成型主要不良分析及对策分析.docx
《成型主要不良分析及对策分析.docx》由会员分享,可在线阅读,更多相关《成型主要不良分析及对策分析.docx(23页珍藏版)》请在冰豆网上搜索。
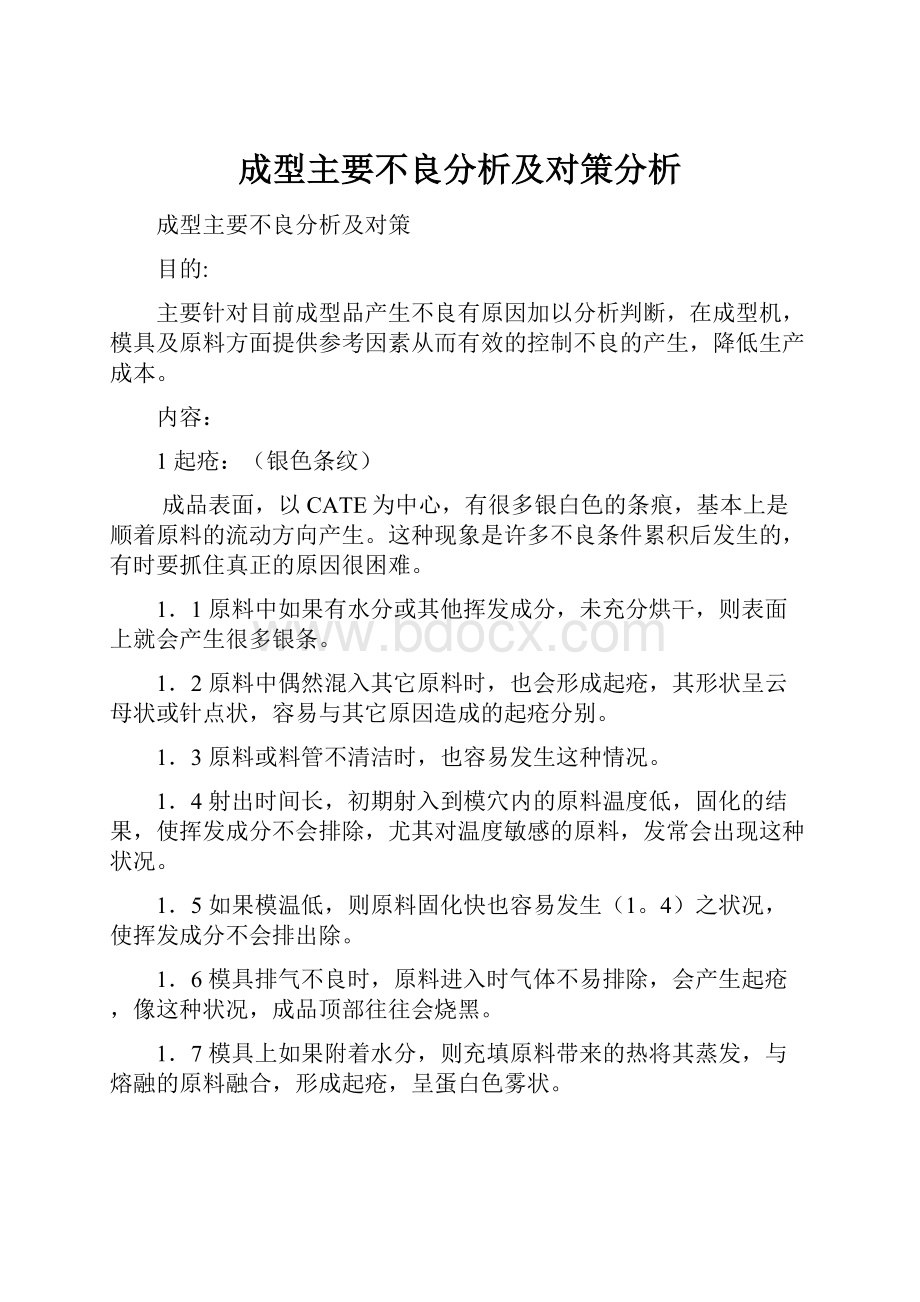
成型主要不良分析及对策分析
成型主要不良分析及对策
目的:
主要针对目前成型品产生不良有原因加以分析判断,在成型机,模具及原料方面提供参考因素从而有效的控制不良的产生,降低生产成本。
内容:
1起疮:
(银色条纹)
成品表面,以CATE为中心,有很多银白色的条痕,基本上是顺着原料的流动方向产生。
这种现象是许多不良条件累积后发生的,有时要抓住真正的原因很困难。
1.1原料中如果有水分或其他挥发成分,未充分烘干,则表面上就会产生很多银条。
1.2原料中偶然混入其它原料时,也会形成起疮,其形状呈云母状或针点状,容易与其它原因造成的起疮分别。
1.3原料或料管不清洁时,也容易发生这种情况。
1.4射出时间长,初期射入到模穴内的原料温度低,固化的结果,使挥发成分不会排除,尤其对温度敏感的原料,发常会出现这种状况。
1.5如果模温低,则原料固化快也容易发生(1。
4)之状况,使挥发成分不会排出除。
1.6模具排气不良时,原料进入时气体不易排除,会产生起疮,像这种状况,成品顶部往往会烧黑。
1.7模具上如果附着水分,则充填原料带来的热将其蒸发,与熔融的原料融合,形成起疮,呈蛋白色雾状。
1.8胶道冷料窝有冷料或者小,射出时,冷却的原料带入模穴内,一部分会迅速固化形成薄层,刚开始生产时模温低也会开成起疮。
1.9原料在充填过程中,因模穴面接触部分急冷形成薄层,又被后面的原料融化分解,形成白色或污痕状,多见於薄壳产品。
1.10充填时,原料成乱流状能,使原料流径路线延长,并受模穴内结构的影响产生磨擦加之充填速度比原料冷却速度快,GATE位置处于筋骨处或者小容易产生起疮,成品肉厚急剧化的地方也容易产生起疮。
1.11GATE以及流道小或变形,充填速度快,瞬间产生磨擦使温度急升造成原料分解。
1.12原料中含有再生料,未充分烘干,射出时分解,则产生起疮。
1.13原料在料管中停留时间久,造成部分过热分解。
1.14背压不足,卷入空气(压缩比不足)。
起疮:
表一
成
型
机
可塑化能力不足。
树脂过热分解(料管温度)
料管内原料停留久,造成部分过热。
射出压力过高。
螺杆卷入空气(背压不足)。
模
具
模具内排气不良。
模具温度低。
胶道冷料窝存储小。
GATE过小或变形。
模具表面有水分。
模穴的形状不良(横截面或壁厚变化较多较急)。
原
料
原料中由水分及挥发成分。
原料烘干不足。
混入其它原料。
2会胶线
会胶线是原料在合流处产生细小的线,由于没完全融合而产生,成品正、反面都在同一部位上出现细线,如果模具的一方温度高,则与其接触的会胶线比另一方浅。
1提高原料温度,增加射出速度则会胶线减小.
2提高模具温度,使原料在模具内的流动性增加,则原料会合时温度较高,使其会胶线减小.
3CATE的位置决定会胶线的位置,基本上会胶线的位置都进胶方向一致.
4模具中间有油或其它不易挥发成分,则它们集中在结合处融合不充分而成会胶线,
5受模具结构的影响,完全消除会胶线是不可能的,所以调机时不要约束在去除会胶线方面,而是将会胶线所产生的不良现象控制中最小限度,这一点更为重要.
会胶线:
表二
成
型
机
原料温度低,流动性不足
射出压力低
射出速度慢
灌嘴冷料或太长
灌嘴处变形造成阻力大(压力损失)
模
具
模具温度低
模具内排气不良
GATE位置不良
GATE流道过小
从GATE到会胶线产生位置的距离过长(L/T的关系)
模具温度不平衡
原
料
原料流动性不良
原料固化速度快
原料烘干不足
3气泡
成品壁厚处的内部所产生的空隙,不透明的产品不能从外面看到,必须将其刨开后才能见到.
壁厚处的中心是冷却最慢的地方,因此迅速冷却,快速收缩的表面会将原料拉引起来产生空隙,形成气泡.
1射出压力尽可能高,减少原料收缩。
2成型品上肉厚变化急剧时,各部分冷却速度不同,容易发后气泡。
3由于停滞空气的原因而产生气泡。
4GATE过小,成品肉厚变化快。
5在GATE固化前,必须保持充分的压力。
气泡:
表三
成
型
机
原料温度高,气体产生机会多
射出压力低
射出速度过快或过慢
保压低
保压时间短
保压转换位置太快
原料温度低,流动性低
背压不足
冷却时间长
模
具
模具温度低
模具排气不良
GATE,流道胶口过小
原料
烘干不足
原料收缩比率大
4翘曲:
射出时,模具内树脂受到高压而产生内部应力,脱模后,成品两旁出现变形弯曲,薄壳成型的产品容易产生变形。
1成型品还没有充分冷却时,进行顶出,通过顶针对表面施加压力,所以会造成翘曲或变形。
2成型品各部冷却速度不均匀时,冷却慢收缩量加大,薄壁部分的原料冷却迅速,粘度提高,引起翘曲。
3模具冷却水路位置分配不均匀,须变更温度或使用多部模温机调节。
4模具水路配置较多的模具,最好用模温机分段控制,已过到理想温度。
翘曲:
表四
成
型
机
原料温度低,流动性差
保压高
保压时间长
射出压力高
射出速度慢
冷却时间短
模
具
模具温度低
模具上有温差
模具冷却不均匀,不充分
脱模不良
原料
原料的流动性不够
5流痕:
原料在模穴内流动时,在成品表面上出现以GATE为中心的年轮状细小的邹纹现象。
1增加原料温度以及模具温度,使原料容易流动。
2充填速度慢,则在充填过程中温度下降,而发生这种现象。
3如果灌嘴过长,则在灌嘴处温度下降,因此,冷却的原料最先射出,发生压力下降,而造成流痕。
4冷却窝小,射出初期,温度低的原料被先充填造成流痕。
流痕:
表五
成
型
机
原料温度低,流动性不够
射出速度快或慢
灌嘴孔径过小或灌嘴过长
射出压力低
保压不足
保压时间短
模
具
模具温度低
模具冷却不适当
GATE小或流道小
冷料窝存储小
原料
原料的流动性不良
6欠肉
成品未充填完整,有一部分缺少的状能,作为其原因认为有以下几点:
1成品面积大,机台射出容量各可塑化能力不足,此时要选择能力大的机台。
2模具排气效果不佳,模穴内的空气如果没有在射出时排除,则会由于残留空气的原因而使充填不完整,有时产生烧焦现象。
3模穴内,原料流动距离长,或者有薄壁的部分,则在原料充填结束前冷却固化。
4模具温度低,也容易造成欠肉,但是提高模温则冷却时间延长,造成成型周期时间也延长,所以,必须考虑从与生产效率相关角度来决定适当的模温。
5熔融的原料温度低或射出速度慢,原料在未充满模穴之前就固化而造成短射的现象。
6灌嘴孔径小或灌嘴长,要提高灌嘴温度,减小其流动的阻力,灌嘴的选择尽可能短,若选择灌嘴孔径小或灌嘴长的,则不仅使其流动的磨擦阻力加大,而且由于阻力的作用而使速度减慢,结果原料提前固化。
7成品模穴数量较多,流量不平衡,要设整GATE的大小来控制,GATE小模穴阻力大往往会欠肉,如有热胶道系统,也可单独调整某欠肉模穴温度来控制。
8射出压力低,造成充填不足。
欠肉:
表六
成
型
机
射出能力(容量,可塑化能力)不足
原料料量不足(计量不足)
射出压力低
原料温度低,流动性不足
射出速度慢
灌嘴变形(温度孔径)压损失
保压压力转换位置过快
射出时间设定过短
逆止阀破裂
螺杆直径大,射出压力低
灌嘴处溢料
模
具
GATE或流道平衡不良(因此不同时充填)
模具排气不良
GATE变形或流道小(压力损失)
模具温度低(原料温度过早的下降到熔点以下)
模穴壁厚过薄(与L/T的关系)
GATE位置不适当
模具冷却不适当
原料
原料流动性不足
7毛边
成品出现多余的塑胶现象,多在于模具的合模处,顶针处,滑块处等活动处。
1滑块与定位块如果磨损,则容易出现毛边。
2模具表面附著异物时,也会出现毛边。
3锁模力不足,射出时模具被打开,出现毛边。
4原料温度以及模具温度过高,则粘度下降,所以在模具仅有间隙上也容易产生毛边。
5料量供给过多,原料多余射出产生毛边。
毛边表七
成
型
机
计量多(过分充填)
射出压力高
射出速度快
原料温度高
锁模力低
射出时间长
保压压力高
保压压力转换位置慢
计量不准确,有误差(背压、螺杆转速)
机台固、定板可动板平行不良
模
具
合模面接触不良
模具接触面上附有异物
模穴内有碰伤
模具温度高
模具刚性不良(强度不足)
滑动部位间隙配合不良
模具结构设计
原
料
原料的流动性太好
影响MFI值因素
一:
目的:
为使成品MFI值合格,提供参考条件。
二:
内容:
影响成品MFI值的不合格因素大概可分为以下几点:
1.原料
1.1选取整袋相同批号同种原料,从四角中及中央五个不同位置取出原料,分别测试其MFI数值,然后再测试五个位置原料混匀的MFI值,可判别出原料之差异,可考虑原料混凝土匀后吸入料桶内;
1.2烘干机是否有故障,其烘干温度是否在原料烘干物性范围之内,烘干时间是否足够;
1.3要保持原料桶内满桶,使热风均匀的充满整个空间,每颗料粒充分烘干,这样可充分发挥烘干机烘干效果;
1.4原料是否完全烘干,原料水份测试值要小于0.02%,水份测试操作方法要正确;
1.5检查原料使用是否正确,是否混到其它种原料,可从外观,颜色及燃烧等方法区别;
1.6原料在小料斗内停留时间太长是否过久,原料已装满小料斗,而使之无法烘干从而吸收水份使原料性能下降,可调整电眼及上料时间来控制;
1.7烘干机到机台入料口处上料管有无破损,漏气。
2.料管温度
料管温度的设定对成品MFI数值起着直接作用。
2.1设定的料温是否在其物性范围之内,可参照原料物性表,温度设定不一定越低越好,要在一个合理的范围内,同时要考虑到对成品外观的影响。
3.2检查料管是否正常,感温棒安装是否正确及有无松动,可用温度量测仪量测其加热是否正常,方法如下:
2.2.1手动加料,融熔原料在料管内按其循环时间停留后再射出;
2.2.2温度仪探头迅速放入射出之融熔的原料内,左右晃动使探头始终位于熔融的原料中部,然后记录最高温度数值;
2.2.3如此动作反复做三次以上,选取最高温度数值与设定温度实际值相比较,由此可看出温度差异范围判断料管加热是否正常;
2.2.4为保证量测数值准确真实,每次量测后要将探头清理干净。
热胶道温度
为使热胶道温度检测准确,每次重启电源设定温度后要进行PID演算热胶道温度检查主方法同料温检查方法相同,但无滑胶口之热胶道系统要确保前端不会有溢料,流涕现象,会影响到MFI值及成品稳定性,有滑胶口之热胶道要检查PIN针动作有无变形,关闭时是否紧密,前端有无冷料。
螺杆
4.1所使用机台螺杆直径大小,其L/D比及压缩比,基本上螺杆直径越小MFI值越好,L/D值越小越好,压缩比越短越好入料段深度越小越好。
4.2逆止环有无破损,可从射出计量中作出判断。
4.3螺杆压缩区的料温设定微高一些,这样做可降低由螺杆旋转磨擦产生的剪切热。
成型条件
5.1循环时间是否过久,使原料在料管内停留时间延长,造成过热分解。
5.2背压压力是否太高,螺杆转速太快,造成料管内产生很高的剪切热,使原料分解,原则上背压,转速低一些,尽可能降低剪切热,但背压要适当调整不要太低,以免使进入料管内气体不易排出,影响MFI,也容易造成品质不良。
1.3射出压是否太高,射速应尽可能慢些,降低射出时产生的磨擦热。
5.4松退距离是否太长,将气体吸入料管内使原料分解。
其它因素
1SPRUE与灌嘴配合是否紧密,有无溢料现象。
2灌嘴孔直径是否太细。
3灌嘴孔前有无被压变形。
4灌嘴孔是否太长。
5灌嘴处电热是否紧靠其感温棒,不要相距太远而使温度加热失去真实。
6成品表面是否有油污。
7成品粉碎后,颗粒太大,测试MFI时较不易放入电热管内同时使加热时间延长,应保证颗粒小而且均匀,近似于原料粒大小为佳。
8成品从取出直到MFE测试,一定要保证成品及粉碎颗粒清洁,不要用手直接接触,要戴干净的手套及使用干净的胶袋子。
9GATE是否小或变形,GATE越大越好。
10流道以圆形最好,容易充填。
例:
以PC+PETUT1018—1357原料为例,于5KGLOADING单位g/10mim,常温25度,以下列温度测试出MFI值结果:
料号
测试温度
MFI值
PC+PETUT1081-1357
255
1.8
265
12.2
275
27.5
由以上结果可得知温度对MFI值得影响严重性,尤其对温度相当敏感的原料,要特别注意料管温度的控制。
变形:
Deformationduringmolding
雾气:
Moisturesteams
气泡:
Airstreaks/Bubble
缩水:
Sinkmarks
龟裂:
Stresswhitening
黑点:
Darkspots
黑线:
Blackstreaks
烧焦:
Burning
毛边:
Oversprayedparts/Flash
色差:
Colordefect
拉模:
Pullmolding
脱模不良:
PartSticking
污、油渍:
Oilsurfacedefect
熔结线:
Weldline
缺料:
Incompletelyfilledparts
顶、拉白:
Visibleejectorwhitemark
亮斑、痕:
Lightmark
灌点不良:
Dullspotsnearthesprue
模、水波痕:
Recordgrooveseffect
流痕:
Flowmark
断字:
Fractureletter
偏位:
Wrongposition
不完整:
Incompletion
模糊:
Illegible
变形:
Deformationduringprinting
翘曲:
Warpage
污渍:
Dirtymark
表面光泽不良:
Lusterless/Surfacehaze
色差:
Colordefect
漏墨:
Inkleadage
不良数:
DefectNo.
良品数:
PassNo.
备注:
Remark
成型不良的原因及对策
· 充填不足
充填不足也可叫做短射,这是熔融树脂进入模穴之内,有某一部分无法到达模穴内某一角落,而产生填料不足的现象,所得到的成形品,则缺少这一部分。
充填不足的原因和对策,因其条件的不同而不同。
成型机规格数值引起的短缺
射出能力的规格数值,是以每一次射出的重量为基准而用射出容量或射出重量(以PS换算采用)来表示。
成形品在常温的比重,和成形材料在熔融的材料温度(200~230)之下,有很大差异,有些材料甚至有70%的差异。
因此熔融材料因比重差异所引起的重量降低,就显得相当具有影响性了。
在加以螺杆因回转使树脂原料向前推进的同时,有些微材料会沿着螺杆而逆流;一般射出成型机所能成型的成形品重量(或容量)应为额定值的80%以下。
多数模穴中一部分填充不良
这种不良最主要起因是由于浇口不平衡,通常在接近主浇道的模穴中浇口较大的多位良品,但是其它离主浇道较远或浇口较小者常为不良品。
对策:
可以采用浇口平衡的方法,也就是在远离主浇道附近的模穴,将其浇口的形状做成粗大且短,而靠近主浇道者则做成较小且长,如此可以使树脂温度及压力降在远近两方面都达到平衡效果,促使每一个模穴获得相同的结果。
树脂流动性不足
如果树脂本身的流动性不足,则熔融树脂在尚未流至模具末端和合模部之前已经开始产生固化现象,必然产生填充不足的现象。
增加树脂的流动性,如果提高气缸温度或者螺杆的背压,或提高树脂的加热温度都可以达到这个目的。
除此之外,若提高模具的温度,加速射出速度时也有显著的效果,再不然,还可以选用流动性良好的树脂原料。
流动阻力过大
由于成型品的形状影响,在成形品的某一部分或因主浇道、浇道、浇口处因模具制作上而导致流动阻力较大时,也将产生填充不足的情形。
成形品形状的影响,大部分都发生在肉厚较薄及直角转弯的部分产生流动阻力,对策上应尽可能增加肉厚,追加补助浇道,并且在转弯处追加R角。
而模具主浇道、浇道及浇口所产生的流动阻力,则可以因增大其尺寸而减轻其流动阻力,尤其改为圆形或梯形剖面形状的浇道。
此外浇口背之树胶存量不足时,也可能影响流动阻力,应该增大为佳。
模穴内通气不良
因为这个原因所引起的充填不足,是很常见的例子,但经常被误认为是其他原因,无法好好的采取对策。
先来考虑一下,在射出成形时,模具内的空气里懂得情形。
但熔融树脂进入模穴内时,模穴内的空气将被压缩,而且被挤压到角落。
这些空气很可能从模具分模面的间隙或模仁或侧模芯的空隙溢出模具之外,但是由于肉厚不均而产生但空气已被外围成型部分围住/或模具有深的空穴部分时,则这个被压缩的空气无法溢出模穴之外,而导致填充不良。
这种充填不良的情形,特别容易发生在被厚肉壁包围的薄肉壁部分或是长而深的凸缘末端,有时在分模面上亦有可能发生。
如果单纯以充填不良的现象来看,常常以为是流动性不良引起的结果,但是如果因此而将射出速度提高而予以成形时,则将因空气的绝热压缩而使树脂产生高温,产生烧焦或黑线条纹之现象;此时,应马上降回射出速度,而认真考虑空气逸出的方法。
根本的对策是改变模具的构造,想办法制作空气逸出的管路,在分模面上可以利用模具接触面上作出空气逸出道,长而深的凸缘部分,不要采用直接加工模穴的方法,而使用套入模仁的方式以增加空气逸出的管道。
如果成形品具有薄肉壁的部分时,则除了采用类似的套入模仁方式之外,应同时在浇口位置亦增高空气逸出部分可大大地加以改善。
树脂供给不足
这种情形,大概是由以下两种原因所引起。
其一,由漏斗至成形机时,由于树脂粒堵在成形机的进转口处,有些许树脂材料无法落入成形机之内,将产生树脂供给不足的情形。
另一种可能是,漏斗下部过热或树脂粒因具备润滑性而押送螺杆无法完全将树脂粒往前推送的结果。
对策上,除了选用正确的成形条件之外,应选用过度润滑性的树脂粒,以降低押送不足的现象。
· 模具伤痕及拖痕
模具伤痕因表面受损伤而导致成形品表面显现模具的伤痕,此时,除了赶快修模之外,别无他法。
但是,当成形后,在顶出成形品时,由于模窝或模芯因具备逆推拨时,则在顶出成形品后,在成形品表面将产生拖拉之痕迹;简单的对策,可以采取提高加热汽缸温度及模具温度,并且降低射出压力,以减少成形品之成形收缩量;这种方法只可能减少拖痕的程度而无法完全去除之,最主要还是要能够确实加以修改模具的推拨度。
也就是因为模具推拨度的不足,在模具分离时,成形品的一部分被固定模具侧卡住,被勉强斜斜地被顶出之时,便产生拖拉磨擦的现象,而导致拖痕,这种不良除了推拨度不足,亦可能是推拨度汪均,或是由于顶出销前端面倾斜所致,这些原因所导致的拖痕,基本上的对策,只有将模具予以修改。
特别是经过电镀后的模具,因角隅部分容易增厚之故,将产生推拨度不足的现象。
另外还有如果在模具面上施以纹面加工时,因凹凸的互相咬合亦产生推拨度不足。
因此,上述这些原因的基本对策,只好加大模窝及模芯间的推拨度了。
如果是顶出作用点不适当的理由时,则因倾斜顶出而导致的拖痕对策,除了校准顶出销的精度之外,还可以追加顶出销的数目,并且选择正确的顶出销设置的位置。
· 成形品毛头过多
成形品毛头(burr)过多的现象,是在模具接合面上或是嵌入模仁时,因接合面不够密接,而导致成形时,产生膜片生成的结果。
一旦发生毛头时,则因杠杆作用又使毛头更容易由该处增长而冒出,然后再由于增加成形投影面之故又因此助长毛头生成部分模具面上的凹陷磨损,综合结果有恶性助长毛头的生成的现象。
因此如果在发生毛头现象之时,应该赶快将模具予以修理,以免快速恶化。
锁模力不足
成形品的投影面积所计算得到的最低限锁模力,若超出成形时所设定的真正锁模力之时,则由于射出压力太大,将模具可动部分向外顶出,则在合模面上产生非常小的间隙,成形时,即在此接合面上产生毛头;毛头产生之后更增加投影面积,相对的又提高顶开的总合推力,更增长锁模力不足之恶果。
特别是当中央部具有孔穴的成形品,利用侧面浇口(sidegate)来加以成形时,浇道部亦将增加射出压力的负担,容易更增长毛头的发生。
解决方法除了提高锁模力之外,亦可以降低射出压力。
该锁模力及投影面的关系,亦适用于侧模芯的情形。
还有,在射出成形机中,使用肘节式机构时出无法得到额定的锁模力,亦可能产生不均衡的锁模力。
此外模具承板两平面间的平行度若有所偏差时,亦将影响锁模力的大小。
模具密合不良、变形而产生
模具在合模面上的密合不良,当然也是发生毛头的原因之一。
尤其是埋值件的接触毛头的不良。
即使密著性良好,模具密著上若留有异物,亦将产生毛头不良,这种情形,当然是要清扫模具的密著即可。
如果模板本身厚度不足,在射出压力的负担下,将产生变形,特别是在模具中央部分,如果具备孔穴时,则在孔穴的周围便容易产生毛现象。
这种毛头的发生,通常可以利用降低射出压力,及提高树脂温度的方法来减轻毛头发生的程度,但是如果再无法解决时,则必然是模具设计上的严重不良,只利用变更成形条件的方法是无法予以解决的。
树脂流动性太好
当然,只是树脂流动性太好时,理论上不可能是产生毛头的原因。
但时实际上,如因流动性太好时,则任何些微的间隙都会因树脂流入之故而产生毛头。
对策是方法是降低树脂温度及射出压力,或者是降低模具温度降低射 出速度都同样具备相同的效果。
· 收缩
收缩(俗称缩水)是成形品表面上凹陷不良情况,是成形品中发生频度最高的不良现象。
收缩凹陷是树脂成形收缩而产生。
是非常难以消除的不良现象。
当进行射出成形时,将融溶的热树脂注入低温的模具之内,因此成形时其固化的动作是由表面向内渐渐凝固的,但是由于树脂的热传导性非常差,而且传导的过程亦比模具的热传导较佳之侧先行凝固,然后在其对面热传导较差的部分再行凝固,因此在热传导性较差之面上发生收缩凹陷的现象。
因此在成形品及模具设计的阶段,应该在设计时先行考虑防止收缩凹陷的方法才是。
考虑时应连同考虑内部的收缩现象,一并予以处理。
收缩不足
与成形的肉厚或容积比较起来,如果主浇道、浇道、浇口太过于细小之时,则注入模窝内的树脂很难保持十足的射出压力,而无法到达保压的目的,造成增大成形品收缩率的结果,缩水凹陷亦随之增加。
特别是在采用针点浇口、侧面浇口、潜入浇口等限制形浇口的情况下,即使十分给予保压的时间,由于浇口本身容易固化之故,模具(窝)内其实并无法保持这个射出压力,于是收缩凹陷的情形当然更加严重了。
此外,树脂材料本身的成形收缩率之值较大,而且融点温度非常明显的结晶性树脂也比非结晶性树脂更容易产生收缩凹陷。
通常成形收缩率较低的非结晶性树脂中的含玻璃纤维的强化树脂(FRTP),都具备较少收缩凹陷的特性。
对策上,采取直接的方法,一方面提高射出压力并降低加热汽缸温度,另一方面维持十足的保压,如果再无法克服或减轻收缩凹陷的情形时,则只好加大主浇道、浇道、浇口的