赖氨酸课程设计.docx
《赖氨酸课程设计.docx》由会员分享,可在线阅读,更多相关《赖氨酸课程设计.docx(34页珍藏版)》请在冰豆网上搜索。
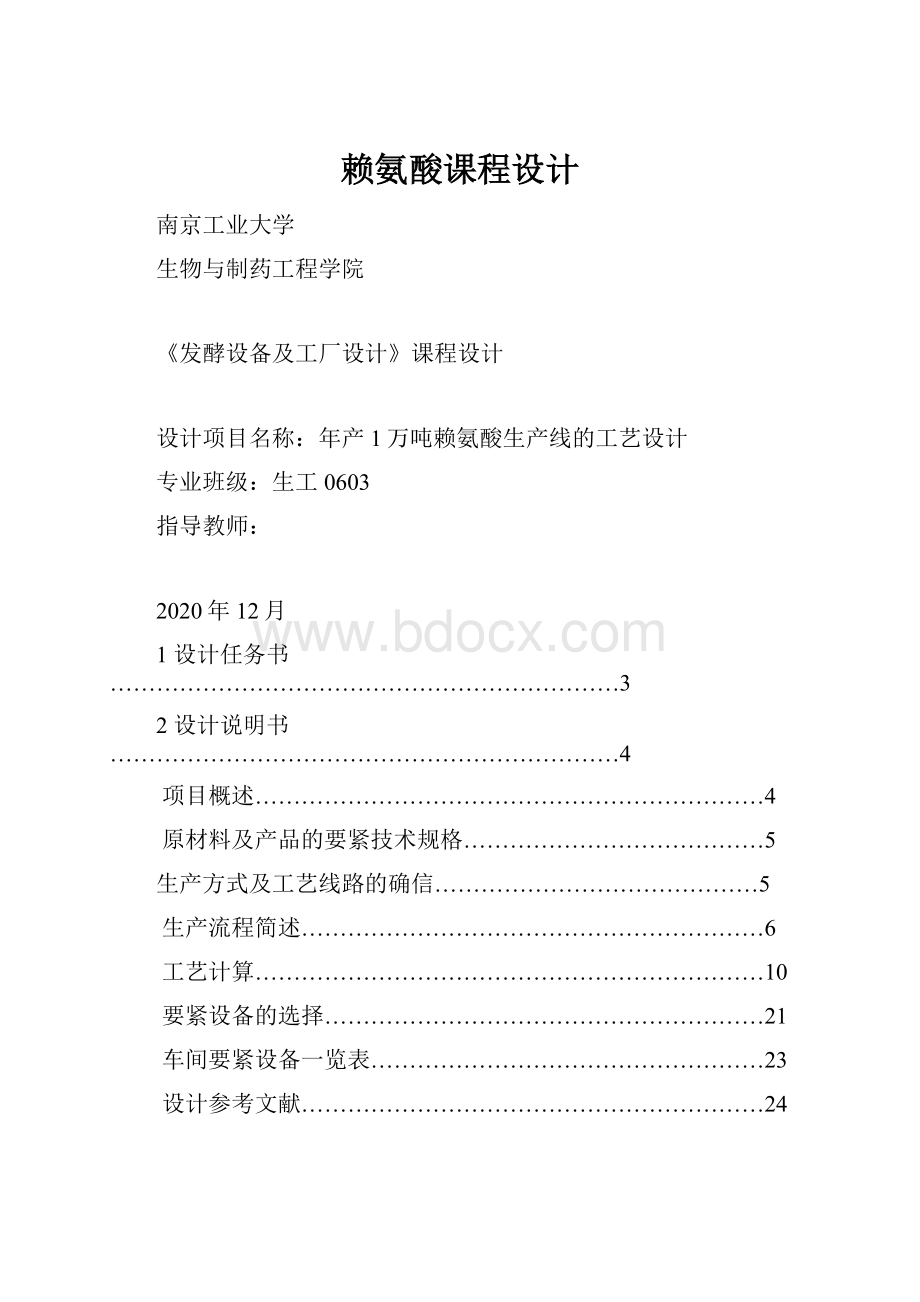
赖氨酸课程设计
南京工业大学
生物与制药工程学院
《发酵设备及工厂设计》课程设计
设计项目名称:
年产1万吨赖氨酸生产线的工艺设计
专业班级:
生工0603
指导教师:
2020年12月
1设计任务书…………………………………………………………3
2设计说明书…………………………………………………………4
项目概述…………………………………………………………4
原材料及产品的要紧技术规格…………………………………5
生产方式及工艺线路的确信……………………………………5
生产流程简述……………………………………………………6
工艺计算…………………………………………………………10
要紧设备的选择…………………………………………………21
车间要紧设备一览表……………………………………………23
设计参考文献……………………………………………………24
一、设计任务书
项目名称:
年产1万吨赖氨酸生产线的工艺设计
一、建设规模、产品方案、生产方式和工作制度
1)建设规模:
年产10000T。
2)产品标准:
L—赖氨酸盐L—LYSINE·HCL
分子式:
C6H14N2O2·HCL
分子量:
18264
性状:
淡棕色粒、易溶于水。
国家标准GB8245—87规定了饲料级L—氨基酸盐酸盐产品的质量准。
3)生产方式:
以玉米淀粉乳为原料,采纳双酶法,使淀粉乳先糖化而转化为葡萄糖,然后再以糖类为发酵原料,日本多采纳短杆菌诱发株为菌种,以通用的碳水化合物及其他营养素为培育基,通过发酵、过滤、中和、精制、干燥而得成品,必要时进行重结晶。
4)工作制度:
:
年工作日按300d计
二、目建设地址为南方某市其气候条件为:
年平均气温:
15.3℃
历年平均最高气温:
38℃
历年平均最低气温:
-4.2℃
最热平均相对湿度:
85%
最冷平均相对湿度:
75%
年平均气压:
夏日平均气压:
年均风速:
3.6m/s
年均降落量:
1025.6mm
日最大降水量:
219.6mm
三、求达到的技术经济指标
要求达到的技术经济指标:
发酵产酸率
13%
染菌率
1%
转化率
100%
发酵周期
64hr
提取收率
90%
平均通过气比为
1:
四.设计要求
就该项目的发酵工段或空气处置系统进行工艺设计,要求完成:
2.确信合理的工艺线路,提供工艺流程示用意;
3.进行工段的工艺计算,包括物料、热量、水、紧缩空气耗量等平稳计算,并提供相应的工艺计算平稳图;
4.对标准设备及非标设备的数量进行计算,选定标准设备型号并就至少一种非标设备的结构进行简单的结构计算,提供所需设备的一览表并至少提供一种非标设备的总装图。
5.绘制带操纵节点的工艺流程图;
6.绘制车间设备布置图;
7.绘制设备配管图;
8.编写初步设计说明书。
二、设计说明书
项目概述
赖氨酸(L-Lysine),化学名称2,6-二氨基己酸,分子式为C6H4N2O2,纯品为白色针状结晶,无味或稍带特殊臭味,易溶于水,溶液的PH值为~,难溶于有机溶液,有旋光性,熔点263~264C.赖氨酸难于结晶,市售商品一样为98%的L-赖氨酸盐酸盐。
具有旋光性。
由于游离的L-赖氨酸极易潮解,因具有氨基酸而易发黄变质,并具有刺激性腥味,难于长期保留。
因此,一样商品都是L-赖氨酸盐酸盐。
赖氨酸盐酸通常较稳固,高温下易结块,相对湿度60%以下稳固,60%以上那么生成二水合物,与维生素C和维生素K并存那么着色。
碱性条件及直接在还原糖存在加热那么分解,易溶于水,水溶液呈中性至微酸性,与磷酸、盐酸、氢氧化钠、离子互换树脂等一路加热,能起到外消旋作用。
饲料中添加的赖氨酸有两种,即L-赖氨酸和DL-赖氨酸。
因动物只能利用L-赖氨酸,故要紧为L-赖氨酸产品,DL-赖氨酸产品应标明L-赖氨酸含量保证值。
作为商品的饲用级赖氨酸一般是纯度为%以上的L-赖氨酸盐酸盐,相当于含赖氨酸(有效成份)%以上,为白色一淡黄色颗粒状粉末,稍有异味,易溶于水。
90%以上的L-赖氨酸是以糖蜜为原料发酵生产的产品。
另外,日本、美国、德国等国已利用化学合成的2-氨基ω-己内酰胺作原料,通过微生物酶消旋和水解生产L-赖氨酸。
建设规模及产品方案
1)建设规模:
年产10000T。
2)产品标准:
L—赖氨酸盐L—LYSINE·HCL
分子式:
C6H14N2O2·HCL
分子量:
18264
性状:
淡棕色粒、易溶于水。
国家标准GB8245—87规定了饲料级L—氨基酸盐酸盐产品的质量准。
3)生产方式:
以玉米淀粉乳为原料,采纳双酶法,使淀粉先经液化、糖化而转化为葡萄糖,然后再以糖类为发酵原料,日本多采纳短杆菌诱发株为菌种,以通用的碳水化合物及其他营养素为培育基,通过发酵、过滤、中和、精制、干燥而得成品,必要时进行重结晶。
4)工作制度:
:
年工作日按300d计
原材料及产品的要紧技术规格
2.2.1原材料的选择及技术规格
本设计要求以玉米淀粉乳为原料,可是,工业上选择生产原料时,不但要考虑工艺上的要求,还要考虑生产治理和经济上的可行性。
在大规模工业生产中,选择原料一样要考虑到下述要求:
(1)因地制宜,就近取材,价钱低廉;
(2)原料中可利用成份高,末严峻污染,抑制生长和产酸的物质要少或能够去除,能知足工艺上的要求;
(3)原料资源丰硕,便于采购运输,适于大规模储藏,保证生产上的供给。
生产方式及工艺线路的确信
赖氨酸是人和动物自身不能合成的一种氨基酸,必需从外界摄取,而植物中所含的各类赖氨酸很少,被称为植物中的第一限制性氨基酸。
1960年日本的木下祝郎等用紫外线照射谷氨酸柞杆菌取得一株营养缺点型变异株,从此开始了发酵法工业生产商品赖氨酸。
世界上生产的要紧方式有微生物发酵法、化学酶法、提取法和合成法四种。
其中最重要的是化学酶法和微生物发酵法。
其具体操作进程如下。
2.3.1 化学酶法
此法是借助于有机合成与生物化学工程相结合的生产技术,能够己内酰胺或二氢呋喃为起始原料,或以糠醛为原料制取。
制取尼龙原料己内酰胺时,有大量的还己烯生成,用环己烯易于合成DL—氨基己内酰胺(DL-ACL),以此为原料采纳水解酶法生产赖氨酸,分为两步反映进行。
先用L—ACL水解酶,不对称水解L-ACL的环状酰胺链,生成L—赖氨酸,再用ACL消旋酶使残余的D-ACL消旋化反映。
具体工艺中采纳罗氏隐环酵母等进行水解反映,用奥巴无色杆菌进行消旋反映。
100/L的DL-ACL几乎全数转化为L—赖氨酸。
微生物发酵法
发酵法包括一步法和经由二氨基庚二酸的二步法。
通常以废糖蜜,淀粉(或直接用木薯片粉碎至80目)为原料,采纳双酶法,使淀粉先经液化、糖化而转化为葡萄糖,然后再以糖类为发酵原料,日本多采纳短杆菌诱发株为菌种,以通用的碳水化合物及其他营养素为培育基,通过发酵、过滤、中和、精制、干燥而得成品,必要时进行重结晶。
成品对糖总得率为35%,每吨成品耗糖蜜8吨(或淀粉吨),本钱约1万元(折人民币)。
L-赖氨酸的生产工艺与味精(谷氨酸钠)类似,工艺较简单,日本的技术经济指标较先进。
微生物发酵法为生产L-赖氨酸的最要紧技术,反映所用碳源为玉米、甘蔗等淀粉质或葡萄糖母液、甘蔗糖蜜等废料,所用高产菌种有BrevibacteriumSP。
PI—B等,在优选菌种配方中含有HPP\KH2PO4、乙酸钠等组分,在添加2%硫酸铵后可取得高产菌种。
将适宜的配方组分注入500ml的三角烧瓶内于120C加热15min加压灭菌后,在通氧下培育出菌种在顶峰期内接入种子培育液在常温常压下发酵,再用膜分离法或化学法分离。
制备L—赖氨酸在14L的发酵器中进行。
通过菌种培育,生长菌体和发酵工艺生产赖氨酸,挑选出的FHI28高产菌株,遗传性能稳固,是一株适合工业化生产的优良菌种,在20ml发酵罐中产L—赖氨酸~%,发酵周期59~67h.
工艺的关键技术在于培养和优选最适宜的菌种,采用不同的原料其结果会大不相同,甚至同一原料也会因原料产地和产出时间的差异使结果有很大差别。
国内的发酵法工艺提取率为80%~85%,糖转化率40%~43%,产品收率大于90%。
在发酵和菌种培养中,必须有专人负责,在经过对菌种培养和溶变处理,培养出变异菌种,经筛选和最优化选择出最佳菌种,在培养高峰期加入碳源内,经调整PH后,在发酵期内灭菌处理,在接入种子培养物使其发酵后,按照规定处理方法经分离后得精品L—赖氨酸。
微生物发酵法是利用微生物合成其自身所需的各种氨基酸的能力,通过菌株的溶变等处理,选育出各种营养缺陷型及抗性的变异菌种,以解除代谢调节重的反馈与阻遏,达到过量合成某种氨基酸的一种方法。
发酵法生产赖氨酸通常以淀粉、甘蔗或甜菜制糖后的废糖蜜为原料,其工艺过程为:
淀粉在酸或酶的作用下水解成淀粉糖,假如营养盐调PH值后,进入发酵罐进行灭菌处理,然后接入种子培养物使其发酵,经过微生物发酵后的浓缩液冷冻结晶、离心分离、烘干提纯后即得产品。
制备L—赖氨酸在14L的发酵器中进行。
通过菌种培育,生长菌体和发酵工艺生产赖氨酸,挑选出的FHI28高产菌株,遗传性能稳固,是一株适合工业化生产的优良菌种,在20ml发酵罐中产L—赖氨酸~%,发酵周期59~67h.
2.3.3 其他方式
生产赖氨酸的方发出上述两种方式外,还有由血粉、酪蛋白、脱脂大豆水解后,用离子互换树脂分离而生产的蛋白质水解法,和用化学合成制得廉价中间体,借助酶的生物催化作用生产赖氨酸的化学合成法,但这些方式应用较少。
生产流程简述
不同原科的深层发酵工艺大同小异,要紧不同在于前面的原料处置工艺,而在发酵工段的区别仅在于两个方面,即是不是采纳种子培育和是不是采纳补料工艺。
赖氨酸生产工艺流程图:
空气菌种水淀粉
加压α-淀粉酶液化
冷却糖化酶糖化
除水玉米浆过滤互换柱脱铁
棉花过滤糖蜜糖化液滤渣恢柱脱色
二级种子无机盐配料脱色液
补糖持续灭菌消泡剂蒸发结晶
发酵液氨储晶
等电点分离
回收谷氨酸分离母液赖氨酸
赖氨酸母液干燥
活性炭中和粉碎
脱色赖氨酸
过滤
废炭过滤液
2.4.1原料预处置
目前国内外生产上采纳淀粉加工葡萄糖的液化、糖化方式要紧有:
双酶法、酶酸法、酸法、酸酶法等几种。
与传统酸法水解淀粉相较,酶法具有独特的优势:
可在常温常压和温和酸度下,高效地进行催化反映,简化了设备,改善了劳动条件和降低了本钱;酶催化所需的活化能极低,催化效率远比无机酸高,α-淀粉酶与糖化酶一起作用于淀粉,取得的葡萄糖液DE值达98%以上;酶水解具有专一性,制得产品的纯度高;酶本身是蛋白质,无毒,对酸碱度极为灵敏,故可简单地采纳调剂酸碱度、改变反映温度或添加抑制剂等方式来操纵反映的进行;酶的来源普遍,许多动植物和微生物都可作为某些酶的原料;酶能够回收,重复利用。
此刻生产中大多利用此法。
可是,一般的酶法制糖相对生产周期较长,糖液过滤困难。
2.4.2种子培育
若是不采纳种子培育,即直接采纳孢子悬浮液接种至发酵罐。
采纳种子培育,那么先将孢子接入种子罐中进行培育,然后接入发酵罐。
种子培育的目的是使黄色短杆菌发芽
二级种子培育基:
水解糖%,蜜糖%,尿素%,磷酸氢二钾.%,硫酸镁%,玉米浆%~%,泡敌%,硫酸锰100ml,硫酸亚铁100ml
采纳种子培育工艺有以下优势:
1.缩短了发酵罐的发酵时间,一般可缩短30h左右,从而提高了设备利用率。
虽然增设了种子罐,但包括种子罐在内的总罐容量较小,节省设备投资。
2.种子培养的质量易于控制。
直接接种孢子到生产罐中时,相当于在生产罐中进行种子培养。
由于受发酵条件的制约,生产罐中的营养物(如氮源,磷源等)不能过多,往往不能满足孢子发芽和生长的需要,因此种子发育较慢。
而在种子罐中可以添加适量营养物,以促进种子快速发育,并提高其产酸能力。
事实证明可以达到这种效果。
3.有利于防止杂菌污染。
独立的种子培养车间比发酵车间小的多,环境卫生易于控制。
在种子罐中单独培养时,接入孢子的密度约是直接接入生产罐的10倍,加上种子发育快,受感染的可能性大大降低。
而且,生产罐接入菌丝球以后,很快进入产酸阶段,受感染的可能性小的多。
另外,如果出现菌种退化或者在孢子扩大培养阶段出现染菌,也能在种子培养时提早发现,以便即时采取措施。
即时倒罐,种子罐的损失也只有生产罐的10%。
4.总能耗降低。
因为种子单独培养时,通气搅拌的动力消耗远低于在生产罐中培养。
此外,由于受杂菌感染的可能性大大降低,从而生产培养基的灭菌强度要求较低,节省能耗,也避免了高强度灭菌带来的一些不良后果。
2.4.3微生物发酵
发酵培育基:
水解糖%,蜜糖%,硫酸镁%,氯化钾%,尿素%,磷酸氢二钾.%,玉米浆%,泡敌%,硫酸锰100ml,硫酸亚铁100ml,植物油%,接种量2%。
赖氨酸生产:
1.接种
按种前必需对按种管道进行灭菌,灭菌与大罐灭菌同时进行。
操作肘,打开生产罐按种口通大气的阀门,由种子罐阀门站或底部通入蒸汽,使蒸汽通过种子罐出料管和按种管道通到大罐按种口,排入大气,如此约20min后,关小蒸汽,但仍维持少量出汽,直等到大罐内发酵按冷到35℃以下才关闭接种口通大气的阀门,并关闭蒸汽阀。
然后打开接种阀通发酵罐,关闭种子罐的阀门,并关闭蒸汽阀,用无菌空气将种子培育液压入发酵罐个,按种操作应在半小时内完成。
若是种子顾的气压突然下降,那么表示料液已经排完,因为这时空气直通到生产罐中,同的,控大罐中的压力升高。
接种后关闭接种阀,仍打开通大气的阀门。
种子罐与接种管道要及时清洗,排除残余料液。
接种操作时应该注意种子罐的气压不要超过表压,以防泄漏等事故发生,同时要注意生产罐培育基冷却到预定温度后,冷却水仍在畅开,造成培育基冷却过度。
2.操纵
①温度操纵整个发酵进程操纵32±一、34±1或35±1℃,具体依照菌种和实际情形制定,—般采纳自动操纵。
②罐压操纵一样操纵在表压通风系统压力不足时,可降低罐压,以维持适当的通风量。
③风量操纵50m3标准机械搅拌发酵罐的参考通风量如下:
0—18h:
~vvm
18—30h:
vvm
30h以后:
vvm
罐体积小于50m3时通风量要适当增大,大于50m3那么要减小。
通风量还应该依照发酵进程的产酸情形灵活把握。
加大风量可使产酸速度加速,但菌体呼吸强度和杂酸生成量可能增加。
减小风量会降低产酸速度。
④搅拌转速采纳箭叶涡轮搅拌桨,转速操纵如下:
罐容积5m3150~300r/min
25—30m3110~120r/min
50m390~115r/min
80m390~110r/min
⑤pH操纵糖化完成后可适当加大风量使发酵进入旺盛产酸期。
在产酸期内操纵风量使产酸速度维持在2~3g/h•1,不得过快,以进一步利用糖化作用和避免菌体过早衰老。
⑥发酵进程监测发酵进程的上述参数能够通过仪表检测,而酸度和残被一样靠化学方式检测。
这两项参数是捡验发酵进程好坏的目的指标。
接种后半小时测总糖一次,以后8h测残糖和酸度一次,最后每2h测一次。
⑦放罐条件以酸度再也不增加或残糖再也不降低为放罐条件,正常发酵能达到顶定的产酸度和须定的残糖量,不然为不正常发酵。
不正常发酵时该两次指标达不到,但只要不升酸或不降糖就要放罐。
2.4.4赖氨酸提取
发酵液放罐后直接经Ultra-flo超滤系统过滤,能使真正收率达到99%以上,滤渣中含有大量的蛋白质及菌丝等营养物质,烘干后作饲料,可进行包装销售。
整个工艺进程除最终产品赖氨酸和副产品饲料、硫酸铵外,无多余废水排放。
特点:
1)酵液超滤过滤无须任何预处理,节约成本。
菌渣可直接做饲料,完全消除废液污染。
滤液不含蛋白质量高,保证连续离交进料要求。
过滤收率可达98-99%。
2)由于减少了蛋白对树脂的污染,可增加树脂的吸附容量10%以上,并有效延长树脂寿命。
3)减少悬浮物在连续离交树脂罐内的沉积,减少反冲次数,减少树脂破碎。
4)纳滤低成本的预浓缩,降低能耗。
部分无机盐透过纳滤膜,减少产品灰份。
纳滤透析水回用顶洗,闭路循环提高收率减低成本。
(根据实践表明纳滤浓缩平均成本为20元/吨水)
5)纳滤废水处理系统能将硫酸铵废水处理成回用水,并且回收硫酸铵做肥料。
膜系统适应性强,能随时跟上今后用户对处理后的污水排放水质进一步提高的要求。
6)本工艺膜系统运行平稳,维修容易。
膜系统可分性强,可根据料液流量大小随时切换膜的运行数量,其余可进行清洗、保护或更换等操作,故膜系统无传统工艺的每年大修要求,在40℃~45℃左右用低压力大流量对膜进行清洗,只需清洗一小时左右即能使膜通量恢复,而不用拆卸设备,可实现全自动运行与清洗。
7)本工艺的占地面积大大缩小。
由于膜设备都是由膜元件叠加起来的,使膜设备占地极小。
膜系统为全封闭系统,无物料和气体的泄漏,噪音小,并容易实现全自动化运行。
工艺计算
原料预处置车间:
计算依据:
全年按300天计算,发酵周期64hr,要紧生产原料为玉米淀粉乳,设计生产技术提取总收率90%,玉米淀粉含淀粉86%,淀粉原料单耗t
(一)物料平稳计算
A生产过量总物料衡算
1.总原料需求:
t
成只天天产量:
t取整数为34t
实际成品年产:
t/a
天天投料量:
t
2.总物料衡算
1000㎏纯淀粉理论上能生产100%赖氨酸的量为:
1000㎏纯淀粉事实上能生产的100%赖氨酸的量为:
1000㎏工业淀粉(含量86%的玉米淀粉)产生的100%赖氨酸的量为:
3.淀粉的单耗
生产1000㎏100%赖氨酸理论上消耗纯淀粉的量为:
生产1000㎏100%赖氨酸理论上消耗工业淀粉的量为:
生产1000㎏100%赖氨酸实际消耗纯淀粉的量为:
生产1000㎏100%赖氨酸实际消耗工业淀粉的量为:
4.总收率
淀粉利用率:
生产进程的总损失:
5.原料及中间体的计算
淀粉用量为:
糖化液量纯糖量为:
换算成含量24%的糖液量为:
发酵液量的计算:
提掏出来的赖氨酸的量为:
换算成含量90%的提取液为d
赖氨酸废液量(以排出的废液含0.7g/100ml赖氨酸计算):
表1:
年产1万吨赖氨酸生产工艺的总物料衡算结果
项目
以玉米淀粉为原料
生产1万吨100%赖氨酸
(t/d)
原料淀粉/t
21240
24%糖液量/t
82790
90%的赖氨酸量/t
9500
100%赖氨酸量/t
10000
34
排出含%谷氨酸的废液量/m3
173823
591
B.淀粉制糖工艺的物料衡算
1.淀粉浆量及加水量
赖氨酸生产进程中加水的比例为1:
,即1000㎏的工业淀粉调浆时的加水量为2500㎏,由此制得的淀粉浆量为3500㎏
淀粉浆中干物质(淀粉)的浓度:
2.液化用酶的量
淀粉液化用酶是α-淀粉酶,其用量为淀粉浆的%,即α-淀粉酶的用量为:
3.
的加入量
由于α-淀粉酶是一种金属酶,
能使α-淀粉酶的活性大为提高,一样来讲,
的加入量是淀粉浆量的%,那么
量为:
4.糖化酶的用量
糖化酶的用量是淀粉浆量的%,即糖化酶量:
5.糖化液的量
淀粉经α-淀粉酶液化、糖化酶糖化后,制得的24%糖化液的量为:
24%的糖液的相对密度为,那么糖化液的体积就为
6.加珍珠岩量和滤渣量
淀粉通过液化、糖化后的糖化液过滤比较困难,需加入珍珠岩进行助滤,加入量为糖化的%,即
而过滤后的滤渣是含水70%的废珍珠岩,滤渣量有
表2:
制糖工艺的物料衡算
进入糖化过程的物料
离开糖化过程的物料
项目
物料比例/㎏
日投料量/㎏
项目
物料比例/㎏
日投料量/㎏
工业淀粉
1000
72220
糖化液
3898
281514
配料水
2500
180550
滤渣
1408
液化酶
43
108
糖化酶
108
珍珠岩
422
(二)热量衡算
1)淀粉液工序的热量衡算
A.液化加热蒸量
淀粉液化时加热需要消耗的蒸汽量(
)可按下式计算:
式中,G为淀粉浆的重量,㎏/h;C为淀粉浆的比热容,kJ/(㎏·k);
为淀粉浆的初始温度,℃;
为液化温度,℃;I为加热蒸汽的热焓,2738kJ/㎏﹙,表压);λ为加热蒸汽凝结水的热焓,363K时377kJ/㎏
B.淀粉浆量G
依照物料衡算知,日投工业淀粉量为,24h持续液化,即每小时的处置量为
,液化调浆时淀粉与水的比例关系为1:
,淀粉浆量就为
,淀粉浆中淀粉的浓度为
淀粉浆的比热容C可按下式计算:
kJ/(㎏·k)
式中
为淀粉的比热容,kJ/(㎏·k);
为淀粉浆中淀粉的含量(浓度);
为水的比热容,kJ/(㎏·k)
C.蒸汽用量
灭酶用的蒸汽量
灭酶时需将液化液由90℃加热至100℃,100℃时蒸汽的λ为419kJ/㎏,那么灭酶用的蒸汽量
灭酶进程一样要求在20min内使液化液由90℃加热至100℃,那么蒸汽的顶峰用量为
因此,液化进程的平均用蒸汽量为
,每日蒸汽平均用量为d,而顶峰时用气量为
D.液化液的冷却水用量
液化、灭酶进程完成后,需将物料由100℃降温至65℃,假设冷却水的入口温度是20℃,出水温度是58.7℃,那么需要的冷却水用量即为:
天天的用水量为
2)液化液糖化进程的热量衡算
年产万吨赖氨酸的工厂,按前面的计算,日产含糖24%的糖液281t,按相对密度,其体积为
,糖化操作的周期是30h,选用100
的糖化罐,装料75
,生产上需要的糖化罐只数为:
,取用5只罐
按生产上的流程利用板式换热器,使糖化液(经灭菌后)由85℃降至60℃,用二次水冷却,冷却水的入口温度20℃,出口温度为45℃,其平均用水量为:
生产上一样要求在2h内把75
的糖液冷却至40℃,其顶峰用水量为:
由于天天同时运转的糖化罐有
,天天冷却水用量是:
(三)进程水的衡算
糖化工序用水量:
(1)配料用水量:
年产万吨赖氨酸的生产工厂日投工业淀粉量为,配料时的加水比例是1:
,用水量就能够够算出是
,即h
(2)液化液冷却水用量:
前面已算出液化液冷却水的用量是d
(3)糖化液冷却水用量:
前面已算得糖化液冷却水用量是d,顶峰时用水量h
(四)设备的选择
生产设备
设备名称
规格、容积
材质
台数
糖化罐
100
Q235-A/防腐
5
板式换热器
60
1Cr18Ni9
2
动力
蒸汽
25t/h
电力
5400kw
冷冻机
520kw
8AS17
3
空气压缩机
60
/min
4
3
凉水塔
300t/h
2
发酵车间
持续发酵和发酵工序热量衡算
1.培育液持续灭菌用蒸汽量
假设发酵进程所用的发酵罐为200m3,装料系数为那么每只罐产