气缸的工作原理.docx
《气缸的工作原理.docx》由会员分享,可在线阅读,更多相关《气缸的工作原理.docx(9页珍藏版)》请在冰豆网上搜索。
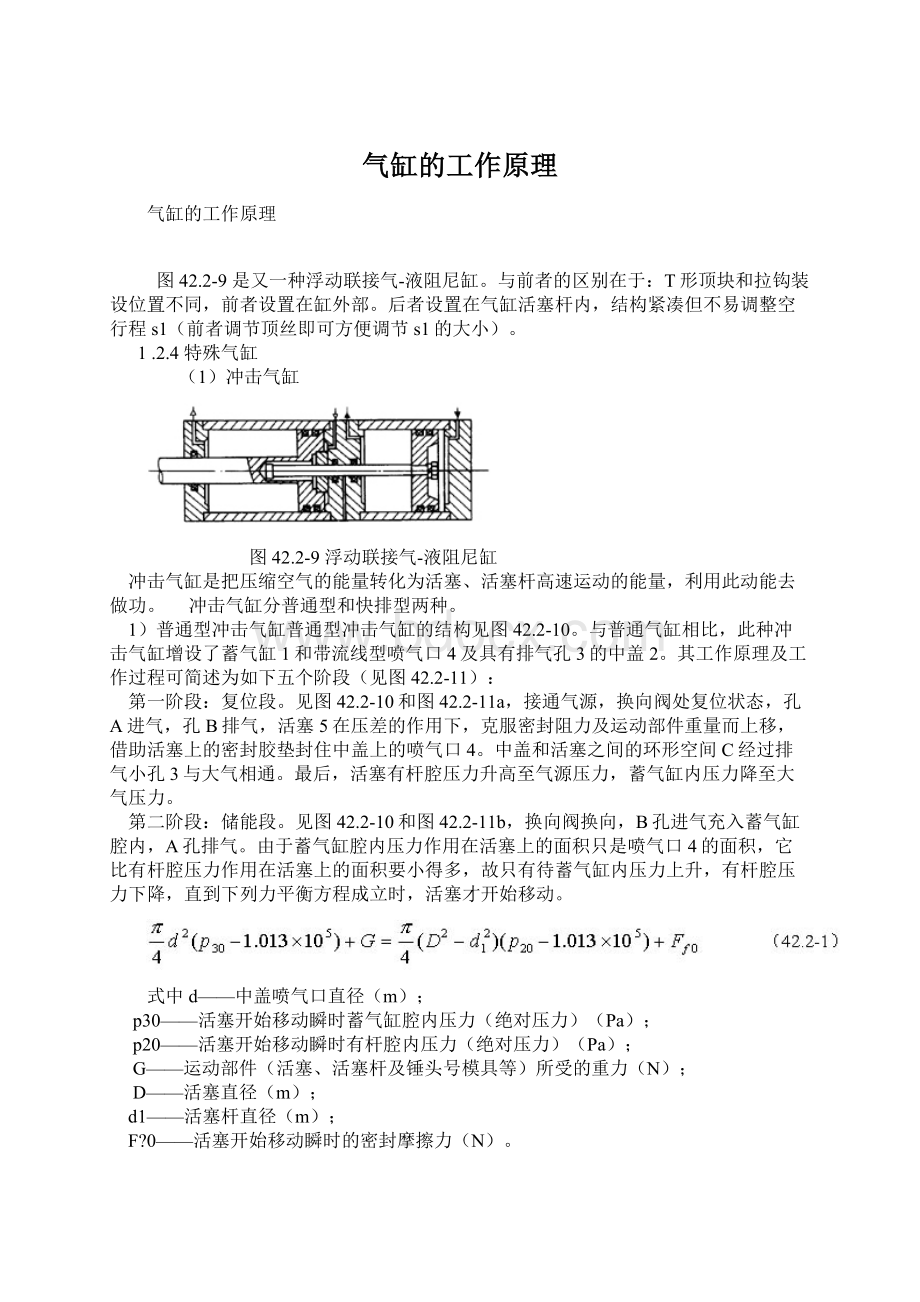
气缸的工作原理
气缸的工作原理
图42.2-9是又一种浮动联接气-液阻尼缸。
与前者的区别在于:
T形顶块和拉钩装设位置不同,前者设置在缸外部。
后者设置在气缸活塞杆内,结构紧凑但不易调整空行程s1(前者调节顶丝即可方便调节s1的大小)。
1.2.4特殊气缸
(1)冲击气缸
图42.2-9浮动联接气-液阻尼缸
冲击气缸是把压缩空气的能量转化为活塞、活塞杆高速运动的能量,利用此动能去做功。
冲击气缸分普通型和快排型两种。
1)普通型冲击气缸普通型冲击气缸的结构见图42.2-10。
与普通气缸相比,此种冲击气缸增设了蓄气缸1和带流线型喷气口4及具有排气孔3的中盖2。
其工作原理及工作过程可简述为如下五个阶段(见图42.2-11):
第一阶段:
复位段。
见图42.2-10和图42.2-11a,接通气源,换向阀处复位状态,孔A进气,孔B排气,活塞5在压差的作用下,克服密封阻力及运动部件重量而上移,借助活塞上的密封胶垫封住中盖上的喷气口4。
中盖和活塞之间的环形空间C经过排气小孔3与大气相通。
最后,活塞有杆腔压力升高至气源压力,蓄气缸内压力降至大气压力。
第二阶段:
储能段。
见图42.2-10和图42.2-11b,换向阀换向,B孔进气充入蓄气缸腔内,A孔排气。
由于蓄气缸腔内压力作用在活塞上的面积只是喷气口4的面积,它比有杆腔压力作用在活塞上的面积要小得多,故只有待蓄气缸内压力上升,有杆腔压力下降,直到下列力平衡方程成立时,活塞才开始移动。
式中d——中盖喷气口直径(m);
p30——活塞开始移动瞬时蓄气缸腔内压力(绝对压力)(Pa);
p20——活塞开始移动瞬时有杆腔内压力(绝对压力)(Pa);
G——运动部件(活塞、活塞杆及锤头号模具等)所受的重力(N);
D——活塞直径(m);
d1——活塞杆直径(m);
F?
0——活塞开始移动瞬时的密封摩擦力(N)。
若不计式(42.2-1)中G和F?
0项,且令d=d1,
,则当
时,活塞才开始移动。
这里的p20、p30均为绝对压力。
可见活塞开始移动瞬时,蓄气缸腔与有杆腔的压力差很大。
这一点很明显地与普通气缸不同。
图42.2-10普通型冲击气缸
第三阶段:
冲击段。
活塞开始移动瞬时,蓄气缸腔内压力p30可认为已达气源压力ps,同时,容积很小的无杆腔(包括环形空间C)通过排气孔3与大气相通,故无杆腔压力p10等于大气压力pa。
由于pa/ps大于临界压力比0.528,所以活塞开始移动后,在最小流通截面处(喷气口与活塞之间的环形面)为声速流动,使无杆腔压力急剧增加,直至与蓄气缸腔内压力平衡。
该平衡压力略低于气源压力。
以上可以称为冲击段的第I区段。
第I区段的作用时间极短(只有几毫秒)。
在第I区段,有杆腔压力变化很小,故第I区段末,无杆腔压力p1(作用在活塞全面积上)比有杆腔压力p2(作用在活塞杆侧的环状面积上)大得多,活塞在这样大的压差力作用下,获得很高的运动加速度,使活塞高速运动,即进行冲击。
在此过程B口仍在进气,蓄气缸腔至无杆腔已连通且压力相等,可认为蓄气-无杆腔内为略带充气的绝热膨胀过程。
同时有杆腔排气孔A通流面积有限,活塞高速冲击势必造成有杆腔内气体迅速压缩(排气不畅),有杆腔压力会迅速升高(可能高于气源压力)这必将引起活塞减速,直至下降到速度为0。
以上可称为冲击段的第Ⅱ区段。
可认为第Ⅱ区段的有杆腔内为边排气的绝热压缩过程。
整个冲击段时间很短,约几十毫秒
。
见图42.2-11c。
图42.2-11普通型冲击气缸的工作原理
1— 蓄气缸;2—中盖;3—排气孔;4—喷气口;5—活塞
第四阶段:
弹跳段。
在冲击段之后,从能量观点来说,蓄气缸腔内压力能转化成活塞动能,而活塞的部分动能又转化成有杆腔的压力能,结果造成有杆腔压力比蓄气-无杆腔压力还高,即形成“气垫”,使活塞产生反向运动,结果又会使蓄气-无杆腔压力增加,且又大于有杆腔压力。
如此便出现活塞在缸体内来回往复运动—即弹跳。
直至活塞两侧压力差克服不了活塞阻力不能再发生弹跳为止。
待有杆腔气体由A排空后,活塞便下行至终点。
第五阶段:
耗能段。
活塞下行至终点后,如换向阀不及时复位,则蓄气-无杆腔内会继续充气直至达到气源压力。
再复位时,充入的这部分气体又需全部排掉。
可见这种充气不能作用有功,故称之为耗能段。
实际使用时应避免此段(令换向阀及时换向返回复位段)。
对内径D=90mm的气缸,在气源压力0.65MPa下进行实验,所得冲击气缸特性曲线见图42.2-12。
上述分析基本与特性曲线相符。
对冲击段的分析可以看出,很大的运动加速使活塞产生很大的运动速度,但由于必须克服有杆腔不断增加的背压力及摩擦力,则活塞速度又要减慢,因此,在某个冲程处,运动速度必达最大值,此时的冲击能也达最大值。
各种冲击作业应在这个冲程附近进行(参见图42.2-11c)。
冲击气缸在实际工作时,锤头模具撞击工件作完功,一般就借助行程开关发出信号使换向阀复位换向,缸即从冲击段直接转为复位段。
这种状态可认为不存在弹跳段和耗能段。
2)快排型冲击气缸由上述普通型冲击气缸原理可见,其一部分能量(有时是较大部分能量)被消耗于克服背压(即p2)做功,因而冲击能没有充分利用。
假如冲击一开始,就让有杆腔气体全排空,即使有杆腔压力降至大气压力,则冲击过程中,可节省大量的能量,而使冲击气缸发挥更大的作用,输出更大的冲击能。
这种在冲击过程中,有杆腔压力接近于大气压力的冲击气缸,称为快排型冲击气缸。
其结构见图42.2-13a。
快排型冲击气缸是在普通型冲击气缸的下部增加了“快排机构”构成。
快排机构是由快排导向盖1、快排缸体4、快排活塞3、密封胶垫2等零件组成。
快排型冲击气缸的气控回路见图42.2-13b。
接通气源,通过阀F1同时向K1、K3充气,K2通大气。
阀F1输出口A用直管与K1孔连通,而用弯管与K3孔连通,弯管气阻大于直管气阻。
这样,压缩空气先经K1使快排活塞3推到上边,由快排活塞3与密封胶垫2一起切断有杆腔与排气口T的通道。
然后经K3孔向有杆腔进气,蓄气一无杆腔气体经K4孔通过阀F2排气,则活塞上移。
当活塞封住中盖喷气口时,装在锤头上的压块触动推杆6,切换阀F3,发出信号控制阀F2使之切换,这样气源便经阀F2和K4孔向蓄气腔内充气,一直充至气源压力。
图42.2-12 冲击气缸特性曲线
图42.2-13快排型冲击气缸结构及控制回路
a)结构图;b)控制回路
1—快排导向盖;2—密封胶垫;3—快排活塞;4—快排缸体;5—中盖
T—方孔;C—环形空间;6—推杆;7—气阻;8—气容
冲击工作开始时,使阀F1切换,则K2进气,K1和K3排气,快排活塞下移,有杆腔的压缩空气便通过快排导向盖1上的多个圆孔(8个),再经过快排缸体4上的多个方孔T(10余个)及K3直接排至大气中。
因为上述多个圆孔和方孔的通流面积远远大于K3的通流面积,所以有杆腔的压力可以在极短的时间内降低到接近于大气压力。
当降到一定压力时,活塞便开始下移。
锤头上压块便离开行程阀F3的推杆6,阀3在弹簧的作用下复位。
由于接有气阻7和气容8,阀3虽然复位,但F2却延时复位,这就保证了蓄气缸腔内的压缩空气用来完成使活塞迅速向下冲击的工作。
否则,若F3复位,F2同时复位的话,蓄气缸腔内压缩空气就会在锤头没有运动到行程终点之前已经通过K4孔和阀F2排气了,所以当锤头开始冲击后,F2的复位动作需延时几十毫秒。
因所需延时时间不长,冲击缸冲击时间又很短,往往不用气阻、气容也可以,只要阀F2的换向时间比冲击时间长就可以了。
在活塞向下冲击的过程中,由于有杆腔气体能充分地被排空,故不存在普通型冲击气缸有杆腔出现的较大背压,因而快排型冲击气缸的冲击能是同尺寸的普通型冲击气缸冲击能的3~4倍。
(2)数字气缸
如图42.2-14所示,它由活塞1、缸体2、活塞杆3等件组成。
活塞的右端有T字头,活塞的左端有凹形孔,后面活塞的T字头装入前面活塞的凹形孔内,由于缸体的限制,T字头只能在凹形孔内沿缸轴向运动,而两者不能脱开,若干活塞如此顺序串联置于缸体内,T字头在凹形孔中左右可移动的范围就是此活塞的行程量。
不同的进气孔A1~Ai(可能是A1,或是A1和A2,或A1、A2和A3,还可能是A1和A3,或A2和A3等等)输入压缩空气(0.4~0.8MPa)时,相应的活塞就会向右移动,每个活塞的向右移动都可推动活塞杆3向右移动,因此,活塞杆3每次向右移动的总距离等于各个活塞行程量的总和。
这里B孔始终与低压气源相通(0.05~0.1MPa),当A1~Ai孔排气时,在低压气的作用下,活塞会自动退回原位。
各活塞的行程大小,可根据需要的总行程s按几何级数由小到大排列选取。
设s=35mm,采用3个活塞,则各活塞的行程分别取α1=5mm;α2=10mm;α3=20mm。
如s=31.5mm,可用6个活塞,则α1、α2、α3……α6分别设计为0.5、1、2、4、8、16mm,由这些数值组合起来,就可在0.5~31.5mm范围内得到0.5mm整数倍的任意输出位移量。
而这里的α1、α2、α3……αi可以根据需要设计成各种不同数列,就可以得到各种所需数值的行程量。
(3)回转气缸
如图42.2-15a所示,主要由导气头、缸体、活塞、活塞杆组成。
这种气缸的缸体3连同缸盖6及导气头芯10被其他动力(如车床主轴)携带回转,活塞4及活塞杆1只能作往复直线运动,导气头体9外接管路,固定不动。
固转气缸的结构如图42.2-15b所示。
为增大其输出力采用两个活塞串联在一根活塞杆上,这样其输出力比单活塞也增大约一倍,且可减小气缸尺寸,导气头体与导气头芯因需相对转动,装有滚动轴承,并以研配间隙密封,应设油杯润滑以减少摩擦,避免烧损或卡死。
回转气缸主要用于机床夹具和线材卷曲等装置上。
(4)挠性气缸
挠性气缸是以挠性软管作为缸筒的气缸。
常用挠性气缸有两种。
一种是普通挠性气缸见图42.2-16,由活塞、活塞杆及挠性软管缸筒组成。
一般都是单作用活塞气缸,活塞的回程靠其他外力。
其特点是安装空间小,行程可较长。
图42.2-14 数字气缸
1—活塞;2—缸体;3—活塞杆
图42.2-15回转气缸
a)原理图;b)结构图
1—活塞杆;2、5—密封圈;3—缸体;4—活塞;6—缸盖;7、8—轴承
9—导气头体;10—导气头芯;11—中盖;12—螺栓
图42.2-16 普通挠性气缸
第二种挠性气缸是滚子挠性气缸见图42.2-17。
由夹持滚子代替活塞及活塞杆,夹持滚子设在挠性缸筒外表面,A端进气时,左端挠性筒膨胀,B端排气,缸左端收缩,夹持在缸筒外部的滚子在膨胀端的作用下,向右移动,滚子夹带动载荷运动。
可