空调换热器翅片冲压模设计设计说明书.docx
《空调换热器翅片冲压模设计设计说明书.docx》由会员分享,可在线阅读,更多相关《空调换热器翅片冲压模设计设计说明书.docx(12页珍藏版)》请在冰豆网上搜索。
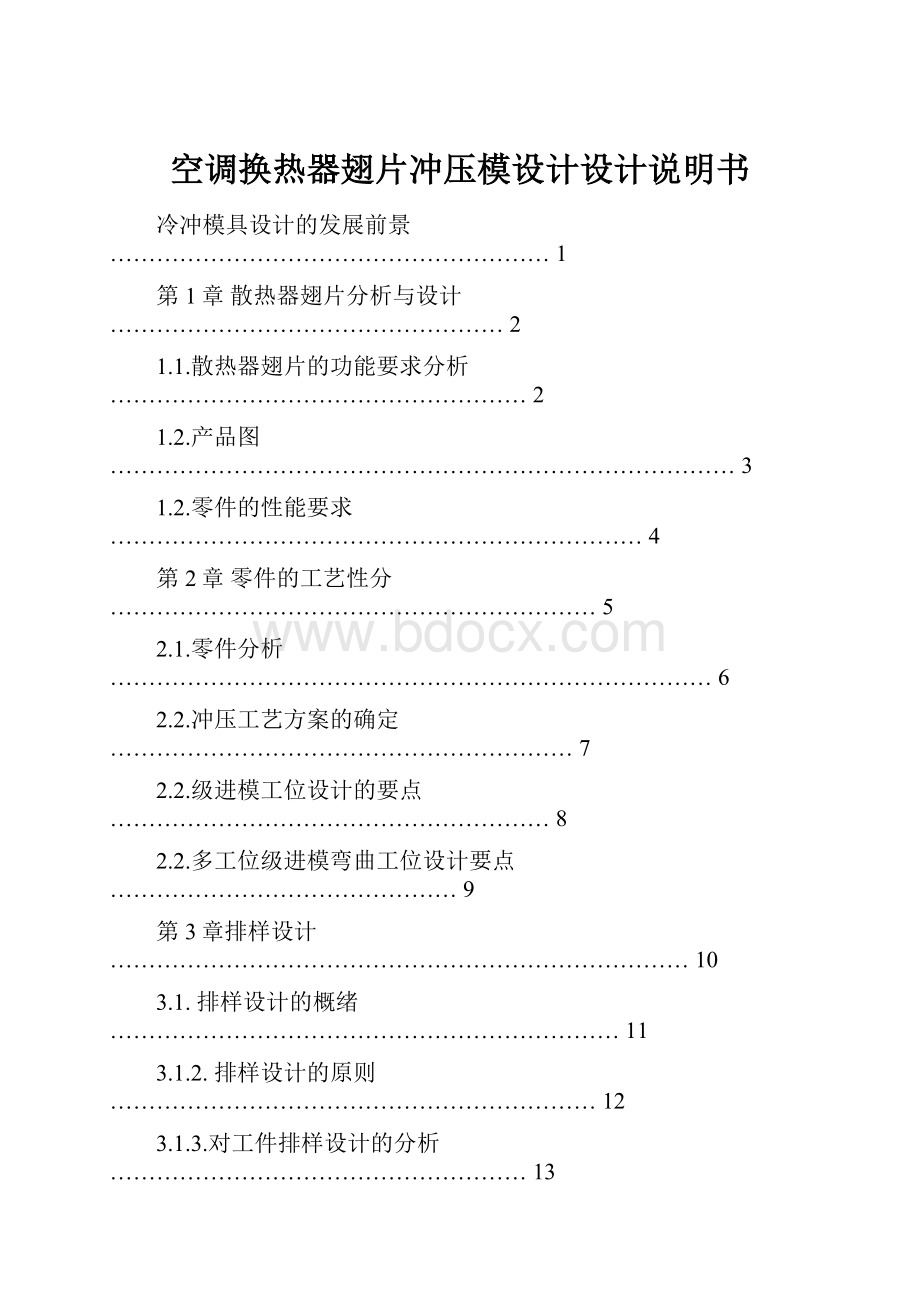
空调换热器翅片冲压模设计设计说明书
冷冲模具设计的发展前景…………………………………………………1
第1章散热器翅片分析与设计……………………………………………2
1.1.散热器翅片的功能要求分析………………………………………………2
1.2.产品图………………………………………………………………………3
1.2.零件的性能要求……………………………………………………………4
第2章零件的工艺性分………………………………………………………5
2.1.零件分析……………………………………………………………………6
2.2.冲压工艺方案的确定……………………………………………………7
2.2.级进模工位设计的要点…………………………………………………8
2.2.多工位级进模弯曲工位设计要点………………………………………9
第3章排样设计…………………………………………………………………10
3.1.排样设计的概绪…………………………………………………………11
3.1.2.排样设计的原则………………………………………………………12
3.1.3.对工件排样设计的分析………………………………………………13
3.2.排样设计…………………………………………………………………14
第4章模具设计…………………………………………………………………15
4.1.模具的基本机构设计………………………………………………………16
4.2.凸模机构的安装……………………………………………………………17
4.3.凹模结构及安装……………………………………………………………18
4.4.冲压设备的选择……………………………………………………………19
4.4.冲压设备的选用……………………………………………………………20
4.4.模具强度的校核……………………………………………………………21
4.6.成形零件设计……………………………………………………………22
参考文献…………………………………………………………………………23
设计总结…………………………………………………………………………24
致谢…………………………………………………………………………………25
冷冲模具设计的发展前景
随着科学技术的不断进步和工业生产的迅速发展,许多新技术、新工艺、新设备、新材料不断涌现,因而促进了冲压技术的不断革新和发展。
其主要表现和发展方向如下:
(1)冲压成形理论及冲压工艺方面
冲压成形理论的研究是提高冲压技术的基础。
目前,国内外对冲压成形理论的研究非常重视,在材料冲压性能研究、冲压成形过程应力应变分析、板料变形规律研究及坯料与模具之间的相互作用研究等方面均取得了较大的进展。
特别是随着计算机技术的飞跃发展和塑性变形理论的进一步完善,近年来国内外已开始应用塑性成形过程的计算机模拟技术,即利用有限元(FEM)等有值分析方法模拟金属的塑性成形过程,根据分析结果,设计人员可预测某一工艺方案成形的可行性及可能出现的质量问题,并通过在计算机上选择修改相关参数,可实现工艺及模具的优化设计。
这样既节省了昂贵的试模费用,也缩短了制模具周期。
(2)冲模是实现冲压生产的基本条件.
在冲模的设计制造上,目前正朝着以下两方面发展:
一方面,为了适应高速、自动、精密、安全等大批量现代生产的需要,冲模正向高效率、高精度、高寿命及多工位、多功能方向发展,与此相比适应的新型模具材料及其热处理技术,各种高效、精密、数控自动化的模具加工机床和检测设备以及模具CAD/CAM技术也在迅速发展;另一方面,为了适应产品更新换代和试制或小批量生产的需要,锌基合金冲模、聚氨酯橡胶冲模、薄板冲模、钢带冲模、组合冲模等各种简易冲模及其制造技术也得到了迅速发展。
精密、高效的多工位及多功能级进模和大型复杂的汽车覆盖件冲模代表了现代冲模的技术水平。
目前,50个工位以上的级进模进距精度可达到2微米,多功能级进模不仅可以完成冲压全过程,还可完成焊接、装配等工序。
我国已能自行设计制造出达到国际水平的精度达2~5微米,进距精度2~3微米,总寿命达1亿次。
我国主要汽车模具企业,已能生产成套轿车覆盖件模具,在设计制造方法、手段方面已基本达到了国际水平,但在制造方法手段方面已基本达到了国际水平,模具结构、功能方面也接近国际水平,但在制造质量、精度、制造周期和成本方面与国外相比还存在一定差距。
模具制造技术现代化是模具工业发展的基础。
计算机技术、信息技术、自动化技术等先进技术正在不断向传统制造技术渗透、交叉、融合形成了现代模具制造技术。
其中高速铣削加工、电火花铣削加工、慢走丝切割加工、精密磨削及抛光技术、数控测量等代表了现代冲模制造的技术水平。
高速铣削加工不但具有加工速度高以及良好的加工精度和表面质量(主轴转速一般为15000到40000r/min),加工精度一般可达10微米,最好的表面粗糙度Ra≤1微米),而且与传统切削加工相比具有温升低、切削力小,因而可加工热敏材料和刚性差的零件,合理选择刀具和切削用量还可实现硬材料(60HRC)加工;电火花铣削加工(又称电火花创成加工)是以高速旋转的简单管状电极作三维或二维轮廓加工(像数控铣一样),因此不再需要制造昂贵的成形电极,模具加工过程中的检测技术也取得了很大的发展,现在三坐标测量机除了能高精度地测量复杂曲面的数据外,其良好的温度补偿装置、可靠的抗振保护能力、严密的除尘措施及简单操作步骤,使得现场自动化检测成为可能。
此外,激光快速成形技术(RPM)与树脂浇注技术在快速经济制模技术中得到了成功的应用。
利用RPM技术快速成形三维原型后,通过陶瓷精铸、电弧涂喷、消失模、熔模等技术可快速制造各种成形模。
(3)冲压设备和冲压生产自动化方面
性能良好的冲压设备是提高冲压生产技术水平的基本条件,高精度、高寿命、高效率的冲模需要高精度、高自动化的冲压设备相匹配。
为了满足大批量高速生产的需要,目前冲压设备也由单工位、单功能、低速压力机朝着多工位、多功能、高速和数控方向发展,加之机械乃至机器人的大量使用,使冲压生产效率得到大幅度提高,各式各样的冲压自动线和高速自动压力机纷纷投入使用。
如在数控四边折弯机中送入板料毛坯后,在计算机程序控制下便可依次完成四边弯曲,从而大幅度提高精度和生产率;在高速自动压力机上冲压电机定转子冲片时,一分钟可冲几百片,并能自动叠成定、转子铁芯,生产效率比普通压力机提高几十倍,材料利用率高达97%;公称压力为250KN的高速压力机的滑块行程次数已达2000次/min以上。
近年来,为了适应市场的激烈竞争,对产品质量的要求越来越高,且其更新换代的周期大为缩短。
冲压生产为适应这一新的要求,开发了多种适合不同批量生产的工艺、设备和模具。
其中,无需设计专用模具、性能先进的转塔数控多工位压力机、激光切割和成形机、CNC万能折弯机等新设备已投入使用。
特别是近几年来在国外已经发展起来、国内亦开始使用的冲压柔性制造单元(FMC)和冲压柔性制造系统(FMS)代表了冲压生产新的发展趋势。
FMS系统以数控冲压设备为主体,包括板料、模具、冲压件分类存放系统、自动上料与下料系统,生产过程完全由计算机控制,车间实现24小时无人控制生产。
同时,根据不同使用要求,可以完成各种冲压工序,甚至焊接、装配等工序,更换新产品方便迅速,冲压件精度也高。
(4)冲压标准化及专业化生产方面
模具的标准化及专业化生产,已得到模具行业和广泛重视。
因为冲模属单件小批量生产,冲模零件既具的一定的复杂性和精密性,又具有一定的结构典型性。
因此,只有实现了冲模的标准化,才能使冲模和冲模零件的生产实现专业化、商品化,从而降低模具的成本,提高模具的质量和缩短制造周期。
目前,国外先进工业国家模具标准化生产程度已达70%~80%,模具厂只需设计制造工作零件,大部分模具零件均从标准件厂购买,使生产率大幅度提高。
模具制造厂专业化程度越不定期越高,分工越来越细,如目前有模架厂、顶杆厂、热处理厂等,甚至某些模具厂仅专业化制造某类产品的冲裁模或弯曲模,这样更有利于制造水平的提高和制造周期的缩短。
我国冲模标准化与专业化生产近年来也有较大发展,除反映在标准件专业化生产厂家有较多增加外,标准件品种也有扩展,精度亦有提高。
但总体情况还满足不了模具工业发展的要求,主要体现在标准化程度还不高(一般在40%以下),标准件的品种和规格较少,大多数标准件厂家未形成规模化生产,标准件质量也还存在较多问题。
另外,标准件生产的销售、供货、服务等都还有待于进一步提高。
第1章散热器翅片分析及设计
1.1散热器翅片的功能要求分析
翅片是换热设备中影响换热系数的重要元件之一。
因涉及的行业多,产品的特点是系列化、多元化。
随着市场的不断扩展,翅片的日需求量增加,模具的需求量也增大。
由于普通模具的成本很高,为了降低模具成本,尽可能地减少模具品种,分析了零件的结构特点,对原有模具结构进行改进,决定采用级进模具生产。
本文针对X型换热器翅片设计了一副级进模,主要介绍并详细说明了换热器翅片的级进模具的设计方法及理论依据。
让读者充分了解此模具的设计过程。
对结构复杂、工序比较零散的工件,用级进模代替普通模具生产,很大程度的减少了模具种类,化简了加工工序,提高生产效率、工件精度,降低生产成本,可充分满足市场需求,创造了更大的经济效益。
1.2产品图
在满足空调的使用要求的前提下,经济是我们首要考虑的问题。
最终设计空调支架如
下图所示:
材料40Mn,然后根据图示零件设计模具。
1.2冲裁的工艺性要求
1.材料性能
τ=410~465MP
(取τ=420MP
)σ
=400~510MP
(取σ
=460MP
)
σ
=350MP
δ=30%Е=19800MP
知:
40Mn钢板有较好的塑性,有较低度的硬度,适用于各种压力加工。
2.冲裁件的尺寸精度与端面粗糙度
产品的外形尺寸不是重点设计对象,冲裁件各尺寸精度为IT12级就能满足使用要求,是冲裁可以保证的精度。
第2章零件工艺性分析
由图2.1可以看出,该零件外形尺寸不大,但有多处折弯,且有6条翻边,零件表面质量要求高,各弯曲成形角度误差须小于±30′,零件属于中小型精密冲压件。
为了确保零件精度和模具质量,首先根据零件尺寸算出展开料,在线切割机上切割几件坯料,通过成形实验发现,尺寸18±0.05mm变大,这是因为这条边冲压成形时,在16mm长边的折弯中,由于R3mm圆弧的影响,使成形高度减小,成形后回弹又影响了18±0.05mm这个尺寸,据此可知,先冲R4mm圆弧再折弯成形是不可取的。
零件成形的另一个难点是B处的翻边成形,先成形这条边会给后面成形带来干涉,后成形这条边又会对尺寸精度带来影响,因此工件的合理排样及减小成形时的相互干涉,将成为零件能否顺利成形的关键。
2.3冲压工艺方案的确定
2.3.1冷冲压模具的介绍
单工序模又称简单模,是指在压力机的一次行程内,只完成单一工序的模具,如落料模、冲孔模、弯曲模、和拉深模等。
特点是模具结构简单,制造成本低,但如果制件结构复杂就需要多套模具,而且每道工序之间的累计误差较大,制件精度较低。
复合模是在压力机的一次行程内在模具的一个工位上完成两道以上冲压工序的模具,是一种多工序冲压模。
结构复杂,不宜制造,制件精度较高,但存在最小壁厚问题。
如制件有多道工序,则模具结构特别复杂。
级进模也是多工序模具,即在压力机的一次行程内,在连续模具的不同工位上完成多道冲压工序。
于单工序模、复合模相比,级进模的主要特点是生产效率高,容易实现生产机械化和自动化。
级进模精度高、寿命长,其工作元件常采用高速钢或硬质合金钢制造。
适用于制件的大批量生产。
制件质量可靠、稳定,及制件尺寸的一致性好。
级进模结构复杂,制造精度高,调试,维修困难,价格昂贵。
由于有自动送料装置和自动出料装置,适合于高速冲床上进行自动化冲制。
也适合卷料、带料供料。
级进模可以完成冲裁、弯曲、拉深、成形等多道工序,效率比复合模高且在基金模具上可以工序分散,任意留出空位,故不存在复合模的最小壁厚的问题,因而保证了模具的强度,延长了模具的寿命。
模具的主要零件具有互换性,使模具维修方便,更换迅速、可靠。
在本次设计中由于制件较为复杂,如果选用单工序模,则就会用到多套模具,而制件精度较高,用单工序模各道工序之间的定位误差累积较大,故在这次设计中不宜选用单工序模。
由于制件工序较多,复合模也不适合用于这次设计。
所以选定用级进模具。
2.3.2级进模的介绍
多工位级进模是在普通级进模的基础上发展起来的一种高精度、高效率、长寿命的模具,是技术密集型模具的重要代表,是冲模发展方向之一。
这种模具除进行冲孔落料工作外,还可根据零件结构的特点和成形性质,完成压筋、冲窝、弯曲、拉深等成形工序,甚至还可以在模具中完成装配工序。
冲压时,将带料或条料由模具入口端送进后,在严格控制步距精度的条件下,按照成形工艺安排的顺序,通过各工位的连续冲压,在最后工位经冲裁或切断后,便可冲制出符合产品要求的冲压件。
为保证多工位级进模的正常工作,模具必须具有高精度的导向和准确的定距系统,配备有自动送料、自动出件、安全检测等装置。
所以多工位级进模与普通冲模相比要复杂,具有如下特点:
(1)在一副模具中,可以完成包括冲裁,弯曲,拉深和成形等多道冲压工序;减少了使用多副模具的周转和重复定位过程,显著提高了劳动生产率和设备利用率。
(2)由于在级进模中工序可以分散在不同的工位上,故不存在复合模的“最小壁厚”问题,设计时还可根据模具强度和模具的装配需要留出空工位,从而保证模具的强度和装配空
间。
(3)多工位级进模通常具有高精度的内、外导向(除模架导向精度要求高外,还必须对细小凸模实施内导向保护)和准确的定距系统,以保证产品零件的加工精度和模具寿命。
(4)多工位级进模常采用高速冲床生产冲压件,模具采用了自动送料、自动出件、安全检测等自动化装置,操作安全,具有较高的生产效率。
目前,世界上最先进的多工位级进模工位数多达50多个,冲压速度达1000次/分以上。
(5)多工位级进模结构复杂,镶块较多,模具制造精度要求很高,给模具的制造、调试及维修带来一定的难度。
同时要求模具零件具有互换性,在模具零件磨损或损坏后要求更换迅速,方便,可靠。
所以模具工作零件选材必须好(常采用高强度的高合金工具钢、高速钢或硬质合金等材料),必须应用慢走丝线切割加工、成型磨削、坐标镗、坐标磨等先进加工方法制造模具。
(6)多工位级进模主要用于冲制厚度较薄(一般不超过2mm)、产量大,形状复杂、精度要求较高的中、小型零件。
用这种模具冲制的零件,精度可达IT10级。
由上可知,多工位级进模的结构比较复杂,模具设计和制造技术要求较高,同时对冲压设备、原材料也有相应的要求,模具的成本高。
因此,在模具设计前必须对工件进行全面分析,然后合理确定该工件的冲压成形工艺方案,正确设计模具结构和模具零件的加工工艺规程,以获得最佳的技术经济效益。
显然,采用多工位级进模进行冲压成形与采用普通冲模进行冲压成形在冲压成形工艺、模具结构设计及模具加工等方面存在许多不同,重点介绍它们在冲压工艺与模具设计上的不同之处。
表2.1就级进模具各主要零件的功能做了简要分类:
表2.1
单元
功能
主要零件
工作单元
成型加工
凸模、凹模
辅助单元
卸料
卸料板、卸料螺钉、弹簧
定位
X向
挡料销、侧刃
Y向
导料板、侧压装置
Z向
浮顶销
精定位
导正销
导向
外导向
模架、导柱、导套
内导向
小导柱、小导套
固定
凸模固定板、上下模座。
模柄、螺钉、销钉
其他
承料板、限位板、安全检测器
2.4级进模冲裁工位的设计要点
(1)在级进冲压中,冲裁工序常安排在前工序和最后工序,前工序主要完成切边(切出制件外形)和冲孔。
最后工序安排切断或落料,将载体与工件分离。
(2)对复杂形状的凸模和凹模,为了使凸模、凹模形状简化,便于凸模,凹模的制造和保证凸模、凹模的强度,可将复杂的制件分解成为一些简单的几何形状多增加一些冲裁工位。
(3)对于孔边距很小的工件,为防止落料时引起离工件边缘很近的孔产生变形,可将孔旁的外缘以冲孔方式先于内孔冲出,即冲外缘工位在前,冲内孔工位在后。
对有严格相对位置要求的局部内,外形,应考虑尽可能在同一工位上冲出,以保证工件的位置精度。
2.5多工位级进模弯曲工位设计要点
2.5.1冲压弯曲方向设计要点
在多工位级进模中,如果工件要求向不同方向弯曲,则会给级进加工造成困难。
弯曲方向是向上,还是向下,模具结构设计是不同的。
如果向上弯曲,则要求在下模中设计有冲压方向转换机构(如滑块、摆块);若进行多次卷边或弯曲,这时必须考虑在模具上设置足够的空工位,以便给滑动模块留出活动的余地和安装空间。
若向下弯曲,虽不存在弯曲方向的转换,但要考虑弯曲后送料顺畅。
若有障碍则必须设置抬料装置。