换周期符合工艺规范要求。
6g-2)确保湿拉工序中模子轮廓及更换周期符合工艺规范要求。
6g-3)如果结构的不规则是由于偏析引起的,那么检验热处理工艺是否与
工艺规范一致。
6h—表面瘤(马氏体型)
缺陷特征:
在断裂区可发现在一根母线上有很明显的瘤。
缺陷在钢丝截面积上占有相
当大的尺寸,但在长度方向不大。
通常,有瘤部分的部分或全部发亮(缺
少黄铜),其它部分的钢丝正常。
金相分析显示出瘤的马氏体结构。
其基
体与钢丝的其余截面不一致。
如果瘤是由于热扩散时电火花引起的,那么
表面缺陷的钢丝与正常钢丝会交替出现。
瘤的硬度约是其余部分钢丝的
1.5-2倍。
马氏体结构可以用PICRAL腐蚀液来显现。
产生缺陷的大致原因:
热处理电镀线上在热扩散区钢丝与热扩散轮接触处出现电火花。
在钢丝上
产生微小的疤痕。
采取措施:
检验热扩散轮的清洁以及钢丝在扩散轮上的绷紧状况。
断裂原因:
表面夹杂(表面瘤)
断裂形式:
6h表面瘤(马氏体型)
6i表面瘤(WC型)
6i—表面瘤(烧结碳化钨WC型)
缺陷特征:
在断裂部位可见一个瘤(及其基体)位于断头的末端。
而且在断裂线上还
有其它的小碎片嵌入表面。
这些碎片间的距离比较远,但它们常常通过一
个小折叠连在一起。
缺陷常常发生在有限长的钢丝上。
金相分析显示,瘤
与钢丝其余部分完全分离,常常带有尖锐的角(瘤体嵌入表面)。
在瘤边的空穴内,可发现铜或氧化物。
(在这种情况下,瘤产生在湿拉的
开头几道)瘤的硬度是其余钢丝的3到5倍。
烧结碳化钨瘤的结构可用
Murakani试剂浸蚀。
产生缺陷的大致原因:
拉丝过程中烧结WC碎片从模具内脱落嵌入钢丝表面。
在钢厂内,轧辊上的WC碎片嵌入盘条表面。
采取措施:
确保各个拉丝工序中模具的更换周期与工艺规范规定一致。
确保调换的模具不破损。
就原材料缺陷问题投诉供货商。
7.0捻股/并线(带双捻)
前言:
发生在捻股和并线工序的断裂,其特征与湿拉工序中的断裂没有根本的区
别。
唯一明显的不同是在断裂区具有扭转应力的作用。
在断头的长度方向截面上作金相分析清楚地显示,在断头的边缘,有扭转应力作用区。
7a—表面开裂和折叠
缺陷特征:
断裂形状象一把“刀尖”;沿着一根母线,钢丝上频繁出现表面缺陷和严重
的发亮(无黄铜)。
显微镜检查显示,在引起断裂的开裂或折叠内常常有痕
量铜或黄铜。
金相试验分析断裂区(“刀尖”)显示这部分的硬度远远低
于周围区域的硬度。
产生缺陷的大致原因:
在大拉中拉工序,由于拉丝或润滑不好而造成过度拉伸,产生表面撕裂。
采取措施:
按缺陷4i和5c的处理方法。
断裂原因:
细拉引起的表面缺陷。
断裂形式:
表面开裂或折叠
7b—表面开裂或折叠
缺陷特征:
钢丝的断裂样品常常有一个或多个严重发白的母线(无黄铜)母线上有小而频繁的开裂。
断头常常形成一个不规则的“隙缝”状,并能或多或少地判断出与带缺陷母线是一致的。
金相分析显示母线发亮的钢丝表面过硬。
产生缺陷的大致原因:
a—因为在热处理电镀线上钢丝在其路径上的磨损面造成黄铜镀层全部
或部分从镀铜钢丝及母线(基面上)脱落。
b—黄铜镀层的结合力差。
b—一个或多个模具的轮廓线不规则(出现锐角)或过度磨损(磨损环)
特别是在开头的几道拉丝中。
采取措施:
检查镀铜线上钢丝路径是否正确特别是钢丝的导面部件,以及旋转部件。
确认电解酸冼和镀槽的正常工作。
更换磨损或不规则的模具。
断裂原因:
缩丝(逼细)
断裂形式:
拉断
7c—缺陷特征:
在断裂部位出现典型截面收缩区域。
产生缺陷的大致原因:
a)并线或拉线机上线工字轮刹车过急。
b)在并线或拉丝机的旋转部件上,钢口受到过度的磨损。
c)所拉钢丝的镀层不均匀。
c)并线或拉线机上钢丝的导向或旋转部件功能不正常。
采取措施:
a)调节并线/拉丝机上线工字轮的制动装置。
b)检查飞轮上导套的磨损程度。
c)检查镀黄铜和细拉阶段工作条件是否合格。
d)检查拉丝/并线机上导向和回转部件的动作情况。
断裂原因:
杯锥状
断裂形式:
形成轴向的开裂。
7d缺陷特征:
断头的一端有一个锥形,断头另一端有一个同样形状的杯状。
对锥形端的截
面作金相分析,显示以下特征:
7d-1)断裂的钢丝头(锥部)结构上没有硬化现象。
(纤维没有被拉伸)。
7d-2)断裂的钢丝头(锥部)结构上完全硬化。
(纤维被拉伸)。
7d-3)6g-1,6g-2的断裂形式,但结构不均匀。
断裂的大致原因:
7d-1)由干拉时的不规则操作,而使钢丝在热处理电镀线前产生轴开
裂。
7d-2)湿拉时因为模具的轮廓线不规则(工作锥角太大)或者模子磨损
过度(磨损环),而产生轴向的开裂。
7d-3)因为脱碳或者热处理镀铜阶段热处理不良引起钢丝中心偏析,从
而产生轴向的开裂。
采取措施:
7d-1)在粗拉,中拉工序确认模具的轮廓线和更换时间附合工艺规范要
求。
7d-2)确认湿拉工序中模具的轮廓和更换时间陈附合工艺规范要求。
7d-3)如果结构不良是由于钢的偏析引起的,那么记录下来并就此投诉
供货商。
如果结构不良是由于热处理引起的,那么确认热处理电
镀线上的所有操作符合工艺规范要求。
断裂原因:
表面瘤
断裂形式:
表面瘤(马氏体型)
7e—表面瘤(马氏体型)
缺陷特征:
断裂部位在钢丝的一根母线上有很明显的瘤。
有时,缺陷与钢丝截面相比
非常的大。
缺陷仅在有限的钢丝区段上出现。
有瘤的区域通常部分或全部
发白(缺少黄铜),而钢丝其余部分是完全正常的。
金相分析显示,瘤的结构为
马氏体,那么,有缺陷的钢丝和没有缺陷的钢丝会交替出现。
瘤的硬度是其
余区域硬度的1.5-2倍。
这种马氏体结构可以用PICKAL腐蚀液来浸蚀。
产生缺陷的大致原因:
在热扩散轮上出现电火花,使钢丝表面产生微小的烧痕。
采取措施:
确认热扩散轮的清洁,以及钢丝热扩散轮上必须保持一定的张紧力。
7f—表面瘤(烧结的型)
缺陷特征:
断头的末端有一个瘤(及其基体)。
通常在断裂部位还可见其它的一些小
碎片嵌入钢丝的表面。
这些碎片相距较远,但它们通过一个小折叠连在一
起。
缺陷通常在有限的钢丝段上发现。
金相分析常常显示,瘤与其余部分钢丝完全分离。
瘤常常带有锐边(瘤体
嵌入表面)。
瘤旁边的空穴内可以发现痕量铜和氧化物。
(在这种情况下,
瘤是在细拉以前形成的)。
瘤的硬度是其余区域硬度的3-5倍。
烧结WC
瘤的结构可用Murakani试剂来显现。
产生缺陷的大致原因:
在拉丝过和程中,模具中脱落的WC碎片嵌入钢丝的表面。
钢厂内轧辊上的WC碎片脱落后嵌入钢丝表面。
确认在各个拉丝阶段模具的更换时间是否与工艺规范一致。
确认调换模具无损坏。
记录并就材料缺陷问题投诉供货