支座铸造工艺课程设计.docx
《支座铸造工艺课程设计.docx》由会员分享,可在线阅读,更多相关《支座铸造工艺课程设计.docx(18页珍藏版)》请在冰豆网上搜索。
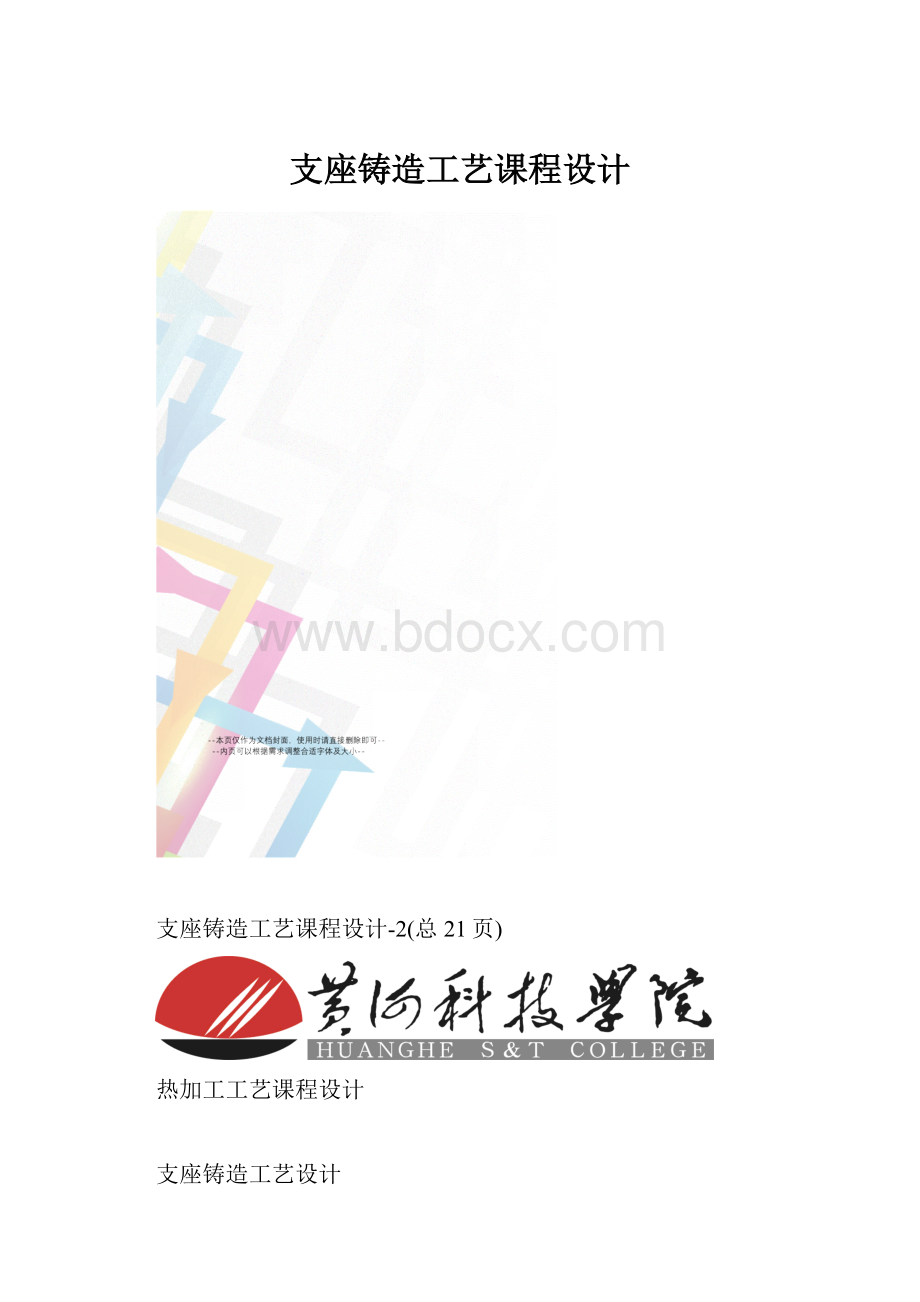
支座铸造工艺课程设计
支座铸造工艺课程设计-2(总21页)
热加工工艺课程设计
支座铸造工艺设计
院系:
工学院机械系
专业:
机械设计制造及其自动化
班级:
姓名:
学号:
指导老师:
时间:
黄河科技学院课程设计任务书
工学院机械系机械设计制造及其自动化专业2011级1班
学号姓名指导教师
设计题目:
支座铸造工艺设计
课程名称:
热加工工艺课程设计
课程设计时间:
5月22日至6月6日共2周
课程设计工作内容与基本要求(已知技术参数、设计要求、设计任务、工作计划、所需相关资料)(纸张不够可加页)
1、已知技术参数
图1支座零件图
2、设计任务与要求
1)设计任务
1选择零件的铸型种类,并选择零件的材料牌号。
2分析零件的结构,找出几种分型方案,并分别用符号标出。
3从保证质量和简化工艺两方面进行分析比较,选出最佳分型方案,标出浇注位置和造型方法。
4画出零件的铸造工艺图(图上标出最佳浇注位置与分型面位置、画出机加工余量、起模斜度、铸造圆角、型芯及型芯头,图下注明收缩量)
5绘制出铸件图。
2)设计要求
1设计图样一律按工程制图要求,采用手绘或机绘完成,并用三号图纸出图。
2按所设计内容及相应顺序要求,认真编写说明书(不少于3000字)。
3、工作计划
熟悉设计题目,查阅资料,做准备工作1天
确定铸造工艺方案1天
工艺设计和工艺计算2天
绘制铸件铸造工艺图1天
确定铸件铸造工艺步骤2天
编写设计说明书3天
答辩1天
4.主要参考资料
《热加工工艺基础》、《金属成形工艺设计》、《机械设计手册》
系主任审批意见:
审批人签名:
时间:
2013年月日
支座铸造工艺设计
摘要
铸造是指将液态金属或合金浇注到与零件尺寸、形状相适应的铸型型腔里,待其冷却凝固后获得毛坯或零件的方法。
铸造成形是机械类零件和毛坯成形的重要工艺方法之一,尤以适合于制造内腔和外形复杂的毛坯或零件。
本文主要分析了支座的结构,并根据其结构特点确定了它的砂型铸造工艺。
支座是支撑其他零部件的重要承力零件,主要承受着径向压缩及轴向摩擦的作用,它具有结构稳定、形状简单、廉价实用等特点,故在机械零件的设计、加工制造中支座都起着不可替代的作用。
本文设计了支座的砂型铸造工艺,包括铸型(型芯)及造型方法的选择、分型面选择和浇注位置的确定、浇注系统及冒口的设置、落砂清理及检验等。
绘制了铸件的零件图及铸造工艺图。
本文还对支座的铸造质量指标(包括加工余量、拔模斜度、收缩率及变形等)进行了分析与评估,以便于工艺更好的完善。
关键词:
砂型铸造,浇注,加工余量,拔模斜度,收缩率
铸件的尺寸分析
致谢........................................................................................................................................13
参考文献…………………………………………………………………………………………14
1绪论
铸造是人类掌握比较早的一种金属热加工工艺,已有约6000年的历史。
中国约在公元前1700~前1000年之间已进入青铜铸件的全盛期,工艺上已达到相当高的水平。
铸造是指将固态金属溶化为液态倒入特定形状的铸型,待其凝固成形的加工方式。
被铸金属有:
铜、铁、铝、锡、铅等,普通铸型的材料是原砂、黏土、水玻璃、树脂及其他辅助材料。
特种铸造的铸型包括:
熔模铸造、消失模铸造、金属型铸造、陶瓷型铸造等。
(原砂包括:
石英砂、镁砂、锆砂、铬铁矿砂、镁橄榄石砂、兰晶石砂、石墨砂、铁砂等)。
我国古代铸造技术居世界先进行列。
由于过长的封建社会影响了科学技术的发簪,阻滞了铸造技术前进的步伐。
心中过成立以来的50多年中,自20世纪50年代初至今,几乎从零开始,逐步发展到现在这样的规模,成绩是巨大的。
现在铸造在我国是一个很大的行业,产量居世界第二位,达年产1000万-1200万吨,厂点多大2万多个,职工100-130万人,其中工程技术人员约占%,已经成为了国家重要的的基础工业之一。
支座铸造工艺设计的总体思路是:
首先确定支座的铸造工艺方案,分析铸件的结构,然后选定铸件材料、确定铸型(型芯)的造型(制芯)方法、确定浇注位置、绘制铸造工艺图。
重点考虑浇注位置,铸型分型面,型芯的形状、尺寸和数量及固定方法,加工余量,收缩率,浇注系统,起模斜度,冒口和冷铁的尺寸和位置等。
铸件材料是依据支座的强度、刚度以及使用寿命、加工精度等方面的要求来选择,本设计中支座材料选用HT150。
另外,型砂和芯砂的配制和使用直接影响铸件质量和成本,铸型材料选粘土砂,型芯则采用树脂砂。
采用恰当的工艺措施可控制铸件质量,明显提高生产率,降低成本。
2支座的结构及工艺性分析
支座的结构及尺寸分析
支座是机械工程中最为常用的一种零件,其工作环境也相对比较复杂,可能受到各种力的的作用,在这些力中对支座影响最大的是收到了轴向的压缩作用,为了防止其受到这些因素而发生裂纹或破坏,我们在选择材料进行浇注加工时尤为注意选择能使在工作过程中不至于受压破坏。
而铸造件在铸造的时候必须严格按照铸造工艺手册中正确的操作方式对支座零件进行有效的铸造操作使其能有效的符合我实用时的标准,是经济性实用性大大的提升。
对于要求更高的支座可通过对其相应的处理使其得更好的力学性能。
同时用铸件做零件毛坯可以减少用材,和二次切削所浪费的材料,不仅节约材料也大大的提高了经济性。
合理的铸件结构是获得优质铸件的前提,也是简化铸造工艺、提高生产率和降低成本的根本保证。
需要铸造的零件的结构不仅要满足工作性能和力学性能的要求,同时还应该满足铸造工艺、方法和砂型铸造性能的基本要求,还能在很小改动下使铸件结构与这些要求相适应,力求工艺简单,能够经济、迅速的生产出合格的铸件。
铸件具有以下几个优越性:
1)可以制成形状复杂的,特别是复杂内嵌的毛坯、2)由于是直接用液态金属浇注形成的形状复杂各异的铸件。
此机架铸件以中心轴为对称轴有一个尺寸为50mm的空心圆柱,长为200mm。
两边有两个凸台,每个凸台中都有一个尺寸我Φ15的空心圆柱,此两空心圆柱线间的距离为145mm。
凸台高30mm,表面粗糙度为.支架为120mm,下底面表面粗糙度为,上顶面表面粗糙度为,支架大圆为Φ80mm。
铸件的特点是通过制作出各种形状复杂的金属结构材料模型,然后融化金属材料对模型进行系统性的浇注,然后冷却、凝固从而获得所需的具有复杂结构特点的毛坯、零件。
这样所得的铸件具有稳定性好,结构性强,经济性好等特点。
铸造方法可分为:
砂型铸造、熔模铸造、金属型铸造、压力铸造、低压铸造、离心铸造等,其中砂型铸造是最为常见的也是最基本的工艺方法,它适用于各种形状、大小、批量及各种合金铸件的生产。
掌握砂型铸造是合理选择铸造方法和正确设计铸件的基础。
确定好铸造方式后还要对其进行造型及造芯的选择等,其中造型的方法包含了:
砂箱造型、劈箱造型、叠箱造型、刮板造芯等。
在制定工艺方案之前,对熟悉图样和铸件的使用要求,掌握实际生产的现有条件,以图样技术要求、生产批量和使用信息为依据,分析铸件结构,选择铸型种类、确定造型和造芯的方法等,以便为铸造工艺的拟定奠定基础。
支座的工艺分析
根据支座的工作条件,综合考虑支座的结构及其在经济性、工艺性和使用性等方面的要求,对支座的工艺性进行深入的分析。
支座零件结构的铸造工艺性是指零件的结构应符合铸造生产的要求,易于保证铸件品质,简化铸件工艺过程和降低成本。
审查、分析应考虑如下几个方面:
(1)铸件应有合壁厚,为了避免浇不到、冷隔等缺陷,铸件不应太薄;
(2)铸件结构不应造成严重的收缩阻碍,注意薄壁过渡和圆角铸件薄厚壁的相接拐弯等厚度的壁与壁的各种交接,都应采取逐渐过渡和转变的形式,并应使用较大的圆角相连接,避免因应力集中导致裂纹缺陷;
(3)铸件内壁应薄于外壁,铸件的内壁和肋等,散热条件较差,应薄于外壁,以使内、外壁能均匀地冷却,减轻内应力和防止裂;
(4)壁厚力求均匀,减少肥厚部分,防止形成热节;
(5)利于补缩和实现顺序凝固;
(6)防止铸件翘曲变形;
(7)避免浇注位置上有水平的大平面结构。
3支座铸造工艺方案设计
铸型及造型方法的选择
图支座三维图(外形图)
支座零件具有支座底平面、紧固孔、与支座底平面相垂直的支承孔及支承孔两端面等。
支座的外形图如图所示,支座的零件图如图所示,支座的外形轮廓尺寸为200mm*110mm*120mm,主要壁厚26mm,最小壁厚15mm,为一小型铸件;铸件除满足几何尺寸精度及材质方面的要求外,无其他特殊技术要求.
支座零件具有内腔、小空、圆角、凸台、以及锥角,形状复杂,其表面无特殊要求。
零件的最大轮廓尺寸为200mm,零件较复杂,应选砂型铸造成型,采用单件小批量生产。
中小型铸件尽量选择湿型,因此铸件的铸型种类为湿砂型铸造。
由于支座零件为回转体结构件,产品生产性质适合于做批量生产。
零件材料选用HT150.
图支座的零件图
分型面的选择
分型面的选择应遵循以下几点:
(1)应使铸件全部或大部分位于同一砂型内,或使主要加工面与加工的基准面处于同一砂型中,以防错型,保证铸件尺寸精度,便于造型和合型操作。
若铸件的加工面很多,又不可能都与基准面放在分型面的同一侧时,则应使加工基准面与大部分加工面处在分型面的同一侧。
(2)应尽量减少分型面的数量,最好只有一个分型面。
这样可简化操作过程,提高铸件精度(因多一个分型面,铸型就增加一些误差)
(3)应尽量使型腔和主要型芯处于下型,以便于造型,下芯,合型及检验型腔尺寸。
但下型的型腔不宜过深,并避免使用吊芯和大的吊砂。
(4)应尽量选用平直面作分型面,少用曲面,以简化制模和造型工艺。
(5)应尽量减少型芯和活块的数量,以简化制模、造型、合型等工序。
(6)分型面应选在铸件的最大截面处,以保证从铸型中取出模样,而不损坏铸型。
具体选择铸件分型面时,为保证铸件质量,应尽量避免合型后翻转砂型。
一般应首先确定浇注位置,再考虑、分型面。
对于质量要求不高的铸件,应先选择能使工艺简化的分型面,而浇注位置的选择则处于次要地位。
本设计选择分型面主要考虑使铸件全部或大部分置于同一半型内,并尽量减少分型面的数目,且分型面应尽量选用平面,以便于下芯、合箱和检测,不使砂箱过高,受力件的分型面的选择不应削弱铸件结构强度,注意减轻铸件清理和机械加工量。
综合所述,支座铸件的分型面选择如图所示。
图支座的分型面
浇注位置的确定
浇注位置确定应符合铸件凝固方式,保证铸型充填及铸件质量,而尽量置于有理部位,因此讲支撑台水平浇注,可使两端加工面处于侧立位置,以利于保证铸件质量及精度,并利于型芯稳固、排气落砂和检验。
铸件的浇注位置是指浇注时铸件在型内所处的状态和位置。
确定浇注位置是铸造工艺设计中重要的环节,关系到铸件的内在质量,铸件的尺寸精度及造型工艺过程的难易程度。
浇注位置的确定遵循下列原则:
(1)铸件的重要部分应尽量置于下部;
(2)重要加工面应朝下或直立状态;
(3)使铸件的答平面朝下,避免夹砂结疤内缺陷;
(4)应保证铸件能充满;
(5)应有利于铸件的补缩;
(6)避免用吊砂,吊芯或悬臂式砂芯,便于下芯,合箱及检验。
综合以上的分析,选择图所示的浇注位置。
图浇注位置
铸造工艺参数的确定
铸造工艺设计参数通常是指铸型工艺设计时需要确定的某些数据,这些工艺数据一般都与模样及芯盒尺寸有关,及与铸件的精度有密切关系,同时也与造型、制芯、下芯及合箱的工艺过程有关。
这些工艺数据主要是指加工余量、起模斜度、铸造收缩率、最小铸出孔、型芯头尺寸、铸造圆角等。
工艺参数选取的准确、合适,才能保证铸件尺寸精确,使造型、制芯、下芯及合箱方便,提高生产率,降低成本。
支座的尺寸公差为CT8~12级,取CT9级。
支座的轮廓尺寸为200mm*110mm*100mm,由《铸造工艺设计》得:
支座尺寸公差数值为。
表1为铸件的基本尺寸及尺寸公差数值,另外在机械加工余量方面也应该认真考虑。
机械加工余量是铸件为了保证其加工面尺寸和零件精度,应有加工余量,即在铸件工艺设计时预先增加的,而后在机械加工时又被切去的金属层厚度。
支座为砂型铸造机器造型大批量生产,支座的加工余量为E~G级,取G级。
支座的轮廓尺寸为160mm*135mm*100mm,支座加工余量数值为,取2mm。
在铸造收缩率方面,铸造收缩率又称铸件线收缩率,用模样与铸件的长度差除以模样长度的百分比表示:
ε=[(L1-L2)/L1]*100%;ε为铸造收缩率;L1为模样长度;L2为铸件长度;支座的受阻收缩率为%。
浇注系统设置
浇注系统是铸型中引导液体金属进入型腔的通道,它由浇口杯,直浇道,横浇道和内浇道组成。
浇注系统分为封闭式浇注系统,开放式浇注系统,半封闭式浇注系统和封闭-开放式浇注系统。
支座就是采用湿型的铸件小件,所以选择封闭式浇注系统。
支座结构较为简单且是小型件,每个铸件上只用一个内浇道。
内浇道开,支座的浇注顺序为由下至上凝固,这样有利于支座的重要部分先凝固并得到补缩,如此内浇道则设置在底部侧面引入金属液,如图所示。
。
图浇注系统分布
铸造工艺图绘制
铸造工艺图是在零件图上以规定的红、蓝等色符号表示铸造工艺内容所得到的图形,如图所示。
实际生活中使用的铸造工艺图,大多将分型线、加工余量、浇注系统等均用红线表示,且分型线的两侧用红线标出“上”、“下”字样以表示上、下型位置。
其主要内容包括:
浇注位置、分型面、铸造工艺参数(机械加工余量、起模斜度、铸造圆角、收缩率、芯头等)。
铸造工艺图是指导铸造生产的技术文件,也是验收铸件的主要依据。
图支座铸造工艺图
铸件图的绘制
铸件图反映了铸件实际形状、尺寸和技术要求,是铸造生产铸件检验与验收的主要依据。
支座的铸件图如图所示。
图支座铸件图
4支座铸造工艺卡
支座铸造工艺卡如表所示。
表支座铸造工艺卡
铸件名称
材料牌号
生产类型
毛坯质量
平均壁厚
零件图
支座
灰铸铁
单件
15mm
造
型
造型方法
砂型铸造
砂箱内部尺寸/mm
规格
长
宽
高
紧固方法
上箱
240mm
150mm
110mm
压铁紧固600Kg
下箱
240mm
150mm
110mm
砂
型
烘
干
烘干温度/°C
烘干时间/h
方法
500
15
烘干炉
浇冒口尺寸
/mm
浇道数量
长
宽
高
截面积
横浇道
32
22
35
950mm2
内浇道
24
21
10
255mm2
浇注工艺规范
出炉温度/°C
浇注温度/°C
浇注温度/°C
冷却时间/h
>1400
>1250
30-50
>24
热处理工艺
加热5-7h至850摄氏度左右,保温均热3-5小时。
炉温冷至400-500度出炉空冷
总结
为期两周的热加工工艺设计已近尾声,在整个设计过程中,我学到了很多。
从刚开始对制造工艺只有一点感性认识到现在已熟悉铸造工艺的国内外现状及发展趋势,并能对工件的铸造工艺方案进行设计,同时对铸造工艺流程也比较清楚了。
在设计时,要用到许多基础理论,由于有些知识已经遗忘,所以我们又重新复习了以前的知识。
一开始对本课题的设计任务有了大致的了解,并也有了设计的感觉。
同时,由于设计的需要,查阅并收集了大量关于机械制造方面的文献,进而对这些文献进行分析和总结,这些都提高了对专业知识的综合运用能力和分析解决实际问题的能力。
通过本次设计还使我更深切地感受到了团队的力量与合作精神,在与同学们的讨论中发现问题并及时解决问题,这些使我们相互之间的沟通协调能力得到了提高,可以说,课程设计体现了我们对本课程所学知识的熟悉程度和运用能力,也检验了我们的综合素质和实际能力。
课程设计也锻炼了我发现问题、解决问题的能力。
由以前的不懂不问,而到现在是一探究竟。
致谢
在本次设计中,感谢刘万福老师对我的教育与指导,他细心的教授我各种关于设计工艺的知识,让我对这方面有了更深入的了解,并对我的设计提出了很多宝贵的意见与建议,耐心的解答各种问题,老师以其严谨求实的治学态度、高度的敬业精神、兢兢业业孜孜以求的工作作风和大胆创新的进取精神对我产生重要影响。
他渊博的知识、开阔的视野和敏锐的思维给了我深深的启迪。
这次的热加工工艺设计是在刘老师的精心指导和帮助下完成的。
在此也感谢所有教过我的老师,没有他们的教导和帮助,很难完成这次设计工作。
同时也感谢在这次课程设计中帮助我的同学们!
由于水平有限加之时间仓促,难免有错误和不足之处,肯请老师批评指正。
参考文献
【1】王爱珍主编:
《机械工程材料》:
北京航空航天大学出版社
【2】王爱珍主编:
《热加工工艺基础》:
北京航空航天大学出版社
【3】王爱珍主编:
《金属成型工艺设计》:
北京航空航天大学出版社
【4】胡传鼎主编:
《铸铁件生产使用技术》:
化学工业出版社
【5】徐凤琴范晓光主编:
《铸造工技能图解》:
机械工业出版社
【6】邓文英主编:
《金属工艺学》:
高等教育出版社
【7】丁殿忠主编:
《金属工艺学课程设计》:
机械工业出版社