烧结余热技术说明书.docx
《烧结余热技术说明书.docx》由会员分享,可在线阅读,更多相关《烧结余热技术说明书.docx(68页珍藏版)》请在冰豆网上搜索。
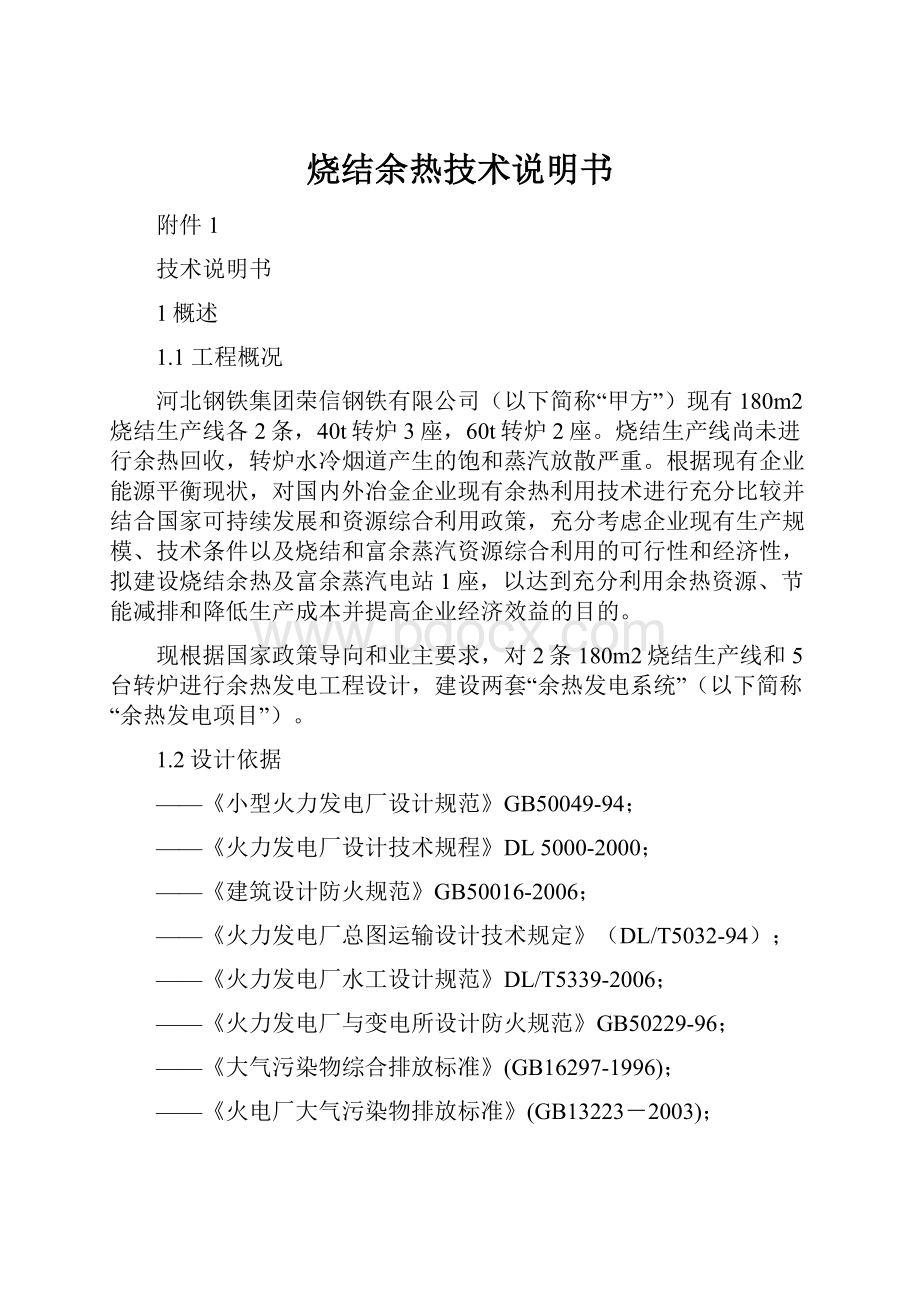
烧结余热技术说明书
附件1
技术说明书
1概述
1.1工程概况
河北钢铁集团荣信钢铁有限公司(以下简称“甲方”)现有180m2烧结生产线各2条,40t转炉3座,60t转炉2座。
烧结生产线尚未进行余热回收,转炉水冷烟道产生的饱和蒸汽放散严重。
根据现有企业能源平衡现状,对国内外冶金企业现有余热利用技术进行充分比较并结合国家可持续发展和资源综合利用政策,充分考虑企业现有生产规模、技术条件以及烧结和富余蒸汽资源综合利用的可行性和经济性,拟建设烧结余热及富余蒸汽电站1座,以达到充分利用余热资源、节能减排和降低生产成本并提高企业经济效益的目的。
现根据国家政策导向和业主要求,对2条180m2烧结生产线和5台转炉进行余热发电工程设计,建设两套“余热发电系统”(以下简称“余热发电项目”)。
1.2设计依据
——《小型火力发电厂设计规范》GB50049-94;
——《火力发电厂设计技术规程》DL5000-2000;
——《建筑设计防火规范》GB50016-2006;
——《火力发电厂总图运输设计技术规定》(DL/T5032-94);
——《火力发电厂水工设计规范》DL/T5339-2006;
——《火力发电厂与变电所设计防火规范》GB50229-96;
——《大气污染物综合排放标准》(GB16297-1996);
——《火电厂大气污染物排放标准》(GB13223-2003);
——《火力发电厂劳动安全和工业卫生设计规程》(DL5053-96)
——《火力发电厂初步设计文件内容深度规定》DLGJ9-92;
——《工程建设标准强制性条文》(2006年);
甲方提供的基础资料。
其它现行的国家规章、规范、标准等。
1.3设计原则
由于影响烧结余热回收效率的因素很多,如烧结矿的产量、燃烧温度、料层层厚,冷却机的速度,冷却介质的初温和废气流量等。
根据烧结机的设计和运行情况,结合以往烧结余热电站的设计、调试及运行经验,在充分利用余热资源的条件下,以“稳定可靠,技术先进,降低能耗,节省投资”为基准,遵守下列原则:
1)遵循国家规范、规程、规定和行业相关强制性标准;
2)贯彻“安全、可靠、经济、适用、符合国情”的电力建设方针;
3)在保证烧结工艺生产安全和稳定的前提下利用余热资源;
4)采用热量梯级利用原则,最大程度回收烟气热量;
5)选用技术先进、成熟、运行可靠的余热回收及发电设备;
6)余热回收及发电系统满足国家关于节能减排及高效环保的要求。
1.4工程主要技术经济指标
项目
数值
单位
1)180m2烧结余热发电
余热发电装机容量
1×12
MW
设计发电功率
12
MW
设计平均发电功率
9.6
MW
烧结年作业时数
8150
h
发电年作业时数
7800
h
2)5台转炉饱和蒸汽发电
余热发电装机容量
1×4.5
MW
设计发电功率
4.5
MW
设计平均发电功率
4.2
MW
炼钢年作业时数
7900
h
发电年作业时数
7800
h
3)两台机合计
年发电量
7488+3276
104kW.h
电站年自耗电量
电站投用后,烧结风机节电量
2066
304
104kW.h
电站自耗电率
电站自耗电率(扣除节电)
19.2
16.4
%
年外供电量(合并节电量)
8697(8998)
104kW.h
1.5初步设计方案及相关配套图纸拟定后,必须经甲方审核。
有权对不符合工艺要求的管线、设备等提出更改或增加相应设备的权利。
2总图及道路运输
2.1总平面
本工程主要建设内容包括:
2台单压余热锅炉,2台双压余热锅炉,1座烧结余热发电主厂房、1座转炉余热发电主厂房、1套12MW机组循环水系统、1套4.5MW机组循环水系统、1套除盐水系统等。
烧结余热发电:
由余热锅炉、汽轮机房、电气楼、循环水站、除盐水站组成。
余热锅炉布置在烧结环冷机旁,其余部分均布置在烧结旁预留电站场地内。
转炉余热发电:
由汽轮机房、电气楼、循环水站及蒸汽蓄热站组成。
电气楼、主厂房、循环水站及除盐水站均按电站常规布置;具体布置方案待甲方提供总图位置后进行。
2.2运输及道路
余热电站建成投产后,能源介质均采用管道和电缆输送,站内只有药品、备件及油品运输需求,运量较小,厂区现有道路及运输设施即可满足要求。
2.3区域绿化
本工程不考虑新增集中绿化用地,仅利用边角地绿化。
新建的主厂房和循环水系统区域的绿化权衡考虑,做到环境优美,小景协调,力求投资和美化效果双赢。
3工艺系统
3.1烧结工艺及余热资源
烧结生产线由烧结机和冷却机两大部分组成。
烧结原料经点火并烧结后,烧结矿从烧结机尾部卸到冷却机上进行冷却,冷却后的烧结矿经输送机送至矿仓以备高炉冶炼取用。
一般情况下,烧结终点相邻几个风箱烟气温度较高,约250~450℃,当烧结终点不能较好控制在倒数第二个风箱时,烧结机尾部烟气有一定热量可以利用;同时,烧结环冷机进口的给矿温度平均在650~750℃之间,环冷机出口的矿温在150℃以下。
烧结矿冷却过程中,烧结矿所携带的热量被转换成废气显热,废气温度从前到后逐步降低,给矿部废气温度最高,一般在450℃左右,排矿部温度最低。
根据两台烧结及环冷机气固换热的计算参数及经验评估,每台烧结机尾部可用烟气分布在最后4个风箱内;采用热风循环工艺后,每台环冷机可用废气约为前部40%风箱对应料面上热风。
具体参数见下表:
烧结机回收烟气参数
名称
#1烧结机
#2烧结机
单位
余热废气平均风量
80000
80000
Nm3/h
余热废气平均温度
~350
~350
℃
环冷机回收废气参数
名称
#1环冷机
#2环冷机
单位
余热废气平均风量
250000
250000
Nm3/h
余热废气平均温度
~330
~330
℃
3.2炼钢工艺及余热资源
炼钢厂现有40t转炉3座,60t转炉2座,钢产量约345t/h。
转炉设有汽化冷却系统,蒸汽产量约为27~35t/h,运行压力约0.8MPa;目前,企业无余热回收装置,剩余蒸汽大量放散,既浪费了能源,同时还造成环境污染;因此,炼钢余热蒸汽回收利用符合国家和企业利益,需要快速建成并达产增效。
3.3烧结余热回收方案
3.3.1烧结机余热回收
根据烧结工艺运行要求,为了更好的保证烧结机独立运行的稳定性和可靠性,2台烧结机分别设置余热锅炉回收烟气余热为宜。
正常情况下,烧结机尾部4个风箱并联余热锅炉运行,后部烟气经余热锅炉后返回主抽烟道,烟道和锅炉分别设置分断阀和调节阀进行系统投切和运行调节,以保证烧结工艺和余热回收系统的正常和高效运行。
根据烟气余热条件、除尘工艺要求并结合环冷机余热回收方案,烧结余热锅炉选用单压系统,蒸汽压力1.6MPa、温度330℃;2台烧结余热锅炉所产生过热蒸汽与环冷机余热锅炉所产相同压力的蒸汽混合后送入汽轮发电机组做功发电,凝结水循环使用。
3.3.2环冷机余热回收
根据环冷机余热资源条件,按梯级取风原则,将环冷机废气进一步细化成一段高温、一段中温和二段中温三部分。
其中,高温废气为环冷机前部风箱上部的热空气,中温废气为环冷机中前部风箱上部的热空气,具体参数如下表所示:
高温废气参数
名称
1#环冷机
2#环冷机
单位
余热废气风量
100000
100000
Nm3/h
余热废气温度
340~400
340~400
℃
中温废气参数
名称
1#环冷机
2#环冷机
单位
余热废气风量
150000
150000
Nm3/h
余热废气温度
280~340
280~340
℃
注:
以上环冷机废气参数将随工艺条件的变化而变化。
当实际参数发生变化时,余热锅炉及余热发电参数也将会作相应的改变。
根据以上余热资源条件、现场实际和已建成同类项目经验,为增加余热回收系统运行灵活性,两台烧结冷却机各配置1台余热锅炉,回收废气余热生产蒸汽,锅炉排气送回环冷机循环使用。
余热锅炉选用双压系统,余热锅炉产生两种压力的过热蒸汽,其中,高参数蒸汽压力1.6MPa、温度350℃;低参数蒸汽压力0.3MPa、温度190℃;两种压力的过热蒸汽均送入补汽凝汽式汽轮发电机组做功发电,其中高参数蒸汽还需与烧结余热蒸汽混合均匀后共同进入汽轮机,凝结水循环使用。
3.4炼钢余热蒸汽回收方案
将炼钢5座转炉所产余热蒸汽汇入同一母管,并设置蒸汽蓄热器进行负荷波动调节,使富余蒸汽得以平稳输出,在设置汽水分离装置脱出蒸汽所含99%的机械水后,利用1套汽轮发电机组将饱和蒸汽热能转化为电能输出。
3.5热力系统及装机方案
3.5.1热力系统及工艺流程
1)烧结余热发电
本系统包括:
烧结单压余热锅炉系统2套,环冷双压余热锅炉系统2套及补汽凝汽式汽轮发电机组1套。
经计算并结合烧结余热发电的特点和经验,选择高参数锅炉给水压力2.1MPa,给水温度150℃;低参数锅炉给水压力0.8MPa,给水温度40℃。
烧结余热锅炉所产过热蒸汽参数为1.6MPa、330℃;环冷余热锅炉所产高参数过热蒸汽参数为1.6MPa、350℃,低参数过热蒸汽参数为0.3MPa、190℃。
来自余热锅炉的过热蒸汽按不同压力级别各自混合后,通过主蒸汽、补汽管道分别送至汽轮机主汽及补汽入口,蒸汽进入汽轮机内共同做功后凝结成水,凝结水经凝结水泵加压后送出,经轴封冷却器加热后分别送往2台环冷余热锅炉凝结水加热器,热水进入低压汽包自除氧,部分除氧水在低参数蒸发系统自然循环产生蒸汽,部分除氧水由锅炉给水泵送往环冷余热锅炉高参数省煤器继续升温,出水分两路,一路进烧结锅炉汽包,一路进环冷锅炉高参数汽包,在各自蒸发系统内自然循环产生蒸汽;不同压力和不同锅炉所产饱和蒸汽分别经各自过热器升温后送出,按不同压力级别混合后前往汽轮机,完成一个完整的热力循环;系统补水进入凝汽器,在真空条件下达到预除氧目的。
2)转炉饱和蒸汽发电
本系统包括:
蒸汽蓄热系统1套及饱和汽轮发电机组1套。
汽轮机组进汽要求其进汽品质执行国家标准GB/T1576-2008、GB/T12145-2008标准。
转炉蒸汽经蓄热器缓冲后混合输出,饱和蒸汽脱水后进入汽轮发电机组,在汽轮机内做功后凝结成水,经水泵加压后送回炼钢,分别进入各转炉除氧系统,除氧后利用给水泵送入汽化冷却系统,强制循环吸热蒸发后再次送出,完成一个完整的热力循环。
3.5.2余热电站装机方案
1)烧结余热发电
按照前述的余热废气量、温度及余热回收方案,在两台烧结机旁各设置8t/h单压余热锅炉1台;两台环冷机旁各设置(20+5)t/h双压余热锅炉1台;根据余热锅炉装机方案,正常生产时,4台余热锅炉可产1.6MPa、344℃(混合后)的过热蒸汽56t/h,0.3MPa饱和蒸汽10t/h;两种压力的过热蒸汽均送入补汽凝汽式汽轮机做功发电,根据蒸汽特性、现有同类机组运行情况和机组系列化参数要求,选取汽机进汽参数分别为:
1.4MPa(a)、335℃和0.3MPa(a)、180℃;根据前述蒸汽条件计算,电站装机参数如下表:
序号
名称
参数
单位
1
总回收蒸汽量
56+10
t/h
2
设计发电功率
12
MW
3
电站装机功率
12
MW
2)炼钢余热发电
5座转炉共产生0.8MPa饱和蒸汽27~35t/h;为调节系统蒸汽产消量,稳定蒸汽输出、保证机组运行稳定性,需要设置350m3蒸汽蓄热器,考虑原系统已有蓄热器后,增设1台150m3蒸汽蓄热器(暂定),将发电蒸汽压力控制在0.5MPa以上;所有剩余饱和蒸汽均进入饱和蒸汽轮机做功发电。
根据蓄热器运行参数、现有同类机组运行情况和机组系列化参数要求,选取汽机进汽压力为0.5MPa(a);根据前述蒸汽条件计算,电站装机参数如下表:
序号
名称
参数
单位
1
总回收蒸汽量
27~35
t/h
2
设计发电功率
3.3~4.2
MW
3
电站装机功率
4.5
MW
3.6主要设备选型
3.6.1烟风系统
烧结环冷机余热利用烟风系统由风机、管道和阀门组成,主要设备是循环风机,循环风机及电机主要设备参数如下:
热风循环风机
项目
型号及规格
型式
单吸离心风机
数量
1台
额定风量
290000Nm³/h
额定风温
135℃
额定全压
5500Pa
配套电机
项目
型号及规格
型式
高压三相异步
数量
1台
电机功率
1000kW
电机转速
730r/min
电机电压
10.5kV
电机防护等级
IP54
电机功率暂定,待风机订货后调整。
3.6.2主体设备
1)烧结余热发电
根据余热回收方案,本系统设置单压和双压余热锅炉各2台,汽轮发电机组1台,余热锅炉及汽轮发电机组主要参数如下:
烧结余热锅炉主要参数表
名称
规格参数
单位
额定蒸发量
8
t/h
额定蒸汽压力
1.6
MPa
额定蒸汽温度
330
℃
环冷余热锅炉主要参数表
名称
规格参数
单位
高参数段
额定蒸发量
20
t/h
额定蒸汽压力
1.6
MPa
额定蒸汽温度
350
℃
低参数段
额定蒸发量
5
t/h
额定蒸汽压力
0.3
MPa
额定蒸汽温度
190
℃
汽轮机主要参数表
项目
型号及规格
型号
N12-1.4/0.3
型式
补汽凝汽式
最大功率
12MW
额定功率
12MW
额定主蒸汽进汽量
56t/h
额定主蒸汽进汽参数
1.4MPa(a)、335℃
额定补汽进汽量
10t/h
额定补汽进汽参数
0.3MPa(a)、180℃
额定排汽压力
0.007MPa
额定转速
3000r/min
一阶临界转速
~1580r/min
转向
顺时针
发电机主要参数表
项目
型号及规格
型号
QF-12-2/10
额定功率
12MW
额定功率因数
0.85(滞后)
额定频率
50Hz
额定转速
3000rpm
额定电压
10.5kV
冷却方式
空内冷
励磁系统
无刷励磁
2)转炉余热发电
根据发电需求,本系统增设蒸汽蓄热装置1套(暂定),汽水分离装置1套,汽轮发电机组1套,达到饱和蒸汽发电目的;各设备主要参数如下:
汽轮机主要参数表
项目
型号及规格
型号
N4.5-0.5
型式
凝汽式饱和汽轮机组
额定功率
4.5MW
计算功率
3.3~4.2MW
额定进汽量
27~35t/h
额定进汽压力
0.5MPa(a)
额定排汽压力
0.007MPa
额定转速
3000r/min
一阶临界转速
~1580r/min
转向
顺时针
发电机主要参数表
项目
型号及规格
型号
QF-4.5-2/10
额定功率
4.5MW
额定功率因数
0.85(滞后)
额定频率
50Hz
额定转速
3000rpm
额定电压
10.5kV
冷却方式
空内冷
励磁系统
无刷励磁
蒸汽蓄热器主要参数表
项目
规格参数
水容积
150m3
蒸汽储量
3.5t/h
设计压力
1.6MPa
充热压力
0.8MPa
放热压力
0.5MPa
充热速度
15t/h
放热速度
8t/h
蒸汽含水率
≤3%
4余热锅炉
本工程设8t/h单压余热锅炉和(20+5)t/h双压余热锅炉各2台。
4.1结构形式
4.1.1烧结余热锅炉
烧结余热锅炉采用立式布置,锅炉本体外形尺寸5m×5m×15m(L×W×H),从上往下依次是:
过热器、蒸发器。
热风自上而下流动,来自主烟道尾部的高温风从锅炉顶部进风,从底部出风返回主烟道;锅炉底部设置了积灰斗,在灰斗的上侧部设置锅炉排风口。
所有锅炉组件均布置在同一个框架内。
受热面均使用环向翅片换热管,采用顺列布置减少灰尘冲刷;同时,将过热器和蒸发器前三排的换热管选用加厚管并加装防磨护板,较大程度地降低磨损,延长使用年限。
余热锅炉采用型钢框架和内做隔热层的轻型护壁;锅炉组件之间的管箱护壁上设人孔,锅炉进口设截断阀,出口设调节阀,便于锅炉运行调节和检修。
4.1.2环冷余热锅炉
烧结余热锅炉采用立式布置,锅炉本体外形尺寸12m×5m×25m(L×W×H),从上往下依次是:
高参数过热器、高参数蒸发器、低参数过热器、高参数省煤器、低参数蒸发器和给水加热器。
热风自上而下流动,来自环冷机的高温风从锅炉顶部进风。
在锅炉底部设置了积灰斗,在灰斗的上侧部设置了锅炉的排风口。
所有锅炉组件均布置在同一个框架内。
过热器、蒸发器和省煤器使用环向翅片换热管,并采用错列布置加强换热;同时,在过热器和高参数蒸发器前三排的换热管选用加厚型并加装防磨护板,较大程度地降低磨损,延长使用年限。
余热锅炉采用型钢框架和内做隔热层的轻型护壁;锅炉组件之间的管箱护壁上均设有人孔,以便于锅炉的检修。
4.2锅炉给水
烧结余热锅炉供水系统包含凝水泵、锅炉给水泵及管路系统。
来自凝汽器的冷凝水经过汽封加热器加热后送到环冷锅炉给水加热器,然后进入低压汽包除氧,除氧水经锅炉给水泵加压送入环冷余热锅炉高参数省煤器,出水分别向烧结余热锅炉和环冷余热锅炉高参数汽包供水。
除盐水站补水进入余热锅炉除氧器和汽机凝汽器。
凝结水管道需增加低压加热器一台及附属设施一套。
4.3炉水校正
炉水校正系统包括储药、搅拌、溶液箱、加药泵及加药管路等。
余热锅炉运行过程中,须定期对锅炉炉水水质监测。
当炉水碱度低时,通过加药泵和加药管路将磷酸三钠(Na3PO4)药液分别送至余热锅炉高、低参数汽包,以调节锅内水质。
本系统设炉水加药装置2套,每套装置承担一条烧结生产线2台余热锅炉系统加药任务。
4.4主要设备参数
烧结余热锅炉主要参数表
名称
参数
单位
烟气流量
80000
Nm3/h
平均入口烟温
~340
℃
平均出口烟温
220
℃
烟气含尘量
<5
g/Nm3
额定蒸发量
≤8
t/h
额定蒸汽压力
1.6
MPa
额定蒸汽温度
330
℃
环冷余热锅炉主要参数表
名称
参数
单位
烟气流量
250000
Nm3/h
平均入口烟温
~330
℃
平均出口烟温
135
℃
废气含尘量
<3
g/Nm3
高参数过热蒸汽蒸发量
≤20
t/h
低参数饱和蒸汽蒸发量
≤5
t/h
高参数蒸汽压力
1.6
MPa
低参数蒸汽压力
0.3
MPa
高参数过热蒸汽温度
350
℃
环冷余热锅炉除氧器
名称
参数
单位
工作温度
104
℃
工作压力
~0.32
MPa
除氧水量
34
t/h
出水含氧量
<0.05
mg/L
环冷锅炉引风机参数表
名称
参数
单位
风机入口风量
250000
Nm3/h
风机入口风温
135
℃
风机全压
5500
Pa
电机功率
900
kW
电机电压
10
kV
5汽轮发电机组
5.1汽轮发电机组成套范围
本工程设置补汽凝汽式汽轮发电机组1套,饱和蒸汽汽轮发电机组1套。
其中,汽轮机组包括:
汽轮机主机、凝汽系统、真空系统、汽封系统、供油系统、调节系统、保安系统、工业水系统、循环水系统、加热器系统、润滑油系统、等主辅系统;发电机组包括:
发电机主机、空冷装置、励磁装置等主辅机。
5.2调节、保安和润滑
5.2.1供油系统
本工程供油系统由油箱、主油泵、启动油泵、润滑油泵、事故油泵、注油器、冷油器、滤油器、减压阀等组成。
主油泵与汽轮机转子直联,由注油器供油;起动油泵为交流高压电动油泵,用于机组起动时的供油,机组起动后,当主油泵出口油压大于起动油泵油压出口时,高压电动油泵可自动停机或人工停机。
润滑油泵为低压电动油泵,用于机组盘车时的供油。
事故油泵为直流电动油泵,用于交流电源断电时,主油泵、高压油泵、低压油泵均无法工作时的润滑油供油。
油箱设有事故放油口、就地指示液位计和远传液位计、排油烟机,可以进行液位巡视和集中监视。
供油系统相关设备随汽轮机主机成套供货,相关技术参数由汽轮机制造商确定,以满足在规定工况下汽轮机均能正常工作为原则。
5.2.2调节系统
本项目汽轮机采用汽机配套专用数字式电-液调节系统进行控制。
电液控制装置接收汽轮机运行过程中的转速、发电功率和主汽压力信号,输出转速、功率或压力等相应的控制信号;电-液转换器接收此控制信号并调节二次油压,经由错油门、油动机等调节汽轮机主汽门开度来调节汽轮机进汽量,达到调节汽轮机转速、发电功率和主汽压力的目的。
除上述调节功能外,还使用电液控制装置完成汽轮机启动时的自动升速。
5.2.3保安系统
保安系统由危急遮断器、电磁泄油阀和主汽门等共同组成。
5.3抽真空装置
抽真空系统由射水抽气器、射水泵、射水箱等共同组成。
凝汽器内产生的不凝结气体,由射水泵向射水抽气器射水抽出,维持凝汽器内真空度。
5.4汽封系统
汽封系统由均压箱、压力调节阀、轴封冷却器、滤汽器、节流孔板等共同组成。
在补汽阀前引出新蒸汽作为汽源,经过节流孔板后供给均压箱,均压箱上装有直接作用的压力调节阀,保持箱内压力稳定在0.101~0.127MPa(a)范围内,均压后的蒸汽向汽轮机两端轴封供给密封用蒸汽。
汽轮机轴封漏汽、主汽门、调节汽阀的阀杆漏汽均引入轴封冷却器,用于加热凝结水,提高电站热效率。
6循环水系统
6.1概述
本系统主要供汽轮机凝汽器、空冷器、冷油器、锅炉给水泵、风机、射水抽气系统等设备的冷却用水采用工业水与循环水双向冷却(凝汽器除外)。
由于两套汽轮发电机组距离较远,拟分别设置循环供水系统。
射水箱溢流到冷却塔。
6.1.1循环冷却水量
本系统所需循环冷却水量约7160m3/h,具体计算如下:
循环冷却水量计算表
项目
12MW机组(m3/h)
4.5MW机组(m3/h)
汽轮机凝汽器冷却水
4290
2510
冷油器冷却水
80
40
空冷器冷却水
100
60
锅炉给水泵及射水抽气器等冷却水
10
4
循环风机轴承及汽水取样器冷却水
40
1
小计
4520
2615
其它用水
20
5
总计
4540
2620
606.1.2循环冷却水补水量
本系统所需循环冷却水补水量约为128m3/h,具体计算如下:
循环冷却水补水量计算表
序号
项目
最大小时用水(m3/h)
1
冷却塔蒸发损失
93
2
冷却塔风吹损失
22
3
排污及渗漏损失
13
4
合计
128
6.2循环冷却水系统
6.2.1供水方案及流程
循环水加压泵从冷水池取水,加压后送往各用水设备,冷却回水进入冷却塔降温后回到冷水池。
系统补水来自厂区管网,从厂区现有生产新水管网上就近接点,接出两条DN100的给水管道分别为两套循环水站补水,补水管道上设置流量计。
根据电站用水需求和气象条件,循环水系统采用开式冷却系统,设置机械通风冷却塔;冷却系统外供水量为7200m3/h,供水压力按0.24MPa设计。
两套循环水系统分别为烧结余热汽轮发电机组循环水及转炉余热汽轮发电机组循