清洁生产案例分析doc.docx
《清洁生产案例分析doc.docx》由会员分享,可在线阅读,更多相关《清洁生产案例分析doc.docx(16页珍藏版)》请在冰豆网上搜索。
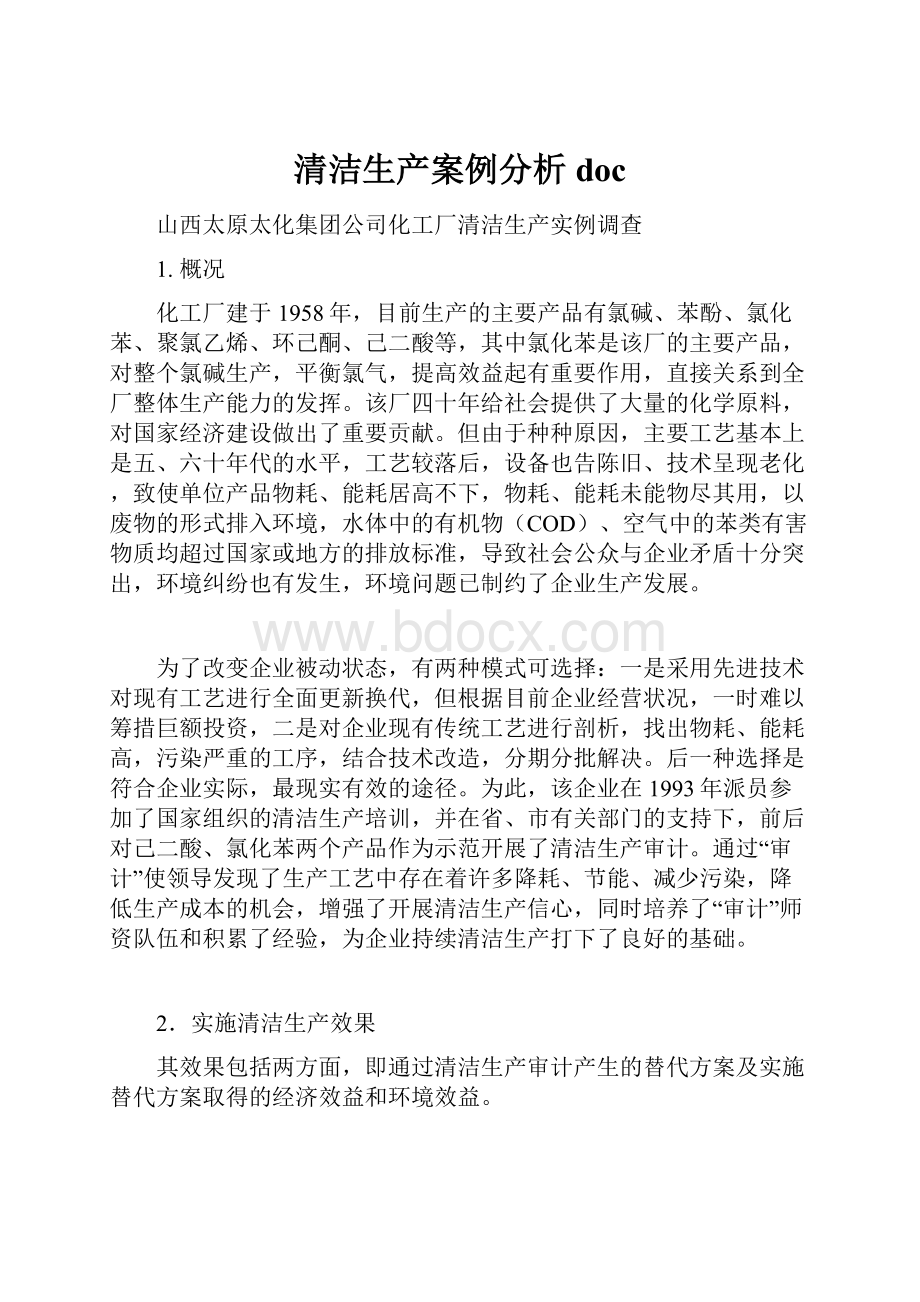
清洁生产案例分析doc
山西太原太化集团公司化工厂清洁生产实例调查
1.概况
化工厂建于1958年,目前生产的主要产品有氯碱、苯酚、氯化苯、聚氯乙烯、环己酮、己二酸等,其中氯化苯是该厂的主要产品,对整个氯碱生产,平衡氯气,提高效益起有重要作用,直接关系到全厂整体生产能力的发挥。
该厂四十年给社会提供了大量的化学原料,对国家经济建设做出了重要贡献。
但由于种种原因,主要工艺基本上是五、六十年代的水平,工艺较落后,设备也告陈旧、技术呈现老化,致使单位产品物耗、能耗居高不下,物耗、能耗未能物尽其用,以废物的形式排入环境,水体中的有机物(COD)、空气中的苯类有害物质均超过国家或地方的排放标准,导致社会公众与企业矛盾十分突出,环境纠纷也有发生,环境问题已制约了企业生产发展。
为了改变企业被动状态,有两种模式可选择:
一是采用先进技术对现有工艺进行全面更新换代,但根据目前企业经营状况,一时难以筹措巨额投资,二是对企业现有传统工艺进行剖析,找出物耗、能耗高,污染严重的工序,结合技术改造,分期分批解决。
后一种选择是符合企业实际,最现实有效的途径。
为此,该企业在1993年派员参加了国家组织的清洁生产培训,并在省、市有关部门的支持下,前后对己二酸、氯化苯两个产品作为示范开展了清洁生产审计。
通过“审计”使领导发现了生产工艺中存在着许多降耗、节能、减少污染,降低生产成本的机会,增强了开展清洁生产信心,同时培养了“审计”师资队伍和积累了经验,为企业持续清洁生产打下了良好的基础。
2.实施清洁生产效果
其效果包括两方面,即通过清洁生产审计产生的替代方案及实施替代方案取得的经济效益和环境效益。
2.1己二酸产品“审计”及效果
己二酸生产工艺分为两个工段,即己二酸工段和尾气工段12个工序。
己二酸工段包括氧化、结晶、压缩、压滤、离心和干燥六个工序;尾气工段包括供水、供料、配酸、风机、吸收和浓缩六个工序。
其生产工艺见流程图(图1)。
图1己二酸生产工艺流程
该企业在1994年开展了己二酸产品清洁生产审计,通过“审计”提出了12项替代方案,其中无费方案8项,低费方案2项,中费和高费方案各1项。
2.1.1不同替代方案名称及改进措施(见表1)。
表1己二酸工艺替代方案名称及改进措施
类型
序号
方案名称及问题
改进措施
无
费
方
案
F1
氧化釜盖不严、漏料
更换氧化系统釜盖密封
F2
氧化釜反应温度、时间难控制
在加料塔上加孔板
F3
压滤工序常跑料
严格操作,加强员工培训
F4
离心设备局部跑料
定期维修,严格控制加料速度
F5
干燥尾气工序易跑料
严格控制风量、加料量
F6
产品包装易跑料
及时更换布袋
F7
氧化釜加料不合理
调整加料量和时间
F8
压滤监控分析仪有故障
加强仪器维修和人员培训
低费
方案
F9
氧化终点控制不合理,影响转化率
调整氧化反应温度和湿度
F10
浓缩尾气冷却器损坏,影响回收
检修和更换冷却器提高回收回流液效率
中费
F11
尾气系统改造,吸收塔老化
改塑料塔为不锈钢塔
高费
F12
生产系统改造
改间断为连续生产工艺,扩大生产能力
2.1.2实施替代方案的效果
1.实施无费方案的经济效益(见表2)
表2实施无费方案的经济效益
序号
经济效益
F1
通过严格生产管理,对设备维修、保养,加强员工培训,提高操作有效性,实施无费方案取得的效果。
原料己二醇转化率由92%提高到93%。
产品己二酸总收率由83%提高到84.5%。
每吨己二酸消耗的环己醇定额下降了11.98公斤,相当年多生产己二酸产品21吨,以每吨己二酸产品售价6700元,年创经济效益14.07万元。
F2
F3
F4
F5
F6
F7
F8
2.实施低价、中费方案生产工艺简述及经济分析
替代方案工艺简述
氧化终点控制(F9)硝酸氧化环己醇的转化率偏低,工艺控制指标不完善,在现有工艺条件下,通过改变工艺反应控制指标,如:
温度、压力、时间等来探讨提高环己醇转化率最佳参数,控制低级酸产生。
浓缩回流液回收(F10)因浓缩尾气部分冷却器损坏,浓缩蒸发气体难以冷却,影响回流液的回收。
通过检修和更新恢复使用冷却器的效能。
尾气系统改造(F11)原氮氧化物(NOx)尾气吸收塔为塑料材质,易老化和泄漏,吸收率低,采取了改塑料材质的塔为不锈钢材质。
增加高效填料和冷却器,提高吸收效率。
实施替代方案的经济性(见表3)
表3 实施替代方案的经济性分析(万元)
方案类型
序号
投资
收益
运行成本
净收益
投资回收期(年)
低费
F9
2.6
52.92
0.02
52.9
0.05
低费
F10
20.84
9.91
4.87
5.04
4.13
中费
F11
55
47.77
25.04
22.73
2.42
合计
78.44
110.6
29.93
80.67
1.37
实施替代方案的环境效益(见表4)
表4 实施替代方案的环境分析
替代方案
非产品回收
环境效益
氧化终点控制(F9)
年回收己二酸3.25吨
年减少COD排放4吨
浓缩回流液回收(F10)
年回收回流液1300m3,硝酸56吨
年减少COD排放81吨
硝酸尾气回收(F11)
年回收硝酸340吨
年减少NOx排放240吨
2.2氯化苯产品“审计”及效果
氯化苯生产工艺采用苯直接通氯气,在氯化铁催化下生成氯化苯的连续生产工艺。
该装置分为:
收送料、苯干燥、氯化、水洗中和、粗馏、精馏、包装、尾气吸收、多氯化物工序。
其生产工艺见流程图2。
图2氯化苯生产重点工艺流程图
该企业在完成了己二酸生产工艺“审计”,基础上于1995年开展了对氯化苯生产工艺的清洁生产审计,通过“审计”提出了12项替代方案。
其中无费方案4项,低费、中费和高费分别为2项、3项和3项。
2.2.1不同替代方案的名称及改进措施(见表5)
表5氯化苯生产工艺替代方案名称及改进措施
方案
方案名称及问题
改进措施
类型
序号
无费方案
F1
氯化尾气冷却器,冷却效果差
改并联喷淋为串联喷淋
F2
尾气捕集器,废水直排
由直排为回收利用
F3
苯干燥废水直排
由直排为回收利用
F4
粗馏冷却器尾气放空
由放空为回收利用
低费方
案
F5
氯化冷却器改造
改卧式冷却器为立式冷却器
F6
碱洗下水改造
增1台氯化分离罐,改一级分离为二级分离
中费方案
F7
水洗下水改造
回收水洗下水用于氯化尾气吸收,加水制盐酸
F8
多氯化物改
增加多氯化物分离塔的塔高和塔板数
F9
工艺改造
更新粗馏、精馏加热器
高费方案
F10
尾气搬迁(含工艺改进)
调整工序局部改尾气两级为三级吸收
F11
冷却水循环利用
新增一座小时400吨水冷却塔
F12
生产改造
扩大生产能力
该企业对提出的12项替代方案,按照先易后难,边审计边改进的原则,结合企业资金、技术实际,通过严格生产管理,加强对设备维修、维护,结合技术改造,分批分期的实施了替代方案。
2.2.2实施替代方案的效果,包括经济效益和环境效益。
1.实施无费方案的效果(见表6)
表6实施无费方案的经济效益
氯化尾气冷却器(F1)
实施无费方案(F1?
/FONT>F4),吨氯化苯产品消耗苯定额降低28.3公斤,以年产15000吨氯化苯计,年节约苯424.5吨,按吨苯2000元计,年节约苯价值为84.90万元
尾气捕集器(F2)
苯干燥工序(F3)
粗馏冷却器(F4)
2.实施替代方案工艺简述
氯化冷却器改造原氯化冷却器采用的卧式冷却器其冷却效果差,难以满足生产工艺要求,后利用原冷却器改卧式为立式,改善了冷却效果,减少了氯化尾气中苯排放,提高了苯的转化率。
测试结果表明,使单位产品氯化苯的苯和氯化苯分别减少了8.36公斤和0.39公斤。
按1998年氯化苯产量15000吨计算,年节约苯125.4吨,节约氯化苯5.85吨。
按吨苯价值2000元,吨氯化苯2700元计,年节约价值分别为25.08万元和1.58万元,合计为26.66万元。
碱洗下水工序改造氯化液经水洗除去部分氯化氢,剩余氯化氢需用碱中和,并经分离回收苯后的废液排入下水。
由于原有装置为一级分离,加上设备、工艺落后,操作等原因,使氯化液和碱洗分离不完全,致使下水含苯达68g/L,氯化苯达26g/L。
为了降低苯的消耗,减轻对环境的污染,投资了6.3万元,改一级分离为两级分离,提高了分离效果,吨氯化苯产品苯消耗降低了20公斤,以年生产氯化苯15000吨计,约节约苯3000吨,按吨苯2000元计,节约价值60万元,扣除年运行成本1.75万元,净收益58.25万元。
下水每升含苯由68克降到0.78克,下降了90%以上。
水洗下水工序改造水洗中和工序加入一定量的水,将氯化液中的氯化氢洗去后排入下水,它是氯化苯生产中一股主要酸性废水。
为了利用酸性水制取盐酸,投资了14.7万元,对水洗下水工序进行了改造,采用了闭路循环工艺,将水洗下水(含8~10%HCl)打入氯化气吸收工序,用于副产盐酸的吸收液,年制取27%的副产盐酸2500吨左右,按吨盐酸200元,计其年经济效益为50万元左右,扣除年运行成本约10万元,净收益40万元左右。
每年减少排入水环境中含酸废水1.8万吨,减少排入大气环境中氯化氢900多吨,减轻了对环境的污染。
多氯化物改造及真空泵下水回收由于原有蒸馏是真空蒸馏,靠水环真空泵提供真空,蒸馏塔塔板较低,使塔的生产工艺无法按要求操作,影响了分离效果。
为了提高分离效果,投资了30.7万元,增加了塔的高度和塔板数。
实施该方案后,1998年与1994年相比,每天苯的排放量由19.5公斤降到0.6公斤,年节约7.2吨,氯化苯由每天30公斤降到4.2公斤,年节约氯化苯9.29吨,以吨苯和氯化苯价值2000元和2700元计,年节约价值分别为1.44万元和2.51万元,合计约4万元。
其环境效益表7。
表7真空泵排水污染物变化
年份
苯
氯化苯
流量
Mg/L
Kg/d
Mg/L
Kg/d
M3/hr
1994
1300
19.5
2000
30.0
2.5
1998
50
0.6
350
4.2
2.0
减少率(%)
96.15
18.90
82.5
86.0
20
由此看出,实施该项替代方案,重要是环境效益,而经济效益不太明显。
尾气搬迁(含工艺改进)尾气系统指氯化反应的气相经冷却,喷淋吸收后的部分,直到产生合格的副产盐酸。
由于气相主要成分是氯化氢,属强腐蚀性介质,原该工序与氯化苯生产系统在同一厂房内,它不仅对员工操作岗位带来影响,而且对设备产生严重腐蚀。
为了使尾气与氯化苯分开,1997年投资了87.96万元,对尾气工序进行了搬迁,异地改造,将尾气系统搬到合成盐酸厂房,同时改进了工艺,改两级吸收为三级吸收。
实施替代方案后不仅节约了原料,而且污染物大幅度下降,见表8。
表8副产盐酸尾气污染物变化
项目
1994年
1998年
增减(±)%
环境标准
流量(Nm3/hr)
30
60
+100
氯化氢
Mg/Nm3
32000
140
-99.56
150
Kg/hr
0.96
0.009
-99.06
1.7
氯气
Mg/Nm3
15000
50
-99.67
85
Kg/hr
0.45
0.003
-99.33
1.0
苯
Mg/Nm3
1700000
45000
-97.35
17
Kg/hr
51.00
2.70
-94.71
3.3
氯化苯
Mg/Nm3
120000
750
-99.38
85
Kg/hr
3.6
0.045
-98.75
2.9
由表看出,1998年与1994年相比氯化氢、氯气、苯、氯化苯四项有害物,均减少90%以上,除苯和氯化苯外(尚无国家标准),均符合国家现定的排放标准。
以年运行330天计,年减少苯排放为382.54吨,年减少氯化苯排放量28.16吨,按吨苯和氯化苯价值分别为2000元和2700元计,年节约价值76.51万元和7.6万元,合计84.11万元。
冷却水循环利用为了节约用水,降低生产成本,投资了87.7万元。
新建了一座小时400立方米冷却水系统,循环水用于各种换热器及其它工艺上,以减少新鲜水用量,使新鲜水用量由1994年的吨产品73.3吨下降到1998年的5.5吨,吨产品节约新鲜水67.8吨,按年生产氯化苯产品15000吨计,年节约新鲜水101.7吨,按吨新鲜水1.6元计,年节约水价值为162.72万元,扣除年运行成本32.3万元,年净效益为130.42元。
工艺改造为了扩大生产能力,降低生产成本需对生产工艺关键设备即更新粗馏,精馏加热器。
为此,1997年投资22.13万元,进行了工艺改造。
实施该替代方案后,不仅提高了生产能力,而且吨氯化苯生产成本由3380元降到3330元,吨产品节约蒸汽200公斤,其污染物排放维持在原水平上,按吨氯化苯2700元和吨蒸汽按47元计,年节约生产成本为75万元,年节约蒸汽价值14万元,合计经济价值89万元。
生产改造为了进一步提高产量,在前期工艺改造基础上,1998年投资334万元,通过增加设备,提高设备利用率来提高产量,该方案实施后,在不增加污染物排放量的情况下,氯化苯产量由原来不足10000吨增加到目前的15000吨。
3.实施替代方案的效果
氯化苯生产工艺,通过实施清洁生产审计提出的替代方案(F5?
/FONT>F11)取得了明显的经济效益和环境效益,见表9?
/FONT>10。
表9 实施不同替代方案经济性分析(万元)
方案类型及名称
投资
收益
运行成本
净收益
投资偿还期(年)
低费方案
氯化冷却器改造(F5)
3.00
26.6
26.6
0.11
碱洗下水改造(F6)
6.30
60
1.75
58.25
0.10
中费方案
水洗下水改造(F7)
14.70
50.0
10.00
40.0
0.35
多氯化物改造(F8)
30.70
4.0
4.0
7.70
工艺改造(F9)
22.13
89.0
89.0
0.35
高费方案
尾气搬迁(F10)
87.96
84.11
84.11
1.05
冷却水循环(F11)
87.70
162.72
32.30
130.42
0.67
合计
252.49
476.43
44.05
432.38
0.62
由表看出:
实施7项替代方案的项目工程投资为252.49万元,年净收益为432.38万元,投资回收期不到一年。
表10 实施替代方案的环境效益
废物类型
有害物质名称
排放量(吨)
废水排放量
其中:
349000
氯化氢
900
苯
47.94
氯化苯
43.41
尾气排放
其中:
氯化氢
6.85
氯气
3.22
苯
347.76
氯化苯
25.6
由此可见,实施替代方案后年减少废水34.9万吨,废水和尾气中氯化氢906.85吨,395.72吨,氯化69.01吨,氯气3.22吨。
4.实施清洁生产成功经验
太原太化集团公司化工厂自参加国家首批清洁生产培训以来,进行了不间断地清洁生产,各级领导清洁生产意识不断得到增强,克服了资金和技术方面的困难,分批分期实施了己二酸和氯化苯生产工艺审计提出的替代方案,取得了明显的经济效益和环境效益,积累了进行清洁生产的经验,增强了持续深入开展清洁生产的信心,其成功经验表现在:
1.培育了清洁生产意识该企业1994年7月首次开展对己二酸生产工艺清洁生产审计,年底完成了“审计”报告,通过“审计”及实施无费、低费方案取得的效果,使企业领导认识到:
生产工艺中存在很多“降耗,节能,减污”的机会,实施清洁生产对降低消耗,增加收益,减轻污染有着重要的意义,树立了开展清洁生产的信心,在完成己二酸产品“审计”后,1995年初相继对氯化苯生产工艺进行了“审计”,当年提出了“审计”报告,目前已起步对烧碱,乙烯两个产品进行清洁生产审计,做到“审计”工作不间断的进行。
2.克服了资金技术障碍就全国企业实施清洁生产情况来看,资金和技术尤其资金短缺,是影响实施清洁生产普遍存在的关键障碍,该企业不消极地等待外部条件,而着眼自身努力,寻求多种途径克服资金和技术的困难:
按照先易后难的原则,优先实施无费、低费或中费方案获取的收益,来弥补实施高费方案的资金短缺;
依靠企业技术人员和员工的努力,完成替代方案中设备改进或制造及安装任务,节省工程投资;
把清洁生产替代方案,纳入到企业设备检修或生产工艺技术改造中一并解决;
带着实施清洁生产中的技术难点,到同行业中调查和收集先进技术、信息,克服实施清洁生产中的技术障碍。
截止1998年,分期分批完成了己二酸和氯化苯两个产品清洁生产审计提出的24项替代方案。
3.巩固清洁生产成果
为了巩固清洁生产成果,该企业针对清洁生产审计发现生产管理中存在的缺陷,调整了环保机构,完善健全了环保、生产管理制度。
调整环保机构在传统的尾端治理污染的模式下,该企业设了独立环保处,主要负责企业排污口的污染物是否符合国家或地方规定的污染物排放标准,忽视了生产工艺过程中原料消耗,污染物产生量,致使环保与生产相脱节。
实施清洁生产后,为了在生产工艺过程中控制污染物的产生,调整了原单设的环保处为生产环保处,环保管理不仅监督尾端污染物排放情况,更重要的是把环保管理内容渗透到生产管理之中,互为补充,相互促进,求得了环保与生产内在统一。
完善健全了管理制度针对清洁生产审计发现的生产工艺中跑、冒、漏及物料流失等问题,完善了设备完好率,运转率和定期检修制度以及修定了原料消耗定额等规章,并将每个员工工作优劣与奖金、工资挂钩,实行守章者有奖,违章者受罚,按月评定,奖惩兑现。
运用行政管理制度和经济鼓励相结合的手段,增强了员工的工作责任感和学习技术的积极性,它对巩固清洁生产成果起有重要的作用。
设立环保、生产“监理员”为了“管理”制度持续地有效实行,该企业建立了“监理员”制度。
机构编制每班三人,其中监理人员两人,监测人员一人,每天三班24小时实行现场监督和环保监测。
“监理员”职责范围和检查内容:
范围:
涉及生产所有单位的监督管理。
内容:
包括生产操作控制指标执行情况及查阅原始记录;环保装置运行价查;非正常排放管理,“三废”排放抽查。
以上每项均有具体价查考核标准。
“监理员”权限“监理员”对现场监督检查发现的问题有权下发限期整改通知单,对生产现场出现的一些属设备管线问题,通知分厂立即抢修,维护,跟踪复查落实,对限期不整改的进行处罚,直接下发经济处罚单。
对属人为造成的问题,直接下发经济处罚单。