第六章其它含硫原料制造硫酸.docx
《第六章其它含硫原料制造硫酸.docx》由会员分享,可在线阅读,更多相关《第六章其它含硫原料制造硫酸.docx(25页珍藏版)》请在冰豆网上搜索。
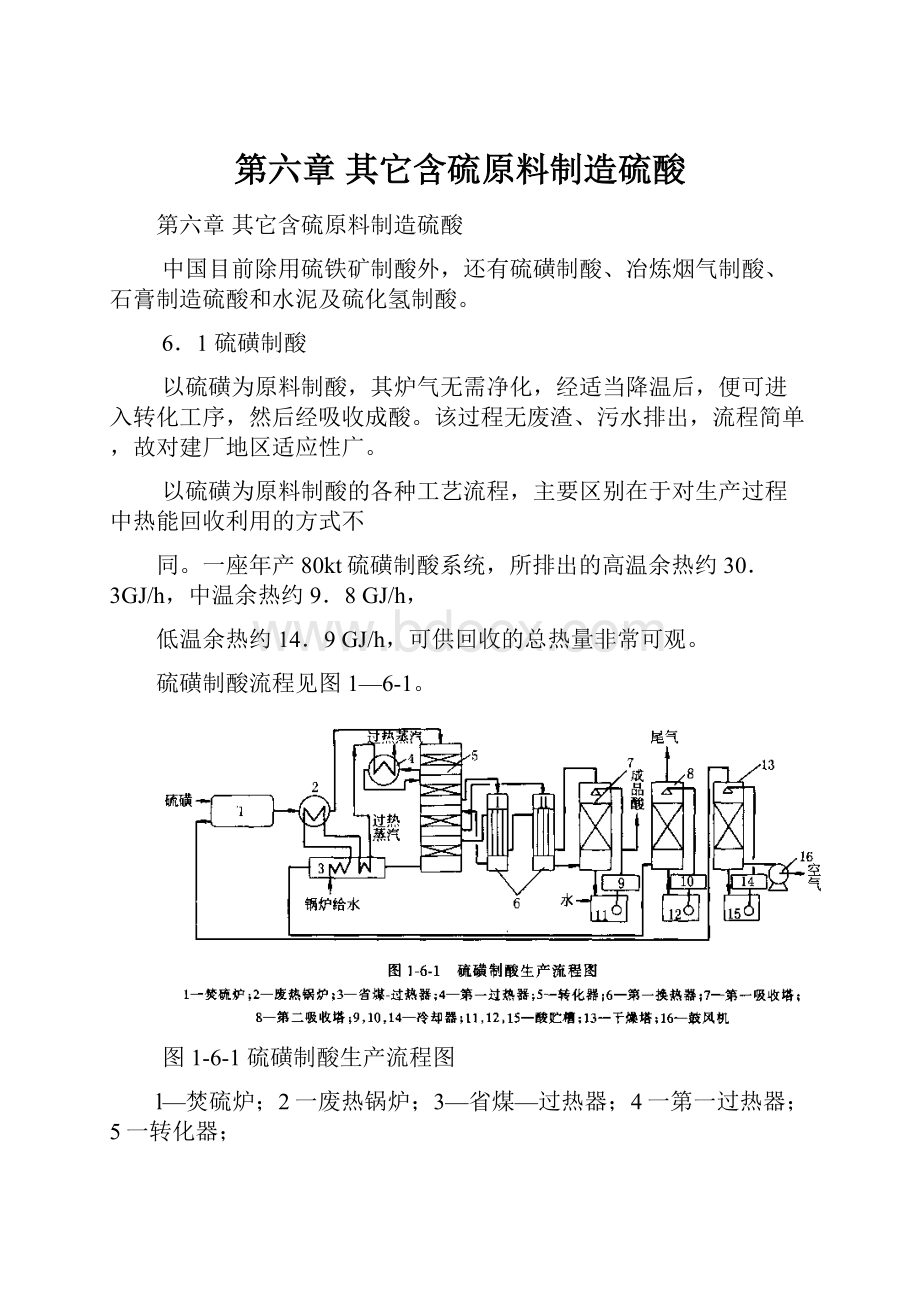
第六章其它含硫原料制造硫酸
第六章其它含硫原料制造硫酸
中国目前除用硫铁矿制酸外,还有硫磺制酸、冶炼烟气制酸、石膏制造硫酸和水泥及硫化氢制酸。
6.1硫磺制酸
以硫磺为原料制酸,其炉气无需净化,经适当降温后,便可进入转化工序,然后经吸收成酸。
该过程无废渣、污水排出,流程简单,故对建厂地区适应性广。
以硫磺为原料制酸的各种工艺流程,主要区别在于对生产过程中热能回收利用的方式不
同。
一座年产80kt硫磺制酸系统,所排出的高温余热约30.3GJ/h,中温余热约9.8GJ/h,
低温余热约14.9GJ/h,可供回收的总热量非常可观。
硫磺制酸流程见图1—6-1。
图1-6-1硫磺制酸生产流程图
l—焚硫炉;2一废热锅炉;3—省煤—过热器;4一第一过热器;5一转化器;
6一第一换热器;7一第一吸收塔;8—第二吸收塔;9,10,14—冷却器;
12,15一酸贮槽;13一干燥塔;16一鼓风机
空气经鼓风机加压后送入干燥塔,用浓硫酸干燥。
干燥空气在焚硫炉内与喷入的液体硫磺反应,生成二氧化硫气体。
高温二氧化硫气直接进入废热锅炉,气温降到适合于进转化器温度,进入转化器。
转化采用3+1式两次转化工艺。
一次转化时.转化气分别通过一段床、第一过热器、二段床、第一换热器I、三段床、第一换热器Ⅱ,再进入中间吸收塔。
经过一次吸收后的转化气再次通过第一换热器I(壳程)、第一换热器Ⅱ(壳程).再进入转化器四段,进行第二次转化。
从转化器四段出来的气体.在过热—省煤器冷却,然后进入第二吸收塔,用浓硫酸将第二次生成的三氧化硫吸收,然后通过烟囱排入大气。
国外硫磺制酸工艺近十几年来有很大发展,生产规模日趋大型化,不断采用新技术和新设备,制酸过程的自动化水平大大提高。
日产1800t(以l00%H2SO4计)、0.2MPa的硫磺制酸布劳德(BMwder)流程见图l-6-2。
据文献报道,布劳德硫磺制酸工艺经济技术指标令人满意。
如转化率可达99.96%,排放尾气中SO2含量<50ml/m3,投资为现有两次转化两次吸收同等生产规模厂的88%。
布劳德制酸工艺的最大特点是能回收系统近于全部能量的装置。
能量回收利用流程见图1-6-3。
图162布劳德硫磺制酸流程
全系统高、中、低位热能回收后可发电6200kW。
此发电装置由两个透平驱动,一个为过热蒸汽;另一个为过热丙烷(或其它低沸点工作介质)。
6,2冶炼烟气制酸
有色金属矿多以硫化物形态存在.在冶炼过程中有SO2烟气产生。
因此,冶炼烟气亦一种制酸原料。
从冶炼烟气的数量多少及其能否直接用以制造硫酸等多方面考虑.最理想的气源是炼铜和炼锌烟气。
由于冶炼设备和操作技术水平所限,过去冶炼烟气的气量和浓度波动很大,而且SO2浓度低、成分复杂。
近年来,国内外对冶炼技术和设备进行了较大改进,如冶炼过程采用富氧密闭操作,或新型冶炼设备,如采用闪速熔炉、氧气顶吹转炉以及湿法冶金技术等。
其结果是烟气中SO2浓度得到提高,能很好地适应烟气制酸的要求。
—般地,冶炼烟气中的杂质可分为灰尘、烟雾和挥发性金属三种。
如果这些杂质去除得不彻底,不仅直接影响成品酸的质量.还会堵塞电除雾器,污染催化剂,并加速管道、设备的腐蚀。
因此,利用冶炼烟气制酸同硫铁矿炉气制酸具有相似的工序,即净化、干燥、转化、吸收,而且所用工艺和设备亦基本相同。
由于这个原因,国外将冶炼烟气制酸及硫铁矿制酸统称为冶金型制酸。
但是,由于冶炼烟气含有的有害杂质种类及含量与硫铁矿烟气的不完全相同,特别是挥发性金属及含尘量差别较大,因此在净化工序的工艺及设备稍有不同。
不同点主要是清除挥发性金属。
所采用的方法主要为稀酸洗涤,例如多塔洗涤工艺和动力波洗涤工艺。
此外,瑞典玻立登公司湿法除砷工艺和氯化法除汞技术等均适应于冶炼烟气制酸的特殊要求。
6.3H2S湿法催化氧化制造硫酸
在各种可燃气体(焦炉气、发生炉煤气、石油炼厂气及油田气和天然气)中含有数量可观的H2S.在使用过程中必须脱除。
脱除H2S方法不同,可得到硫磺、硫化氢或其它硫化物。
以H2S为原料生产硫酸的方法:
燃烧硫化氢气得湿SO2炉气,用湿法催化氧化,冷凝成酸。
国外生产厂的实践说明,从工程投资,生产成本,以及各项经济指标来看,它是有发展前途的。
硫化氢的燃烧反应如下
H2S十1.5O2=SO2十H2O
ΔH298⊙=518.86kJ/mol
硫化氢在氧气中的最低着火温度为220℃;在空气中的最低着火温度为292℃;燃烧产物是SO2和水蒸气,同时还有一定量的一氧化硫(SO)中间产物
H2S十O2=H2O+SO
SO随即氧化成SO2,当氧不足时,SO分解成SO2及硫磺蒸气。
用空气燃烧H2S过程中生成SO3极少(0.1%以下)。
在生产条件下,从燃烧设备出来的气体冷却时,由于金属设备的壁面能起到一定的催化氧化作用,使SO3含量有所增加。
还要指出的是H2S与空气的混合物的爆炸极限范围,下限为4.3%一5.9%,上限为19%一45.5%,随火焰延伸方向不同而异。
典型的鲁奇康开持(Concat)法H2S制酸流程见图l—6—4。
从图1—6、4可见,含硫化氢的尾气在焚烧炉中用轻油或燃料气焚烧。
焚烧炉是康开特法的重要设备。
转化器进口温度(约440一500℃)和适宜的SO2/O2比率通过比例调节来控制。
转化器内填充钒催化剂,在焚烧炉中未燃尽的少量H2S、COS、CS2和硫蒸气在一段转化器中完全氧化成SO2。
一段转化器出口气体通过空气冷激降到约420℃,经二段转化器后形成的湿SO3气体在约420℃以下直接进入热冷凝文丘里器,当气体与高度分散的酸顺流接触时,大部分硫酸从气相中冷凝下来。
气体所携带的热量和冷凝热通过与浓循环酸接触直接除去。
气体在进入冷凝塔前,通过与冷空气混合而直接冷却,同时降低了气体中硫酸蒸气的分压。
冷凝塔中通过喷淋稀硫酸,气体进一步冷却,残余硫酸蒸气从气相中冷凝下来,最后通过纤维过滤器除去残余的酸雾后放空。
在过滤器得到的稀硫酸输送到冷凝塔的循环酸槽中,循环酸的浓度用补入水维持不变。
康开特法流程的特点:
A.脱硫率高。
燃烧时未氧化的H2S、COS、CS2和硫蒸气都在钒催化剂上完全氧化,尾气中SO2<200m1/m3,SO3可以降到100mg/m3,总脱硫率大于99.5%。
B.投资省。
与其它尾气脱硫工艺相比,本工艺约为克劳斯脱硫装置投资的30%。
C.能耗低。
除风机和循环泵需电力外,不用其它动力设备,冷却水消耗量少。
D.产品质量可靠。
产品为78%的H2SO4或93%H2SO4的硫酸.不产生废物和副产物。
中国山西化肥厂已建成康开持法回收处理H2S制酸装置,流程见图1-6-5。
图1-6-5康开特法的生产流程图
1-燃烧炉;2-锅炉;3一换热器;4一转化器;5-文丘里冷凝器;
6,8—循环酸槽;7一冷凝塔;9一丝网除沫器;10-纤维除沫器;11-烟囱
6.4石育制造硫酸和水泥
中国的石膏蕴藏量很丰富,且分布广泛,加之高效磷肥生产时副产大量磷石膏,因此中国硫酸生产以石膏为原料并联产水泥,是综合利用资源的可行方法之一。
天然石膏有两种形态:
一种是无水石膏(CaSO4),理论含硫量为23.53%;另一种是二水石膏(CaSO4•2H2O)。
二水石膏用于制酸时.必须经过煅烧脱水变成半水石膏(中国目前生产用)或无水石膏。
硫酸钙受热可直接分解,反应如下。
CaSO4=CaO十SO2十1/2O2
由于硫酸钙存在各种不同结构形式,故其直接分解温度范围较大。
一般认为1200℃开始分解,直至1400℃左右分解完全。
如果用在高温下以碳还原的方法,可以降低反应温度。
还原反应按下式进行。
2CaSO4十C=2CaO十2SO2十CO2-566.2kJ(1—6—4)
显然,碳既作为还原剂,也有一部分燃烧用于供给反应所需热量。
各种含碳原料对CaSO4的分解有着不同的影响,其中以焦炭最为理想。
另外,在燃烧时亦可加入某些矿物质如氧化铁、氧化硅及高岭土(A12O3·2SiO2)等,其作用可与CaSO4形成低熔点化合物,加速CaSO4的分解.加入的矿物质和CaSO4的分解产物CaO只要有适当的配比,便可形成硅酸盐水泥熟料,并同时制得SO2气体。
每生产1t硫酸,副产水泥熟料lt;约消耗0.4t燃料煤,焦炭0.15t左右,硬石膏1.5~1.7t,以及适量粘土、硅砂。
如炉料中氧化铁含量不足时,可酌量加入硫铁矿或其烧渣,前者可使炉气中SO2含量提高,且可减少燃料。
如使用含煤硫铁矿时,效果更好。
上述生产方法所得窑炉气温度为500~600℃,成分为
SO28%~9%CO0.1~0.5%
O20.3%~0.5%NO0.005~0.03%
CO221%~22%H2S0.001~0.0035
其余为氮气。
窑炉气中尚有3%~12%矿尘状炉料被带出窑外,矿尘状炉料经旋风分离器和殿除尘器予以清除,炉气送制酸系统。
磷石膏制酸的工艺流程与以硫铁矿为原料制酸的传统流程没有多大区别。
石膏分解时所生成的SO3比焙烧硫铁矿少得多,且炉气中没有砷、氟、硒和其它有害杂质,因此湿法净化工序只需设两个洗涤塔和一个电除雾装置已足够稳妥。
因窑炉气严重缺氧,要在干燥塔前适当补入空气使炉气在进入转化系统之前O2/SO2〉1.1。
磷石膏制SO2炉气和水泥熟料的生产流程如图l—6—6所示。
石膏制造硫酸,由于炉气SO2浓度较低,故在相同产量下,净化、转化、干吸工序的设备要比普通采用标准浓度炉气的要大,其中转化系统的热交换面积也要大些。
但在流程设计和设备结构上,一般与硫铁矿为原料制酸相同。
此外,石膏制酸还有两个重要的特点:
A.由于窑气中含有氮的氧化物,所以成品酸个含有N2O30.001%~0.03%,使酸的用途受到一定限制;B窑气中还含有碳氢化台物和氢,这些物质在催化反应器中氧化生成水,在SO3吸收过程中会产生酸雾。
这两个问题应予以注意。
石膏制酸技术的发展方向是采用流化床分解石膏,这一技术将较大地降低能耗。
6.5不同原料制硫酸的评比
如上所述,国内外生产硫酸采用的原料有硫铁矿(包括有色金属硫化物矿、浮选尾砂)、冶炼烟气、硫磺、石膏以及硫化氢等。
由于原料不同工厂布局、生产流程及综合利用都各有其特点,如表1—6—1所示。
根据表l—6—l所列原料与生产过程的关系,结合各国硫资源条件、技术水平以及对环境保护要求的差异,目前世界各国生产硫酸所用原料路线有很大不同,各种含硫原料所占的比例仍在不断地改变中。
总的趋势是硫磺制酸增加.硫铁矿制酸的比重下降,冶炼烟气也已成为制酸的主要原料之一。
中国由于天然硫资源比较缺乏,回收硫磺又少,近年国际硫磺价格较平稳,进口硫磺生产硫酸的量有所增加。
硫磺制酸有投资少、流程简单,易于自控、无污染等优点,有条件时应大力发展。
硫铁矿和有色金属硫化物矿制酸,有成熟的生产技术经验,今后在提高硫铁矿品位的基础上,辅以烧渣炼铁,在相当长的时间内,生产硫酸仍然会以硫铁矿为主。
结合有色金属工业的发展,为了保护环境,不使SO2污染大气.充分利用硫资源,有色金属硫化矿与冶炼烟气制酸必须发展。
石膏(包括磷石膏)为原料生产硫酸与水泥,有些国家虽已淘汰,但中国天然石膏贮量丰富.而且在发展高效肥料的同时,充分利用磷石膏生产硫酸和水泥是一有效途径。
随着石油工业的发展,将合成气脱硫所得硫化氢,直接用于制取硫酸,对综合利用、保护环境、防止污染都是有益的。
第七章三废治理与综台利用
随着工业生产规模的扩大和人们物质消费水平的提高,也带来了严重的环境污染问题。
环境污染问题已成为困扰人类最严峻的四大问题之一,它直接关系到人类的生存与发展。
中国的环境状况不容乐观。
为此,中国80年代初开始逐步加大了治理污染源的力度,并先后制订了有关行业的污染物排放标淮和相关法律。
1997年起,中国开始实施新的污染物排放标准,使中国治理污染、保护环境走上了发展的快车道。
硫酸生产过程排放的污染物主要有含SO2、SO3(酸雾)的尾气,固体烧渣和酸泥,有毒性废液、废水等。
这些物质的排放情况,与硫酸生产所用原料、工艺流程、设备选型以及管理水平、操作水平等密切相关。
以硫磺、硫化氢为原料,生产过程的污染物主要是尾气中的SO2和酸雾,基本不存在废渣和废液的污染问题。
以硫铁矿为制酸原料,特别是含硫20%一30%的中低品位矿,不仅排放大量含有害物的尾气、废水,而且还要排放大量废渣。
以冶炼烟气、石膏为原料,制酸过程亦遇到废气、废水、废渣的处理问题。
对三废的处理有两个意义:
A减轻对环境的污染,保护人类生存环境;B充分回收利用三废中各种有用成分,使三废资源化。
实践证明,对三废进行处理不但可减少对环境的污染,而且还有它的经济意义。
近年来,一些新建的先进制酸装置不仅合理利用了原料中的各种有用资源,而且亦达到了有害物排放标准,使硫酸生产逐渐成为无污染的工业部门。
7.1尾气中有害物的处理和利用
经转化—吸收系统出来的气体,除含有大量无害的N2、O2外,还含有有害的SO2、SO3。
一转一吸流程排出的尾气,含SO20.2%~0.3%,含酸雾45mg/m3;两转两吸流程排出的尾气,含SO20.04%~0.05%,操作较好的可低于0.03%,酸雾含量与一转一吸相近。
因此,减少用气中有害物的排放很有必要。
采用一转一吸流程,排放的尾气一般都要经过处理后才可放空;采用两转两吸流程,如操作正常,转化率可达到99.70%以上,尾气可以不经处理直接放空,能够达到目前的排放标准。
因此,越来越多的制酸装置,特别是新建的装置都采用了该流程。
在国外,由于排放标准日趋严格,有的工厂将两转两吸系统排出的尾气再经过卫生塔和尾气电除雾器,进一步除去SO2和酸雾。
尾气中SO2的处理与含低浓度SO2烟气的处理方法基本相同,方法甚多,各具特色,概括起来有以下三个途径:
A.建筑高烟囱,使尾气扩散稀释,在到达地面时达到安全浓度;B.尾气脱硫,在尾气排放前,将硫含量降低到排放标准;c通过改进工艺,减少尾气中硫含量。
第一种途径较为简便,但有两大缺点,一是造价太高,二是没有从根本上解决二氧化硫对大气的污染,现行标准也不允许。
第二种途径是国内外研究得最多、也是比较积极的、应用较为普遍的途径。
该途径的方法很多,一般采用吸收剂或吸附剂将SO2与尾气分离,所吸收的SO2重新被利用,但因尾气中SO2含量低(<0.5%)、气量大,已属于工业应用不经济范围。
第三种途径可以从根本上解决制酸尾气对大气污染的问题,目前广泛采用的两转两吸流程就属于该途径。
从实质上讲,第二种与第三种途径皆可解决SO2的污染问题,并能将硫资源加以利用,而且,它们均在提高硫的利用率的同时增加投资、付出额外的运行费。
它们的区别仅在于,后者的设备是制酸装置整体的一部分,而前者是在制酸装置上附加的一部分。
就目前的技术状况,采用两转两吸流程,可使尾气中SO2达到目前的排放标准,且其投资少于现有的各种尾气脱硫技术,运行费用办相对较低,所以在世界范围内得到了普通应用。
国外大多采用两转两吸流程。
在中国,新建和在建装置均为两转两吸流程,很多早建的一转一吸装置除已建有尾气回收装置的外,近几年已逐步改为两转两吸,但是,由于历史原因及人们对环保认识不足,个别小型装置仍未对尾气进行处理。
这是不允许的,应予重视。
因尾气排放的标准日趋严格,采用两转两吸流程的装置对SO2转化率和SO3吸收率仍有必要采取措施加以提高。
主要从工艺设计和设备的改进着手。
尾气脱硫技术是一个重要的解决尾气污染的方法,特别是在排放标准日趋严格的今天,仍有其存在和发展的意义。
此外,该类技术还对其它行业含硫废气的治理也可资借鉴。
尾气脱硫技术分为湿法、干法两类。
湿法就是采用液体吸收剂与尾气接触并将SO2与尾气分离的方法。
干法就是采用固体吸收剂(或吸附剂)与尾气接触并将SO2与尾气分离的方法。
在目前,湿法技术成熟、脱硫率高,应用较为广泛,但处理后的尾气温度低、湿度大,有“白雾”二次污染产生,而且流程较长。
因此、干法脱硫技术的研究和开发受到重视。
湿法脱硫主要有以下几类:
氨法、碱法、金属氧化物法等。
氨法是指用氨水或铵盐溶液吸收SO2方法。
这一大类方法在吸收过程中,都以亚硫酸铵—亚硫酸氢铵为吸收液,如氨—酸法、碳酸氢氨—亚硫酸铵法等。
运行时,连续引出部分吸收液进行处理。
随着处理方法不同,所获得的产品不同,因而又分为多种。
其中应用最广泛的是氨—酸法。
碱法是指采用碱液吸收尾气中SO2的方法。
该法可以免除氨法中尾气含氨和夹带雾沫的缺陷。
常用的碱吸收液有碳酸钠、氢氧化镁溶液和石灰乳等。
其中,石灰乳吸收法的突出优点是石灰来源广泛、价格低廉、投资和操作费用都较低,日、美、英等国普通用来处理烟道气中SO2气体。
金属氧化物法即采用金属氧化物形成的碱性溶液吸收尾气中SO2的方法。
例如:
氧化镁溶液、氧化锌溶液是常用的吸收液。
该种方法的脱硫率高,所得硫产品的应用范围较广,因而得到较广泛应用。
此外,还有有机物作吸收剂的方法,如柠檬酸钠法、MN法(以密胺浆液为吸收剂)等。
这些方法亦得到了一定范围的应用。
干法脱硫主要有活性炭法、金属氧化物干式脱硫法,以及近年新开发成功的电子束照射法,等等。
活性炭法在国外已有工业装置,在国内也有了工业示范装置。
该种方法由于活性炭的活化方法及再生方法不同又分为几种类型。
中国开发的“PAFP”法即属活性炭法,该法在活性炭再生时得到浓度约30%稀硫酸,该稀酸进一步与磷矿作用制得约10%磷酸,然后用氨水中和,最终制得磷铵复肥。
工业性装置的实验证明.该法具有良好的推广应用价值。
7.2烧渣的综合利用L6?
j
用硫铁矿制酸,只是利用了原料矿中的硫资源。
据统计,硫的价值仅占伴生矿工业价值
的40%一50%,其它元素的价值约占50%左右。
如果仅仅利用矿石中的元素硫,其余元素
不加回收而抛弃,不仅浪费资源,而且,由于烧按量大(1t酸排演员为700一800k8),长期堆放,占用地面,污染环境而成为公害。
中国制酸原料以硫铁矿为主,且多为含硫20%一35%的中低品位矿、其中一部分是伴
生金属硫化矿尾砂。
硫铁矿中除了硫化铁(Fe52)外.尚含一定量的cu、zn、Pb、co等有
色金属及少量的Au、A8,在矿石烙烧时,与氧化铁一起以烧渣形式排出。
因此,烧渣的综
合利用对以硫铁矿为原料的制酸厂消除污染有重要意义,而且对渣的价值亦是一个提高。
渣的利用主要有以下几个方面。
7.2.1铁资源的回收利用
(1)作为高炉炼铁原料
根据高炉炼铁特性,原料含铁每增加1%,焦比降低2%,产量可提高3%.而原料中
杂质含量直接影响到生铁质量n因此,对炼铁原料中铁及杂质的含量有一定的要求和限制,
如表1—7—l所示。
表1.7—1炼铁用原料的要求
高品位硫铁矿的烧渣,其铁含量高,如果其它成分符合要求的话,可直接用作高炉炼铁
原料。
中低品位硫铁矿的烧渣中,铁含量较低,有害杂质含量较高,不符合炼铁要求,必须
进行预处理。
饶渣选矿是一种常用的预处理方法,可以利用烧渣中各种物质的不向磁性而分
离铁和杂质,称为磁选;亦可利用其相对密度不同而分离.称为重选。
具体选择,需根据矿
浚的类型和成分而定。
磁选工艺较简单,将水加入物度一定的烧酒中,搅拌成均匀矿浆,然后送入具有一
场强度的磁选机中,进行粗选和精选,选出桔矿后,剩余的为尾砂。
如果尾砂还需作一次重选,则可再送入格床或螺旋溜槽中进行选别。
为了提高铁的选出率,位烧渣中磁性铁的比例增加,可选择适当的硫铁矿焙饶工艺
是把烧渣进行磁化处理。
(2)制取三氯化铁和铁粉
用温度为40一50℃的盐酸(浓度在30%左右)加入烧渣中
三氯化铁溶液。
将溶液过滤、蒸发.并浓缩到1.6—1.7kA/m’*
以上的三氯化铁结晶。
三氯化铁可用作净水剂和防渗剂,也可用于颜料工业。
搅拌、静置,可得到液体
冷却后即可得纯度达85%
用氢气还原三氯化铁,可制得还原铁粉,它是一种重要的化工原料。
(3)制造硫酸亚铁和铁红
硫酸亚铁可作为净水剂、消毒剂,以及用作化肥、农药。
硫酸亚铁也可制造铁红粉.一
种着色力和遮盖力很强的着色剂,广泛应用于橡胶工业、建筑工业及塑料工业。
硫酸亚铁还
可用于制造电子工业中广泛应用的磁性材料。
用硫铁矿烧渣和硫酸作原料制取硫酸亚铁,再通过干法和湿法处理
粉。
其基本反应如下:
Fq03十3H2S04=Fez(S0‘)3十3H20
Fd3十HzS〔)4=FeSOL十H20
反应过程中加入铁屑,使硫酸铁还原:
Fq(5()4)?
十Fe=3FeS04(1—7—3)
生成的Fe04再加水和水蒸气溶解,除去杂质,清液中的Fe04经过结晶、干燥脱水
后,即为Fes04产品。
然后在高温(700℃左右)下假烧FeD4,得产物三氧化二铁,经研
磨即成为氧化铁红粉。
7.2.2铁和有色金属的综合回收
当硫铁矿侥渣中有色金属含量较高时,如烧渣直接用作高炉炼铁原料,将不仅影响炼铁
作业的顺利进行,而且影响生铁质量。
因此,在炼铁之前,必须对烧酒进行处理,脱除对炼
铁有害的元素。
同时回收利用侥渣中的有色金属,提高烧渣的使用价值。
提取有色金属的方法,可根据烧渣的成分及有色金属的性质决定。
氯化焙烧法综合利用
烧渣是比较成熟的方法。
选用ca(;12作为氯化剂,在一定温度下
属氯化物,达到有色金属与铁分离的目的。
氯化的主要反应是:
MeO十2CaCl2十十0h——MeCl2十2CaO十C12(1—7—4)
式中Me代表有色金属元素*
烧渣中的硫在一定温度下分解析出sQ和纵,并与cao反应形成ca94,促进了氯化
反应的进行:
CdO十Sq十十02——Ca94(1—7—5)
C8C12十Me()十S0b=Md212十CaSOL(1—7—6)
氯化钠在纵、观或水蒸气的气氛中,亦可作为氯化剂,其反应为
2Na门十S(k十0h=Na2S04十(:
12(1—7—7)
H20?
C124HCl十十r4(1—7—R)
C12十MeO——MeClz十专Oz(1—7—9)
氯化焙烧分中温氯化法和高温氯化法。
两种方法除氯化反应温度不同外,氯化产物的后
处理工艺亦有差异。
中温氯化焙烧法是将氯化剂和烧渣以一定比例混合,在430一600℃的温度下进行氯化
反应,铜锌等有色金属转化成可溶性的氯化物*留在固相烧渣中,氧化铁不被氯化。
然后用
水或稀酸把可镕性有色金属氯化物浸出并回收。
除去了有色金属的氧化铁作为炼铁原料。
高温氯化焙侥法巳建立厂大规模工业装置,其要点是:
把配有氯化钙的烧渣先制成干燥
球团.在1000一1250℃的温度下反应,使生成的有色金属氯化物挥发并进人烟气,然后采
用湿法回收烟气中的有色金属。
脱除了大部分有色金属后的烧渣球团,每个球的抗压强度可
达500kR,硫及有色金属含量均大大下降(S<o.03%,CM、Pb、2n均<0.04%),含铁品
位亦有所提高,成为一种优质的炼铁原料。
7.3.3从烧淹中提取金银
有些硫化矿来自黄金矿山的副产,经过焙烧制取了5q炉气后,烧渣中金、银等贵金
属含量又有所提高(如某厂每吨烧渣含金可达48左右),成为提取金银的宝贵原料。
提取金银等贵金属的各种方法中,最常见的是氰化法。
其基本方法如下:
硫化矿烧渣先经预处理,加入石灰研磨,用氰化钠(钾)溶液浸取,烧渣中的金银与氰
化钠形成络合物留在溶液中,浸渍渣经多级洗涤.以提高金银的浸出串,然后经过磁选提取
其中的铁作为铁精矿回收。
含有金银络合物的溶液经脱氰处理后,用金属锌粉还原置换溶液
中的金、银,使之沉淀分离.沉淀物经滤出后烘干,即为含金约5%一10%的金泥。
含有剧
毒物氰根的溶液采用碱性液氯法处理.残余的CN—经曝气分解后诽放。
干金