压力容器制造实用工艺流程.docx
《压力容器制造实用工艺流程.docx》由会员分享,可在线阅读,更多相关《压力容器制造实用工艺流程.docx(38页珍藏版)》请在冰豆网上搜索。
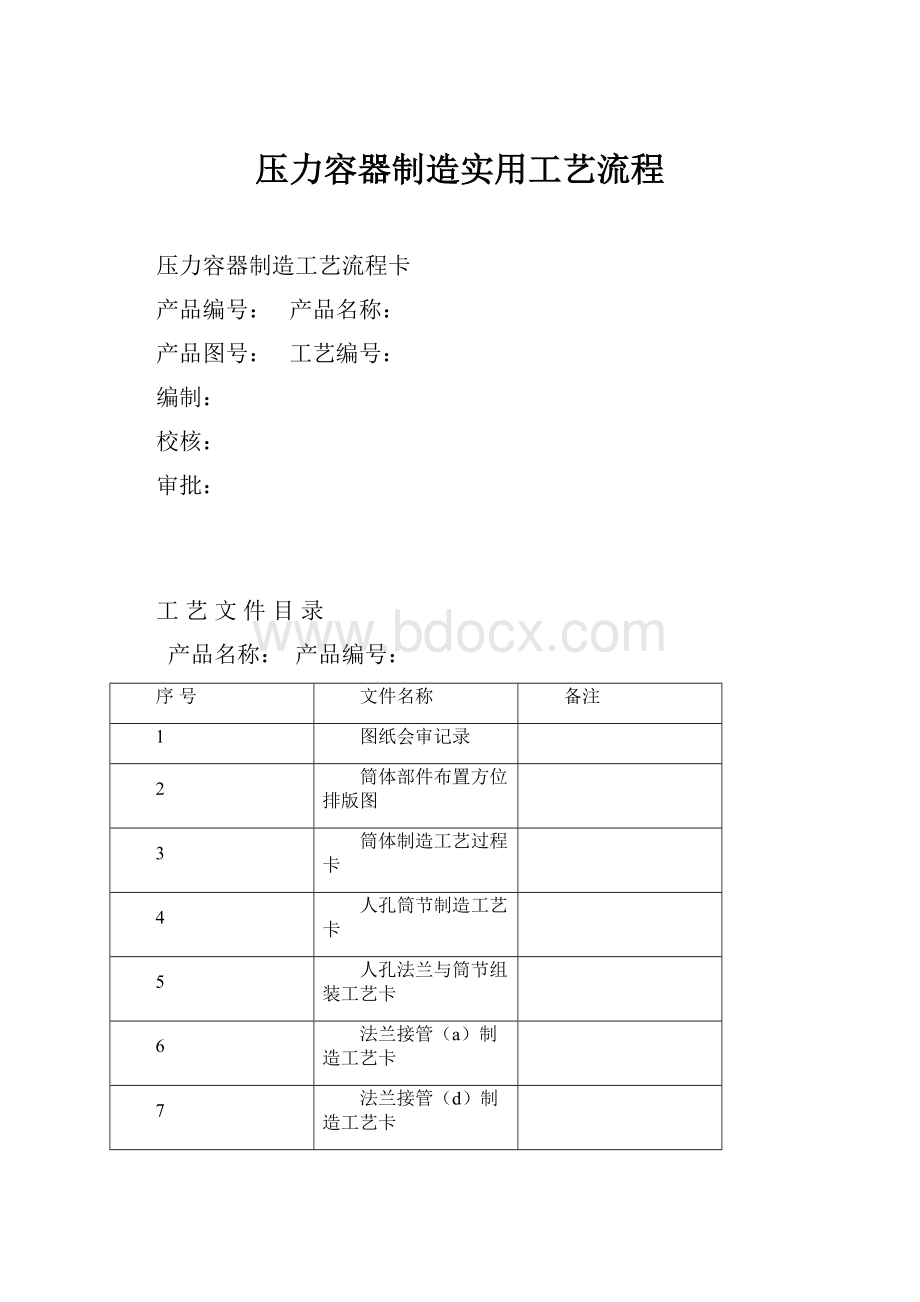
压力容器制造实用工艺流程
压力容器制造工艺流程卡
产品编号:
产品名称:
产品图号:
工艺编号:
编制:
校核:
审批:
工艺文件目录
产品名称:
产品编号:
序号
文件名称
备注
1
图纸会审记录
2
筒体部件布置方位排版图
3
筒体制造工艺过程卡
4
人孔筒节制造工艺卡
5
人孔法兰与筒节组装工艺卡
6
法兰接管(a)制造工艺卡
7
法兰接管(d)制造工艺卡
8
吊耳、垫板制造工艺卡
9
支座、垫板制造工艺卡
10
总装工艺过程卡
11
耐压试验工艺过程卡
12
酸洗钝化、油漆、包装工艺卡
13
14
15
图纸会审记录
产品名称
产品编号
产品图号
一、设计单位
1.压力容器设计资格:
□无□有
2.总图上的资格印章:
□无□有
3.资格印章编号
二、设计所依据的技术标准、技术规范等是否具有有效版本:
□无□有
三、图样:
1.几何尺寸是否正确:
□是□否
2.图面是否整洁、清晰:
□是□否
3.技术要求叙述是否正确、完整、简明:
□是□否
4.管口表是否正确统一:
□是□否
5.技术特性表是否正确统一:
□是□否
6.明细表内容是否齐全、正确:
□是□否
四、图样中存在问
题及更改情况:
五、结论意见:
设计责任师
材料零部件责任师
作业(工艺)责任师
检验与试验责任师
焊接责任师
无损检测责任师
图纸会审日期:
年月日
储气罐部件布置方位排版图
产品名称
产品编号
部件名称
筒体
规格
DN1200
部件方位排版图注:
b管件在上封头,f管件在下封头;部件尺寸详见图纸
产品名称
制造工艺流程卡
结构示意图
产品编号
产品图号
零件名称
壳程筒节
筒体图号
5
筒体编号
A1
件号
\
材质
022Cr19Ni10
规格
δ=6
材检编号
B2014-04
零件加工数量
共1件第1件
序号
控制点
工艺过程工艺要求
检验项目及数据
自检(操作者)
专检(检查员)
工序名称
工艺要求
项目
数据
结论
签名
结论
签名
日期
1
R
备料
所用材料应具有质量证明书,标记齐全。
确认材质规格及检号
/
2
E
划线
下料
划线长度允差±1mm,宽度允差±1mm,两对角线之差≤2mm。
下料人员作好材料标记移植,检验员确认后,按线下料。
下料尺寸
3787×1320
标记移植
B2014-04
3
E
坡口加工
每侧坡口角度30°,钝边0~2mm,加工后清除坡口两侧20mm范围内的氧化物等有害杂质,露出金属光泽。
角度
30°
钝边
0~2mm
4
E
卷筒成型
按左、中、右三点确认预弯弧度,卷制成型,并在卷板机上点焊,对口间隙0~1mm,错边量b≤2mm。
错边量b
≤2mm
组对间隙
0~1mm
5
E
焊接
按焊接工艺卡施焊。
焊缝质量
无缺陷
6
E
校圆
筒体校圆,要求同一断面上最大最小直径差e≤12mm,棱角度E≤2.6mm。
椭圆度
≤12mm
棱角度
≤2.6mm
7
R
无损检测
对焊缝进行20%且不小于250mm的RT检测,按JB/T4730.2-2005标准Ⅲ级合格。
见无损检测报告单
/
8
准备
转入壳程组装工序。
检验结论:
检查员:
年月日
产品名称
制造工艺流程卡
结构示意图
产品编号
产品图号
零件名称
人孔筒节
筒体图号
4
筒体编号
A2
件号
e
材质
06Cr19Ni10
规格
δ=5
本厂材编
B2014-06
零件加工数量
共1件第1件
序号
控制点
工艺过程工艺要求
检验项目及数据
自检(操作者)
专检(检查员)
工序名称
工艺要求
项目
数据
结论
签名
结论
签名
日期
1
R
备料
所用材料应具有质量证明书,标记齐全。
确认材质规格及检号
/
2
E
划线
下料
划线长度允差±1mm,宽度允差±1mm,两对角线之差≤2mm。
下料人员作好材料标记移植,检验员确认后,按线下料。
下料尺寸
200×1322
标记移植
B2014-06
3
E
坡口加工
每侧坡口角度30°,钝边0~2mm,加工后清除坡口两侧20mm范围内的氧化物等有害杂质,露出金属光泽。
角度
30°
钝边
0~2mm
4
E
卷筒成型
按左、中、右三点确认预弯弧度,卷制成型,并在卷板机上点焊,对口间隙0~1mm,错边量b≤2mm。
错边量b
≤2mm
组对间隙
0~1mm
5
E
焊接
按焊接工艺卡施焊。
焊缝质量
无缺陷
6
E
校圆
筒体校圆,要求同一断面上最大最小直径差e≤12mm,棱角度E≤2.5mm。
椭圆度
≤4mm
棱角度
≤2.5mm
7
R
无损检测
对焊缝进行100%RT检测,按JB/T4730.2-2005标准Ⅲ级合格。
见无损检测报告单
/
8
E
准备
转入人孔法兰与人孔筒节组对工序
检验结论:
检查员:
年月日
产品名称
制造工艺流程卡
人孔法兰
产品编号
产品图号
零件名称
人孔法兰
筒体图号
4
部件编号
RK2014-01
件号
e
材质
06Cr19Ni10
规格
δ=5
本厂材编
B2014-07
零件加工数量
共1件第1件
序号
控制点
工艺过程工艺要求
检验项目及数据
自检(操作者)
专检(检查员)
工序名称
工艺要求
项目
数据
结论
签名
结论
签名
日期
1
R
备料
领出人孔法兰及制备好的人孔筒节
确认材质规格及检号
/
2
E
组对
四点定位点固,接管与法兰密封面的垂直度偏差不超过1%Di。
垂直度
≤1%Di
管口布置
跨中
3
E
焊接
焊接角焊缝,按焊接工艺卡施焊、焊脚尺寸应≥10mm,焊脚应凹形圆滑过渡。
焊缝质量
无缺陷
焊脚尺寸
≥10mm
4
5
6
7
8
准备
转入总装工序
检验结论:
检查员:
年月日
产品名称
制造工艺流程卡
说明
接管法兰与接管短节组对
产品编号
产品图号
零件名称
法兰接管
部件图号
7/6
法兰接管编号
7/6
件号
a
法兰
材质
S30408
规格
PL80-10RF
材检编号
FL2014-01-01
接管
材质
06Cr19Ni10
规格
89*6
材检编号
G2014-03
序号
控制点
工艺过程工艺要求
检验项目及数据
自检(操作者)
专检(检查员)
工序
名称
工艺要求
项目
数据
结论
签名
结论
签名
日期
1
R
备料
领出接管法兰及制备好的接管短节
确认材质规格及检号
/
2
E
划线
按照图纸接管直径89mm,接管长度尺寸163mm进行划线。
并做好标记移植
规格
89*6
尺寸
163mm
标记移植
G2014-03
3
E
下料
按照划线尺寸163mm,用锯床进行切割下料
规格
89*6
尺寸
163mm
4
E
组对
四点定位点固,接管与法兰密封面的垂直度偏差不超过1%Di。
垂直度
≤1%Di
管口布置
跨中
5
E
焊接
焊缝焊接按焊接工艺卡施焊,焊角应凹型圆滑过渡
焊缝质量焊脚
无缺陷
焊脚尺寸
≥6mm
6
准备
转入总装工序
检验结论:
检查员:
年月日
产品名称
制造工艺流程卡
说明
接管法兰与接管短节组对
产品编号
产品图号
零件名称
法兰接管
部件图号
11
法兰接管编号
11
件号
d
法兰
材质
S30408
规格
PL80-10RF
材检编号
FL2014-01-02
接管
材质
06Cr19Ni10
规格
89*6
材检编号
G2014-03
序号
控制点
工艺过程工艺要求
检验项目及数据
自检(操作者)
专检(检查员)
工序名称
工艺要求
项目
数据
结论
签名
结论
签名
日期
1
R
备料
领出接管法兰及制备好的接管短节
确认材质规格及检号
/
2
E
划线
按照图纸接管直径89mm,接管长度尺寸450mm进行划线。
并做好标记移植
规格
89*6
尺寸
450mm
标记移植
G2014-03
3
E
下料
按照划线尺寸450mm,用锯床进行切割下料
规格
89*6
尺寸
450mm
4
E
组对
四点定位点固,接管与法兰密封面的垂直度偏差不超过1%Di。
垂直度
≤1%Di
管口布置
跨中
5
E
焊接
焊缝焊接按焊接工艺卡施焊、焊脚应凹型圆滑过渡
焊缝质量
无缺陷
焊脚尺寸
≥6mm
6
准备
转入总装工序
检验结论:
检查员:
年月日
产品名称
制造工艺流程卡
说明
产品编号
产品图号
零件名称
吊耳垫板
部件图号
12
吊耳垫板编号
12
件号
\
材质
022Cr19Ni10
规格
14mm
材检编号
B2014-05
零件加工数量
共2件
序号
控制点
工艺过程工艺要求
检验项目及数据
自检(操作者)
专检(检查员)
工序名称
工艺要求
项目
数据
结论
签名
结论
签名
日期
1
R
备料
所用材料应具有质量证明书,标记齐全。
确认材质规格及检号
/
2
E
划线
按照图纸标准垫板规格尺寸400×200×14mm,进行划线。
并做好标记移植
规格
14mm
尺寸
400×200
标记移植
B2014-05
3
E
下料
按照划线尺寸400×200×14mm的规格,用空气等离子切割进行切割下料
规格
14mm
尺寸
400×200
4
E
坡口
坡口角度50°±5°,钝边4mm,加工后清除坡口两侧20mm范围内的氧化物等有害杂质,露出金属光泽。
坡口角度
50度
钝边
4mm
5
E
压弧
压制顶部吊耳垫板弧度,垫板应与封头曲面紧密贴合,其间隙不得大于1mm,
弧度
与封头吻合
吻合间隙
≤1mm
6
E
钻孔
在垫板所规定的位置钻孔,用规格8.5mm钻头进行钻孔
钻孔直径
8.5mm
7
E
攻丝
在垫板8.5孔上进行攻螺纹M10孔
螺纹规格
M10
8
准备
转入总装工序
检验结论:
检查员:
年月日
产品名称
制造工艺流程卡
说明
产品编号
产品图号
零件名称
吊耳
部件图号
12
吊耳垫板编号
12
件号
\
材质
Q235B
规格
30mm
材检编号
B2014-09
零件加工数量
共2件
序号
控制点
工艺过程工艺要求
检验项目及数据
自检(操作者)
专检(检查员)
工序名称
工艺要求
项目
数据
结论
签名
结论
签名
日期
1
R
备料
所用材料应具有质量证明书,标记齐全。
确认材质规格及检号
/
2
E
数控
下料
在数控空气等离子机床上按照图纸标准封头顶部TPP-4吊耳形状规格尺寸输入数控数据,并做好标记移植后,进行切割下料。
规格
30mm
形状尺寸
TPP-4
标记移植
B2014-09
3
E
打磨
清理
下料后用角向磨光机清除打磨坡口两侧20mm范围内以及等离子切割时残留的的氧化物、等有害杂质,露出金属光泽。
打磨质量
表面光滑,无缺陷
4
E
厚度
加工
将30mm厚的吊耳用铣床加工成吊耳标准规定的厚度28mm
标准吊耳厚度
28mm
5
E
坡口
加工
用铣床加工吊耳坡口坡口型式K型,坡口角度55±5°,钝边0~2mm,,
坡口型式
K型
坡口角度
505
坡口钝边
0~2mm
6
E
准备
转入总装工序
检验结论:
检查员:
年月日
产品名称
制造工艺流程卡
说明
产品编号
产品图号
零件名称
支座垫板
部件图号
2
支座垫板编号
2
件号
\
材质
022Cr19Ni10
规格
10mm
材检编号
B2014-07
零件加工数量
共3件
序号
控制点
工艺过程工艺要求
检验项目及数据
自检(操作者)
专检(检查员)
工序名称
工艺要求
项目
数据
结论
签名
结论
签名
日期
1
R
备料
所用材料应具有质量证明书,标记齐全。
确认材质规格及检号
/
2
E
划线
按照图纸标准垫板规格尺寸280×240×10mm,进行划线。
并做好标记移植
规格
10mm
尺寸
280×240
标记移植
B2014-07
3
E
下料
按照划线尺寸280×240×10mm的规格,用空气等离子切割进行切割下料
规格
10mm
尺寸
280×240
4
E
压弧
压制支座垫板弧度,垫板应与封头曲面紧密贴合,其间隙不得大于1mm,
弧度
与封头吻合
吻合间隙
≤1mm
5
E
钻孔
在垫板所规定的位置钻孔,用规格8mm钻头进行钻孔
钻孔直径
8mm
6
E
准备
转入总装工序
检验结论:
检查员:
年月日
产品名称
制造工艺流程卡
说明
产品编号
产品图号
零件名称
支座筋板
部件图号
2
支座筋板编号
2
件号
\
材质
Q235B
规格
10mm
材检编号
B2014-08
零件加工数量
共6件
序号
控制点
工艺过程工艺要求
检验项目及数据
自检(操作者)
专检(检查员)
工序名称
工艺要求
项目
数据
结论
签名
结论
签名
日期
1
R
备料
所用材料应具有质量证明书,标记齐全。
确认材质规格及检号
/
2
E
划线
按照图纸筋板规格寸l=180mm;b=120mm;h=420mm,进行划线。
并做好标记移植
规格
10mm
尺寸
见图
标记移植
B2014-08
3
E
下料
按照划线尺寸,用空气等离子切割进行切割下料
规格
10mm
尺寸
见图
4
E
打磨
加工后用角向磨光机清除打磨坡口两侧20mm范围内以及等离子切割时残留的的氧化物、等有害杂质,露出金属光泽。
打磨质量
表面无缺陷
5
准备
转入总装工序
检验结论:
检查员:
年月日
产品名称
制造工艺流程卡
说明
产品编号
产品图号
零件名称
支座底板
部件图号
2
支座底板编号
2
件号
\
材质
Q235B
规格
10mm
本厂材编
B2014-08
零件加工数量
共3件
序号
控制点
工艺过程工艺要求
检验项目及数据
自检(操作者)
专检(检查员)
工序名称
工艺要求
项目
数据
结论
签名
结论
签名
日期
1
R
备料
所用材料应具有质量证明书,标记齐全。
确认材质规格及检号
/
2
E
划线
按照图纸标准底板板规格尺寸170×120×10mm,进行划线。
并做好标记移植
规格
10mm
尺寸
170×120
标记移植
B2014-08
3
E
下料
按照划线尺寸170×120×10mm的规格,用空气等离子切割进行切割下料
规格
10mm
尺寸
170×120
5
E
打磨
加工后用角向磨光机清除打磨坡口两侧20mm范围内以及等离子切割时残留的的氧化物、等有害杂质,露出金属光泽。
打磨质量
表面光滑,无缺陷
5
E
钻孔
在底板中心的位置钻地脚螺栓孔,用规格24mm钻头进行钻孔
钻孔直径
24mm
6
E
准备
转入总装工序
检验结论:
检查员:
年月日
产品名称
制造工艺流程卡
说明
按JB/T4712.4-2007支座A2图纸进行制作
产品编号
产品图号
零件名称
支座组装
部件图号
2
支座编号
2
件号
\
材质
Q235B
规格
10mm
材检编号
B2014-08
零件加工数量
共3件
序号
控制点
工艺过程工艺要求
检验项目及数据
自检(操作者)
专检(检查员)
工序名称
工艺要求
项目
数据
结论
签名
结论
签名
日期
1
R
备料
准备好制备的支座筋板、底板及垫板
确认材质规格及检号
/
2
E
划线
按照支座图纸标准规格尺在底板和垫板上,进行组装方位线。
规格
10mm
尺寸
见JB/T4712.4支座A2
3
E
组装
按照图样支座规格进行组装点固成型
规格
10mm
尺寸
见JB/T4712.4支座A2
5
E
焊接
将组装好的支座进行焊接(不包括垫板),焊接要求按照JB/T4712.1.7-2007支座制造技术要求
焊接质量应符合JB/T4712.1.7-2007
无缺陷
6
E
清理打磨
清理焊渣及飞溅。
清理质量
露出金属光泽
7
E
准备
转入总装工序
检验结论:
检查员:
年月日
产品名称
总装工艺流程卡
说
明
见图纸
产品编号
图号
容器类别
第Ⅰ类
序号
控制点
工序过程工艺要求
检验项目及数据
自检(操作者)
专检
工序名称
工艺要求
检验项目
数据
结论
签名
结论
签名
日期
1
/
备料
1)准备好组装用零部件,自检应符合图纸要求。
2)按图确