煤气CO变换技术.docx
《煤气CO变换技术.docx》由会员分享,可在线阅读,更多相关《煤气CO变换技术.docx(43页珍藏版)》请在冰豆网上搜索。
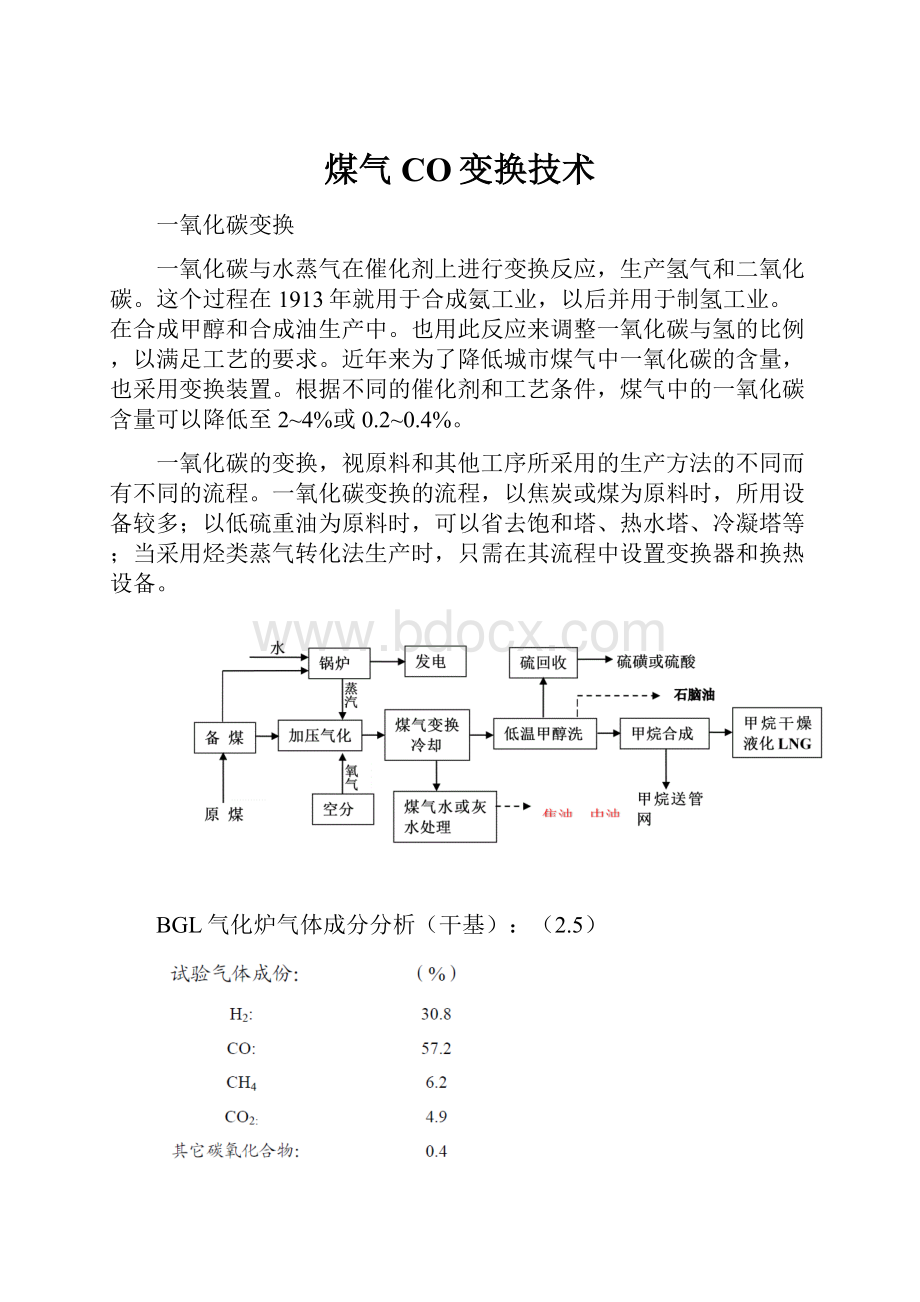
煤气CO变换技术
一氧化碳变换
一氧化碳与水蒸气在催化剂上进行变换反应,生产氢气和二氧化碳。
这个过程在1913年就用于合成氨工业,以后并用于制氢工业。
在合成甲醇和合成油生产中。
也用此反应来调整一氧化碳与氢的比例,以满足工艺的要求。
近年来为了降低城市煤气中一氧化碳的含量,也采用变换装置。
根据不同的催化剂和工艺条件,煤气中的一氧化碳含量可以降低至2~4%或0.2~0.4%。
一氧化碳的变换,视原料和其他工序所采用的生产方法的不同而有不同的流程。
一氧化碳变换的流程,以焦炭或煤为原料时,所用设备较多;以低硫重油为原料时,可以省去饱和塔、热水塔、冷凝塔等;当采用烃类蒸气转化法生产时,只需在其流程中设置变换器和换热设备。
BGL气化炉气体成分分析(干基):
(2.5)
由于甲烷化要求H2/(CO+CO2)=3.1~3.3,但粗煤气中的氢/碳比达不到要求,所以需要进行变换来调节氢碳比。
第一节一氧化碳变换的工艺原理
一氧化碳变换是在催化剂的作用下,且在一定的温度(高于催化剂的起始活性温度)条件下,CO和水蒸汽发生反应,将CO转化为氢气和二氧化碳。
其化学反应式为:
H2O+CO=CO2+H2+41.19kJ——
(1)
这是一个可逆、放热、反应前后体积不变的化学反应。
压力对反应平衡没有影响,降低温度和增大水/气比(水/气比是指进口气体水蒸汽的分子数与总干气分子数之比)会有利于反应平衡向右移动。
其他副反应:
(1)甲烷化反应
但是,在一氧化碳与水蒸气共存的系统中,是含有C、H、O三个元素的系统。
从热力学学角度,不但可能进行
(1)式的变化反应,而且还可进行其他反应,如:
CO+H2=C+H2O
CO+3H2=CH4+H2O
CO+2H2=CH4+CO2
CO2+4H2=CH4+2H2O
这一点与甲烷蒸气转化、煤气化等系统中所出现的反应式有相似之处。
但是,由于所用催化剂对反应
(1)具有良好的选择性,从而抑制了其他反应的发生。
在计算反应系统平衡组成时,采用反应
(1)式的平衡关系,其结果基本符合实际情况。
从以上反应式看,降低温度和增加压力有利于生成甲烷的反应。
但在实际生成中采用的工艺条件下,这一副反应是不会发生的。
降低床层的热点温度、增加水/汽、提高空速都可以抑制甲烷化副反应的影响。
控制反应的深度有两种方法:
(1)通过控制反应的水/汽比,可控制反应的平衡,从而控制反应的深度。
但需要指出的是,当水/气较小、床层的热点温度较高时(一般大于400℃时),就可能引发甲烷化付反应,因此,水气比的选取要保证床层的热点温度不高于400℃。
(水汽比在0.25,但要保证床层温度不超过400℃)
(2)第二种方法:
控制催化剂的装量也能达到控制反应深度的目的。
(2)一氧化碳的分解:
一氧化碳在某种条件下会发生分解反应而生成游离碳和二氧化碳。
2CO=C+CO2
生成的游离碳极易附着在催化剂表面上,使催化剂活性降低,严重时将使催化剂不能使用,而且消耗了一部分一氧化碳,所以这一副反应非常有害。
一氧化碳的分解是放热和体积缩小的反应,所以在降低温度和增加压力的条件下,会使反应向生成碳的方向进行;金属铁和碳化铁的存在也会加速此反应的进行。
另一方面,一氧化碳的分解与变换催化剂的组成和反应时气体中的水蒸气含量有关。
相关文献表明:
在200~500℃时,一氧化碳的分解反应速度很慢,在较高的蒸汽比下,实际上不产生析碳反应,但在低蒸汽比及高温下有利于析碳反应。
但在蒸汽:
CO=4:
1,空间速度100及400小时—1,200~450℃下,在Fe系及ZnO系催化剂上变换时,没有产生碳黑。
一氧化碳变换率和平衡变换率:
一氧化碳变换程度通常用变换率表示。
一氧化碳变换反应是等体积反应,反应前后体积相等。
在工业生产中,为了简便起见,采用分析蒸汽冷凝的干气组分来计算变换率。
对于干气体积来说,反应后的气体体积有所增加,因为一个CO分子反应后生成CO2和H2分子各一个,都在干气中,其变化率x的计算为:
其计算公式:
x=(1-Y2/Y1)/(Y1+Y2)
式中:
Y1和Y2是变换前后气体中CO的干基浓度
平衡变换率是变换反应达到化学平衡时,有多少CO(干)进行了变换反应。
平衡只是一种理想状态,所以,平衡变换率可用来衡量CO变换的最大程度。
合成氨生产中,原料气有效成分为H2、N2,通常根据后系统净化工艺的不同,要求最终CO的变换率不同。
过高的变换率需要消耗大量的蒸汽,液氮洗净化工艺要求变换出口的CO含量1.5%以下时比较节能。
一氧化碳变换反应的化学平衡
一、变换反应的热效应
变换反应的标准反应热ΔH298(101325Pa,25℃),可以用有关气体的标准生成热数据进行计算:
ΔH298=(ΔH298、CO2+ΔH298、H2)——(ΔH298、CO+ΔH298、H2O)
=(—393.52+0)—(—110.53—241.83)
=41.16kJ/mol
反应放出的热量,随着温度升高而降低。
不同温度下反应热推荐用下式计算
—ΔH=9512+1.619T—3.11×10—3T2+1.22×10—6T3
H2O+CO=CO2+H2的反应热
温度/K
298
400
500
600
700
800
900
ΔH/kJ/mol
41.16
40.66
39.87
38.92
37.91
36.87
35.83
不同的文献发表的反应热计算或反应热数据略有差异,主要是由于所取的恒压热容数据不同所致,但差别很小,对于工业计算没有显著的影响。
当操作压力低(3MPa)时,压力对于反应热影响很小,可以忽略不计。
所以,在工业生产中,一旦升温完毕转入正常生产后,即可利用其反应热,以维持生产过程的连续进行。
在某些流程中,还可利用部分反应热发生蒸汽,以促进反应的进行。
二、变换反应的平衡常数
变换反应一般在常压或压力不甚高的条件下进行,故计算平衡常数时,各组分用分压表示也就足够准确了。
平衡常数是温度的函数,可通过范特荷埔方程式计算:
dlnKp=
一氧化碳变换反应平衡常数
温度/K
200
250
300
350
400
450
500
Kp
210.82
83.956
38.833
20.303
11.723
7.3369
4.9777
三、反应温度
根据化学平衡移动原理,升高温度可促进反应平衡向左方移动,降低温度反应便向右方移动。
因此,反应温度愈低,愈有利于变换反应的进行。
但降低反应温度必须与反应速度和催化剂的性能一并考虑。
对于一氧化碳含量较高的半水煤气,开始反应时,为了加快反应速度,一般在较高的温度下进行,而在反应的后一阶段,为了要使反应比较完全,就必须使反应温度降低一些,工业上一般采用两段中低温变换就是根据这一概念确定的。
对于一氧化碳含量为2~4%的中温变换后的气体,就只需要在230℃左右,用低温变换催化剂进行一段变换。
反应温度与催化剂的活性温度有很大的关系,一般工业用的的变换催化剂低于某一温度反应便不能正常进行,但高于某一温度也会损坏催化剂,因此,一氧化碳变换反应必须在催化剂适用温度范围内选择优惠的工艺条件。
温度对反应平衡的计算可以通过范特荷埔方程式计算。
所以,根据气体的组分及各温度的平衡常数,可以计算出经过一氧化碳变换后气体的平衡组成。
四、压力
在一氧化碳变换反应前后,气体的分子数相同,若为理想气体,压力对反应的平衡没有影响。
目前的工业操作条件下:
压力在4MPa以下,温度为200~500℃时,压力对变换反应没有显著的影响。
在很高的压力下,各种气体与理想气体有一定偏差,必须根据各气体组分的逸度计算Kp,因此,压力对平衡有一定的影响。
Kp与压力的关系Kp与压力的关系
原料气成分:
H2O50%,CO50%原料气成分:
H2O80%,CO20%
从上图可以看出:
Kp不仅受压力的影响,而且也受气体组成的影响。
五、蒸汽添加量
一氧化碳变换为一可逆反应,增加蒸汽添加量可使反应向生成氢和二氧化碳的方向进行。
因此,工业上一般均采用加入一定的过量水蒸气的方法,以提高一氧化碳变换率。
在不同反应温度下蒸汽添加量与一氧化碳平衡变换率的关系(CO100%)
在不同反应温度下蒸汽添加量与一氧化碳平衡变换率的关系(CO40%,H250%,CO25%,N25%)
在不同反应温度下蒸汽添加量与一氧化碳平衡变换率的关系(CO100%)(左)
在不同反应温度下蒸汽添加量与一氧化碳平衡变换率的关系(CO40%,H250%,CO25%,N25%)(右)
从图中可见:
(1)温度愈低,愈有利于反应的进行,并可以节省蒸汽。
(2)在同一温度下,多加热蒸汽有利于反应的进行,但开始时一氧化碳变换率增加很快,以后逐渐减慢。
(3)要达到很高的变换率,如96%~98%,需要大大的增加蒸汽添加量。
这样不仅在经济上不合理,而且在反应时维持其热量平衡有很大的困难。
实际上,当使用半水煤气为原料,在使用中温铁铬催化剂的工业流程中,一般采用H2O(气)/CO=3~4:
1;在使用铁镁催化剂的工艺流程中,一般采用H2O(气):
CO=3~5:
1。
关于变换气中一氧化碳含量与每体积一氧化碳所用蒸汽量(体积)关系如图所示:
变换后气体CO含量与最初H2O/CO比值的关系。
六、二氧化碳对反应平衡的影响
从一氧化碳的反应方程式来看,如果能够除去生成的二氧化碳,有利于反应向生成氢的方向进行,并使变换反应接近于完成。
除去二氧化碳可以采用两种方式:
一种是利用碱性氧化物与二氧化碳作用生成碳酸盐,例如:
CaO+CO2=CaCO3
或利用碱性氧化物作为变换催化剂的一中组分吸收二氧化碳。
由于上式为放热反应,要对反应生成的热量采取一定的措施。
更重要的是这一反应在进行至一定程度后要更换吸收剂,增加了生产操作的复杂性,因此在实际上很少采用。
另一种方法是在两段中温变换之间或中温变换与低温变换之间,将气体送往脱出二氧化碳装置,然后再进行第二次变换。
这种方法相互干扰较少,比较容易实现,但增加了换热和脱除二氧化碳的设备,流程复杂一些。
变换反应的动力学
一、变换反应的机理
在催化剂存在的条件下,不少学者对变换反应的机理进行了研究,尚没取得一致的意见。
目前比较公认的机理是:
水的分子首先被催化剂的活性表面吸附,而分解成氢与吸附态的氧,氢再进入气相,在催化剂表面上生成氧原子的吸附层,当一氧化碳撞击到氧原子的吸附层时,即被氧化生成二氧化碳,并离开催化剂表面。
然后,催化剂表面又与水分子作用,重新生成氧原子的吸附层,如此反应反复进行。
催化剂若用【K】表示,则化学反应过程可表示如下:
【K】+H2O(g)=【K】O+H2
【K】O+CO=【K】+CO2
实验证明,在这两个步骤中,第二步的反应速度比第一步慢,因此,第二步是决定整个反应速度的控制步骤。
二、变换反应的动力学
一氧化碳变换的反应动力学,许多学者都进行了研究,并进行了综合报道,但是没有得到一致的结论。
Arrhenius研究了许多气相反应的速率,做了大量的研究工作。
他提出了活化能的概念,并揭示了反应的速率常数与温度的依赖关系,即:
热力学和动力学对r~T关系看法的矛盾
(1)热力学观点
根据van’tHoff公式:
1.对于吸热反应:
温度升高:
有利于正向反应
2.对于放热反应:
温度升高:
不利于正向反应
(2)动力学观点
通常活化能总为正值,所以温度升高,正向反应速率总是增加。
对于放热反应,实际生产中,为了保证一定的反应速率,也适当提高温度,略降低一点平衡转化率,如合成氨反应。
所以,对于放热反应就有:
Tm——为最适宜温度;Te——为平衡温度。
三、扩散过程对变换反应的影响
一氧化碳变换是多相催化反应,分5个阶段进行;
(1)反应气体由气流向催化剂外表面扩散(外扩散)
(2)反应气体由催化剂外表面向内表面扩散(内扩散)
(3)气体在表面上进行反应
!
:
气体反应物在表面上进行化学吸附
!
!
:
气体在表面上进行化学反应
!
!
!
:
气体反应产物在表面上进行化学脱附
(4)反应产物由内表面向外扩散(内扩散)
(5)反应物自外表面向气流中扩散(外扩散)
扩散是否对过程有影响,这是在研究变换器计算中首先需要解决的问题。
但是对于这个问题,还存在着不同的意见。
综上所述影响变换反应的因素
1、温度
变换反应是放热反应,随反应进行,温度不断升高。
大体上CO浓度每降低1%(干基),温度要升高9/(1+W)~10/(1+W)℃(W为水气比)。
对于可逆放热反应而言,存在着最佳反应温度。
温度升高,反应速度常数增大,对反应速度有利;但同时CO平衡含量增大,反应推动力变小,对反应速度又不利。
对一定的触媒及气相组成,必将出现最大的反应速度值,其对应的温度即为最佳反应温度。
随着反应在床层上的不断进行,最佳反应温度与平衡温度一样是逐渐降低的,根据最佳反应温度与CO浓度的变化关系作成的曲线,称为最佳反应温度线。
如果反应能按最佳反应温度线进行,催化剂用量最少、变换效率最高。
实际上由于绝热操作线正好相反,因此很难完全按最佳温度线进行。
综合各方面因素,变换温度条件一般这样来决定:
(1)应在触媒的活性温度范围来操作,运行中床层热点不要超过温度上限。
(2)在触媒使用初期或触媒活性较好的情况下,应尽量控制在较低的温度,既可以达到反应要求,又可以起到防止催化剂过早衰老的效果;而在触媒使用后期或触媒活性下降后,就应逐渐提高反应温度,以反应速度的提高来弥补活性的下降,最终达到变换率的要求。
(3)为了尽可能接近最佳温度线进行反应,可采用分段冷却。
这也是设置两个低变炉的原因之一。
对于低变炉,值得注意的是,操作温度不仅受到触媒活性温度的限制,而且还必须高于气体在该压力和水气比下的露点温度以上20℃。
两段变换过程T—x关系(中间简介冷却)
2、压力
由于变换反应是等体积反应,故压力对平衡无影响,但压力变化影响反应速度,反应速度大约与压力的平方根成正比。
3、汽/气比
汽/气比(水蒸汽组分与原料气中的干气组分的摩尔比或标准状况下的体积比)或水碳比(H2O/CO)是变换操作的一个重要调节手段。
从平衡关系可知,汽/气比增大,则CO的平衡变换率提高,从而有利于降低CO残余含量,加速变换反应的进行;同时较大的水气比,还对副反应有抑制作用。
但是,水蒸汽用量是变换过程中最主要消耗指标。
蒸汽比例过高,还将造成催化剂床层阻力增大,CO停留时间缩短,余热回收设备负荷加重等,工艺冷凝液增多。
汽/气比:
原料气中的水蒸汽组分与原料气中的干气组分的摩尔比标准状况下的体积比,通常用S/G表示。
4、空速对催化剂活性的影响
由于进料速度大小直接反映了系统生产能力的高低,因而,催化剂对高空速的适应能力也是衡量催化剂性能优劣的一个重要标志,随空速的提高,变换率呈线性降低,见下图:
第二节变换催化剂
一氧化碳与水蒸气反应生成氢与二氧化碳必须在催化剂的帮助下方能进行。
催化剂能够加速反应,但不能改变反应的化学平衡,催化剂本身虽参加反应,但反应后任保持原量,而其化学组成与化学性质均不变。
工业上对催化剂的要求:
(1)催化剂的活性好,能在较低或中等温度下以较快的速度进行反应。
(2)催化的寿命要长,要求经久耐用。
(3)催化剂要有一定的抗毒能力,也就是能耐气体中含有的少量有毒气体。
(4)催化剂的机械性能要好,以免在使用中破碎或粉碎,增加变换阻力。
(5)催化剂有一定的热稳定性,在一定温度范围内,不致因反应后温度升高而损坏催化剂
(6)催化剂要防止发生副反应,主要是一氧化碳分解析碳和生成甲烷的反应。
(7)催化剂的原料容易获得,制造成本低廉。
一氧化碳变换催化剂类型:
(1)60年代以前,主要应用以Fe2O3为主的Fe—Cr系催化剂,使用范围为350~550℃,由于操作温度的限制,气体经变换任有3%左右的一氧化碳。
(1912年德国人W.Wied利用FeO—Al2O3作为一氧化碳变换催化剂,A.Mitasch等研制成功了Fe——Cr系催化剂,并与1913年在德国的BASF公司合成氨工厂首先得到应用,该系列催化剂称为高温变换催化剂)。
(2)60年代以来,随着制氨路线的改变和脱硫技术的进展,气体中总硫含量可以降低到0.1ppm以下,有可能在更低温度下使用活性高而抗毒性差以CuO为主的Cu—Zn系催化剂,操作温度为200~280℃,残余一氧化碳可降到0.3%左右。
(1963年美国Giraler公司开发了Cu——Zn系列催化剂)
为了区别上述两种温度范围的变换过程,国外和我国大型氨厂习惯上将前者称为高温变换,国内中小型氨厂则称为中温变换;而后者称为低温变换。
(3)对于渣油和煤制氨工艺,因气化过程回收高位能热量方式不同而分激冷流程和废锅流程。
若在激冷流程中任采用传统的先脱硫、后变换工艺,由于脱硫都是在较低温下进行,这样就会造成粗原料气冷却过程将回收大量的蒸汽冷凝。
于是将变换直接串联在油(煤)气化之后,然后用一步法同时脱硫脱碳,促使人们开发了Co—Mo系的耐硫变换催化剂。
但对废锅流程,可用先脱硫,在进行一氧化碳变换。
今年来我国开发了Co——Mo系宽温变换催化剂(活性温度为160~500℃),使变换气中CO含量从3%将至1%。
一氧化碳变换催化剂的制造:
一氧化碳变换三种催化剂的制造方法主要沉淀法、混合法和浸渍法。
(1)沉淀法:
沉淀法又有:
单组分沉淀法;
共沉淀法;
均匀沉淀法;
超均匀沉淀法。
(2)浸渍法:
(3)混合法:
液液混合;
固固混合(干式混合);
液固混合(湿式混合)。
Fe—Cr系催化剂
以氧化铁为主体的多组分催化剂有许多优点:
(1)在350℃~450℃时具有很高的活性;
(2)机械强度较好,不易粉碎;(3)对硫化氢的毒害不如铜锌系催化剂敏感,即使中毒,在使用纯净的气体后,基本可以恢复到原有的活性;(4)耐热性能较好;(5)能防止一氧化碳分解和生成甲烷的副反应;(6)制造方法简单;(7)原料易得,成本较低;(8)使用寿命较长。
1、各种促进剂的作用:
以三氧化二铁为主体的催化剂,为了改善其性能,一般要加一定数量的促进剂,稳定剂及活性或非活性的粘结剂。
促进剂是铬、铝及钾的氧化物,可以只加一种或几种。
氧化铬是最通常采用的促进剂。
氧化铬在铁铬催化剂中的作用,有人曾进行过较详细的研究。
目前研究者大多认为催化剂中含有适量的氧化铬会起下列作用:
(1)增加堆积比重;
(2)增加比表面积;(3)铬的加入能导致催化剂形成更细的孔结构,从而提高活性;(4)铬分布在催化剂中,起着稳定剂的作用,它能阻碍四氧化三铁再结晶,使催化剂的耐热性提高,使用寿命延长;(5)在制备催化剂的工艺过程中,采用适当形式的铬,能提高其机械强度和抗毒性能。
水合氧化铝是一种粘结剂,可以改进催化剂的机械性能。
氧化镁除了防止硫化物中毒的稳定剂外,也有类似的作用。
2、铁铬催化剂的品种
铁铬催化剂主要成分为三氧化二铁和促进剂三氧化二铬或三氧化铬,其操作温度为135~485℃。
早期由于原料煤气净化较差,有些产品中含有一定数量的氧化镁,为了便于区别,我们将后者称为铁镁催化剂,这种催化剂的操作温度为400~500℃。
以氧化铁为主体的多组分催化剂,也可以用于加压变换,但要求较高的机械强度。
铁镁催化剂现在只用于某些不经脱硫或含硫量较高的原料气体。
对于净化较好的气体一般采用铁铬催化剂。
今后铁铬催化剂的发展方向是提高低温活性,以降低蒸汽消耗和减少变换气中一氧化碳的含量;另一方面希望催化剂能在较宽温度范围操作。
3、Fe——Cr系催化剂的性质
(1)氧化与还原
以三氧二铁为主体的变换催化剂,在使用以后,由原来的赤褐色变成黑色的四氧化三铁,其反应方程式如下:
3Fe2O3+CO=2Fe3O4+CO2
(1)
3Fe2O3+H2=2Fe3O4+H2O
(2)
以上两式均为放热反应,当进行还原操作时,大量水蒸汽和水煤气一并进入变换器,式
(2)的反应不易向右方进行,因此主要的还原是
(1)式,并且一氧化碳开始还原的温度约为200℃,要比氢低一些。
不论
(1)式,
(2)式或还原完毕的一氧化碳都是放热反应,故在操作中必须严格控制煤气的加入量,以避免温度急剧上升,影响催化剂的活性、机械强度及使用寿命。
另一方面,当水煤气与极少量的蒸汽(<3%)还原催化剂时,会生成碳化铁及碳,产生此反应的开始温度为300~350℃,另外用纯氢或氢氮混合气还原催化剂会生成铁。
催化剂中的Cr2O3不再被水煤气还原,但铬化和物如CrO3,则将与水煤气发生下列反应:
CrO3+3H2=Cr2O3+H2O
CrO3+3CO=Cr2O3+3CO2
CrO3还原时放出大量的热,如还原过速,有可能产生超温而损坏催化剂。
当催化剂中含有硫酸根时,会被氢还原生成硫化氢,并随气体带出,因此在操作中应力求避免硫化氢进入低温变换催化剂。
另一方面在生产催化剂时要尽可能降低产品中硫酸根的含量。
氧能将四氧化三铁氧化成三氧化二铁,其反应方程式如下:
4Fe3O4+O2=6Fe2O3
上式也是放热反应,我们必须限制进入变换器的气体中的氧含量,以免难以控制操作温度。
在系统停工拆开检修时,也必须注意这一反应,如催化剂未彻底冷却及通入空气(氧气)催化剂的温度也会急剧上升。
(2)铁铬系变换催化剂的中毒
当煤气中含有硫、磷、砷、氟、硼及氢氰酸等化合物时,以氧化铁为主体的变化催化剂就会中毒。
当催化剂含硼时,对活性影响很大。
磷和砷的化合物的中毒是不可逆的。
氯化物的影响比硫化化合物严重,但当氯的含量小于1ppm时,其影响是不显著的。
煤气中通常含有硫化物,硫化氢与催化剂的反应如下:
Fe3O4+3H2S+H2=3FeS+4H2O
煤气中含硫化氢愈多,催化剂活性降低愈大,此外催化剂层温度愈低,其活性降低也愈大。
此反应是可逆的。
对于含一定量硫化氢的煤气,在一定的操作条件下,对催化剂的活性有一定的影响,当恢复使用纯净的煤气时,催化剂的活性也可以较快的恢复。
对于含氧化镁的变换催化剂,硫化氢与氧化镁起下列反应:
MgO+H2S=MgS+H2O
当水蒸汽含量增加或煤气中的硫化物含量减少时,反应平衡就向左方移动。
因此,铁镁崔环境有一定的耐硫性能,但是由于铁镁催化剂活性温度较高,变换所需的蒸汽消耗较多。
铁镁催化剂对于硫化氢含量为0.2g/Nm3的煤气没有影响,对于含硫化氢16~20g/Nm3的煤气活性略有所降低,而一旦硫化氢含量降低时,即可恢复催化剂原来的活性。
有机硫化物在半水煤气中含量随原料及气化方法而变动。
以煤、焦为原料时,一般在60~800mg/Nm3之间,对于优质原料其含量接近下限,有机硫化合物的主要成分为氧硫化碳,其次为二硫化碳。
在一氧化碳变换时,氧硫化碳90%以上可转变为硫化氢。
COS+H2=H2S+CO
COS+H2O=H2S+CO2
二硫化碳、硫醇等亦类似的反应,因此变换气中的硫化氢含量往往高于半水煤气中硫化氢的含量,在考虑硫化合物对催化剂中毒时,要考虑有机硫化合物的影响。
在正常操作温度条件下,噻吩在铁铬变换催化剂上不起反应,对催化剂也没有影响。
由蒸汽中带入的磷或硅的化合物对催化剂有不良影响。
煤气中的灰尘,部分氧化法制气未除净的碳黑以及蒸汽中的盐类都会影响气体分子向催化剂内部传递,从而影响催化剂的活性。
由蒸汽中带入的磷或硅的化合物对催化剂对催化剂有不良影响。
煤气中的灰尘、部分氧化法制气未除净的炭黑以及蒸汽中的盐类都会影响气体分子向催化剂内部传递,从而影响催化剂的活性。
(3)中温变换催化剂的活性温度及空间速度
中温变换催化剂的活性温