制造工程基础第7章机械加工精度.docx
《制造工程基础第7章机械加工精度.docx》由会员分享,可在线阅读,更多相关《制造工程基础第7章机械加工精度.docx(21页珍藏版)》请在冰豆网上搜索。
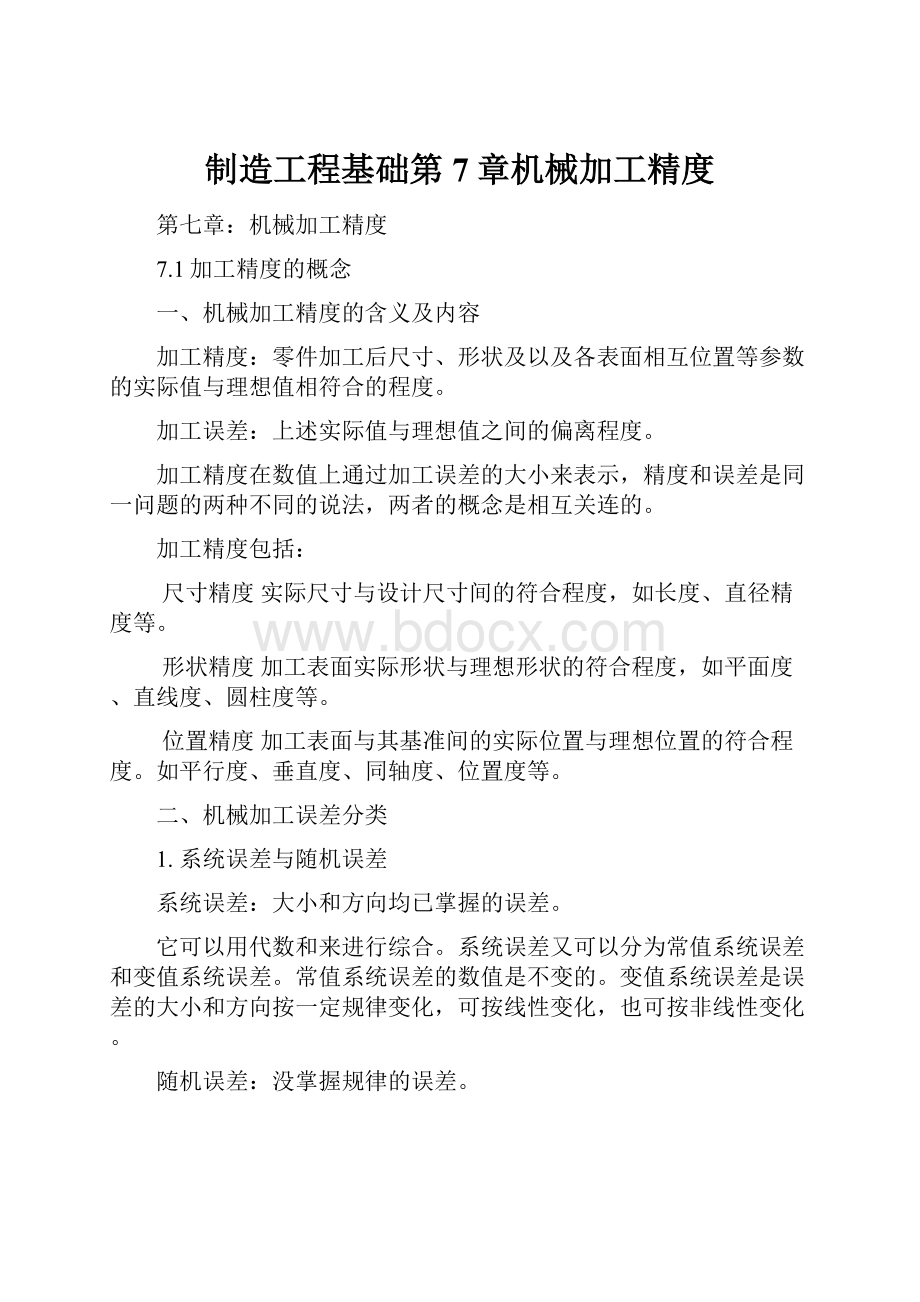
制造工程基础第7章机械加工精度
第七章:
机械加工精度
7.1加工精度的概念
一、机械加工精度的含义及内容
加工精度:
零件加工后尺寸、形状及以及各表面相互位置等参数的实际值与理想值相符合的程度。
加工误差:
上述实际值与理想值之间的偏离程度。
加工精度在数值上通过加工误差的大小来表示,精度和误差是同一问题的两种不同的说法,两者的概念是相互关连的。
加工精度包括:
尺寸精度实际尺寸与设计尺寸间的符合程度,如长度、直径精度等。
形状精度加工表面实际形状与理想形状的符合程度,如平面度、直线度、圆柱度等。
位置精度加工表面与其基准间的实际位置与理想位置的符合程度。
如平行度、垂直度、同轴度、位置度等。
二、机械加工误差分类
1.系统误差与随机误差
系统误差:
大小和方向均已掌握的误差。
它可以用代数和来进行综合。
系统误差又可以分为常值系统误差和变值系统误差。
常值系统误差的数值是不变的。
变值系统误差是误差的大小和方向按一定规律变化,可按线性变化,也可按非线性变化。
随机误差:
没掌握规律的误差。
有可能是掌握了误差的大小但不掌握其方向或掌握了误差的方向而不掌握大小。
它不能用代数和来进行综合,只能用数理统计方法来处理。
系统误差与随机误差之间的分界线不是固定不变的,随着科学技术的不断向前发展,人们对误差规律的逐渐掌握,随机误差不断向系统误差转移。
2.静态误差与切削状态误差
静态误差:
工艺系统在不切削状态下仍存在的误差。
例如机床的几何精度和传动精度等。
切削状态误差:
仅在切削状态下所出现的误差。
如机床在切削时的受力变形和受热变形等。
7.2工艺过程的精度保证
1.试切法
操作工人在每一步或走刀前进行对刀,然后切出一小段测量其尺寸是否合适,如不合适,调整刀具再试切出一小段,直到达到尺寸要求后才加工这一尺寸的全部表面(图6-1)。
2.调整法
先按规定尺寸调整好机床、夹具、刀具和工件的相对位置及进给行程,从而保证在加工时自动获得尺寸。
调整法可以分主静调整法和动调整法两类:
1)静调整法:
在不切削的情况下,用对刀块或样件来调整刀具的位置。
又称样件法(图6-2、6-3)
2)动调整法:
直接测量试切零件的尺寸,可以试切一件或一组零件,所有试切零件合格,即调整完毕,可以进行加工。
动调整法又称尺寸调整法,
3.尺寸刀具法
用定尺寸的刀具来加工,获得精度。
如钻头、镗刀块、拉刀及铰刀等。
有些孔加工刀具可以获得非常高的精度,生产率也非常高。
由于刀具有磨损,磨损后尺寸就不能保证,因此成本较高,多用于大批大量生产中。
用成形刀具加工也属于这一类
4.主动测量法
加工中,实时测量加工尺寸,达到要求时就立即停止加工,
图6-4表示了在外圆磨床上进行主动测量的情况。
7.3加工误差产生的原因及提高精度的措施
影响加工精度的主要因素有:
机床受力变形、工件受力变形、机床导轨磨损、刀具的尺寸磨损和刀具的受热变形等,另外还有度量误差和对刀误差(调整误差)。
一、加工误差产生的原因
(一)原理误差
由于采用了近似的加工运动或者近似的刀具轮廓而产生的误差。
如在用滚刀切削渐开线齿轮、渐开线花键轴时,是利用展成法原理,滚刀切出的齿形是由各个刀齿轨迹的包络线所形成的,是一条近似的折线,如图6-5。
(二)工艺系统精度和磨损的影响
工艺系统中机床、刀具、夹具本身的制造精度及磨损对工件的加工精度有不同程度的影响。
1.机床精度的影响
1)导轨误差
导轨是机床中确定主要部件相对位置的基准,也是运动的基准,它的各项误差直接影响被加工工件的精度。
导轨在垂直平面内的弯曲对加工精度的影响就不大一样,小到可以忽略不计的程度。
如图6-6a表示由于导轨在垂直面内位移量为z,引起工件上的半径误差R。
忽略高阶小项,得:
即工件上的直径误差为:
图6-6b表示在水平面内的弯曲使刀尖在水平面内位移y,引起工件上的误差R′。
因
R′=y,
所以在工件直径上的加工误差将为
D=2y。
假设y=z=0.1mm,D=40mm,则
可见R′比R大400倍。
这就是说,在垂直面导轨的弯曲对加工精度很小,可以忽略不计;而在水平面内同样大小的导轨弯曲就不能忽视。
2)主轴误差
在运转的情况下主轴轴心线和定位端面位置的稳定性。
主轴的回转精度不但和轴部件的制造精度(包括加工精度和装配精度)有关,而且还和受力后主轴的变形有关,并且随着主轴转速的增加,还需要解决主轴轴承的散热问题。
在主轴部件中,由于存在着主轴轴颈的圆度误差、同轴度误差、轴承本身的各种误差、轴承之间的同轴度误差、主轴的挠度和支承端面对轴颈轴心线的垂直度误差等原因,主轴在每一瞬时回转轴心线空间位置都是变动的。
主轴的误差的四种基本形式:
纯径向跳动、纯角度摆动、纯轴向窜动和轴心漂移(图6-7)。
实例:
镗孔径向跳动的影响:
镗轴旋转,工件不转(图6-8)。
设由于主轴纯径向跳动而使主轴轴心线在y坐标方向上作简谐直线运动,其频率与主轴每秒钟的转数相同,振幅为A;再设主轴中心偏移最大(等于A)时,镗刀尖正好通过水平位置1.则当镗刀再转过一个角时(位置1’),刀尖轨迹的水平分量和垂直分量各为:
上式是个椭圆方程式即镗出的孔成椭圆形。
主轴的纯轴向窜动对于孔加工和外圆加工并没影响,但在加工端面时,造成端面与内外圆不垂直,主轴每转一周,就要沿轴向跳动一次,向前窜动的半周中形成了右螺旋面,向后窜动的半周中形成了左螺旋面(如图6-10),最后切出了如同端面凸轮一般的形状,而在端面中心附近出现一个凸台。
在这种情况下车削螺纹,也必然会产生单个螺距内的周期误差。
2.刀具精度和磨损的影响
定尺寸刀具:
制造精度影响加工尺寸精度,如钻头、扩孔钻、铰刀、镗刀块和圆孔拉刀等,这些刀具磨损后加工尺寸就会产生变化,而且其中某些刀具难以修复或补偿。
其它刀具精度不会影响加工尺寸,如车刀、立铣刀、镗刀等,主要靠刀具位置的调整(即对刀)来保证。
砂轮的磨损比一般金属切削刀具大得多,砂轮的磨损与其硬度有关。
在外圆磨床上,由于砂轮直径一般都比较大,砂轮的磨损对工件尺寸精度、形状精度影响较小,而对于内圆磨床,由于砂轮直径较小,砂轮磨损对工件精度的影响就比较大,因此在精密外圆磨床、精密内圆磨床、齿轮磨床及花键磨床上多有砂轮补偿机构,砂轮修整后及时进行尺寸补偿。
修整砂轮的装置有时采用定时自动修整并及时补偿的联合机构。
为了减少刀具尺寸磨损对加工精度的影响,可以采取如下措施:
1)进行尺寸补偿。
在数控机床上可以比较方便地进行刀具尺寸补偿,它不仅可以补偿尺寸磨损,而且可以补偿刀具刃磨后的尺寸变化,如棒铣刀、圆盘铣刀等。
2)采用合理切削用量,不使刀具过快磨损。
3)选用耐磨性较高的刀具材料,如涂层刀具、陶瓷、立方氮化硼等。
3.夹具的制造精度和磨损
夹具的制造精度主要表面在定位元件、对刀装置和导向元件等本身的精度以及它们之间的相对位置精度。
定位元件确定工件与夹具的相对位置,
对刀装置和导向元件确定刀具与夹具的相对位置,
通过夹具就间接确定了工件和刀具之间的相对位置,从而保证了加工精度。
夹具中定位元件、对刀装置和导向元件的磨损会直接影响加工精度。
(三)工艺系统受力变形对加工精度的影响
1.刚度的概念
工艺系统中机床、刀具、夹具及工件等在受到切削力、传动力、惯性力、重力、夹紧力和内应力等作用时会产生弹性变形,当超过弹性变形极限后会产生塑性变形,工艺系统的变形一般都属于弹性变形。
刚度是物体受力后抵抗外力的能力,也就是物体在受力方向上产生单位弹性变形所需要的力
式中:
柔度是物体受单位力时在受力方向的变形,它是刚度的倒数。
物体在受力后产生变形,力和变形之间的关系不一定是线性的,上述刚度是指平均刚度,
瞬时刚度:
物体受力的增量与该方向上产生的变形增量的比值。
在工艺系统中,往往一个方向的力同时产生几个方向的变形,如图6-14所示。
因此工艺系统的变形具有复合性。
2.刚度曲线及影响刚度的因素
1)工艺系统的变形曲线
(1)加载变形曲线:
非线性
图6-15表示了一台机器或一个部件的加载变形曲线,可以明显地看出,载荷和变形不成线性关系,而成曲线关系,这主要是由于接触变形的影响,也可能有刚度很差的零件存在。
这类变形曲线又可以分为两类,一是凹形曲线(a),一是凸线(b)。
凹形曲线的特点是开始变形很大,逐渐刚度变好;而凸形曲线的特点是开始刚度好,随着载荷的加大,刚度愈来愈差。
(2)正反加卸载变形曲线:
不重合
图6-16表示了某一结构正反加卸载变形曲线。
先在正方向加载,得加载变形曲线,然后卸载,得到卸载曲线,可见两条线不重合,产生类似“磁滞”现象,这主要是由于接触面上的塑性变形,零件位移时的摩擦力消耗以及间隙的影响。
同理在反方向加载和卸载,又可得到加载变形曲线和卸载变形曲线,两者也不重合,同时整个加卸载过程最后不回原点,最终最大间隙为y。
2)影响工艺系统刚度的因素
(1)接触面的表面质量
接触面间的变形与零件的表面粗糙度、几何形状、接触面积大小及材料的物理机械性质有关。
如图6-18所示,接触变形中包括弹性变形和塑性变形两部分,卸载弹性变形可恢复,而塑性变形不可恢复,这是造成加载与卸曲线不重合的原因之一。
(2)系统存在薄弱环节—刚度较差的零件
机器或部件中,经常采用镶条、键等联结零件。
这些零件本身的刚度很差,极易变形,使整个系统刚度变差,变形曲线成凹形。
(3)连接件夹紧力的影响
机器和部件中的许多零件是用螺钉等连接起来的,当外加载荷方向与螺钉的夹紧力方向相反时,开始载荷小于螺钉所形成的夹紧力,这时变形较小,刚度较高;当载荷大于螺钉所形成的夹紧力时,螺钉将变形,因此变形较大,刚度较差,所以有连接件的一引动结构中,多出现凸形变形曲线。
(4)摩擦力的影响
在加载时,零件间外摩擦力阻碍零件的间隙位移,材料内摩擦力阻碍变形增加;在卸载时,外摩擦力阻碍零件的间隙恢复,内摩擦力阻止变形减小。
但摩擦力总是会造成能量的消耗,因此使得加载曲线与卸载曲线不重合。
(5)间隙的影响
在机器或部件上进行正向加载,由于间隙的存在,当载荷大于零件间的摩擦力时就会产生位移。
反向加载时也是一样。
因而造成正向加载曲线的起始点与反向卸曲线的终结点不重合。
3)工艺系统刚度及其组成
工艺系统的受力变形等于机床、刀具、工件及夹具的受力变形之和。
因此工艺系统的柔度就等于机床、刀具、工件及夹具的柔度之和。
用刚度来表示,就有
3.切削力对加工精度的影响
工艺系统受切削力的作用将产生变形,当切削力变化时造成变形量的变化,因此将会影响工件的尺寸精度、形状精度及位置精度。
误差复映现象:
在车床上安装一个阶梯轴试件,试件上有三组阶梯,,阶梯的差值相等,一次走刀将这三个地方的阶梯车去后,因系统有弹性变形,故阶梯的高度差仍然存在,但数值大为减小,这种现象称之为误差复映现象(图6-22)。
4.传动力对加工精度的影响
在车床、磨床上加工轴类零件时,住往用顶尖孔定位,通过装在主轴上的拨盘、传动销拨动装在工件工端的夹头使工件回转。
在拨盘转动的过程中,传动力F与切削力Fy有时同向,有时反向。
当传动力F与切削侵略Fy方向相同时,切深将减小,但两者方向相反时,切深将增加。
由于切削力不等,变形各异,因而引起加工误差。
5.惯性力对加工精度的影响
调整回转零件的不平衡会产生离心力,离心力在零件回转过程中不断改变方向,有时与切削分力Fy同向,有时反向。
同向时,减小了实际切深,反向时,增加了实际切深,由于工艺系统的受力变形,因此产生加工误差。
6.夹紧力对加工精度的影响
对于刚度比较差的零件,在加工时由于夹紧力安排不当使零件产生弹性变形。
加工完后,卸下工件,这时弹性恢复,结果造成开关误差。
7.重力对加工精度的影响
在加工中,由于机床部件或工件产生移动,其重力作用点变化而产生的弹性变形,如大型立车、龙门铣床、龙门刨床等。
其主轴箱或刀架在横梁上面移动时,由于主轴箱的重力使横梁的变形在不同位置是不同的,因而造成加工误差,这时工件表面将成凹形。
8.内应力对加工精度的影响
1)毛坯制造中产生的内应力
在铸、锻、焊、热处理等加工过程中,内于各部分冷热收缩不均匀以及金相组织转变引起的体积变化,使毛坯内部产生了相当大的内应力。
毛坯的结构愈复杂,各部分的厚度愈不均匀,散热的条件相差愈大,则在毛坯内部产生的内应力也愈大。
具有内应力的毛坯由于内应力暂时处于相对平衡的状态,在短时期内还看不出有什么变动。
但在切削去除某些表面部分以后,就打破了这种平衡,内应力重新分布,零件就明显地出现了变形。
图6-32
2)冷校直带来的内应力
冷校直带来的内应力,可以用图6-33说明。
(四)工艺系统受热变形对加工精度的影响
在金属切削加工过程中,工艺系统的温度会产生复杂的变化,这是由该系统受到的切削热、摩擦热以及日光和供暖设备的辐射热而引起的。
1.工艺系统的热源
1)切削热
切削过程中,切削变形及摩擦所消耗的能量,绝大部分转化为切削热,这些热量将传到工件、刀具、切屑和周围介质中去。
切削热是工件和刀具热变形的主要热源。
2)传动系统的摩擦热和能量损耗
轴承、齿轮副、摩擦离合器、溜板和导轨、丝杠和螺母等运动副的摩擦热以及动力源能量损耗,如电动机、液压系统的发热等是机床热变形的主要热源。
3)派生热源
部分切削热由切削液、切屑带走,它们落到床上,再把热量传到床身,就形成派生热源。
此外,摩擦热还通过润滑油的循环散布到各处,也是重要的派生热源。
4)外部热源
外部热源主要指周围环境温度通过空气的对流以及环境热源,如日光、照明灯具、加热器等通过辐射传到工艺系统的热量。
2.工件的热变形
1)工件比较均匀地受热
一些形状较简单的轴类、套类、盘类零件的内、外圆加工时,切削热比较均匀地传入工件,宽砂轮磨短轴时亦可认为是接近这种情况。
如不考虑工件温升后的散热,其温度沿工件全长和圆周的分布都是比较均匀的,热变形也较均匀,它只引起工件尺寸的变化,而几何形状则不受影响。
2)工件不均匀受热
在加工时工件的温升与传入其间的热量、工件的质量、工件材料的热容量等有关,而传入工件的切削热主要决定于切削用量,由于加工条件的复杂性和多样性,大多数情况是工件不均匀受热。
铣、刨、磨平面时,工件只在单面受切削热作用,上下表面的温差导致工件拱起,中间被多切去,加工完毕冷却后,加工表面就产生中凹的误差,如图6-38。
3.刀具的变形
传给刀具的热主要是切削热,刀具质量小,热容量小,故会有很高的温升,例如高速钢的工作表面可达700℃~800℃。
刀具受热伸长主要影响工件的尺寸精度,在加工大型零件时,如车削长轴的外圆,也会影响零件的几何形状精度。
如图6-39车刀受热变形与切削时间的关系。
4.机床的热变形
各类机床(包括夹具)的结构和工件条件相关很大,故引起机床热变形的热源和变形特性也是多种多样的。
除切削热有一小部分会传入机床外,传动系统、导轨等运动零件产生的摩擦热为机床的主要热源。
另外液压系统、冷却润滑液等也是机床的热源。
研究机床热变形对加工精度的影响时,主要考虑主轴位置的变化以及导轨的变形,因为它们都影响刀具相对于工件加工表面的位置。
(图6-39a,b,c)
二、提高精度的措施
(一)提高工艺系统刚度的措施
工艺系统刚度的提高可以从各部分元件本身的刚度和接触刚度这两方面着手。
1)机床构件自身刚度的提高
在机床设计时要注意支承件、传动件及主轴系统本身刚度的提高。
2)提高工件安装时的刚度
工件在安装时应考虑刚度问题。
应避免因工件伸太高而刚度较差现象。
中心架、跟刀架(下载)
3)提高加工时刀具的刚度
加工时刀具的悬伸应尽量短,刀杆应尽可能粗些,以提高自身的刚度。
要特别注意多刀加工时,整个刀具系统的刚度。
4)提高工装零件表面质量
接触刚度与零件的表面质量有密切关系,因此要注意接触表面的粗糙度、形状精度及物理机械性质等。
5)减少接触面
6)加预紧力
加预紧力使接触面产生预变形,减小间隙,提高刚度。
对于相互静止的结构,可加150MPa的预紧力;对于相互运动的结构(如滚动导轨、轴承等),可加10~20MPa的预紧力。
(二)减小热变形对加工精度影响的措施
1)减少热源的能量
分离热源:
凡是有可能从主机分离出去的热源,如电机、变速箱、液压装置的油箱等,尽可能放置在机床外部。
隔热:
如热源不能从机床中分离出去,可在发热部件与机床大件间用绝热材料隔开。
冷却:
对发热量大的热源,如既不能从机内移出,又不便隔热,则可采用有效冷却。
2)用热补偿方法减小热变形
单纯地减小温升往往不能收到满意的效果,此时可采用热补偿方法使机床的温度场比较均匀,从而使机床仅产生不影响加工精度的均匀变形。
例如平面磨床,磨削热使磨床床身的温度升高,则床身形成上热下冷而使导轨产生中凸的热变形;若将液压系统的油池设计在床身低部,油使床身下部温度升高而产生热变形,使导轨产生中凹的热变形,以补偿由于磨削热产生的导轨中凸热变形。
3)改善机床结构来减小热变形
从机床结构上要考虑有利于热的传导,如传统的牛头刨床滑枕截面结构(图6-41)由于导轨面的高速滑动,使滑轨上冷下热,就会产生较大的弯曲变形,将导轨布置在截面中间使上、下对称,就可以大大减小滑枕的弯曲而提高机床的精度。
4)保持工艺系统的热平衡
由热变形规律可知,大的热变形发生在机床开动后的一段时间内,当达到热平衡后,热变形趋于稳定,此后加工精度才有保证。
因此在精加工前可先使机床空转一段时间(机床预热),等达到热平衡时再开始加工,加工精度比较稳定。
5)控制环境温度
对精加工机床应避免日光直接照射,布置采暖设备也应避免使机床受热不均匀,对精密机床则应安装在恒温车间。